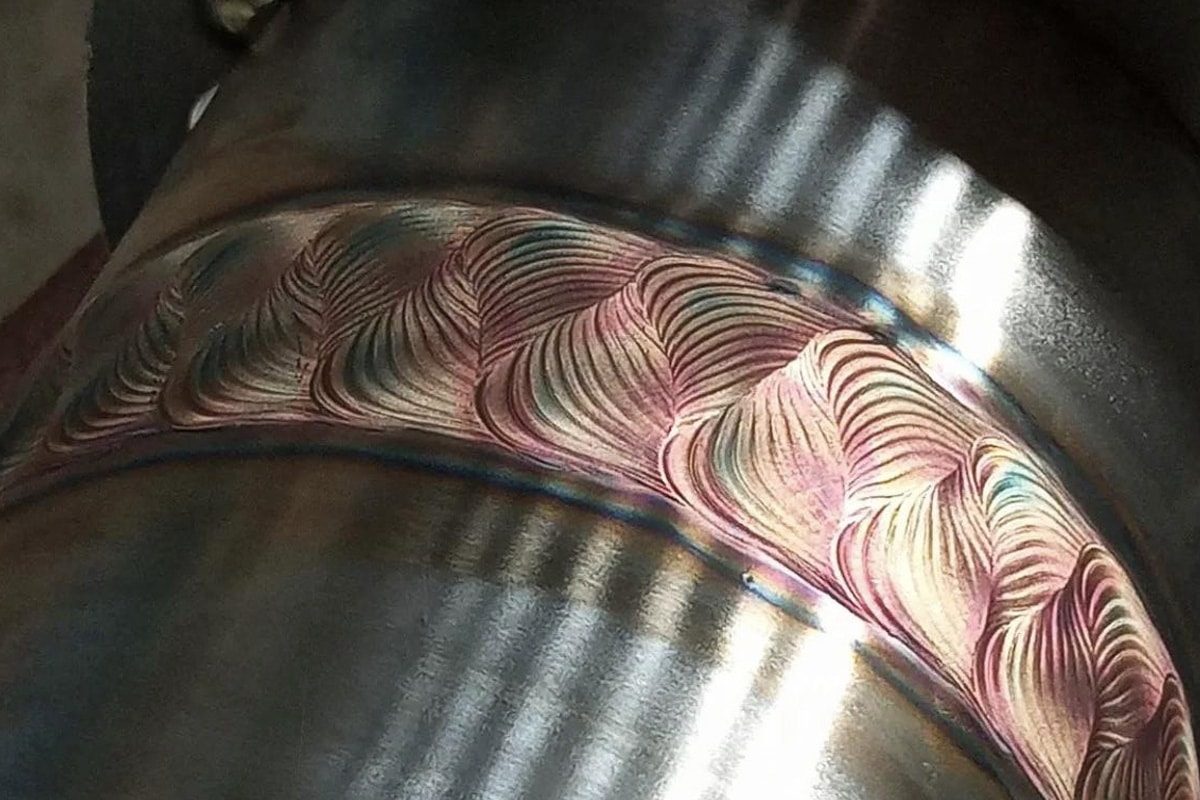
¿Cómo minimizar la distorsión y la deformación de la soldadura láser?
La soldadura láser ha revolucionado la fabricación moderna, ofreciendo una precisión, eficiencia y versatilidad inigualables en todas las industrias. Desde componentes automotrices y aeroespaciales hasta dispositivos médicos y electrónicos, la soldadura láser proporciona una solución de alta velocidad y alta calidad para unir metales. Sin embargo, a pesar de sus muchas ventajas, la soldadura láser no es inmune a los desafíos comunes de la soldadura, como la distorsión y la deformación. Estos problemas, causados por un calentamiento y enfriamiento desiguales durante el proceso de soldadura, pueden comprometer la precisión dimensional, la integridad mecánica y el atractivo estético de los componentes soldados.
Minimizar la distorsión y la deformación es fundamental para garantizar la calidad del producto, reducir el desperdicio de material y mantener la eficiencia de la fabricación. Para lograrlo, es necesario comprender en profundidad los factores que contribuyen a las tensiones térmicas, así como implementar técnicas optimizadas y tecnologías avanzadas. Este artículo explora las causas de la distorsión en la soldadura láser y ofrece estrategias prácticas para que los fabricantes mitiguen estos desafíos y obtengan soldaduras sin distorsión para aplicaciones de alto rendimiento.
