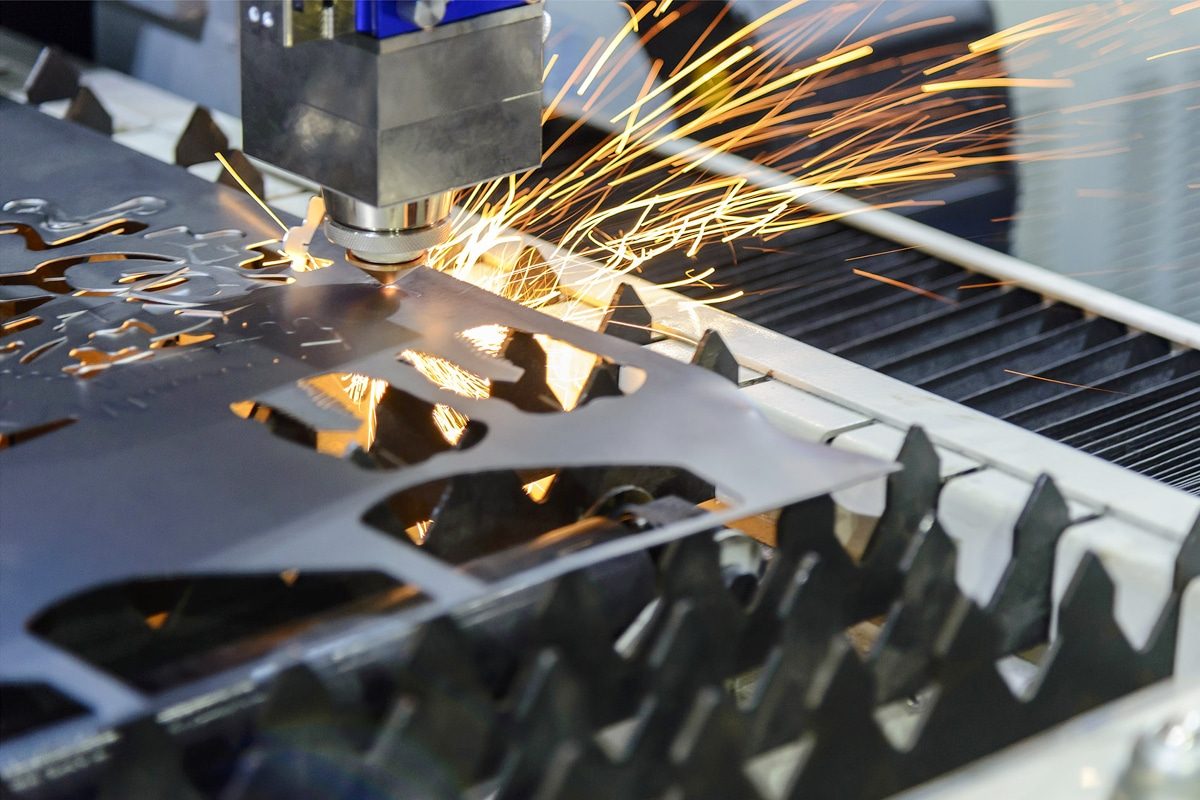
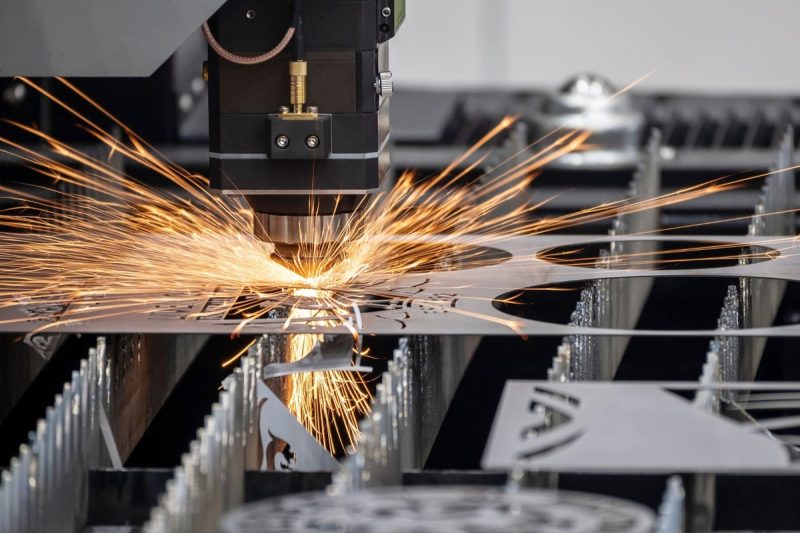
Learn About Laser Cutting
Laser Cutting Description
Types of Lasers Used in Cutting Applications
Fiber Laser
CO2 Laser
Components of A Laser Cutting System
The typical laser cutting system consists of several key components that work together to provide precise and efficient cutting performance:
- Laser Source: This is the core component that produces the laser beam. Depending on the application, the laser source can be a fiber laser generator, a CO2 laser generator, or another type of laser generator.
