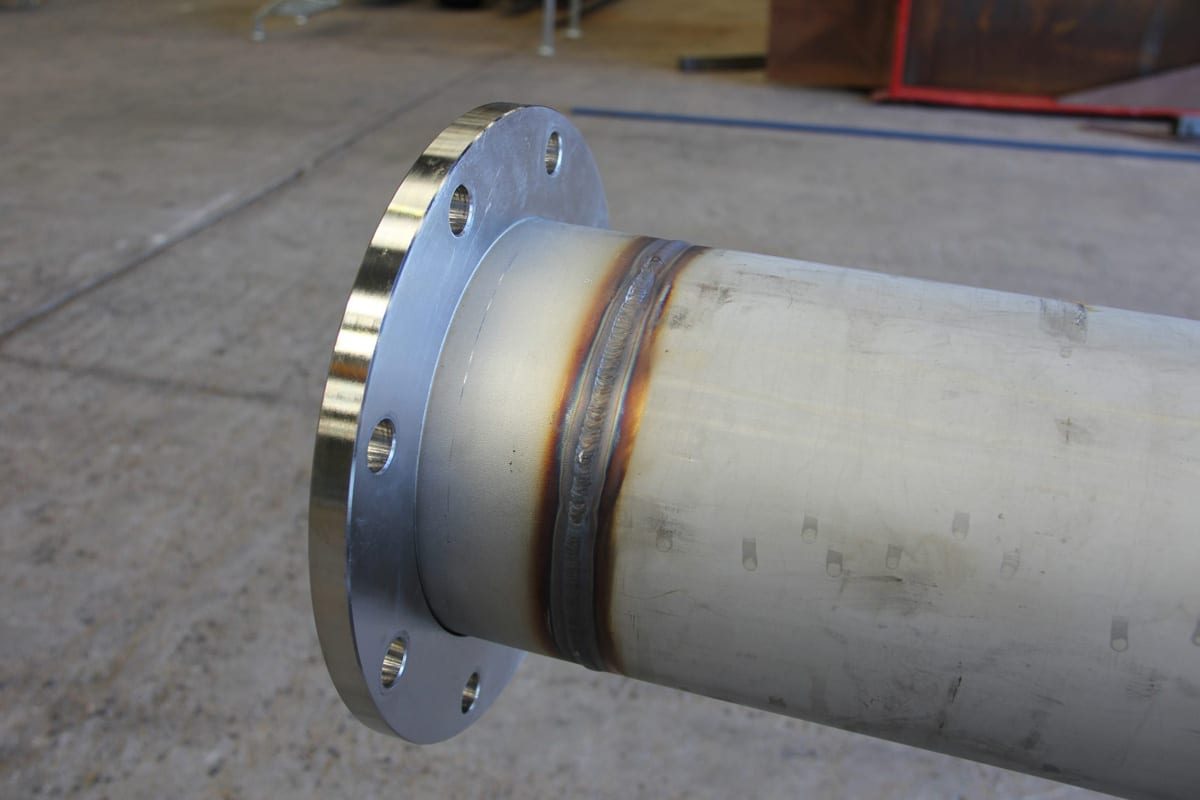
Cómo mejorar la resistencia de las uniones soldadas con láser
La soldadura láser se ha utilizado ampliamente en las industrias de fabricación de automóviles, aeroespacial y electrónica como una tecnología de soldadura eficiente y precisa debido a su bajo aporte de calor, soldadura de penetración profunda y excelentes capacidades de automatización. Esta tecnología puede mejorar en gran medida la eficiencia de la producción al tiempo que garantiza la calidad de la soldadura y reduce la deformación del material y los pasos de procesamiento. Por lo tanto, la soldadura láser se ha convertido en un medio indispensable e importante en la fabricación moderna.
Sin embargo, la resistencia de las uniones soldadas está directamente relacionada con el rendimiento y la confiabilidad de los productos, especialmente en aplicaciones sujetas a entornos de trabajo complejos o de alto estrés. Cómo optimizar los materiales, los procesos y los diseños para mejorar aún más la resistencia de las uniones soldadas es una cuestión clave en la investigación y el desarrollo de tecnología y en las aplicaciones industriales. Este artículo comenzará con los principales factores que afectan la resistencia de la soldadura, analizará en detalle las tecnologías avanzadas para mejorar la resistencia, explorará la importancia del tratamiento posterior a la soldadura y brindará soluciones a los desafíos comunes.
