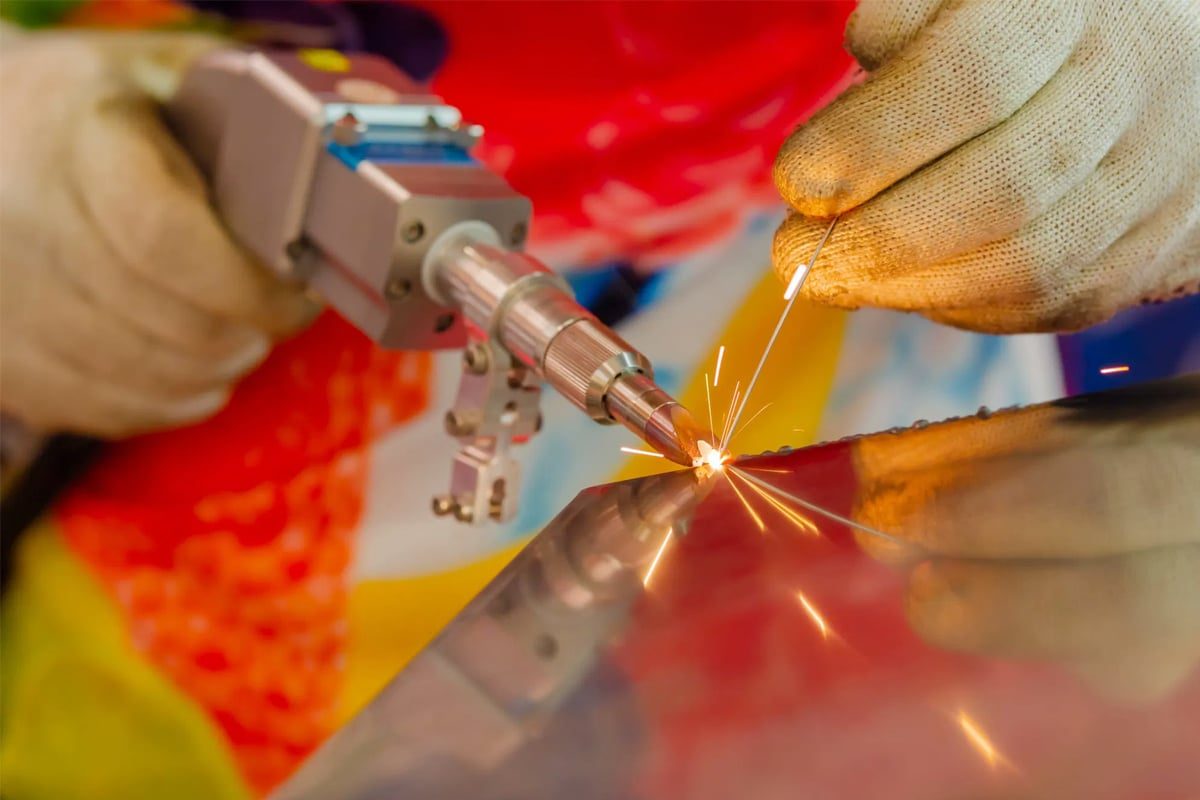
¿Cuáles son los factores que afectan el espesor de la soldadura láser?
En la soldadura láser, controlar el espesor de la soldadura es esencial para garantizar la resistencia, la durabilidad y la calidad estética de la unión. El espesor de una soldadura láser está influenciado por una variedad de factores, desde los ajustes del láser como la potencia, el enfoque del haz y la velocidad hasta las propiedades físicas y químicas del material que se está soldando. Además, el diseño de la unión, la elección del gas de protección y las condiciones ambientales en el espacio de trabajo desempeñan un papel fundamental a la hora de determinar la profundidad con la que el láser penetra en el material y el perfil general de la soldadura. Al optimizar estos factores, los fabricantes pueden lograr un espesor de soldadura preciso, lo que es especialmente importante en industrias donde la precisión y la consistencia son cruciales, como la automotriz, la aeroespacial y la electrónica. Este artículo explora las numerosas variables que afectan el espesor de la soldadura en la soldadura láser, ofreciendo información sobre cómo los ajustes en los parámetros del proceso y los materiales pueden afectar la profundidad y la calidad de la soldadura.
Tabla de contenido
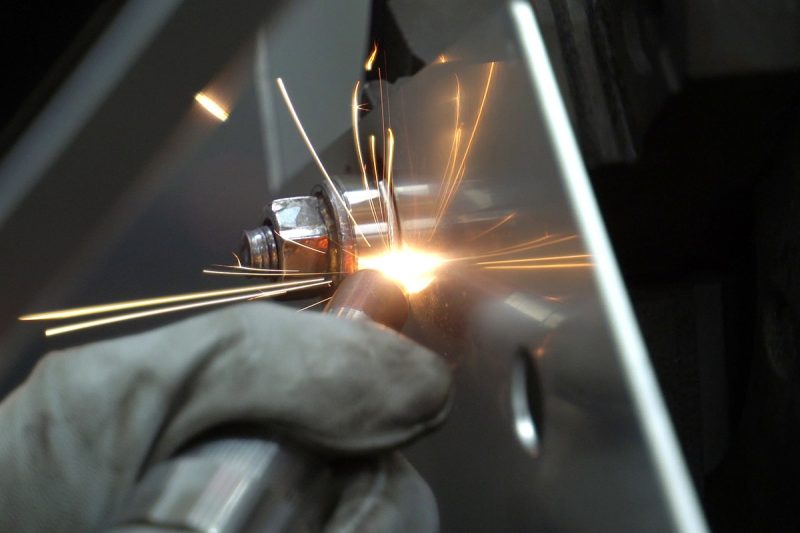
Comprensión de la soldadura láser
La soldadura láser se basa en un haz láser enfocado como fuente de calor intenso para unir materiales, principalmente metales. El haz láser, que normalmente se produce mediante una fuente láser como un láser de fibra, CO2 o de estado sólido, se enfoca en la superficie del material. La intensa energía del láser calienta y funde rápidamente el área objetivo, creando un baño de fusión que fusiona las piezas. A medida que el láser se mueve a lo largo de la unión, el baño de fusión se solidifica, lo que da como resultado una soldadura continua.
