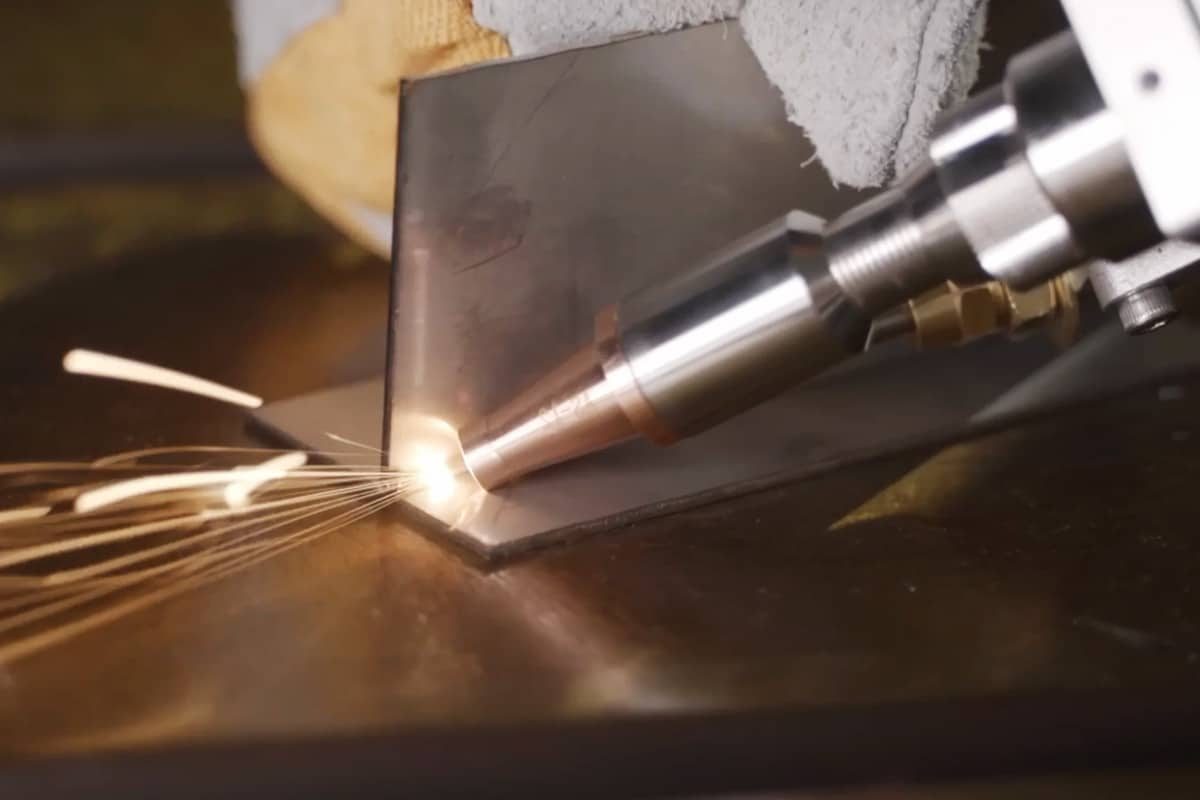
Diseño de juntas de soldadura láser
La soldadura láser se ha utilizado ampliamente en la industria aeroespacial, la fabricación de automóviles, equipos electrónicos, equipos médicos y otras industrias gracias a su alta precisión, bajo aporte de calor y alta eficiencia. En comparación con los métodos de soldadura tradicionales, la soldadura láser ofrece ventajas como soldaduras estrechas, alta velocidad de soldadura, una zona afectada por el calor reducida y baja deformación, lo que la convierte en la opción ideal para sectores de fabricación de alta demanda. Sin embargo, a pesar de sus numerosas ventajas, la estabilidad de la calidad de la soldadura y la fiabilidad del producto final dependen en gran medida del diseño de la unión soldada. Un diseño de unión adecuado garantiza la integridad y la resistencia mecánica de la soldadura, reduce defectos como grietas, poros y penetración de la soldadura que pueden producirse durante el proceso, optimizando al mismo tiempo el consumo de energía, mejorando la eficiencia de la producción y reduciendo la tasa de retrabajo y los costes de producción.
