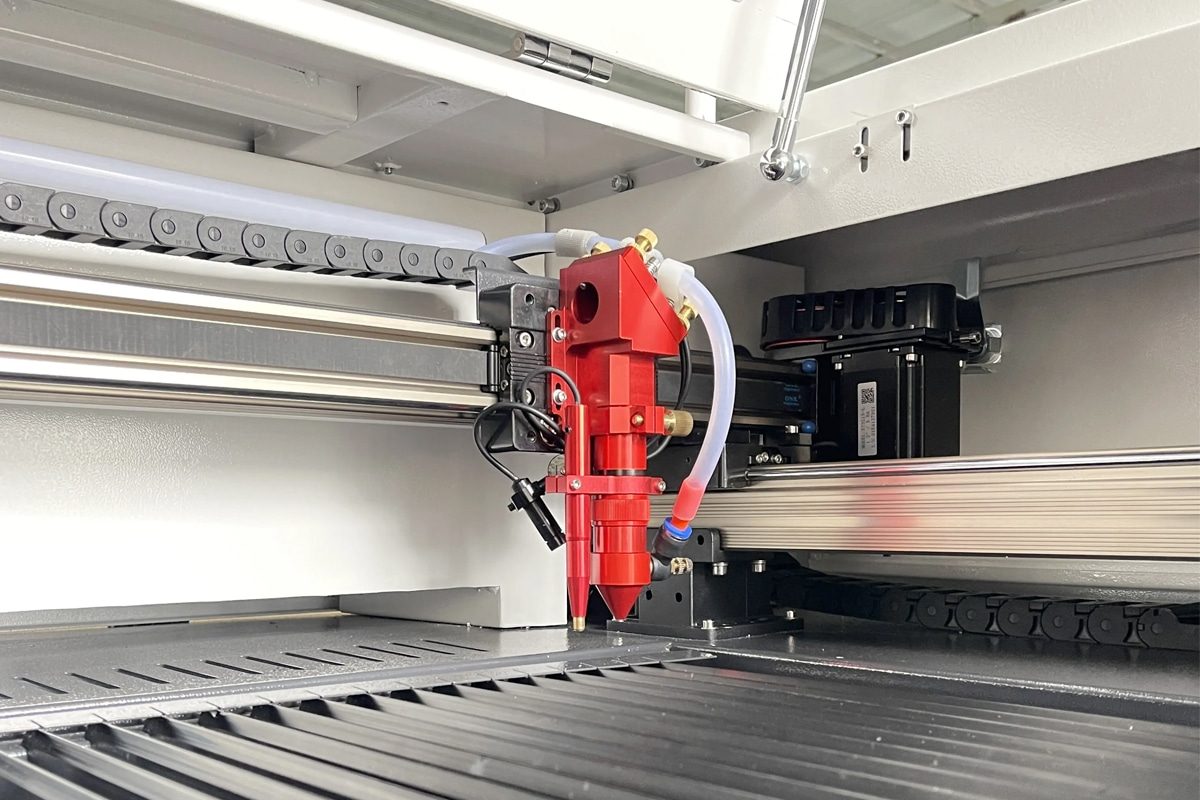
Energy Consumption And Power Requirements Of CO2 Laser Cutting Machines
In modern manufacturing, CO2 laser cutting machines are widely used in metal processing, manufacturing, and other fields. These highly efficient cutting tools consume large amounts of energy during operation. The energy consumption of a CO2 laser-cutting machine depends on several factors, including the type, thickness, and shape of the material being cut, as well as parameters such as cutting speed and laser power. Among them, the energy consumption and power requirements of the CO2 laser cutting machine are important factors affecting its operating cost and efficiency. This article will focus on the energy consumption and power requirements of CO2 laser-cutting machines. By reasonably controlling cutting parameters, selecting appropriate laser power, and improving energy utilization efficiency, production efficiency can be improved to better meet market demand.
