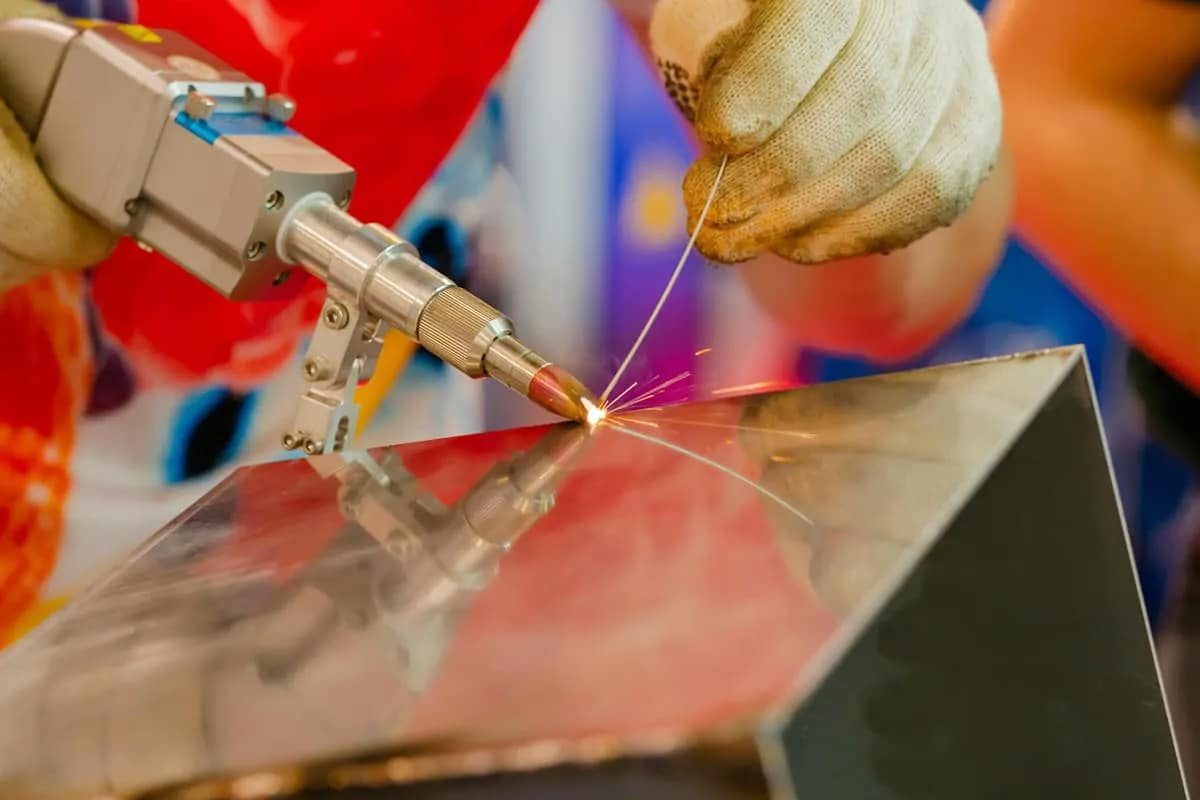
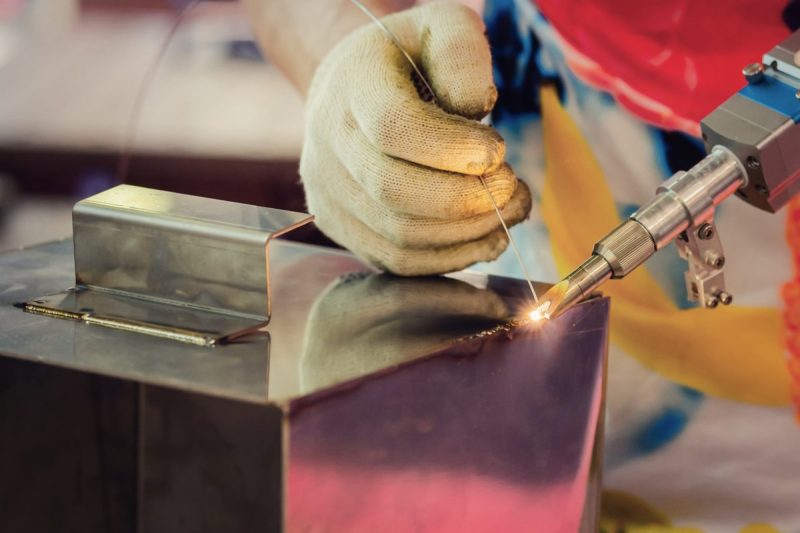
Parámetros del láser
Potencia láser
La potencia del láser es un parámetro fundamental en la soldadura láser y determina la cantidad de energía entregada al área de soldadura. El ajuste de potencia afecta la velocidad de soldadura y la profundidad de penetración.
- Alta potencia: el uso de alta potencia del láser aumenta la velocidad de soldadura y la profundidad de penetración, lo que permite soldar materiales más gruesos. Es particularmente útil para aplicaciones que requieren soldaduras profundas o alta productividad. Sin embargo, una potencia demasiado alta puede provocar sobrecalentamiento, fusión excesiva y defectos como salpicaduras y porosidad.
- Baja potencia: Las potencias láser más bajas son adecuadas para materiales más delgados y aplicaciones que requieren alta precisión, como la microsoldadura. Sin embargo, una potencia insuficiente puede provocar soldaduras débiles debido a una fusión incompleta o una penetración insuficiente.
- Optimización: Lograr una potencia láser óptima requiere equilibrar las necesidades de penetración y velocidad con los riesgos de defectos. Esto requiere una calibración cuidadosa basada en el tipo de material, el espesor y los requisitos de soldadura específicos.
Longitud de onda
La longitud de onda de un láser afecta qué tan bien el material que se está soldando absorbe la energía del láser. Diferentes materiales tienen diferentes características de absorción a diferentes longitudes de onda.
- Longitudes de onda comunes: Las longitudes de onda típicas utilizadas en la soldadura láser incluyen infrarrojos (IR), luz visible y ultravioleta (UV). Cada longitud de onda tiene sus ventajas, según el material y la aplicación.
- Láseres infrarrojos (IR): los láseres IR, como los de CO2 y de fibra, se usan comúnmente para soldar metales y son efectivos en materiales con alta absorción en el espectro infrarrojo.
- Láseres visibles y UV: estas longitudes de onda son absorbidas más fácilmente por los no metales y algunos metales reflectantes, lo que las hace útiles para aplicaciones que involucran plásticos y cerámicas.
- Consideraciones específicas del material: Materiales como el aluminio y el cobre, que son altamente reflectantes en el rango infrarrojo, pueden requerir láseres con longitudes de onda que estos metales absorben más fácilmente. Los recubrimientos especiales o fuentes láser con longitudes de onda específicas pueden mejorar la absorción y la eficiencia de la soldadura.
