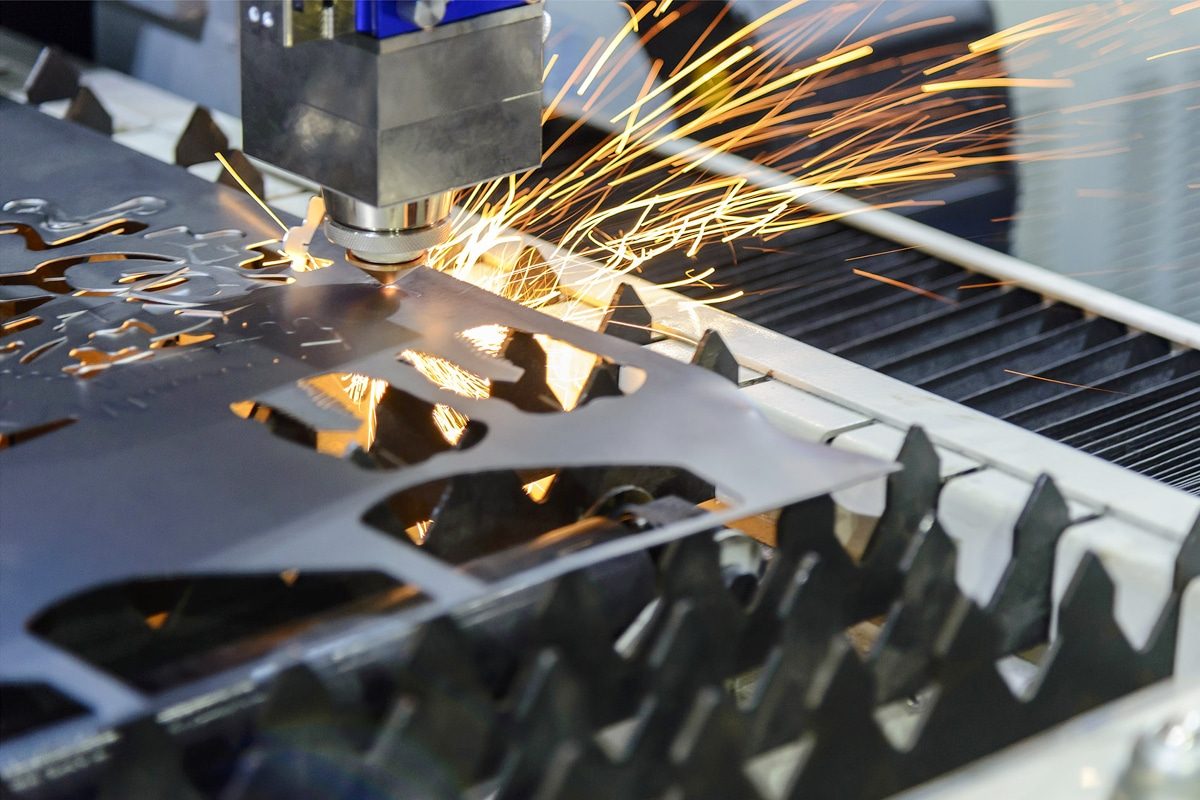
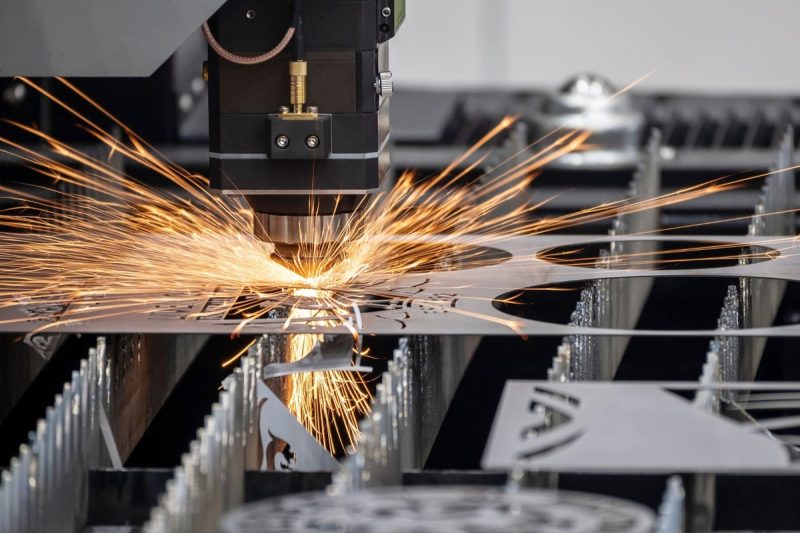
Aprenda sobre el corte por láser
Descripción del corte por láser
Tipos de láseres utilizados en aplicaciones de corte
Láser de fibra
Láser de CO2
Componentes de un sistema de corte por láser
Lo tipico sistema de corte por láser consta de varios componentes clave que trabajan juntos para proporcionar un rendimiento de corte preciso y eficiente:
- Fuente láser: este es el componente central que produce el rayo láser. Dependiendo de la aplicación, la fuente láser puede ser un generador de láser de fibra, un generador de láser de CO2 u otro tipo de generador de láser.
