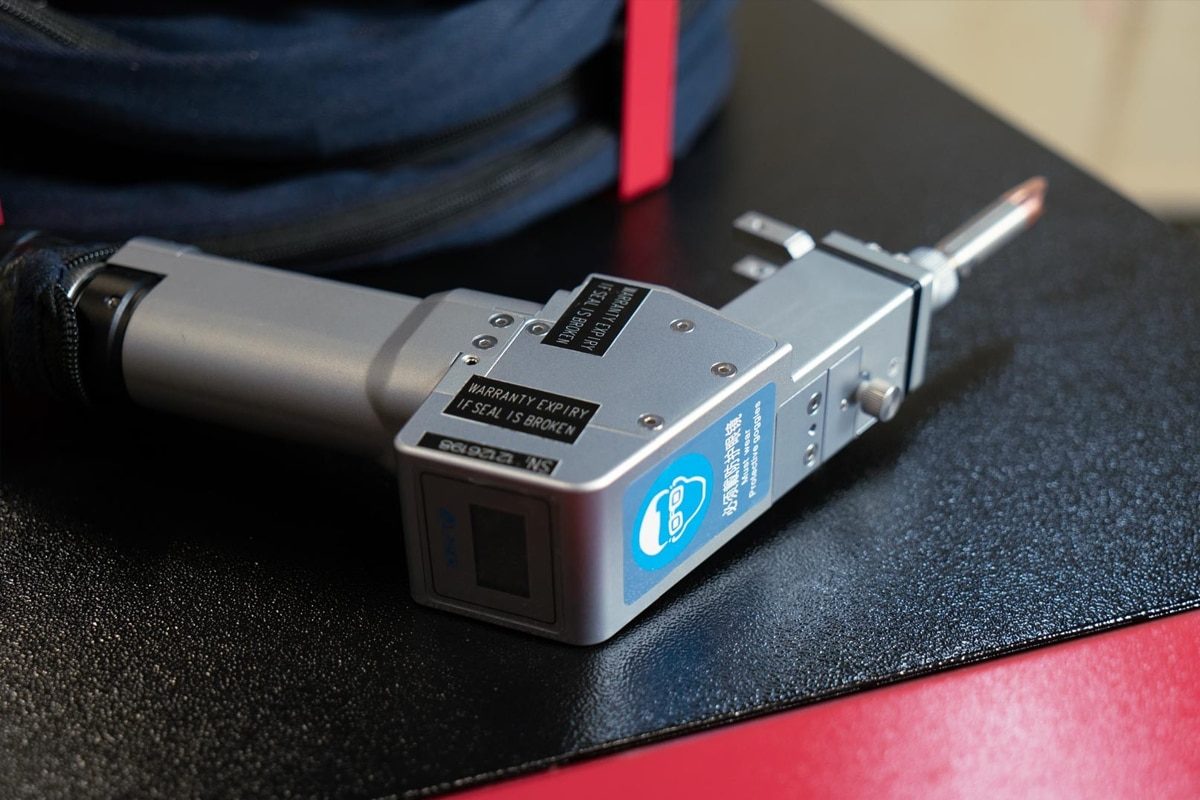
Does The Laser Welding Machine Provide Accurate And Accurate Welding Capacity?
In modern manufacturing, precision and accuracy are crucial. As industries seek more efficient and reliable methods of joining materials, laser welding has emerged as a promising solution. Laser welding machines utilize highly concentrated beams of energy to provide unparalleled precision in fusing metals and other materials. But can this technology really deliver on its promise of precise welding capabilities? In this article, We will take an in-depth look at the benefits and challenges associated with laser welding technologies and examine their potential to provide precision welding in a variety of industrial applications. Uncover the truth behind laser welding’s touted accuracy and precision with a comprehensive understanding of its capabilities and limitations.
