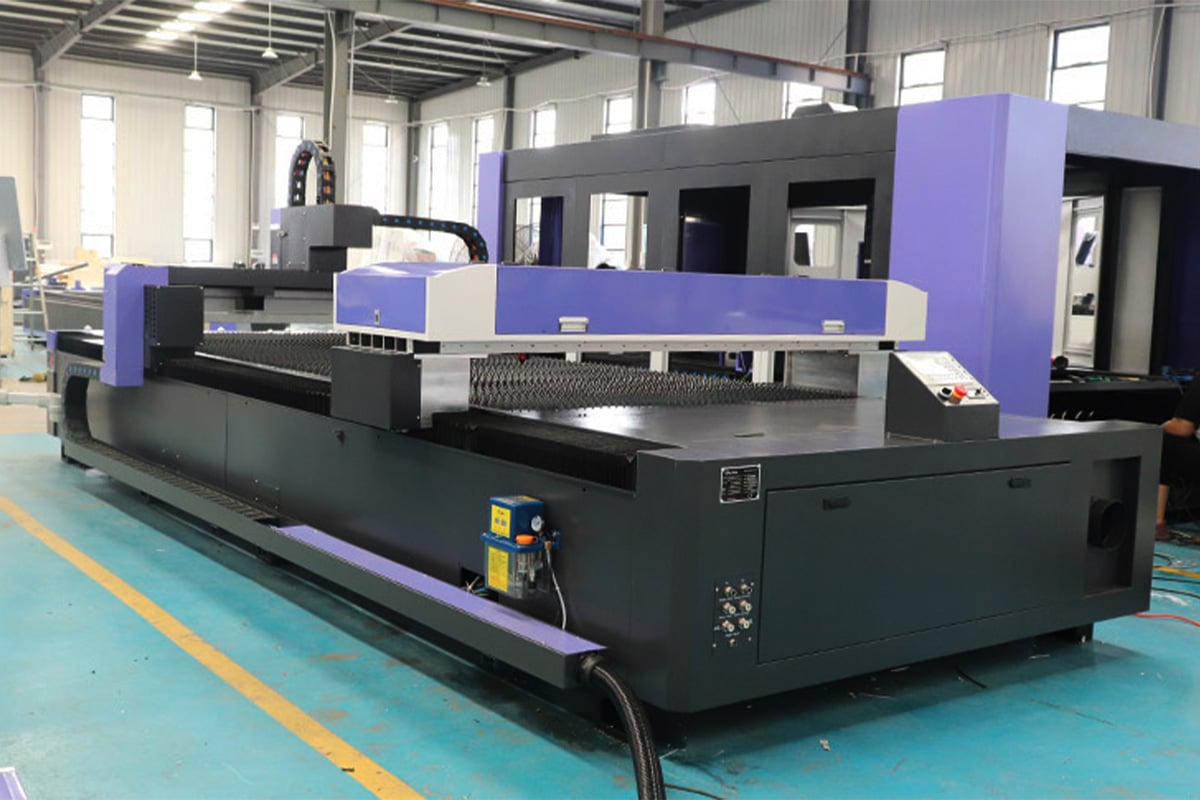
¿Cómo lograr el ancho de incisión mínimo en el corte por láser de CO2?
La tecnología de corte por láser de CO2 se ha utilizado ampliamente en el corte de diversos materiales, como metal, plástico, madera, tela, etc., gracias a sus ventajas de alta precisión, alta velocidad y procesamiento sin contacto. El ancho de corte se refiere al ancho de la incisión formada por el rayo láser durante el proceso de corte. Este indicador afecta directamente la precisión y la calidad del corte. Un ancho de corte menor permite lograr un procesamiento más refinado, mejorar la precisión del producto, reducir el desperdicio de material y los costos de producción. Por lo tanto, es un criterio importante para medir la calidad del corte por láser.
