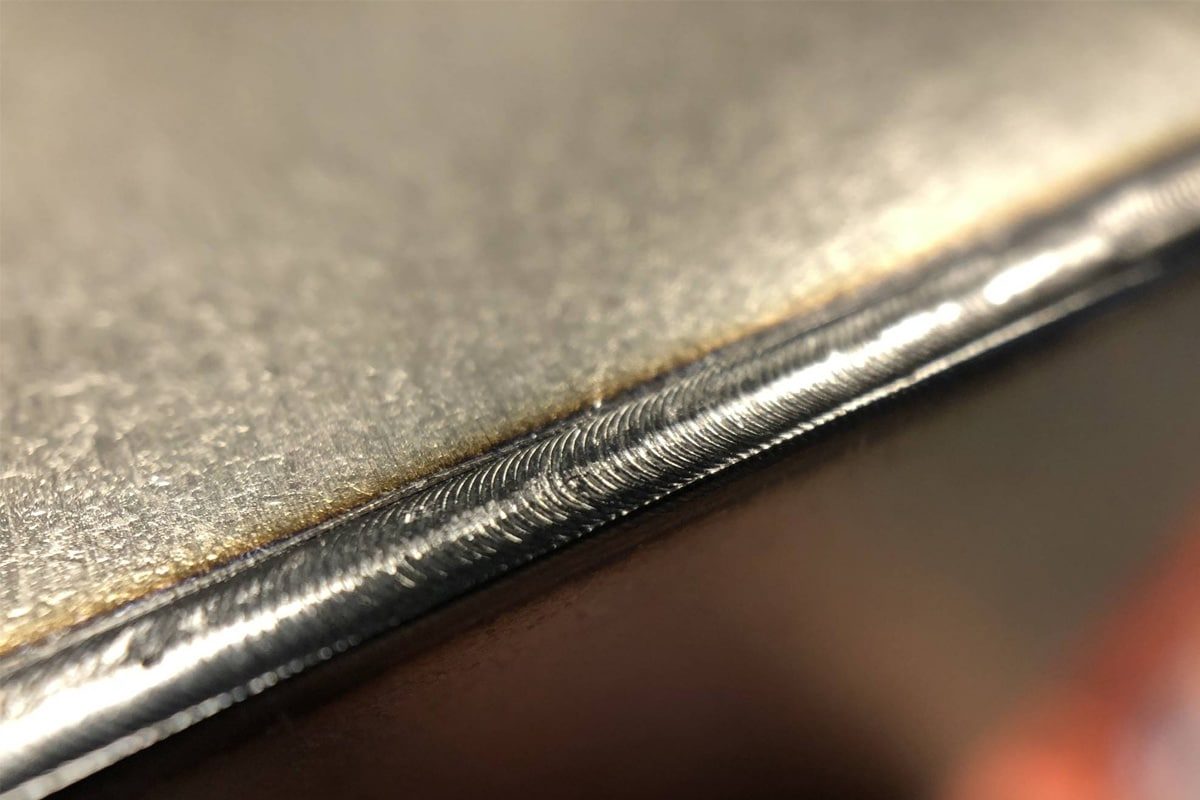
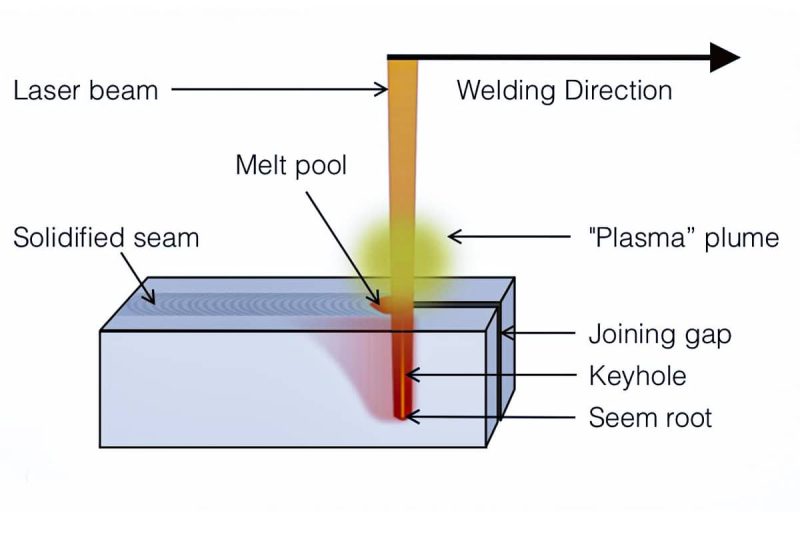
Comprensión de la soldadura láser
Conceptos básicos de la soldadura láser
Tipo de soldadura láser
- Soldadura láser de onda continua: adecuada para necesidades de soldadura de alta intensidad y a largo plazo, ampliamente utilizada para la conexión y sellado de placas de metal gruesas.