Duración y frecuencia del pulso
La duración y la frecuencia del pulso son parámetros críticos en la soldadura por láser pulsado, donde el láser opera en pulsos cortos en lugar de una onda continua.
- Duración del pulso: la duración de cada pulso láser puede afectar significativamente las características térmicas de la soldadura. Los pulsos más cortos entregan energía en ráfagas breves e intensas, minimizando la zona afectada por el calor (HAZ) y reduciendo la deformación térmica. Las duraciones de pulso más largas entregan más energía, pero pueden aumentar la ZAT y el riesgo de daño térmico.
- Frecuencia de pulso: La frecuencia de los pulsos, o la cantidad de pulsos por segundo, afecta la entrega general de energía y la velocidad de soldadura. Las frecuencias más altas pueden aumentar la velocidad de soldadura, pero también pueden aumentar el riesgo de acumulación de calor, lo que puede causar defectos.
- Optimización: la combinación de duración y frecuencia del pulso debe optimizarse en función de las propiedades del material y las características de soldadura deseadas. El ajuste fino de estos parámetros ayuda a lograr un equilibrio entre la velocidad de soldadura, la penetración y el efecto térmico.
Calidad del haz
La calidad de un rayo láser se define por parámetros como la estructura del modo y el perfil del haz, que impactan directamente en la eficiencia de la soldadura.
- Modo de haz: El modo de un rayo láser (por ejemplo, TEM00) determina su distribución de intensidad. Una estructura de modo de alta calidad garantiza una entrega de energía concentrada y uniforme, lo que resulta en una soldadura consistente y precisa.
- Perfil de viga: un perfil de viga uniforme y bien definido minimiza las pérdidas de energía y garantiza la máxima entrega de energía al área de soldadura. La mala calidad del haz (caracterizada por un perfil distorsionado o irregular) da como resultado un calentamiento desigual y defectos de soldadura.
- Viabilidad: La alta calidad del haz permite un mejor enfoque, lo que permite que el láser alcance tamaños de punto más pequeños para aplicaciones que requieren alta precisión y detalles finos.
Posición focal
La posición del punto focal del láser con respecto a la superficie del material es un parámetro crítico que afecta la eficiencia y calidad de la soldadura.
- Enfoque correcto: enfocar correctamente el rayo láser en el área de soldadura garantiza la máxima densidad de energía y una fusión eficiente del material. La posición focal óptima depende del espesor del material y de las características de soldadura deseadas. Para la soldadura de penetración profunda, el punto focal generalmente se coloca ligeramente por debajo de la superficie del material.
- Distancia focal: la distancia focal de la óptica láser determina la profundidad focal y el tamaño focal. Las distancias focales cortas producen tamaños de punto más pequeños y densidades de energía más altas para tareas de soldadura fina. Las distancias focales más largas proporcionan mayores profundidades focales, lo que resulta beneficioso para soldar materiales más gruesos.
- Tolerancia de enfoque: Mantener una posición focal consistente puede ayudar a lograr una calidad de soldadura uniforme. Las variaciones en la posición focal pueden provocar una penetración inconsistente, una fusión incompleta y defectos. Los sistemas automatizados con ajuste de enfoque en tiempo real pueden ayudar a mantener un enfoque óptimo durante el proceso de soldadura.
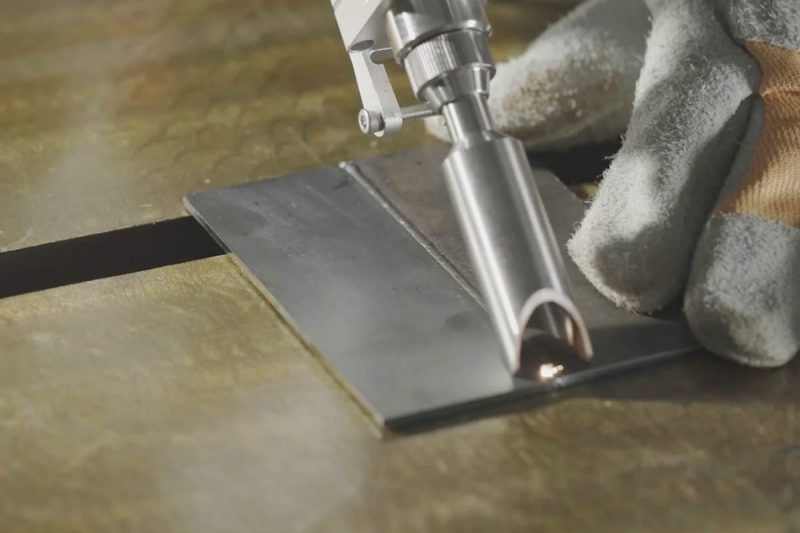
Propiedades materiales
tipo de material
El tipo de material que se está soldando es el factor principal para determinar la eficiencia de la soldadura láser. Los diferentes materiales absorben y conducen la energía láser de diferentes maneras, lo que afecta la calidad de la soldadura y los parámetros del proceso.
- Metales: Los metales comúnmente soldados incluyen acero, aluminio, titanio y cobre. Cada metal tiene diferentes propiedades:
- Acero: Generalmente se puede soldar bien con láser debido a su buena absorción de la energía láser. Varios grados de acero, incluidos el acero al carbono, el acero inoxidable y el acero aleado, pueden requerir diferentes configuraciones del láser.
- Aluminio: El aluminio es conocido por su alta reflectividad y conductividad térmica, y soldar aluminio con láser puede ser un desafío. Longitudes de onda o recubrimientos especiales pueden mejorar la absorbancia.
- Titanio: El titanio se puede soldar eficazmente con un láser debido a su moderada reflectividad y propiedades térmicas. Es ampliamente utilizado en aplicaciones aeroespaciales y médicas.
- Cobre: La alta reflectividad y conductividad térmica del cobre dificultan la soldadura con una configuración láser tradicional. A menudo se utilizan láseres de fibra con longitudes de onda específicas para mejorar la eficiencia.
- No metales: materiales como plásticos, cerámicas y compuestos también se pueden soldar con láser. Cada no metal requiere parámetros láser específicos para una soldadura eficiente:
- Plásticos: Los plásticos generalmente absorben bien la energía del láser, pero sus propiedades térmicas requieren un control cuidadoso de los parámetros de soldadura para evitar quemarse o derretirse.
- Cerámica: La cerámica es frágil y puede agrietarse bajo estrés térmico. La soldadura por láser de cerámica generalmente requiere precalentamiento y uso de láseres con longitudes de onda específicas para reducir la tensión.
- Compuestos: Los compuestos combinan diferentes materiales y requieren un ajuste cuidadoso de los parámetros para garantizar una calidad de soldadura uniforme en los diferentes componentes.
Espesor
El espesor del material es un factor clave que afecta la eficiencia de la soldadura láser. Afecta la potencia láser requerida, la velocidad de soldadura y la estabilidad general del proceso.
- Materiales delgados: Los materiales delgados requieren una menor potencia del láser y velocidades de soldadura más altas para evitar quemaduras y una entrada excesiva de calor. El control preciso de los parámetros del láser permite realizar soldaduras limpias y sin defectos.
