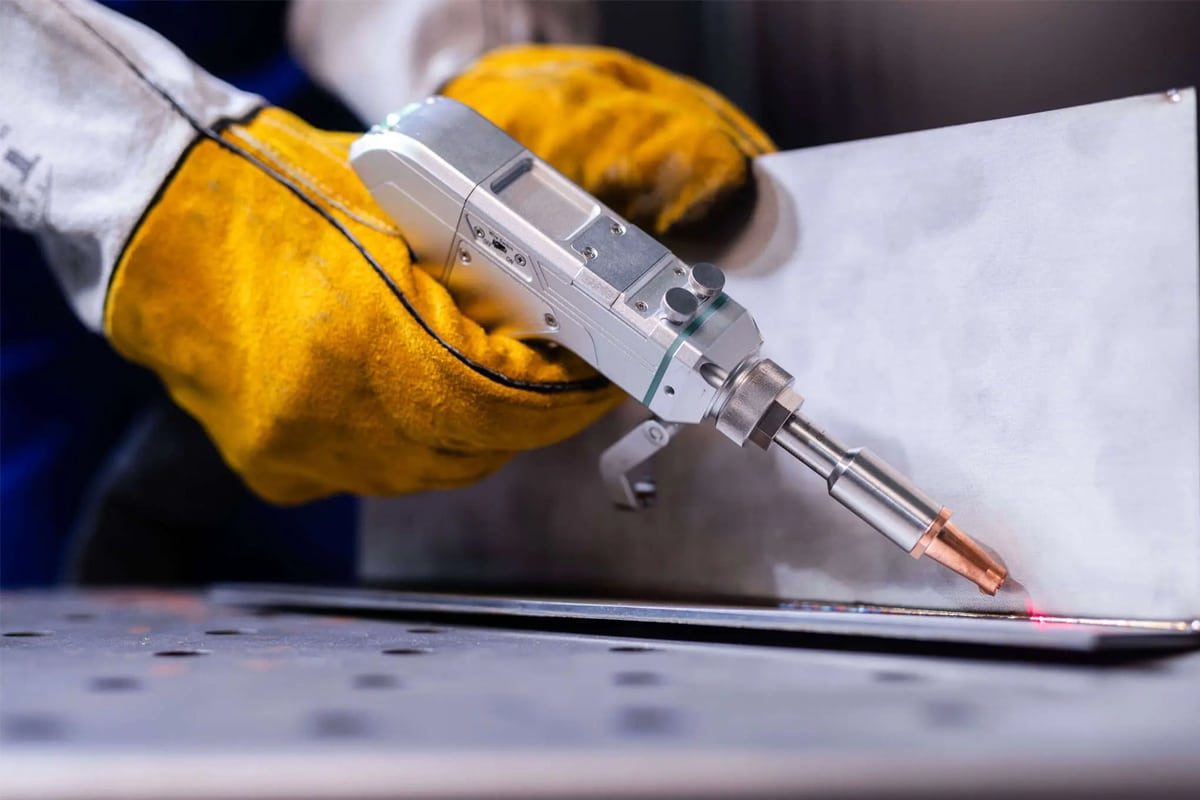
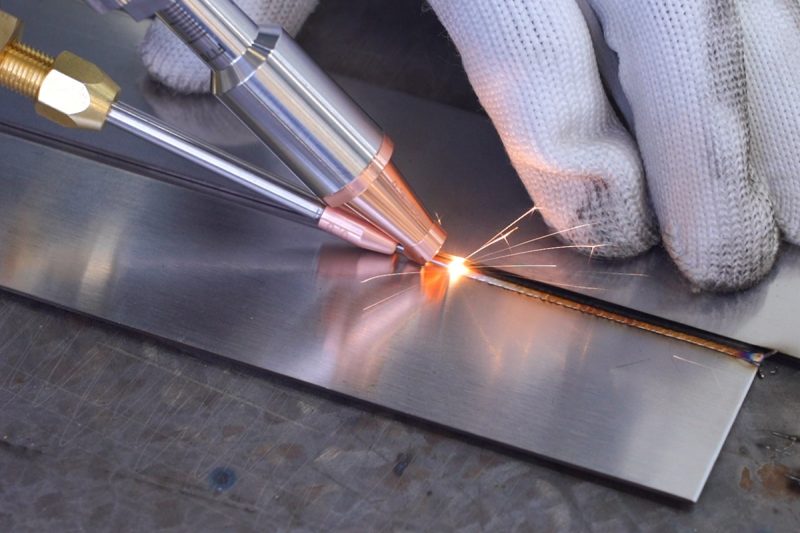
Descripción general de la soldadura láser
¿Qué es la soldadura láser?