El control del ancho de incisión no solo mejora la calidad del producto, sino que también está estrechamente relacionado con la tasa de utilización de materiales, la facilidad de procesamiento posterior y la eficiencia general de la producción. Para los fabricantes, la optimización del ancho de incisión está directamente relacionada con el control de los costos de producción. Especialmente en la producción a gran escala, un ancho de incisión demasiado grande puede generar desperdicio de material y afectar la fluidez de los procesos posteriores. Por lo tanto, un control preciso del ancho de incisión es fundamental para lograr una producción eficiente y económica.
Tabla de contenido
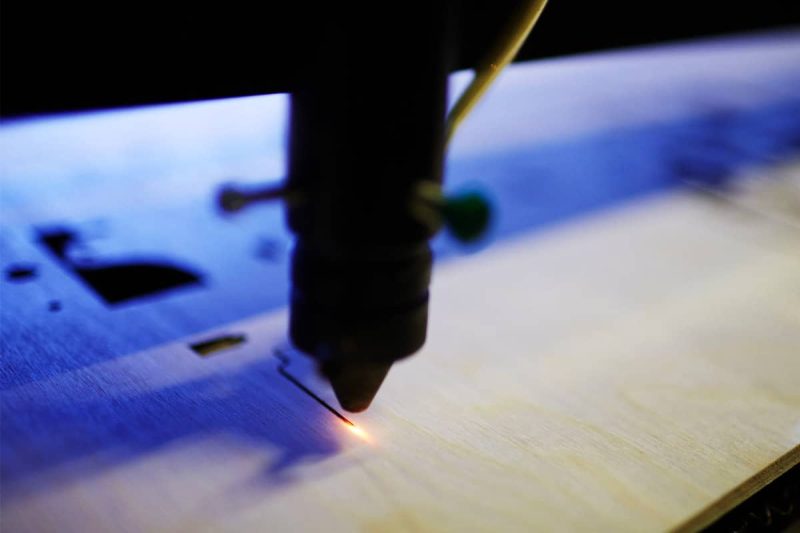
Factores clave que afectan el ancho de corte del láser de CO2
El efecto de corte de la tecnología láser de CO2 se ve afectado por numerosos factores, y el ancho de corte es uno de los indicadores más críticos. Mediante un ajuste y optimización razonables de estos factores, los fabricantes pueden mejorar la eficiencia de la producción y reducir la pérdida de material, garantizando a la vez una alta precisión. A continuación, se presentan varios factores clave que afectan el ancho de corte y sus estrategias de optimización:
Tamaño del foco láser: El tamaño del foco láser afecta directamente el diámetro del punto de corte. Cuanto más pequeño sea, más estrecha será la incisión. Cuanto más preciso sea el enfoque, mayor será la concentración de energía del haz láser, lo que mejora la precisión de corte. Para optimizar el ancho de corte, es importante elegir la lente con la distancia focal adecuada. Generalmente, una lente con distancia focal corta proporciona un diámetro de enfoque menor, logrando así un corte más preciso. Para diferentes materiales y requisitos de corte, se puede optimizar el tamaño del foco ajustando la distancia focal para garantizar el mejor efecto de corte.
Potencia del láser: La potencia del láser determina directamente la intensidad de la energía térmica del haz láser, lo que afecta los efectos de fusión, evaporación y corte durante el proceso. Si la potencia del láser es demasiado alta, es fácil que la incisión sea demasiado amplia o incluso que atraviese el material; si es demasiado baja, podría no penetrar completamente el material, lo que resultaría en un corte incompleto. Es crucial ajustar la potencia del láser al valor óptimo según el espesor y las propiedades de los diferentes materiales. Por ejemplo, para materiales más gruesos, la potencia debe aumentarse adecuadamente, mientras que para materiales delgados, puede reducirse para evitar que la incisión sea demasiado amplia. Mediante un ajuste preciso de la potencia, los fabricantes pueden lograr un corte preciso y eficiente.