Table of Contents
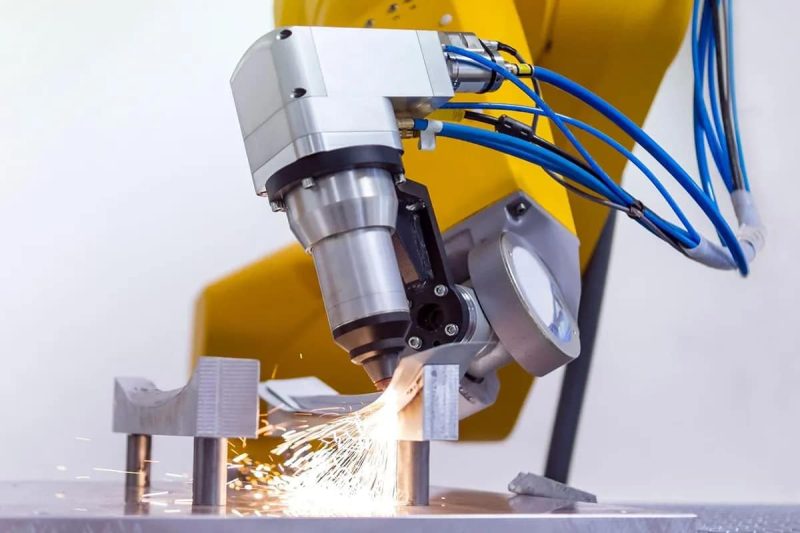
Learn About Laser Welding Technology
To solve this problem, we must first understand the basic principles of laser welding. Unlike traditional welding methods that rely on an electrical current or flame to generate heat, laser welding utilizes a concentrated, coherent beam of light to melt and fuse materials. The basic principle is as follows:
- Laser Beam Generation: Laser welding begins by generating a high-energy laser beam. This process typically involves the use of a laser source such as a solid-state laser generator, a fiber laser generator, or a CO2 laser generator. These laser generators emit light through a stimulated emission process, producing a coherent and focused beam of light with precise characteristics.
- Focusing Optics: Once generated, the laser beam is directed through a series of focusing optics, including mirrors and lenses. These optics shape and concentrate the laser beam, allowing for precise control over its intensity and focus. By adjusting the position and orientation of the focusing optics, operators can tailor the laser beam to the specific requirements of the welding application.
- Material Interaction: As the focused laser beam interacts with the materials to be welded, several key processes occur. The laser energy is absorbed by the material’s surface, causing it to rapidly heat up and reach its melting point. This localized heating results in the formation of a molten pool at the weld joint, where the materials fuse to create a strong bond.
- Control System: A control system governs the operation of the laser welding process, ensuring precise and consistent results. This system monitors and adjusts various parameters, including laser power, beam diameter, pulse duration, and travel speed, to optimize the welding process for each specific application. Advanced control systems may also incorporate feedback mechanisms, such as sensors and cameras, to provide real-time monitoring and adjustment of the welding parameters.
By mastering the basic principles and steps of laser welding technology, manufacturers can harness its capabilities to achieve precise, high-quality welds in a wide range of materials and applications. From automotive and aerospace components to medical devices and electronics, laser welding continues to drive innovation and excellence in modern manufacturing processes.