La soldadura láser es un proceso de unión preciso y eficiente que utiliza un haz láser altamente enfocado para calentar y fusionar materiales. El haz láser genera una fuente de calor concentrada, lo que permite realizar soldaduras estrechas y profundas con mínimas zonas afectadas por el calor (ZAT). La soldadura láser funciona en dos modos principales, según la densidad de potencia y las propiedades del material:
- Soldadura en modo ojo de cerradura: en este modo, un haz láser de alta densidad de potencia vaporiza el material, creando un ojo de cerradura estrecho y profundo lleno de metal fundido y vapor. El ojo de cerradura actúa como un conducto para la energía láser, lo que permite una penetración profunda y soldaduras con una alta relación de aspecto. Este modo es ideal para aplicaciones que requieren soldaduras profundas y estrechas, como en las industrias automotriz y aeroespacial.
- Soldadura por conducción: este modo se produce con densidades de potencia más bajas en comparación con la soldadura por orificio de cerradura, donde el láser calienta el material sin vaporizarlo. La conducción de calor desde la superficie crea un baño de soldadura más ancho y poco profundo. La soldadura por conducción es adecuada para materiales delgados o cuando se desea una penetración y una entrada de calor mínimas.
Ventajas de la soldadura láser
La soldadura láser ofrece varias ventajas que la hacen ventajosa frente a los métodos de soldadura tradicionales:
- Precisión y exactitud: el rayo láser concentrado permite un control preciso, produciendo soldaduras precisas con una distorsión mínima.
- Procesamiento de alta velocidad: La alta densidad de energía del láser permite velocidades de soldadura rápidas, aumentando la productividad y reduciendo los tiempos de ciclo.
- Zona mínima afectada por el calor: la propagación térmica reducida minimiza la distorsión, lo que hace que la soldadura láser sea adecuada para componentes delicados o delgados.
- Capacidad de automatización: la soldadura láser se integra fácilmente en sistemas automatizados y brazos robóticos, lo que mejora la eficiencia para la producción de gran volumen.
- Versatilidad del material: capaz de soldar una amplia gama de metales y aleaciones, incluidos materiales difíciles de soldar, como el titanio y el acero inoxidable.
- Proceso sin contacto: No se requiere contacto físico, lo que reduce el desgaste de las herramientas y elimina el riesgo de contaminación de los electrodos.
Aplicaciones de la soldadura láser
La soldadura láser se utiliza en numerosas industrias debido a sus capacidades únicas y precisión:
- Industria automotriz: se utiliza para soldar paneles de carrocería, engranajes, componentes de transmisión y sistemas de escape, donde la alta precisión y velocidad son fundamentales.
- Industria aeroespacial: Adecuado para soldar componentes livianos y de alta resistencia, como álabes de turbinas, piezas estructurales y componentes de motores.
- Industria electrónica: ideal para microsoldadura de circuitos delicados, conectores y carcasas en dispositivos electrónicos.
- Fabricación de dispositivos médicos: se utiliza para soldar dispositivos médicos complejos, instrumentos quirúrgicos y componentes implantables donde la precisión y la limpieza son primordiales.
- Joyería y arte: permite realizar reparaciones complejas y fabricar diseños de joyería complejos y trabajos artísticos en metal.
- Fabricación industrial: se aplica en la unión de láminas de metal, tuberías y componentes estructurales de alta resistencia en diversos sectores industriales.
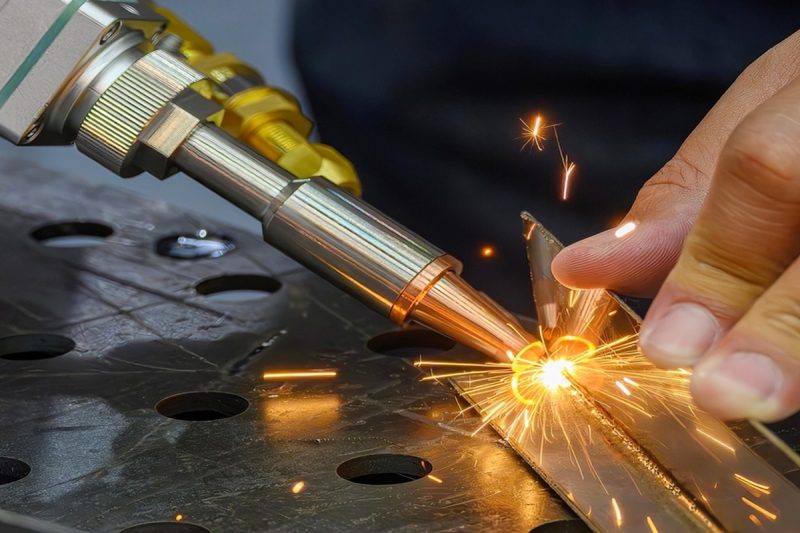
Defectos de soldadura más comunes en la soldadura láser
Porosidad
Causas
- Contaminación de la superficie: el aceite, la grasa, la humedad y el óxido en la superficie de la pieza de trabajo pueden generar gas cuando se calienta, lo que provoca burbujas atrapadas dentro de la soldadura.