- Soldadura láser pulsada: calienta el material a través de pulsos de alta energía de corta duración, más adecuado para soldar placas delgadas o microcomponentes, con mayor precisión de control.
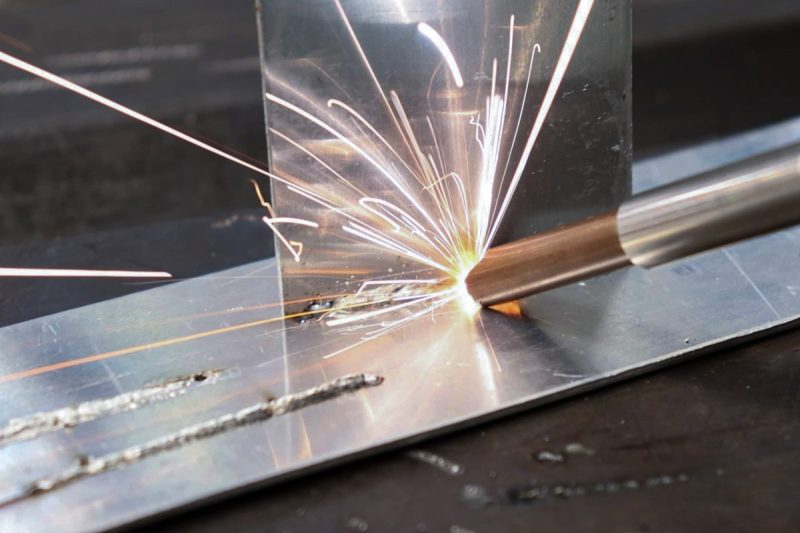
Factores que afectan el ancho de la soldadura
Parámetros del láser
- Potencia del láser: La potencia del láser es uno de los parámetros más críticos que afectan a los resultados de la soldadura. Cuanto mayor sea la potencia del láser, más calor se genera y también aumenta el volumen de la zona afectada por el calor y el baño de fusión, lo que aumenta el ancho de la soldadura. Por el contrario, si la potencia es demasiado baja, no puede proporcionar suficiente energía para fundir el material y la junta de soldadura puede ser insuficiente, lo que da como resultado una soldadura estrecha o una soldadura incompleta. Por lo tanto, la potencia del láser debe seleccionarse razonablemente de acuerdo con el grosor, el tipo y la velocidad de soldadura del material para lograr el ancho óptimo de la soldadura.
- Velocidad de soldadura: La velocidad de soldadura tiene una influencia importante en el aporte de calor. Cuando la velocidad de soldadura es lenta, el láser permanece en el área de soldadura durante más tiempo, lo que da como resultado una mayor transferencia de calor al material base, formando un baño de fusión más grande y una zona afectada por el calor, lo que aumenta el ancho de la soldadura. Por el contrario, una velocidad de soldadura demasiado rápida reducirá el aporte de calor, lo que dará como resultado una soldadura incompleta, soldaduras demasiado estrechas y posiblemente soldaduras débiles. Por lo tanto, el control razonable de la velocidad de soldadura es la clave para garantizar el ancho de soldadura adecuado.