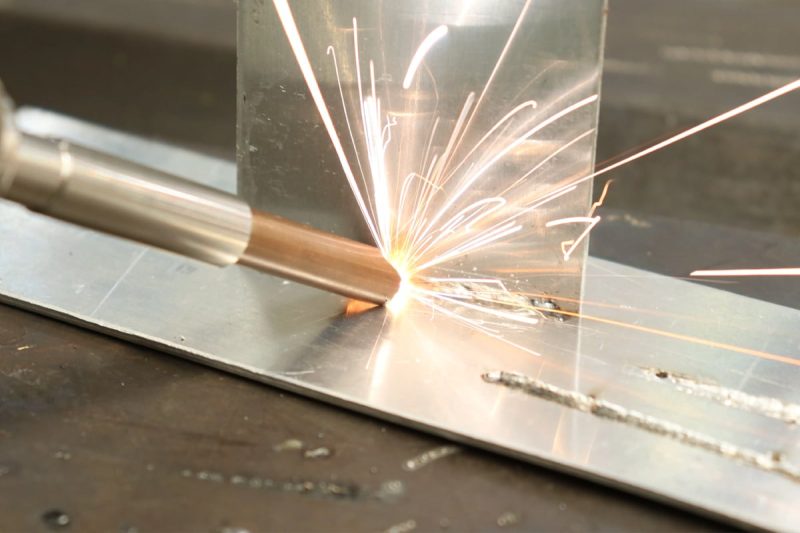
The Accuracy And Accuracy Of Laser Welding
Precision and accuracy are important benchmarks for modern manufacturing processes, determining the quality and reliability of the final product. Laser welding technology provides unparalleled precision in joining materials by utilizing a highly concentrated beam of light. Let’s explore how laser welding technology enables superior precision and accuracy.
Controlled Energy Delivery
Laser welding achieves precision and accuracy through controlled energy delivery. Unlike traditional welding methods that rely on broad heat sources, laser beams can be precisely focused and directed onto the weld joint. This focused energy minimizes heat dispersion and allows for precise control over the welding process, resulting in accurate welds with minimal distortion.
Minimal Heat-Affected Zone (HAZ)
Laser welding minimizes the size of the heat-affected zone (HAZ) surrounding the weld area. By delivering heat in a highly localized manner, laser welding reduces the risk of thermal distortion and preserves the mechanical properties of the base material. This precision in heat application ensures that the welded components maintain their structural integrity and dimensional accuracy.
Fine Control Over Parameters
Laser welding systems offer fine control over various welding parameters, including laser power, beam diameter, pulse duration, and travel speed. Operators can tailor these parameters to suit the specific requirements of each welding application, ensuring precise and consistent results. This level of control allows for tight tolerances and high repeatability in the welding process, leading to accurate welds with minimal variability.
High Resolution And Positioning Accuracy
Laser welding machines often incorporate advanced motion control systems and high-resolution positioning devices. These systems enable precise movement and positioning of the laser beam relative to the workpiece, ensuring that the weld is deposited with utmost accuracy. Whether welding complex geometries or intricate components, laser welding technology can achieve precise weld placement with micron-level accuracy.
Real-Time Monitoring And Feedback
Many modern laser welding systems feature real-time monitoring and feedback mechanisms. Sensors, cameras, and automated inspection systems continuously monitor the welding process, providing instant feedback to the control system. This real-time feedback allows for on-the-fly adjustments to welding parameters, ensuring that the weld quality remains consistent and accurate throughout the process.
In conclusion, through controlled energy delivery, fine parameter control, high-resolution positioning, and real-time monitoring, laser welding systems can achieve precise welds with minimal distortion and variability. As industries continue to demand higher levels of precision and reliability, laser welding stands as a cornerstone of modern manufacturing, driving innovation and excellence in material joining processes.
