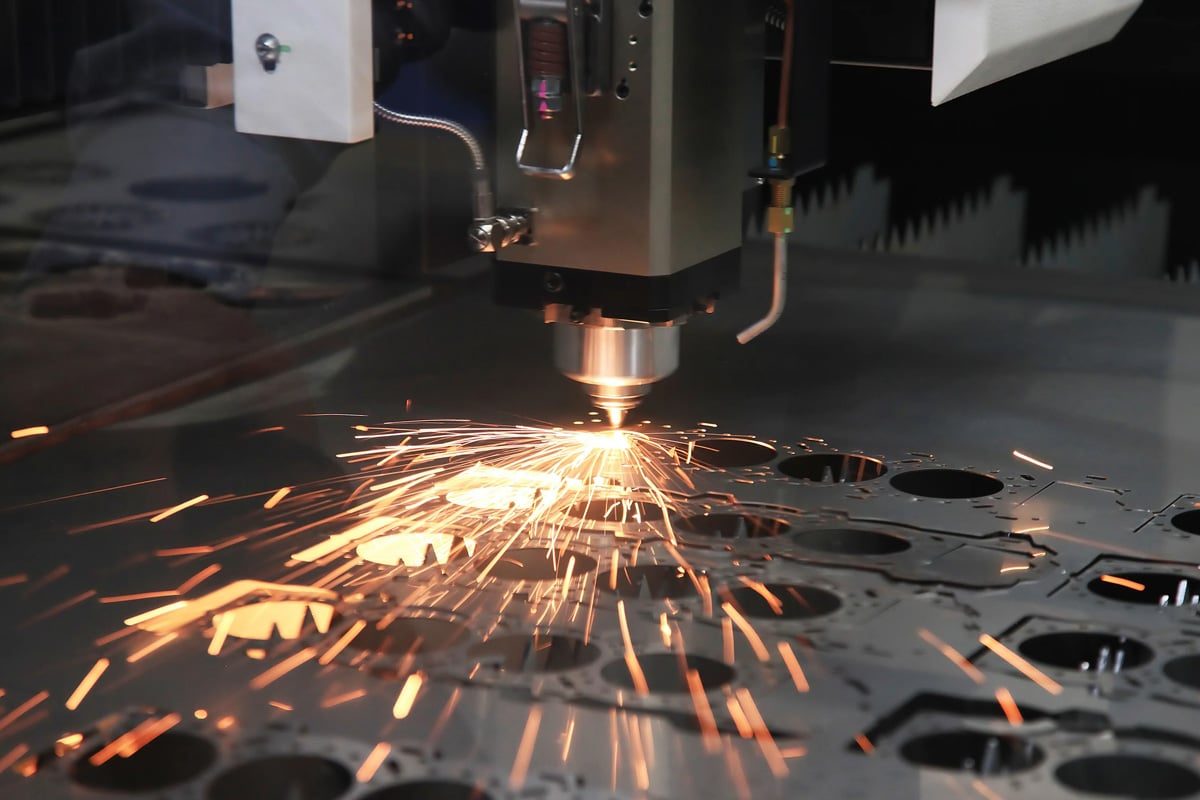
Effect of Laser Wavelength on Cutting Ability
Laser cutting technology is widely used in modern manufacturing due to its high efficiency and precision, especially in aerospace, automobile manufacturing, metal processing and electronics industries. However, the laser cutting effect is affected by many factors, among which the laser wavelength is one of the key parameters. Lasers of different wavelengths have different absorption characteristics of materials, which directly affects the cutting speed, quality and efficiency. Understanding the impact of laser wavelength on cutting ability can help engineers choose the best cutting solution, thereby improving production efficiency and reducing costs. In addition, the emergence of new laser generators such as fiber laser generators and CO2 laser generators has further enriched the application scenarios of laser cutting technology. Therefore, an in-depth study of the selection of laser wavelength and its impact will provide important support for enterprises to optimize production processes and promote the future development of laser cutting technology.
Table of Contents
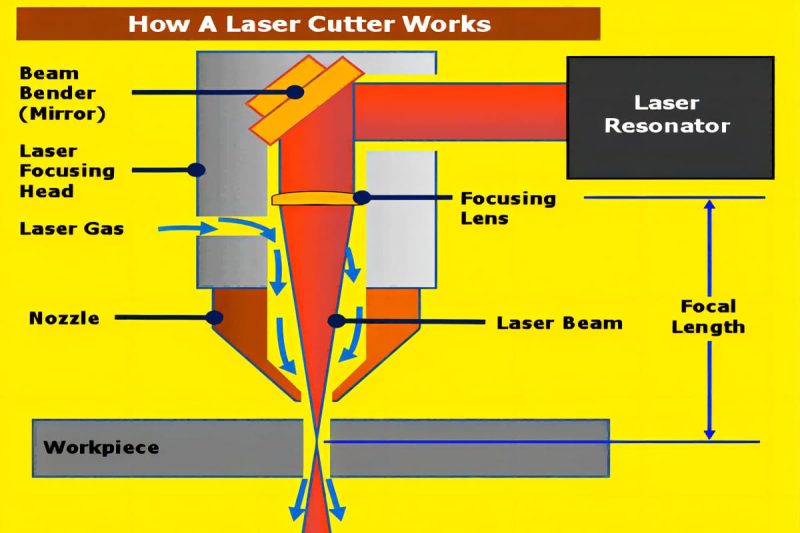
Laser Cutting Basics
Laser Cutting Technology Principle
Laser cutting is a technology that uses a high-energy-density laser beam to focus on the surface of a material, and achieves local high-temperature melting or vaporization through the absorption of laser energy by the material, thereby achieving precise cutting. The laser beam is highly focused into an extremely fine spot through an optical system, and its diameter is usually less than 0.1 mm. This extremely high energy density can locally heat the material to the melting or vaporization temperature in a very short time. By combining with auxiliary gases (such as oxygen, nitrogen, or compressed air), the molten material will be blown away, forming a smooth cutting surface.