- Problemas con el gas protector: una cobertura inadecuada del gas protector, caudales bajos o un tipo de gas inadecuado pueden provocar contaminación atmosférica, como la intrusión de oxígeno y nitrógeno, que forma bolsas de gas.
- Composición del material: Altas concentraciones de hidrógeno, azufre, carbono u otras impurezas en el metal base pueden provocar la evolución de gases durante la soldadura.
- Enfriamiento rápido: La solidificación rápida del baño fundido puede atrapar el gas antes de que escape.
Soluciones
- Limpieza de superficies: Limpie completamente las piezas de trabajo antes de soldar, eliminando contaminantes como grasa, aceite y óxido.
- Flujo de gas de protección optimizado: utilice gases de protección adecuados, como argón o helio, para garantizar el caudal y la cobertura correctos para proteger el baño de soldadura.
- Selección y preparación de materiales: Elija materiales con bajo contenido de impurezas y realice tratamientos previos a la soldadura, como desgasificación.
- Ajuste de parámetros: ajuste los parámetros del láser para permitir un enfriamiento controlado, dando tiempo a los gases para escapar.
Agrietamiento
Tipos de agrietamiento
- Agrietamiento en caliente: se produce a altas temperaturas durante la solidificación debido a tensiones de tracción o segregación de impurezas (por ejemplo, azufre).
- Agrietamiento en frío: se forma después del enfriamiento, a menudo asociado con fragilización por hidrógeno, tensiones residuales o composición inadecuada del material.
Causas
- Gradientes térmicos elevados: Los ciclos rápidos de calentamiento y enfriamiento pueden introducir tensiones residuales que favorecen el agrietamiento.
- Composición del material: Ciertas aleaciones, particularmente aquellas con alto contenido de azufre o carbono, son más susceptibles al agrietamiento.
- Impurezas: Elementos como el azufre y el fósforo pueden segregarse en los límites de los granos, debilitando la estructura.
- Absorción de hidrógeno: el hidrógeno introducido a través de la humedad, el gas de protección contaminado o el metal base puede provocar un agrietamiento retardado.
Soluciones
- Precalentamiento y tratamiento térmico posterior a la soldadura: precaliente la pieza de trabajo para reducir los gradientes térmicos y realice tratamientos térmicos posteriores a la soldadura para aliviar las tensiones residuales.
- Control de materiales: Seleccionar materiales con bajos niveles de impurezas y optimizar su composición química para reducir la susceptibilidad a las grietas.
- Control de hidrógeno: Seque los materiales y utilice procesos con bajo contenido de hidrógeno, como el uso de gases de protección secos y evitando la humedad.
- Técnicas de alivio de tensión: utilice accesorios y diseños de juntas adecuados para minimizar la concentración de tensión.
Vender a menor precio que
Causas
- Entrada de calor excesiva: la alta potencia del láser o las velocidades de desplazamiento lentas pueden provocar una fusión localizada y una pérdida de material sin suficiente metal de relleno.
- Ángulo del haz incorrecto: la desalineación del haz láser con respecto a la unión puede provocar la eliminación de material en lugar de la fusión.
- Enfoque inadecuado: un enfoque láser incorrecto puede concentrar la energía de manera desigual.
Soluciones
- Optimice la entrada de calor: ajuste la potencia del láser, la velocidad de desplazamiento y el diámetro del haz para controlar la distribución del calor.
- Alineación del haz: alinee correctamente el haz láser con la junta para garantizar una fusión y un llenado uniformes.
- Técnica de soldadura: Ajuste el ángulo y la posición del láser para reducir la pérdida de material.
Falta de fusión
Causas
- Entrada de calor insuficiente: una potencia láser baja o una velocidad de desplazamiento excesiva pueden impedir la fusión completa de los materiales base.
- Preparación inadecuada de la unión: un ajuste deficiente, espacios o una desalineación entre las piezas de trabajo pueden inhibir la fusión completa.
