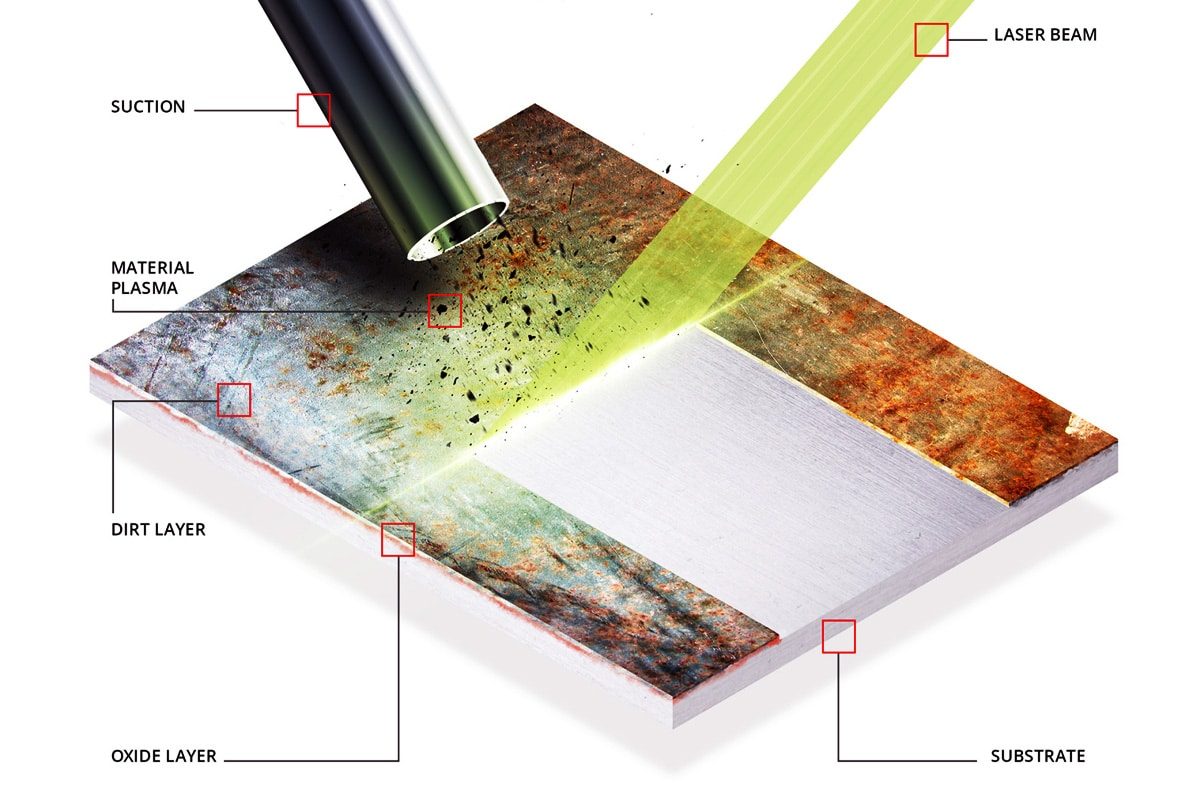
Una guía completa para evaluar superficies después de la limpieza con láser
La tecnología de limpieza láser se ha utilizado ampliamente en diversas industrias gracias a su precisión, selectividad, respeto al medio ambiente y proceso sin contacto. Ya sea en el procesamiento de metales, la fabricación de automóviles, la industria aeroespacial o la restauración de reliquias culturales, máquinas de limpieza láser Puede eliminar contaminantes sin dañar el sustrato. Sin embargo, no basta con completar la limpieza. La evaluación de la limpieza de la superficie es crucial. Esto no solo afecta la calidad del producto final, sino que también implica cumplimiento normativo y rendimiento a largo plazo.