En aplicaciones de soldadura láser, el diseño de uniones debe considerar múltiples factores, como las propiedades metalúrgicas del sustrato, el método de soldadura, la potencia del láser, la forma de la soldadura, la precisión del ensamblaje y los requisitos de procesamiento posteriores. Un excelente diseño de unión permite aprovechar al máximo las ventajas de la soldadura láser para lograr resultados de alta calidad y bajo costo. Este artículo analizará en profundidad los principios básicos, los factores influyentes y las estrategias de optimización del diseño de uniones mediante soldadura láser para ayudar a empresas e ingenieros a mejorar la calidad de la soldadura, optimizar los procesos de producción y prolongar la vida útil de las estructuras soldadas en aplicaciones prácticas.
Tabla de contenido
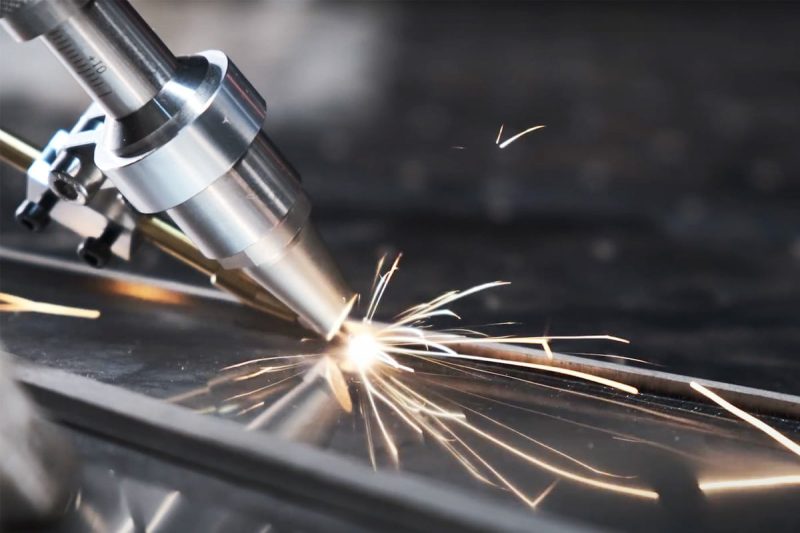
Principios básicos del diseño de juntas de soldadura láser
Como proceso de soldadura de alta precisión y eficiencia, la soldadura láser se utiliza ampliamente en industrias como la automotriz, la aeroespacial, la de equipos electrónicos y la de dispositivos médicos. Un diseño de unión adecuado es crucial para la integridad, la resistencia y la eficiencia de producción de la soldadura. Un diseño de unión optimizado no solo reduce los defectos de soldadura y mejora la calidad de la misma, sino que también reduce los costos de producción y mejora la eficiencia general de fabricación. Este artículo analizará los componentes clave de las uniones de soldadura láser y su papel en la optimización de la calidad de la soldadura, además de analizar cómo lograr resultados de soldadura eficientes y estables mediante el diseño científico.
Componentes clave de las uniones soldadas por láser
Sustrato
La elección del material base afecta directamente la calidad de la soldadura y el rendimiento del producto final. Al seleccionar materiales de soldadura, hay varios factores clave a considerar:
- Propiedades mecánicas: La resistencia, dureza, ductilidad y otras propiedades del material afectarán la estabilidad de la unión soldada.
- Propiedades metalúrgicas: Incluye la composición de la aleación, la compatibilidad y los cambios de microestructura del material posteriores a la soldadura para garantizar la confiabilidad de la soldadura.
- Conductividad térmica y temperatura de fusión: afectan la absorción y transferencia de energía láser. Los materiales con alta conductividad térmica (como el cobre) pueden requerir un generador láser de mayor potencia, mientras que los materiales con baja conductividad térmica (como el titanio) deben evitar daños estructurales causados por sobrecalentamiento.
Configuración del conector
Diferentes tipos de configuraciones de unión son adecuados para distintas necesidades de soldadura. Los tipos de unión más comunes incluyen:
- Unión a tope: Adecuada para aplicaciones de soldadura de alta resistencia, con excelente rendimiento de soldadura, pero con requisitos de alta precisión de procesamiento.
- Junta traslapada: adecuada para soldadura de placas delgadas, proceso simple y velocidad de soldadura rápida, pero se debe prestar atención a la reducción de la concentración de tensión.
- Junta en T: Se utiliza comúnmente en soldadura estructural, con una fuerte capacidad de soporte de soldadura, pero es necesario asegurar una penetración suficiente para evitar defectos de soldadura.