- Optics: Mirrors and lenses are used to direct and focus the laser beam onto the material being cut. The quality of the optics affects the accuracy and efficiency of the cutting process.
- Cutting Head: The cutting head contains the focusing lens and nozzle through which the laser beam and assist gas are directed. It is responsible for maintaining the correct focal length and ensuring optimal cutting conditions.
- Worktable: Supports the material being cut and usually includes a mechanism to move the material under the cutting head.
- CNC Controller: The CNC controller manages the movement of the laser cutting head and workpiece, following the programmed cutting path to produce the desired shape and pattern.
- Assist Gas Supply: Assist gas assists the cutting process by blowing away molten material, cooling the cutting zone, and preventing oxidation. Common assist gases include oxygen, nitrogen, and compressed air.
- Exhaust System: Removes fumes and debris generated during the cutting process to maintain a clean working environment and protect the optics and laser components.
- Cooling System: Laser cutting generates a lot of heat that needs to be dissipated to prevent damage to the laser source and other components. Cooling systems, such as water chillers, are used to maintain optimal operating temperatures.
Key Parameters Affecting Laser Cutting Performance
Several parameters can affect the performance and quality of the laser-cutting process. Understanding and optimizing these parameters can help achieve the desired results:
- Laser Power: The power output of the laser source determines the thickness and type of material that can be cut. Higher powers allow for the cutting of thicker materials, but other parameters may need to be adjusted to maintain cut quality.
- Cutting Speed: The speed at which the cutting head moves across the workpiece. Optimal cutting speed ensures a balance between productivity and cut quality. Too fast a speed can result in incomplete cuts, while too slow a speed can cause excessive heat buildup and material damage.
- Focal Position: The position of the laser beam focal point relative to the material surface. Correct focus ensures maximum energy density at the cutting point, resulting in clean and precise cuts. Misalignment can result in poor cut quality and reduced efficiency.
- Assist Gas Type and Pressure: The type and pressure of the assist gas used (oxygen, nitrogen, or compressed air) has a significant impact on the cutting process. Correct gas selection and pressure optimizes the removal of molten material, prevent oxidation, and improves cut quality.
- Material Type and Thickness: Different materials and thicknesses react differently to laser cutting. When setting cutting parameters, material properties such as reflectivity, thermal conductivity, and melting point must be considered.
- Beam Quality: The quality of the laser beam, characterized by its focus and mode structure, affects the precision and quality of the cut. A high-quality beam with a small focal spot size produces finer cuts with minimal cut width.
- Nozzle Design: The design of the nozzle, including its diameter and shape, affects the flow of assist gas and the removal of molten material. An optimized nozzle design improves cutting efficiency and quality.