Laser cutting technology is characterized by fast cutting speed, fine incision, small heat-affected zone, non-contact cutting, and no need for physical tools to contact the material surface, so it is suitable for high-precision processing tasks. This technology is widely used in the cutting of metal materials (such as stainless steel, carbon steel, aluminum, etc.) and non-metallic materials (such as plastics, wood, ceramics, etc.), especially in high-end manufacturing industries such as aerospace, automobile manufacturing, electronics, and medical devices.
Key Components of Laser Cutting Systems
The laser cutting system consists of multiple components that work together, each of which has a critical impact on the overall performance and cutting quality of the system. The main components include:
- Laser generator: The laser generator is the core component of the laser cutting machine, which produces a high-energy laser beam. Types of laser generators include CO2 laser generators, fiber laser generators, and solid-state laser generators. Different types of laser generators have different wavelengths and are suitable for cutting different materials. For example, fiber laser generators are usually used for cutting metal materials, while CO2 laser generators are more suitable for cutting non-metallic materials.
- Beam transmission system: After the laser beam is emitted from the laser generator, it needs to be transmitted to the cutting head through the beam transmission system. For CO2 laser generators, the beam is transmitted through lenses and reflectors; while fiber laser generators are transmitted through optical fibers, with low energy loss during transmission and stable beam quality.
- Focusing lens: After the laser beam passes through the beam transmission system, it needs to be focused on the surface of the material through the focusing lens to form an extremely fine light spot. The quality of the focusing lens directly determines the focal size of the laser beam, which in turn affects the cutting accuracy and speed.
- Cutting head: The main function of the cutting head is to guide the focused laser beam to the workpiece surface. It is usually equipped with an auxiliary gas nozzle for blowing away the molten material. The height control of the cutting head is very important, because improper height may lead to reduced cutting surface quality or equipment damage.
- Control system: The control system of the laser cutting machine is responsible for the operation coordination of the whole machine, including the precise control of laser output power, cutting speed, and trajectory planning. Modern laser cutting systems usually use CNC technology or computer control to provide high-precision automated cutting capabilities.
Factors Affecting Cutting Ability
The cutting ability of laser cutting is affected by a variety of factors, mainly including the following aspects:
- Laser power: The power of the laser generator is a key factor affecting cutting capabilities. High-power laser generators can provide more energy, causing the material to melt and vaporize faster, thereby cutting thicker materials. Generally speaking, the thicker the cutting thickness, the higher the laser power required.
- Cutting speed: Cutting speed is closely related to laser power. Increasing cutting speed can improve production efficiency, but if the speed is too fast, it may lead to reduced cut quality, incomplete cutting, or rough material edges. Controlling the appropriate cutting speed is the key to achieving high-quality cutting results.
- Material characteristics: Different materials have different abilities to absorb laser energy, melting points, and reflectivity, so the cutting effects vary greatly. Metal materials such as aluminum and copper have high reflectivity and are difficult to absorb laser energy. They require higher power or specific wavelength lasers for cutting. For some highly reflective materials, fiber laser generators are usually used because they can effectively reduce energy reflection losses.
- Laser wavelength: Different types of laser generators emit different laser wavelengths and are suitable for cutting different materials. For example, fiber laser generators usually operate in the 1.06 micron wavelength range, which is suitable for cutting metal materials, while CO2 laser generators have a wavelength of 10.6 microns, which is suitable for processing non-metallic materials.
- Auxiliary gas type and pressure: Auxiliary gas, such as oxygen, nitrogen, or compressed air, is usually used in the laser cutting process. Oxygen is usually used for cutting carbon steel because it can react with molten metal exothermically, speeding up the cutting speed. Nitrogen is suitable for cutting stainless steel and aluminum because it does not react with the material and can effectively avoid oxidation of the cut. The pressure of the auxiliary gas affects the cutting speed and the quality of the cutting edge. Higher pressure helps to quickly blow away the molten material, thereby improving the cutting quality.
By properly adjusting these factors, the performance of laser cutting can be optimized to ensure efficient and precise processing results.
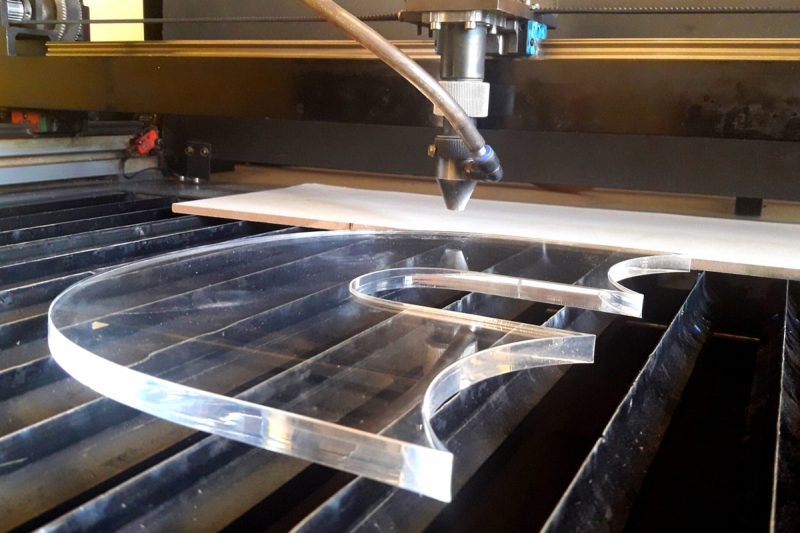
Understanding Laser Wavelengths
Laser wavelength refers to the wavelength of laser light waves, usually in nanometers (nm) or micrometers (µm), and is a key parameter that determines the properties and application areas of lasers. The wavelength of lasers directly affects the interaction between lasers and matter and determines the absorption rate, reflectivity, and scattering of lasers in different materials. Depending on the wavelength, lasers can cover a wide spectrum range from ultraviolet light and visible light to infrared light. Different types of laser equipment can achieve a variety of processing tasks by generating lasers of different wavelengths.