Velocidad de corte: La velocidad de corte también juega un papel importante en el corte láser. Aumentar la velocidad de corte adecuadamente no solo reduce la zona afectada por el calor y el impacto del material fundido en el borde del corte, sino que también mejora la eficiencia de producción. Sin embargo, si la velocidad de corte es demasiado rápida, el rayo láser podría no tener tiempo suficiente para penetrar completamente el material, lo que resulta en un corte incompleto. Por el contrario, una velocidad demasiado lenta puede provocar un corte demasiado ancho y producir un exceso de material fundido. Para optimizar el efecto de corte, la velocidad de corte debe ajustarse con precisión según el tipo y el grosor del material para garantizar que se minimice el ancho de corte.
Tipo y presión del gas auxiliar: El gas auxiliar desempeña un papel fundamental en el corte láser. Los gases auxiliares más utilizados son el oxígeno, el nitrógeno y el aire. El oxígeno puede mejorar la reacción de combustión durante el proceso de corte y es adecuado para cortar materiales como hierro y acero; el nitrógeno puede reducir la oxidación y es adecuado para materiales como el acero inoxidable; el aire se utiliza ampliamente en diversos materiales debido a su economía. Además del tipo de gas, la presión del gas también influye en la calidad del corte. Una presión de gas adecuada puede ayudar a eliminar la masa fundida y evitar que se adhiera al borde de la incisión, reduciendo así su anchura. Una presión de gas baja puede impedir la eliminación eficaz de la masa fundida y aumentar la anchura de la incisión, por lo que se debe seleccionar la presión y el tipo de gas adecuados para optimizar el corte.
Propiedades del material: Las propiedades de los diferentes materiales pueden afectar significativamente la precisión del corte láser. Propiedades como la tasa de absorción, la conductividad térmica y el punto de fusión afectan directamente la eficiencia de transmisión del haz láser y la calidad del corte. Los materiales altamente reflectantes (como el aluminio y el cobre) tienden a provocar que el haz láser se refleje y disperse, reduciendo así el efecto de corte. Para estos materiales, es necesario optimizar los parámetros del láser, especialmente para aumentar la densidad de potencia, a fin de garantizar su penetración efectiva. Por el contrario, los materiales poco reflectantes, como el acero, son más fáciles de cortar. Al cortar diferentes materiales, los fabricantes deben ajustar los parámetros de corte según sus características para garantizar la mejor calidad de corte y el menor ancho de incisión.
Optimización de la trayectoria de corte: Optimizar la trayectoria de corte también es crucial para controlar el ancho de incisión. Una trayectoria de corte uniforme puede reducir el error del haz láser al cambiar de dirección y evitar incisiones irregulares. Especialmente al cortar formas complejas, un diseño razonable de la trayectoria y la reducción de giros y paradas de emergencia pueden mejorar significativamente la precisión de corte. Además, optimizar las estrategias de avance y retracción también puede ayudar a reducir la ablación del material y evitar la deformación de la incisión causada por un calentamiento excesivo. Al diseñar la trayectoria, se deben evitar en la medida de lo posible los giros rápidos y las rutas irregulares para garantizar una distribución uniforme de la energía durante el proceso de corte, controlando así el ancho de incisión.
Al controlar y optimizar con precisión estos factores clave, los fabricantes pueden reducir los costos de producción, mejorar la utilización del material y aumentar la eficiencia de la producción garantizando al mismo tiempo un corte de alta precisión.