Además, durante el proceso de soldadura, el tamaño de la holgura, la precisión del ensamblaje y la alineación de la unión afectarán directamente la calidad de la soldadura. Optimizar estos parámetros puede reducir la deformación de la soldadura y mejorar la resistencia de la unión.
Material de relleno
En algunas aplicaciones de soldadura láser, se pueden utilizar materiales de aportación para optimizar la calidad de la soldadura. Los principales efectos incluyen:
- Mejora la resistencia de la soldadura, previene grietas en la soldadura y mejora las propiedades mecánicas de la soldadura.
- Ajustar las propiedades metalúrgicas y mejorar la estructura de la soldadura optimizando la composición de la aleación.
- Reduce defectos de soldadura como poros y falta de fusión y mejora la estabilidad de la soldadura.
La selección del material de relleno debe coincidir con las características del material base y ajustarse razonablemente en combinación con el proceso de soldadura.
Componentes clave de las uniones soldadas por láser
El diseño optimizado de la unión soldada debe cumplir simultáneamente los siguientes objetivos:
- Garantizar la integridad y la resistencia de la soldadura: diseñar racionalmente la estructura de la unión para garantizar una buena fusión y suficiente resistencia mecánica en el área de soldadura.
- Reducir los defectos de soldadura: reduzca problemas comunes como poros, grietas y falta de fusión al optimizar la selección del material, la estructura de la unión y el proceso de soldadura.
- Optimice la eficiencia y la productividad del proceso: diseñe una configuración de unión razonable para aumentar la velocidad de soldadura, reducir el desperdicio de material y reducir los costos de procesamiento, mejorando así la eficiencia general de la producción.
El diseño de las uniones soldadas por láser es crucial para la calidad de la soldadura y la eficiencia de la producción. Mediante la selección racional del material base, la optimización de la estructura de la unión y los materiales de relleno, y el perfeccionamiento del proceso de soldadura, se puede mejorar eficazmente la calidad de la soldadura, reducir los defectos y optimizar la eficiencia de la producción. El diseño científico de las uniones no solo garantiza la resistencia y la estabilidad de la soldadura, sino que también optimiza el proceso de fabricación, ayudando a las empresas a mantener su competitividad en el campo de la fabricación de alta precisión.
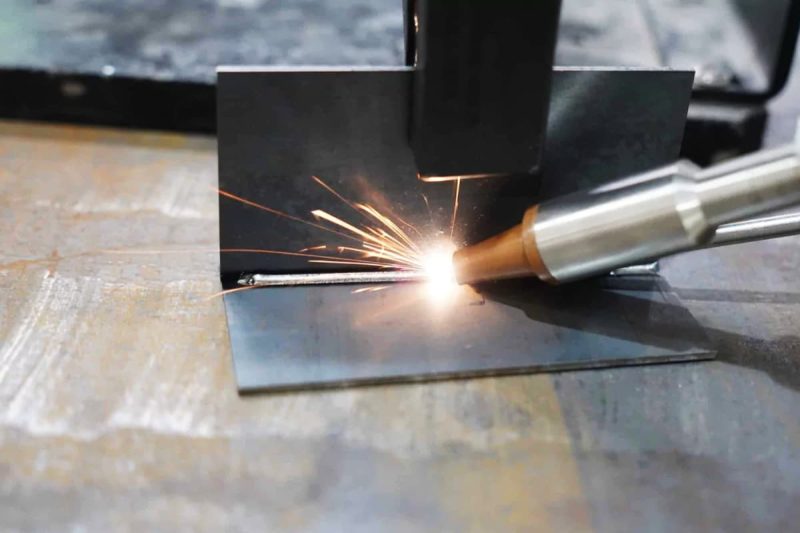
Factores que afectan el diseño de juntas de soldadura láser
El diseño de uniones soldadas por láser no solo implica la selección de estructuras básicas, sino que también se ve afectado por múltiples factores, como las propiedades del material, la configuración de la unión, los parámetros de soldadura y los requisitos de la aplicación. La correcta consideración de estos factores puede ayudar a optimizar la calidad de la soldadura, mejorar su resistencia, reducir los defectos y optimizar la eficiencia de la producción.
