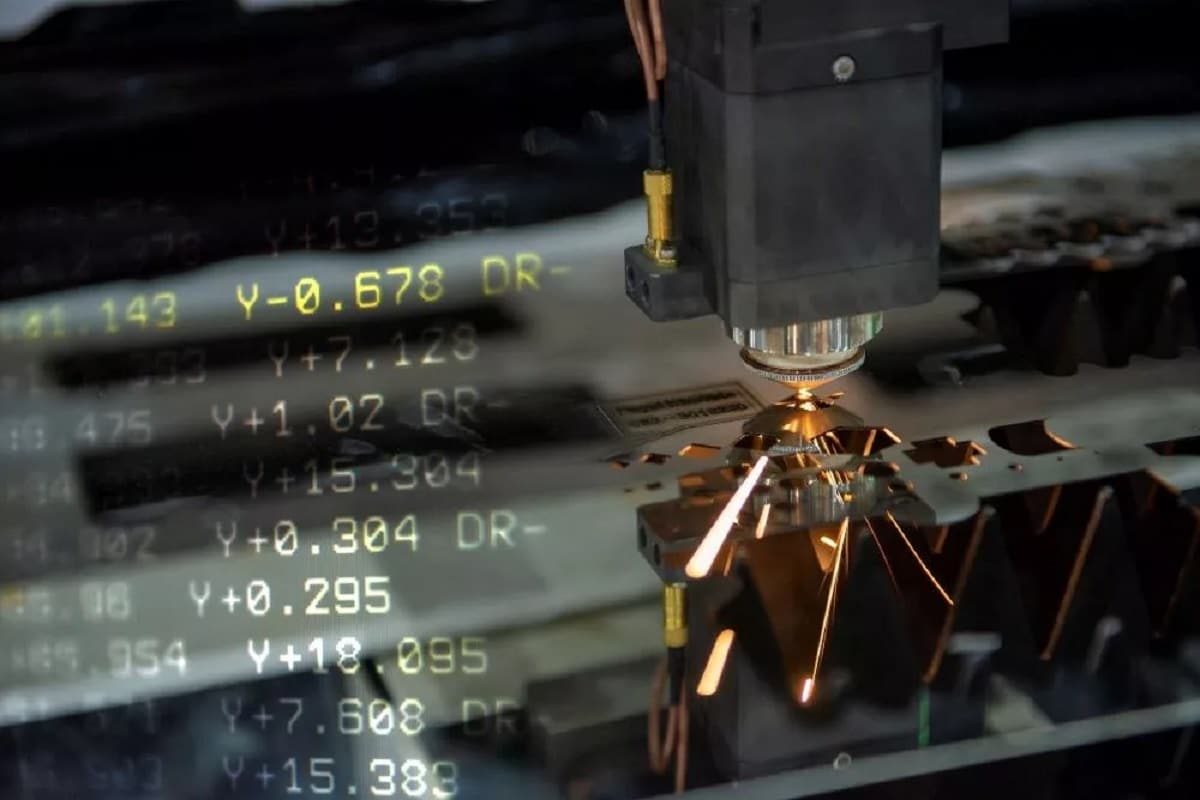
Effect of Laser Cutting Power
Laser-cutting technology has become the cornerstone of modern manufacturing and fabrication processes, delivering unparalleled precision and versatility. A fundamental parameter underpinning the effectiveness of this technology is laser cutting power. In this comprehensive article, we’ll delve into the complexities of laser cutting power, exploring its profound impact on material interactions, cut thickness, cut quality, cutting speed, material compatibility, and heat-affected zones. Additionally, we will discuss methods for determining optimal laser cutting power for various applications.
Table of Contents
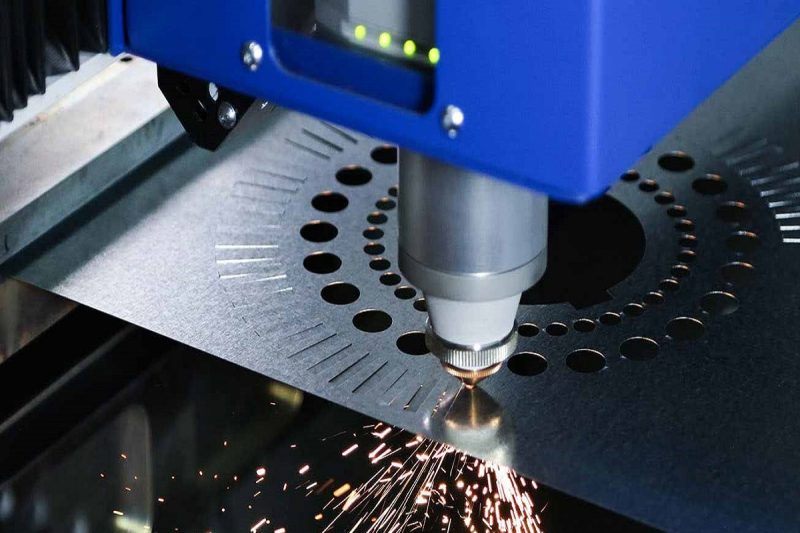
Definition of laser cutting power
Laser-cutting power refers to the amount of energy emitted by the laser generator during the laser-cutting process. It is usually measured in watts (W) or kilowatts (kW). Laser cutting power is a key parameter in laser cutting technology, which directly affects cutting performance, speed, and processing quality.