La alta densidad de energía del láser permite una penetración precisa y profunda con mínimas zonas afectadas por el calor (ZAT), lo que reduce la distorsión térmica en comparación con los métodos de soldadura convencionales. La soldadura láser se puede realizar en diferentes entornos, incluidas cámaras de vacío, atmósferas de gas inerte o al aire libre, según la aplicación específica y los requisitos del material. Esta versatilidad y precisión hacen que la soldadura láser sea muy eficaz para geometrías complejas y materiales con propiedades térmicas variables.
Conceptos básicos del proceso de soldadura láser
El proceso de soldadura láser generalmente implica tres etapas principales: preparación previa a la soldadura, interacción láser-material y enfriamiento y solidificación posteriores a la soldadura.
- Preparación previa a la soldadura: antes de soldar, las superficies de los materiales deben estar limpias, libres de contaminantes y correctamente alineadas. Los contaminantes como aceites, óxidos o residuos pueden interferir con la absorción de energía y reducir la calidad de la soldadura.
- Interacción láser-material: durante la soldadura, el haz láser se enfoca sobre la pieza de trabajo, donde su energía es absorbida por la superficie, lo que provoca una fusión localizada. Existen dos modos principales de interacción láser-material:
- Soldadura por conducción: se produce cuando la densidad de potencia del láser es relativamente baja, lo que provoca la fusión de la superficie sin vaporización. El calor se conduce hacia el material, lo que da como resultado soldaduras superficiales y anchas. Este modo se utiliza a menudo para aplicaciones que priorizan la estética y el bajo aporte de calor.
- Soldadura en ojo de cerradura: cuando la densidad de potencia del láser es lo suficientemente alta como para vaporizar el material, se forma un ojo de cerradura o cavidad de vapor dentro del baño de fusión. El ojo de cerradura permite que la energía del láser penetre profundamente, creando soldaduras estrechas y profundas con una alta relación de aspecto. La soldadura en ojo de cerradura es adecuada para materiales gruesos y aplicaciones que requieren uniones resistentes.
- Enfriamiento y solidificación posteriores a la soldadura: a medida que el láser se desplaza a lo largo de la junta de soldadura, el baño de fusión se solidifica y forma una unión continua entre los materiales. La velocidad de enfriamiento adecuada puede evitar defectos como grietas o tensiones residuales y lograr las propiedades mecánicas deseadas de la soldadura.
La soldadura láser ofrece alta precisión, mínima distorsión y la capacidad de producir uniones limpias y robustas. Sin embargo, factores como la potencia del láser, el enfoque del haz, la velocidad de soldadura y las características del material deben controlarse cuidadosamente para lograr el espesor y la calidad de soldadura deseados, lo que hace que la soldadura láser sea un proceso complejo y altamente adaptable para la fabricación moderna.
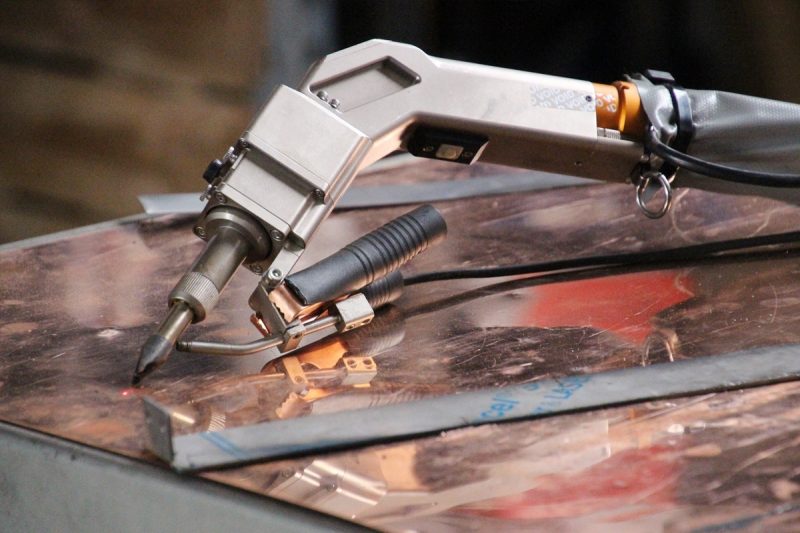
Aplicaciones de la soldadura láser
La soldadura láser se ha convertido en una tecnología fundamental en numerosas industrias debido a su precisión, velocidad y capacidad para producir soldaduras uniformes y de alta calidad con una distorsión térmica mínima. A medida que evolucionan las demandas de fabricación, la versatilidad y adaptabilidad de la soldadura láser siguen convirtiéndola en una herramienta invaluable.
- Industria automotriz: En el sector automotriz, la soldadura láser se utiliza ampliamente para ensamblar carrocerías, componentes de motores, engranajes de transmisión, sistemas de escape y módulos de baterías para vehículos eléctricos. El proceso permite realizar uniones resistentes y de alta precisión, al tiempo que minimiza el peso de los componentes. La capacidad de la soldadura láser para unir materiales diferentes, como el aluminio y el acero, la hace especialmente útil para diseños de vehículos livianos y energéticamente eficientes.