- Contaminación: Los óxidos de la superficie, la suciedad u otros contaminantes pueden actuar como barreras para la fusión.
Soluciones
- Aumente la entrada de calor: utilice suficiente potencia láser o reduzca la velocidad de desplazamiento para lograr una fusión adecuada.
- Mejore el ajuste de las juntas: garantice la alineación y el ajuste adecuados entre las piezas de trabajo para una penetración de soldadura constante.
- Limpieza de superficies: elimine óxidos, aceites y otros contaminantes de las superficies de soldadura.
Penetración incompleta
Causas
- Potencia baja del láser: entrada de energía insuficiente para fundir completamente el espesor del material.
- Alta velocidad de desplazamiento: el láser se mueve demasiado rápido para calentar y derretir completamente la unión.
- Enfoque inadecuado del haz: enfocar el láser de forma incorrecta puede provocar una penetración superficial.
Soluciones
- Aumente la potencia del láser: ajuste la configuración de potencia para garantizar una penetración completa a través de la junta.
- Reducir la velocidad de desplazamiento: deja más tiempo para que el láser caliente y derrita el material.
- Enfoque correcto del haz: enfoque correctamente el láser para lograr una profundidad de penetración constante.
Salpicar
Causas
- Potencia excesiva del láser: Los ajustes de alta potencia pueden provocar una ebullición violenta del baño de metal fundido.
- Contaminantes: Las impurezas de la superficie pueden reaccionar con el calor, creando una vaporización rápida.
- Gas de protección inadecuado: Una protección inadecuada puede provocar oxidación y provocar salpicaduras.
Soluciones
- Ajustar los parámetros del láser: reduzca la potencia del láser y optimice la configuración del pulso para evitar una entrada excesiva de energía.
- Limpieza de superficies: Asegúrese de que las superficies estén libres de contaminantes antes de soldar.
- Optimización del gas de protección: utilice el gas de protección adecuado y mantenga los caudales adecuados.
Irregularidades en el cordón de soldadura
Causas
- Velocidad de viaje inconsistente: las fluctuaciones en la velocidad provocan una entrada de calor desigual.
- Variabilidad de la potencia del láser: los cambios en la potencia de salida pueden provocar una fusión inconsistente.
- Enfoque incorrecto del haz: un enfoque desalineado provoca una distribución desigual de la energía.
Soluciones
- Mantenga una velocidad de desplazamiento constante: asegúrese de tener una velocidad uniforme durante todo el proceso de soldadura.
- Estabilizar la salida de potencia: utilice una fuente de energía estable para mantener una salida láser constante.
- Ajustar el enfoque del haz: asegúrese de que la alineación y el enfoque del haz sean correctos para lograr una distribución uniforme de la energía.
Quemadura
Causas
- Entrada de calor excesiva: una potencia láser alta o velocidades de desplazamiento lentas pueden provocar una fusión excesiva.
- Material delgado: Las láminas delgadas son más propensas a quemarse.
- Enfoque incorrecto del haz: concentrar la energía en un área pequeña puede agravar la fusión.
Soluciones
- Reducir la entrada de calor: Disminuya la potencia del láser o aumente la velocidad de desplazamiento.
- Ampliar el enfoque del haz: distribuye la energía del láser de manera más uniforme.
- Utilice el espesor de material apropiado: Adapte el espesor del material a los requisitos de soldadura.
Deformación y distorsión
Causas
- Estrés térmico: Los ciclos rápidos de calentamiento y enfriamiento provocan expansión y contracción.
- Materiales delgados: más susceptibles a deformarse y doblarse.
- Entrada excesiva de calor: una entrada elevada de energía puede provocar una distorsión grave.
Soluciones
- Optimice la entrada de calor: utilice parámetros láser controlados para minimizar el calor excesivo.
- Fijación y sujeción: mantenga las piezas de trabajo en su lugar con fijaciones para reducir el movimiento.
- Soldadura equilibrada: utilice técnicas que equilibren el calentamiento y minimicen el estrés.
Oxidación y decoloración
Causas
- Gas de protección inadecuado: un flujo de gas bajo o una cobertura deficiente pueden exponer el baño de soldadura al aire.
- Composición inadecuada del gas: La elección incorrecta del gas de protección puede no lograr prevenir la oxidación.
- Contaminantes: Las impurezas de la superficie pueden reaccionar y causar oxidación.
Soluciones
- Asegúrese de una protección adecuada: utilice un flujo adecuado de gas protector para proteger el baño de soldadura.
- Seleccione la composición de gas adecuada: elija un gas de protección que prevenga eficazmente la oxidación (por ejemplo, argón).