Tabla de contenido
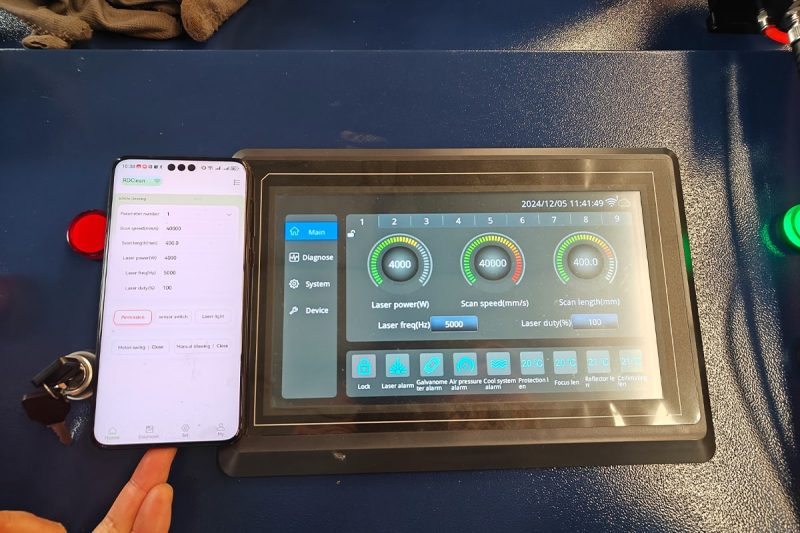
Aprenda sobre la limpieza láser
La limpieza láser es una tecnología de tratamiento de superficies eficiente, precisa y respetuosa con el medio ambiente, ampliamente utilizada en aplicaciones industriales como la eliminación de óxido metálico, la eliminación de capas de óxido, el decapado de recubrimientos y el pretratamiento de soldaduras, entre otras. En comparación con la limpieza química tradicional o el pulido mecánico, la limpieza láser puede eliminar contaminantes sin dañar el sustrato, mejorando así la estabilidad del proceso y la calidad del producto. A continuación, se presentan las cuatro ventajas principales de la limpieza láser.
Precisión: La limpieza láser utiliza un haz láser de alta energía que se enfoca en la superficie del material, actuando únicamente en la zona contaminada, logrando una limpieza precisa a nivel micrométrico. Este control preciso permite eliminar eficazmente la suciedad, el óxido o el recubrimiento, y evitar el desgaste, la deformación o la corrosión química del material que pueden causar los métodos de limpieza tradicionales. La precisión de la limpieza láser es especialmente crucial en industrias como la aeroespacial, la electrónica de precisión y la fabricación de moldes, que exigen una calidad superficial extremadamente alta.
Selectividad: A diferencia de la limpieza con solventes químicos o chorro de arena, la limpieza láser permite ajustar con precisión los parámetros según los diferentes materiales, tipos de contaminantes y requisitos de la aplicación para lograr una limpieza altamente selectiva. Por ejemplo, en el proceso de eliminación de recubrimientos, el láser solo puede eliminar el recubrimiento superficial sin afectar el sustrato; en el campo de la restauración de reliquias culturales, el láser puede eliminar contaminantes a la vez que protege el material original de la reliquia. Esta selectividad mejora considerablemente la controlabilidad del proceso de limpieza y reduce pérdidas innecesarias.
Protección del medio ambiente: Los métodos de limpieza tradicionales suelen utilizar disolventes químicos o materiales abrasivos, que pueden producir líquidos residuales nocivos, gases tóxicos o contaminación por polvo, lo que supone una amenaza para el medio ambiente y la salud de los operarios. La limpieza láser es un proceso puramente físico que utiliza únicamente la energía láser para vaporizar o descomponer los contaminantes. No requiere el uso de reactivos químicos ni produce contaminación secundaria. Cumple plenamente con los requisitos de la industria moderna en materia de protección del medio ambiente y desarrollo sostenible. Por lo tanto, la limpieza láser se ha utilizado ampliamente en industrias con estrictos requisitos de limpieza y protección del medio ambiente, como la fabricación de automóviles, equipos médicos y equipos de procesamiento de alimentos.
Proceso sin contacto: Otra característica destacada de la limpieza láser es su funcionamiento sin contacto, lo que significa que no se requiere contacto directo con el sustrato durante el proceso, evitando así el desgaste del material causado por fricción, presión o daños mecánicos. Esta ventaja es especialmente adecuada para la limpieza de equipos de precisión, componentes microelectrónicos o materiales frágiles, como chips semiconductores, moldes de precisión, etc. Además, la limpieza sin contacto también permite la integración automatizada y puede combinarse con robots, sistemas CNC o líneas de montaje para lograr procesos de limpieza industrial eficientes y estables.