Table of Contents
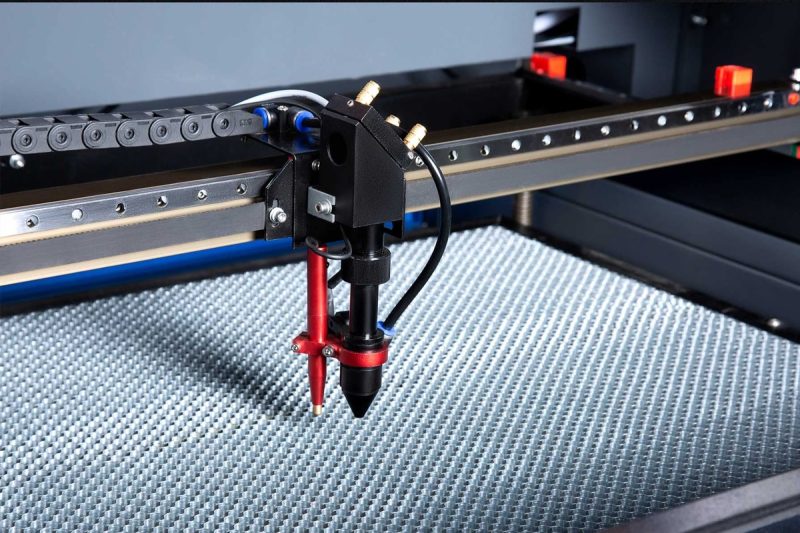
Working Principle Of CO2 Laser Cutting Machine
CO2 laser cutting machines use high-energy beams emitted by CO2 (carbon dioxide) laser generators to cut. Here’s how it works:
- The laser generator generates a laser beam: First, the CO2 laser generator generates a laser beam by exciting a gas (usually carbon dioxide) with an electric current. These laser beams typically have a wavelength of 10.6 microns and are suitable for cutting most metallic and non-metallic materials.
- Beam focusing: Through the lens system, the laser beam is focused into a spot with high energy density. The focused beam is very energetic and can heat the surface of the material to a temperature where it melts or evaporates.
- Cutting materials: After the laser beam is focused, it is precisely directed to the surface of the material to be processed. When the laser beam interacts with the material surface, the material absorbs the light energy and rapidly heats to high temperatures. At high temperatures, the surface of the material begins to melt or evaporate.
- Gas injection assist: Typically, CO2 laser cutting machines will also utilize a gas injection system, such as nitrogen or oxygen, to blow away molten or vaporized material and help maintain a clear-cutting area.
- Form cutting contour: By moving the workpiece or laser head, the laser beam cuts the material along a predetermined trajectory to form the required cutting contour.
Through these steps, CO2 laser cutting machines can efficiently and accurately cut various materials and are widely used in manufacturing and other fields.
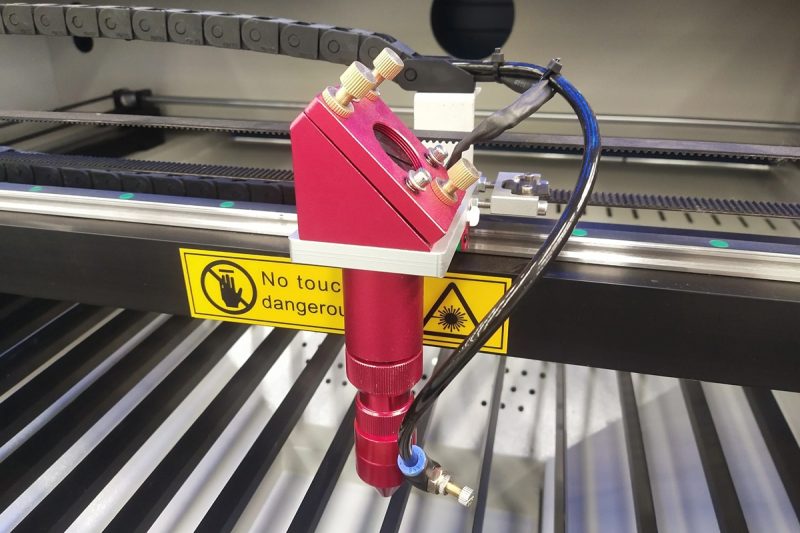
Factors Affecting Energy Consumption And Power Of CO2 Laser Cutting Machines
The energy consumption and power requirements of CO2 laser cutting machines are affected by many factors, which directly affect the energy consumption and operating efficiency of the cutting machine. Here are some of the main influencing factors:
- Type and thickness of cutting materials: Different types and thicknesses of materials have different requirements for the energy consumption of CO2 laser cutting machines. Typically, cutting thicker materials requires more energy to fully penetrate and therefore consumes more power. In addition, some materials may have different absorption rates for lasers, affecting cutting efficiency.