For example, the wavelength of an ultraviolet laser generator is usually 355 nanometers (nm), which is a short-wavelength laser and is suitable for micro-processing, while the wavelength of a fiber laser generator is usually 1.06 micrometers (µm), which is suitable for metal cutting. The shorter the wavelength, the more concentrated the laser energy is, which is suitable for precision processing tasks, while the longer wavelength laser is suitable for material surface treatment and large-area cutting.
Relationship Between Wavelength and Material Absorption
The interaction between laser and material depends largely on the characteristics of laser wavelength. The absorption rate of laser energy by materials varies with wavelength. Generally speaking, the shorter the wavelength, the more concentrated the laser energy, the stronger its penetration ability, and the higher the laser energy absorbed by the material. Short-wavelength lasers can produce higher energy density on the surface of materials, which is suitable for delicate and precise processing, such as the manufacture of electronic devices and medical equipment. On the contrary, the long-wavelength laser has a longer wavelength and more dispersed energy distribution, which is suitable for heating, melting, or vaporizing large-area materials, such as metal cutting and welding.
Different materials have different absorption characteristics for lasers, which depends on the electronic structure, optical properties and thermal conductivity of the material. For example, metal materials have a higher absorption rate for short-wavelength fiber laser generators (1.06 µm), which is suitable for metal cutting, welding and marking. Non-metallic materials such as glass and plastic have a better absorption rate for CO2 lasers (10.6 µm), so CO2 laser generators are widely used in cutting and engraving these materials.In addition, some high-reflectivity materials (such as copper and aluminum) have a higher reflectivity for lasers of specific wavelengths, and laser generators of specific wavelengths are required to avoid reflection losses. For example, when using a fiber laser generator to cut copper and aluminum, lasers with shorter wavelengths can reduce reflection problems, thereby improving cutting efficiency.
Commonly Used Laser Wavelengths in Cutting Applications
Laser wavelength is an important factor affecting the cutting effect. Lasers with different wavelengths are suitable for different materials and processing scenarios. The following are several common laser wavelengths and their application areas:
CO2 Laser Generator (10.6 µM)
CO2 laser generators operate in the far infrared band with a wavelength of 10.6 microns. Lasers of this wavelength are very suitable for processing non-metallic materials such as wood, plastic, glass, and acrylic. CO2 laser generators have a large power range and are suitable for a variety of applications from light engraving to thick plate cutting. Due to its long wavelength, the energy density of CO2 laser generators is low, so it is suitable for heating and melting larger areas of materials. It is widely used in billboard production, the packaging industry, and the textile industry.
Fiber Laser Generator (1.06 µM)
The wavelength of a fiber laser generator is usually 1.06 microns, which belongs to the near-infrared band. Lasers of this wavelength have high energy density and are particularly suitable for cutting metal materials such as stainless steel, carbon steel, aluminum, copper, etc. The fiber laser generator has a short wavelength, good beam quality, and high transmission efficiency, and is particularly suitable for metal cutting and welding that requires high precision and high speed. In addition, the fiber laser generator has low maintenance costs and a long equipment life and is widely used in industries such as automotive manufacturing, metal processing, and aerospace.
Nd Laser Generator (1.064 µM)
Nd (neodymium-doped yttrium aluminum garnet) laser generator is also a laser generator working in the near-infrared band with a wavelength of 1.064 microns. This laser generator is characterized by high peak power and good beam quality and is suitable for cutting, punching, and welding of thick metal plates. Due to its good pulse output characteristics, Nd laser generators are also widely used in precision processing, such as the manufacture of electronic products and medical devices. However, compared with fiber laser generators, Nd laser generators have lower photoelectric conversion efficiency, so they are gradually replaced by fiber laser generators.
Laser wavelength is one of the core parameters that determine the performance and application range of laser generators. The absorption characteristics of different materials to lasers vary with wavelength, so choosing the right laser wavelength is the key to ensuring the processing effect. In laser cutting applications, CO2 laser generators, fiber laser generators, and Nd laser generators each have their specific application fields, and reasonable selection can greatly improve processing efficiency and quality.