In laser cutting, a high-intensity laser beam is focused onto the surface of the material, causing localized heating and vaporization. Laser power determines the intensity of this energy. Selecting the appropriate laser power level depends on factors such as material type, thickness, desired cut quality, and application requirements. By adjusting laser power settings, operators can tailor the cutting process to achieve optimal results in a variety of industrial and manufacturing applications.
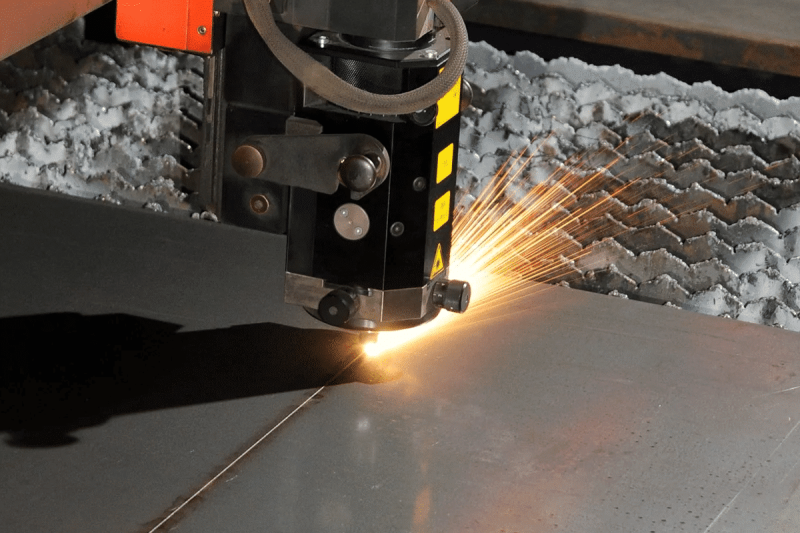
Effect of laser cutting power
Laser cutting power is a key parameter in laser cutting technology, which can have a significant impact on all aspects of the cutting process and its cutting results. If you want to understand the impact of laser cutting power, let’s take a closer look at how it affects the cutting process.
Matter interaction
- Higher power: When a laser cutter operates at higher power levels, the laser beam delivers more energy to the material. This increased energy causes the material to heat up quickly and cause the material to melt or evaporate faster. Therefore, higher power levels enable faster, more efficient material removal.
- Lower power: Lower laser power levels provide less energy to the material and may require slower cutting speeds to achieve the desired cut. The material removal process is more gradual and may take longer to cut the same thickness of material.
Cutting thickness
- Higher power: Thicker materials often require higher laser power to ensure full penetration and efficient cutting. Higher power provides the energy needed to effectively cut thick materials.
- Lower power: Lower power levels when cutting thick materials may result in incomplete cuts or require multiple passes to achieve the desired cut result. This increases laser processing time and may cause problems such as melting or deformation.
Cutting quality and precision
- Higher Power: Higher laser power settings produce smoother, cleaner edges on cut materials. Increased power typically produces a finer finish with minimal roughness, which is ideal for applications where cut quality is critical.
- Lower Power: Lower laser power settings reduce the risk of overcutting or material damage, making them suitable for complex designs or delicate materials. However, if the power is too low, the cutting may be incomplete and multiple cuts may be required to complete the cutting, which will have a certain impact on the cutting quality and accuracy.
Cutting speed
- Higher power: Laser cutting at higher power levels allows for faster cutting speeds. The increased energy provided by higher power settings causes materials to vaporize faster, which is beneficial in high-production environments where speed is critical.
- Lower power: Lower power settings may require slower cutting speeds to ensure precise cuts. A slower, more controlled cutting method is beneficial when working with complex or delicate materials.
Material compatibility
- Metal: Metal is often highly reflective, making it difficult to cut with a laser. Therefore, they typically require higher laser power for effective cutting. High-power laser generators, such as fiber laser generators, are often used to cut metallic materials.
- Non-metallic: Non-metallic materials such as plastic, wood, and fabric are generally more absorptive, meaning they absorb laser energy more easily. This allows them to be cut efficiently using lower laser power settings.
Heat-affected zone (HAZ)
- Higher power: Due to the increased heat generated during cutting, higher laser power results in a larger heat-affected zone (HAZ) near the cut edge, which may affect material properties near the cut edge.
- Lower power: Lower power settings minimize the size of the heat-affected zone, which is beneficial in applications where material integrity must be maintained, such as medical device manufacturing or electronics manufacturing.
Laser cutting power is a key parameter that significantly affects the laser cutting process and cutting quality. Selecting the appropriate laser power level depends on a variety of factors, including the material being cut, its thickness, desired cut quality, and application requirements. Balancing power and cutting speed helps achieve the best cutting results from laser cutting in a variety of industrial and manufacturing applications.