- Óptica: Se utilizan espejos y lentes para dirigir y enfocar el rayo láser sobre el material que se está cortando. La calidad de la óptica afecta la precisión y eficiencia del proceso de corte.
- Cabezal de corte: El cabezal de corte contiene la lente de enfoque y la boquilla a través de la cual se dirige el rayo láser y el gas auxiliar. Se encarga de mantener la distancia focal correcta y garantizar unas condiciones de corte óptimas.
- Mesa de trabajo: Soporta el material que se está cortando y generalmente incluye un mecanismo para mover el material debajo del cabezal de corte.
- Controlador CNC: El controlador CNC gestiona el movimiento del cabezal de corte láser y la pieza de trabajo, siguiendo la ruta de corte programada para producir la forma y el patrón deseados.
- Suministro de gas auxiliar: El gas auxiliar ayuda al proceso de corte eliminando el material fundido, enfriando la zona de corte y previniendo la oxidación. Los gases auxiliares comunes incluyen oxígeno, nitrógeno y aire comprimido.
- Sistema de escape: Elimina los humos y los desechos generados durante el proceso de corte para mantener un entorno de trabajo limpio y proteger los componentes ópticos y láser.
- Sistema de enfriamiento: el corte por láser genera una gran cantidad de calor que debe disiparse para evitar daños a la fuente láser y otros componentes. Los sistemas de refrigeración, como los enfriadores de agua, se utilizan para mantener temperaturas de funcionamiento óptimas.
Parámetros clave que afectan el rendimiento del corte por láser
Varios parámetros pueden afectar el rendimiento y la calidad del proceso de corte por láser. Comprender y optimizar estos parámetros puede ayudar a lograr los resultados deseados:
- Potencia del láser: la potencia de salida de la fuente láser determina el grosor y el tipo de material que se puede cortar. Potencias más altas permiten cortar materiales más gruesos, pero es posible que sea necesario ajustar otros parámetros para mantener la calidad del corte.
- Velocidad de corte: La velocidad a la que el cabezal de corte se mueve a través de la pieza de trabajo. La velocidad de corte óptima garantiza un equilibrio entre productividad y calidad de corte. Una velocidad demasiado rápida puede provocar cortes incompletos, mientras que una velocidad demasiado lenta puede provocar una acumulación excesiva de calor y daños materiales.
- Posición focal: la posición del punto focal del rayo láser con respecto a la superficie del material. El enfoque correcto garantiza la máxima densidad de energía en el punto de corte, lo que da como resultado cortes limpios y precisos. La desalineación puede resultar en una mala calidad de corte y una reducción de la eficiencia.
- Tipo y presión del gas auxiliar: El tipo y la presión del gas auxiliar utilizado (oxígeno, nitrógeno o aire comprimido) tienen un impacto significativo en el proceso de corte. La selección y presión correctas del gas optimizan la eliminación del material fundido, previenen la oxidación y mejoran la calidad del corte.
- Tipo de material y espesor: Los diferentes materiales y espesores reaccionan de manera diferente al corte por láser. Al configurar los parámetros de corte, se deben considerar las propiedades del material como la reflectividad, la conductividad térmica y el punto de fusión.
- Calidad del haz: La calidad del haz láser, caracterizada por su enfoque y estructura de modo, afecta la precisión y calidad del corte. Un haz de alta calidad con un tamaño de punto focal pequeño produce cortes más finos con un ancho de corte mínimo.
- Diseño de la boquilla: El diseño de la boquilla, incluido su diámetro y forma, afecta el flujo de gas auxiliar y la eliminación del material fundido. Un diseño de boquilla optimizado mejora la eficiencia y la calidad del corte.