- Longitud de onda: La longitud de onda del láser determina cómo interactúa el láser con el material. Los láseres de longitud de onda corta (como los emitidos por los generadores láser de fibra) pueden ser mejor absorbidos por los materiales metálicos porque tienen una mayor concentración de energía y pueden proporcionar más energía en un área más pequeña, mejorando así la eficiencia de la soldadura y haciendo que la soldadura sea más estrecha. En términos relativos, los láseres de longitud de onda larga (como los emitidos por los tubos láser de CO2) tienen una mala absorción de los materiales metálicos y la distribución de energía durante la soldadura es relativamente amplia, lo que conduce fácilmente a un mayor ancho de soldadura. Por lo tanto, los láseres de longitud de onda corta son más adecuados para la soldadura de alta precisión.
- Duración del pulso: la soldadura láser pulsada tiene la ventaja única de optimizar la soldadura mediante el ajuste de la duración del pulso. Cuanto más corta sea la duración del pulso, más corto será el tiempo de entrada de calor del láser, lo que ayuda a reducir la expansión de la zona afectada por el calor y a formar una soldadura más pequeña. Las duraciones de pulso más largas dan como resultado una mayor entrada de calor y una soldadura más ancha. A través de la tecnología de modelado de pulso, el ancho y el intervalo del pulso del láser se pueden controlar con precisión para optimizar la distribución del calor y la morfología de la soldadura durante la soldadura.
- Calidad del haz: La calidad y el control del enfoque del haz láser son fundamentales para la precisión de la soldadura. Los láseres con una mejor calidad del haz tienen tamaños de enfoque más pequeños y una energía más concentrada, lo que puede lograr una soldadura de mayor precisión. Una mayor calidad del haz ayuda a reducir la difusión del calor, de modo que el calor se concentra más en el área de soldadura y el ancho de la soldadura se vuelve más pequeño. Si la calidad del haz es deficiente, provocará una distribución desigual de la energía del láser, lo que aumentará el ancho de la soldadura.
Propiedades materiales
- Tasa de absorción: La tasa de absorción del material por el láser afecta directamente el efecto de la soldadura. La tasa de absorción de los materiales metálicos suele ser alta, especialmente cuando el láser de longitud de onda corta se combina con el metal, la tasa de absorción se mejora aún más. En el proceso de soldadura láser, una mayor tasa de absorción significa que la energía del láser se puede convertir de manera efectiva en energía térmica, lo que da como resultado una soldadura más pequeña. Por el contrario, si la tasa de absorción del material es baja, la tasa de utilización efectiva de la energía del láser es deficiente, lo que puede provocar que la soldadura sea demasiado ancha o incompleta.
- Conductividad térmica: La conductividad térmica del material afecta la velocidad de difusión del calor en el sustrato. Los materiales con mayor conductividad térmica (como cobre y aluminio) dispersará rápidamente el calor, lo que dará como resultado una dispersión excesiva del calor en el área de soldadura y soldaduras más anchas. Por el contrario, los materiales con menor conductividad térmica (como acero inoxidable) puede mantener más calor concentrado en el área de soldadura, formando una soldadura más estrecha. Por lo tanto, al soldar materiales con diferentes conductividades térmicas, es necesario ajustar los parámetros de soldadura de acuerdo con sus propiedades térmicas para garantizar que el ancho de soldadura sea apropiado.
- Reflectividad: Los materiales con alta reflectividad (como el aluminio y el cobre) producirán una mayor reflexión del láser y reducirán la eficiencia de absorción de la energía láser, lo que afectará la calidad de la soldadura y puede hacer que aumente el ancho de la soldadura. Para superar este problema, puede elegir un tipo de láser que sea adecuado para materiales altamente reflectantes (como usar un láser de longitud de onda corta) o aumentar la potencia del láser para compensar la pérdida de reflexión. Además, usar un haz enfocado y una longitud de onda láser adecuada también puede ayudar a aumentar la tasa de absorción láser de los materiales reflectantes.
Entorno de soldadura
- Gas de protección: El gas de protección desempeña un papel importante en la soldadura láser. No solo evita la oxidación y la contaminación durante la soldadura, sino que también afecta la conducción de calor y el ancho de la soldadura al controlar el flujo de gas. Por ejemplo, el argón y el nitrógeno se utilizan a menudo como gases de protección en la soldadura láser. Pueden reducir eficazmente el alcance de la zona afectada por el calor y evitar la generación de soldaduras excesivas. La selección y el control del gas de protección deben ajustarse según los materiales específicos y los requisitos de soldadura.