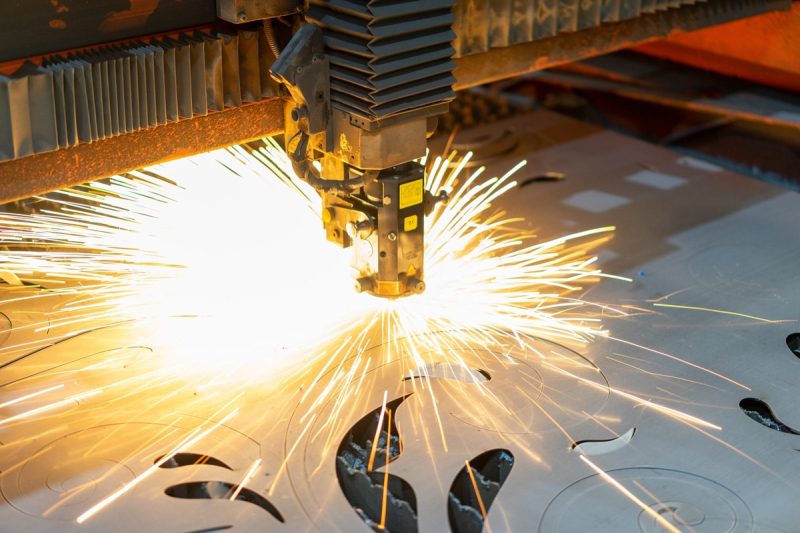
Effect of Laser Wavelength on Cutting Parameters
Material Absorption Characteristics
Different materials have significantly different absorption characteristics of laser wavelengths, which affects the cutting effect. The optical properties of a material determine its absorption rate of laser light of a specific wavelength. For example, metallic materials generally absorb short-wavelength lasers (such as fiber lasers and Nd lasers) better. The wavelength of fiber laser is about 1.06 microns, which is suitable for efficient cutting of metal materials such as stainless steel, aluminum, copper, and carbon steel. Since metal has a higher absorption rate for this wavelength, energy can be concentrated in the cutting area more quickly, achieving high-efficiency cutting and better edge quality.
In contrast, non-metallic materials such as wood, plastic, and glass have a higher absorption rate for long-wavelength CO2 lasers (10.6 microns) and are suitable for cutting and engraving with CO2 laser generators. This is because the CO2 laser has a longer wavelength and relatively dispersed energy, which is more suitable for processing large-area materials. In addition, the surface reflectivity of the material is also related to the laser wavelength. When cutting certain high-reflectivity materials (such as copper, aluminum, etc.) using a fiber laser generator, special treatment may be required to reduce energy loss and cutting instability caused by reflection.
Penetration Depth
Laser wavelength has a significant impact on the penetration depth of materials. Short-wavelength lasers generally have stronger penetrating capabilities and are suitable for cutting thicker materials. For example, due to their shorter wavelength and higher energy density, fiber lasers and Nd lasers are suitable for deep cutting, especially with better penetration in metal materials. Therefore, when cutting thick metal sheets, short-wavelength laser generators are usually the first choice, which can penetrate larger thicknesses while ensuring cutting accuracy.
In comparison, the CO2 laser has a longer wavelength and relatively weaker penetration ability, making it suitable for thinner non-metallic materials such as wood, plastic, cardboard, etc. In addition, the penetration depth also depends on the adjustment of parameters such as laser power, focal length, and cutting speed. Choosing the right laser wavelength can maximize the penetration depth while ensuring cutting accuracy and efficiency.
Heat Affected Zone (HAZ) and Thermal Effects
Different laser wavelengths directly affect the heat-affected zone (HAZ) during material cutting. The heat-affected zone refers to the area where the material melts or undergoes physical changes during the laser-cutting process. Generally, short-wavelength lasers produce smaller heat-affected zones because their energy is more concentrated, which can complete the cutting process faster and reduce heat diffusion to the surrounding area. A smaller heat-affected zone helps reduce thermal deformation and physical damage to the material, which is particularly important in applications with high precision requirements.
In contrast, CO2 lasers with longer wavelengths have a relatively large heat-affected zone due to their wider energy distribution. This is not particularly obvious when cutting non-metallic materials, but when cutting metal materials, it may cause problems such as thermal deformation of the material surface, slag, and reduced edge quality. Therefore, when cutting metals, short-wavelength lasers (such as fiber lasers) are usually superior to CO2 lasers because they can better control thermal effects and provide higher-quality cutting results.
Cutting Speed and Efficiency
Laser wavelength not only affects the absorption characteristics and heat-affected zone of the material but also directly affects the cutting speed and efficiency. The right laser wavelength can optimize the absorption of laser energy in the material, thereby increasing the cutting speed and reducing production costs. For example, fiber lasers are often faster than CO2 lasers in metal cutting due to their short wavelength and high energy density, especially in the cutting of thin metal sheets. Fiber lasers also have a high electro-optical conversion efficiency, which further reduces operating costs and improves production efficiency.
In the cutting of non-metallic materials, the long wavelength of the CO2 laser generator is not as fast as the fiber laser generator in cutting speed, but it is still very efficient in cutting specific materials such as wood, acrylic, and plastic. By selecting the appropriate laser wavelength and power, combined with optimized cutting parameters (such as focus position, cutting speed, and gas assist system), high efficiency and high-quality cutting effect can be achieved in the cutting process of different materials.
Laser wavelength is one of the key factors affecting cutting performance, directly affecting the material’s absorption characteristics, penetration depth, heat-affected zone, and cutting speed and efficiency. By selecting the appropriate laser wavelength based on the material characteristics, it is possible to improve cutting efficiency while reducing material deformation and damage, thereby achieving a higher-quality cutting effect. In laser cutting applications, fiber laser generators, and CO2 laser generators each have their own advantages at different wavelengths, providing reliable solutions for a variety of industrial applications.