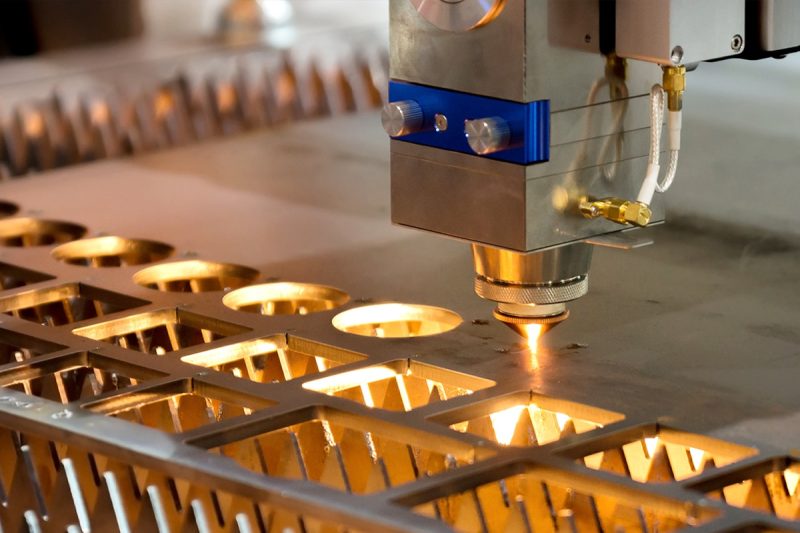
The Role of Assist Gases in Laser Cutting
Removing Molten Material
During the laser cutting process, a high-intensity laser beam melts the material at the point of the cut. Assist gas is directed through a nozzle to the cutting area, where it helps remove molten material from the kerf (the gap created by the laser). Effectively removing molten material maintains cut quality and prevents defects.
- Efficient Jetting: The high pressure of the assist gas blows molten material away from the kerf, preventing it from re-solidifying onto the workpiece and ensuring a clean cut.
- Preventing Slag Formation: By rapidly evacuating molten material, the assist gas minimizes the formation of slag (residual material adhering to the bottom surface of the cut), reducing the need for post-processing.
- Maintaining Kerf Width: Continuous removal of molten material helps maintain the desired kerf width, ensuring dimensional accuracy and precision of the final cut.
Cooling The Cutting Zone
The intense heat generated by the laser beam can cause significant thermal effects on the workpiece, including warping, deformation, and changes in material properties. Assist gas helps control these thermal effects by cooling the cutting zone.
- Dissipating Heat: The flow of assist gas absorbs and dissipates excess heat in the cutting area, preventing overheating and minimizing thermal deformation of the material.
- Reducing the Heat Affected Zone (HAZ): Cooling the cutting zone helps limit the size of the HAZ, maintaining the material’s mechanical properties and reducing the risk of warping or other thermal damage.
- Increasing Cutting Speeds: Efficient cooling increases cutting speeds because the material is less likely to develop thermally induced defects, resulting in faster, more efficient production.
Protecting the Lens
The lens in the cutting head focuses the laser beam onto the workpiece. Contaminants such as smoke, dust, and debris generated during the cutting process can damage the lens or degrade its performance. Assist gas protects the lens from contaminants.
- Lens Shielding: Assist gas forms a barrier between the lens and the cutting area, preventing contaminants from reaching and depositing on the lens surface.
- Maintaining Optical Quality: By keeping the lens clean and free of debris, the assist gas ensures optimal beam focus and consistent cutting performance.
- Extending Lens Life: Preventing contamination reduces wear on the lens, extending its life and reducing maintenance costs.
Enhance Cutting Reaction
Assist gases can affect the chemical reactions that occur during laser cutting, thereby enhancing the cutting performance of different materials. The type of gas used can promote or inhibit certain reactions, which can affect cutting quality and efficiency.
- Oxygen (O₂): Oxygen is commonly used to cut carbon steel. It promotes an exothermic reaction with the molten metal, generating additional heat, which increases cutting speed. This reaction helps produce a clean cut with less dross but can cause oxidation on the cut edge.
- Nitrogen (N₂): Nitrogen is an inert gas that is commonly used to cut stainless steel, aluminum, and other nonferrous metals. It prevents oxidation by forming an inert atmosphere around the cutting zone. This produces a clean, oxide-free edge, making it ideal for applications that require a high-quality surface finish.