- Condiciones ambientales: Los factores ambientales como la temperatura y la humedad también tienen un cierto impacto en el efecto de la soldadura láser. En entornos de baja temperatura, la conductividad térmica de los materiales metálicos puede cambiar, lo que afecta la gestión térmica durante la soldadura. Además, los entornos con alta humedad pueden provocar la dispersión de la energía láser y afectar la calidad de la soldadura. Las condiciones ambientales estables ayudan a mantener la estabilidad del haz láser y garantizan la consistencia del ancho de la soldadura durante la soldadura.
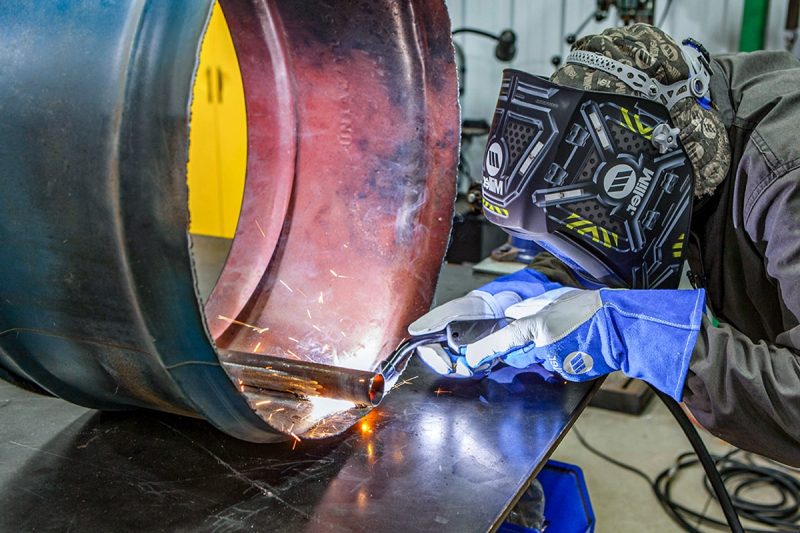
Tecnología para lograr un ancho de soldadura mínimo
Selección del tipo de láser
- Generador de láser de fibra: El generador de láser de fibra es una de las fuentes láser más utilizadas en la soldadura láser. Tiene alta potencia, alta calidad de haz y excelente capacidad de enfoque. El haz del generador de láser de fibra se puede enfocar con precisión en un área muy pequeña, lo que hace que el ancho de soldadura sea menor y pueda procesar materiales de placa delgada de manera eficiente. Los generadores de láser de fibra son muy adecuados para tareas de soldadura rápida y de alta precisión y pueden lograr pequeñas soldaduras de alta calidad y reducir la expansión de la zona afectada por el calor (ZAT) del material.
- Tubo láser de CO2: el tubo láser de CO2 es otra fuente láser que se utiliza habitualmente para la soldadura de metales. Aunque la calidad del haz de los tubos láser de CO2 no suele ser tan buena como la de los generadores láser de fibra, puede proporcionar mayor potencia y mayor profundidad de penetración, lo que resulta adecuado para soldar materiales más gruesos. Aunque no es tan preciso como el láser de fibra, se pueden conseguir anchos de soldadura relativamente pequeños mediante una regulación de potencia razonable y una velocidad de soldadura optimizada.
Selección de longitud de onda del láser
Optimización de parámetros láser
- Ajuste de la potencia del láser: La potencia del láser es el factor principal que afecta la entrada de calor de la soldadura. Una potencia excesiva hará que el calor excesivo se extienda al área circundante, ensanchando así la soldadura e incluso provocando defectos de soldadura. Reducir adecuadamente la potencia puede ayudar a reducir la entrada de calor y reducir el ancho de la soldadura, especialmente cuando se sueldan materiales de placa delgada. Sin embargo, una potencia demasiado baja puede dar como resultado una soldadura inadecuada. Por lo tanto, un ajuste razonable de la potencia del láser para que coincida con las propiedades del material, la velocidad de soldadura y los requisitos de soldadura puede lograr una soldadura precisa y controlar eficazmente el ancho de la soldadura.