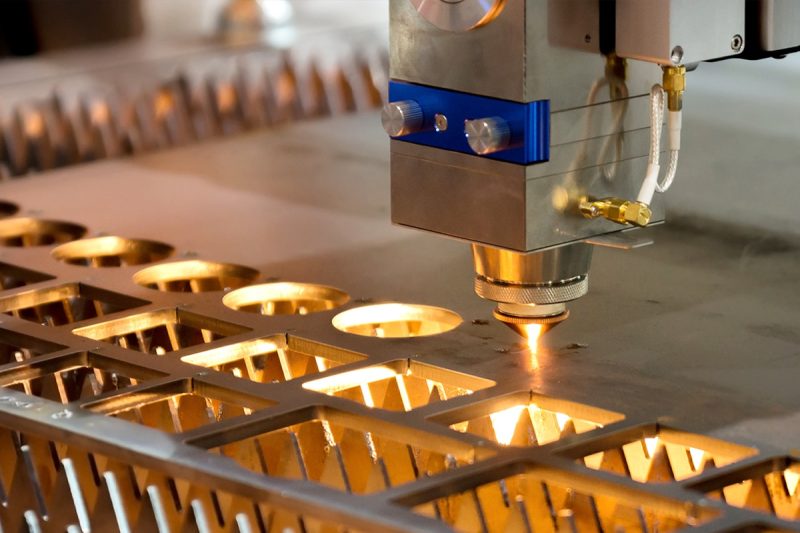
El papel de los gases auxiliares en el corte por láser
Eliminación de material fundido
Durante el proceso de corte por láser, un rayo láser de alta intensidad funde el material en el punto de corte. El gas auxiliar se dirige a través de una boquilla al área de corte, donde ayuda a eliminar el material fundido del corte (el espacio creado por el láser). La eliminación eficaz del material fundido mantiene la calidad del corte y previene defectos.
- Jetting eficiente: La alta presión del gas auxiliar expulsa el material fundido del corte, evitando que se vuelva a solidificar en la pieza de trabajo y asegurando un corte limpio.
- Prevención de la formación de escoria: al evacuar rápidamente el material fundido, el gas auxiliar minimiza la formación de escoria (material residual que se adhiere a la superficie inferior del corte), lo que reduce la necesidad de posprocesamiento.
- Mantenimiento del ancho de corte: La eliminación continua del material fundido ayuda a mantener el ancho de corte deseado, lo que garantiza la exactitud dimensional y la precisión del corte final.
Enfriamiento de la zona de corte
El intenso calor generado por el rayo láser puede provocar efectos térmicos importantes en la pieza de trabajo, como deformaciones, deformaciones y cambios en las propiedades del material. El gas auxiliar ayuda a controlar estos efectos térmicos enfriando la zona de corte.
- Disipación de calor: el flujo de gas auxiliar absorbe y disipa el exceso de calor en el área de corte, evitando el sobrecalentamiento y minimizando la deformación térmica del material.
- Reducción de la zona afectada por el calor (HAZ): enfriar la zona de corte ayuda a limitar el tamaño de la HAZ, manteniendo las propiedades mecánicas del material y reduciendo el riesgo de deformación u otros daños térmicos.
- Aumento de las velocidades de corte: el enfriamiento eficiente aumenta las velocidades de corte porque es menos probable que el material desarrolle defectos inducidos térmicamente, lo que resulta en una producción más rápida y eficiente.
Proteger la lente
La lente del cabezal de corte enfoca el rayo láser sobre la pieza de trabajo. Los contaminantes como el humo, el polvo y los residuos generados durante el proceso de corte pueden dañar la lente o degradar su rendimiento. El gas auxiliar protege la lente de los contaminantes.
- Protección de la lente: el gas auxiliar forma una barrera entre la lente y el área de corte, evitando que los contaminantes alcancen la superficie de la lente y se depositen en ella.
- Mantenimiento de la calidad óptica: al mantener la lente limpia y libre de residuos, el gas auxiliar garantiza un enfoque óptimo del haz y un rendimiento de corte constante.
- Prolongación de la vida útil de las lentes: Prevenir la contaminación reduce el desgaste de las lentes, extendiendo su vida útil y reduciendo los costos de mantenimiento.
Mejorar la reacción de corte
Los gases auxiliares pueden afectar las reacciones químicas que ocurren durante el corte por láser, mejorando así el rendimiento de corte de diferentes materiales. El tipo de gas utilizado puede promover o inhibir ciertas reacciones, lo que puede afectar la calidad y eficiencia del corte.
- Oxígeno (O₂): El oxígeno se utiliza comúnmente para cortar acero al carbono. Promueve una reacción exotérmica con el metal fundido, generando calor adicional, lo que aumenta la velocidad de corte. Esta reacción ayuda a producir un corte limpio con menos escoria, pero puede provocar oxidación en el borde cortado.
- Nitrógeno (N₂): El nitrógeno es un gas inerte que se usa comúnmente para cortar acero inoxidable, aluminio y otros metales no ferrosos. Previene la oxidación formando una atmósfera inerte alrededor de la zona de corte. Esto produce un borde limpio y libre de óxido, lo que lo hace ideal para aplicaciones que requieren un acabado superficial de alta calidad.
- Aire comprimido: el aire comprimido es una alternativa rentable que se puede utilizar para cortar una variedad de materiales. Combina las propiedades del oxígeno y el nitrógeno para proporcionar un rendimiento de corte adecuado a un costo menor. Sin embargo, puede introducir impurezas que afectan la calidad del corte.