Tabla de contenido
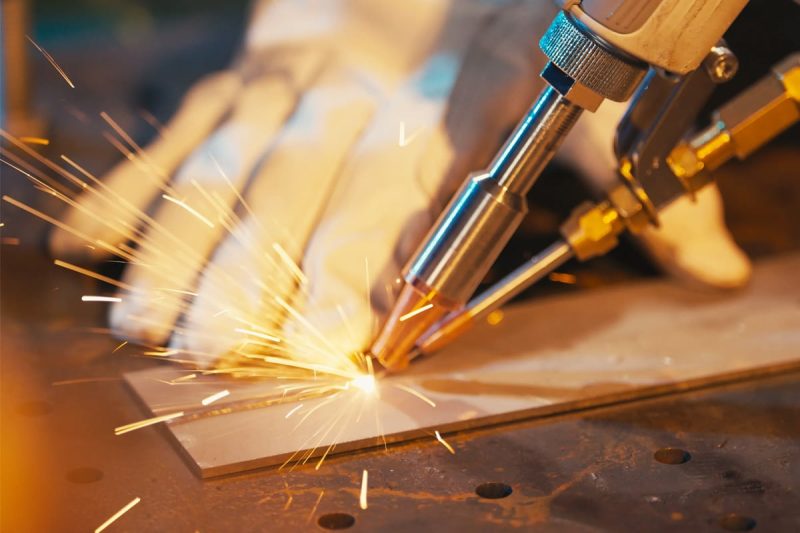
Comprensión de la distorsión y deformación de la soldadura láser
La soldadura láser, conocida por su precisión y eficiencia, aún puede producir distorsiones y deformaciones, lo que pone en riesgo la integridad estructural y la calidad de los componentes soldados. Estas deformaciones se deben a diversos factores, incluidos los efectos térmicos, las propiedades del material y el tipo de distorsión que se produce durante el proceso de soldadura. Comprender estos aspectos puede ayudar a minimizar la distorsión y garantizar soldaduras de alta calidad.
Efectos térmicos durante la soldadura
La soldadura láser implica la aplicación rápida de calor concentrado en una zona localizada, lo que crea gradientes térmicos pronunciados. A medida que el material se calienta, se expande y, durante el enfriamiento, se contrae. La naturaleza localizada de este proceso suele provocar una expansión y contracción térmica desigual, lo que genera tensiones residuales en el material.
Los efectos térmicos clave incluyen:
- Expansión y contracción térmica: el calentamiento rápido expande el material de manera desigual, mientras que el enfriamiento rápido crea fuerzas de contracción que distorsionan la pieza de trabajo.
- Zona afectada por el calor (ZAT): El área que rodea la soldadura está sujeta a ciclos térmicos que alteran su microestructura, provocando a menudo tensiones adicionales.
- Velocidades de enfriamiento: Las velocidades de enfriamiento más rápidas pueden generar deformaciones más significativas debido a una contracción térmica abrupta.
Propiedades del material que afectan la distorsión
El comportamiento de los materiales durante la soldadura láser está influenciado en gran medida por sus propiedades físicas y térmicas. Estas propiedades determinan cómo se absorbe, conduce y disipa el calor, lo que afecta el grado de distorsión y deformación.
Las propiedades clave del material incluyen:
- Conductividad térmica: Materiales como el aluminio, con alta conductividad térmica, disipan el calor rápidamente, reduciendo los gradientes térmicos pero requiriendo mayor potencia láser.
- Coeficiente de expansión térmica (CTE): Los materiales con un CTE más alto, como las aleaciones de aluminio, experimentan una mayor expansión y contracción, lo que aumenta la probabilidad de distorsión.
- Módulo elástico: Los materiales con un módulo elástico más bajo son más propensos a deformarse bajo estrés térmico.
- Capacidad calorífica específica: Los materiales con alta capacidad calorífica absorben más energía antes de cambiar la temperatura, lo que afecta la distribución de la entrada de calor.
Tipos de distorsión en la soldadura
La distorsión durante la soldadura láser se manifiesta de varias formas, según el material, el diseño de la unión y los parámetros de soldadura. Los tipos más comunes incluyen:
- Contracción longitudinal: se produce a lo largo de la costura de soldadura debido a la contracción durante el enfriamiento, acortando el material longitudinalmente.
- Contracción transversal: Esto ocurre perpendicularmente a la costura de soldadura, provocando que el material se contraiga lateralmente.
- Distorsión angular: causada por una distribución desigual del calor entre los bordes de la unión, lo que produce un desplazamiento angular.
- Pandeo: Los materiales delgados pueden deformarse o doblarse debido al aporte excesivo de calor, lo que genera una pieza de trabajo inestable.
- Distorsión rotacional: se encuentra en piezas circulares o curvas donde las tensiones térmicas inducen torsión.
Al analizar y comprender la interacción de los efectos térmicos, las propiedades del material y los tipos de distorsión, los fabricantes pueden implementar estrategias para mitigar estos desafíos y producir soldaduras de alta calidad y sin distorsión.