- Tecnología de modelado de pulsos: la tecnología de soldadura láser de pulsos puede controlar con precisión la entrada de calor durante la soldadura ajustando la frecuencia, la duración y la energía del pulso láser. Cuanto más corto sea el ancho del pulso, más corto será el tiempo de entrada de calor y menor será la acumulación de calor en el área de soldadura, lo que hace que la soldadura sea más estrecha. Además, al ajustar la frecuencia y la energía del pulso, se puede controlar la velocidad de soldadura y la morfología del baño de fusión, lo que a su vez afecta el ancho de la soldadura. Usando la tecnología de modelado de pulsos, especialmente en la micro soldadura, la distribución de calor de cada pulso se puede controlar con precisión para lograr efectivamente el ancho de soldadura mínimo.
- Control del enfoque del haz: La precisión y el ancho de la soldadura de la soldadura láser están estrechamente relacionados con la posición focal del haz. Cuanto menor sea el enfoque del haz láser, mayor será la densidad de energía, que se puede concentrar en el área de soldadura, produciendo así una soldadura estrecha y fina. Por lo tanto, el control del enfoque del láser es muy importante. Al ajustar la posición del enfoque, la energía del haz láser se puede concentrar más en el área de soldadura, evitando la difusión del calor al área circundante y, por lo tanto, reduciendo el ancho de la soldadura.
Preparación de materiales
- Limpieza de la superficie: La limpieza de la superficie del material de soldadura afecta directamente el efecto de la soldadura láser. Los óxidos, el aceite, el óxido y otros contaminantes en la superficie afectarán la tasa de absorción del láser, lo que provocará la incapacidad de concentrar eficazmente el calor en el área de soldadura, lo que afectará la calidad de la soldadura y aumentará el ancho de la soldadura. Asegurarse de que la superficie de soldadura esté limpia y libre de contaminación es un requisito previo para optimizar la calidad de la soldadura. Los contaminantes de la superficie generalmente se pueden eliminar mediante limpieza química, limpieza mecánica o limpieza láser.
- Recubrimiento de superficies: En algunos casos, especialmente en el caso de materiales que son difíciles de soldar, el recubrimiento de superficies puede mejorar significativamente la eficiencia de absorción del láser. Los materiales de recubrimiento (como el recubrimiento de cobre, el recubrimiento de zinc, etc.) pueden mejorar la interacción entre el láser y el material y mejorar la acumulación de calor en el área de soldadura, lo que ayuda a controlar con precisión el ancho de la soldadura durante el proceso de soldadura. Además, los recubrimientos especiales también pueden mejorar la estabilidad del baño de fusión durante la soldadura y reducir los defectos durante la soldadura.
Tecnología avanzada de soldadura
- Soldadura láser híbrida: la tecnología de soldadura láser híbrida combina las ventajas de los métodos de soldadura láser y tradicionales (como la soldadura TIG o la soldadura MIG), y mejora la entrada de calor y la precisión de la soldadura al combinar las ventajas de diferentes fuentes de calor. La combinación de métodos de soldadura láser y tradicionales puede reducir eficazmente el ancho de la soldadura, especialmente al soldar materiales más gruesos. La tecnología de soldadura láser híbrida puede proporcionar una mayor estabilidad del baño de fusión y zonas afectadas por el calor más pequeñas, logrando así efectos de soldadura más refinados.
- Tecnología de microsoldadura: La microsoldadura láser es una tecnología de soldadura de alta precisión para procesar soldaduras ultrapequeñas, especialmente adecuada para unir piezas pequeñas. La tecnología de microsoldadura utiliza pulsos láser finamente controlados para lograr una transferencia de energía eficiente en un área de soldadura muy pequeña, lo que garantiza la formación de soldaduras muy estrechas. La microsoldadura se usa comúnmente en industrias como la electrónica, los instrumentos de precisión y los dispositivos médicos, y puede lograr una alta precisión de soldadura y minimizar el impacto térmico del área de soldadura.