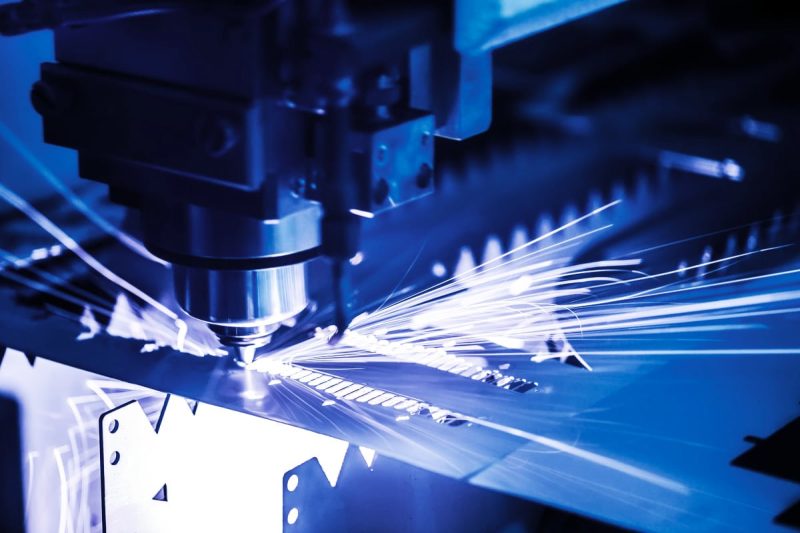
The Influence of Laser Wavelength on Cutting Quality
Cut Surface Finish and Edge Quality
Laser wavelength has a direct impact on the surface finish and edge quality of the material during the cutting process. Generally, lasers with shorter wavelengths, such as fiber lasers (1.06 microns), have higher energy density and can be more accurately focused on the cutting line of the material, thus producing smoother cutting surfaces and sharper edges in the cutting of metal materials. When cutting with fiber lasers, the energy is concentrated and the cutting path is clear, reducing slag and burrs on the cutting edge.
In contrast, long-wavelength CO2 lasers (10.6 microns) can also provide high-quality edge quality when cutting non-metallic materials such as wood, acrylic, and plastics. Still, the edge finish may be slightly inferior to that of short-wavelength lasers when cutting metal materials. This is because the energy density of CO2 lasers is relatively low, resulting in a larger range of heat diffusion during cutting, producing more slag and heat-affected zones. Therefore, when pursuing high precision and high-quality edges, fiber laser generators or Nd laser generators are usually the preferred options, especially in processing thin metal sheets.
Control of Incision Width and Taper
Laser wavelength plays an important role in controlling the incision width and taper. Lasers with shorter wavelengths (such as fiber lasers or Nd lasers) can usually achieve narrower incisions and finer cutting effects. Short-wavelength laser beams can be focused more accurately, the cutting path is narrow and straight, and the edges on both sides of the incision are very flat, which is suitable for industrial applications with high precision requirements, such as electronic component manufacturing, precision machining, etc.
In contrast, long-wavelength lasers such as CO2 lasers can result in wider cuts in some cases, especially when cutting thicker materials, where the taper of the cut may be more pronounced. This is because the laser beam scatters to a certain extent when penetrating the material, resulting in an uneven distribution of laser energy in the thickness direction of the material, resulting in a tapered cut. In these applications, the cut is wider on the upper side and narrower on the lower side, which is not conducive to applications that require precise, straight cutting. Therefore, choosing the right laser wavelength (especially short-wavelength lasers) can effectively control the width and taper of the cut and ensure cutting quality.
Reduces Thermal Deformation and Dross Formation
The choice of laser wavelength is critical in reducing thermal distortion and scum formation. Due to its concentrated energy and fast cutting speed, the short-wavelength laser can quickly complete the melting or vaporization of materials, reducing the heat load on the material during the cutting process. This high energy density results in a smaller heat-affected zone (HAZ), thereby reducing thermal deformation and edge warping of the material. Especially in the cutting of thin metal materials, the use of fiber laser or Nd laser can significantly reduce material deformation caused by thermal effects, thus improving the overall processing quality.
On the contrary, the long-wavelength CO2 laser has a relatively wide energy distribution and a large range of material heating, so the heat-affected zone is wide, which can easily cause material deformation, especially in the cutting of metal materials. Dross formation is another issue that needs to be considered. During cutting, if the material is not fully vaporized or melted, the residual metal slag may adhere to the cutting edge, affecting the cleanliness of the cutting and subsequent processing steps. Short-wavelength lasers can reduce the generation of slag through their efficient heat conduction and melting ability, keeping the incision clean and smooth.
Laser wavelength has a profound impact on the quality during the cutting process. Short-wavelength lasers (such as fiber lasers and Nd lasers) can achieve higher surface finish, narrower incisions, and more precise taper control due to their high energy density, especially in the cutting of metal materials. At the same time, short-wavelength lasers reduce the range of the heat-affected zone, avoid thermal deformation of the material and the formation of scum, and ensure the efficiency and quality of cutting. Long-wavelength lasers (such as CO2 lasers) are more suitable for cutting non-metallic materials, and their larger heat-affected zones are suitable for large-area, lower-precision material processing. By selecting the appropriate laser wavelength, users can optimize the cutting quality according to material characteristics and processing requirements, and achieve an efficient production and processing process.