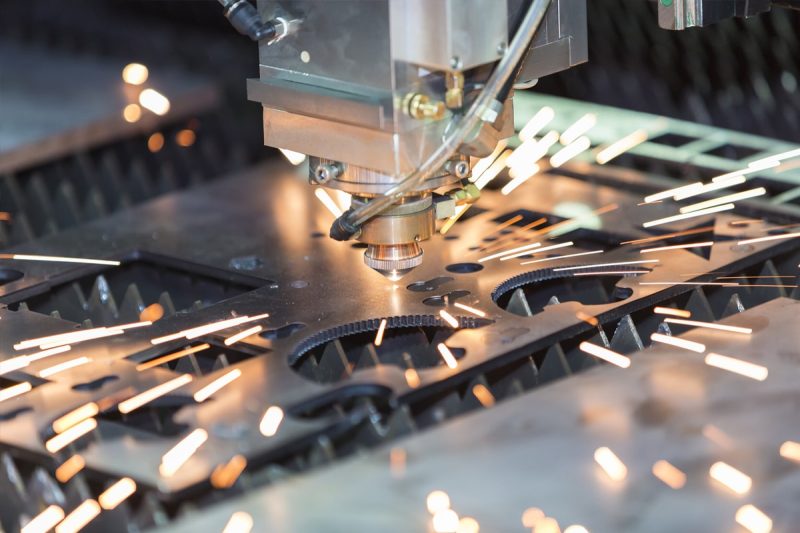
Tipos de gases auxiliares
Oxígeno (O₂)
Ventajas
- Mayor velocidad de corte: el oxígeno reacciona con el material en una reacción exotérmica, liberando calor adicional. Este calor adicional aumenta la velocidad de corte, lo que hace que el corte asistido por oxígeno sea significativamente más rápido, especialmente con materiales más gruesos.
- Eficiencia mejorada: la reacción exotérmica reduce la potencia del láser necesaria para cortar el material, lo que mejora la eficiencia energética general del proceso de corte.
- Cortes más limpios en materiales gruesos: el oxígeno ayuda a producir cortes más limpios en materiales más gruesos, reduciendo la escoria y la escoria, lo que reduce la necesidad de un posprocesamiento extenso.
Desventajas
- Oxidación: la reacción entre el oxígeno y el material puede provocar la oxidación del borde cortado, lo que da como resultado un acabado superficial más áspero y posibles problemas de corrosión.
- Zona afectada por el calor (HAZ): el calor adicional generado por la reacción exotérmica aumenta el tamaño de la HAZ, lo que puede cambiar las propiedades mecánicas del material cerca del borde cortado y causar problemas como deformación o integridad estructural reducida.
- Limitaciones de los metales no ferrosos: el oxígeno no es tan eficaz como los metales no ferrosos como el aluminio y el cobre, que no reaccionan tan fácilmente con el oxígeno.
Nitrógeno (N₂)
Ventajas
- Corte sin oxidación: El nitrógeno es un gas inerte que no reacciona con el material durante el proceso de corte. Esta propiedad previene la oxidación, lo que da como resultado un borde limpio, brillante y libre de óxido que es ideal para aplicaciones que requieren un acabado superficial de alta calidad.
- Acabado superficial de alta calidad: La ausencia de oxidación da como resultado un borde y un acabado superficial más lisos, lo que reduce o elimina la necesidad de posprocesamiento.
- Zona minimizada afectada por el calor (ZAT): El nitrógeno ayuda a mantener una pequeña zona afectada por el calor, preservando las propiedades mecánicas del material y minimizando la deformación térmica. Esto se puede utilizar para lograr cortes de precisión y aplicaciones que requieren tolerancias estrictas.
Desventajas
- Velocidades de corte más lentas: sin la reacción exotérmica proporcionada por el oxígeno, el corte asistido por nitrógeno generalmente da como resultado velocidades de corte más lentas, especialmente con materiales más gruesos. Esta velocidad más lenta afecta la productividad general.
- Mayores requisitos de potencia del láser: dado que el nitrógeno no proporciona calor adicional al proceso de corte, el láser debe proporcionar toda la energía necesaria para cortar el material. Este requisito puede resultar en un mayor consumo de energía y costos operativos.
- Consideraciones de costos: el nitrógeno puede ser más costoso que otros gases y el mayor consumo causado por mayores requisitos de potencia del láser puede aumentar aún más los costos operativos.
Aire comprimido
Ventajas
- Rentable: el aire comprimido está más disponible y es menos costoso que los gases puros como el nitrógeno y el oxígeno. Esto lo convierte en una opción económica para muchas aplicaciones de corte por láser, especialmente aquellas que involucran materiales más delgados.
- Versatilidad: el aire comprimido se puede utilizar para cortar una amplia gama de materiales, incluidos acero dulce, acero inoxidable y aluminio. Su versatilidad lo convierte en una opción práctica para cortes de uso general.