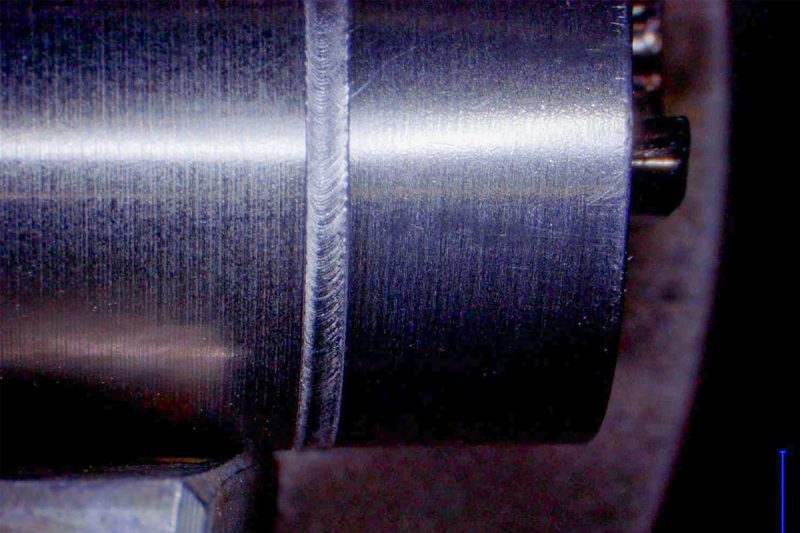
Desafíos y soluciones
Gestión térmica
Desafío
Solución
- Utilice un gas auxiliar de refrigeración: el uso de un gas de protección o un gas auxiliar (como argón, nitrógeno u oxígeno) adecuado no solo puede evitar la oxidación del área de soldadura, sino que también elimina eficazmente el exceso de calor generado durante la soldadura, lo que reduce la expansión de la zona afectada por el calor. El caudal y la presión del gas auxiliar deben optimizarse según el material de soldadura, la velocidad de soldadura y la potencia del láser para garantizar el mejor efecto de refrigeración.
- Optimización de la velocidad de soldadura: aumentar adecuadamente la velocidad de soldadura puede reducir la entrada de calor por unidad de tiempo y reducir el tiempo de calentamiento del material, evitando así de manera eficaz el sobrecalentamiento del área de soldadura. Las velocidades de soldadura más altas pueden hacer que el calor se extienda rápidamente a un área más grande, reducir el aumento de temperatura local y, por lo tanto, controlar el ancho de la soldadura y la zona afectada por el calor.
- Regulación de la fuente de calor: ajustando la potencia del láser o utilizando un láser pulsado, se puede controlar con precisión la entrada de calor durante el proceso de soldadura. Especialmente en la soldadura pulsada, los pulsos cortos y las frecuencias de pulso más altas pueden garantizar que el calor se concentre y distribuya rápidamente en el área de soldadura para evitar la difusión del calor.
Reflectividad del material
Desafío
Solución
- Utilice láseres de longitud de onda corta: los láseres de longitud de onda corta (como los producidos por los generadores de láser de fibra) tienen una mayor tasa de absorción para materiales altamente reflectantes. Los láseres de longitud de onda corta pueden ser mejor absorbidos por los materiales, reducen los reflejos y garantizan que se utilice más energía láser de manera efectiva en el proceso de soldadura, mejorando así la eficiencia de la soldadura y reduciendo el ancho de la soldadura. En comparación con los láseres de CO2 de longitud de onda larga, los generadores de láser de fibra son más adecuados para procesar materiales con mayor reflectividad.
- Ajuste de la potencia del láser: para materiales con alta reflectividad, la reducción adecuada de la potencia del láser puede evitar una reflexión excesiva de energía. Los ajustes de potencia más bajos ayudan a reducir las reflexiones y evitar el desperdicio de energía, lo que permite controlar eficazmente el ancho de la soldadura y optimizar la calidad de la misma.
- Utilice materiales recubiertos: algunos materiales metálicos altamente reflectantes, como el aluminio y el cobre, pueden utilizar tecnología de recubrimiento, como recubrimiento de aluminio, recubrimiento de cobre y otros métodos de tratamiento de superficies. Estos recubrimientos tienen una reflectividad menor, lo que puede mejorar la eficiencia de absorción del láser y reducir la interferencia de la reflexión en el proceso de soldadura, lo que permite controlar mejor el ancho de la soldadura.