- Materiales gruesos: soldar materiales gruesos requiere una mayor potencia del láser y velocidades de soldadura más lentas para garantizar una penetración y fusión adecuadas. Se pueden utilizar técnicas avanzadas como la soldadura de múltiples pasadas o la soldadura híbrida (que combina soldadura por láser y por arco) para lograr una penetración total.
- Zona de transición: al soldar materiales de diferentes espesores, los parámetros del láser deben ajustarse dinámicamente para adaptarse a las diferencias en la absorción y conducción del calor.
Condición de la superficie
El estado de la superficie de un material puede afectar la absorción del láser, la transferencia de calor y la calidad general de la soldadura. La preparación adecuada de la superficie ayuda a lograr una soldadura láser eficiente.
- Limpieza: Contaminantes como aceite, grasa, suciedad y capas de óxido pueden interferir con la absorción del láser y causar defectos en la soldadura. Es necesario limpiar minuciosamente la superficie antes de soldar para garantizar resultados óptimos.
- Rugosidad de la superficie: la rugosidad de la superficie de un material puede afectar la interacción del rayo láser. Las superficies más lisas generalmente dan como resultado una mejor absorción del láser y soldaduras más consistentes. Se pueden utilizar tratamientos superficiales como pulido o granallado para mejorar las condiciones de la superficie.
- Recubrimientos y Tratamientos: Algunos materiales pueden tener recubrimientos o tratamientos que afectan la soldadura láser. Por ejemplo, el acero galvanizado tiene un recubrimiento de zinc que requiere ajustes específicos del láser para evitar la evaporación y la porosidad. Comprender los efectos de estos recubrimientos puede ayudar a ajustar los parámetros de soldadura en consecuencia.
Propiedades termales
Las propiedades térmicas de un material, incluida la conductividad térmica, la capacidad calorífica específica y el punto de fusión, afectan la forma en que el material interactúa con la energía láser.
- Conductividad térmica: Los materiales con alta conductividad térmica, como el cobre y el aluminio, disipan el calor rápidamente y requieren potencias láser más altas para lograr una fusión adecuada. Los materiales con baja conductividad térmica, como el acero inoxidable, retienen el calor por más tiempo, por lo que la entrada de calor debe controlarse cuidadosamente para evitar una fusión excesiva.
- Capacidad calorífica específica: La capacidad calorífica específica de un material determina la cantidad de energía necesaria para elevar su temperatura. Los materiales con altas capacidades caloríficas específicas requieren más energía para soldarse, lo que afecta la elección de la potencia del láser y la velocidad de soldadura.
- Punto de fusión: el punto de fusión de un material determina la cantidad de energía necesaria para iniciar la fusión y la fusión. Los materiales de alto punto de fusión, como el titanio y ciertas aleaciones, requieren potencias láser más altas y un control preciso de los parámetros de soldadura para lograr una soldadura eficiente.
Propiedades metalúrgicas
Las propiedades metalúrgicas de un material, incluida su composición, microestructura y transformaciones de fase, desempeñan un papel fundamental en el proceso de soldadura láser.
- Composición: La composición química de un material afecta su soldabilidad. Los elementos de aleación afectan la absorción de energía láser por parte del material, el comportamiento de fusión y la susceptibilidad a defectos como agrietamiento y porosidad. Comprender la composición ayuda a seleccionar los parámetros láser y el gas de protección adecuados.
- Microestructura: La microestructura de un material, incluido el tamaño de grano y la distribución de fases, afecta sus propiedades mecánicas y su respuesta a la soldadura. Los materiales de grano fino generalmente se sueldan mejor que los materiales de grano grueso, que pueden requerir atención especial para evitar grietas y deformaciones.
- Transformaciones de fase: algunos materiales sufren transformaciones de fase durante la soldadura, lo que puede afectar las propiedades finales de la soldadura. Por ejemplo, algunos aceros se transforman de austenita a martensita a medida que se enfrían, lo que da como resultado una soldadura dura y quebradiza. Controlar las velocidades de enfriamiento y el tratamiento térmico posterior a la soldadura puede ayudar a controlar estas transformaciones y mejorar la calidad de la soldadura.
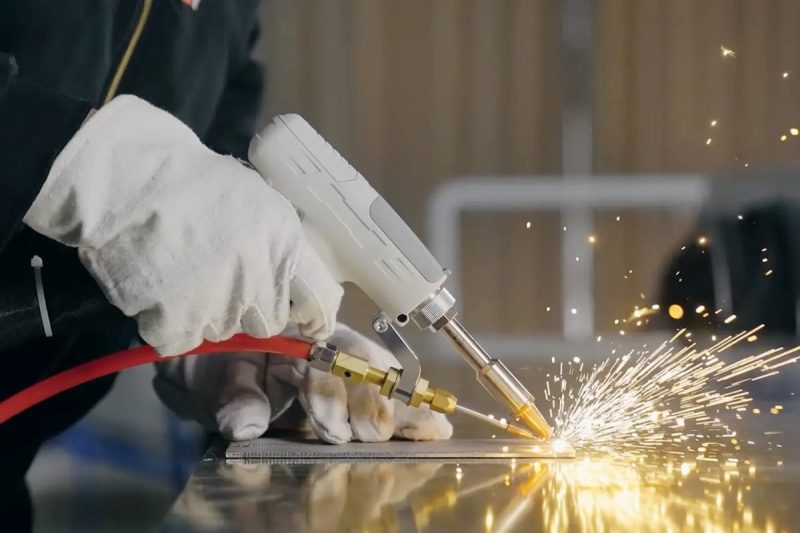
Diseño conjunto
Configuración conjunta
La configuración de la junta tiene un impacto significativo en el proceso de soldadura láser. Los diferentes tipos de juntas ofrecen distintos grados de accesibilidad, facilidad de soldadura y resistencia mecánica.
- Junta a tope: En una junta a tope, se colocan dos piezas de material de borde a borde. Esta configuración es común en la soldadura láser porque es simple y permite una penetración profunda. Sin embargo, sólo una alineación precisa y espacios mínimos pueden garantizar una soldadura de alta calidad.
- Junta traslapada: En una junta traslapada, una pieza de material se superpone a otra. Esta configuración se utiliza a menudo para soldar materiales delgados y es fácil de montar. Sin embargo, requiere un control cuidadoso de los parámetros del láser para evitar una fusión excesiva y garantizar que las dos capas se fusionen correctamente.
- Junta en T: Las juntas en T se forman soldando una pieza de material perpendicular a otra. Esta configuración se utiliza a menudo en aplicaciones estructurales. El desafío de las juntas en T es lograr una penetración uniforme y evitar defectos en la intersección.
- Junta de esquina: Las juntas de esquina se utilizan para unir dos piezas de material en ángulo recto. Se utilizan con frecuencia en estructuras y marcos en forma de caja. Garantizar una fusión adecuada en las esquinas requiere un control preciso de los parámetros del láser y la preparación de las juntas.