- Compressed Air: Compressed air is a cost-effective alternative that can be used to cut a variety of materials. It combines the properties of oxygen and nitrogen to provide adequate cutting performance at a lower cost. However, it can introduce impurities that affect cut quality.
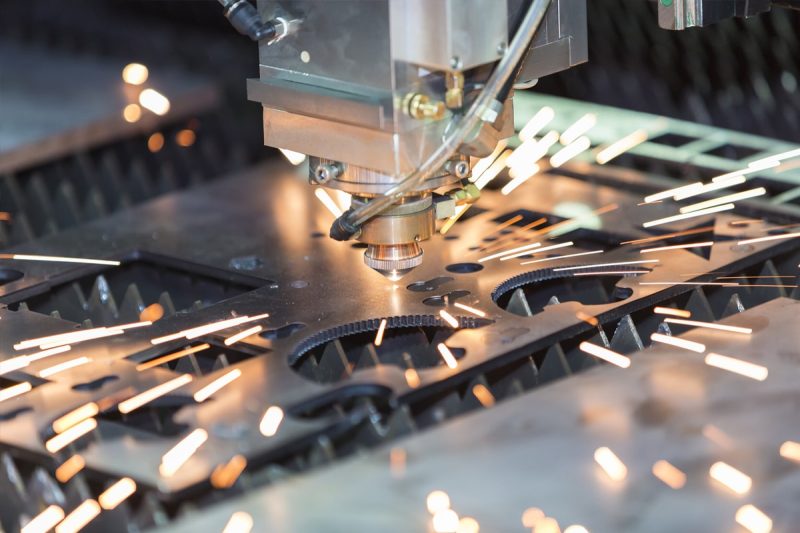
Types of Assist Gases
Oxygen (O₂)
Advantages
- Increased Cutting Speed: The oxygen reacts with the material in an exothermic reaction, releasing additional heat. This additional heat increases cutting speed, making oxygen-assisted cutting significantly faster, especially with thicker materials.
- Improved Efficiency: The exothermic reaction reduces the laser power required to cut the material, improving the overall energy efficiency of the cutting process.
- Cleaner Cuts on Thick Materials: Oxygen helps produce cleaner cuts on thicker materials, reducing dross and slag, which reduces the need for extensive post-processing.
Disadvantages
- Oxidation: The reaction between oxygen and the material can cause oxidation of the cut edge, resulting in a rougher surface finish and possible corrosion issues.
- Heat-Affected Zone (HAZ): The additional heat generated by the exothermic reaction increases the size of the HAZ, which can change the mechanical properties of the material near the cut edge and cause issues such as warping or reduced structural integrity.
- Limitations for Non-Ferrous Metals: Oxygen is not as effective as non-ferrous metals such as aluminum and copper, which do not react as readily with oxygen.
Nitrogen (N₂)
Advantages
- Oxidation-Free Cutting: Nitrogen is an inert gas that does not react with the material during the cutting process. This property prevents oxidation, resulting in a clean, bright, oxide-free edge that is ideal for applications that require a high-quality surface finish.
- High-Quality Surface Finish: The absence of oxidation results in a smoother edge and a smoother surface finish, which reduces or eliminates the need for post-processing.
- Minimized Heat-Affected Zone (HAZ): Nitrogen helps maintain a small heat-affected zone, preserving the mechanical properties of the material and minimizing thermal deformation. This can be used to achieve precision cuts and applications that require tight tolerances.
Disadvantages
- Slower Cutting Speeds: Without the exothermic reaction provided by oxygen, nitrogen-assisted cutting typically results in slower cutting speeds, especially with thicker materials. This slower speed affects overall productivity.
- Higher Laser Power Requirements: Since nitrogen does not provide additional heat to the cutting process, the laser must provide all the energy required to cut the material. This requirement can result in higher energy consumption and operating costs.
- Cost Considerations: Nitrogen can be more expensive than other gases, and the increased consumption caused by higher laser power requirements can further increase operating costs.