La limpieza láser se está convirtiendo en una de las tecnologías más populares en el campo de la limpieza industrial moderna gracias a su precisión, selectividad, respeto al medio ambiente y proceso sin contacto. En comparación con los métodos de limpieza tradicionales, la limpieza láser no solo mejora la calidad de la limpieza, sino que también reduce la contaminación ambiental y los costes de mantenimiento, y es adecuada para diversas aplicaciones complejas. Con el continuo avance tecnológico, la limpieza láser aprovechará sus ventajas en más industrias y ofrecerá a las empresas soluciones de limpieza más eficientes y sostenibles.
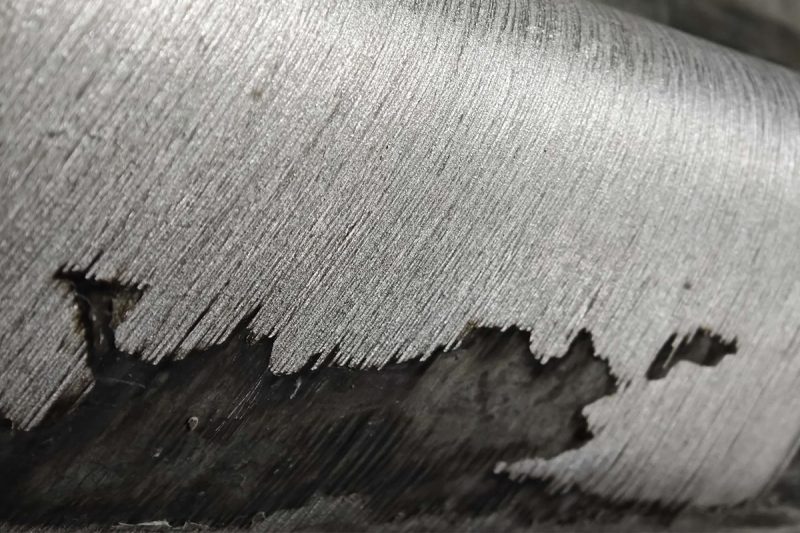
Comprensión de la evaluación de la limpieza
Como tecnología eficiente para el tratamiento de superficies, la limpieza láser se utiliza ampliamente en diversos campos, como la fabricación de metales, la industria electrónica, la restauración de automóviles, la industria aeroespacial y la restauración de reliquias culturales. Sin embargo, la medición del efecto de limpieza no se basa únicamente en la observación visual, sino que también requiere una evaluación sistemática de la limpieza. Este proceso implica múltiples aspectos, como la identificación de contaminantes, la sensibilidad de la superficie, el cumplimiento normativo y la verificación del rendimiento, para garantizar que la superficie limpia cumpla con los estándares de la industria y los requisitos de la aplicación.
Identificación de contaminantes: En la evaluación de la limpieza, el primer paso es identificar con precisión el tipo y la distribución de los contaminantes. Los contaminantes presentes en la superficie de diferentes materiales pueden incluir capas de óxido, herrumbre, grasa, residuos de recubrimiento, polvo, residuos químicos, etc., y cada contaminante se adapta de forma diferente al proceso de limpieza.
- Los contaminantes orgánicos (como aceite, resina y lubricante) generalmente requieren vaporización con láser de pulso corto de alta energía para eliminarlos.
- Los contaminantes inorgánicos (como óxidos, óxido y residuos metálicos) dependen de la evaporación a alta temperatura de los láseres.
- La contaminación por partículas (como polvo y partículas finas) puede requerir adsorción al vacío o asistencia del flujo de aire para evitar la contaminación secundaria.
La identificación precisa de contaminantes no solo puede optimizar los parámetros de limpieza, sino que también garantiza la precisión de la evaluación de la limpieza para evitar residuos después de la limpieza que afecten la calidad del producto.
