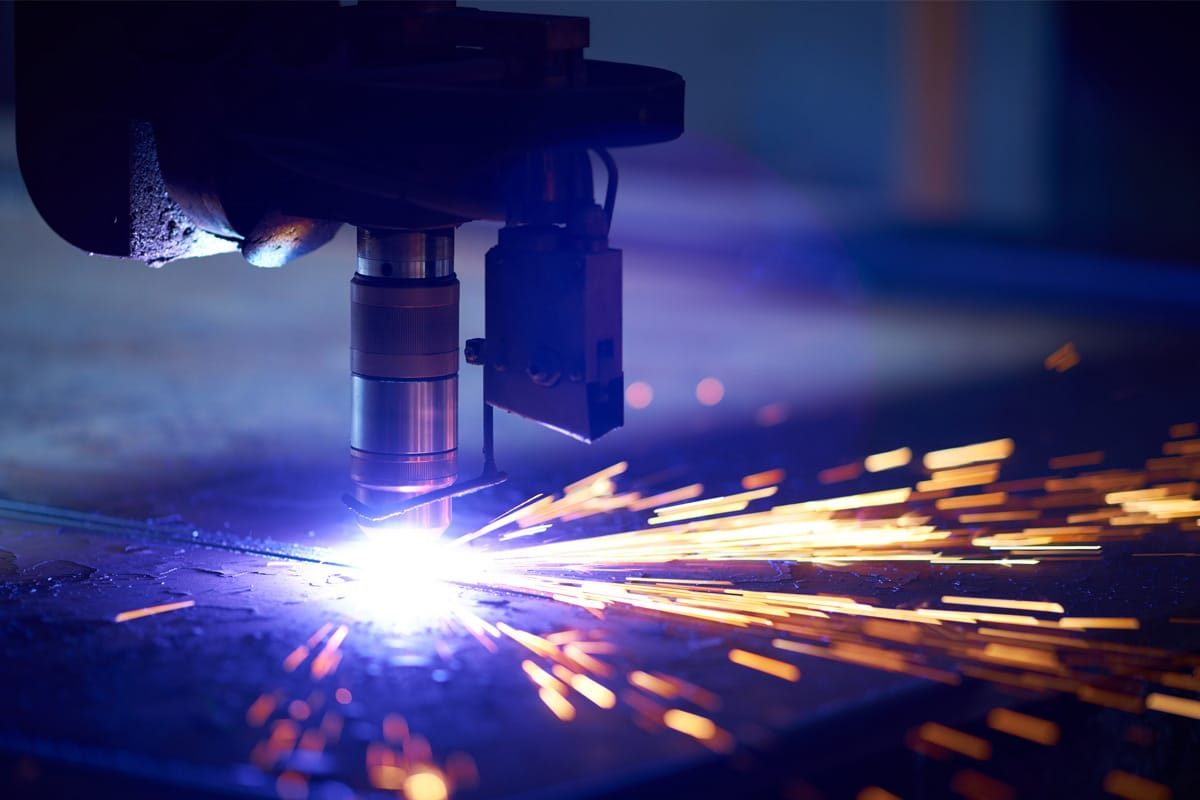
Problemas y soluciones habituales del corte por láser de fibra
La tecnología de corte por láser de fibra se utiliza ampliamente en el corte y procesamiento de diversos materiales metálicos y no metálicos debido a su alta eficiencia, alta precisión y funcionamiento flexible. Utiliza un rayo láser de alta potencia para irradiar la superficie de la pieza de trabajo para fundirla o vaporizarla, logrando así un corte preciso de la pieza de trabajo. Sin embargo, en aplicaciones prácticas, el corte por láser de fibra también enfrenta algunos problemas y desafíos comunes, como la calidad de corte reducida, la baja eficiencia de corte y la rápida pérdida de equipos. Comprender y abordar estos problemas no solo puede extender la vida útil del equipo, sino también mejorar la eficiencia de producción y la calidad del procesamiento.
Tabla de contenido
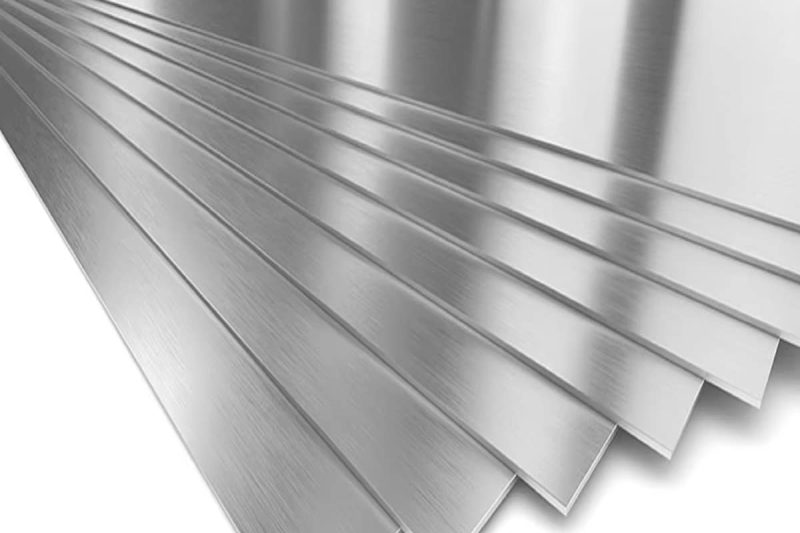
Desafíos relacionados con los materiales
Reflectividad y conductividad
Cuanto mejor sea la conductividad del material, menor será la tasa de absorción de la energía láser. Por ejemplo, el oro, la plata, el cobre, el aluminio y otros materiales tienen buena conductividad y mala absorción de energía, por lo que también se puede decir que reflejan la longitud de onda del láser. Por lo tanto, cuanto mayor sea la conductividad del metal, mayor será su reflectividad.
Desafío
- Alta reflectividad: Los metales como el aluminio y el cobre tienen una alta reflectividad. Especialmente cuando el haz láser incide en un ángulo cercano a la normal de la superficie del material, la mayor parte de la energía láser se reflejará en el generador láser o el sistema de transmisión láser, lo que no solo reduce la eficiencia de procesamiento, sino que también puede causar daños al equipo láser, como quemar la lente o la fibra óptica.
- Absorción de energía insuficiente: debido a la alta reflectividad, la energía láser efectiva absorbida por la superficie del material se reduce, lo que da como resultado una profundidad de procesamiento insuficiente, una velocidad de corte lenta o una calidad de procesamiento deficiente.
Solución
- Utilice láseres de alta potencia: aumentar la potencia del generador láser puede aumentar directamente la energía láser irradiada a la superficie del material. Incluso si parte de la energía se refleja, la energía restante es suficiente para un procesamiento eficiente. Seleccione un generador láser con un ancho de pulso y una frecuencia adecuados para materiales específicos para optimizar la transferencia de energía y los efectos de procesamiento.