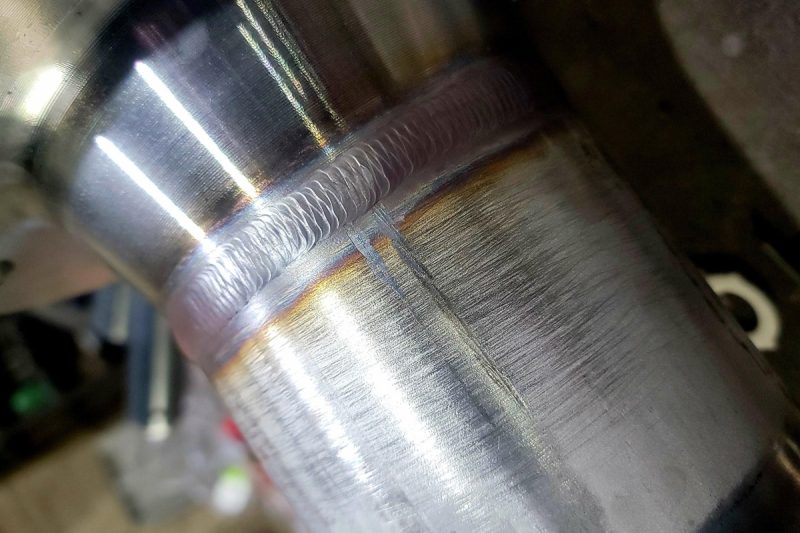
Materiales propensos a deformarse y deformarse después de la soldadura
El grado de distorsión y deformación después de la soldadura láser depende de las propiedades físicas y térmicas del material. Algunos materiales son inherentemente más susceptibles debido a sus índices de expansión térmica, conductividad y características mecánicas. Comprender qué materiales son propensos a la distorsión ayuda a los fabricantes a adoptar estrategias personalizadas para minimizar estos efectos.
Aluminio y aleaciones de aluminio
El aluminio es muy propenso a la distorsión debido a su bajo punto de fusión y alto coeficiente de expansión térmica (CTE). Estas características provocan una importante expansión térmica durante la soldadura y una rápida contracción al enfriarse. Además, la alta conductividad térmica del aluminio disipa el calor rápidamente, lo que requiere un mayor aporte de energía, lo que puede exacerbar los gradientes térmicos y provocar deformaciones.
Principales desafíos:
- Un CTE alto provoca una expansión y contracción pronunciadas.
- Las secciones delgadas son particularmente propensas a deformarse o distorsionarse angularmente.
- La rápida disipación del calor produce perfiles térmicos desiguales.
Estrategias de minimización:
- Utilice accesorios y abrazaderas para restringir el movimiento.
- Optimice la velocidad de soldadura y la potencia del láser para controlar la entrada de calor.
- Precaliente los componentes para reducir los gradientes térmicos.
Acero inoxidable
El CTE relativamente alto y la baja conductividad térmica del acero inoxidable pueden hacerlo propenso a la distorsión, especialmente en secciones delgadas. La mala disipación del calor del material a menudo da como resultado tensiones térmicas concentradas cerca de la zona de soldadura, lo que provoca contracción y distorsión angular.
Principales desafíos:
- El calor concentrado en la zona de soldadura aumenta las tensiones residuales.
- Susceptible a distorsión angular y transversal en secciones delgadas.
- Los cambios en la microestructura en la zona afectada por el calor (ZAT) pueden amplificar las tensiones.
Estrategias de minimización:
- Equilibre la potencia y la velocidad del láser para controlar la entrada de calor.
- Utilice diseños de juntas simétricas para distribuir el calor de manera uniforme.
- Utilice técnicas de soldadura por retroceso o por saltos para permitir el enfriamiento entre pasadas.
Aceros con alto contenido de carbono
Los aceros con alto contenido de carbono son susceptibles a la distorsión debido a su alta expansión térmica y al potencial de cambios significativos en la microestructura durante la soldadura. El enfriamiento rápido de los aceros con alto contenido de carbono puede introducir tensiones residuales, lo que provoca deformaciones o grietas.
Principales desafíos:
- Alto riesgo de expansión y contracción térmica durante la soldadura.
- El enfriamiento rápido aumenta las tensiones residuales.
- Los cambios microestructurales pueden provocar fragilidad y deformación.
Estrategias de minimización:
- Precalentar y controlar las velocidades de enfriamiento para reducir las tensiones térmicas.
- Utilice técnicas de soldadura por pulsos para minimizar la entrada de calor.
- Optimice el ajuste de las juntas para reducir los espacios y el calentamiento desigual.
Chapas finas de metal
Independientemente del tipo de material, las láminas metálicas delgadas son especialmente propensas a la distorsión porque carecen de la rigidez necesaria para resistir las tensiones térmicas. Incluso un aporte mínimo de calor durante la soldadura láser puede provocar deformaciones u ondulaciones.
Principales desafíos:
- Rigidez limitada para contrarrestar tensiones térmicas.
- Mayor susceptibilidad a la distorsión angular y al pandeo.
- La rápida absorción y disipación del calor amplifican los gradientes térmicos.
Estrategias de minimización:
- Utilice sujeciones y fijaciones rígidas para mantener la forma.
- Reducir la entrada de calor aumentando la velocidad de soldadura o utilizando láseres pulsados.
- Utilice barras de respaldo o disipadores de calor para estabilizar la pieza de trabajo.
Titanio y aleaciones de titanio
El titanio presenta una susceptibilidad moderada a la distorsión debido a su CTE relativamente alto y su baja conductividad térmica. Si bien es menos propenso a deformarse en comparación con el aluminio o el acero fino, un control inadecuado del calor durante la soldadura puede provocar una distorsión angular o longitudinal.