Estabilidad del proceso
Desafío
Solución
- Sistema avanzado de control láser: mediante el uso de sistemas avanzados de control láser, se pueden monitorear y ajustar en tiempo real parámetros clave como la potencia del láser, la velocidad de soldadura, el enfoque del haz, etc. para garantizar la consistencia de los parámetros del láser durante cada proceso de soldadura. Los sistemas de soldadura láser modernos suelen estar equipados con sensores de alta precisión y funciones de ajuste automático, que pueden detectar la temperatura del área de soldadura, la morfología del baño de fusión y la posición del haz en tiempo real, y ajustar automáticamente la salida del láser para mantener la estabilidad del proceso de soldadura.
- Retroalimentación en tiempo real y control de bucle cerrado: el uso de la tecnología de retroalimentación en tiempo real y control de bucle cerrado permite ajustar los parámetros en tiempo real durante el proceso de soldadura para hacer frente a los cambios en las propiedades del material y el entorno de soldadura. Por ejemplo, los sensores pueden monitorear el tamaño, la forma y la temperatura del baño de fusión, y el sistema puede ajustar automáticamente la potencia del láser y la velocidad de soldadura para mantener la consistencia de la calidad de la soldadura. Esta tecnología puede mejorar significativamente la confiabilidad del proceso de soldadura y evitar problemas de soldadura causados por fluctuaciones del proceso.
- Optimización de la trayectoria de soldadura: Durante el proceso de soldadura, optimizar la planificación de la trayectoria del láser es otra forma importante de mejorar la estabilidad del proceso. Al controlar con precisión la trayectoria y la secuencia de soldadura, se pueden reducir la deformación del material y los cambios en la zona afectada por el calor, lo que garantiza una distribución uniforme de la temperatura durante cada proceso de soldadura y, por lo tanto, se logran resultados de soldadura estables.
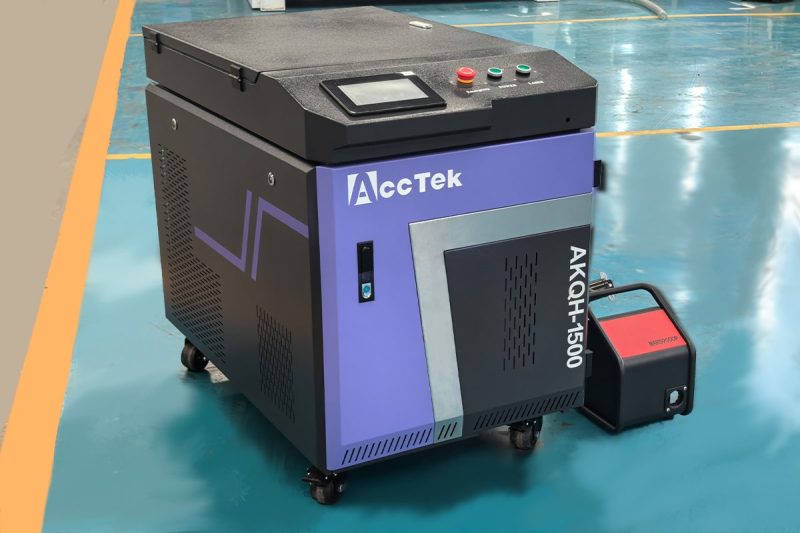
Resumir
En este proceso, nuestro máquinas de soldadura láser se han convertido en líderes de la industria con su tecnología superior y diseño innovador. Las máquinas de soldadura láser de nuestra empresa utilizan la última tecnología de láser de fibra, que puede lograr una soldadura eficiente al tiempo que garantiza un control preciso de la temperatura durante el proceso de soldadura, controlando así de manera efectiva el ancho de la soldadura y reduciendo la zona afectada por el calor. Nuestro equipo de soldadura no solo tiene capacidades de ajuste de haz láser de alta precisión, sino que también está equipado con un sistema de control de temperatura avanzado que puede ajustar automáticamente los parámetros durante el proceso de soldadura, optimizando así el efecto de soldadura y asegurando una calidad estable y constante en cada punto de soldadura.
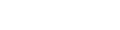
- [email protected]
- [email protected]
- +86-19963414011
- No. 3 Zona A, Zona Industrial de Lunzhen, Ciudad de Yucheng, Provincia de Shandong.