Sensibilidad de la superficie: Cada material tiene distinta sensibilidad al proceso de limpieza. La limpieza láser requiere ajustar parámetros como la potencia, la longitud de onda y la velocidad de escaneo según las características del material para garantizar la eliminación eficaz de contaminantes sin dañar el sustrato.
- Los materiales altamente reflectantes (como el aluminio y el cobre) tienen tasas de absorción láser bajas y requieren el uso de generadores láser con longitudes de onda específicas o mayor energía de pulso.
- Los materiales frágiles (como la cerámica y el vidrio) pueden agrietarse debido al choque térmico y requieren el uso de láseres de pulso corto y baja potencia para reducir la zona afectada por el calor.
- Los componentes de precisión (como semiconductores y circuitos electrónicos) requieren estándares de limpieza extremadamente altos, evitando al mismo tiempo daños causados por el láser en circuitos sensibles o capas aislantes.
Una parte importante de la evaluación de la limpieza es confirmar si la superficie del material, después de la limpieza, conserva sus propiedades físicas y químicas originales. Por ejemplo, la superficie metálica no debe presentar microfisuras ni rugosidad excesiva después de la limpieza, ya que esto podría afectar el recubrimiento, la soldadura o el ensamblaje posteriores.
Cumplimiento normativo: Diferentes industrias tienen estándares y regulaciones estrictas para la limpieza de superficies. La evaluación de la limpieza debe cumplir con las especificaciones pertinentes de la industria y los sistemas de gestión de calidad para garantizar que el producto supere la inspección de calidad sin problemas.
- Aeroespacial: Según lo especificado por la NASA y la FAA, no deben quedar contaminantes que puedan afectar la unión o la corrosión en la superficie de los componentes de la nave espacial.
- Automotriz: La norma ISO 16232 (VDA 19) especifica métodos de prueba de limpieza para piezas de automóviles para garantizar que los componentes clave, como motores y sistemas de combustible, estén libres de contaminantes.
- Dispositivos médicos: La norma ISO 13485 estipula que los dispositivos médicos deben cumplir estrictos estándares de limpieza para evitar cualquier contaminante que pueda afectar la seguridad del paciente.
- Industria electrónica: Las normas IPC exigen que la superficie de las placas de circuitos alcance un nivel de limpieza extremadamente alto antes de soldar para evitar cortocircuitos o soldaduras deficientes.
Durante el proceso de evaluación de la limpieza, las empresas deben realizar pruebas basadas en estándares relevantes y registrar los resultados de la limpieza para cumplir con los requisitos de cumplimiento y mejorar la competitividad de mercado de sus productos.
Verificación del rendimiento: La limpieza láser no solo debe eliminar contaminantes, sino también garantizar que la superficie limpia cumpla con los requisitos de los procesos posteriores o su uso final. Por lo tanto, la verificación del rendimiento es un elemento clave en la evaluación de la limpieza, e incluye los siguientes aspectos:
- Prueba de integridad de la superficie: asegúrese de que no haya daños microscópicos en el material después de la limpieza, como grietas microscópicas, cambios en la rugosidad de la superficie, etc.
- Prueba de adhesión: si después de la limpieza es necesario recubrir, pintar o soldar la superficie, se debe probar la resistencia de adhesión de la nueva unión para evitar la pérdida de adhesión debido a la contaminación de la superficie.
- Evaluación de la resistencia a la corrosión: algunos materiales metálicos pueden enfrentar riesgos de oxidación o corrosión después de la limpieza, y se requiere una evaluación de la resistencia a la corrosión, como la prueba de niebla salina.
- Análisis microscópico óptico: utilice un microscopio, un microscopio electrónico de barrido (SEM) o una espectroscopia de rayos X (XPS) para detectar contaminantes microscópicos y garantizar que no queden residuos en la superficie después de la limpieza.
A través de la verificación sistemática del rendimiento, se puede garantizar la confiabilidad de la tecnología de limpieza láser en diferentes escenarios de aplicación para cumplir con los requisitos de calidad de los clientes.