Principales desafíos:
- La baja disipación de calor aumenta las tensiones térmicas localizadas.
- La alta reactividad con el oxígeno durante la soldadura puede agravar la deformación.
- Sensible al sobrecalentamiento y a la exposición prolongada a altas temperaturas.
Estrategias de minimización:
- Utilice gas protector para mantener la calidad de la soldadura y minimizar los efectos térmicos.
- Utilice accesorios de precisión para mantener las piezas en su lugar.
- Optimice los parámetros de soldadura para una entrada de calor controlada.
Cobre y aleaciones de cobre
La alta conductividad térmica del cobre dificulta su soldadura constante, ya que el calor se disipa rápidamente y crea gradientes térmicos desiguales. Sin embargo, su alto CTE lo hace susceptible a la distorsión cuando el aporte de calor es excesivo.
Principales desafíos:
- La disipación rápida del calor requiere una alta potencia del láser.
- Un CTE alto provoca una expansión y contracción significativa.
- El calentamiento desigual provoca deformaciones en geometrías complejas.
Estrategias de minimización:
- Utilice precalentamiento para reducir el gradiente térmico.
- Optimice el enfoque y la potencia del láser para garantizar una aplicación de calor constante.
- Utilice la monitorización en tiempo real para controlar la entrada de calor.
Acero inoxidable dúplex
Los aceros inoxidables dúplex son menos propensos a la distorsión que los aceros inoxidables austeníticos debido a su mayor rigidez. Sin embargo, la aplicación desigual del calor puede provocar distorsión angular y transversal, en particular en soldaduras asimétricas.
Principales desafíos:
- Un enfriamiento desigual puede generar tensiones residuales.
- Distorsión angular en geometrías complejas.
- Cambios microestructurales debidos al ciclo térmico.
Estrategias de minimización:
- Utilice técnicas de soldadura equilibradas para distribuir el calor uniformemente.
- Controle las temperaturas entre pasos para evitar un enfriamiento desigual.
- Utilice soldadura láser con monitoreo en tiempo real para lograr precisión.
Los materiales propensos a la distorsión después de la soldadura comparten características comunes, como coeficientes de expansión térmica elevados, baja rigidez y sensibilidad al calentamiento desigual. Para abordar estos desafíos es necesario seleccionar cuidadosamente los parámetros de soldadura, las soluciones de fijación y las técnicas de control térmico. Al comprender el comportamiento de cada material bajo tensión térmica, los fabricantes pueden implementar estrategias personalizadas para lograr soldaduras sin distorsión y mantener la integridad de sus componentes.
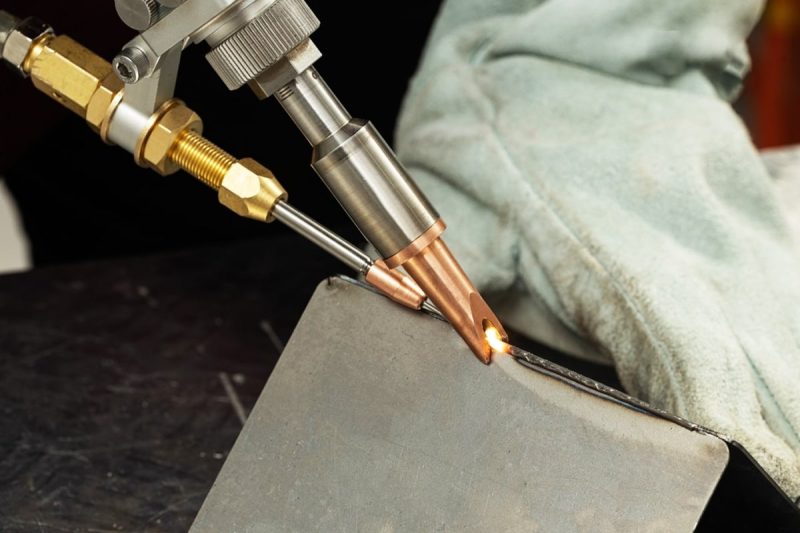
Factores que influyen en la distorsión y la deformación en la soldadura láser
La soldadura láser es un proceso preciso y eficiente, pero su aporte de calor localizado y su enfriamiento rápido pueden causar distorsión y deformación. Comprender los factores que contribuyen a estos desafíos puede ayudar a implementar estrategias efectivas para minimizarlos.
Entrada de calor y gradientes térmicos
El aporte de calor durante la soldadura láser y los gradientes térmicos resultantes juegan un papel fundamental a la hora de determinar el grado de distorsión y deformación.
- Entrada de calor localizada: la soldadura láser concentra un calor intenso en una zona pequeña, lo que crea gradientes de temperatura pronunciados. Estos gradientes provocan una expansión y contracción desiguales del material, lo que genera tensiones residuales.
- Entrada de calor excesiva: si la potencia del láser es demasiado alta o la velocidad de soldadura demasiado lenta, la entrada de calor excesiva puede agrandar la zona afectada por el calor (ZAT) y amplificar la distorsión.