- Costos operativos reducidos: debido a que el aire comprimido es económico y está ampliamente disponible, el uso de aire comprimido puede reducir los costos operativos generales, lo que lo hace adecuado para operaciones a pequeña escala o proyectos con presupuesto limitado.
- Beneficios ambientales: el uso de aire comprimido reduce la dependencia del gas envasado, lo que a su vez reduce la huella de carbono asociada con la producción y el transporte de gas, lo que proporciona un beneficio ambiental.
Desventajas
- Menor calidad del corte: El oxígeno y las impurezas del aire comprimido pueden afectar la calidad del corte, lo que genera bordes más ásperos, mayor escoria y posible contaminación de la superficie de corte. Este problema es particularmente notable en aplicaciones que requieren alta calidad o precisión de la superficie.
- Velocidades de corte limitadas: el aire comprimido generalmente corta a velocidades más lentas que el corte asistido por oxígeno, especialmente para materiales más gruesos. Esta limitación afecta la productividad y puede no ser adecuada para una producción de gran volumen.
- Resultados inconsistentes: La calidad y el rendimiento del corte con aire comprimido pueden ser inconsistentes debido a diferencias en la composición y presión del suministro de aire. Esta inconsistencia hace que sea difícil lograr resultados uniformes de un trabajo de corte a otro.
- Oxidación y formación de escoria: el aire comprimido contiene una variedad de gases, incluido el oxígeno, que pueden causar oxidación y formación de escoria en el borde cortado, lo que requiere un posprocesamiento adicional para lograr los resultados deseados.
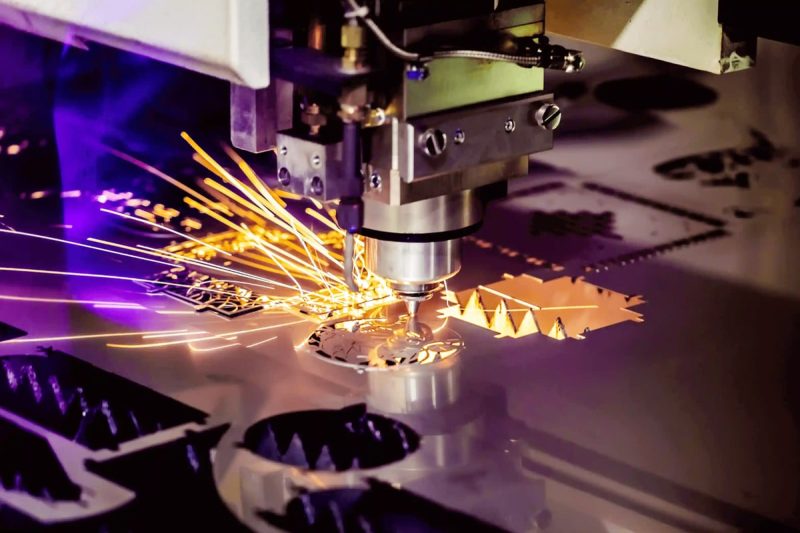
Impacto en diferentes materiales
Acero carbono
Oxígeno
- Ventajas: El oxígeno se utiliza a menudo para cortar acero al carbono porque reacciona exotérmicamente con el material. Esta reacción genera calor adicional, lo que aumenta significativamente la velocidad y la eficiencia de corte. Los cortes resultantes suelen ser limpios con un mínimo de escoria y el calor mejorado ayuda a cortar secciones de acero al carbono más gruesas.
- Desventajas: La reacción exotérmica con el oxígeno provoca oxidación que, si no se trata, puede provocar un acabado superficial más rugoso y posible corrosión. La zona afectada por el calor (ZAT) también es más grande, lo que puede afectar las propiedades mecánicas del material cerca del borde cortado.
Nitrógeno
- Ventajas: El nitrógeno no reacciona con el acero al carbono, evitando la oxidación y produciendo un corte limpio y libre de óxido. Esto da como resultado un acabado superficial de alta calidad y una HAZ más pequeña, que preserva las propiedades mecánicas del material.
- Desventajas: La falta de una reacción exotérmica significa que el corte asistido por nitrógeno es más lento que el corte asistido por oxígeno. Para lograr la misma velocidad de corte, se requiere una mayor potencia del láser, lo que aumenta los costos operativos.
Aire comprimido
- Ventajas: El aire comprimido es una alternativa rentable para cortar acero al carbono. Logra un equilibrio entre costo y rendimiento y es adecuado para cortar secciones más delgadas de acero al carbono.
- Desventajas: El oxígeno del aire comprimido puede provocar cierta oxidación y formación de escoria, lo que afecta la calidad del corte. Las velocidades de corte y la calidad son generalmente más bajas que cuando se utiliza oxígeno o nitrógeno puro.