Tabla de contenido
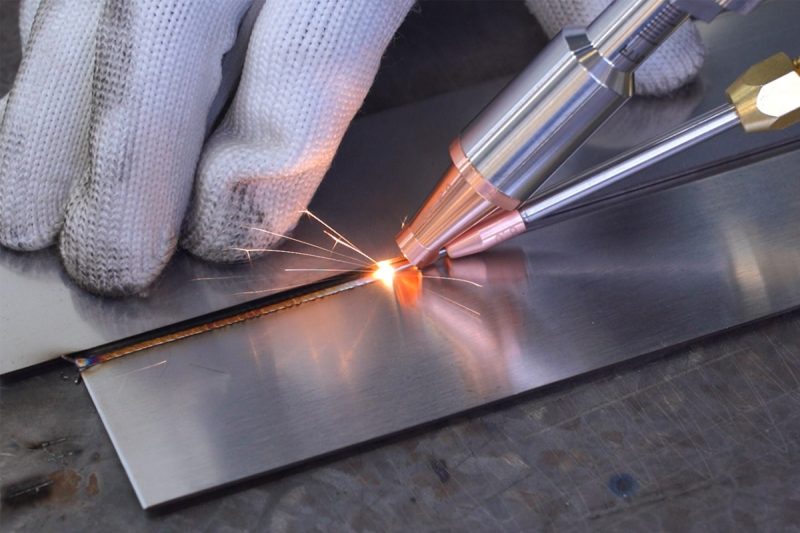
Aprenda sobre la soldadura láser
La soldadura láser utiliza un haz láser de alta energía como fuente de calor, que se puede enfocar en un punto muy pequeño para lograr un aporte de calor bajo y efectos de soldadura de penetración profunda. Las ventajas únicas de esta tecnología son su precisión y flexibilidad, lo que la hace particularmente adecuada para estructuras geométricas complejas, requisitos de alta precisión y áreas de soldadura de difícil acceso. En comparación con los métodos de soldadura tradicionales, la soldadura láser no solo puede reducir significativamente la deformación térmica y la tensión residual, sino que también mejora la velocidad de procesamiento y la eficiencia de producción.
Además, máquina de soldadura láser Se puede aplicar a la conexión de una variedad de materiales, incluidos varios metales y materiales de aleación, y desempeña un papel vital, especialmente en el contexto de la creciente demanda de componentes livianos y de alta resistencia en la industria manufacturera. Sin embargo, si bien se logra una soldadura eficiente, la resistencia de la unión soldada sigue siendo un problema clave que afecta el rendimiento y la confiabilidad del producto. Esto requiere una mejora continua de la calidad de la soldadura mediante la optimización de materiales, procesos y diseños para satisfacer las necesidades de aplicaciones industriales de alto estándar.
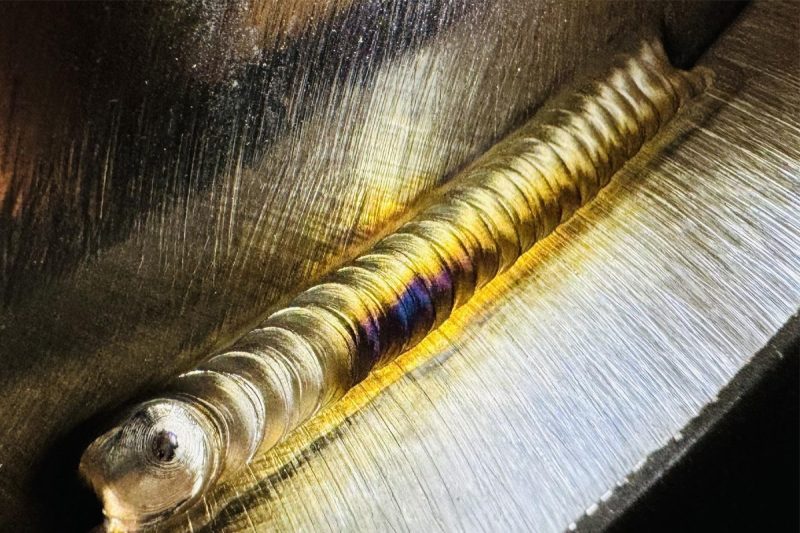
Factores que afectan la resistencia de la soldadura
La resistencia de las uniones soldadas por láser se ve afectada por una combinación de factores, entre los que se incluyen las propiedades del material, los parámetros del láser, el diseño de la unión y el entorno de soldadura. Para lograr uniones soldadas de alta calidad, es necesario tener un conocimiento profundo del papel específico de estos factores y su influencia mutua, para optimizar cada vínculo en aplicaciones prácticas. A continuación, analizaremos estos factores en detalle.