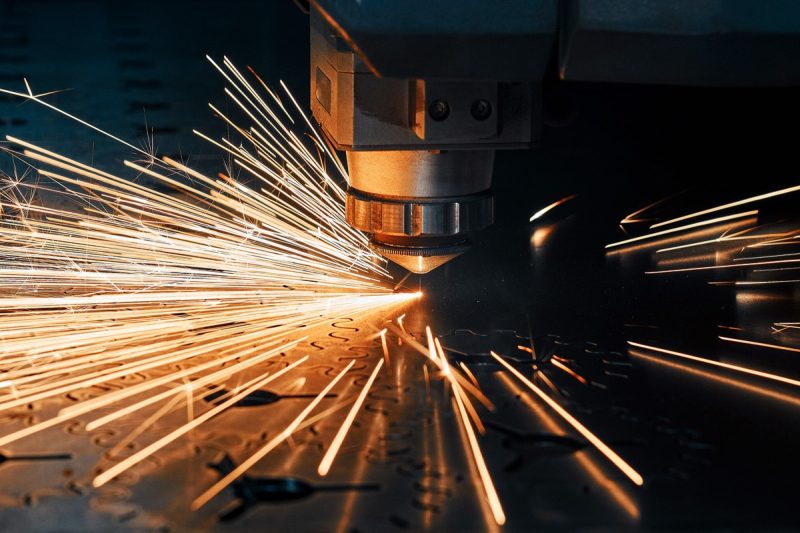
Comparative Analysis of Different Laser Wavelengths
CO2 laser generator
Describe
The CO2 laser generator has an operating wavelength of 10.6 microns, which is a long-wavelength laser type and is mainly used for cutting and processing non-metallic materials. Due to its efficient energy transmission characteristics, CO2 laser generators are widely used in the processing of non-metallic materials such as wood, plastic, glass, paper, and leather, especially in the advertising industry and home decoration.
Features
- The high absorption rate for non-metallic materials: The wavelength of the CO2 laser generator is suitable for processing non-metallic materials. Such materials have a high absorption rate for long-wavelength lasers, so the energy conversion efficiency is excellent. This makes the CO2 laser generator an ideal choice for cutting and engraving materials such as acrylic, wood, and leather.
- Fast cutting speed: When processing non-metallic materials, the cutting speed of the CO2 laser generator is relatively fast, especially when cutting thin plates and soft materials, it can complete the task quickly and efficiently.
- Poor cutting effect on metal materials: CO2 laser generators are not suitable for cutting and welding metal materials due to the low absorption rate of metals to 10.6 micron long-wavelength lasers. Although the absorption rate can be increased by coating an absorption layer on the metal surface, the effect and efficiency are still not as good as short-wavelength laser generators specifically used for metal processing.
- Commonly used in non-metal processing: such as cutting and engraving of materials such as plastic, paper, rubber, cloth, etc., widely used in billboard production, packaging, clothing manufacturing, and other industries.
- Application fields: CO2 laser generators are widely used in the processing of non-metallic materials, such as the advertising industry, handicraft manufacturing, home decoration, electronic and electrical fields, etc. Its outstanding performance on flexible materials makes it have important application value in these fields.
Fiber Laser Generator
Describe
The fiber laser generator has an operating wavelength of 1.06 microns and is the most commonly used short-wavelength laser generator in industrial laser-cutting applications. Fiber laser generators are particularly suitable for cutting and processing metal materials, and due to their high photoelectric conversion rate, they are outstanding in energy saving and environmental protection. Fiber laser generators have high energy density and can accurately cut thick metal materials.
Features
- High cutting efficiency: Fiber laser generators have extremely high energy density and can quickly concentrate energy on the metal surface to achieve efficient cutting. Whether it is a thin sheet of metal or a thicker steel plate, fiber laser generators can provide fast and precise cutting results. Especially for stainless steel, carbon steel, aluminum alloy, and other materials, its cutting speed and quality have significant advantages.
- Low energy consumption and low maintenance cost: The photoelectric conversion efficiency of the fiber laser generator can reach more than 30%. Compared with other types of laser generators, the energy loss is lower, so the operating cost is more economical. In addition, the fiber laser generator adopts all-fiber transmission, does not require complex optical lens adjustment, and requires less daily maintenance.
- High equipment price: Although fiber laser generators have many advantages in performance, their initial purchase cost is relatively high, especially for small businesses, equipment investment is an important consideration. However, with the development of technology and the gradual decline in equipment costs, the cost-effectiveness of fiber laser generators is constantly improving.
- Ideal choice for metal processing: Fiber laser generators are particularly suitable for cutting, welding and marking of metal materials, and are widely used in automotive manufacturing, aerospace, precision machinery and other fields.
- Application areas: Fiber laser generators are the main equipment in the field of metal processing and are widely used in industries such as automobile manufacturing, aerospace, home appliance manufacturing, and metal sheet processing. They have irreplaceable advantages, especially in industrial scenarios that require high-precision and fast processing.
Nd Laser Generator
Describe
The operating wavelength of the Nd laser generator (Nd-doped YAG laser generator) is 1.064 microns, which is similar to that of a fiber laser generator. Due to its good pulse characteristics, the Nd laser generator is suitable for specific fine-processing applications, such as marking, welding, and cutting. Unlike fiber laser generators, the Nd laser generator is more effective in certain specific applications, especially in the local processing of plastics and metals.
Features
- Strong cutting ability: Although not as efficient and widely used as fiber laser generators, the pulsed laser of Nd laser generators can provide high peak energy, which is suitable for fine cutting and micro-processing of metals, plastics and other materials. It can cut thick metal materials under high-intensity conditions, especially in fine processes such as marking and drilling on the surface of metal materials.
- Low efficiency: Compared with fiber laser generators, the photoelectric conversion efficiency of Nd laser generators is lower, usually only 2%-10%, so its operating energy consumption is relatively high. This feature makes Nd laser generators suitable for some specific processing scenarios rather than large-scale, efficient production lines.
- Suitable for special applications: Due to its excellent pulse characteristics, Nd laser generators have unique advantages in applications that require high precision and special pulse control. They are mainly used in metal welding, drilling, precision marking and other fields, especially in situations where high processing accuracy and surface quality are required.
- Application fields: Nd laser generators are widely used in high-precision processing fields, such as electronic product manufacturing, medical device processing, mold repair, and other industries. In addition, it is also commonly used in metal welding and marking in the aerospace field and plays a role in precision processing scenarios that require high energy density.