Compressed Air
Advantages
- Cost-Effective: Compressed air is more readily available and less expensive than pure gases such as nitrogen and oxygen. This makes it an economical choice for many laser-cutting applications, especially those involving thinner materials.
- Versatility: Compressed air can be used to cut a wide range of materials, including mild steel, stainless steel, and aluminum. Its versatility makes it a practical choice for general-purpose cutting.
- Reduced Operating Costs: Because compressed air is inexpensive and widely available, using compressed air can reduce overall operating costs, making it suitable for small-scale operations or budget-conscious projects.
- Environmental Benefits: Using compressed air reduces reliance on bottled gas, which in turn reduces the carbon footprint associated with gas production and transportation, providing an environmental benefit.
Disadvantages
- Lower Cut Quality: Oxygen and impurities in compressed air can affect cut quality, resulting in rougher edges, increased dross, and potential contamination of the cut surface. This problem is particularly noticeable in applications that require high surface quality or precision.
- Limited Cutting Speeds: Compressed air generally cuts at slower speeds than oxygen-assisted cutting, especially for thicker materials. This limitation affects productivity and may not be suitable for high-volume production.
- Inconsistent Results: The quality and performance of cutting with compressed air can be inconsistent due to differences in the composition and pressure of the air supply. This inconsistency makes it challenging to achieve uniform results from one cutting job to another.
- Oxidation and Dross Formation: Compressed air contains a variety of gases, including oxygen, which can cause oxidation and dross formation on the cut edge, requiring additional post-processing to achieve the desired results.
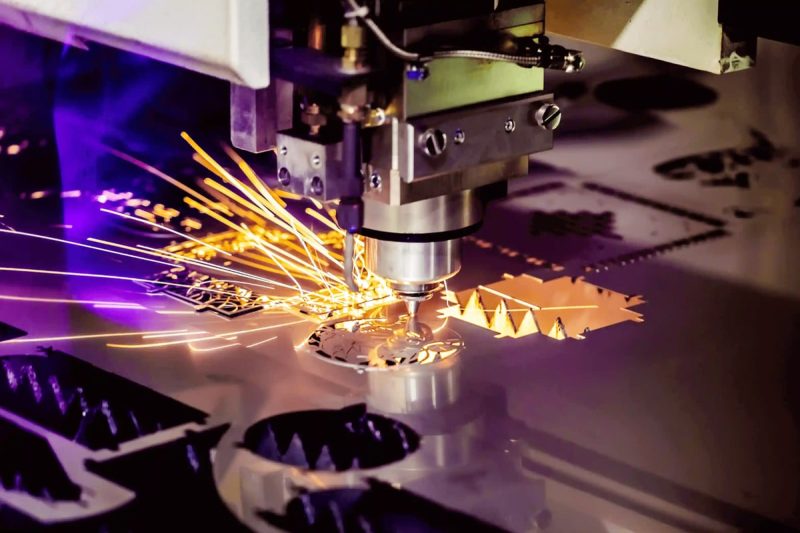
Impact on Different Materials
Carbon Steel
Oxygen
- Advantages: Oxygen is often used to cut carbon steel because it reacts exothermically with the material. This reaction generates additional heat, which significantly increases cutting speed and efficiency. The resulting cuts are typically clean with minimal dross, and the enhanced heat helps cut thicker carbon steel sections.
- Disadvantages: The exothermic reaction with oxygen causes oxidation, which, if not treated, can result in a rougher surface finish and possible corrosion. The heat-affected zone (HAZ) is also larger, which can affect the mechanical properties of the material near the cut edge.
Nitrogen
- Advantages: Nitrogen does not react with carbon steel, preventing oxidation and producing a clean, oxide-free cut. This results in a high-quality surface finish and a smaller HAZ, which preserves the mechanical properties of the material.
- Disadvantages: The lack of an exothermic reaction means that nitrogen-assisted cutting is slower than oxygen-assisted cutting. To achieve the same cutting speed, higher laser power is required, which increases operating costs.
Compressed Air
- Advantages: Compressed air is a cost-effective alternative for cutting carbon steel. It strikes a balance between cost and performance and is suitable for cutting thinner carbon steel sections.