Propiedades materiales
Las propiedades físicas y químicas del sustrato son fundamentales para el rendimiento de las uniones soldadas por láser. Al diseñar uniones soldadas, es importante prestar atención a los siguientes aspectos clave:
- Compatibilidad del sustrato: La compatibilidad de la soldadura entre diferentes materiales metálicos determina la calidad de la misma. Por ejemplo, las aleaciones de composición similar suelen tener buenas propiedades de fusión, mientras que la soldadura con metales diferentes puede producir grietas o defectos debido a diferentes coeficientes de expansión térmica o a la formación de compuestos intermetálicos frágiles.
- Propiedades mecánicas y metalúrgicas: Las propiedades mecánicas (como dureza, ductilidad y resistencia a la tracción) afectan la fiabilidad de la soldadura. Las propiedades metalúrgicas determinan los cambios en los elementos de aleación durante la soldadura. Por ejemplo, algunos aceros con alto contenido de carbono pueden producir estructuras endurecidas durante la soldadura, lo que aumenta el riesgo de grietas. Por lo tanto, es necesario ajustar los parámetros del proceso de soldadura a las diferentes propiedades del material para garantizar la calidad de la soldadura.
- Conductividad térmica y temperatura de fusión: La conductividad térmica y el punto de fusión del material afectan la transmisión y absorción de la energía láser. Por ejemplo, los metales con alta conductividad térmica (como... cobre y aluminio) disipan el calor rápidamente y requieren mayor potencia láser o una mayor concentración de energía. Los materiales con puntos de fusión más altos pueden requerir mayor energía de soldadura para garantizar una fusión y una resistencia de unión suficientes.
Configuración del conector
El tipo, la precisión del ensamblaje y la alineación de la unión afectan directamente la estabilidad del proceso de soldadura y su calidad. Los tipos de unión más comunes incluyen:
- Junta a tope: Adecuada para soldaduras que requieren alta resistencia y baja deformación. La separación de la junta a tope debe controlarse estrictamente para garantizar una fusión completa y evitar defectos como la fusión incompleta o la inclusión de escoria.
- Junta de solape: Adecuada para la soldadura de placas delgadas, la parte superpuesta de la soldadura proporciona mayor resistencia. Sin embargo, debido al efecto de apilamiento, puede quedar gas en el espacio, por lo que es necesario optimizar los parámetros de soldadura para reducir la porosidad.
- Junta en T: Se utiliza generalmente en piezas estructurales que soportan mayor tensión. La soldadura de las juntas en T debe garantizar una penetración suficiente para evitar el agrietamiento causado por la concentración de tensiones.
Además, en el diseño de uniones soldadas también es necesario considerar:
- Montaje y tamaño de la holgura: Una holgura demasiado grande puede resultar en un relleno de soldadura insuficiente, mientras que una holgura demasiado pequeña puede resultar en una fusión incompleta o deformación de la soldadura. Por lo tanto, un montaje preciso y el control de la holgura son fundamentales para la calidad de la soldadura.
- Transmisión del rayo láser y canal de procesamiento de piezas: Asegúrese de que el rayo láser alcance el área de soldadura con fluidez para evitar que la soldadura se vea afectada por obstrucciones o reflejos. Asimismo, en la línea de producción automatizada, es necesario optimizar el método de fijación de las piezas y el diseño del canal de soldadura para garantizar la estabilidad y consistencia de la soldadura.
Parámetros de soldadura
Un ajuste razonable de los parámetros de soldadura puede optimizar la calidad de la soldadura y reducir los defectos. Los parámetros clave comunes incluyen:
- Potencia del láser: Afecta la profundidad de la soldadura y la formación del baño de fusión. Una potencia alta es adecuada para la soldadura de penetración profunda, mientras que una potencia baja es adecuada para la soldadura de precisión.
- Posición del foco y diámetro del haz: El control preciso del foco influye en la densidad de energía y la profundidad de soldadura. Los diámetros de haz más pequeños son adecuados para soldaduras de alta precisión, mientras que los haces más grandes se pueden utilizar para requisitos de soldadura más amplios.
- Velocidad de soldadura y dirección de avance: Una velocidad de soldadura demasiado rápida puede provocar una penetración insuficiente y afectar la resistencia de la soldadura, mientras que una velocidad demasiado lenta puede causar deformación o expansión de la zona afectada por el calor (ZAC). Por lo tanto, la velocidad de soldadura debe ajustarse en función del material y la estructura de la unión.