Different types of laser generators have their own unique advantages in cutting applications due to their different working wavelengths. CO2 laser generators are more suitable for the processing of non-metallic materials, fiber laser generators are star equipment in the field of metal processing, with high efficiency and low energy consumption, and Nd laser generators have a place in precision processing due to their pulse characteristics. According to specific processing requirements and material characteristics, choosing the appropriate laser wavelength and laser generator type can greatly improve cutting efficiency and processing quality.
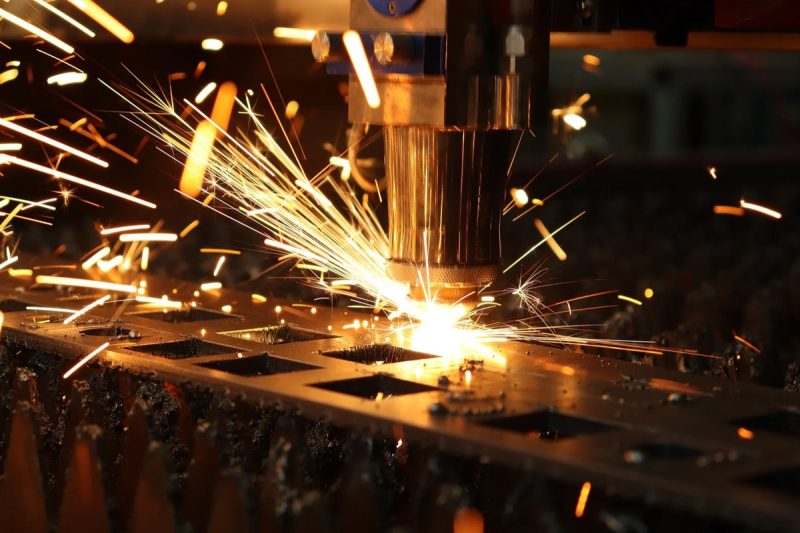
Optimization Strategy for Laser Wavelength Selection
In laser cutting, it is very important to choose the right laser wavelength, which not only affects the cutting quality but also directly determines the processing efficiency, cost-effectiveness, and overall energy utilization. Optimizing the selection of laser wavelength can help companies achieve efficient production while minimizing operating costs. The following will be analyzed in detail from multiple aspects such as material properties, cutting efficiency, beam transmission, and cost control.
Material Type and Thickness Considerations
There are significant differences in the absorption rate of laser by different materials, so when choosing the appropriate laser wavelength, you first need to consider the type and thickness of the material to be processed. The shorter the laser wavelength, the higher the energy concentration, and the more suitable it is for cutting high-density materials such as metal. Longer wavelength lasers, such as CO2 lasers, are more suitable for cutting non-metallic materials, such as wood, acrylic, leather, etc.
- Metal materials: Metal materials, such as steel, aluminum, stainless steel, etc., usually absorb short-wavelength lasers (such as fiber lasers and Nd lasers) better. These materials can efficiently absorb lasers with a wavelength of about 1 micron, producing a rapid melting effect, making the cutting process smoother and more efficient. Fiber laser generators are particularly suitable for metal cutting, and can quickly process thicker metal sheets and provide good cutting quality.
- Non-metallic materials: For non-metallic materials such as plastics, wood, glass and organic materials, the long wavelength (10.6 microns) of the CO2 laser generator is more ideal. CO2 laser has a high energy absorption rate when processing non-metallic materials, which can effectively achieve fast cutting and engraving. Especially on thinner non-metallic materials, CO2 laser processing accuracy is higher, cutting edges are smooth, and the possibility of material deformation is reduced.
- Material thickness: Material thickness is also an important factor in selecting laser wavelength. For thicker materials, short-wavelength lasers (such as fiber lasers) usually have higher penetration capabilities, can provide stronger focusing capabilities, and improve processing efficiency. For thin materials, choosing a moderate wavelength can prevent excessive ablation and maintain the quality of the cutting edge.
Strategies to Maximize Cutting Efficiency and Quality
By selecting the appropriate laser wavelength according to the material characteristics, cutting efficiency and quality can be greatly improved. The two key goals of laser cutting are cutting speed and cutting quality, and the correct wavelength selection can achieve a balance between the two.
- Optimization of cutting speed: Short-wavelength lasers (such as fiber lasers) have high energy density and can quickly heat the surface of metal materials and quickly complete cutting. This feature is especially important in metal material processing because higher cutting speeds mean shorter production cycles and higher production efficiency. Similarly, for non-metallic materials, CO2 lasers can quickly cut thinner materials and improve production efficiency.
- Improved cutting quality: Lasers with shorter wavelengths usually produce smaller heat-affected zones (HAZ), which helps reduce the thermal deformation of materials and ensures the flatness and smoothness of the cut edges. Especially in precision processing scenarios, such as the manufacture of electronic products, the precise selection of laser wavelength is crucial to improving the quality of finished products.
The Importance of Adaptive Optics and Beam Delivery Systems
Adaptive optics and efficient beam delivery systems play an important role in the laser cutting process. They not only improve the focusing ability of the laser but also make real-time adjustments based on the surface characteristics of different materials to ensure cutting stability and accuracy.
- Advantages of adaptive optics: Adaptive optics can adjust the shape and focal position of the laser beam according to the working conditions of the laser generator and the characteristics of the material, thereby improving cutting efficiency and quality. This technology is particularly effective when processing materials with irregular surfaces or large thickness variations. It can automatically adjust the focus so that the laser always maintains the best energy distribution, thereby avoiding the reduction of cutting accuracy due to focus offset.