- Junta de borde: Las juntas de borde implican soldar a lo largo del borde de una o ambas piezas de material. Esta configuración es adecuada para materiales delgados y aplicaciones donde se requiere una superposición mínima. Lograr soldaduras consistentes en juntas de bordes requiere una alineación precisa y control de espacios.
Preparación conjunta
Una preparación adecuada de las juntas ayuda a lograr soldaduras de alta calidad. El estado de la superficie de la unión afecta directamente la absorción del láser, la transferencia de calor y la integridad general de la soldadura.
- Limpieza: La superficie de la junta debe estar libre de contaminantes como aceite, grasa, suciedad y óxidos. Los contaminantes pueden interferir con la absorción del láser y causar defectos como porosidad y fusión incompleta. Se pueden utilizar métodos de limpieza como desengrasado, cepillo de alambre y limpieza química, según el material y los contaminantes presentes.
- Tratamiento de superficie: Los tratamientos de superficie, como el pulido con chorro de arena, el esmerilado o el mecanizado, pueden mejorar la condición de la superficie y mejorar la absorción del láser. Estos tratamientos ayudan a crear una superficie lisa y uniforme con un riesgo reducido de defectos.
- Preparación de los bordes: La preparación adecuada de los bordes garantiza un buen ajuste y minimiza los espacios. Técnicas como biselado, achaflanado y redondeado de bordes pueden mejorar el ajuste de la articulación y promover una mejor fusión.
Tolerancia a la brecha
Mantener tolerancias de separación estrechas puede ayudar a lograr soldaduras láser consistentes y de alta calidad. Los espacios entre las superficies de las juntas pueden provocar una fusión incompleta, soldaduras débiles y defectos.
- Espacio mínimo: Idealmente, las superficies de las juntas deben tener un espacio mínimo para garantizar una fusión completa y una soldadura fuerte. Los espacios pequeños se pueden cubrir con material fundido, pero los espacios excesivos pueden provocar una fusión incompleta y una unión débil.
- Tolerancia permitida: La tolerancia de separación permitida depende del material, la configuración de la junta y los parámetros de soldadura. En general, las aplicaciones de alta precisión y los materiales delgados requieren tolerancias más estrictas, mientras que los materiales más gruesos pueden tolerar espacios ligeramente mayores.
- Ajustes: Si existen espacios, ajustar la potencia del láser, la velocidad de soldadura y la posición del enfoque puede ayudar a compensar y garantizar una fusión adecuada. Sin embargo, se deben evitar espacios excesivos ya que pueden afectar la calidad y resistencia de la soldadura.
Accesorios y sujeción
Los dispositivos de fijación y sujeción eficaces pueden garantizar la estabilidad y alineación de la unión durante el proceso de soldadura láser. Los dispositivos de fijación y sujeción adecuados evitan el movimiento, la deformación y la desalineación, mejorando así la eficiencia y la calidad de la soldadura.
- Estabilidad: El accesorio debe sujetar firmemente el material en su lugar para evitar cualquier movimiento durante el proceso de soldadura. Incluso un movimiento leve puede provocar desalineación, defectos y cambios en la calidad de la soldadura.
- Alineación: El sistema de sujeción debe garantizar que las superficies de las juntas estén alineadas con precisión. La desalineación puede provocar una fusión deficiente y soldaduras débiles. Los accesorios ajustables y las herramientas de sujeción de precisión pueden ayudar a lograr una alineación precisa.
- Gestión del calor: Los accesorios y abrazaderas también deben gestionar el calor generado durante el proceso de soldadura. El calor excesivo puede hacer que la articulación se deforme y se mueva. El uso de materiales con buena conductividad térmica para la luminaria o sistemas de refrigeración integrados puede ayudar a gestionar el calor y mantener la estabilidad.
- Accesibilidad: El diseño del accesorio y del sistema de sujeción debe permitir que el rayo láser llegue fácilmente al área de soldadura. Las geometrías complejas y los espacios reducidos requieren accesorios personalizados para garantizar un acceso adecuado al láser y condiciones óptimas de soldadura.
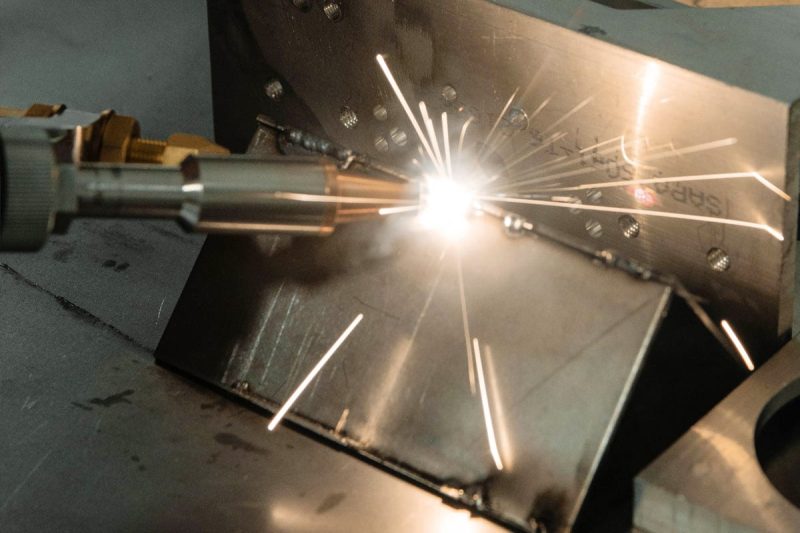
Condiciones ambientales
Temperatura ambiente
La temperatura ambiente puede afectar el proceso de soldadura láser de varias maneras. Mantener un ambiente de temperatura controlada garantiza una calidad de soldadura constante y evita problemas con el equipo.
- Rendimiento de soldadura constante: las temperaturas extremas, ya sean demasiado altas o demasiado bajas, pueden afectar las características térmicas de los materiales que se están soldando. Las altas temperaturas ambiente pueden provocar un aporte excesivo de calor y una mayor deformación térmica, mientras que las bajas temperaturas pueden provocar un enfriamiento rápido y posibles grietas.
- Estabilidad del equipo: El equipo de soldadura láser, incluida la fuente láser y el sistema de enfriamiento, funciona mejor dentro de un rango de temperatura específico:
- Alta temperatura: el calor excesivo puede causar expansión térmica del material de soldadura, lo que provoca desalineación y deformación. También puede afectar la velocidad de enfriamiento de la soldadura, afectando la microestructura y las propiedades mecánicas de la unión.
- Baja temperatura: Los ambientes extremadamente fríos pueden causar condensación en la óptica del láser y las superficies de los materiales, lo que interfiere con la absorción del láser y potencialmente causa defectos. Las bajas temperaturas también pueden afectar la conductividad térmica y el comportamiento de fusión del material.