- Limpieza de superficies: Limpie minuciosamente las superficies de las piezas de trabajo para minimizar las reacciones durante la soldadura.
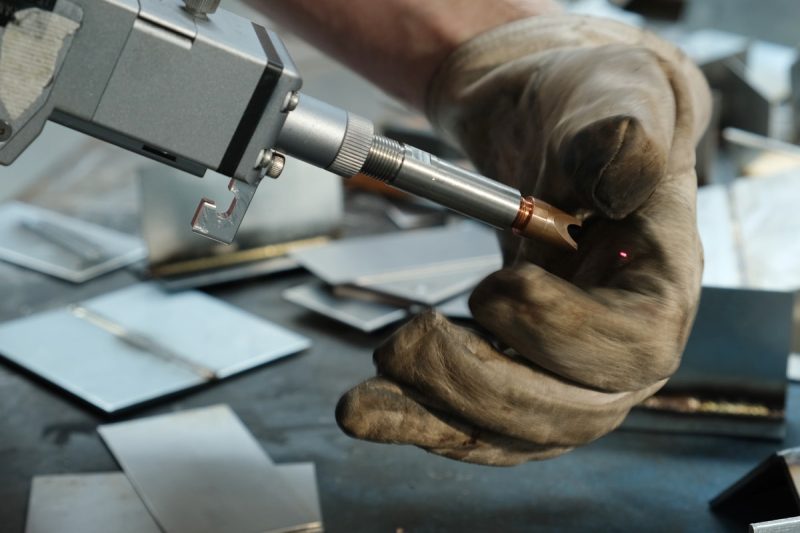
Factores que influyen en los defectos de soldadura
Propiedades materiales
Las propiedades de los materiales que se sueldan juegan un papel importante a la hora de determinar la calidad de la soldadura y la probabilidad de defectos.
- Conductividad térmica: los materiales con alta conductividad térmica, como el aluminio, tienden a disipar el calor rápidamente, por lo que requieren una mayor potencia del láser o velocidades de desplazamiento más lentas para lograr una penetración y fusión suficientes. Un control insuficiente puede provocar defectos como la falta de fusión o una penetración incompleta.
- Punto de fusión: los materiales con distintos puntos de fusión requieren distintos parámetros láser. Por ejemplo, el titanio tiene un punto de fusión alto y requiere un mayor aporte de energía, mientras que los materiales con un punto de fusión bajo, como el zinc, pueden sufrir quemaduras si no se manejan con cuidado.
- Reflectividad: Los materiales altamente reflectantes, como el cobre y ciertas aleaciones de aluminio, pueden reflejar una parte de la energía del láser, lo que reduce la entrada de calor efectiva. Esto puede provocar una fusión incompleta, una penetración inconsistente o salpicaduras, ya que la energía reflejada puede afectar las áreas circundantes.
- Composición del material e impurezas: elementos como el azufre, el fósforo y el hidrógeno en el material pueden aumentar la probabilidad de defectos como porosidad y agrietamiento. Por ejemplo, un alto contenido de hidrógeno puede causar porosidad, mientras que el azufre y el fósforo aumentan el riesgo de agrietamiento en caliente. Seleccionar materiales con bajos niveles de impurezas o realizar tratamientos previos a la soldadura puede ayudar a mitigar estos problemas.
Parámetros de soldadura
La selección y el control adecuados de los parámetros de soldadura láser son fundamentales para prevenir defectos. Entre los parámetros clave se incluyen los siguientes:
- Potencia del láser: una potencia láser adecuada es esencial para lograr una penetración y fusión completas. Una potencia insuficiente puede provocar una falta de fusión o una penetración incompleta, mientras que una potencia excesiva puede provocar quemaduras, salpicaduras y deformaciones.
- Velocidad de desplazamiento: La velocidad de desplazamiento afecta el aporte de calor por unidad de longitud de la soldadura. Una velocidad demasiado alta puede impedir que el material se caliente adecuadamente, lo que produce defectos como falta de fusión y penetración incompleta. Por el contrario, una velocidad demasiado lenta puede provocar un aporte de calor excesivo, lo que provoca quemaduras y distorsión.
- Enfoque del haz: el enfoque correcto del haz es esencial para la concentración de energía. Una alineación incorrecta o una posición focal incorrecta pueden provocar una penetración insuficiente, perfiles irregulares del cordón y porosidad en la soldadura. Para una penetración profunda, es necesario un haz enfocado con un tamaño de punto pequeño, mientras que un haz desenfocado puede ser adecuado para soldaduras más anchas y poco profundas.