- Tecnología antirreflejo: Al ajustar la forma y el ángulo de divergencia del haz láser, la energía láser se distribuye de manera más uniforme en la superficie del material, lo que reduce el problema del exceso de reflexión local. Utilice elementos ópticos ajustables dinámicamente (como espejos deformables o moduladores de luz espacial de cristal líquido) para corregir la distorsión del frente de onda del haz láser en tiempo real, mejorar la calidad de enfoque del haz láser y reducir la reflexión y la dispersión. Algunos metales tienen diferentes características de reflexión para los láseres en diferentes estados de polarización. Al ajustar la dirección de polarización del láser, se puede reducir la pérdida de reflexión.
- Optimizar el tratamiento de la superficie del material: aplicar un revestimiento o película que absorba la energía láser sobre la superficie del material para aumentar la tasa de absorción de la energía láser y reducir la reflectividad. Aumentar la rugosidad de la superficie del material mediante un pretratamiento mecánico, químico o láser, mejorar la dispersión y absorción de la energía láser y reducir la reflexión directa. Formar una capa de absorción sobre la superficie del material o cambiar sus propiedades químicas superficiales para aumentar la tasa de absorción láser.
- Ajuste de los parámetros de procesamiento: optimice el ángulo de incidencia del haz láser para evitar que incida directamente de forma perpendicular a la superficie del material y así reducir la reflexión especular. Ajuste la velocidad, la potencia, la distancia focal y otros parámetros del procesamiento láser para encontrar las mejores condiciones de procesamiento y garantizar la calidad y la eficiencia del procesamiento.
Deformación y alabeo del material
La deformación del material es causada por la deformación, que es causada por la tensión residual dentro del material y se distribuye de manera desigual a lo largo y ancho del material.
Desafío
Durante el proceso de corte por láser, el calentamiento local puede provocar la deformación del material, especialmente en materiales de placas delgadas. Esto se debe a que el láser concentrará una gran cantidad de energía térmica en un área pequeña durante el corte, lo que hará que la temperatura del área aumente rápidamente, lo que provocará la expansión y contracción térmica del material y, en última instancia, hará que el material se deforme.
Solución
- Ajustar la potencia del láser: reducir la potencia del láser puede reducir la concentración de calor, reduciendo así la deformación térmica del material.
- Optimizar la velocidad de corte: aumentar adecuadamente la velocidad de corte puede reducir el tiempo de residencia del láser en el material y reducir la acumulación de calor.
- Utilice gas auxiliar: seleccionar un gas auxiliar adecuado (como nitrógeno u oxígeno) y ajustar su caudal puede eliminar eficazmente el calor generado durante el proceso de corte y reducir la deformación del material.
Espesor del material
En el proceso de corte por láser de fibra, el espesor del material afectará directamente la calidad de corte, la eficiencia y el rendimiento de la máquina. Los materiales más delgados son más fáciles de cortar, con mayor velocidad y mayor precisión, pero los materiales más gruesos pueden dar como resultado bordes de corte ásperos o requerir mayor potencia y gas auxiliar.
Desafío
Al cortar materiales más gruesos, el láser tarda más en penetrar el material, lo que puede provocar fácilmente un corte desigual. Los materiales gruesos tienen una conductividad térmica deficiente y el calor no se disipa fácilmente, lo que da como resultado escoria y superficies de corte irregulares en el borde de corte.
Solución
- Elija la potencia del láser adecuada: elija la potencia del láser adecuada según el grosor del material para garantizar que la energía del haz se concentre en el área de corte para lograr el mejor efecto de corte.
- Ajustar los parámetros de corte: incluidos parámetros como la velocidad de corte, la posición focal y la presión del gas auxiliar para garantizar la estabilidad y uniformidad del proceso de corte.
- Corte múltiple: Para materiales particularmente gruesos, se pueden utilizar múltiples métodos de corte, cortando una parte del espesor cada vez, cortando capa por capa, para reducir la acumulación de calor y los problemas de corte desigual.
Mediante los métodos anteriores, se pueden resolver de manera efectiva los problemas de alta reflexión del material, deformación, alabeo y corte desigual de materiales gruesos durante el corte por láser, y se puede mejorar la calidad y la eficiencia del corte.
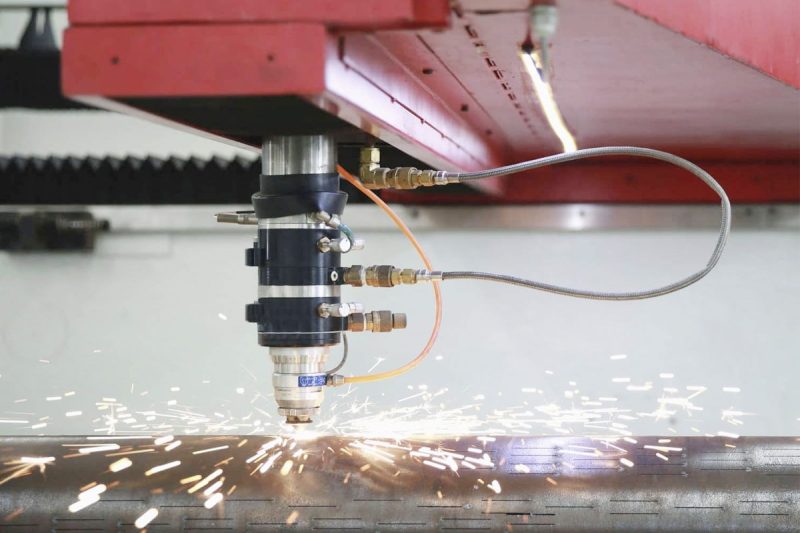
Calidad del borde y ancho de corte
La suavidad del borde de corte y la cantidad de rebabas son fundamentales para evaluar la precisión del corte. Si la energía del láser se distribuye de manera desigual o la velocidad de corte no es la adecuada, el borde puede aparecer áspero o con rebabas. El ancho de la ranura depende de la estabilidad del foco del láser. Si el foco es inestable o la potencia del láser fluctúa, el ancho de la ranura puede variar de manera inconsistente, lo que afecta la precisión del corte.
Bordes ásperos y rebabas
Desafío
- Durante el corte por láser, si la energía es desigual o la velocidad de corte es demasiado rápida o demasiado lenta, el borde de corte suele presentar rebabas y desniveles. Especialmente cuando la potencia de salida del rayo láser es inestable, la superficie del material cortado puede sobrecalentarse localmente o fundirse de manera desigual, lo que da como resultado bordes ásperos.
- En algunos materiales metálicos (como aluminio, acero inoxidable, etc.), la distribución desigual del calor inducirá estrés térmico, lo que a su vez conduce a la formación de rebabas.
- Además, el uso inadecuado de gas auxiliar (flujo de aire insuficiente o presión inadecuada) también afectará la eficiencia de descarga del material fundido y aumentará la cantidad de rebabas.
Solución
- Es fundamental optimizar la potencia del láser y la velocidad de corte. Asegúrese de que la potencia del láser sea lo suficientemente alta y la salida sea estable para mantener una distribución uniforme del calor en la superficie del material. Al mismo tiempo, la velocidad de corte debe ajustarse según el grosor y las características del material, ni demasiado rápida (para evitar un corte insuficiente del material) ni demasiado lenta (para evitar una fusión excesiva).