- Enfriamiento rápido: La soldadura láser a menudo implica un enfriamiento rápido, lo que puede crear cambios abruptos de temperatura y aumentar el riesgo de deformación.
Estrategias de mitigación:
- Optimice la potencia del láser y la velocidad de soldadura para equilibrar la entrada de calor y minimizar los gradientes térmicos.
- Utilice técnicas de soldadura por pulsos para controlar el suministro de calor y reducir el calentamiento excesivo.
- Utilice imágenes térmicas o sistemas de monitoreo en tiempo real para rastrear y ajustar los perfiles de temperatura durante la soldadura.
Espesor del material y diseño de juntas
El espesor del material y el diseño de la junta de soldadura afectan significativamente el comportamiento de distorsión durante la soldadura láser.
- Espesor del material: los materiales delgados son más propensos a la distorsión debido a su baja rigidez y a su incapacidad para resistir tensiones térmicas. Los materiales más gruesos son menos susceptibles, pero pueden requerir una mayor potencia del láser, lo que aumenta la ZAT.
- Diseño de la junta: el tipo y el ajuste de la junta soldada influyen en la distribución del calor. Las juntas mal diseñadas pueden exacerbar los gradientes térmicos y provocar una expansión y contracción desiguales.
Tipos comunes de articulaciones y su impacto:
- Uniones a tope: generalmente minimizan la distorsión cuando están correctamente alineadas.
- Juntas traslapadas: pueden crear gradientes térmicos significativos, lo que provoca deformaciones.
- Juntas en T y juntas de esquina: Las geometrías más complejas pueden concentrar tensiones, aumentando los riesgos de distorsión.
Estrategias de mitigación:
- Seleccione diseños de juntas que promuevan la simetría y distribuyan el calor de manera uniforme.
- Asegúrese de que las juntas estén bien ajustadas para minimizar los espacios y el calentamiento desigual.
- Utilice técnicas de preparación de bordes, como el biselado, para mejorar la estabilidad de la unión y reducir la distorsión.
Sujeción y fijación
Una sujeción y fijación adecuadas son esenciales para mantener la pieza de trabajo en su lugar y contrarrestar las fuerzas que distorsionan la soldadura.
- Sujeción rígida: proporciona un soporte fuerte pero puede introducir tensiones residuales si se restringe demasiado.
- Sujeción flexible: permite cierto movimiento para reducir la acumulación de tensión, pero puede que no evite por completo la deformación.
- Disipadores de calor: Los accesorios que actúan como disipadores de calor pueden ayudar a disipar el calor, reduciendo los gradientes térmicos.
Efectos de una fijación inadecuada:
- Un soporte insuficiente permite que la pieza de trabajo se mueva o se deforme durante la soldadura.
- La restricción excesiva puede generar tensiones, lo que provoca deformaciones posteriores a la soldadura.
Estrategias de mitigación:
- Utilice accesorios robustos para mantener las piezas firmemente en su lugar sin restringirlas demasiado.
- Incorpore disipadores de calor en los accesorios para gestionar la disipación del calor.
- Utilice soldadura por puntos o soldadura secuencial para mantener la alineación durante el proceso.
Tasas de precalentamiento y enfriamiento
El ciclo térmico de precalentamiento y enfriamiento tiene un impacto significativo en el grado de distorsión y deformación en la soldadura láser.
- Precalentamiento: aumentar la temperatura de la pieza de trabajo antes de soldar reduce los gradientes térmicos, ya que el material se expande de manera más uniforme.
- Enfriamiento controlado: la gestión de la velocidad de enfriamiento evita contracciones abruptas que generan tensiones residuales y deformaciones.
Consideraciones clave:
- El precalentamiento es especialmente beneficioso para materiales con coeficientes de expansión térmica elevados, como el aluminio o los aceros con alto contenido de carbono.
- El sobrecalentamiento puede aumentar la ZAT e introducir cambios metalúrgicos no deseados.
- El enfriamiento no controlado puede exacerbar las concentraciones de tensión y aumentar la distorsión.
Estrategias de mitigación:
- Precaliente toda la pieza de trabajo de manera uniforme utilizando hornos o calentamiento por inducción para reducir las diferencias de temperatura.
- Controle las velocidades de enfriamiento con tratamientos térmicos posteriores a la soldadura o métodos de enfriamiento lento.
- Supervise las temperaturas durante el precalentamiento y el enfriamiento con termopares o sensores infrarrojos para garantizar la consistencia.
Para minimizar la distorsión y la deformación en la soldadura láser es necesario prestar especial atención a los factores que influyen en el aporte de calor, el comportamiento del material, el diseño de la unión y la gestión térmica. Al optimizar estos parámetros e incorporar técnicas de precalentamiento y sujeción eficaces, los fabricantes pueden reducir significativamente los riesgos de distorsión, lo que garantiza una mayor calidad de la soldadura y precisión dimensional.