- Industria aeroespacial: La soldadura láser es vital en la industria aeroespacial debido a su capacidad para crear uniones precisas y de alta resistencia para componentes críticos como álabes de turbinas, marcos estructurales y tanques de combustible. Su zona mínima afectada por el calor ayuda a mantener la integridad estructural de materiales aeroespaciales livianos y sensibles al calor, como aleaciones de titanio y compuestos. La precisión de la soldadura láser garantiza el cumplimiento de estrictos estándares de seguridad y rendimiento.
- Energía y generación de energía: En el sector energético, la soldadura láser se utiliza para fabricar componentes para turbinas eólicas, paneles solares, equipos de petróleo y gas y plantas de energía nuclear. La capacidad de producir soldaduras resistentes y sin defectos garantiza la fiabilidad y la seguridad en entornos de alta presión y alta temperatura. La soldadura láser también respalda la fabricación de intercambiadores de calor, tuberías y recipientes de alta presión.
- Construcción naval e industria marina: La industria de la construcción naval se beneficia de la capacidad de la soldadura láser para producir soldaduras fuertes y resistentes a la corrosión. Se utiliza para unir placas de acero estructural, componentes del casco y accesorios interiores. El proceso reduce el peso total de los buques marinos, aumenta la eficiencia del combustible y permite realizar diseños complejos con alta precisión.
- Electrónica de consumo y electrodomésticos: La soldadura láser se emplea en el ensamblaje de productos electrónicos de consumo, como teléfonos inteligentes, tabletas y electrodomésticos. Garantiza uniones confiables y estéticamente atractivas en carcasas de metal, conectores y paquetes de baterías. El proceso respalda las líneas de producción automatizadas de alta velocidad, lo que mejora la productividad y la consistencia.
- Industria de alimentos y bebidas: La soldadura láser se utiliza en la industria de alimentos y bebidas para producir equipos de acero inoxidable, como tuberías, equipos de cervecería y máquinas de llenado. Las soldaduras higiénicas y sin costuras producidas por la soldadura láser evitan el crecimiento bacteriano y simplifican los procesos de limpieza, lo que la hace ideal para aplicaciones de grado alimenticio.
- Construcción y arquitectura: La soldadura láser se utiliza en los sectores de la construcción y la arquitectura para crear estructuras metálicas resistentes y estéticamente agradables. Se utiliza para fabricar vigas estructurales, elementos decorativos, fachadas, etc. La precisión y velocidad del proceso permiten la creación de diseños personalizados y geometrías complejas.
- Agricultura y maquinaria pesada: La industria agrícola depende de la soldadura láser para fabricar componentes robustos para maquinaria y equipos, como arados, tractores y cargadores. Las uniones soldadas con láser brindan alta resistencia y durabilidad para soportar duras condiciones operativas.
Las diversas aplicaciones de la soldadura láser en distintas industrias ponen de relieve su papel como herramienta fundamental para la fabricación y la ingeniería modernas. La capacidad de controlar el espesor y la calidad de las soldaduras con precisión garantiza que la soldadura láser cumpla con las exigentes demandas de productos de alto rendimiento, conjuntos complejos y normas regulatorias estrictas.
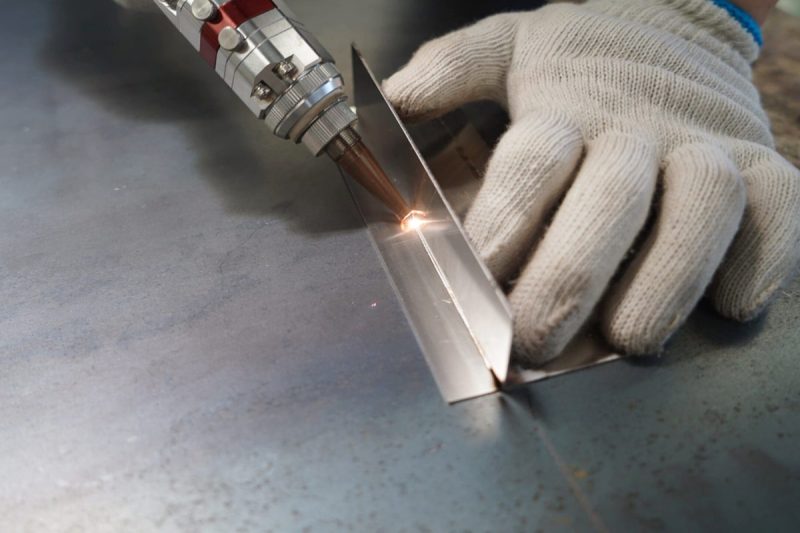
Factores que afectan el espesor de la soldadura láser
Lograr el espesor deseado en la soldadura láser es un proceso complejo en el que influyen numerosos factores. Cada uno de estos factores afecta directamente la profundidad de penetración, la calidad y la integridad de la soldadura. Comprender estas variables permite a los fabricantes adaptar el proceso de soldadura láser para lograr espesor, resistencia y precisión óptimos.
Potencia láser
- Impacto en el espesor de la soldadura: la potencia del láser es uno de los factores más críticos para determinar el espesor de la soldadura. Una mayor potencia del láser aumenta el aporte de energía, lo que permite una penetración más profunda y soldaduras más gruesas. Por el contrario, los niveles de potencia más bajos producen soldaduras menos profundas, que pueden ser más adecuadas para materiales delgados o aplicaciones donde se requiere un aporte mínimo de calor.
- Optimización: el ajuste de la potencia del láser según el espesor del material y la profundidad de penetración deseada garantiza un uso eficaz de la energía. Para materiales más gruesos o soldaduras profundas, se debe aplicar suficiente potencia para lograr la penetración necesaria sin causar zonas afectadas por el calor (ZAT) excesivas.