Propiedades materiales
Las propiedades del material son una base importante para determinar los resultados de la soldadura, que se manifiestan principalmente en la composición del material base, el espesor del material y el estado de la superficie.
- Composición del sustrato: Los distintos materiales tienen diferentes índices de absorción de los láseres. Por ejemplo, los metales muy reflectantes (como el aluminio y el cobre) tienen índices de absorción bajos de la energía láser, lo que puede provocar fácilmente una penetración insuficiente. Es necesario mejorar el efecto de la soldadura ajustando los parámetros del láser o recubriendo la superficie con materiales absorbentes.
- Grosor del material: el grosor del material afecta directamente la distribución de energía del láser. Los materiales demasiado gruesos pueden provocar una penetración insuficiente del láser, lo que da como resultado soldaduras con penetración incompleta; mientras que los materiales demasiado delgados son propensos a quemarse debido al exceso de energía del láser, lo que requiere un ajuste cuidadoso de los parámetros.
- Estado de la superficie: la limpieza, la película de óxido y la rugosidad de la superficie del material afectarán la transmisión y la absorción del láser. La contaminación o la oxidación de la superficie pueden provocar la formación desigual de un baño de fusión y reducir la resistencia de la soldadura. Por lo tanto, es esencial realizar una limpieza previa a la soldadura y un tratamiento adecuado de la superficie.
Parámetros del láser
Los parámetros del láser determinan directamente el aporte de calor y la formación del baño de fusión durante la soldadura.
- Potencia del láser: una potencia demasiado baja puede provocar una penetración insuficiente y debilitar la resistencia de la soldadura, mientras que una potencia demasiado alta puede provocar fácilmente la perforación del material o la formación de un baño de fusión excesivamente grande, lo que debilita la resistencia de la unión soldada. Por lo tanto, es necesario seleccionar el nivel de potencia adecuado según las propiedades y el espesor del material.
- Velocidad de soldadura: Una velocidad de soldadura demasiado rápida puede provocar una formación insuficiente de baño de fusión y pueden aparecer poros o grietas en la soldadura; mientras que una velocidad demasiado lenta puede provocar una entrada de calor excesiva, causando sobrecalentamiento o incluso la deformación del material.
- Posición del foco: la posición precisa del foco del láser ayuda a maximizar el uso eficaz de la energía y a garantizar la profundidad y uniformidad del baño de fusión. La desviación del foco reducirá la eficiencia de la soldadura y puede causar defectos de calidad.
- Parámetros del pulso: En la soldadura láser pulsada, la configuración del ancho y la frecuencia del pulso afecta directamente el proceso de formación y solidificación del baño de fusión. La optimización de los parámetros del pulso puede reducir la generación de grietas y poros y mejorar la resistencia de la soldadura.
Diseño de conectores
El diseño de la unión no solo afecta la facilidad de soldadura sino que también está directamente relacionado con las propiedades mecánicas y la confiabilidad de la soldadura.
- Configuración de la junta: Los distintos tipos de juntas (como juntas a tope y juntas traslapadas) son adecuados para distintos requisitos estructurales y de rendimiento mecánico. Por ejemplo, las juntas a tope son adecuadas para soldaduras de alta resistencia, mientras que las juntas traslapadas son más adecuadas para la soldadura de placas delgadas.
- Ensamblaje y alineación: Un ensamblaje deficiente de las uniones o errores de alineación pueden provocar la migración del baño de soldadura o defectos en la soldadura, lo que reduce la resistencia de la soldadura. En operaciones reales, el uso de accesorios de precisión o sistemas de alineación automática puede mejorar significativamente la precisión del ensamblaje.
- Preparación de los bordes: la calidad de la preparación de los bordes es fundamental para el efecto de la soldadura. Los bordes irregulares o con rebabas pueden provocar grietas o defectos de inclusión, por lo que se requieren equipos de mecanizado de precisión para manipular los bordes.
Entorno de soldadura
El entorno de soldadura es un factor externo que afecta la calidad de la soldadura, incluida la selección del gas de protección y el control de las condiciones ambientales.