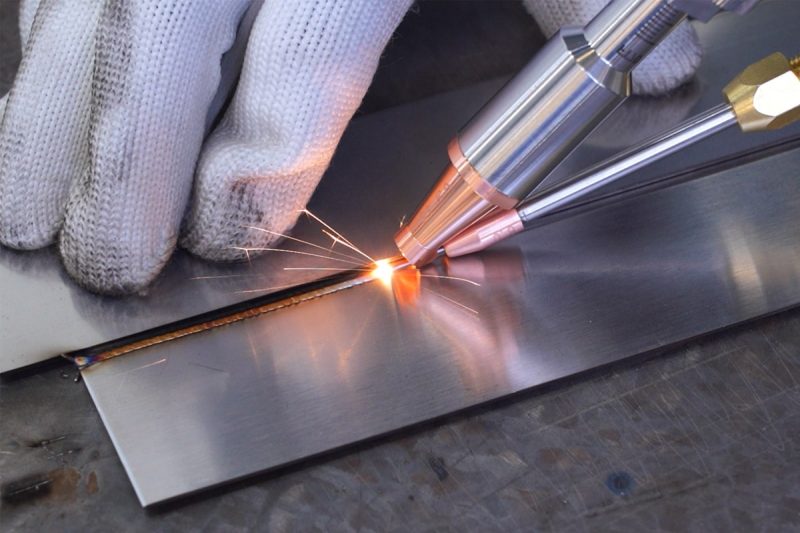
Métodos para minimizar la distorsión y la deformación en la soldadura láser
Para minimizar la distorsión y la deformación en la soldadura láser se requiere un enfoque estratégico que aborde la gestión del calor, el diseño de la unión, la preparación del material y las técnicas de soldadura.
Optimización de los parámetros de soldadura
El ajuste adecuado de los parámetros de soldadura es esencial para controlar la entrada de calor, minimizar los gradientes térmicos y reducir la distorsión.
- Ajuste de la potencia del láser: una potencia láser alta puede generar una entrada de calor excesiva y zonas afectadas por el calor (ZAT) más grandes. Optimice la potencia del láser para lograr una penetración suficiente y minimizar el calentamiento innecesario.
- Control de la velocidad de soldadura: las velocidades de soldadura lentas aumentan la entrada de calor, lo que genera una mayor distorsión. Las velocidades más rápidas reducen los gradientes térmicos, pero se debe tener cuidado para garantizar una fusión completa.
- Uso de láseres pulsados frente a láseres de onda continua: los láseres pulsados permiten la emisión intermitente de calor, lo que reduce la entrada total de calor y minimiza la distorsión. Los láseres de onda continua son más adecuados para aplicaciones de alta velocidad, pero pueden requerir estrategias de enfriamiento adicionales.
Consejos prácticos:
- Utilice pruebas para identificar configuraciones óptimas de potencia y velocidad para materiales específicos.
- Utilice imágenes termográficas para monitorear la distribución del calor durante la soldadura.
- Combine menor potencia con modos láser pulsados para materiales delgados o propensos a distorsiones.
Consideraciones sobre el diseño conjunto
El diseño y la preparación de las uniones soldadas influyen significativamente en la distribución del calor y las concentraciones de tensión.
- Cómo elegir el tipo de unión adecuado: las uniones simétricas, como las uniones a tope, ayudan a distribuir el calor de manera uniforme y reducen la distorsión. Las uniones traslapadas y las uniones en esquina, si bien son necesarias para ciertas aplicaciones, requieren un manejo cuidadoso para controlar la tensión.
- Preparación del borde: La preparación adecuada del borde, como el biselado o el mecanizado, garantiza ajustes ajustados y una aplicación de calor uniforme, lo que reduce el riesgo de calentamiento desigual y deformación.
Consejos prácticos:
- Utilice diseños de juntas que promuevan un flujo de calor uniforme.
- Minimice los espacios entre las juntas mediante un mecanizado preciso.
- Considere utilizar materiales de relleno de forma selectiva para cubrir espacios y mejorar la calidad de la soldadura.
Selección y preparación de materiales
Seleccionar materiales apropiados y garantizar su preparación para la soldadura puede reducir en gran medida la distorsión.
- Compatibilidad de materiales: utilice materiales con coeficientes de expansión térmica (CTE) más bajos o alta conductividad térmica para minimizar las tensiones térmicas.
- Limpieza de la superficie: los contaminantes como aceites, óxidos o suciedad afectan la absorción de calor y provocan un calentamiento desigual. Las superficies limpias garantizan una mejor consistencia de la soldadura y reducen la distorsión.
Consejos prácticos:
- Combine materiales base y rellenos para obtener propiedades térmicas y mecánicas similares.
- Utilice métodos de limpieza químicos o mecánicos para preparar las superficies.
- Precaliente materiales con alta expansión térmica para reducir los gradientes térmicos.
Uso de accesorios y sujeciones
Las técnicas de fijación y sujeción adecuadas evitan el movimiento durante la soldadura y gestionan la disipación del calor de forma eficaz.