- Duración del pulso (en la soldadura láser pulsada): la duración del pulso afecta la cantidad de energía suministrada en cada pulso. Los pulsos cortos reducen la entrada de calor y minimizan el riesgo de deformación, lo que los hace ideales para materiales delicados o sensibles al calor. Los pulsos más largos permiten una mayor penetración, pero pueden aumentar el riesgo de defectos como salpicaduras y porosidad.
Diseño conjunto
El diseño y la preparación de la unión pueden influir significativamente en la calidad de la soldadura y la probabilidad de defectos.
- Tolerancia de ajuste: el ajuste correcto de las uniones es esencial para lograr una calidad de soldadura uniforme. Los espacios o la desalineación entre las piezas de trabajo pueden provocar una falta de fusión, porosidad o penetración inconsistente. Los ajustes ajustados permiten un mejor control del baño de fusión y minimizan el riesgo de defectos.
- Tipo de unión: los distintos tipos de unión (por ejemplo, a tope, traslape, filete) requieren diferentes técnicas y parámetros de soldadura láser. Por ejemplo, las uniones a tope con una alineación deficiente pueden provocar socavaduras o falta de fusión, mientras que las uniones traslapadas con una superposición excesiva pueden provocar salpicaduras y una fusión insuficiente.
- Accesibilidad: En estructuras complejas, el acceso limitado a la unión puede restringir el alcance del haz láser, lo que provoca una fusión incompleta o la formación de cordones irregulares. La fijación y la alineación del láser adecuadas son necesarias para las uniones con accesibilidad limitada.
- Preparación y limpieza: La preparación y limpieza adecuadas del área de unión son fundamentales, ya que los contaminantes de la superficie pueden provocar porosidad, grietas y salpicaduras. La limpieza elimina óxidos, aceites y otras impurezas que pueden interferir con la fusión y generar defectos.
Factores ambientales
Las condiciones ambientales en el área de soldadura pueden afectar directamente la calidad de la soldadura y la aparición de defectos.
- Temperatura ambiente: La soldadura a temperaturas extremas, ya sea demasiado frías o demasiado calientes, puede afectar la velocidad de enfriamiento de la soldadura y provocar tensión térmica y agrietamiento. Los entornos fríos, por ejemplo, pueden provocar un enfriamiento rápido, lo que da lugar a soldaduras frágiles y agrietamiento.
- Humedad: la humedad del ambiente puede introducir hidrógeno en el baño de soldadura, lo que aumenta el riesgo de porosidad y agrietamiento inducido por hidrógeno. Soldar en un ambiente seco y controlado o tomar precauciones para evitar la exposición a la humedad es esencial para lograr soldaduras de alta calidad.
- Calidad y flujo del gas de protección: el gas de protección protege el baño de soldadura derretido de la contaminación atmosférica. Un flujo inadecuado de gas de protección o el uso de gas de baja pureza pueden provocar oxidación, porosidad y decoloración. Además, se deben utilizar gases de protección como argón y helio según los requisitos del material para evitar la contaminación.
- Vibración y movimiento: las vibraciones ambientales o el movimiento en la configuración de soldadura pueden generar cordones de soldadura inconsistentes y otros defectos. La fijación estable y la minimización del movimiento externo son esenciales para garantizar resultados consistentes.
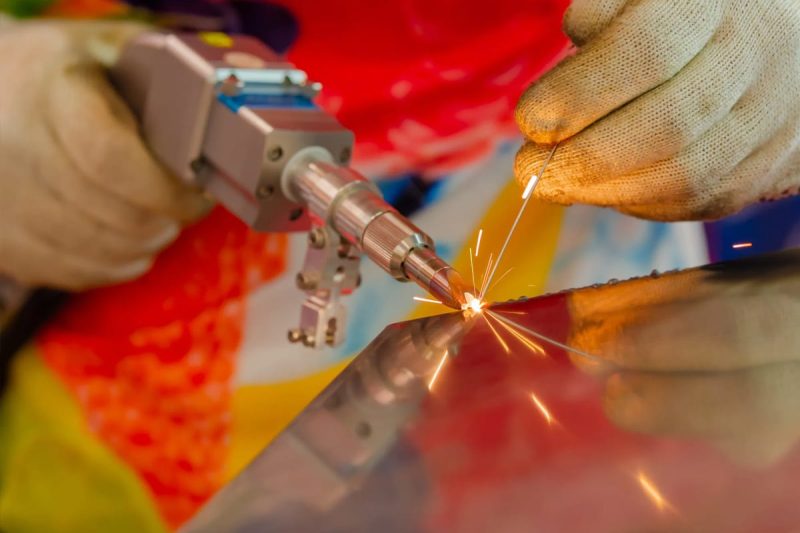
Consideraciones adicionales y mejores prácticas
Selección adecuada del material
Elegir los materiales adecuados para la soldadura láser es esencial para lograr soldaduras de alta calidad y minimizar los defectos.