- El uso del gas auxiliar adecuado, como nitrógeno u oxígeno, puede mejorar los resultados del corte y garantizar una superficie de corte limpia y lisa. El nitrógeno se utiliza a menudo para evitar la oxidación y reducir las rebabas en los bordes, mientras que el oxígeno ayuda a aumentar la eficiencia del corte y la velocidad de fusión.
Variación del ancho de la ranura
Desafío
- La razón principal de la inconsistencia del ancho de la ranura suele estar relacionada con la inestabilidad del enfoque del láser o la fluctuación de la potencia del láser. Cuando el enfoque del láser está desfasado, la concentración de energía cambiará en consecuencia, lo que dará lugar a fluctuaciones en el ancho de la ranura. Si la potencia del láser es inestable, la fluctuación de la energía de salida afectará directamente la precisión del corte y provocará cambios en el ancho de la ranura.
- Además, la contaminación o los daños en los componentes ópticos también pueden provocar cambios en la calidad del haz, afectando así a la uniformidad de la línea de corte. El desgaste de las piezas mecánicas del equipo, como los rieles guía y los cojinetes, también afectará a la precisión del movimiento del cabezal láser, lo que dará como resultado cortes irregulares.
Solución
- Revise y mantenga periódicamente el sistema óptico para garantizar un enfoque y una energía láser estables.
- Limpie o reemplace las lentes ópticas contaminadas para evitar la refracción o dispersión innecesaria durante la transmisión del haz.
- Calibre periódicamente el enfoque y la potencia de salida del equipo láser para garantizar su precisión durante el funcionamiento.
- Mantener las partes mecánicas del equipo para garantizar un movimiento suave y sin obstrucciones del cabezal láser para reducir los errores de corte causados por el desgaste mecánico.
En resumen, configurando correctamente los parámetros y realizando un mantenimiento regular del sistema óptico, se puede mejorar eficazmente la calidad del borde y controlar el ancho de corte.
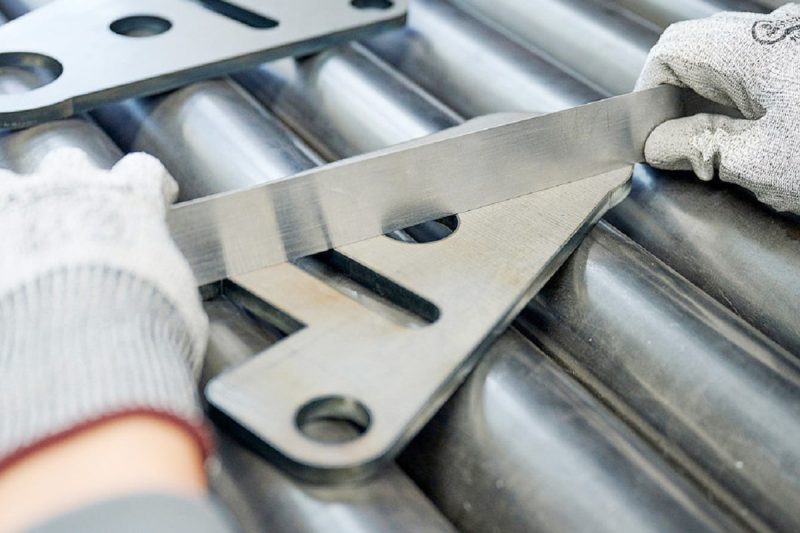
Desafíos relacionados con el proceso
Los desafíos relacionados con el proceso involucran principalmente problemas técnicos que pueden surgir durante el proceso de corte por láser de fibra. Los desafíos comunes relacionados con el proceso incluyen la acumulación de escoria, que es un desafío común en el proceso de corte por láser de fibra, especialmente cuando se cortan materiales más gruesos o difíciles de cortar. Por lo general, la acumulación de escoria se debe a que el material no se funde o evapora por completo, o a un suministro insuficiente de gas auxiliar para expulsar el material fundido del área de corte a tiempo.
Acumulación de escoria
Desafío
- Cuando la energía del láser es insuficiente o el enfoque del haz láser está desviado, la superficie del material no puede alcanzar la temperatura necesaria para fundirse o evaporarse, lo que hace que quede algo de material en el borde de corte. Especialmente en el procesamiento de placas gruesas, la energía del láser debe ser lo suficientemente fuerte como para penetrar todo el espesor del material.
- A menudo se utilizan gases auxiliares como el oxígeno o el nitrógeno para ayudar a expulsar el material fundido del área de corte. Si la presión del gas es demasiado baja y el material fundido no se puede eliminar de manera efectiva, se acumulará escoria en el borde de corte.
- Una velocidad de corte demasiado rápida provocará que el láser no continúe actuando sobre la misma área, el material no se derrita completamente o el gas no pueda expulsar el residuo a tiempo, lo que provocará una acumulación de escoria.
Solución
- Asegúrese de que se proporcione suficiente presión de gas para ayudar a eliminar eficazmente el material fundido y evitar la acumulación de escoria. El nitrógeno es adecuado para materiales no oxidantes, mientras que el oxígeno puede acelerar la velocidad de corte, pero requiere una mayor presión de gas.
- Optimice la velocidad de corte según el espesor y las características del material para garantizar que la energía del láser pueda actuar completamente sobre el área de corte. La combinación adecuada de potencia del láser y velocidad de corte puede reducir las zonas innecesariamente afectadas por el calor, evitando así el problema de la fusión incompleta de los materiales.
- Asegúrese de que los componentes ópticos del generador láser estén en las mejores condiciones y puedan generar de manera estable la potencia láser requerida para garantizar la consistencia del proceso de corte.
Al ajustar exhaustivamente estos parámetros, se pueden reducir significativamente los problemas de acumulación de escoria, mejorar la calidad del corte y reducir el trabajo de pulido y limpieza posterior.
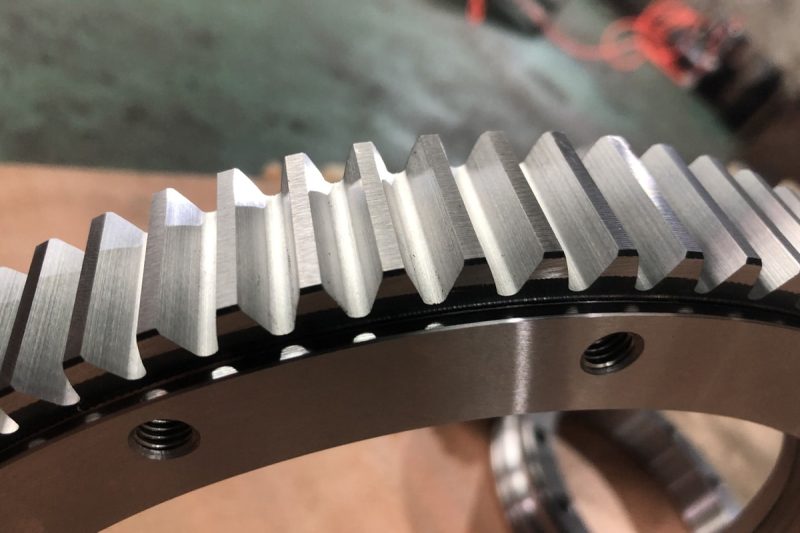
Problemas de pinchazos y arranque
Durante el proceso de corte por láser de fibra, los problemas de perforación y arranque son desafíos comunes, especialmente cuando se trata de materiales más gruesos o altamente reflectantes. El proceso de perforación es el punto de partida del corte por láser, y su estabilidad y eficiencia afectan directamente el efecto de todo el proceso de corte. Si el tiempo de perforación es demasiado largo o falla, puede provocar desperdicio de material y desgaste del equipo, e incluso afectar la calidad del corte. La inestabilidad del proceso de arranque provocará cortes desiguales y una mala calidad del filo de corte, lo que afectará la precisión y la apariencia del producto terminado.