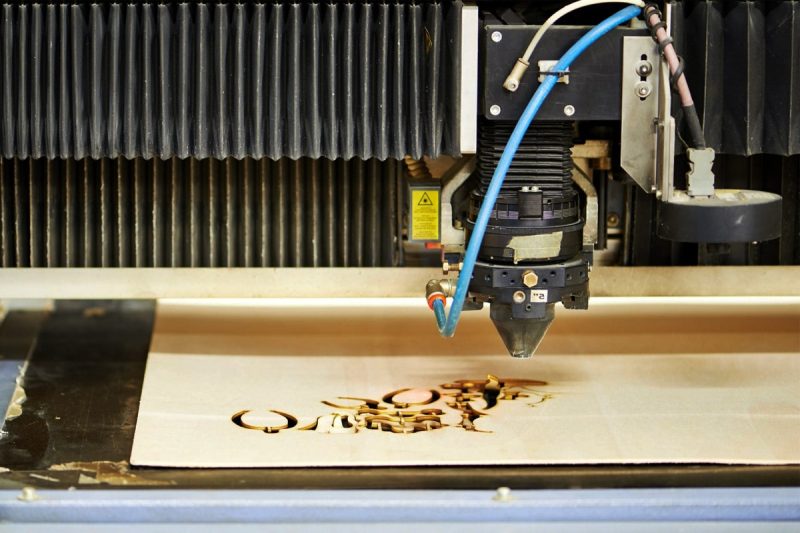
Estrategia de optimización para lograr un ancho de corte mínimo
Para lograr el ancho de corte mínimo en el corte por láser de CO2, se deben considerar múltiples estrategias de optimización. Estas estrategias no solo mejoran la precisión del corte, sino que también reducen eficazmente el desperdicio de material y mejoran la eficiencia de la producción. Los siguientes son los métodos de optimización clave para lograr el ancho de corte mínimo:
Optimice el sistema óptico: La calidad del sistema óptico afecta directamente el efecto de enfoque del haz láser, lo que a su vez afecta la precisión de la incisión. Seleccionar una lente óptica de alta calidad puede garantizar que el haz láser se enfoque uniformemente sobre la superficie del material objetivo, obteniendo así un corte estable y preciso. El uso de una lente de distancia focal corta (como una de 2,5 pulgadas) es una estrategia importante para optimizar el enfoque del haz láser. Una lente de distancia focal corta puede enfocar un diámetro de punto más pequeño, reduciendo así la difusión del haz láser y reduciendo considerablemente el ancho de la incisión. Un punto más pequeño no solo mejora la precisión de corte, sino que también reduce el impacto térmico en el material y garantiza la estabilidad durante el proceso de corte.
Ajuste preciso de la potencia y la velocidad del láser: La potencia del láser y la velocidad de corte son dos factores importantes que afectan el ancho de la incisión. El mejor efecto de corte se puede lograr ajustando con precisión la combinación de potencia y velocidad del láser. El modo de pulso puede reducir el tiempo de calentamiento continuo, reduciendo así la zona afectada por el calor (ZAC) y reduciendo el fenómeno de fusión en el borde de la incisión. El modo de pulso hace que la distribución de la energía láser sea más uniforme y evita el problema de sobrecalentamiento causado por la salida continua de alta potencia. Al mismo tiempo, ajustar la potencia del láser en combinación con el espesor del material puede asegurar que el haz láser pueda penetrar completamente el material y controlar el ancho de la incisión. Para materiales más delgados, reduzca la potencia adecuadamente para evitar la acumulación excesiva de calor; para materiales más gruesos, aumente la potencia adecuadamente para garantizar la calidad del corte, pero preste atención al control del ancho de la incisión.
Ajuste de los parámetros del gas auxiliar: El gas auxiliar desempeña un papel fundamental en el corte por láser de CO2. No solo ayuda a eliminar la masa fundida producida durante el corte, sino que también controla la calidad del mismo optimizando la presión del gas. Aumentar adecuadamente la presión del gas permite eliminar eficazmente la escoria producida durante el corte y evitar que se adhiera al borde de la incisión, manteniendo así un ancho de corte estrecho. Al seleccionar un gas auxiliar, el nitrógeno es uno de los más utilizados, especialmente para materiales que necesitan reducir la oxidación y mejorar el acabado del corte. El nitrógeno no solo reduce eficazmente la oxidación de la superficie del material, sino que también mantiene la suavidad de la incisión durante el proceso de corte, obteniendo así un resultado de corte de mayor calidad.