- Técnicas de sujeción adecuadas: sujete firmemente la pieza de trabajo en su lugar para evitar distorsiones, pero evite sujetarla excesivamente, lo que puede causar tensiones residuales.
- Uso de barras de respaldo y disipadores de calor: las barras de respaldo sostienen el área de soldadura y reducen la distorsión al estabilizar el material, mientras que los disipadores de calor disipan el exceso de calor para controlar los gradientes térmicos.
Consejos prácticos:
- Diseñe accesorios personalizados para adaptarse a geometrías de piezas de trabajo específicas.
- Incorpora abrazaderas ajustables para mayor flexibilidad sin comprometer el soporte.
- Utilice materiales con alta conductividad térmica para respaldar barras o disipadores de calor para controlar la disipación del calor.
Precalentamiento y tratamiento térmico posterior a la soldadura
La gestión térmica antes y después de la soldadura reduce significativamente las tensiones residuales y la distorsión.
- Precalentamiento controlado: el precalentamiento de la pieza de trabajo reduce los gradientes térmicos, especialmente para materiales como el aluminio y el acero con alto contenido de carbono.
- Tratamiento térmico posterior a la soldadura: el enfriamiento gradual o el recocido para aliviar tensiones después de la soldadura reduce las tensiones residuales y estabiliza el material.
Consejos prácticos:
- Precaliente las piezas de trabajo de manera uniforme utilizando hornos, sopletes o calentadores de inducción.
- Controlar las velocidades de enfriamiento con mantas aislantes o tratamientos térmicos para evitar contracciones abruptas.
- Supervise las temperaturas mediante termopares para una gestión térmica constante.
Planificación de la secuencia de soldadura
La planificación estratégica de la secuencia de soldadura ayuda a distribuir el calor de manera uniforme y a controlar la acumulación de tensión.
- Soldadura equilibrada: las soldaduras alternas en lados opuestos de la pieza de trabajo equilibran la entrada de calor y minimizan la deformación.
- Técnicas de soldadura por saltos: suelde secciones intermitentes, permitiendo el enfriamiento entre soldaduras para evitar la acumulación excesiva de calor en cualquier área.
Consejos prácticos:
- Divida las soldaduras grandes en secciones más pequeñas para permitir un enfriamiento intermedio.
- Comience a soldar en áreas de bajo estrés y avance gradualmente hacia regiones de alto estrés.
- Utilice herramientas de software para simular la distribución de tensiones y optimizar las secuencias de soldadura.
Empleo de técnicas avanzadas
Las tecnologías de soldadura innovadoras ofrecen soluciones avanzadas para minimizar la distorsión y la deformación.
- Soldadura láser híbrida: combina la soldadura láser con otras técnicas como la soldadura por arco para mejorar la distribución del calor y reducir la distorsión.
- Soldadura láser adaptativa: utiliza sensores y sistemas de retroalimentación para ajustar los parámetros de soldadura en tiempo real en función de las condiciones del material y del proceso.
- Monitoreo y control en tiempo real: incorpora imágenes térmicas, retroalimentación de potencia láser y sensores de deformación para mantener condiciones de soldadura óptimas.
Consejos prácticos:
- Invierta en sistemas híbridos para aplicaciones complejas o de alta tolerancia.
- Utilice sistemas de monitorización en tiempo real para detectar y corregir desviaciones al instante.
- Implementar sistemas de control de circuito cerrado para mantener parámetros de soldadura consistentes.
Al implementar estos métodos, los fabricantes pueden minimizar eficazmente la distorsión y la deformación en los procesos de soldadura láser. La optimización de los parámetros de soldadura, el diseño de uniones adecuadas, la preparación de los materiales, el uso de los accesorios adecuados, la gestión de los ciclos térmicos y el aprovechamiento de tecnologías avanzadas contribuyen a lograr soldaduras de alta calidad y sin distorsión. Estas estrategias no solo mejoran la precisión dimensional de los componentes soldados, sino que también mejoran la eficiencia de la producción y reducen el desperdicio de material, lo que garantiza resultados de fabricación confiables y rentables.
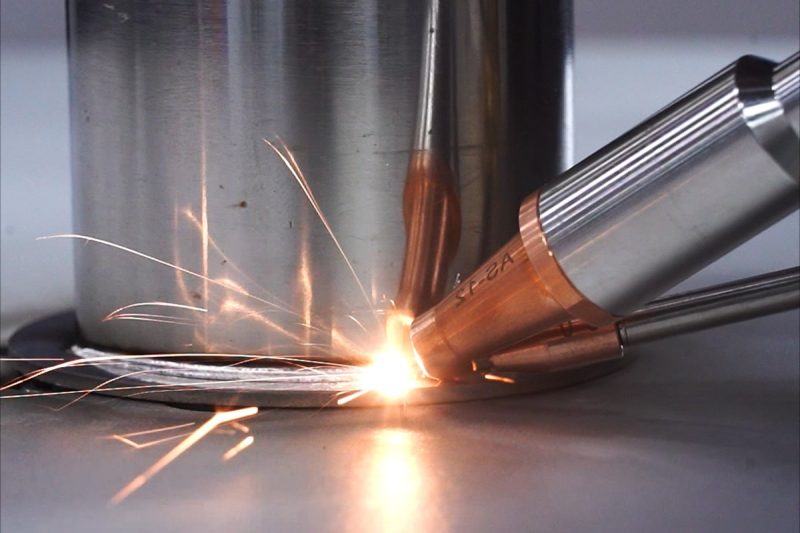
Resumen
Minimizar la distorsión y la deformación en la soldadura láser es fundamental para lograr soldaduras de alta calidad y mantener la integridad estructural de los componentes. La distorsión surge de un calentamiento y enfriamiento desiguales, lo que genera tensiones residuales que deforman el material. Al abordar factores clave como el aporte de calor, las propiedades del material, el diseño de las uniones y la gestión térmica, los fabricantes pueden mitigar estos desafíos de manera eficaz.