Retrasos y fallos en la perforación
Desafío
Los retrasos en la perforación suelen deberse a que el haz láser no logra concentrar rápidamente la energía suficiente para penetrar el material, lo que da como resultado un tiempo de perforación prolongado. Los retrasos en la perforación son especialmente notorios en materiales más gruesos o reflectantes (como el aluminio y el cobre), e incluso pueden provocar fallos en la perforación. Las razones de los fallos en la perforación pueden incluir potencia láser insuficiente, enfoque láser inexacto, gas auxiliar insuficiente o selección de gas inadecuada. Esto puede provocar inicios de corte desiguales o fallidos, desperdicio de material y posibles daños en el equipo láser.
Solución
- Asegúrese de que la potencia del láser se pueda concentrar rápidamente, especialmente en materiales de placas gruesas, donde se requiere mayor energía para la perforación. Ajuste el enfoque del láser para garantizar que se concentre en la superficie del material, lo que reduce la dispersión de energía y acorta el tiempo de perforación.
- Al perforar en modo de pulso corto, se puede reducir el sobrecalentamiento y la deformación del material, al tiempo que se reduce la posibilidad de falla de la perforación. Esta técnica es particularmente adecuada para materiales más gruesos y materiales altamente reflectantes.
- El uso de nitrógeno y oxígeno tiene un impacto significativo en el proceso de perforación. El oxígeno puede acelerar el proceso de perforación, pero puede provocar la oxidación del material, por lo que se debe seleccionar el gas y la presión adecuados en función de las características del material.
- En el caso de materiales muy gruesos, se pueden utilizar técnicas de perforación en varias etapas, que penetran el material capa por capa en lugar de hacerlo en todas a la vez. Este método puede evitar eficazmente los fallos por perforación y los efectos térmicos excesivos.
Inicio inestable
Desafío
El arranque inestable se manifiesta principalmente como un ancho de corte desigual y una mala calidad del borde al comienzo del corte por láser, e incluso puede provocar un fallo en el proceso de corte. Esto suele deberse a una energía láser inestable, cambios en el caudal de gas, características superficiales del material inconsistentes (como oxidación o recubrimiento), etc. Un arranque inestable puede provocar una mala calidad de corte en la pieza inicial, especialmente en aplicaciones de corte de precisión; esta inestabilidad afectará la precisión y la consistencia del producto terminado.
Solución
- Antes de comenzar, se puede precalentar la superficie del material, especialmente en el caso de materiales muy reflectantes. Esto ayuda a reducir los reflejos del láser y hace que el proceso de corte sea más fluido.
- Asegúrese de que el generador láser alcance rápidamente un estado estable al iniciarse ajustando la tasa de aumento de la potencia del láser y el caudal de gas auxiliar. Esto puede evitar de manera eficaz las fluctuaciones de energía al iniciarse.
- Para materiales con capas de óxido u otras impurezas en la superficie, se puede realizar una limpieza simple de la superficie o la eliminación del revestimiento antes del inicio para reducir los reflejos del láser y la inestabilidad durante el proceso de inicio.
- Utilice un sistema de monitoreo en tiempo real para monitorear el proceso de corte, especialmente durante la fase de inicio, y garantizar la estabilidad y consistencia del proceso de corte ajustando los parámetros.
En general, mediante la optimización de los parámetros del láser, la selección del gas auxiliar adecuado, el uso de la tecnología de perforación por pulsos y el preprocesamiento antes del inicio, se pueden reducir significativamente los problemas de retraso de la perforación, fallas e inicio inestable, y se puede mejorar la eficiencia y la calidad del corte. Estas soluciones no solo mejoran la eficiencia operativa, sino que también garantizan el funcionamiento estable a largo plazo del equipo.
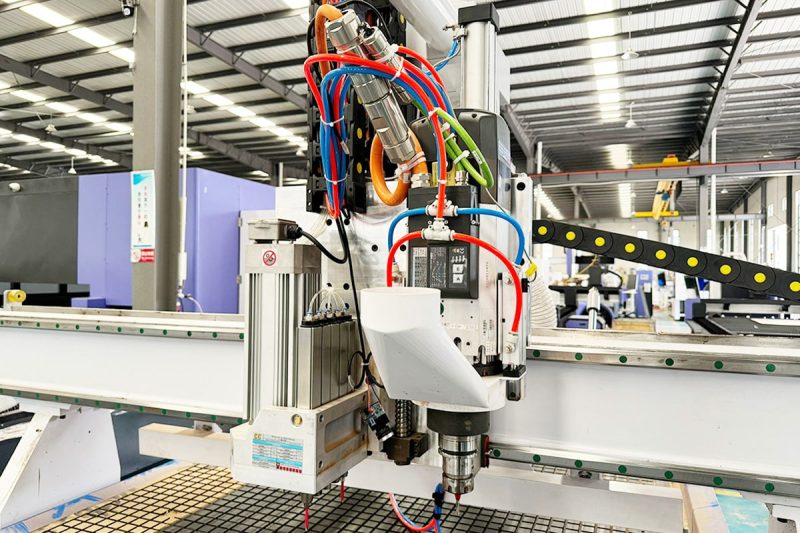
Desafíos relacionados con las máquinas
En el corte por láser de fibra, el rendimiento de la máquina afecta directamente la calidad y la eficiencia del corte. El sistema de transmisión del haz y los componentes mecánicos de la propia máquina pueden presentar diversos problemas tras un uso prolongado, lo que afectará a la precisión y la estabilidad del corte por láser.
Problemas con el sistema de entrega de rayos
Desafío
El sistema de transmisión del haz es el sistema central que transmite la energía de la fuente láser al cabezal de corte. Su rendimiento determina directamente la estabilidad energética del haz láser y la calidad del corte. Si el sistema de transmisión del haz no se inspecciona y mantiene periódicamente, el polvo, las impurezas o el desgaste mecánico también pueden dañar los componentes ópticos, lo que reduce aún más la eficiencia del sistema.