- Medidas de control: La implementación de un sistema de control climático en el entorno de soldadura puede ayudar a mantener una temperatura ambiente estable. Esto garantiza la coherencia en el comportamiento del material y el rendimiento del equipo, lo que da como resultado un proceso de soldadura más eficiente y confiable.
Humedad
Los niveles de humedad en el entorno de soldadura pueden afectar tanto al equipo láser como a los materiales que se están soldando.
- Condensación: La humedad elevada puede provocar la formación de condensación en la óptica del láser y en las superficies de los materiales. Esto puede dispersar el rayo láser, reduciendo su intensidad y precisión, y también puede introducir contaminantes en la soldadura.
- Oxidación y Corrosión: Los materiales susceptibles a la oxidación y la corrosión se ven afectados por la alta humedad. La presencia de humedad puede acelerar estos procesos, provocando contaminación de la superficie y defectos de soldadura.
- Comportamiento del material: Algunos materiales, especialmente aquellos que son sensibles a la humedad, pueden presentar cambios en sus propiedades debido a la humedad. Esto puede afectar a su soldabilidad y a la calidad de la soldadura final.
- Medidas de control: Usar un deshumidificador y asegurar una ventilación adecuada puede ayudar a controlar los niveles de humedad. Mantener el área de soldadura seca y libre de humedad puede mantener condiciones óptimas de soldadura.
Gas protector
El uso de gas protector puede ayudar a lograr una soldadura láser exitosa al proteger el área de soldadura de los contaminantes atmosféricos y mejorar la calidad de la soldadura.
- Tipos de gases protectores: Los gases protectores comunes utilizados en la soldadura láser incluyen argón, helio, nitrógeno y mezclas de estos gases. La elección del gas de protección depende del material de soldadura y de las características de soldadura requeridas.
- Argón: El argón se utiliza ampliamente debido a su inercia y proporciona una excelente protección contra la oxidación y la contaminación. Es adecuado para soldar una variedad de metales, incluidos acero, aluminio y titanio.
- Helio: el helio puede aumentar la penetración de la soldadura y reducir la porosidad, lo que lo hace ideal para soldaduras profundas y materiales de alta conductividad térmica como el cobre y el aluminio.
- Nitrógeno: El nitrógeno se usa a menudo en combinación con otros gases para mejorar la calidad de la soldadura en algunos materiales, pero debe usarse con precaución debido a su posible reactividad con algunos metales.
- Flujo y cobertura: El flujo y la cobertura del gas protector deben controlarse cuidadosamente para garantizar una protección adecuada del área de soldadura. Un flujo de gas insuficiente puede provocar contaminación y defectos, mientras que un flujo excesivo puede provocar turbulencias y problemas de refrigeración.
- Diseño de la boquilla: El diseño y la ubicación de la boquilla del gas de protección pueden ayudar a lograr una cobertura efectiva del gas. El diseño adecuado de la boquilla garantiza un flujo continuo y uniforme de gas sobre el área de soldadura, lo que mejora la calidad y la eficiencia de la soldadura.
Ventilación
La ventilación adecuada del área de soldadura ayuda a mantener un entorno de soldadura seguro y eficiente.
- Extracción de humos: la soldadura láser produce humos y gases que son perjudiciales para el operador y pueden afectar el proceso de soldadura. Un sistema eficaz de extracción de humos elimina estos contaminantes del área de trabajo, garantizando un ambiente limpio y seguro.
- Control del flujo de aire: El flujo de aire controlado ayuda a mantener un entorno de soldadura estable al evitar la acumulación de humos y mantener una cobertura de gas constante en el área de soldadura. El flujo de aire no controlado o la turbulencia pueden alterar el gas de protección y afectar la calidad de la soldadura.
- Gestión del calor: la ventilación ayuda a gestionar el calor generado durante el proceso de soldadura. Un flujo de aire adecuado evita el sobrecalentamiento de materiales y equipos, lo que reduce el riesgo de distorsión térmica y fallas del equipo.
- Calidad del aire: Mantener una buena calidad del aire en el entorno de soldadura evita la acumulación de polvo y otras partículas que pueden interferir con el rayo láser y el proceso de soldadura. El aire limpio garantiza una calidad constante del haz y reduce el riesgo de defectos.
- Medidas de seguridad: Garantizar una ventilación adecuada reduce el riesgo de exposición a humos peligrosos y mejora la seguridad general en el lugar de trabajo. También ayuda a mantener la integridad de la óptica láser y otros componentes sensibles al prevenir la contaminación y la acumulación de partículas.
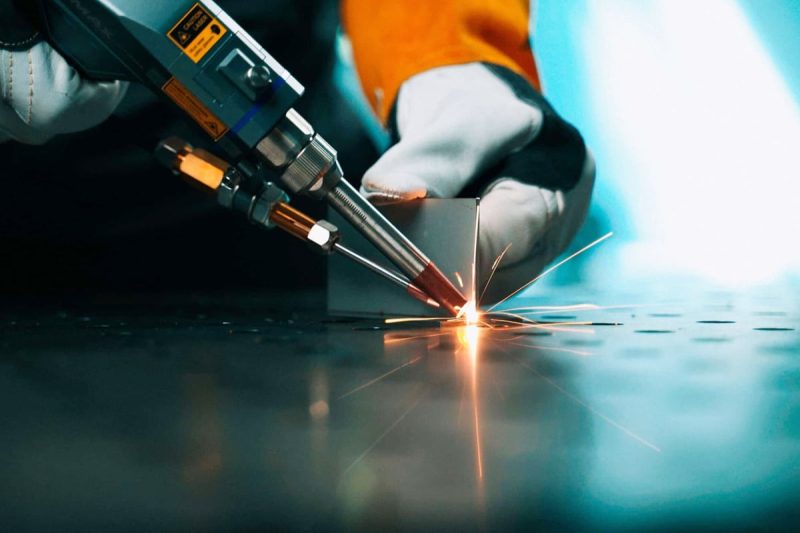
Velocidad de soldadura
Velocidad óptima de soldadura
Lograr la velocidad de soldadura óptima es un delicado equilibrio entre calidad de soldadura y productividad. La velocidad adecuada garantiza que los materiales estén completamente fusionados sin causar defectos.
- Fusión completa: a la velocidad de soldadura óptima, el láser proporciona suficiente energía para derretir y fusionar completamente los materiales. Esto produce una soldadura fuerte, libre de defectos y con buenas propiedades mecánicas.
- Calidad constante: Las velocidades de soldadura constantes garantizan una entrada de calor uniforme a lo largo de la soldadura, lo que da como resultado una calidad de soldadura constante. Las variaciones de velocidad pueden causar irregularidades que afectan la resistencia y apariencia de la soldadura.
Efectos de las altas velocidades de soldadura
Las altas velocidades de soldadura pueden mejorar la productividad, pero conllevan desafíos específicos y posibles inconvenientes.
- Mayor productividad: velocidades de soldadura más altas reducen el tiempo del ciclo, lo que permite completar más soldaduras en un tiempo determinado. Esto es particularmente beneficioso en entornos de fabricación de gran volumen.