Velocidad de soldadura
- Impacto en el espesor de la soldadura: La velocidad de soldadura, o la velocidad a la que se mueve el láser a lo largo de la junta, influye significativamente en el espesor de la soldadura. Una velocidad de soldadura más lenta permite que el material absorba más energía láser, lo que da como resultado soldaduras más gruesas y profundas. Por el contrario, las velocidades más rápidas reducen la entrada de calor, lo que da como resultado soldaduras más superficiales.
- Optimización: equilibrar la velocidad de soldadura con la potencia del láser es esencial para lograr el espesor deseado. Las velocidades excesivamente lentas pueden provocar sobrecalentamiento y defectos, mientras que las velocidades altas pueden provocar una fusión incompleta o falta de penetración.
Posición focal
- Impacto en el espesor de la soldadura: La posición focal del haz láser afecta el lugar donde se concentra la energía en la pieza de trabajo. Enfocar el haz con precisión sobre la superficie del material o ligeramente por debajo de ella puede mejorar la profundidad de penetración, lo que da como resultado soldaduras más gruesas. La desalineación del punto focal puede provocar una penetración inconsistente o insuficiente.
- Optimización: Al ajustar el punto focal según el espesor del material y el modo de soldadura (conducción o por orificio), los fabricantes pueden lograr un espesor de soldadura más controlado. El enfoque preciso mejora la concentración de energía y garantiza una profundidad constante.
Calidad y modo del haz
- Impacto en el espesor de la soldadura: la calidad y el modo del haz (TEM00, TEM01, etc.) afectan la forma en que se distribuye la energía del láser en el área de trabajo. Un haz monomodo de alta calidad (TEM00) proporciona un punto más concentrado e intenso, lo que permite una penetración más profunda y soldaduras más gruesas. Los haces multimodo, por otro lado, pueden dar lugar a soldaduras más amplias pero menos profundas debido a la dispersión de la energía.
- Optimización: la selección de un láser con la calidad y el modo de haz adecuados mejora el control sobre el espesor de la soldadura. Para aplicaciones que requieren soldaduras estrechas y profundas, un láser monomodo de alta calidad es ideal.
Propiedades materiales
- Impacto en el espesor de la soldadura: los distintos materiales responden a la energía láser de forma diferente en función de propiedades como la conductividad térmica, el punto de fusión y la reflectividad. Por ejemplo, los metales con alta conductividad térmica, como el aluminio y el cobre, disipan el calor rápidamente, por lo que requieren una mayor potencia del láser para lograr la penetración deseada. Los materiales con alta reflectividad también pueden reducir la absorción de energía, lo que afecta el espesor.
- Optimización: comprender las propiedades específicas del material ayuda a ajustar los parámetros del láser para lograr el espesor deseado. Por ejemplo, los materiales reflectantes pueden beneficiarse de tratamientos de superficie para mejorar la absorción o requerir mayor potencia para una penetración efectiva.
Precalentamiento
- Impacto en el espesor de la soldadura: precalentar el material antes de soldar puede reducir los gradientes térmicos, lo que permite una penetración más suave y soldaduras más gruesas. También minimiza el riesgo de agrietamiento en materiales propensos a la tensión térmica, como los aceros con alto contenido de carbono.
- Optimización: El precalentamiento ayuda a lograr un espesor uniforme, especialmente en secciones más gruesas donde, de lo contrario, un enfriamiento rápido podría provocar defectos. El grado de precalentamiento debe controlarse para evitar un aporte térmico excesivo.
Condición de la superficie
- Impacto en el espesor de la soldadura: el estado de la superficie del material, incluida la limpieza y la oxidación, afecta la absorción y penetración de energía. Los contaminantes como aceites, óxidos y suciedad pueden reducir la absorción de energía del láser, lo que genera un espesor inconsistente y soldaduras más débiles.
- Optimización: La limpieza y preparación de la superficie antes de la soldadura garantizan que la energía del láser se absorba de manera eficaz, lo que permite controlar el espesor. Los tratamientos de la superficie, como el pulido o el chorro de arena, también pueden mejorar la calidad de la soldadura.
Gas protector y gas auxiliar
- Impacto en el espesor de la soldadura: el gas de protección (como argón, helio o nitrógeno) protege el baño de soldadura de la contaminación atmosférica y puede influir en la penetración y el espesor de la soldadura. Los distintos gases tienen distintas propiedades térmicas, que afectan la entrada de calor y las características de la soldadura. Los gases auxiliares, que se utilizan a menudo en el corte, también pueden desempeñar un papel en el mantenimiento de un baño de soldadura estable.
- Optimización: la elección del gas de protección adecuado mejora la penetración de la soldadura. Por ejemplo, el helio, con una alta conductividad térmica, puede aumentar la penetración, lo que afecta el espesor de la soldadura. El ajuste de los caudales de gas garantiza una protección suficiente sin introducir turbulencias ni defectos.
Modo de soldadura (conducción vs. ojo de cerradura)
- Impacto en el espesor de la soldadura: la soldadura láser puede realizarse en modo de conducción o de ojo de cerradura, cada uno de los cuales afecta el espesor de soldadura alcanzable. La soldadura por conducción produce soldaduras anchas y poco profundas, adecuadas para aplicaciones a nivel de superficie, mientras que la soldadura de ojo de cerradura crea soldaduras profundas y estrechas ideales para materiales más gruesos.