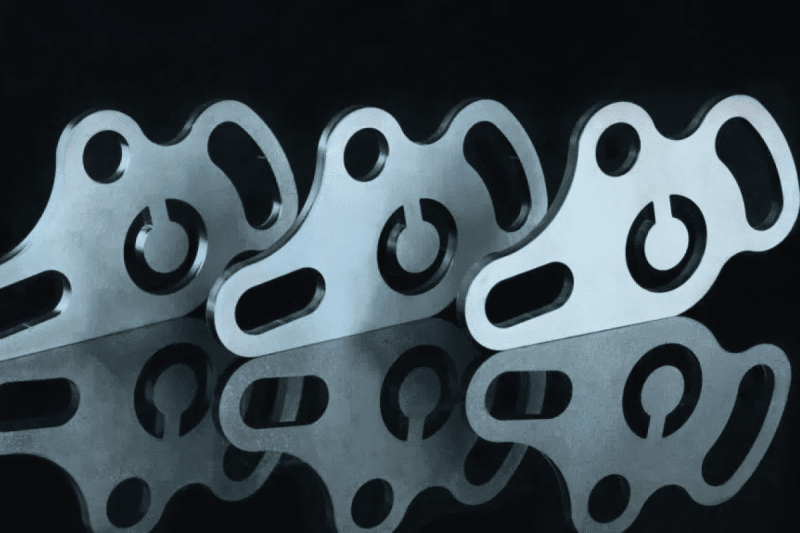
Determining optimal laser cutting power
Determining the optimal laser-cutting power is a critical step in achieving high-quality, efficient laser-cutting results. The optimal power level depends on a variety of factors, including the type of material being cut, material thickness, cut quality required, and specific application requirements. Here is a detailed guide on how to determine the best laser-cutting power:
Material testing
- Material selection: Start by selecting a representative sample of the material you want to cut. The sample should closely match the properties and thickness of the actual workpiece.
- Power range: Establish a range of laser power settings to be tested. This range should include both lower and higher power levels to allow for comprehensive testing.
- Cutting parameters: Determine a set of initial cutting parameters, including laser power, cutting speed, auxiliary gas type, and flow rate. These parameters will serve as a starting point for your testing.
Cut test sample
- Design test patterns: Create test patterns or samples that represent the types of cuts you will perform in your application, including features such as straight cuts, curves, sharp corners, and complex designs.
- Power level array: Create an array of test samples using a range of laser power settings of your choice. Each sample should be cut at a different power level while keeping other parameters constant.
- Systematic approach: Organize test samples in a systematic way so you can easily identify the effect of power on cut quality and characteristics.
Conduct material testing
- Perform cuts: Run a material cutting test using arranged samples and observe how each sample responds to different power levels.
- Evaluate cut quality: Carefully check the cut quality of the test cut piece. Evaluate factors such as edge smoothness, accuracy, and any signs of undesirable effects such as melting or scorching.
- Penetration depth: For thicker materials, check the penetration depth to ensure the laser power is sufficient to complete the cut.
Analyze results
- Comparative analysis: Compares results from different test samples to determine the power level that produces the best overall results by looking for trends and patterns.
- Consider application requirements: Keep in mind the specific requirements of your application. If accuracy is critical, prioritize samples with the required level of detail and accuracy.
- Heat-affected zone (HAZ): Evaluate the size of the heat-affected zone (HAZ) in a material. For some applications, a smaller heat-affected zone may be more appropriate.
Adjust laser power settings
- Fine-tune: Based on your analysis, fine-tune the laser power settings to achieve the desired results. This may involve selecting a specific power level or adjusting power within a range.
- Iterative process: Don’t hesitate to repeat the testing process if necessary. Iterative testing can further optimize and help you determine the optimal laser power.
Document
- Record results: Keep a record of test results, including selected laser power settings and their corresponding cut quality. This document will provide a valuable reference for future projects.
Verify
- Production Trial Run: Prior to large-scale production, perform a trial run using optimal laser power settings to ensure its performance is consistent and meets your application requirements.
Other things to note
- Other factors: Other factors such as type and condition of focusing optics, assist gas selection, and nozzle alignment can also affect cutting results. Regular maintenance and calibration of your laser cutting machine help ensure consistent cutting performance.
Determining optimal laser cutting power is a systematic process that requires careful experimentation and analysis. By conducting material testing and considering the specific needs of your project, you can fine-tune your laser power settings to achieve the best results in terms of cut quality, accuracy, and efficiency.
Summarize
Laser-cutting power is the lifeblood of laser-cutting technology and has a profound impact on material interaction, cut thickness, quality, accuracy, speed, material compatibility, and heat-affected zone. Understanding the complex interplay between laser power and the cutting process can help achieve desired cutting results in a variety of applications. By harnessing the potential of laser-cutting power and fine-tuning power settings, industries can unleash unprecedented precision, efficiency, and innovation, driving manufacturing and technology into the future.
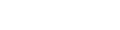
Contact information
- [email protected]
- [email protected]
- +86-19963414011
- No. 3 Zone A, Lunzhen Industrial Zone,Yucheng City , Shandong Province.
Get Laser Solutions