- Gas de protección: el tipo y el caudal adecuados de gas de protección pueden evitar la oxidación del baño de fusión y mejorar la compacidad y la resistencia a la corrosión de la unión soldada. Por ejemplo, el argón y el helio son gases de protección de uso común, y un caudal demasiado elevado o insuficiente afectará el efecto de protección.
- Condiciones ambientales: Un ambiente con mucha humedad, demasiado polvo o una diferencia de temperatura muy marcada puede tener un efecto adverso en el proceso de soldadura e incluso hacer que el rendimiento de la soldadura se deteriore. Por lo tanto, mantener un buen control ambiental en el área de soldadura es una medida importante para garantizar la calidad de la soldadura.
Los factores que afectan la resistencia de las uniones soldadas por láser son complejos y diversos, e involucran todos los aspectos de las propiedades del material, los parámetros del láser, el diseño de la unión y el entorno de soldadura. En aplicaciones prácticas, estos factores deben considerarse de manera integral y se pueden lograr uniones soldadas de alta calidad y alta resistencia mediante una optimización razonable del proceso y el ajuste del equipo.
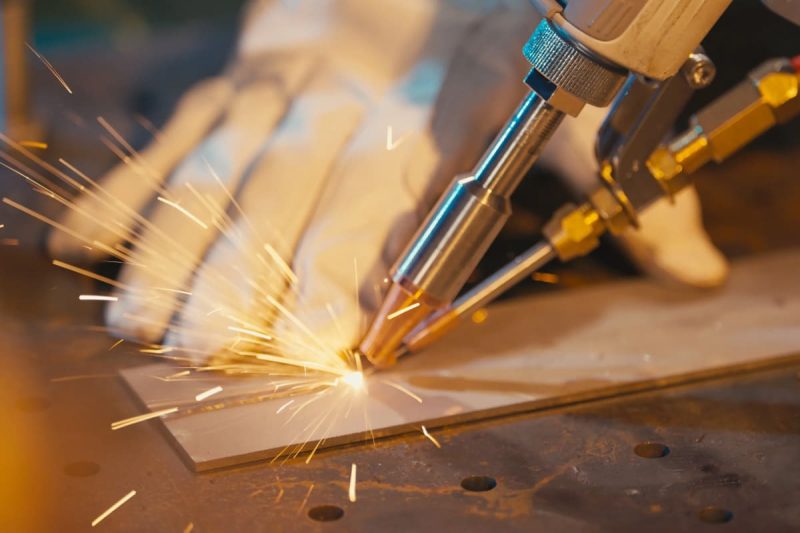
Tecnología para mejorar la resistencia de la soldadura
Para mejorar la resistencia de las uniones soldadas con láser, es necesario optimizar las propiedades de los materiales, la tecnología láser, el control del proceso de soldadura y el tratamiento posterior a la soldadura. Esto incluye no solo la selección y preparación de los materiales de soldadura, sino también el ajuste preciso de los parámetros del láser, el diseño de formas de unión razonables y el uso de tecnología avanzada de control de procesos. Al optimizar integralmente estos vínculos, las propiedades mecánicas y la confiabilidad de la soldadura se pueden mejorar significativamente. A continuación, se detallarán métodos técnicos específicos para mejorar la resistencia de la soldadura.
Selección y preparación de materiales
Los materiales son la base del rendimiento de la soldadura y juegan un papel vital en la resistencia de las uniones soldadas.
- Optimización de la aleación: al seleccionar materiales de alta resistencia adecuados para la soldadura láser y ajustar la composición de la aleación, los resultados de la soldadura se pueden mejorar significativamente. Por ejemplo, al agregar elementos específicos para mejorar la soldabilidad y la resistencia a la fatiga del material, la soldadura puede mantener la estabilidad en entornos hostiles.
- Limpieza de superficies: limpie a fondo la superficie del material antes de soldar para eliminar la grasa, las capas de óxido y otros contaminantes, garantizar una transmisión eficiente de la energía láser y reducir los defectos de soldadura. Los métodos habituales incluyen la limpieza mecánica, la limpieza química y la limpieza con láser.
- Precalentamiento: Para materiales altamente sensibles al calor o materiales que son propensos a agrietarse, un precalentamiento adecuado puede reducir el gradiente térmico durante el proceso de soldadura y reducir el estrés térmico, mejorando así la calidad de la soldadura.