Solución
- Las lentes ópticas y las lentes de los sistemas de corte por láser de fibra son propensas a la acumulación de polvo y aceite. La limpieza regular puede evitar la disminución de la eficiencia de transmisión del haz láser y garantizar la estabilidad del haz.
- Garantizar la estabilidad de los conectores de fibra y la alineación precisa de los rayos láser puede reducir la pérdida de energía. Revise las conexiones de fibra periódicamente para asegurarse de que no estén sueltas ni desgastadas.
- Si ocurren problemas frecuentes de inestabilidad del haz, considere utilizar tecnología de óptica adaptativa para ajustar el sistema de transmisión del haz en tiempo real para garantizar la mejor calidad del haz.
- La acumulación de calor durante la transmisión del haz afecta la calidad del haz, por lo que es fundamental mantener el sistema de refrigeración funcionando de manera eficaz. Compruebe el sistema de refrigeración periódicamente para asegurarse de que pueda disipar el calor con normalidad y reducir el impacto térmico durante la transmisión del haz.
Desgaste mecánico
Desafío
Los componentes mecánicos de las máquinas de corte por láser de fibra, incluidos los rieles guía, los servomotores y los sistemas de accionamiento, se desgastarán gradualmente con el tiempo debido al uso intensivo. El desgaste mecánico no solo provocará un movimiento inestable del cabezal de corte, sino que también puede afectar la precisión de la trayectoria de corte y, en última instancia, la calidad del producto terminado. Especialmente en los requisitos de corte de alta velocidad y alta precisión, el desgaste mecánico acelerará el envejecimiento del equipo y aumentará los costos de mantenimiento y el tiempo de inactividad. Además, el aumento de la vibración y el ruido también son síntomas comunes del desgaste mecánico.
Solución
- Los rieles guía y los sistemas de transmisión deben lubricarse periódicamente para reducir la fricción y prolongar la vida útil de las piezas mecánicas. Al mismo tiempo, se debe verificar el sistema de lubricación para garantizar su funcionamiento normal y evitar el desgaste excesivo de las piezas debido a una lubricación insuficiente.
- Si se descubre que los rieles guía, los engranajes u otras piezas están desgastados o desplazados, las piezas dañadas deben reemplazarse a tiempo para garantizar la precisión y la estabilidad de la máquina.
- En operaciones de alta precisión, la vibración puede afectar la precisión del corte. Al instalar dispositivos antivibración u optimizar la posición de instalación de la máquina, se puede reducir el impacto de la vibración en las piezas mecánicas, lo que retrasa el desgaste.
- Moderno máquinas de corte por láser de fibra Puede equiparse con un sistema de monitoreo para monitorear el estado de las partes mecánicas en tiempo real, predecir posibles fallas con anticipación a través del análisis de datos y evitar tiempos de inactividad repentinos causados por el desgaste mecánico.
Mediante el mantenimiento regular y la optimización del sistema de transmisión del haz y de los componentes mecánicos, se puede mejorar significativamente el rendimiento y la estabilidad de la máquina de corte por láser de fibra, garantizando la continuidad y la alta calidad del efecto de corte.
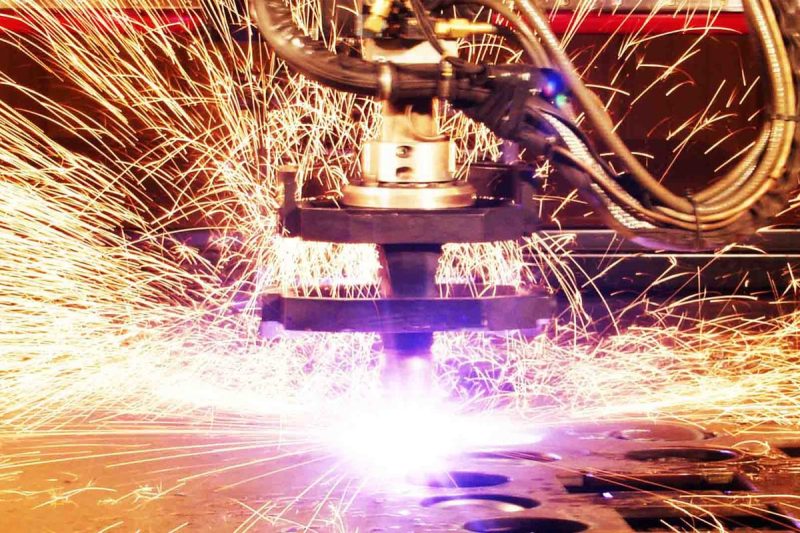
Conicidad y desviación angular
La desviación de ángulo y conicidad son dos problemas de precisión comunes en el proceso de corte por láser de fibra. Los problemas de conicidad suelen manifestarse como anchos superiores e inferiores inconsistentes del borde de corte, mientras que la desviación de ángulo se refiere a la falta de perpendicularidad entre el haz láser y el material, lo que da como resultado una superficie de corte inclinada. Estos problemas afectan la calidad y la apariencia de la pieza de trabajo final, especialmente en tareas de corte de alta precisión.
Afilar
Desafío
El fenómeno de la conicidad suele producirse al cortar materiales gruesos y se manifiesta como que el filo de corte es estrecho en la parte superior y ancho en la parte inferior, o ancho en la parte superior y estrecho en la parte inferior. Esto se debe a que la distribución de energía del haz láser es desigual al atravesar el material. Cuanto mayor sea la profundidad de corte, más evidente será la atenuación de la energía del láser, lo que dará lugar a una diferencia en los anchos superior e inferior del filo de corte. La conicidad afectará a la precisión de la pieza de trabajo, especialmente en el caso de un montaje de alta precisión. La conicidad provocará dificultades de montaje e incluso el desguace de la pieza de trabajo. Además, una presión de gas auxiliar inadecuada y una potencia láser inestable también agravarán el fenómeno de la conicidad.
Solución
- Los problemas de conicidad se pueden reducir de forma eficaz optimizando la profundidad y la posición del foco del láser. Si se coloca el foco en el centro del material en lugar de en la superficie, se ayuda a mantener una distribución uniforme de la energía del láser en todo el espesor de corte.
- Para materiales más gruesos, el uso de un generador láser de mayor potencia puede mantener una salida de energía más estable durante el proceso de corte y reducir los problemas de conicidad causados por la atenuación del láser.
- La conicidad se puede reducir ajustando adecuadamente la presión del gas auxiliar, manteniendo limpia la zona de corte y enfriando eficazmente el filo. Especialmente en el corte de material grueso, el papel del gas auxiliar es crucial.
- Cualquier pequeño problema con el sistema óptico provocará una distribución desigual de la energía del haz láser. Por lo tanto, el mantenimiento y la limpieza regulares de los componentes ópticos para garantizar la calidad del haz láser pueden reducir eficazmente la conicidad.
Desviación angular
Desafío
La desviación angular se refiere a la falta de verticalidad del haz láser en relación con el material, lo que da como resultado un borde de corte inclinado. Esto puede deberse a una instalación inestable del cabezal láser, una alineación incorrecta del haz o una precisión insuficiente del sistema mecánico. La desviación angular hará que la superficie de corte de la pieza de trabajo sea desigual, lo que afectará la precisión y la apariencia, especialmente cuando se requiere cortar la pieza de trabajo en ángulos rectos.