- Disadvantages: The oxygen in compressed air can cause some oxidation and dross formation, affecting cut quality. Cut speeds and quality are generally lower than when using pure oxygen or nitrogen.
Stainless Steel
Oxygen
- Advantages: Oxygen can be used to cut stainless steel, providing fast cutting speeds due to the exothermic reaction. This reaction can also help achieve clean cuts with minimal dross.
- Disadvantages: Using oxygen can cause oxidation, which can lead to edge discoloration and potential corrosion issues. The oxide layer may require additional post-processing to achieve the desired surface quality.
Nitrogen
- Advantages: Nitrogen is the gas of choice for cutting stainless steel because it prevents oxidation, resulting in a clean, bright, oxide-free edge. The inert nature of nitrogen produces high-quality cuts with minimal need for post-processing. Nitrogen also helps maintain the mechanical properties of the material by minimizing the heat-affected zone.
- Disadvantages: Nitrogen has slower cutting speeds and requires higher laser power than oxygen, resulting in increased energy consumption and operating costs.
Compressed Air
- Advantages: Compressed air can be used to cut thinner sections of stainless steel. It is more cost-effective than pure gas and is a viable option for applications that do not require high precision.
- Disadvantages: Oxygen in compressed air can cause oxidation and dross formation, affecting cut quality. The edge may require additional cleaning and finishing after the cut.
Aluminum and Nonferrous Metals
Oxygen
- Advantages: Oxygen is not generally recommended for cutting aluminum and other nonferrous metals due to their high reflectivity and low absorption of the laser beam. However, in some cases, oxygen can help cut thicker sections by promoting an exothermic reaction.
- Disadvantages: Oxygen can cause severe oxidation, resulting in a rough and porous cut surface. This oxidation can negatively affect the properties and appearance of the material, requiring extensive post-processing.
Nitrogen
- Advantages: Nitrogen is very effective for cutting aluminum and other nonferrous metals. It prevents oxidation, resulting in a clean, bright, and high-quality edge. Nitrogen also helps minimize the heat-affected zone, preserving the mechanical properties of the material.
- Disadvantages: Nitrogen-assisted cutting is slower than using oxygen, and requires higher laser power to cut the material, which increases operating costs.
Compressed Air
- Advantages: Compressed air is a cost-effective option for cutting thinner sections of aluminum and nonferrous metals. It can provide satisfactory cutting performance for applications where precision is not critical.
- Disadvantages: Oxygen in compressed air can cause oxidation and dross formation, affecting cut quality. Edges may require additional post-processing to achieve the desired finish.
Non-Metallic Materials
Oxygen
- Advantages: Oxygen can be used to cut non-metallic materials such as wood, acrylic, and plastic. The exothermic reaction with oxygen can increase cutting speed and efficiency for some materials.
- Disadvantages: Using oxygen can cause materials such as wood and acrylic to scorch and burn, negatively affecting surface quality. This can result in the need for additional finishing processes to achieve the desired appearance.
Nitrogen
- Advantages: Nitrogen is well suited for cutting non-metallic materials such as plastics and ceramics, which must be protected from oxidation. It prevents discoloration and produces clean, high-quality edges while minimizing thermal damage.
- Disadvantages: Nitrogen-assisted cutting can be slower than oxygen, requiring higher laser power to achieve the desired cutting speed.
Compressed Air
- Advantages: Compressed air is a cost-effective solution for cutting non-metallic materials and provides adequate cutting performance for a variety of applications. It is suitable for applications where precision and quality are not critical.
- Disadvantages: Impurities in compressed air can affect cut quality, resulting in rough edges and potential contamination. Cut quality and speed may not be comparable to those of pure gases such as oxygen or nitrogen.