Optimización láser
El ajuste de los parámetros del láser determina directamente la calidad de formación y las propiedades mecánicas de la soldadura.
- Control de densidad de potencia: Ajuste con precisión la densidad de potencia del láser para garantizar una distribución uniforme del baño de fusión, mejorando así la densidad y la resistencia de la soldadura. Una densidad de potencia menor puede provocar una penetración insuficiente, mientras que una densidad de potencia demasiado alta puede provocar fácilmente quemaduras o salpicaduras de metal.
- Conformación del haz: optimizar la forma del punto láser puede mejorar la distribución del calor durante el proceso de soldadura. Por ejemplo, cambiar el punto circular por una forma de haz elíptica o distribuida linealmente puede reducir significativamente la aparición de poros en la soldadura y mejorar la estabilidad de la misma.
- Ajuste del enfoque: el posicionamiento preciso del foco del láser es fundamental para mejorar la calidad de la soldadura. Un enfoque demasiado profundo puede provocar una penetración insuficiente, mientras que un enfoque demasiado superficial puede provocar problemas de ablación de la superficie. Por tanto, la penetración óptima de la soldadura se garantiza mediante el enfoque automático o el ajuste mecánico de precisión.
Control de procesos
La tecnología avanzada de control de procesos proporciona una fuerte garantía de la estabilidad de la calidad de la soldadura.
- Sistema de control adaptativo: utilice equipos de monitoreo en tiempo real (como cámaras y sensores) para monitorear parámetros clave en el proceso de soldadura y ajuste automáticamente la potencia del láser, la velocidad de soldadura, etc. para garantizar que la calidad de la soldadura esté siempre en el mejor estado.
- Retroalimentación de circuito cerrado: el sensor obtiene datos como la forma y la temperatura del baño de fusión y los envía al sistema de control en tiempo real, lo que puede optimizar dinámicamente los parámetros de soldadura y reducir los defectos de soldadura.
- Algoritmo de aprendizaje automático: introduce inteligencia artificial y tecnología de aprendizaje automático para analizar una gran cantidad de datos de soldadura, predecir la mejor combinación de parámetros, optimizar aún más el proceso de soldadura y mejorar el nivel de automatización.
Diseño y preparación de juntas
El diseño de la unión y la preparación de los bordes juegan un papel importante en la resistencia de las uniones soldadas.
- Geometría de unión optimizada: la forma de la unión se diseña de acuerdo con el proceso de soldadura y los requisitos estructurales. Por ejemplo, las uniones a tope son adecuadas para soldaduras de alta resistencia, mientras que las uniones traslapadas son más adecuadas para conexiones de placas delgadas. Al optimizar la geometría de la unión, las propiedades mecánicas de la soldadura se pueden mejorar significativamente.
- Montaje y alineación precisos: utilice accesorios de alta precisión y equipos de posicionamiento automático para garantizar la precisión de alineación de las uniones, evitando así desviaciones de soldadura y uniones deficientes, y mejorando la resistencia general de las soldaduras.
- Preparación del borde: utilice equipo de precisión para procesar el borde de soldadura para que quede suave y sin rebabas, lo que puede reducir eficazmente la tendencia a las grietas y mejorar la consistencia y confiabilidad de la soldadura.
Tratamiento post-soldadura
El tratamiento posterior a la soldadura puede liberar aún más la tensión residual de la soldadura y mejorar las propiedades mecánicas y la vida útil de la soldadura.
- Tratamiento térmico: Libera la tensión de soldadura mediante recocido o templado, mejora la microestructura de la soldadura y los materiales circundantes y mejora la tenacidad y la resistencia del material.
- Acabado superficial: Eliminar partes rugosas y defectos en la superficie de la soldadura mediante esmerilado o pulido, mejorando así su resistencia a la fatiga y su estética.
- Pruebas no destructivas: Utilice métodos de pruebas no destructivas como pruebas ultrasónicas y radiográficas para garantizar que no haya peligros ocultos como grietas y poros dentro de la soldadura, mejorando aún más la confiabilidad del producto.
- Procesamiento mecánico: Mejorar la distribución de la tensión residual en la superficie de la soldadura mediante métodos como el granallado y utilizar tecnología de laminación para mejorar la densidad y la resistencia a la fatiga de la soldadura mediante presión mecánica. Estos métodos de procesamiento mecánico pueden proporcionar medidas de refuerzo adicionales para la soldadura.