- Compatibilidad de materiales: asegúrese de que los materiales de base sean compatibles con la soldadura láser. Los distintos materiales responden de forma diferente a la energía láser debido a las variaciones en los puntos de fusión, la conductividad térmica y la reflectividad. Por ejemplo, los materiales reflectantes como el aluminio pueden requerir medidas especiales para reducir la reflexión y optimizar la absorción de calor.
- Pureza del material: utilice materiales con bajos niveles de impurezas, como azufre y fósforo, que pueden contribuir a la porosidad, el agrietamiento y otros defectos.
- Espesor del material: tenga en cuenta el espesor de los materiales a soldar, ya que influye en la potencia del láser y el aporte de calor necesarios.
Tipo de láser y configuraciones
Seleccionar el tipo de láser apropiado y ajustar su configuración son factores críticos para una soldadura láser exitosa.
- Tipo de láser: elija entre láseres de onda continua (CW) y láseres pulsados según la aplicación. Los láseres de onda continua (CW) son ideales para soldaduras de alta velocidad, mientras que los láseres pulsados son adecuados para componentes delicados o sensibles al calor.
- Configuraciones de potencia y velocidad: optimice la potencia del láser, la velocidad de desplazamiento y la duración del pulso para lograr la penetración deseada, minimizar defectos como salpicaduras o porosidad y controlar la entrada de calor.
- Enfoque y posicionamiento del haz: la alineación y el enfoque adecuados del haz son esenciales para una distribución uniforme de la energía y soldaduras consistentes.
Diseño y montaje de juntas
El diseño y ajuste adecuados de las uniones garantizan una calidad de soldadura constante y reducen la probabilidad de defectos como falta de fusión, porosidad y desalineación.
- Tolerancias de ajuste: asegúrese de que las uniones tengan ajustes firmes y consistentes, minimizando los espacios que podrían provocar una fusión desigual o porosidad.
- Accesibilidad de las juntas: Diseñe las juntas para permitir un fácil acceso del rayo láser, minimizando el riesgo de fusión incompleta o cordones irregulares.
- Preparación de las juntas: Limpie y prepare adecuadamente las superficies de las juntas para eliminar contaminantes, como aceites, óxidos y otras impurezas.
Selección del gas de protección
El gas protector protege el baño de soldadura fundida de la contaminación atmosférica, evitando la oxidación, la porosidad y otros defectos.
- Tipo de gas: seleccione los gases de protección adecuados, como argón, helio o mezclas, según el material de base y las características de soldadura deseadas. Por ejemplo, el argón se utiliza a menudo para el acero inoxidable, mientras que el helio puede mejorar la penetración en materiales más gruesos.
- Caudal: Asegúrese de que el caudal del gas de protección sea suficiente para cubrir el baño de soldadura sin turbulencias ni cobertura inadecuada.
- Pureza: Utilice gas de protección de alta pureza para evitar la contaminación.
Tratamientos pre-soldadura y post-soldadura
Los tratamientos previos y posteriores a la soldadura pueden reducir significativamente la probabilidad de defectos y mejorar la calidad general de la soldadura.
- Limpieza previa a la soldadura: limpie a fondo las piezas de trabajo para eliminar contaminantes, como aceites, óxido y humedad, que pueden provocar porosidad, grietas y otros defectos.
- Precalentamiento: el precalentamiento de los materiales, especialmente aquellos propensos a agrietarse, puede reducir los gradientes térmicos y minimizar las tensiones residuales.
- Tratamiento térmico posterior a la soldadura: Realice tratamientos térmicos posteriores a la soldadura, como recocido o alivio de tensiones, para reducir las tensiones residuales y mejorar las propiedades mecánicas de la soldadura.
Capacitación de los operadores
Los operadores capacitados desempeñan un papel fundamental para garantizar soldaduras láser consistentes y de alta calidad.
- Capacitación técnica: capacitar a los operadores en el manejo adecuado de equipos de soldadura láser, incluido el posicionamiento, el control de velocidad y los ajustes de parámetros.
- Identificación de defectos: educar a los operadores para reconocer defectos comunes, sus causas y cómo realizar los ajustes necesarios para evitar que vuelvan a ocurrir.