- Control del gas de protección y la atmósfera: Un gas de protección adecuado (como argón, nitrógeno o una mezcla de gases) puede reducir la oxidación durante la soldadura y optimizar su calidad. Los distintos materiales tienen diferentes requisitos de gas. Por ejemplo, las aleaciones de titanio deben estar completamente aisladas del oxígeno, mientras que... acero inoxidable Puede protegerse con argón para reducir la decoloración y oxidación de la soldadura.
requerimientos de aplicacion
Además de los factores materiales y de proceso, el diseño de la unión soldada también debe satisfacer las necesidades de escenarios de aplicación específicos, que incluyen:
- Requisitos funcionales y estructurales: Seleccione el tipo de unión y la estructura de soldadura adecuados según el uso final del producto. Por ejemplo, la soldadura láser en la industria automotriz suele requerir alta resistencia y ligereza, mientras que la soldadura con equipos electrónicos prioriza el refinamiento y el control de las zonas afectadas por el calor.
- Acabado y apariencia superficial: En algunas aplicaciones, como la electrónica de consumo o los dispositivos médicos, la estética de la soldadura es crucial. Esto requiere optimizar los parámetros de soldadura, reducir las salpicaduras y la escoria, y mejorar el acabado superficial.
- Procesamiento posterior a la soldadura y procesamiento secundario: Algunos procesos de soldadura pueden requerir un posprocesamiento adicional, como rectificado, tratamiento térmico o recubrimiento, para cumplir con los estándares de calidad del producto final. Por lo tanto, al diseñar las uniones soldadas, también se debe considerar la viabilidad y el costo del procesamiento posterior.
El diseño de las uniones soldadas por láser se ve afectado por numerosos factores, como las características del sustrato, la configuración de la unión, los parámetros de soldadura y los requisitos de la aplicación final. Mediante una selección racional de materiales, la optimización de la estructura de la unión, el control preciso de los parámetros del proceso de soldadura y el ajuste según los requisitos específicos de la aplicación, se puede mejorar eficazmente la calidad de la soldadura, reducir los defectos y optimizar la eficiencia de la producción. Un diseño de unión científico y razonable no solo garantiza la resistencia y la estabilidad de la soldadura, sino que también optimiza el proceso de fabricación, mejorando la competitividad de la producción y garantizando la calidad del producto.
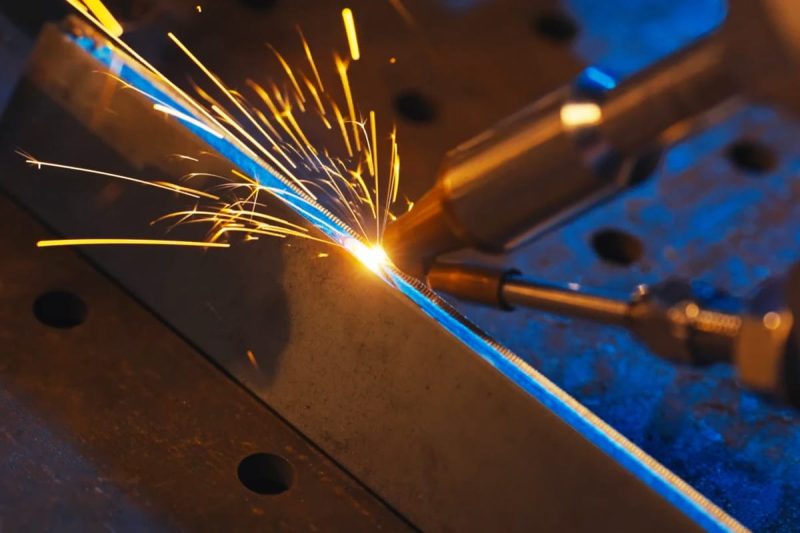
Estrategia de optimización para el diseño de uniones de soldadura láser
El objetivo de optimizar el diseño de uniones de soldadura láser es mejorar la calidad de la soldadura, garantizar su integridad y resistencia, reducir los defectos y mejorar la eficiencia de la producción. Las principales estrategias de optimización incluyen los siguientes aspectos:
Minimizar la zona afectada por el calor (ZAT)
Una zona afectada por el calor (ZAC) extensa puede afectar las propiedades del material e incluso causar fragilización de la soldadura. Al optimizar la potencia del láser, la velocidad de soldadura y el enfoque del haz, se puede controlar eficazmente la entrada de calor para reducir la zona afectada por el calor. Además, una selección adecuada de tipos de unión, como juntas a tope o juntas traslapadas, también puede ayudar a reducir la acumulación de calor y mejorar la estabilidad de la soldadura.