Solución
- El primer paso para solucionar el problema de la desviación del ángulo es asegurarse de que el cabezal láser esté montado firmemente y perpendicular al material. La calibración periódica del cabezal láser y del sistema mecánico garantiza que el haz láser mantenga siempre el ángulo correcto durante el corte.
- La velocidad de corte, la potencia de salida y los ajustes del gas auxiliar afectan la desviación del ángulo. Al optimizar estos parámetros, el rayo láser se puede mantener estable durante el corte, lo que reduce la desviación del ángulo.
- La óptica adaptativa puede ajustar la trayectoria de propagación y el enfoque del rayo láser en tiempo real para garantizar que siempre se mantenga el ángulo correcto con el material durante el corte, reduciendo así la desviación del ángulo.
- Los factores externos, como los cambios de temperatura y humedad y las vibraciones, pueden afectar la precisión del ángulo de corte por láser. La desviación del ángulo se puede reducir aún más manteniendo la estabilidad del entorno de corte, por ejemplo, reduciendo la vibración, controlando la temperatura y la humedad, etc.
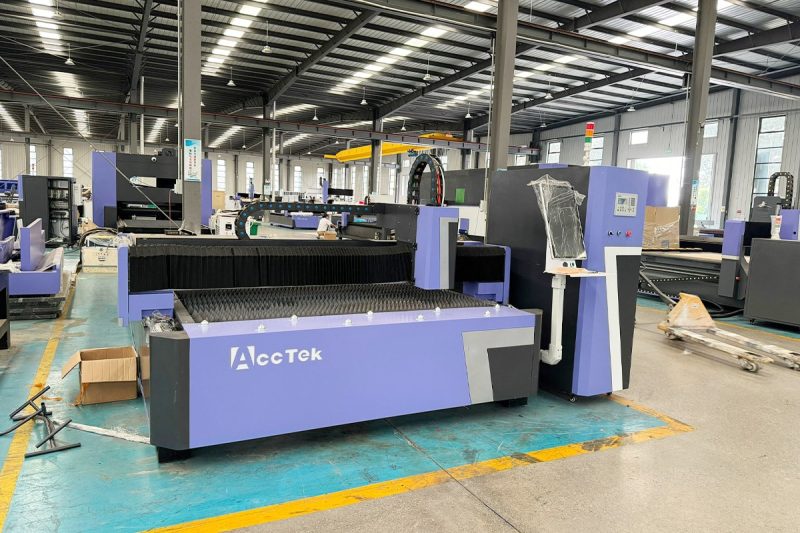
Factores ambientales
Los factores ambientales tienen un impacto directo en la estabilidad y calidad del proceso de corte por láser de fibra. Las fluctuaciones de temperatura y humedad, así como los cambios en la calidad del aire, pueden afectar negativamente el rendimiento del sistema láser, la calidad del corte y la vida útil de la máquina. Comprender y controlar estos factores ambientales puede garantizar que el equipo funcione de manera óptima, reduciendo fallas innecesarias y requisitos de mantenimiento.
Fluctuaciones de temperatura y humedad
Desafío
Las fluctuaciones de temperatura y humedad son un desafío importante en el proceso de corte por láser. El generador láser y el sistema óptico son muy sensibles a los cambios de temperatura y humedad. Por ejemplo, una temperatura demasiado alta puede hacer que el generador láser se sobrecaliente, afectando la calidad y estabilidad del haz láser; mientras que una temperatura demasiado baja puede hacer que el generador láser no alcance la temperatura de funcionamiento requerida, afectando así la potencia de salida. Una humedad demasiado alta puede causar condensación en los componentes ópticos, afectando la eficiencia de transmisión del haz láser e incluso dañando los dispositivos ópticos. Una humedad demasiado baja puede aumentar el riesgo de electricidad estática, que puede interferir con el funcionamiento normal de los componentes electrónicos.
Solución
- Para hacer frente a las fluctuaciones de temperatura y humedad, se recomienda instalar sistemas de control ambiental especializados, como equipos de aire acondicionado y deshumidificación, en el taller de corte. Estos sistemas pueden mantener la temperatura y la humedad constantes en el taller para garantizar que el equipo láser funcione en condiciones óptimas.
- Instalar sensores de temperatura y humedad alrededor del equipo de corte para monitorear las condiciones ambientales en tiempo real. Una vez que se detecta una anomalía, el sistema de control ambiental se puede ajustar automáticamente o se puede suspender el proceso de corte si es necesario para evitar daños al equipo.
- En un ambiente seco, aumente la humedad del aire para reducir el riesgo de electricidad estática y utilice pisos antiestáticos y medidas de conexión a tierra del equipo para garantizar un funcionamiento seguro.
Calidad del aire
Desafío
El impacto de la calidad del aire en el proceso de corte por láser no se puede ignorar. El polvo, la neblina de aceite y otros contaminantes suspendidos en el aire pueden ingresar al sistema óptico o al área de corte del generador láser, lo que afecta la transmisión y el enfoque del rayo láser. Los contaminantes en el aire también pueden reaccionar con el rayo láser durante el proceso de corte, lo que da como resultado resultados de corte deficientes o incluso daños en la superficie de la pieza de trabajo. Además, la exposición prolongada a aire de mala calidad aumentará la frecuencia de mantenimiento de la máquina y acortará la vida útil del equipo.
Solución
- Instale un sistema de purificación de aire en el taller de corte por láser para filtrar las partículas y los contaminantes del aire y garantizar un aire limpio. Especialmente al cortar ciertos materiales (como plásticos y madera), estos materiales pueden liberar gases nocivos durante el proceso de corte por láser, por lo que un sistema de purificación de aire eficaz es especialmente importante.
- Incluso con un sistema de purificación de aire, sigue siendo necesario limpiar periódicamente el sistema óptico del generador láser. Elimine el polvo y los contaminantes que puedan acumularse para garantizar la calidad del haz láser y el efecto de corte.
- En algunos equipos o áreas clave, se pueden adoptar medidas de protección de presión positiva, es decir, al introducir aire filtrado, la presión del aire en el área se mantiene más alta que la del exterior para evitar que entren contaminantes.