- Optimización: la selección del modo de soldadura adecuado permite un control preciso del espesor. El modo de conducción se utiliza cuando se requieren soldaduras superficiales estéticas, mientras que el modo de ojo de cerradura es ideal para aplicaciones que exigen una mayor profundidad de penetración.
Configuración conjunta
- Impacto en el espesor de la soldadura: la configuración de la unión, como a tope, traslape o en T, afecta la forma en que la energía del láser interactúa con los materiales y determina el espesor alcanzable. Por ejemplo, las uniones a tope permiten una soldadura de penetración total, mientras que las uniones traslapadas pueden requerir más potencia del láser para una profundidad equivalente.
- Optimización: Elegir la configuración de unión correcta en función del espesor del material y los requisitos de la aplicación garantiza una distribución eficaz de la energía y del espesor de la soldadura.
Longitud de onda láser
- Impacto en el espesor de la soldadura: la longitud de onda del láser afecta la eficacia con la que el material absorbe la energía. Por ejemplo, las longitudes de onda más cortas, como las de los láseres de fibra, son absorbidas mejor por los metales que las longitudes de onda más largas de los láseres de CO2, lo que afecta la profundidad de penetración y el espesor de la soldadura.
- Optimización: Seleccionar un láser con una longitud de onda que coincida con las características de absorción del material garantiza un uso eficiente de la energía, lo que permite un espesor de soldadura óptimo.
Procesamiento previo y posterior a la soldadura
- Procesamiento previo a la soldadura: la preparación, la limpieza y la alineación de la superficie antes de la soldadura mejoran la absorción de energía del láser, lo que da como resultado un espesor uniforme. Cualquier contaminante o desalineación puede causar defectos o una penetración inconsistente.
- Procesamiento posterior a la soldadura: los tratamientos posteriores a la soldadura, como el tratamiento térmico o el enfriamiento controlado, influyen en la estructura y la estabilidad de la soldadura. Las velocidades de enfriamiento controladas ayudan a mantener un espesor uniforme al evitar la tensión residual o la deformación.
- Optimización: El procesamiento adecuado previo y posterior a la soldadura mejora la calidad de la soldadura, lo que permite obtener propiedades mecánicas y un espesor de soldadura consistentes.
Cada uno de estos factores desempeña un papel crucial a la hora de determinar el espesor y la calidad de las soldaduras láser. Mediante el ajuste y la optimización cuidadosos de cada variable, los fabricantes pueden lograr los espesores de soldadura deseados, garantizando así que la soldadura láser cumpla con los estrictos requisitos de diversas aplicaciones industriales.
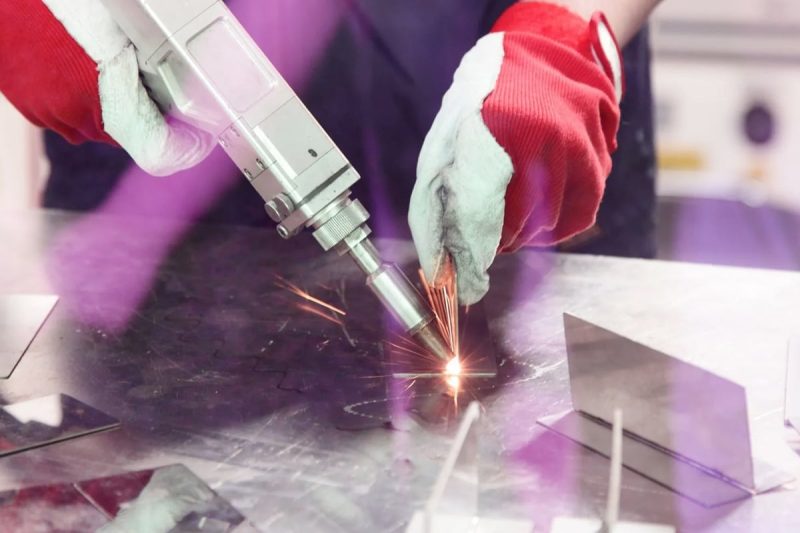
Optimización del espesor de la soldadura
Para optimizar el espesor de la soldadura láser es necesario equilibrar cuidadosamente varios parámetros del proceso y emplear estrategias para lograr un control preciso. Lograr el espesor de soldadura deseado es esencial para garantizar la resistencia de la soldadura, minimizar los defectos y cumplir con las especificaciones de diseño.
Ajuste de parámetros del proceso
Ajuste de potencia del láser
- Impacto: La potencia del láser afecta directamente la profundidad de penetración y el espesor de la soldadura. Aumentar la potencia proporciona más energía al baño de soldadura, lo que permite realizar soldaduras más profundas y más gruesas, mientras que reducir la potencia da como resultado una penetración más superficial.
- Estrategia de optimización: para lograr un espesor de soldadura óptimo, la potencia del láser debe ajustarse cuidadosamente en función de las propiedades del material, la configuración de la unión y los requisitos de espesor. Una potencia excesiva puede provocar defectos como porosidad o fusión excesiva, por lo que es fundamental encontrar un equilibrio que maximice la penetración y minimice los efectos no deseados.
Control de velocidad de soldadura
- Impacto: La velocidad de soldadura determina la cantidad de tiempo que el láser interactúa con el material. Las velocidades más lentas aumentan la absorción de energía, lo que da como resultado soldaduras más profundas y más gruesas, mientras que las velocidades más rápidas reducen la entrada de calor y dan como resultado soldaduras más delgadas.
- Estrategia de optimización: ajustar la velocidad de soldadura junto con la potencia del láser garantiza un espesor uniforme. Se pueden utilizar velocidades más lentas para materiales más gruesos o para una penetración más profunda, pero deben controlarse para evitar el sobrecalentamiento o las zonas afectadas por el calor excesivo.