Para mejorar la resistencia de las uniones soldadas por láser es necesario optimizar de forma integral muchos aspectos, desde la selección y preparación de los materiales hasta el ajuste preciso de los parámetros del láser, pasando por el control avanzado del proceso y el tratamiento posterior a la soldadura; cada eslabón es crucial. Mediante combinaciones de procesos científicas y razonables, no solo se pueden mejorar las propiedades mecánicas de las uniones soldadas, sino que también se puede mejorar la calidad y la fiabilidad generales de la soldadura, lo que proporciona un sólido respaldo para aplicaciones industriales de alto nivel.
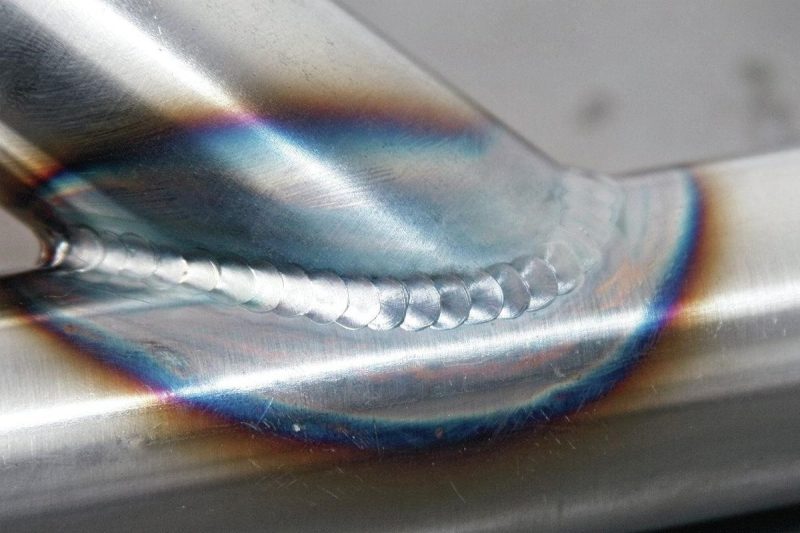
Desafíos y soluciones
En el proceso de soldadura láser, aunque la eficiencia y precisión de la tecnología brindan un fuerte respaldo para aplicaciones multisectoriales, aún existen algunos desafíos en las aplicaciones prácticas, que afectan directamente la calidad y la estabilidad de las uniones soldadas. Para abordar estos desafíos, las soluciones efectivas no solo pueden mejorar la calidad de la soldadura, sino también ampliar el alcance de aplicación de la soldadura láser. A continuación, se analizarán en detalle los tres desafíos clave de la gestión térmica, la compatibilidad de materiales y la estabilidad del proceso y sus soluciones.
Gestión térmica
La gestión térmica es un aspecto importante que debe abordarse durante la soldadura láser. La soldadura láser puede provocar fácilmente un sobrecalentamiento local del material debido a la entrada de calor concentrada, lo que puede causar deformación, grietas térmicas o tensión residual, todo lo cual puede reducir la resistencia y la vida útil de la unión soldada.
Análisis del desafío
- En entornos con alto aporte de calor, la expansión y contracción desiguales de los materiales pueden provocar deformaciones, especialmente en la soldadura de materiales delgados y piezas de precisión.
- Las temperaturas excesivamente altas pueden provocar grietas o corrosión intergranular en la soldadura, afectando el rendimiento de la soldadura.
Solución
- Optimice la trayectoria de soldadura: optimice la trayectoria de soldadura a través del diseño asistido por computadora (CAD), disperse la entrada de calor y reduzca la temperatura del área de acumulación de calor.
- Dispositivo de enfriamiento: la introducción de un dispositivo de enfriamiento por agua o un equipo de enfriamiento por aire durante la soldadura puede controlar eficazmente la intensidad de entrada de calor del área de soldadura y reducir la probabilidad de deformación térmica y grietas.
- Modo láser pulsado: el uso de soldadura láser pulsada en lugar de soldadura láser continua puede controlar mejor la entrada de calor, reducir el rango de zonas afectadas por el calor y, por lo tanto, mejorar la calidad de la soldadura.
Compatibilidad de materiales
En la producción industrial, la soldadura de materiales diferentes es cada vez más común, como acero y aluminio, cobre y acero inoxidable, etc. Las diferencias en las propiedades físicas y químicas de estos materiales pueden provocar dificultades de soldadura.