Optimice el software y los parámetros CNC: Los sistemas CNC de alta precisión pueden mejorar eficazmente la precisión del corte láser y ayudar a reducir las desviaciones de corte causadas por errores mecánicos. Con sistemas CNC avanzados, puede optimizar la trayectoria de corte y reducir los errores causados por cambios en la dirección del haz láser. Una planificación precisa de la trayectoria ayuda a reducir los errores causados por giros y trayectorias irregulares durante el corte. Además, el uso de un sistema de enfoque automático es una estrategia importante para optimizar el ancho de incisión. El sistema de enfoque automático puede ajustar automáticamente la posición del enfoque del láser según el grosor, la forma y los requisitos de corte del material para garantizar que el haz láser siempre se enfoque en la posición óptima, evitando así incisiones irregulares o demasiado anchas debido a una posición de enfoque incorrecta.
Reducir la zona afectada por el calor (ZAC): El tamaño de la ZAC está estrechamente relacionado con la acumulación de calor durante el proceso de corte láser. Un calor excesivo puede provocar una fusión excesiva de la superficie del material, aumentando así el ancho de la incisión y afectando la calidad del corte. Para reducir la zona afectada por el calor, el corte a alta velocidad es una estrategia eficaz. Este corte acelera el movimiento del rayo láser, reduciendo así la acumulación de calor en la superficie del material y evitando la fusión y el ensanchamiento del borde de la incisión. Sin embargo, al utilizar el corte a alta velocidad, es necesario garantizar que la energía del rayo láser sea suficiente para penetrar el material. Para optimizar aún más la calidad del corte, se pueden combinar tecnologías de refrigeración, como la refrigeración por pulverización o la inyección dual de gas, que pueden reducir eficazmente la temperatura del área de corte, evitar el sobrecalentamiento y garantizar un corte más preciso y estable.
Al combinar las estrategias de optimización mencionadas, los fabricantes pueden lograr eficazmente el ancho de corte mínimo en el corte por láser de CO2. Gracias al avance continuo de la tecnología y la optimización continua de los equipos, estas estrategias contribuirán a mejorar la precisión de corte, reducir el desperdicio de material y optimizar la eficiencia de la producción.
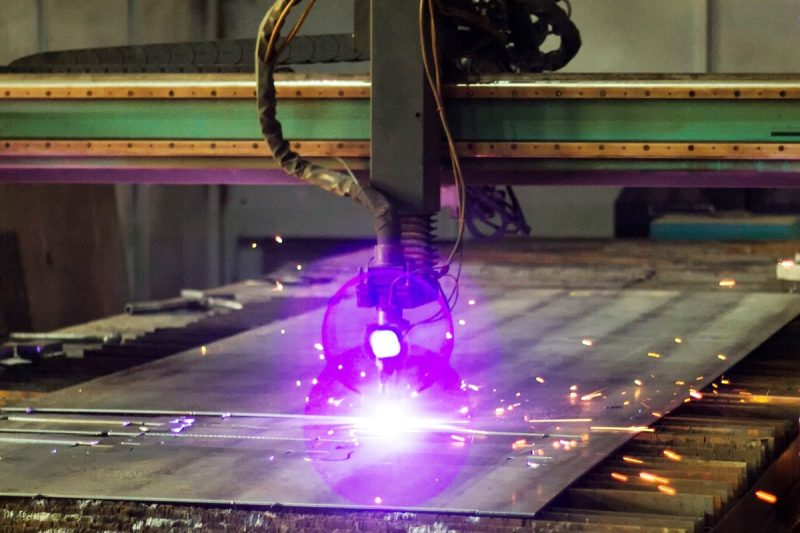
Resumir
Lograr el ancho de corte mínimo no es solo un simple ajuste de parámetros, sino un proceso que requiere una consideración exhaustiva de muchos factores. Al optimizar con precisión el enfoque del láser, la potencia, la velocidad de corte, el tipo y la presión del gas auxiliar, y el control del software, los fabricantes pueden maximizar la eficiencia de la producción y reducir el desperdicio de material, garantizando al mismo tiempo la calidad del corte. Un ajuste preciso del enfoque del láser permite asegurar el tamaño del punto de corte y evitar zonas con exceso de calor durante el proceso, garantizando así un corte fino y uniforme. La combinación precisa de potencia y velocidad de corte evita la acumulación excesiva de calor y reduce el impacto de la masa fundida en el ancho de corte. El gas auxiliar adecuado no solo elimina la escoria, sino que también previene la oxidación, mejorando aún más la calidad del corte. Al mismo tiempo, el uso de software CNC avanzado y tecnología de enfoque automático permite optimizar continuamente la trayectoria de corte y el enfoque del haz láser para garantizar la estabilidad y consistencia del corte.