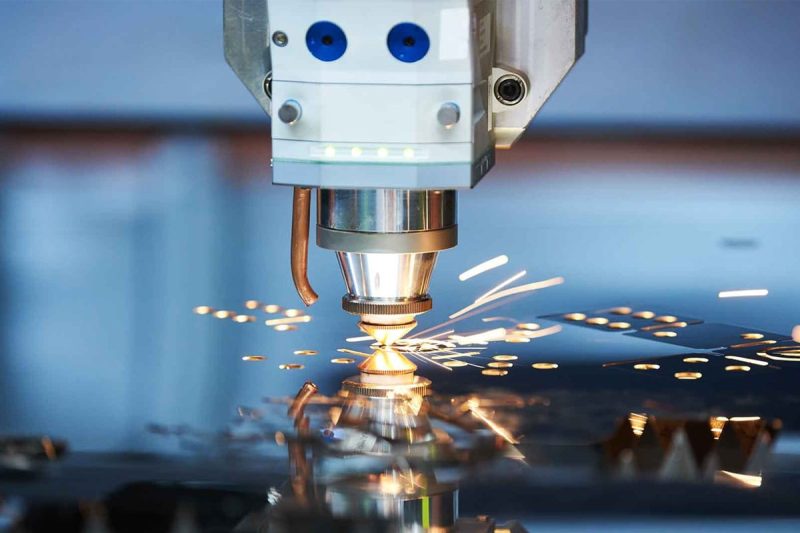
Desafíos relacionados con el operador
Además de los factores ambientales, el nivel de habilidad del operador y la eficiencia laboral también afectan directamente la calidad y la eficiencia del corte por láser de fibra. La falta de capacitación y experiencia, o un flujo de trabajo ineficiente, pueden provocar un funcionamiento inadecuado, mayores tasas de error e incluso daños en el equipo o accidentes de seguridad. Por lo tanto, mejorar la profesionalidad del operador y optimizar el flujo de trabajo son vínculos importantes para garantizar la calidad del corte y la eficiencia de la producción.
Falta de formación y experiencia
Desafío
El corte por láser de fibra es una tecnología de alta precisión que requiere que los operadores tengan un alto nivel de conocimientos y habilidades profesionales. Sin embargo, en algunas empresas, los operadores pueden carecer de la formación suficiente y no pueden comprender y dominar por completo la complejidad del corte por láser. Esta situación puede provocar que los operadores no puedan responder de manera eficaz cuando se enfrentan a problemas técnicos o piezas de trabajo complejas, lo que puede afectar la calidad del corte, aumentar el desgaste del equipo e incluso provocar riesgos de seguridad. Además, el mantenimiento y el cuidado del equipo requieren habilidades y conocimientos específicos. La falta de conocimiento del operador puede provocar que el equipo no se mantenga y cuide con prontitud, acortando la vida útil del mismo.
Solución
- Las empresas deben brindar capacitación sistemática a los operadores, incluidos los principios básicos del corte por láser, la guía de operación del equipo, la resolución de problemas y las soluciones a problemas comunes, etc. A través de la capacitación regular, asegúrese de que los operadores siempre dominen la última tecnología y las especificaciones operativas.
- Establecer un sistema de certificación de operaciones para los operadores, y que sólo el personal certificado pueda operar equipos de corte láser. Esto no sólo mejora el sentido de responsabilidad del operador, sino que también garantiza la calidad y la seguridad de la operación.
- Brindar un sólido apoyo técnico a los operadores, como establecer un departamento especial de consultoría técnica o contratar expertos técnicos para brindar orientación regular para ayudar a los operadores a resolver problemas en las operaciones diarias.
Flujo de trabajo ineficiente
Desafío
La eficiencia del flujo de trabajo afecta directamente la eficiencia general de la producción y la calidad del corte por láser. En algunas empresas, debido a un diseño de flujo de trabajo poco razonable o una coordinación insuficiente, los operadores pueden pasar demasiado tiempo cambiando tareas, depurando equipos o manipulando materiales. Este flujo de trabajo ineficiente no solo desperdicia tiempo y recursos, sino que también puede causar fatiga al operador y aumentar la posibilidad de errores. Además, si la empresa no optimiza el flujo de trabajo con prontitud, a medida que aumenta el volumen de pedidos, el proceso ineficiente se hará más evidente, lo que afectará gravemente la capacidad de producción y la competitividad corporativa.
Solución
- Al analizar y evaluar el flujo de trabajo actual, podemos identificar cuellos de botella y enlaces ineficientes y realizar optimizaciones específicas. Por ejemplo, podemos organizar el orden de las tareas de manera razonable, reducir el tiempo de puesta en servicio de equipos y manipulación de materiales y mejorar la eficiencia del trabajo.
- La introducción de tecnologías de automatización, como sistemas de carga y descarga automática y software de composición tipográfica inteligente, puede reducir significativamente los errores de tiempo y precisión de las operaciones manuales y mejorar la eficiencia del flujo de trabajo general.
- Aplicar principios de producción eficiente para reducir los desperdicios y optimizar la asignación de recursos. A través de la mejora continua y la participación de los empleados, podemos establecer un flujo de trabajo eficiente y flexible para garantizar la eficiencia y la alta calidad del proceso de corte por láser.
Al abordar estos desafíos ambientales y relacionados con el operador, las empresas pueden mejorar en gran medida la eficiencia y la calidad del corte por láser de fibra, obteniendo así una ventaja en la competencia del mercado.
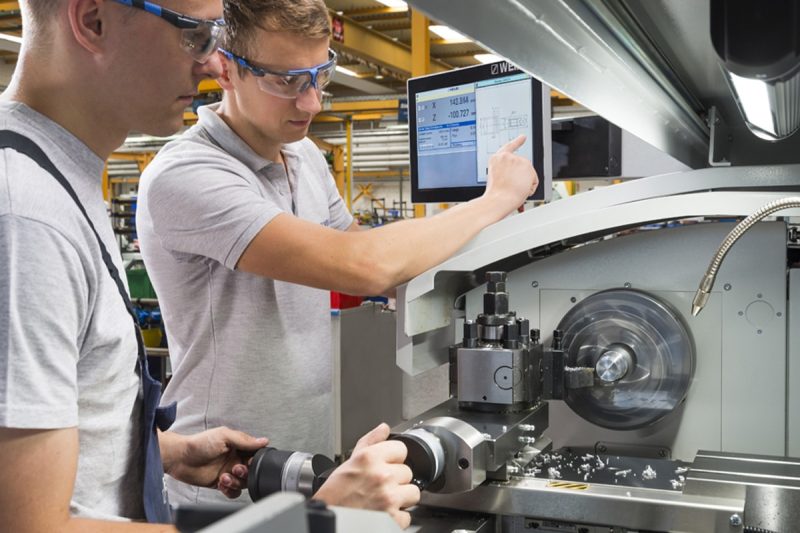
Precauciones y mejores prácticas
Para garantizar el funcionamiento eficiente y continuo del corte por láser de fibra, es fundamental adoptar medidas preventivas y aplicar las mejores prácticas. Mediante el mantenimiento regular de la máquina, la optimización de los parámetros, la capacitación de los operadores y la mejora continua, las empresas pueden reducir eficazmente las tasas de fallas, mejorar la calidad del corte y extender la vida útil del equipo.
Mantenimiento regular de la máquina
Desafío
El funcionamiento prolongado de los equipos de corte por láser puede provocar la contaminación de los componentes ópticos, el desgaste del cabezal láser y el fallo del sistema de refrigeración. Si no se realiza un mantenimiento regular, estos problemas pueden afectar al rendimiento del generador láser, aumentar el tiempo de inactividad de la producción e incluso provocar fallos en el equipo.