- Cutting speed: Cutting speed refers to the speed at which the laser cutting head moves on the surface of the workpiece. Increasing cutting speed improves productivity but also increases energy consumption. Typically, higher cutting speeds require more energy to maintain a stable cutting process.
- Laser power: Laser power refers to the energy of the laser beam generated by the CO2 laser generator. High-power lasers heat the material surface more quickly and are therefore often used for processing thick materials or making quick cuts. However, high-power lasers also consume more energy and increase the energy consumption of the cutting machine.
- The efficiency of the laser generator: The efficiency of the laser generator directly affects the energy utilization efficiency. Efficient laser generators can convert more electrical energy into laser energy, thereby reducing energy waste. Therefore, when choosing a CO2 laser-cutting machine, you need to consider the efficiency of the laser generator and its impact on overall energy consumption.
- Use of auxiliary gas: CO2 laser cutting machines usually use auxiliary gases such as nitrogen and oxygen to help the cutting process. These gases not only blow away molten or vaporized material from the cutting area, but they also improve cut quality and speed. However, the use of auxiliary gas also increases energy consumption.
In short, the energy consumption and power requirements of CO2 laser-cutting machines are affected by many factors. Understanding these influencing factors and taking corresponding measures can help companies reduce production costs and improve production efficiency, thereby better meeting market demand.
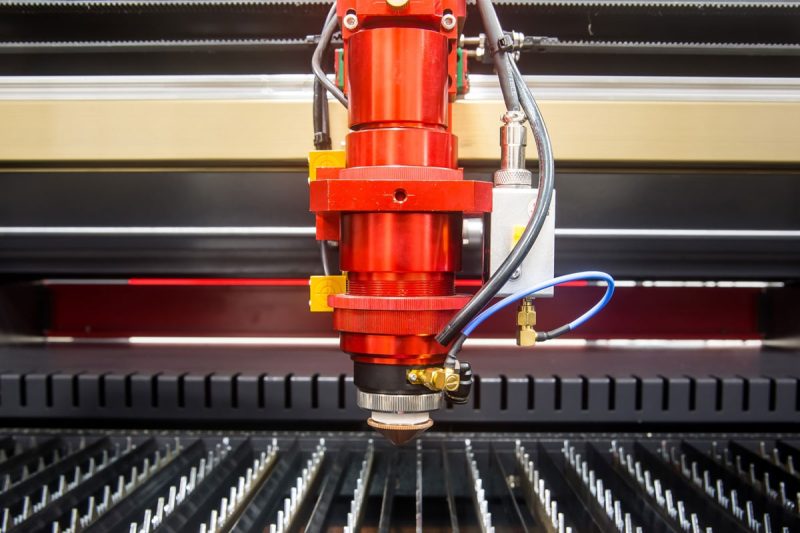
Energy Consumption Assessment Of CO2 Laser Cutting Machines
For the energy consumption assessment of CO2 laser cutting machines, the following aspects need to be considered:
- Energy consumption: First, it is necessary to evaluate the amount of energy consumed by the CO2 laser-cutting machine under normal operating conditions. This includes the consumption of auxiliary energy such as electricity and gas. This can be assessed by monitoring the power usage and gas consumption of the cutting machine.
- Cutting material efficiency: The cutting process of different materials may consume different amounts of energy. Therefore, it is necessary to evaluate the energy consumption when cutting different types and thicknesses of materials. Typically, cutting thicker or harder materials consumes more energy.
- Production efficiency: The production efficiency of CO2 laser cutting machines will also directly affect energy consumption. High-efficiency cutting machines can complete more cutting tasks in a shorter period, thereby reducing energy consumption. Therefore, it is necessary to evaluate the production efficiency of the cutting machine and the energy consumption under different production batches.