Ajuste de la posición focal
- Impacto: La posición del foco del láser en relación con la superficie del material afecta la concentración de energía. Un haz enfocado en la superficie o ligeramente por debajo de ella maximiza la penetración y aumenta el espesor de la soldadura, mientras que una posición focal alineada incorrectamente puede generar resultados inconsistentes.
- Estrategia de optimización: el ajuste preciso del punto focal garantiza un suministro de energía constante a la pieza de trabajo, lo que mejora el espesor de la soldadura. Es posible que se necesiten ajustes de la posición focal para diferentes materiales o configuraciones de unión para lograr los resultados deseados.
Optimización de la calidad y el modo del haz
- Impacto: Los rayos láser de alta calidad con una estructura de modo estable ofrecen una mejor concentración de energía, lo que conduce a soldaduras más profundas y controladas.
- Estrategia de optimización: garantizar el uso de haces de alta calidad y seleccionar el modo de haz adecuado ayuda a lograr un espesor de soldadura preciso y uniforme. Mantener estable la salida del láser y la calidad del haz mediante un mantenimiento regular del equipo es fundamental.
Flujo de gas de protección y asistencia
- Impacto: El tipo y el caudal del gas de protección influyen en la estabilidad y la penetración del baño de soldadura. Una protección adecuada protege contra la contaminación y puede mejorar la absorción de energía, mientras que los gases auxiliares ayudan a mantener un entorno de soldadura estable.
- Estrategia de optimización: selección del gas de protección adecuado (por ejemplo, argón, helio o nitrógeno) y ajuste de los caudales para garantizar una penetración y un espesor de soldadura óptimos. El gas de protección debe adaptarse al material y a las condiciones de soldadura para maximizar su eficacia.
Tasas de precalentamiento y enfriamiento
- Impacto: El precalentamiento de los materiales reduce los gradientes térmicos, lo que mejora la absorción y penetración de energía. Las velocidades de enfriamiento afectan el proceso de solidificación y la estructura de la soldadura.
- Estrategia de optimización: La implementación de precalentamiento controlado y enfriamiento posterior a la soldadura garantiza un espesor uniforme y minimiza el riesgo de defectos como grietas o deformaciones.
Estrategias de control
Mapeo y simulación de procesos
El desarrollo de un mapa de procesos que correlacione los parámetros del láser (por ejemplo, potencia, velocidad, posición focal) con el espesor de la soldadura ayuda a identificar los ajustes óptimos para diferentes materiales y configuraciones de unión. El software de simulación de soldadura puede ayudar a predecir los efectos de los cambios de parámetros en el espesor de la soldadura, lo que reduce la necesidad de costosos ensayos de prueba y error.
Sistemas de monitoreo y retroalimentación en tiempo real
La implementación de sensores y sistemas de monitoreo durante la soldadura láser proporciona datos en tiempo real sobre la penetración, el espesor y la calidad de la soldadura. Los sistemas de retroalimentación automatizados pueden ajustar los parámetros en respuesta a los cambios en el entorno de soldadura, lo que garantiza un espesor de soldadura constante.
Sistemas de control adaptativo
Los sistemas avanzados de soldadura láser pueden ajustar automáticamente la potencia, la velocidad y otros parámetros del láser en función de la información en tiempo real. Esta capacidad minimiza la variabilidad y garantiza un espesor de soldadura uniforme en geometrías complejas o condiciones de material variables.
Preparación de superficies y acondicionamiento de materiales
La preparación adecuada de la superficie, que incluye la limpieza y el acondicionamiento, mejora la absorción de energía y la uniformidad de la soldadura. Estrategias como el pulido, el pulido con chorro de arena o la aplicación de recubrimientos superficiales mejoran la interacción de la energía láser, lo que da como resultado un espesor más uniforme.
Optimización del diseño y montaje de juntas
Minimizar los espacios y garantizar una alineación precisa de los componentes mejora la transferencia de energía y la uniformidad del espesor de la soldadura. El uso de técnicas de sujeción y fijación adecuadas ayuda a mantener condiciones óptimas de unión durante la soldadura.
Validación y prueba de procesos
La realización periódica de pruebas y validaciones de los procesos de soldadura láser ayuda a identificar los parámetros óptimos para aplicaciones específicas. La mejora continua del proceso garantiza que el espesor de la soldadura se mantenga dentro de las tolerancias deseadas.
Al ajustar los parámetros clave del proceso e implementar estrategias de control efectivas, los fabricantes pueden lograr un espesor de soldadura óptimo, mejorar la calidad de las uniones y aumentar la eficiencia general de sus operaciones de soldadura láser. Estas prácticas garantizan que la soldadura láser siga siendo una solución confiable y versátil para diversas aplicaciones industriales.
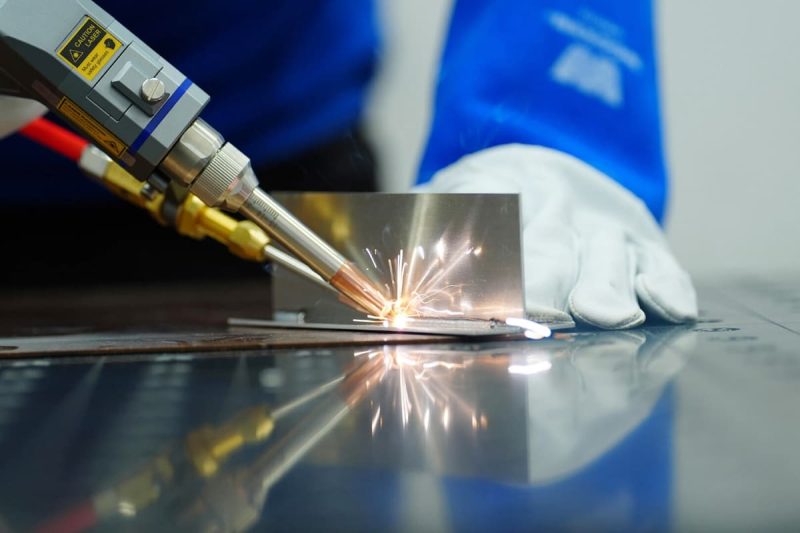
Desafíos y consideraciones
Optimizar el espesor de la soldadura láser no está exento de desafíos. Diversos factores pueden afectar la consistencia, la calidad y el rendimiento de la soldadura. Al comprender los problemas comunes e implementar medidas de control de calidad sólidas, los fabricantes pueden mejorar sus procesos y garantizar soldaduras confiables.