La evaluación de la limpieza es fundamental para garantizar la calidad de la limpieza láser y abarca cuatro aspectos clave: identificación de contaminantes, sensibilidad de la superficie, cumplimiento normativo y verificación del rendimiento. Mediante la identificación precisa de contaminantes, la optimización de los parámetros de limpieza para diferentes materiales, el cumplimiento de los estándares de la industria y una rigurosa verificación del rendimiento, las empresas pueden garantizar que el efecto de limpieza satisfaga las necesidades de las aplicaciones industriales. Con el continuo avance de la tecnología de limpieza, la limpieza láser se convertirá en la solución preferida para el tratamiento de superficies en cada vez más industrias, ofreciendo soluciones de limpieza más eficientes y respetuosas con el medio ambiente para la fabricación de alta gama.
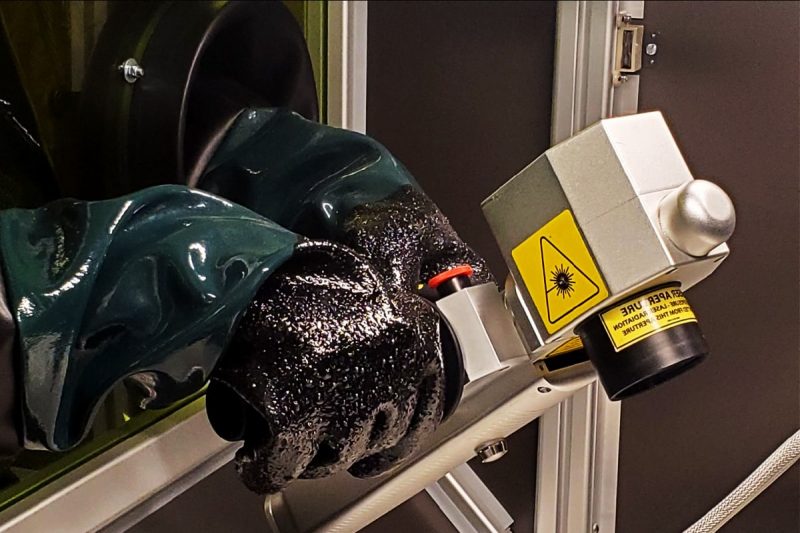
Importancia de evaluar la limpieza después de la limpieza láser
En aplicaciones industriales, es fundamental evaluar la limpieza tras la limpieza láser. Esto no solo determina la calidad del producto, sino que también afecta la fiabilidad de los procesos posteriores. Los cuatro valores fundamentales de la evaluación de la limpieza son los siguientes:
- Cumplimiento de las normas de la industria: Diversas industrias (como la aeronáutica, la automotriz, la electrónica y la médica) tienen requisitos estrictos de limpieza de superficies. Garantizar el cumplimiento de las normas ISO, VDA, IPC y otras normas ayudará a que los productos superen la certificación de calidad sin problemas y a mejorar su competitividad en el mercado.
- Rendimiento y fiabilidad óptimos: Si persisten contaminantes en la superficie después de la limpieza, esto podría afectar el efecto de la soldadura, el recubrimiento o la unión posteriores. Evalúe con precisión la limpieza para garantizar que las piezas mantengan un rendimiento óptimo durante el uso prolongado y reducir el riesgo de fallos.
- Garantía de calidad: La limpieza está directamente relacionada con la consistencia y durabilidad del producto. Los métodos de evaluación científica pueden reducir los errores de producción, mejorar la calidad general de fabricación y cumplir con los altos estándares de los clientes.
- Rentabilidad: Una evaluación de limpieza eficaz puede evitar limpiezas repetidas o reprocesos, desechos y costos de reparación causados por contaminación, al tiempo que reduce el tiempo de inactividad, mejora la eficiencia de la producción y, por lo tanto, reduce los costos operativos generales.
La evaluación de la limpieza no solo es una parte del control de calidad, sino también un vínculo importante para garantizar la estabilidad de la producción, optimizar el flujo del proceso y mejorar los beneficios económicos.

Tecnología de evaluación para la evaluación de la limpieza
Para garantizar que la superficie alcance el estado óptimo tras la limpieza láser, se requieren diversas técnicas de evaluación para detectar la limpieza. Los métodos comunes incluyen:
- Inspección visual: utilice el ojo desnudo o una lupa para realizar una inspección preliminar para determinar rápidamente si hay contaminantes o defectos obvios en la superficie.