Acero inoxidable
Oxígeno
- Ventajas: Se puede utilizar oxígeno para cortar acero inoxidable, lo que proporciona velocidades de corte rápidas debido a la reacción exotérmica. Esta reacción también puede ayudar a lograr cortes limpios con un mínimo de escoria.
- Desventajas: El uso de oxígeno puede provocar oxidación, lo que puede provocar la decoloración de los bordes y posibles problemas de corrosión. La capa de óxido puede requerir un posprocesamiento adicional para lograr la calidad superficial deseada.
Nitrógeno
- Ventajas: El nitrógeno es el gas elegido para cortar acero inoxidable porque previene la oxidación, lo que da como resultado un borde limpio, brillante y libre de óxido. La naturaleza inerte del nitrógeno produce cortes de alta calidad con una mínima necesidad de posprocesamiento. El nitrógeno también ayuda a mantener las propiedades mecánicas del material minimizando la zona afectada por el calor.
- Desventajas: El nitrógeno tiene velocidades de corte más lentas y requiere mayor potencia láser que el oxígeno, lo que genera un mayor consumo de energía y costos operativos.
Aire comprimido
- Ventajas: Se puede utilizar aire comprimido para cortar secciones más delgadas de acero inoxidable. Es más rentable que el gas puro y es una opción viable para aplicaciones que no requieren alta precisión.
- Desventajas: El oxígeno en el aire comprimido puede causar oxidación y formación de escoria, afectando la calidad del corte. El borde puede requerir limpieza y acabado adicional después del corte.
Aluminio y metales no ferrosos
Oxígeno
- Ventajas: Generalmente no se recomienda el oxígeno para cortar aluminio y otros metales no ferrosos debido a su alta reflectividad y baja absorción del rayo láser. Sin embargo, en algunos casos, el oxígeno puede ayudar a cortar secciones más gruesas al promover una reacción exotérmica.
- Desventajas: El oxígeno puede causar una oxidación severa, lo que resulta en una superficie de corte áspera y porosa. Esta oxidación puede afectar negativamente a las propiedades y la apariencia del material, requiriendo un postprocesamiento extenso.
Nitrógeno
- Ventajas: El nitrógeno es muy eficaz para cortar aluminio y otros metales no ferrosos. Previene la oxidación, dando como resultado un canto limpio, brillante y de alta calidad. El nitrógeno también ayuda a minimizar la zona afectada por el calor, preservando las propiedades mecánicas del material.
- Desventajas: el corte asistido por nitrógeno es más lento que el uso de oxígeno y requiere una mayor potencia del láser para cortar el material, lo que aumenta los costos operativos.
Aire comprimido
- Ventajas: El aire comprimido es una opción rentable para cortar secciones más delgadas de aluminio y metales no ferrosos. Puede proporcionar un rendimiento de corte satisfactorio para aplicaciones donde la precisión no es crítica.
- Desventajas: El oxígeno en el aire comprimido puede provocar oxidación y formación de escoria, lo que afecta la calidad del corte. Los bordes pueden requerir un posprocesamiento adicional para lograr el acabado deseado.
Materiales no metálicos
Oxígeno
- Ventajas: El oxígeno se puede utilizar para cortar materiales no metálicos como madera, acrílico y plástico. La reacción exotérmica con el oxígeno puede aumentar la velocidad de corte y la eficiencia de algunos materiales.
- Desventajas: El uso de oxígeno puede hacer que materiales como la madera y el acrílico se quemen y quemen, lo que afecta negativamente la calidad de la superficie. Esto puede resultar en la necesidad de procesos de acabado adicionales para lograr la apariencia deseada.
Nitrógeno
- Ventajas: El nitrógeno es muy adecuado para cortar materiales no metálicos, como plásticos y cerámicas, que deben protegerse de la oxidación. Previene la decoloración y produce bordes limpios y de alta calidad al tiempo que minimiza el daño térmico.
- Desventajas: El corte asistido por nitrógeno puede ser más lento que el oxígeno, lo que requiere una mayor potencia del láser para lograr la velocidad de corte deseada.
Aire comprimido
- Ventajas: El aire comprimido es una solución rentable para cortar materiales no metálicos y proporciona un rendimiento de corte adecuado para una variedad de aplicaciones. Es adecuado para aplicaciones donde la precisión y la calidad no son críticas.
- Desventajas: Las impurezas en el aire comprimido pueden afectar la calidad del corte, lo que genera bordes ásperos y posible contaminación. La calidad y velocidad de corte pueden no ser comparables a las de gases puros como el oxígeno o el nitrógeno.