- Laser generator efficiency: The laser generator is the core component of the CO2 laser cutting machine, and its efficiency directly affects the energy utilization efficiency. It is necessary to evaluate the energy conversion efficiency of the laser generator and the energy consumption under different powers. High-efficiency laser generators can convert more electrical energy into laser energy, thereby reducing energy waste.
- System optimization: Through system optimization and technology improvement, the energy consumption of CO2 laser cutting machines can be reduced. For example, measures such as optimizing cutting parameters, improving laser generator design, and improving auxiliary gas utilization efficiency can reduce energy consumption. Therefore, it is necessary to evaluate the impact of different optimization measures on energy consumption and select an appropriate optimization solution.
Therefore, the energy consumption assessment of CO2 laser-cutting machines needs to consider many aspects. Through comprehensive evaluation and taking the above corresponding measures, the energy consumption of CO2 laser cutting machines can be reduced, energy efficiency improved, and production costs reduced.
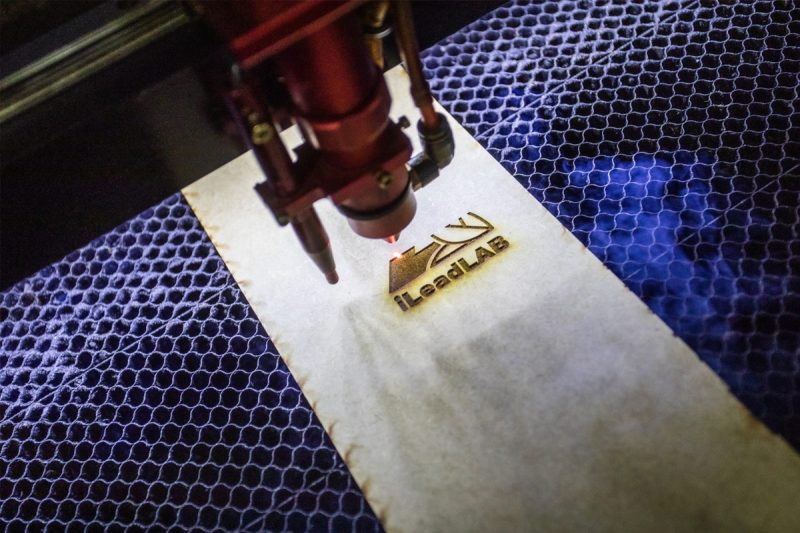
Power Requirements And Adjustments Of CO2 Laser Cutting Machines
The power requirements and adjustments of a CO2 laser cutting machine are some of the key factors affecting its cutting efficiency and cost. Below is a discussion of its power requirements and adjustments:
Power Requirements
The power requirements of a CO2 laser-cutting machine directly affect its cutting capacity and speed. Generally speaking, higher-power lasers heat the material surface faster, allowing for faster cutting speeds and higher productivity. However, high-power lasers also mean higher energy consumption and equipment costs. Therefore, companies need to determine the appropriate laser power based on production needs, material properties, and budget considerations.
Material Type And Thickness
Different types and thicknesses of materials have different laser power requirements. Generally speaking, cutting thicker or harder materials requires a higher-power laser to achieve effective cutting. Therefore, when choosing a CO2 laser cutting machine, you need to consider the types and thicknesses of materials commonly used in production and choose the appropriate power according to their needs.
Adjustment Method
CO2 laser cutting machines usually have the function of adjusting power to meet different materials and cutting requirements. Adjusting the laser power can be achieved by adjusting the working parameters of the laser generator or changing the cutting parameters. For example, the power of the laser output can be changed by adjusting the current or pulse frequency of the laser generator, or the cutting parameters can be adjusted by adjusting the cutting speed and focal length. In this way, the power of the cutting machine can be flexibly adjusted according to actual needs to achieve the best cutting effect and energy efficiency.
Automation Control
Some advanced CO2 laser cutting machines have automatic control functions that can automatically adjust power and cutting parameters according to preset cutting plans. This automated control can adjust laser power in real-time according to different workpieces and cutting requirements, achieving higher production efficiency and cutting quality while maximizing energy savings.
In summary, the power requirements and adjustments of a CO2 laser cutting machine are important factors affecting its cutting efficiency and cost. By properly adjusting and meeting the power requirements of the CO2 laser cutting machine, the best performance and energy efficiency of the CO2 laser cutting machine can be achieved.