Análisis del desafío
- La soldadura de materiales diferentes es propensa a una fusión deficiente, fases frágiles o grietas en la interfaz, que afectan gravemente la resistencia y la confiabilidad de la unión soldada.
- La diferencia en el coeficiente de expansión entre los materiales puede provocar una gran tensión residual en la soldadura durante el enfriamiento, aumentando el riesgo de agrietamiento.
Solución
- Seleccionar aleaciones compatibles: al optimizar la fórmula del material, seleccione aleaciones con mayor compatibilidad como material base para reducir la aparición de malas fusiones y grietas.
- Utilice materiales de relleno: agregar materiales de relleno específicos (como aleaciones maestras o alambres de soldadura) durante el proceso de soldadura puede mejorar el rendimiento de fusión de los dos materiales y al mismo tiempo reducir la complejidad de la reacción de la interfaz.
- Optimización de parámetros láser: ajuste con precisión la potencia del láser, la velocidad de soldadura y la posición de enfoque para satisfacer las necesidades específicas de soldadura de materiales diferentes y garantizar la estabilidad y uniformidad del baño fundido.
Estabilidad del proceso
La soldadura láser es un proceso que depende en gran medida de los parámetros. Las fluctuaciones en los parámetros de soldadura pueden generar inconsistencias en la calidad de la soldadura, lo que afecta la eficiencia de la producción y el rendimiento del producto.
Análisis del desafío
- Una potencia láser o una velocidad de soldadura inestables pueden generar una profundidad, un ancho y una resistencia de soldadura desiguales.
- La vibración en el equipo de soldadura o la sujeción suelta del material pueden provocar defectos de soldadura como falta de fusión, porosidad o problemas de desplazamiento.
Solución
- Control adaptativo: Introduzca un sistema de control adaptativo inteligente para ajustar dinámicamente la potencia del láser y la velocidad de soldadura de acuerdo con los parámetros de soldadura monitoreados en tiempo real (como temperatura, forma del baño fundido, etc.), asegurando así una alta estabilidad del proceso.
- Sistema de retroalimentación de circuito cerrado: utiliza sensores de alta precisión para recopilar datos clave en el proceso de soldadura y los envía al sistema de control para un ajuste automático. Por ejemplo, la posición del foco se ajusta dinámicamente mediante el monitoreo en tiempo real de los cambios de forma del baño de fusión para garantizar la consistencia de la soldadura.
- Optimización de inteligencia artificial: Introducir un algoritmo basado en aprendizaje automático para lograr la optimización automática del proceso de soldadura láser a través del análisis de big data y la predicción de parámetros, reducir el impacto de las fluctuaciones de parámetros y mejorar la confiabilidad y repetibilidad de la soldadura.
En las aplicaciones de soldadura láser, la gestión térmica, la compatibilidad de materiales y la estabilidad del proceso son los tres desafíos clave que afectan la calidad de la soldadura. Estos problemas se pueden resolver de manera eficaz adoptando trayectorias de soldadura optimizadas, aleaciones compatibles, materiales de relleno y tecnología de control inteligente para mejorar las propiedades mecánicas y la estabilidad del proceso de la soldadura. Estas soluciones no solo pueden satisfacer los altos requisitos de la producción industrial actual, sino que también proporcionan una base sólida para el desarrollo futuro de la tecnología de soldadura láser.