- The role of the beam transmission system: An efficient beam transmission system can transmit the laser beam to the work surface with minimal loss. The transmission method of the laser (such as fiber transmission and free space transmission) will affect the energy transmission efficiency of the laser. The all-fiber transmission method of the fiber laser generator greatly reduces energy loss, making it particularly outstanding in long-distance transmission. At the same time, an excellent transmission system can reduce the scattering and diffraction of the laser beam, ensuring the energy concentration after the laser is focused, thereby improving the cutting accuracy.
Cost-Effectiveness and Energy Efficiency Considerations
Choosing the right laser wavelength can not only improve cutting quality but also effectively reduce production costs and energy consumption in long-term operations. The type of laser generator, photoelectric conversion efficiency, and equipment operating costs will directly affect the overall production cost.
- Energy efficiency optimization: Different types of laser generators have large differences in energy conversion efficiency. The photoelectric conversion efficiency of fiber laser generators is as high as 30%-40%, which is much higher than the 10% of CO2 laser generators. This means that under the same processing conditions, fiber laser generators can complete more work with less energy, which not only helps to reduce electricity costs but also reduces the need for equipment heat dissipation and improves the overall stability of the system.
- Reduced maintenance costs: The beam transmission method of fiber laser generators and Nd laser generators is more stable and reliable than that of CO2 laser generators, reducing the dependence on complex optical systems, so the maintenance frequency and maintenance cost is lower. In addition, the non-consumable design of fiber laser generators also makes it more cost-effective in long-term operation.
- Initial equipment cost and long-term return: Although the initial equipment investment of fiber laser generators is relatively high, its high efficiency and low energy consumption characteristics give it a significant cost advantage in long-term operation. The equipment price of a CO2 laser generator is lower and suitable for a wide range of applications of non-metallic materials, but it requires more consumables and maintenance investment.
In laser cutting, the optimal selection of wavelength directly affects processing efficiency, cutting quality, and cost-effectiveness. By rationally analyzing the type, thickness, production requirements, and other factors of the material, selecting the most suitable laser wavelength, combined with adaptive optics and an efficient beam transmission system, can not only significantly improve production efficiency, but also reduce operating costs and maximize the enterprise’s overall benefit. In the highly competitive modern manufacturing industry, the flexible use of these optimization strategies will help companies gain significant competitive advantages in laser cutting technology.
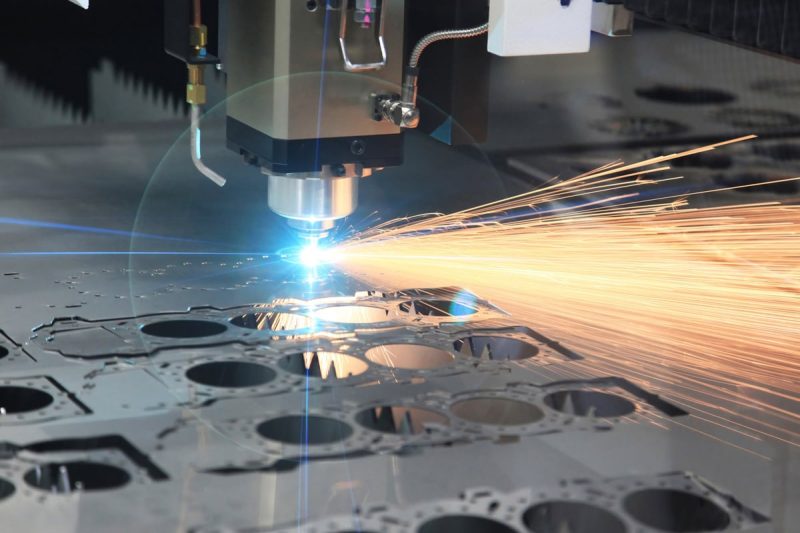
Summarize
The role of laser wavelength in laser cutting is crucial, and it directly affects the precision, efficiency, and quality of cutting. Different materials have different absorption characteristics for lasers of different wavelengths. Therefore, understanding the characteristics of various laser wavelengths is the key to optimizing the cutting effect. By properly selecting the laser wavelength, the best cutting effect for a specific material can be ensured, whether it is metal, non-metal, or composite material. Optimizing the selection of laser wavelength can not only improve the cutting quality, but also reduce the heat-affected zone and deformation during the production process, improve the surface finish, and achieve precise control of the incision width and taper. In addition, the appropriate selection of laser wavelength can improve cutting efficiency, reduce energy consumption, and reduce overall production costs. Combined with adaptive optics technology and efficient beam transmission systems, the performance of the laser can be further optimized to ensure continuous improvement of the cutting process and efficient operation of production. Ultimately, by deeply understanding and optimizing the application of laser wavelengths, the manufacturing industry can better meet different processing needs, thereby promoting the continuous advancement of laser cutting technology, enhancing market competitiveness, and expanding possibilities for future laser applications.
Choosing the right laser wavelength is the key to ensuring cutting efficiency and quality. With its rich industry experience and technical support, AccTek can help you easily determine and select the laser wavelength that best suits your processing needs. Our high-quality laser equipment not only has excellent cutting performance but also provides stable after-sales service guarantees to ensure your worry-free production. Whether it is metal or non-metal material processing, or complex customization needs, AccTek can provide you with the best solution. Contact us now to make your manufacturing process more efficient and more accurate!
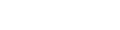
Contact information
- [email protected]
- [email protected]
- +86-19963414011
- No. 3 Zone A, Lunzhen Industrial Zone,Yucheng City , Shandong Province.
Get Laser Solutions