Con el continuo desarrollo tecnológico, el rendimiento y la precisión de control de las máquinas de corte láser de CO2 también mejoran constantemente. Los fabricantes pueden lograr cortes más precisos mediante el ajuste y la optimización continuos de los factores mencionados, junto con el avance continuo de la tecnología óptica, los sistemas de control automatizados y la tecnología de refrigeración eficiente. En definitiva, lograr el ancho de incisión mínimo no solo mejora la precisión de corte, sino que también aumenta la eficiencia de producción, reduce los costos de material y mejora significativamente los beneficios económicos de la línea de producción a largo plazo. Por lo tanto, para los usuarios de Máquinas de corte por láser de CO2El aprendizaje continuo y el dominio de estas estrategias de optimización serán la clave para mejorar la capacidad de producción general y la competitividad.
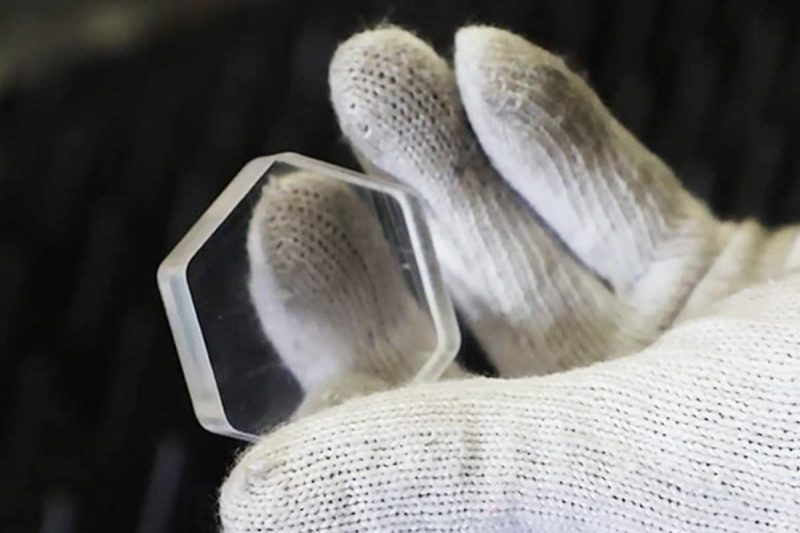
Obtenga soluciones láser
Láser AccTek Proporciona equipos de corte por láser de CO2 de alta precisión que admiten enfoque inteligente, optimización automática de la trayectoria y control eficiente del gas auxiliar para garantizar el ancho de incisión mínimo y lograr un procesamiento preciso. Contáctenos ¡Obtenga soluciones de corte por láser personalizadas para mejorar su eficiencia de producción y precisión de procesamiento!
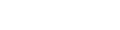
Información del contacto
- [email protected]
- [email protected]
- +86-19963414011
- No. 3 Zona A, Zona Industrial de Lunzhen, Ciudad de Yucheng, Provincia de Shandong.
Obtenga soluciones láser