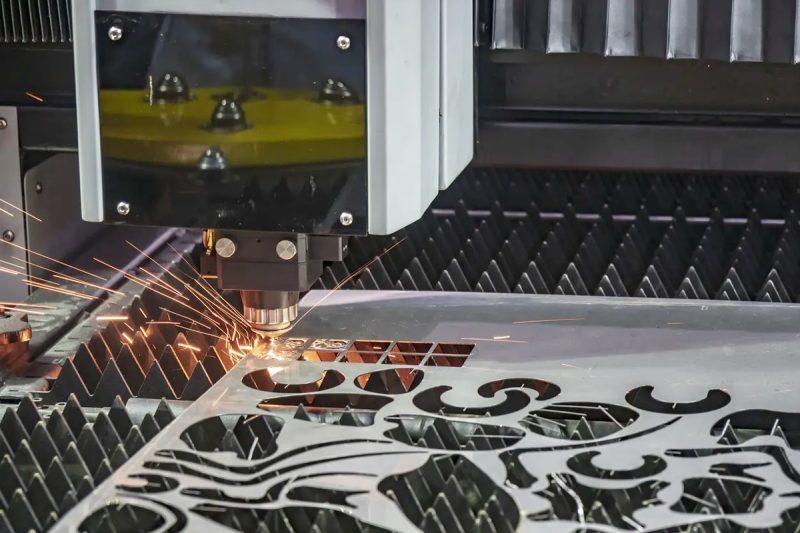
Optimización de la selección del gas auxiliar
Tipo de material y espesor
El tipo y el espesor del material que se corta son consideraciones importantes al seleccionar un gas auxiliar. Los diferentes materiales reaccionan de manera diferente a distintos gases, lo que afecta la calidad y la eficiencia del corte.
- Acero al carbono: el oxígeno suele ser la primera opción para cortar acero al carbono porque reacciona de forma exotérmica, lo que aumenta la velocidad y la eficiencia del corte. Para aceros al carbono más gruesos, el oxígeno puede proporcionar el calor necesario para cortar el material de manera efectiva. Para aceros al carbono más delgados, se puede utilizar nitrógeno para lograr un corte limpio y libre de oxidación, aunque a un ritmo más lento.
- Acero inoxidable: El nitrógeno es ideal para cortar acero inoxidable porque previene la oxidación y produce un borde liso y de alta calidad. Para acero inoxidable muy grueso, se puede utilizar oxígeno para aumentar la velocidad de corte, pero provocará oxidación y requerirá un posprocesamiento.
- Aluminio y metales no ferrosos: El nitrógeno es la primera opción para cortar aluminio y metales no ferrosos para evitar la oxidación y lograr un corte limpio. Para aplicaciones menos críticas, el aire comprimido puede ser una alternativa rentable, aunque puede provocar cierta oxidación.
- Materiales no metálicos: para cortar materiales no metálicos como plásticos, cerámica y madera, a menudo se utiliza nitrógeno para evitar la decoloración y lograr un borde de alta calidad. El oxígeno se puede utilizar para cortar ciertos no metales más rápido, pero puede provocar quemaduras o quemaduras.
Calidad de corte requerida
La calidad de corte requerida es un factor clave a la hora de seleccionar el gas auxiliar adecuado. Las aplicaciones de precisión suelen requerir un corte de alta calidad con oxidación mínima y bordes lisos.
- Acabado superficial de alta calidad: el nitrógeno suele ser la mejor opción para aplicaciones que requieren cortes precisos, limpios y libres de oxidación. Previene la oxidación, lo que da como resultado bordes lisos y un acabado superficial de alta calidad.
- Calidad general: El oxígeno puede proporcionar un corte de alta calidad con un mínimo de escoria, pero los bordes pueden requerir una limpieza adicional debido a la oxidación. El aire comprimido puede ser adecuado para aplicaciones menos críticas donde no es necesario un acabado superficial de la más alta calidad.
Velocidad de corte y eficiencia
La velocidad de corte y la eficiencia se ven afectadas por el tipo de gas auxiliar utilizado. El objetivo es lograr la mayor velocidad posible sin comprometer la calidad del corte.
- Velocidad máxima: Proporciona las velocidades de corte más rápidas para acero al carbono y materiales más gruesos debido a la reacción exotérmica del oxígeno, que agrega calor adicional al proceso de corte.
- Velocidad y calidad equilibradas: el nitrógeno logra un equilibrio entre velocidad y cortes de alta calidad, aunque puede requerir una mayor potencia del láser y cortes a una velocidad más lenta en comparación con el oxígeno.
- Velocidad rentable: el aire comprimido ofrece un compromiso entre velocidad y costo, adecuado para aplicaciones donde son aceptables velocidades de corte moderadas y una calidad razonable.
Consideraciones de costos
El costo es un factor importante para ayudar en la selección del gas, lo que afecta los gastos operativos y la rentabilidad general.