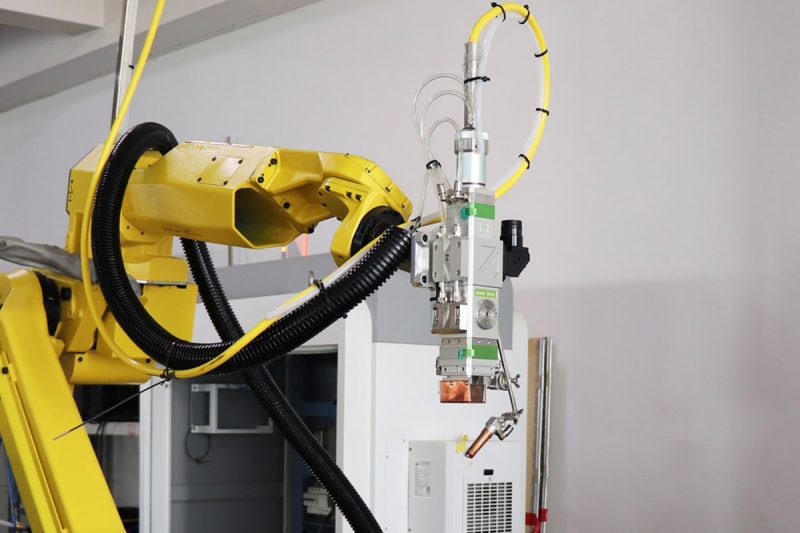
The Advantages Of Laser Welding In Precision Applications
Laser welding technology has become synonymous with precision and excellence in modern manufacturing, offering countless advantages for precision applications. Let’s explore the main advantages of laser welding in precision applications:
High Welding Quality
Laser welding technology provides excellent weld quality, characterized by strong, uniform welds with minimal defects. Precise control of energy delivery and welding parameters ensures consistent fusion and metallurgical integrity, resulting in high-quality joints with superior mechanical properties. This level of welding quality is critical for precision applications where reliability and performance are critical.
Versatile Welding Capabilities
Laser welding offers the versatility to join a variety of materials and component geometries. Whether welding dissimilar metals, thin sheets or complex components, laser welding technology excels in meeting different application requirements. This versatility makes laser welding ideal for precision applications in various industries including automotive, aerospace, electronics and medical device manufacturing.
Narrow Weld Width
One of the main advantages of laser welding is the ability to produce narrow welds with high aspect ratios. The focused laser beam enables precise control of the heat-affected zone, resulting in welds of minimum width and excellent penetration. This narrow weld width is particularly advantageous for precision applications where space constraints or aesthetic considerations require tight tolerances and fine detail.
Minimal Post-Weld Processing
Laser welding produces clean, spatter-free welds with minimal distortion, minimizing the need for extensive post-weld processing. Precise heat input and controlled energy delivery reduce the risk of material deformation or discoloration, eliminating the need for time-consuming grinding, polishing or surface finishing operations. This can result in significant time and cost savings during precision manufacturing processes.
Reduce Heat Affected Zone (HAZ)
Laser welding technology minimizes the size of the heat-affected zone (HAZ) around the weld area, thus preserving the mechanical properties of the base material. Concentrated heat input and rapid cooling rates ensure minimal thermal deformation and metallographic changes, thereby maintaining the integrity of the welded components. Reducing the heat-affected zone is critical for precision applications where dimensional accuracy and material performance are critical.
In summary, laser welding technology offers numerous advantages for precision applications. From high weld quality and versatile welding capabilities to narrow weld widths and minimal post-weld processing requirements, laser welding excels in every aspect of precision manufacturing.
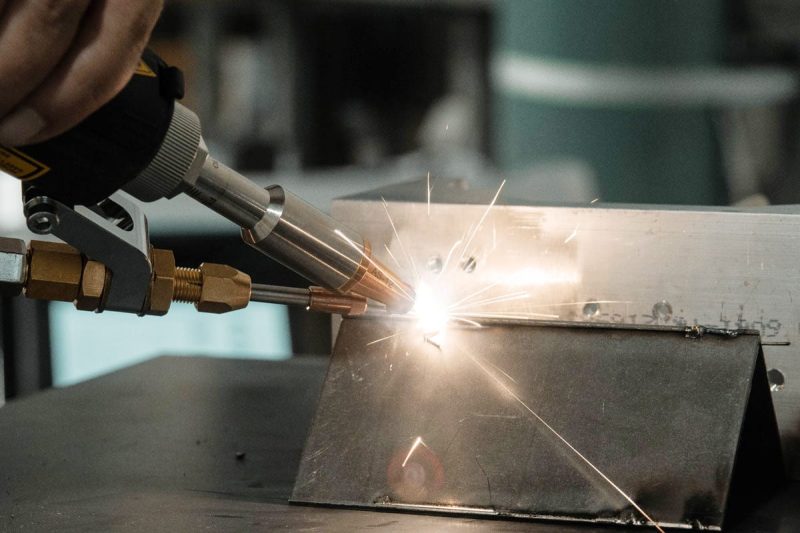
Factors Affecting Welding Quality And Accuracy
Laser welding technology provides a highly controlled and versatile method of joining materials, but several factors can affect the quality and accuracy of the welding process. Let’s explore the key factors that influence welding quality and accuracy in laser welding applications.