- Posibles defectos: Soldar a una velocidad demasiado rápida puede provocar una entrada de calor insuficiente, lo que puede provocar una fusión incompleta, soldaduras débiles y posibles grietas. Es posible que el movimiento rápido no dé tiempo suficiente para que los materiales se derritan y se adhieran adecuadamente.
- Irregularidades de la superficie: a velocidades muy altas, es posible que el charco fundido no tenga tiempo suficiente para asentarse, lo que genera irregularidades en la superficie, como ondulaciones y salpicaduras.
Efectos de las bajas velocidades de soldadura
Si bien velocidades de soldadura más lentas pueden mejorar la calidad de la soldadura, existen ciertas limitaciones y consideraciones.
- Penetración mejorada: Las velocidades de soldadura más lentas aumentan la entrada de calor por unidad de longitud de soldadura, lo que mejora la penetración y garantiza la fusión completa de materiales más gruesos.
- Aumento de la zona afectada por el calor (HAZ): velocidades más lentas dan como resultado un aporte excesivo de calor, lo que resulta en una HAZ más grande. Esto puede causar distorsión térmica, propiedades mecánicas reducidas y posible deformación del componente soldado.
- Productividad reducida: Las velocidades de soldadura más lentas reducen la productividad y aumentan el tiempo total requerido para completar una tarea de soldadura. En un entorno de producción de gran volumen, esto puede suponer una desventaja importante.
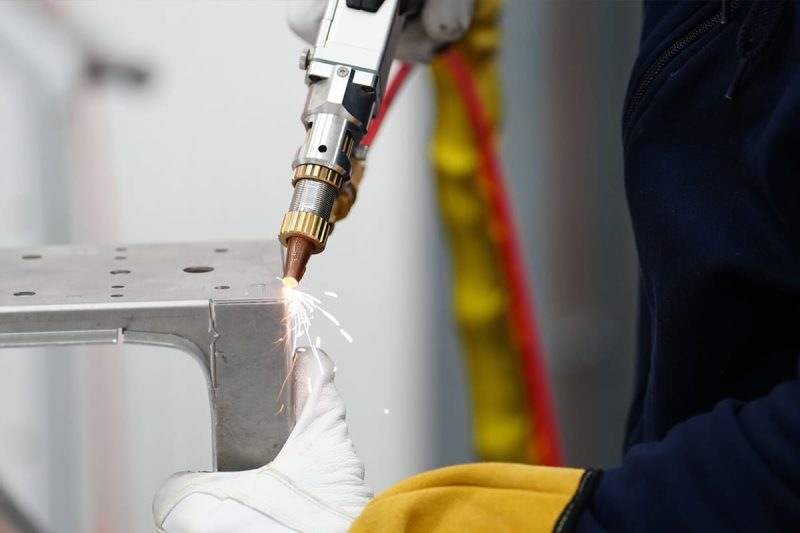
Habilidades y experiencia del operador
Importancia de las habilidades y experiencia del operador
La competencia del operador es fundamental por varias razones, incluida la configuración adecuada del equipo de soldadura, ajustes precisos de los parámetros y la capacidad de identificar y resolver rápidamente los problemas que puedan surgir durante el proceso de soldadura.
- Configuración y calibración: los operadores calificados son expertos en configurar y calibrar equipos de soldadura láser. Esto incluye alinear el láser, ajustar el enfoque, configurar la potencia del láser adecuada y configurar el flujo de gas protector. La configuración adecuada garantiza que el proceso de soldadura comience con la base adecuada, minimizando el riesgo de defectos e ineficiencias.
- Ajuste de parámetros: los operadores experimentados tienen un profundo conocimiento de la relación entre los parámetros de soldadura y la calidad de la soldadura. Pueden realizar ajustes precisos a parámetros como la velocidad de soldadura, la potencia del láser y la frecuencia del pulso para optimizar el proceso de soldadura para diferentes materiales y configuraciones de juntas.
- Solución de problemas y resolución de problemas: durante el proceso de soldadura, pueden ocurrir una variedad de problemas, como desalineación, mala penetración o la formación de defectos como porosidad y grietas. Los operadores capacitados pueden diagnosticar rápidamente estos problemas e implementar acciones correctivas, asegurando un tiempo de inactividad mínimo y una calidad de soldadura constante.
- Adaptabilidad del proceso: diferentes materiales, configuraciones de juntas y tareas de soldadura requieren ajustes específicos. Los operadores experimentados pueden ajustar los parámetros del proceso para adaptarse a diferentes condiciones, garantizando una calidad de soldadura constante en todas las aplicaciones.
Entrenamiento y Certificación
La capacitación y certificación adecuadas ayudan a desarrollar y mantener un alto nivel de habilidades del operador. El programa de formación integral debe cubrir:
- Conocimiento teórico: es fundamental comprender los principios de la soldadura láser, incluida la interacción entre la energía láser y los materiales. Los operadores deben conocer bien la ciencia detrás del proceso para tomar decisiones informadas.
- Experiencia práctica: la capacitación práctica con equipos de soldadura láser permite a los operadores adquirir experiencia en la configuración, calibración y operación de la máquina. La experiencia práctica ayuda a generar confianza y competencia en el mundo real.
- Protocolos de seguridad: La soldadura láser implica peligros potenciales, que incluyen luz intensa, humos y calor. La capacitación debe enfatizar los protocolos de seguridad para proteger a los operadores y garantizar un ambiente de trabajo seguro.
- Programas de Certificación: Los programas de certificación validan las habilidades y conocimientos de los operadores, reconociendo formalmente su experiencia. Los operadores certificados generalmente son más capaces de manejar tareas de soldadura complejas y solucionar problemas de manera efectiva.
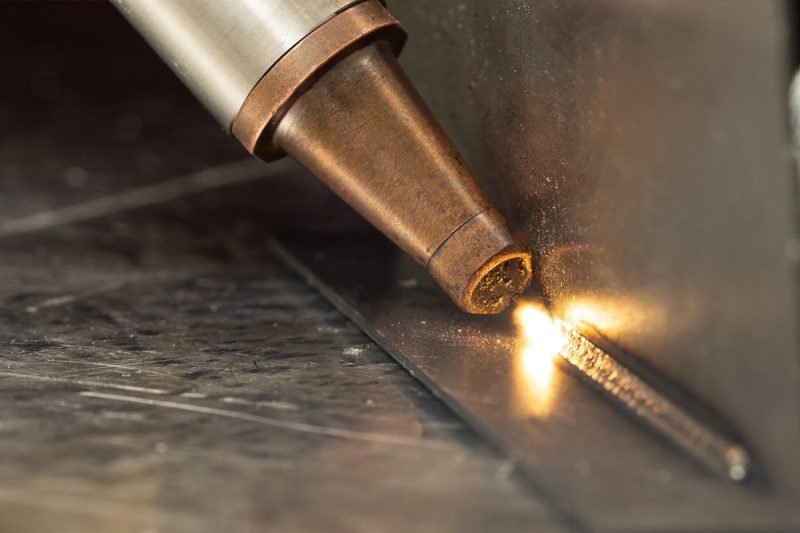
Equipos y Mantenimiento
Fuente láser
La fuente láser es el corazón de un sistema de soldadura láser de fibra, produciendo el haz de alta intensidad necesario para soldar.