Problemas comunes
Profundidad de penetración inconsistente
- Desafío: Las variaciones en la potencia del láser, el enfoque del haz, el espesor del material o la alineación de las juntas pueden generar profundidades de penetración inconsistentes, lo que afecta el espesor de la soldadura. Esta inconsistencia puede generar juntas débiles, falta de fusión o defectos estructurales, lo que compromete la integridad de la soldadura.
- Consideración: La calibración regular de la fuente láser, el monitoreo del enfoque del haz y el control preciso de los parámetros de soldadura son esenciales para lograr una penetración y un espesor de soldadura consistentes.
Zonas afectadas por el calor (ZAT)
- Desafío: El aporte excesivo de calor puede crear una gran zona afectada por el calor, alterando la microestructura del material y reduciendo las propiedades mecánicas cerca de la soldadura. Esto puede provocar deformaciones, tensiones residuales o grietas, especialmente en materiales sensibles a la tensión térmica.
- Consideración: Optimizar la potencia del láser y la velocidad de soldadura, así como utilizar gases de protección adecuados, pueden minimizar las zonas afectadas por el calor y mantener un espesor de soldadura constante.
Porosidad y atrapamiento de gas
- Desafío: Los gases atrapados dentro del baño de soldadura pueden causar porosidad, lo que reduce la resistencia mecánica de la soldadura y genera inconsistencias en el espesor de la misma. La porosidad puede surgir de contaminantes, gas de protección insuficiente o configuraciones de proceso inadecuadas.
- Consideración: Limpiar la superficie antes de soldar, optimizar el flujo de gas protector y reducir los contaminantes puede minimizar la porosidad. El monitoreo en tiempo real ayuda a detectar y abordar problemas de porosidad en las primeras etapas del proceso.
Reflectividad de los materiales
- Desafío: Los materiales altamente reflectantes, como el aluminio y el cobre, reflejan una parte importante de la energía del láser, lo que genera dificultades para lograr una penetración adecuada y un espesor uniforme. Estos materiales pueden requerir consideraciones especiales para mejorar la absorción de energía.
- Consideración: Los tratamientos de superficie, como recubrimientos o texturizados, y el uso de láseres con longitudes de onda más cortas pueden mejorar la absorción de energía y la consistencia de los materiales reflectantes.
Desalineación y espacios entre las articulaciones
- Desafío: Las juntas o los espacios desalineados entre los componentes reducen la capacidad del láser para lograr una penetración uniforme. Esto puede provocar socavaduras, fusión incompleta y espesores de soldadura variables.
- Consideración: La fijación, la alineación y el control de ajuste adecuados garantizan condiciones de unión consistentes, lo que reduce la probabilidad de defectos.
Distorsión térmica y estrés
- Desafío: La distribución desigual del calor y el enfriamiento rápido pueden causar distorsión térmica, tensión residual y deformación, lo que puede afectar el espesor de la soldadura y la integridad de la unión.
- Consideración: El precalentamiento, el enfriamiento controlado y las velocidades de soldadura optimizadas ayudan a reducir las tensiones térmicas y a mantener dimensiones de soldadura constantes.
Medidas de control de calidad
Monitoreo de procesos en tiempo real
- Medición: La implementación de sistemas de monitoreo en tiempo real brinda información sobre parámetros clave, como la potencia del láser, la velocidad de soldadura y la profundidad de penetración. Esto permite realizar ajustes inmediatos, lo que reduce las variaciones en el espesor de la soldadura y mejora la uniformidad general.
- Consideración: Los sensores ópticos, los monitores de temperatura y los sistemas de retroalimentación láser son ejemplos de herramientas que pueden utilizarse para mantener la estabilidad del proceso.
Preparación de la superficie antes de la soldadura
- Medir: Asegurarse de que la superficie de la pieza de trabajo esté limpia, libre de contaminantes y adecuadamente preparada es fundamental para lograr una absorción de energía y una calidad de soldadura constantes.
- Consideración: Los tratamientos de superficie como el pulido, el desengrasado o la aplicación de recubrimientos ayudan a minimizar los contaminantes que podrían interferir con la transferencia de energía.
Calibración y Mantenimiento de Equipos
- Medida: La calibración y el mantenimiento regulares de fuentes láser, ópticas y otros componentes del sistema garantizan una calidad del haz estable, potencia de salida y precisión.
- Consideración: Los controles periódicos evitan la degradación del rendimiento, lo que podría afectar el espesor de la soldadura y la calidad general.
Pruebas no destructivas (END)
- Medición: Las técnicas como las pruebas ultrasónicas, la radiografía y las inspecciones visuales ayudan a evaluar la calidad de la soldadura sin dañar la pieza. Los métodos de END detectan porosidad, grietas, fusión incompleta y otros problemas.