Laser Beam Quality And Focus
The quality and focus of the laser beam play an important role in determining the quality and accuracy of the weld. Factors such as beam shape, intensity distribution, and divergence angle affect the energy distribution and penetration depth of the laser beam. Maintaining a high-quality beam profile and precise focus ensures consistent heat transfer and welding geometry, minimizing defects and ensuring accurate welding.
Welding Parameters And Control
Welding parameters, including laser power, pulse duration, beam diameter and travel speed, directly affect the quality and accuracy of the welding process. Precise control of these parameters facilitates optimal penetration, fusion and weld morphology. The advanced control system monitors and adjusts welding parameters in real time, ensuring precise control of the entire process and consistent welding quality.
Protective Gas
Shielding gas is used to protect the weld pool and surrounding area from atmospheric contamination during laser welding. The choice of shielding gas composition and flow rate can affect weld quality by affecting weld bead shape, porosity, and spatter formation. Proper selection and control of shielding gas parameters enables high-quality, defect-free welds with optimal metallurgical properties.
Material Type And Thickness
The type and thickness of the material being welded significantly affects welding quality and accuracy. Different materials have different thermal properties, absorption coefficients, and melting temperatures, which affect the laser’s interaction with the material and the weld formation process. In addition, changes in material thickness can affect heat dissipation, penetration, and joint strength, requiring adjustments to welding parameters for optimal results.
Environmental Factors
Environmental factors such as ambient temperature, humidity and air cleanliness can affect welding quality and accuracy. Temperature fluctuations and humidity levels can affect laser performance, beam stability and material properties, resulting in changes in weld quality. Maintaining controlled environmental conditions within the welding area minimizes the risk of process instability and ensures consistent weld quality.
System Stability
The stability and reliability of laser welding systems facilitate consistent welding quality and accuracy. Mechanical vibration, optical misalignment and power fluctuations can all adversely affect beam transmission and welding performance. Regular maintenance, calibration and monitoring of welding systems helps ensure stability and reliability, minimizing variations in weld quality.
Therefore, by controlling and optimizing these factors, manufacturers can achieve high-quality, high-precision welding that meets the stringent requirements of modern manufacturing processes.