- Láseres de fibra: conocidos por su alta eficiencia, excelente calidad de haz y robustez, los láseres de fibra son ideales para soldar una amplia gama de materiales, incluidos metales reflectantes como el aluminio y el cobre.
- Mantenimiento: supervise periódicamente la salida de energía para garantizar un rendimiento constante, limpie la óptica para evitar la contaminación y verifique la alineación para mantener la precisión del haz.
Óptica
La óptica dirige y enfoca el rayo láser hacia el área de soldadura, asegurando una entrega precisa de energía.
- Sistema de entrega de haz: Incluye fibra óptica y colimador para entregar el rayo láser con pérdidas mínimas.
- Óptica de enfoque: lentes o cabezales de enfoque que concentran el rayo láser en un tamaño de punto pequeño, aumentando así la densidad de energía.
- Mantenimiento: La limpieza periódica de lentes, espejos y ventanas protectoras, la inspección de daños y las comprobaciones de alineación pueden ayudar a mantener una calidad óptima del haz.
Sistema de movimiento
El sistema de movimiento controla el movimiento del rayo láser y la pieza de trabajo, asegurando un posicionamiento preciso y un funcionamiento suave.
- Tipos: sistemas cartesianos para movimiento lineal de tres ejes, brazos robóticos para movimiento multieje y sistemas de pórtico para aplicaciones a gran escala.
- Mantenimiento: la lubricación regular de las piezas móviles, la calibración regular para un movimiento preciso y la verificación del desgaste o la desalineación ayudan a garantizar un funcionamiento confiable.
Sistema de refrigeración
El sistema de enfriamiento evita que la fuente láser y otros componentes clave se sobrecalienten y mantiene un funcionamiento estable.
- Refrigeración por agua: se utiliza a menudo en generadores láser de fibra de alta potencia debido a su buen efecto de disipación de calor.
- Componentes: Las bombas, los intercambiadores de calor y los depósitos de refrigerante son elementos clave del sistema de refrigeración.
- Mantenimiento: verifique periódicamente si hay fugas y obstrucciones, controle la calidad del refrigerante y reemplace los filtros según sea necesario para garantizar una refrigeración eficiente.
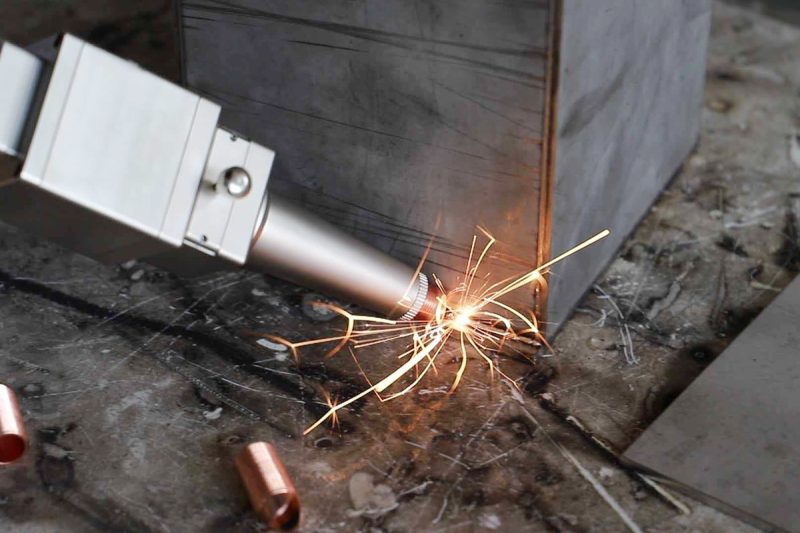
Sistemas de Automatización y Control
Monitoreo en tiempo real
Los sistemas de monitoreo en tiempo real brindan retroalimentación continua sobre el proceso de soldadura, lo que permite realizar ajustes de inmediato para garantizar un rendimiento óptimo.
- Monitoreo de la calidad de la soldadura: sensores y cámaras monitorean el baño de soldadura, detectando defectos como porosidad, grietas y desalineación en tiempo real. Esto permite al operador ajustar la potencia, la velocidad y el enfoque del láser en tiempo real.
- Monitoreo de potencia del láser: el sistema rastrea continuamente la salida de potencia del láser para garantizar que permanezca dentro del rango deseado. Esto ayuda a mantener un suministro de energía y una penetración de la soldadura constantes.
Control adaptativo
Los sistemas de control adaptativos ajustan dinámicamente los parámetros de soldadura basándose en datos en tiempo real para optimizar el proceso en condiciones variables.
- Ajuste de parámetros: estos sistemas ajustan automáticamente la potencia del láser, la velocidad de soldadura y la posición de enfoque en función de los cambios en las propiedades del material, el espesor y la configuración de las juntas. Esto garantiza una calidad de soldadura uniforme y consistente en las diferentes partes de la pieza de trabajo.
- Bucles de retroalimentación: la incorporación de bucles de retroalimentación permite que el sistema aprenda de soldaduras anteriores, mejorando la precisión y la eficiencia con el tiempo.
Integración con sistemas robóticos
La integración de la soldadura por láser de fibra con sistemas robóticos mejora la automatización, la flexibilidad y la repetibilidad.
- Movimiento multieje: el brazo robótico proporciona movimiento multieje para soldar con precisión geometrías complejas y áreas de difícil acceso.
- Calidad constante: el robot garantiza una calidad de soldadura constante al controlar con precisión la trayectoria, la velocidad y el ángulo de la soldadura, lo que reduce las variaciones asociadas con la soldadura manual.
- Aumente el rendimiento: la automatización robótica aumenta el rendimiento al permitir el funcionamiento continuo y reducir los tiempos de ciclo, lo que genera importantes ganancias de productividad.
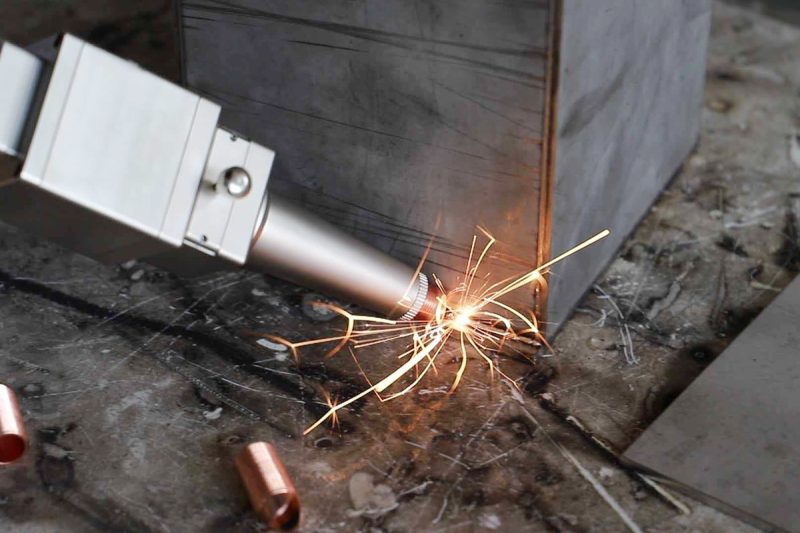
Consideraciones específicas de la aplicación
Combinaciones de materiales
Los diferentes materiales reaccionan de manera única a la soldadura láser y sus combinaciones pueden presentar desafíos específicos.