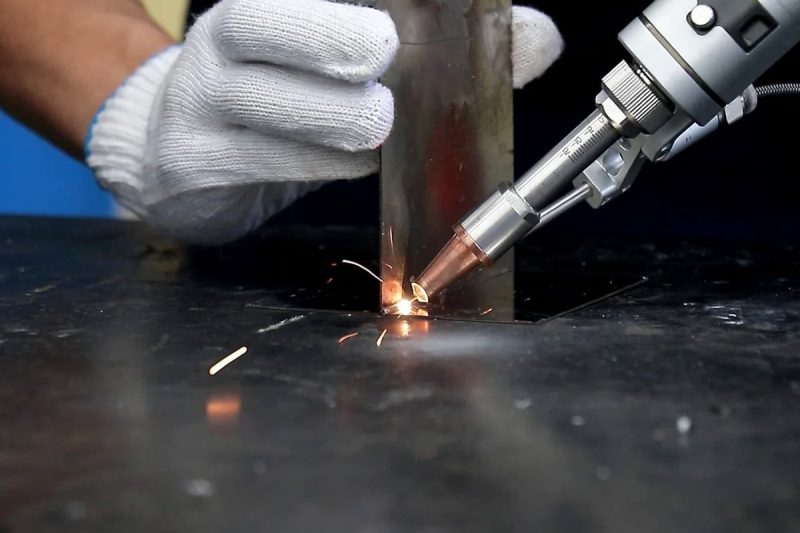
Resumir
Como método de soldadura eficiente y preciso, la tecnología de soldadura láser tiene un gran potencial para mejorar la resistencia de las uniones. Al optimizar la selección de materiales, los parámetros del láser, el diseño de las uniones y el tratamiento posterior a la soldadura, se puede mejorar de manera efectiva la resistencia y la confiabilidad de las uniones soldadas. El control preciso de la potencia del láser, la limpieza adecuada de la superficie, el diseño adecuado de la geometría de la unión y el tratamiento térmico posterior a la soldadura durante la soldadura pueden ayudar a reducir la deformación térmica y mejorar la resistencia a la fatiga de las uniones soldadas. Además, con el avance de la tecnología de control de procesos, especialmente la aplicación del aprendizaje automático y los sistemas de control adaptativo, la estabilidad y la calidad de la soldadura láser se han garantizado sin precedentes. La integración de todas estas tecnologías hace que la soldadura láser sea más competitiva en aplicaciones industriales y brinda soluciones de soldadura más eficientes y confiables a varias industrias.
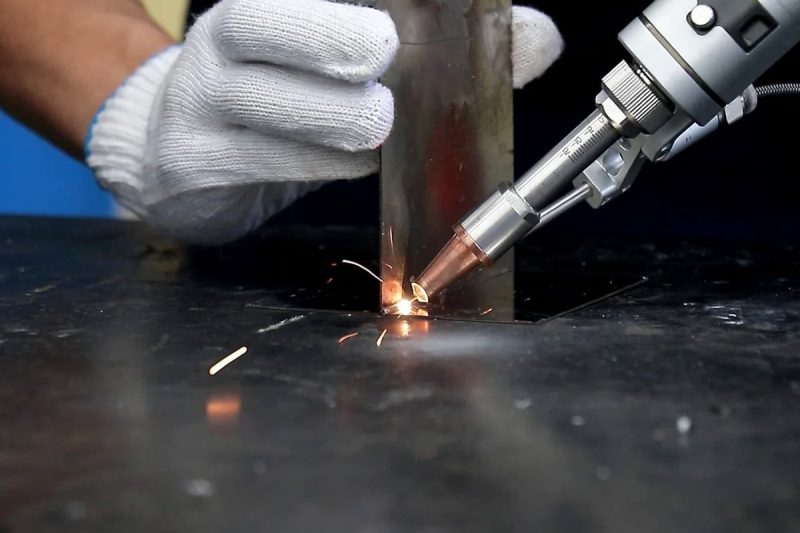
Obtenga soluciones láser
Como líder en el campo de la soldadura láser, Láser AccTek Los generadores láser proporcionan soluciones de soldadura de alta resistencia y alta estabilidad con un excelente rendimiento y tecnología de precisión. Nos centramos en diseñar soluciones a medida para nuestros clientes para garantizar que cada dispositivo pueda adaptarse perfectamente a sus necesidades específicas. Ya sea que se trate de compatibilidad de materiales, control del proceso de soldadura o procesamiento posterior a la soldadura, nuestra tecnología láser puede ayudarlo a lograr el mejor efecto de soldadura y mejorar la eficiencia de producción y la calidad del producto. Nos comprometemos a brindar soporte técnico integral y soluciones a cada cliente para garantizar que su proceso de soldadura esté siempre a la vanguardia de la industria. Si tiene alguna pregunta o necesidad sobre la tecnología de soldadura láser, no dude en contactarnos. ¡Le brindaremos la consulta y los servicios más profesionales para ayudarlo a tener éxito en el camino hacia la soldadura láser!
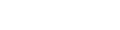
Información del contacto
- [email protected]
- [email protected]
- +86-19963414011
- No. 3 Zona A, Zona Industrial de Lunzhen, Ciudad de Yucheng, Provincia de Shandong.
Obtenga soluciones láser