Mejorar la resistencia de la soldadura
La clave para garantizar la resistencia de las uniones soldadas reside en optimizar la distribución del calor, controlar el tamaño de la holgura y alinear con precisión las piezas. Un proceso de soldadura adecuado puede reducir la concentración de tensiones y evitar problemas como la falta de fusión. En algunas aplicaciones, el uso de materiales de aporte compatibles puede mejorar la adherencia de la soldadura y mejorar la resistencia y durabilidad general de la unión.
Garantizar la calidad de la soldadura
La calidad de la soldadura se ve afectada por numerosos factores, como la potencia del láser, la posición del enfoque, la velocidad de soldadura y el uso de gas de protección. Un ajuste adecuado de estos parámetros puede reducir defectos como poros y grietas. Además, el uso de tecnología de monitoreo en línea para la inspección de calidad puede garantizar la consistencia de la soldadura y mejorar la tasa de calificación del producto.
Optimizar el diseño de las uniones soldadas por láser es fundamental para mejorar la calidad de la soldadura y la eficiencia de la producción. Al reducir la zona afectada por el calor, aumentar la resistencia de la soldadura y controlar estrictamente la calidad de la misma, se puede optimizar eficazmente el efecto de la soldadura para cumplir con los altos estándares de la fabricación industrial.
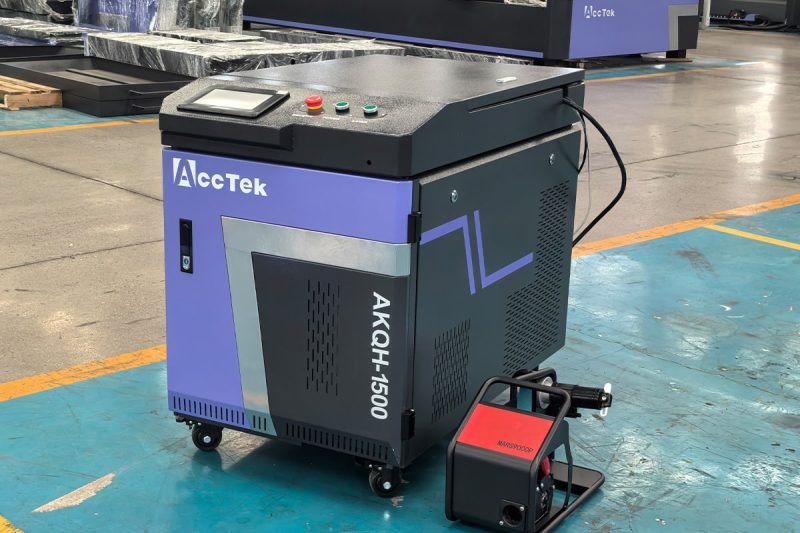
Resumir
El diseño de la unión para soldadura láser es un factor clave para determinar la calidad de la soldadura y la eficiencia de la producción. Al comprender a fondo los principios básicos, los factores que influyen y las estrategias de optimización del diseño de la unión, los fabricantes pueden garantizar la integridad de la soldadura, reducir los defectos y mejorar la calidad general de la misma. Un diseño de unión adecuado no solo mejora la resistencia de la soldadura, sino que también optimiza el proceso de producción para satisfacer las necesidades de diferentes aplicaciones.
Si busca soluciones de soldadura láser eficientes y precisas, Láser AccTek ofrece avanzadas máquina de soldadura lásers que cumplen con los más altos estándares de calidad y eficiencia. Nuestros equipos utilizan tecnología láser avanzada para garantizar la estabilidad y consistencia de la soldadura, ayudándole a alcanzar sus objetivos de producción. Contáctenos ¡Para saber más sobre cómo nuestros productos pueden ayudarle a optimizar su proceso de soldadura!
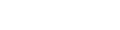
Información del contacto
- [email protected]
- [email protected]
- +86-19963414011
- No. 3 Zona A, Zona Industrial de Lunzhen, Ciudad de Yucheng, Provincia de Shandong.
Obtenga soluciones láser