- Costos operativos reducidos: el aire comprimido es la opción más económica porque está fácilmente disponible y es más barato que los gases puros como el oxígeno y el nitrógeno. Es ideal para cortar materiales menos críticos o cuando las limitaciones presupuestarias son una prioridad.
- Mayor calidad y mayor costo: El nitrógeno, aunque es más caro, proporciona una mejor calidad de corte. El coste adicional se justifica por la mejora de la calidad y la menor necesidad de posprocesamiento.
- Equilibrio entre costo y eficiencia: El oxígeno ofrece un término medio, ya que proporciona velocidades de corte rápidas y una calidad razonable a un costo moderado. Es adecuado para muchas aplicaciones industriales donde tanto la velocidad como la calidad son importantes.
Requisitos de posprocesamiento
Las necesidades de posprocesamiento pueden influir en la selección del gas auxiliar, ya que algunos gases producen cortes más limpios, lo que puede reducir el trabajo de acabado.
- Postprocesamiento mínimo: el nitrógeno produce cortes limpios y libres de oxidación, lo que reduce la necesidad de un posprocesamiento extenso y ahorra tiempo y costos en las operaciones de acabado.
- Postprocesamiento moderado: el corte con oxígeno puede requerir pasos adicionales para eliminar los óxidos y lograr el acabado superficial deseado. Sin embargo, velocidades de corte más rápidas pueden compensar algunos de los costos adicionales.
- Mayor posprocesamiento: el aire comprimido puede causar más escoria y oxidación, lo que requiere un posprocesamiento más extenso para limpiar y terminar el borde. Esto puede aumentar el tiempo y el costo general de producción.
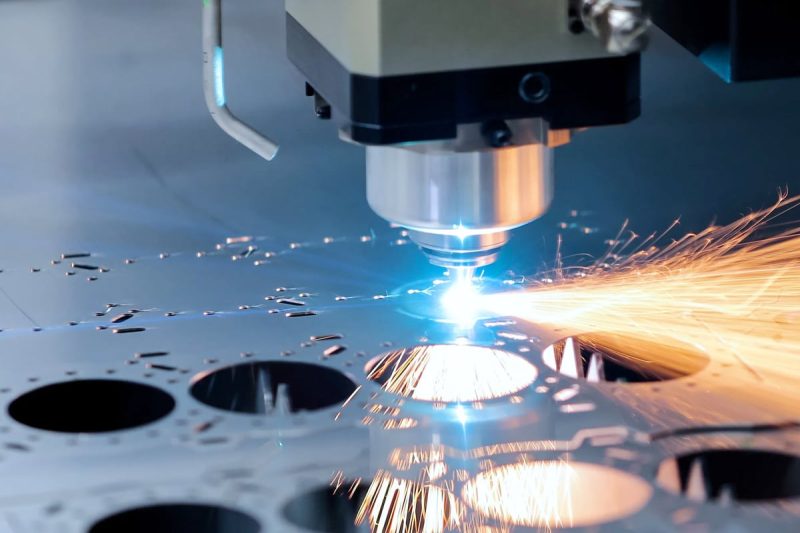
Resumen
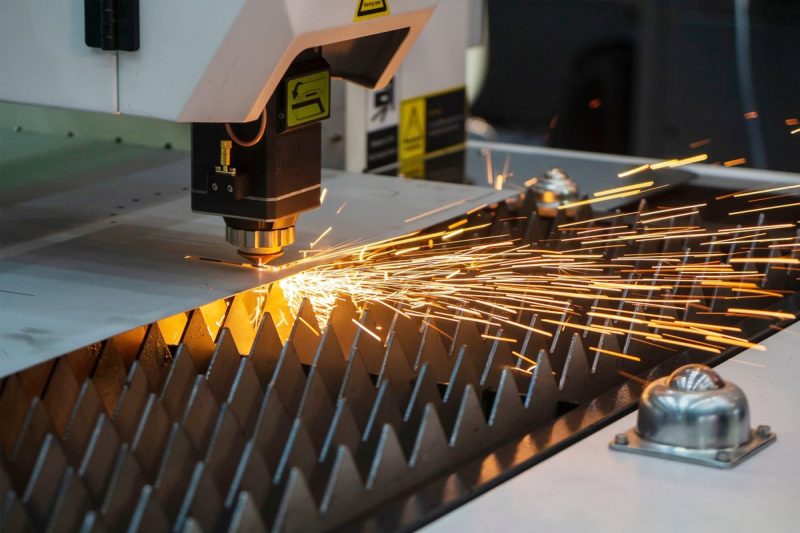
Obtenga soluciones de corte por láser
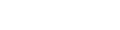
- [email protected]
- [email protected]
- +86-19963414011
- No. 3 Zona A, Zona Industrial de Lunzhen, Ciudad de Yucheng, Provincia de Shandong.