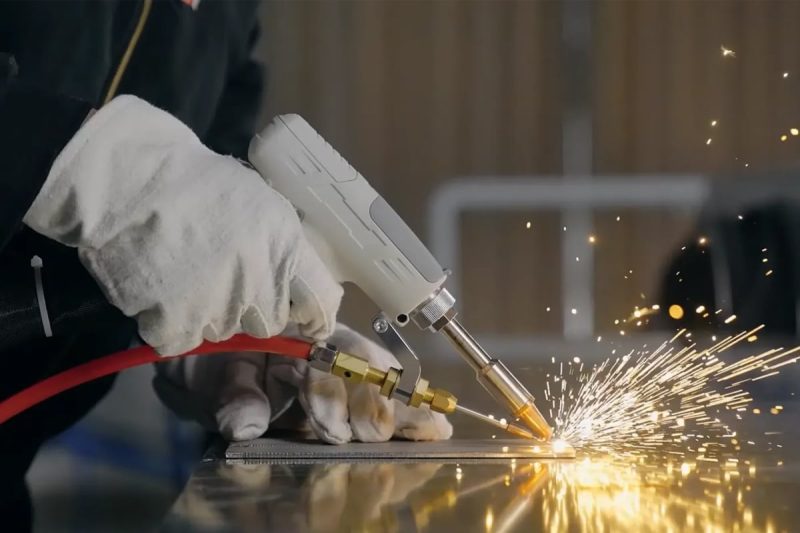
Maintenance And Calibration Of Laser Welding Machines
Consistent welding quality and reliability during the manufacturing process are mainly achieved by maintaining the optimal performance and accuracy of the laser welding machine. Regular maintenance and calibration are critical aspects of maintaining the efficiency and functionality of your laser welding system. Let’s explore the key maintenance and calibration practices that impact laser welding machines:
Regular Cleaning And Inspection
Regular cleaning and inspection of laser welding machines plays an important role in preventing contamination, maintaining functionality and extending the life of the equipment. Operators should regularly clean optics, lenses, and mirrors to remove dust, debris, and residue that may affect beam quality and performance. Additionally, a thorough inspection helps identify and resolve potential issues before they impact weld quality or system reliability.
Calibration And Alignment
Calibration and alignment procedures ensure that laser welding systems operate at optimal performance and accuracy. Laser beam alignment, focus adjustment and welding parameter calibration are important prerequisites for achieving consistent weld quality and geometry. Regular calibration checks and adjustments help maintain system integrity and accuracy, reducing the risk of errors or deviations in weld quality.
System Upgrades And Updates
System upgrades and software updates help laser welding machines maintain the latest technological advancements and improvements. Manufacturers frequently release firmware updates, software patches, and hardware upgrades to enhance system performance, reliability, and functionality. Implementing regular system upgrades and updates ensures that laser welding machines remain competitive, efficient, and able to meet changing industry needs.
Training And Education
Proper training and education of operators and maintenance personnel is critical to optimizing the performance and service life of your laser welding machine. Comprehensive training program covers equipment operation, maintenance procedures, safety protocols and troubleshooting techniques. Well-trained personnel are better able to perform routine maintenance tasks, identify potential problems and effectively respond to challenges, minimizing downtime and maximizing productivity.
Preventive Maintenance Plan
It’s critical to implement a preventive maintenance program that proactively addresses potential issues and minimizes unplanned downtime for your laser welding machine. Regular maintenance tasks such as lubrication, component replacement, and system inspections help prevent equipment failure, extend service life, and ensure consistent performance. Adhering to a regular maintenance schedule reduces the likelihood of costly repairs and production delays.
In summary, maintenance and calibration are important aspects of maintaining the efficiency, accuracy, and reliability of your laser welding machine. By implementing proactive maintenance procedures and investing in operator training, manufacturers can en sure that their laser welding machines are operating at peak performance, delivering high-quality welds consistently and efficiently throughout the manufacturing process.
Summarize
In the rapidly developing manufacturing industry, precision and accuracy are basic requirements to ensure product quality and efficiency. Laser welding machines have long been praised for their ability to provide precise welds in a variety of materials and applications. As the industry continues to push the boundaries of innovation and demand higher levels of precision, laser welding technology is evolving to meet these challenges. We expect efficiency, flexibility and the integration of emerging technologies to increase, with laser welding further cementing itself as a cornerstone of precision manufacturing.
By gaining an in-depth understanding of these factors, you can better understand the laser welding machine market and make informed purchasing decisions. Whether you are a manufacturer or end user, consider us at AccTek Laser when purchasing a laser welding machine to fit your specific needs and budget.
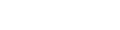
Contact information
- [email protected]
- [email protected]
- +86-19963414011
- No. 3 Zone A, Lunzhen Industrial Zone,Yucheng City , Shandong Province.
Get Laser Solutions