Optimizar los parámetros de soldadura, incluida la potencia y la velocidad del láser y el uso de láseres de onda continua o pulsada, es esencial para controlar la entrada de calor. El diseño de la unión, la selección del material y la preparación de la superficie adecuados mejoran aún más la calidad de la soldadura al garantizar una distribución uniforme del calor y reducir las tensiones térmicas. La sujeción eficaz, el uso de barras de soporte y disipadores de calor, y los tratamientos térmicos estratégicos de precalentamiento y possoldadura también desempeñan un papel fundamental. Las técnicas avanzadas como la soldadura láser híbrida, la monitorización en tiempo real y los sistemas de control adaptativo proporcionan herramientas adicionales para minimizar la distorsión.
Al integrar estas estrategias, los fabricantes pueden producir soldaduras precisas, confiables y sin distorsiones, mejorando la eficiencia y el rendimiento del producto.
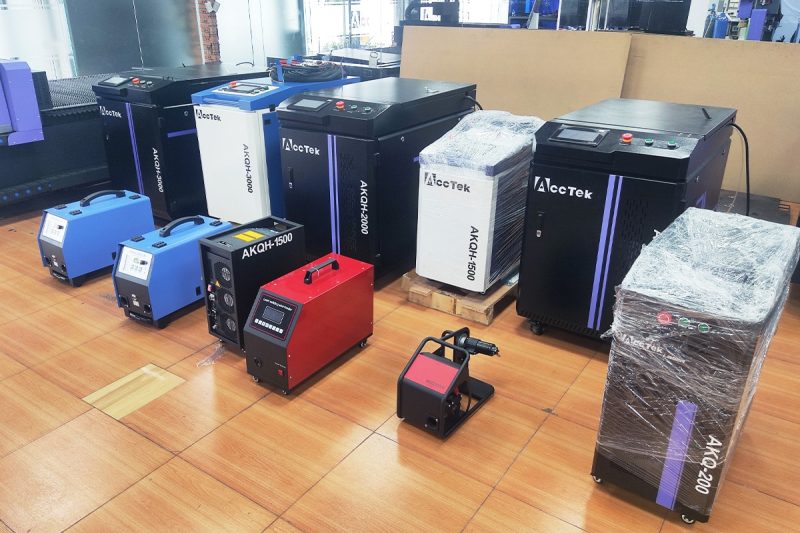
Obtenga soluciones de soldadura láser
En Láser AccTekEntendemos los desafíos que enfrentan los fabricantes para minimizar la distorsión y la deformación durante la soldadura láser. Como fabricante profesional de máquinas de corte por láser, máquinas de soldadura láser, máquinas de limpieza láser, y máquinas de marcado láserNos comprometemos a ofrecer soluciones de vanguardia adaptadas a sus necesidades. Nuestras avanzadas máquinas de soldadura láser están diseñadas para garantizar un control preciso del calor, lo que permite una soldadura sin distorsiones incluso en las aplicaciones más exigentes.
Con una gama de características personalizables, que incluyen configuraciones optimizadas de potencia láser, sistemas de monitoreo en tiempo real y tecnologías de soldadura adaptables, las máquinas de AccTek Laser brindan un rendimiento y una confiabilidad inigualables. Ya sea que trabaje con materiales delicados o geometrías complejas, nuestros expertos pueden guiarlo para seleccionar la mejor configuración para sus requisitos específicos.
Asóciese con AccTek Laser para superar los desafíos de la soldadura y mejorar la eficiencia de su producción. Contáctenos hoy mismo para obtener una consulta integral, soporte técnico y acceso a soluciones de soldadura láser líderes en la industria. Permítanos ayudarlo a lograr la perfección en cada soldadura.
Una sujeción y fijación adecuadas son esenciales para mantener la pieza de trabajo en su lugar y contrarrestar las fuerzas que distorsionan la soldadura.
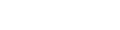
Información del contacto
- [email protected]
- [email protected]
- +86-19963414011
- No. 3 Zona A, Zona Industrial de Lunzhen, Ciudad de Yucheng, Provincia de Shandong.
Obtenga soluciones láser