- Protocolos de seguridad: Asegúrese de que los operadores estén capacitados en los procedimientos de seguridad del láser para protegerse a sí mismos y al entorno de trabajo.
Mantenimiento de equipo
El mantenimiento regular del equipo de soldadura láser es esencial para garantizar un rendimiento constante y evitar defectos.
- Limpieza de ópticas: Limpie periódicamente las lentes, los espejos y otros componentes ópticos para mantener la calidad y la precisión del haz.
- Calibración: calibre periódicamente los sistemas láser para garantizar una salida de potencia, una alineación del haz y un enfoque precisos.
- Inspección de componentes: inspeccione y reemplace los componentes desgastados o dañados, como boquillas y lentes, para mantener la consistencia de la soldadura.
Monitoreo de procesos
La supervisión y el control del proceso son vitales para lograr soldaduras consistentes y sin defectos.
- Monitoreo en tiempo real: utilice sensores y sistemas de monitoreo para detectar y corregir desviaciones en los parámetros de soldadura, como fluctuaciones de potencia, velocidad de desplazamiento y enfoque del haz, en tiempo real.
- Registro de datos: registre los parámetros y resultados de la soldadura para analizar tendencias, identificar las causas fundamentales de los defectos e implementar medidas de mejora continua.
- Inspecciones de calidad: Realice inspecciones periódicas, incluidos métodos de pruebas no destructivas (NDT), para verificar la calidad de la soldadura.
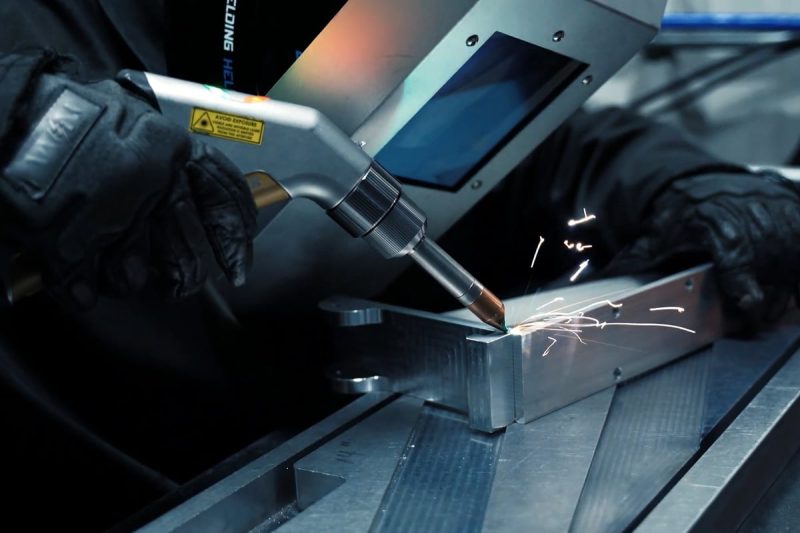
Resumen
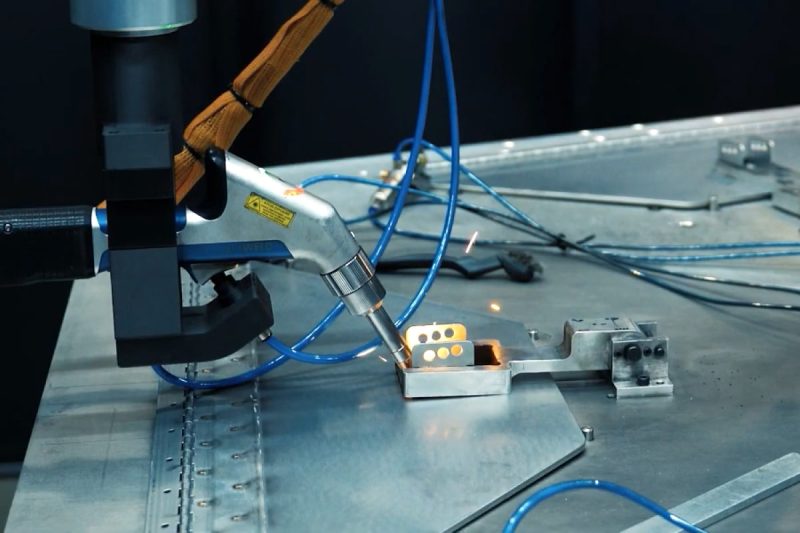
Obtenga soluciones de soldadura láser
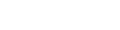
- [email protected]
- [email protected]
- +86-19963414011
- No. 3 Zona A, Zona Industrial de Lunzhen, Ciudad de Yucheng, Provincia de Shandong.