- Consideración: La implementación de procedimientos NDT ayuda a verificar la consistencia de la soldadura y el cumplimiento de las especificaciones, lo que reduce la probabilidad de fallas del producto.
Uso de gas protector y gas auxiliar
- Medida: La selección adecuada y el control del flujo de gases de protección protegen el baño de soldadura de la contaminación atmosférica e influyen en la penetración de la soldadura.
- Consideración: Ajustar el tipo y el caudal de los gases de protección puede minimizar la oxidación, la porosidad y las inconsistencias en el espesor de la soldadura.
Optimización del proceso de soldadura
- Medición: Desarrollar un mapa de proceso que correlacione los parámetros del láser (por ejemplo, potencia, velocidad, posición focal) con el espesor de la soldadura garantiza configuraciones óptimas para diferentes materiales y configuraciones de juntas.
- Consideración: La mejora continua del proceso, respaldada por pruebas y simulación, mejora el control sobre el espesor de la soldadura y reduce la variabilidad.
Capacitación y operadores calificados
- Medida: Los operadores capacitados con un profundo conocimiento de los parámetros, materiales y técnicas de soldadura láser contribuyen significativamente a mantener la consistencia y la calidad de la soldadura.
- Consideración: La capacitación continua y el desarrollo de habilidades permiten a los operadores identificar y resolver problemas rápidamente, mejorando el control del proceso.
Al abordar desafíos comunes e implementar medidas sólidas de control de calidad, los fabricantes pueden optimizar los procesos de soldadura láser para lograr un espesor de soldadura constante, una alta integridad estructural y una calidad superior.

Resumen
El espesor de la soldadura láser es un factor crítico que influye en la resistencia, precisión y rendimiento general de las uniones soldadas. Lograr un espesor óptimo requiere un profundo conocimiento de varios factores, como la potencia del láser, la velocidad de soldadura, la calidad del haz, la posición focal, las propiedades del material y los gases de protección. El ajuste de estos parámetros garantiza una entrada de energía precisa y una penetración constante, lo que da como resultado soldaduras de alta calidad y sin defectos. Los tratamientos previos y posteriores a la soldadura, así como la configuración de la unión y las condiciones de la superficie, afectan aún más el resultado de la soldadura. Al abordar desafíos comunes como la penetración inconsistente, la porosidad y la distorsión térmica, los fabricantes pueden optimizar el espesor de la soldadura y mejorar la confiabilidad general del proceso. La implementación de sólidas medidas de control de calidad, que incluyen monitoreo en tiempo real, calibración adecuada del equipo y capacitación del operador, garantiza resultados consistentes y confiables. Con estos conocimientos, la soldadura láser sigue siendo una solución indispensable para las industrias que exigen precisión, resistencia y alta productividad.
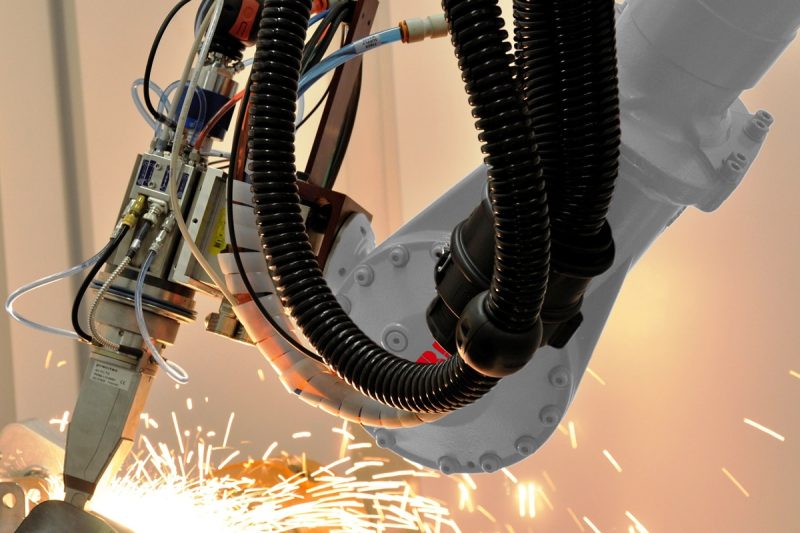
Obtenga soluciones de soldadura láser
Optimizar el espesor de la soldadura láser es esencial para lograr soldaduras precisas, resistentes y confiables en diversas aplicaciones. En AccTek Laser, ofrecemos soluciones avanzadas de soldadura láser diseñadas para satisfacer las demandas únicas de su industria. Nuestros sistemas de soldadura láser de última generación ofrecen un control excepcional sobre parámetros clave, como la potencia del láser, el enfoque del haz y la velocidad de soldadura, lo que garantiza una penetración constante y resultados de alta calidad. Nuestro equipo de expertos está dedicado a ayudarlo a seleccionar el sistema adecuado. máquina de soldadura láser dependiendo del tipo de material, la configuración de la junta y las necesidades específicas de la aplicación.
Ya sea que necesite soldar componentes delgados y delicados o piezas estructurales gruesas, las soluciones de AccTek Laser ofrecen una precisión superior, zonas mínimas afectadas por el calor y una eficiencia inigualable. Con nuestro soporte integral, que incluye asesoramiento previo a la venta, integración de sistemas, capacitación y mantenimiento, puede optimizar su proceso de soldadura y lograr un rendimiento incomparable. Contáctenos hoy para descubrir la solución de soldadura láser perfecta para sus necesidades de producción.
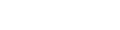
Información del contacto
- [email protected]
- [email protected]
- +86-19963414011
- No. 3 Zona A, Zona Industrial de Lunzhen, Ciudad de Yucheng, Provincia de Shandong.
Obtenga soluciones láser