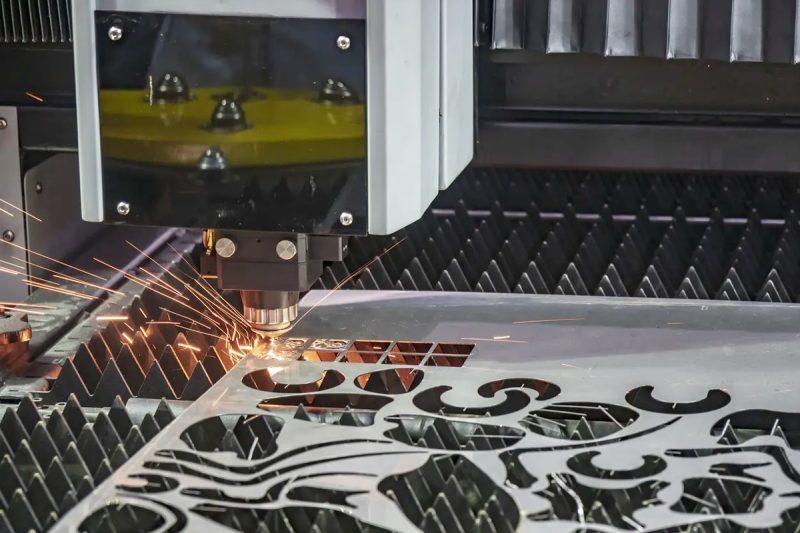
Optimizing Assist Gas Selection
Material Type and Thickness
The type and thickness of the material being cut are major considerations when selecting an assist gas. Different materials react differently to various gases, affecting cut quality and efficiency.
- Carbon Steel: Oxygen is often the first choice for cutting carbon steel because it reacts exothermically, increasing cutting speed and efficiency. For thicker carbon steels, oxygen can provide the heat needed to effectively cut the material. For thinner carbon steels, nitrogen can be used to achieve a clean, oxidation-free cut, albeit at a slower rate.
- Stainless Steel: Nitrogen is ideal for cutting stainless steel because it prevents oxidation and produces a high-quality, smooth edge. For very thick stainless steel, oxygen can be used to increase cutting speeds but will cause oxidation, requiring post-processing.
- Aluminum and Nonferrous Metals: Nitrogen is the first choice for cutting aluminum and nonferrous metals to avoid oxidation and achieve a clean cut. For less critical applications, compressed air can be a cost-effective alternative, although it may cause some oxidation.
- Nonmetallic Materials: For cutting nonmetals such as plastics, ceramics, and wood, nitrogen is often used to prevent discoloration and achieve a high-quality edge. Oxygen can be used to cut certain nonmetals faster but can cause scorching or burning.
Required Cut Quality
The required cut quality is a key factor in selecting the appropriate assist gas. Precision applications typically require a high-quality cut with minimal oxidation and smooth edges.
- High-Quality Surface Finish: Nitrogen is often the best choice for applications that require precise, clean, and oxidation-free cuts. It prevents oxidation, resulting in smooth edges and a high-quality surface finish.
- General Quality: Oxygen can provide a high-quality cut with minimal dross, but the edges may require additional cleaning due to oxidation. Compressed air may be suitable for less critical applications where the highest quality surface finish is not necessary.
Cutting Speed and Efficiency
Cutting speed and efficiency are affected by the type of assist gas used. The goal is to achieve the highest possible speed without compromising cut quality.
- Maximum Speed: Provides the fastest cutting speeds for carbon steel and thicker materials due to the exothermic reaction of oxygen, which adds additional heat to the cutting process.
- Balanced Speed and Quality: Nitrogen strikes a balance between speed and high-quality cuts, although it may require higher laser power and cuts at a slower speed compared to oxygen.
- Cost-Effective Speed: Compressed air offers a compromise between speed and cost, suitable for applications where moderate cutting speeds and reasonable quality are acceptable.
Cost Considerations
Cost is an important factor in assisting gas selection, affecting operating expenses and overall cost-effectiveness.
- Reduced Operating Costs: Compressed air is the most economical choice because it is readily available and cheaper than pure gases such as oxygen and nitrogen. It is ideal for cutting less critical materials or when budget constraints are a priority.
- Higher Quality and Higher Cost: Nitrogen, while more expensive, provides better cut quality. The additional cost is justified by the improved quality and reduced need for post-processing.