- Materiales diferentes: soldar materiales diferentes, como aluminio y acero, puede resultar complicado debido a las diferencias en los puntos de fusión, las conductividades térmicas y las tasas de absorción del láser. Los láseres de fibra son eficaces para soldar estas combinaciones, pero requieren un control preciso de los parámetros para gestionar la entrada de calor y evitar defectos.
- Materiales reflectantes: materiales como el cobre y el aluminio reflejan una parte importante de la energía láser, lo que puede reducir la eficiencia de la soldadura. Los láseres de fibra, particularmente con longitudes de onda más cortas, son más adecuados para estos materiales, pero optimizar los parámetros del láser es esencial para garantizar una absorción de energía efectiva.
- Aleaciones y compuestos: cada aleación o material compuesto puede requerir configuraciones específicas para una soldadura óptima. Comprender las propiedades del material y ajustar la potencia, la velocidad y el enfoque del láser en consecuencia es clave para lograr soldaduras de alta calidad.
Geometría de soldadura
La geometría de la junta soldada afecta el proceso de soldadura y debe considerarse cuidadosamente para garantizar la eficiencia.
- Geometrías complejas: soldar geometrías complejas, como formas curvas o intrincadas, requiere un control preciso del rayo láser y del sistema de movimiento. Los láseres de fibra pueden manejar eficazmente estas geometrías cuando se integran con sistemas de movimiento avanzados y brazos robóticos.
- Secciones delgadas versus gruesas: soldar secciones delgadas requiere menor potencia y mayor precisión para evitar quemaduras, mientras que las secciones gruesas requieren mayor potencia y velocidades más bajas para penetrar completamente. Ajustar los parámetros del láser a geometrías específicas puede lograr una soldadura eficiente.
- Preparación de los bordes: La preparación adecuada de los bordes, como el biselado o la limpieza, garantiza un mejor ajuste y fusión. Mantener una calidad constante de los bordes puede ayudar a lograr soldaduras uniformes.
Volumen de producción
El volumen de producción afecta la elección del equipo de soldadura láser y los parámetros del proceso.
- Producción personalizada o en lotes pequeños: Para la producción personalizada o en lotes pequeños, la flexibilidad y la adaptabilidad son clave. La versatilidad de los láseres de fibra permite un ajuste rápido de los parámetros y configuraciones de soldadura, lo que los hace adecuados para una variedad de tareas de soldadura especializadas.
- Producción de gran volumen: la producción de gran volumen requiere coherencia, velocidad y automatización. Los sistemas de láser de fibra integrados con sistemas de control automatizados y brazos robóticos brindan la precisión y repetibilidad requeridas, lo que aumenta significativamente la producción y la eficiencia.
- Optimización del tiempo de ciclo: en un entorno de producción, minimizar el tiempo de ciclo puede mejorar la eficiencia. Los sistemas láser de fibra equipados con monitoreo en tiempo real y control adaptativo pueden reducir el tiempo de configuración y garantizar velocidades de soldadura óptimas, aumentando así la productividad general.
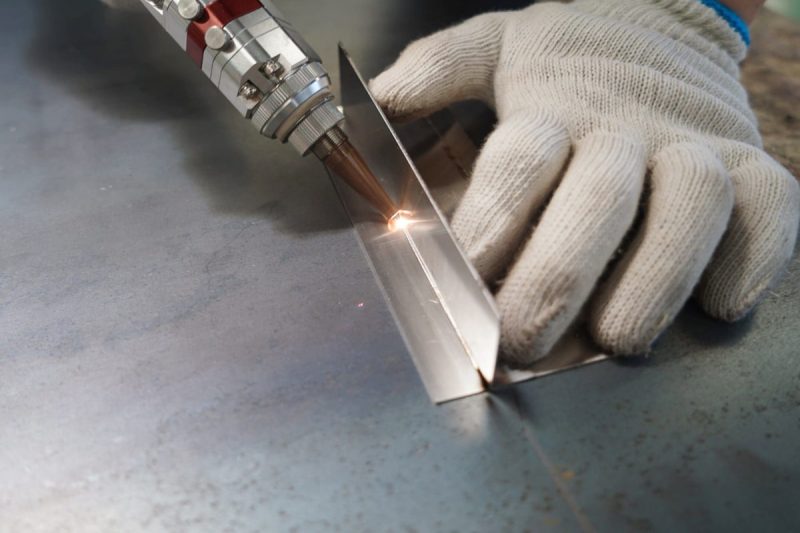
Resumen
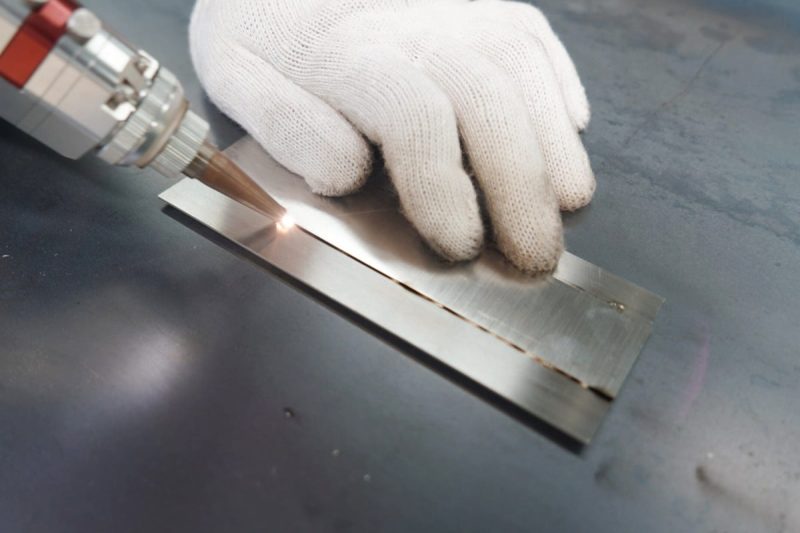
Obtenga soluciones de soldadura láser
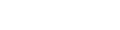
- [email protected]
- [email protected]
- +86-19963414011
- No. 3 Zona A, Zona Industrial de Lunzhen, Ciudad de Yucheng, Provincia de Shandong.