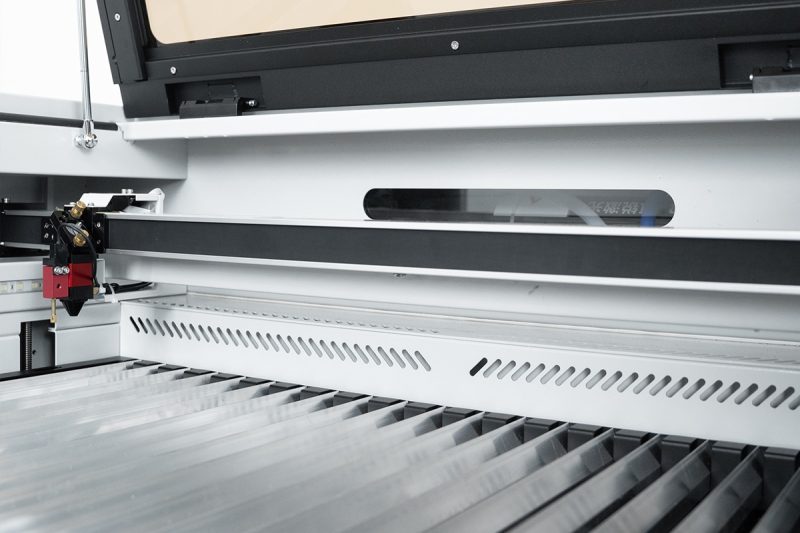
Energy Saving Technologies And Measures
In the field of CO2 laser cutting machines, adopting energy-saving technologies and measures is crucial to reducing energy consumption, improving production efficiency, and reducing costs. Here are some common energy-saving techniques and measures:
- Selection of an efficient laser generator: Choosing an efficient CO2 laser generator is one of the important steps in energy saving. An efficient laser generator can convert more electrical energy into laser energy and reduce energy waste.
- Cutting parameter optimization: By optimizing cutting parameters, a more efficient cutting process can be achieved, thereby reducing energy consumption. For example, parameters such as cutting speed, focal length, and laser power can be adjusted to suit the cutting needs of different materials and thicknesses while minimizing energy consumption.
- Intelligent control system: The intelligent control system can achieve precise control and optimal adjustment of the CO2 laser cutting machine, thereby achieving energy saving. These systems often automatically adjust laser power, cutting speed, and other parameters based on the cutting task and material properties to achieve optimal cutting results and energy efficiency.
- Waste material reuse: Effective collection and reuse of waste materials generated during the cutting process. For example, recycling and processing or reusing waste materials as raw materials can reduce the demand for new materials, and reduce energy consumption and environmental pollution.
- Regular maintenance and upkeep: Regular maintenance and upkeep of the CO2 laser cutting machine can ensure its normal operation and efficient work. By promptly replacing worn parts, cleaning equipment, and adjusting systems, you can reduce energy consumption and extend the life of your equipment.
- Employee training and awareness raising: By improving employees’ energy-saving awareness and skill levels, the effective implementation of energy-saving measures can be promoted, thereby reducing energy consumption and costs.
To sum up, by adopting the above energy-saving technologies and measures, the energy consumption of CO2 laser cutting machines can be effectively reduced, production efficiency improved, costs reduced, and sustainable development and environmentally friendly production achieved.
Summarize
To sum up, the energy consumption and power requirements of CO2 laser cutting machines are technical indicators that need to be paid attention to. When using a CO2 laser cutting machine, it is crucial to understand its energy consumption and power requirements. These parameters directly affect the operating cost and efficiency of the equipment.
Understand and comprehensively utilize these parameters, and configure them reasonably according to actual needs to achieve an efficient and energy-saving cutting process. It can not only improve the production efficiency of equipment, but also reduce energy consumption and operating costs, and promote the sustainable development of industrial production. In future development, we look forward to seeing the emergence of more innovative technologies to bring breakthroughs and progress to the CO2 laser cutting machine industry.
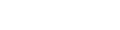
Contact information
- [email protected]
- [email protected]
- +86-19963414011
- No. 3 Zone A, Lunzhen Industrial Zone,Yucheng City , Shandong Province.
Get Laser Solutions