Solución
- Limpie periódicamente el sistema óptico para garantizar la eficiencia de transmisión del rayo láser.
- Revise y reemplace las piezas vulnerables, como boquillas de corte, lentes láser y sistemas de filtrado.
- Revise periódicamente el sistema de enfriamiento para asegurarse de que funciona correctamente y evitar que el generador láser se sobrecaliente.
Optimización de parámetros
Desafío
Los distintos materiales y espesores requieren distintas potencias de láser, velocidades de corte y presiones de gas. Una configuración incorrecta de los parámetros puede provocar una reducción de la calidad del corte, como un aumento de las rebabas o cortes demasiado anchos o demasiado estrechos.
Solución
- Desarrollar tablas detalladas de parámetros de corte para diferentes materiales para garantizar una combinación precisa de potencia y velocidad.
- Pruebe periódicamente la salida láser del equipo para garantizar una potencia y un enfoque estables.
- Utilice software auxiliar para la optimización automatizada de parámetros para mejorar la eficiencia y la calidad del corte.
Capacitación de los operadores
Desafío
La falta de experiencia o habilidades del operador puede provocar errores operativos, aumentar la tasa de fallas y afectar el efecto de corte.
Solución
- Proporcionar capacitación técnica a los operadores periódicamente para garantizar que dominen las especificaciones de funcionamiento de los equipos láser.
- Proporcionar manuales detallados de operación de equipos y establecer un equipo de soporte técnico para resolver problemas diarios.
- Implementar un sistema de certificación de operadores para garantizar que sólo personas calificadas puedan operar el equipo.
Mejora continua
Desafío
Los rápidos cambios en la tecnología y los mercados requieren que las empresas optimicen continuamente los procesos y las tecnologías de producción para seguir siendo competitivas.
Solución
- Introducir conceptos de producción ajustada, analizar y optimizar continuamente los procesos de producción, reducir el desperdicio y mejorar la eficiencia.
- Siga la tendencia de desarrollo de la tecnología de corte por láser y actualice los equipos y el software rápidamente.
- Recopilar datos de producción, analizar indicadores de rendimiento y mejorar continuamente los parámetros de corte y los procedimientos operativos.
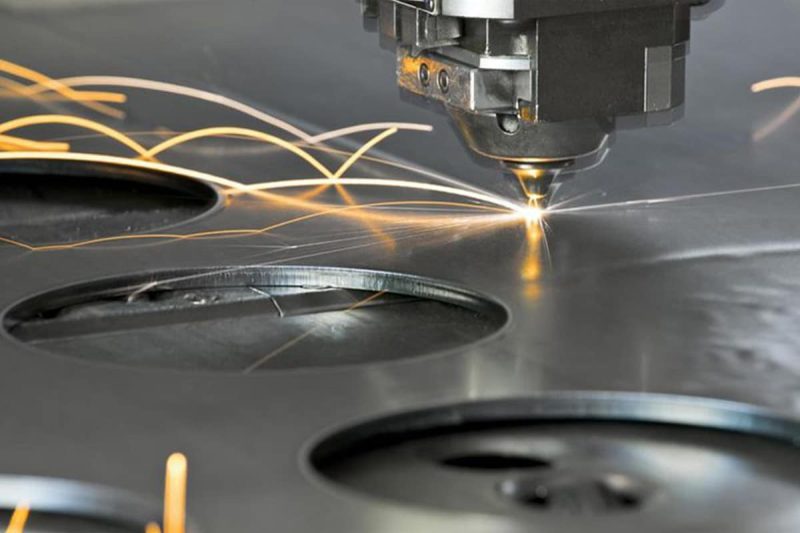
Resumir
Los desafíos del corte por láser de fibra involucran muchos aspectos, incluidas las propiedades del material, el rendimiento del equipo, las condiciones ambientales, etc. A través de un mantenimiento regular, parámetros optimizados, capacitación mejorada y el uso de tecnología avanzada, la calidad y la eficiencia del corte se pueden mejorar significativamente. Las soluciones deben implementarse caso por caso para mejorar la estabilidad del proceso de corte y reducir el tiempo de inactividad de la máquina y los costos de mantenimiento.
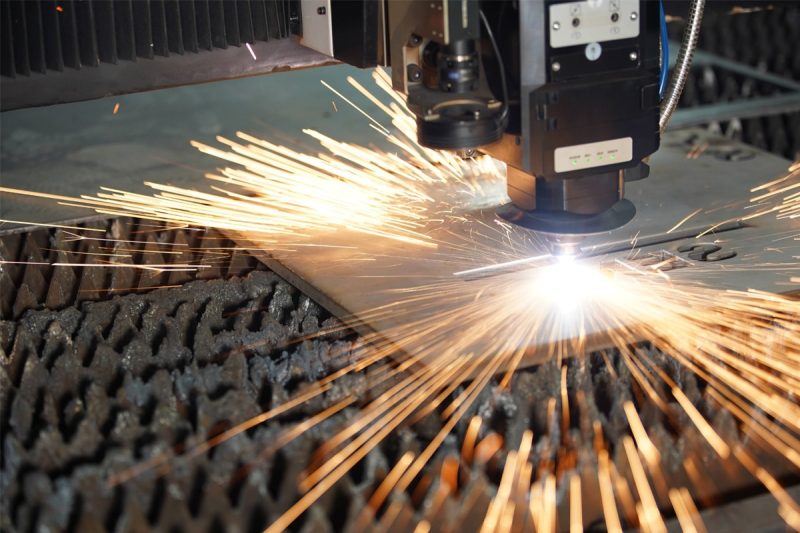
Obtenga soluciones láser
Elegir la máquina de corte por láser de fibra adecuada puede ayudar a optimizar el consumo de energía y lograr una alta eficiencia operativa. Trabajar con un proveedor de confianza garantiza el acceso a tecnología avanzada, asesoramiento personalizado y soporte continuo. En AccTek Laser, ofrecemos una amplia gama de equipos de corte por láser de fibra diseñados para satisfacer una variedad de necesidades industriales. Nuestros expertos pueden ayudarlo a elegir el modelo y la configuración más eficientes energéticamente, teniendo en cuenta factores como el tipo de material, el grosor y el volumen de producción. También ofrecemos características de vanguardia como generadores láser de alta eficiencia, sistemas de enfriamiento inteligentes y software de gestión de energía para maximizar el rendimiento y minimizar el uso de energía. Además, nuestro equipo brinda servicios de mantenimiento periódicos y soporte técnico para mantener su equipo en máxima eficiencia. Al trabajar con nosotros, puede lograr ahorros de energía significativos, reducir los costos operativos y mejorar sus esfuerzos de sostenibilidad. Si tiene alguna pregunta, comuníquese con nosotros a tiempo. ¡AcccTek Laser se compromete a brindar soluciones láser perfectas para cada cliente!
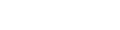
Información del contacto
- [email protected]
- [email protected]
- +86-19963414011
- No. 3 Zona A, Zona Industrial de Lunzhen, Ciudad de Yucheng, Provincia de Shandong.
Obtenga soluciones láser