- Balancing Cost and Efficiency: Oxygen offers a middle ground, providing fast cutting speeds and reasonable quality at a moderate cost. It is suitable for many industrial applications where both speed and quality are important.
Post-Processing Requirements
Post-processing needs can influence assist gas selection, as some gases produce cleaner cuts, which can reduce finishing work.
- Minimal Post-Processing: Nitrogen produces clean, oxidation-free cuts, reducing the need for extensive post-processing, and saving time and cost on finishing operations.
- Moderate Post-Processing: Oxygen cutting may require additional steps to remove oxides and achieve the desired surface finish. However, faster cutting speeds can offset some of the additional costs.
- Increased Post-Processing: Compressed air may cause more dross and oxidation, requiring more extensive post-processing to clean and finish the edge. This can increase overall production time and cost.
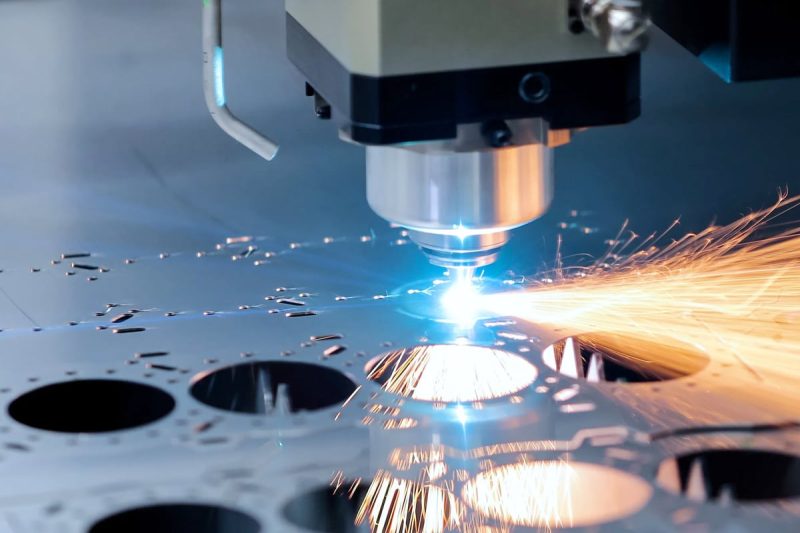
Summary
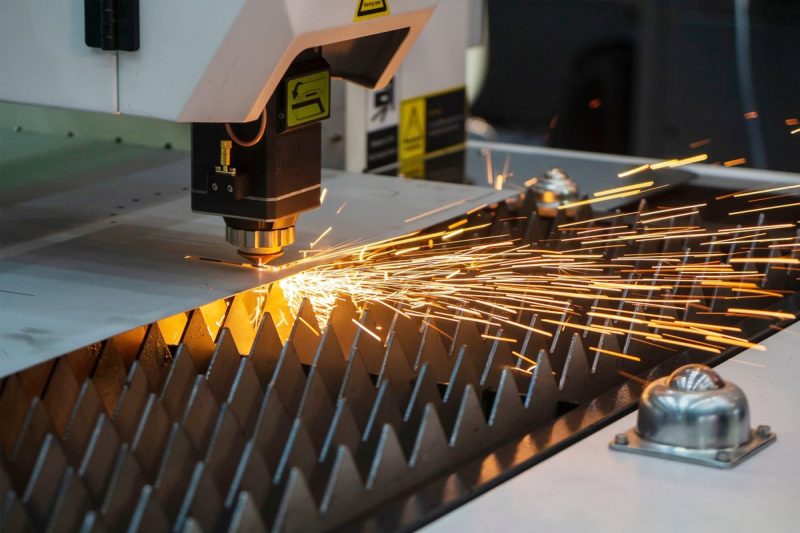
Get Laser Cutting Solutions
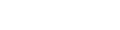
- [email protected]
- [email protected]
- +86-19963414011
- No. 3 Zone A, Lunzhen Industrial Zone,Yucheng City , Shandong Province.