- Análisis del perfil de la superficie: utilice un medidor de rugosidad para detectar cambios en la microestructura de la superficie para garantizar que el procesamiento o recubrimiento posterior no se vea afectado después de la limpieza.
- Análisis de superficies: utilice espectroscopia de rayos X (XPS) o espectroscopia de energía dispersiva (EDS) para analizar la composición de la superficie y detectar si hay óxidos residuales o contaminantes orgánicos.
- Análisis químico: utilice titulación, detección de fluorescencia o cromatografía de gases (GC-MS) para analizar residuos químicos de la superficie y garantizar el cumplimiento de los estándares de limpieza de la industria.
- Microscopio óptico: amplía y observa contaminantes a nivel micrométrico, especialmente adecuado para campos de fabricación de precisión, como electrónica y dispositivos médicos.
- Prueba de adhesión: Evalúe la fuerza de adhesión de recubrimientos de superficies, soldaduras o uniones mediante pruebas de arranque o desprendimiento de cinta para garantizar la calidad de los procesos posteriores.
La combinación de múltiples técnicas de evaluación puede evaluar con mayor precisión los resultados de la limpieza y garantizar que la limpieza láser cumpla con los estándares de la industria y los requisitos de la aplicación.
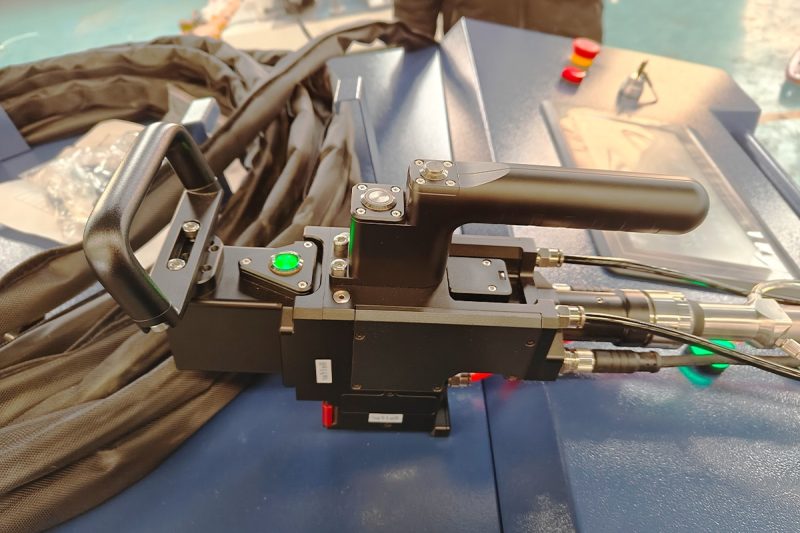
Mejores prácticas para la evaluación de la limpieza
Para garantizar una calidad de superficie consistente y confiable después de la limpieza con láser, las empresas deben seguir una serie de mejores prácticas para mejorar la precisión y la consistencia de las evaluaciones.
- Establecer estándares claros: desarrollar estándares de limpieza basados en las especificaciones de la industria (como ISO, VDA, IPC, etc.) para garantizar que todos los productos cumplan con los requisitos de calidad y sean adecuados para diferentes escenarios de aplicación.
- Utilice múltiples tecnologías: Un solo método de detección puede tener limitaciones. La combinación de diversas tecnologías, como la inspección visual, el análisis de superficies, las pruebas químicas, la observación microscópica y las pruebas de adhesión, permite obtener resultados de evaluación más completos.
- Calibrar los instrumentos: calibre periódicamente el equipo de prueba para garantizar la precisión de los datos de medición y evitar errores de evaluación causados por desviación del equipo.
- Procedimientos estandarizados: establecer un proceso unificado de detección de limpieza para garantizar que todos los operadores sigan los mismos pasos, reducir los errores humanos y mejorar la comparabilidad de los datos.
- Capacitar al personal: Brindar capacitación profesional periódica al personal de pruebas para mejorar su capacidad de identificar contaminantes, métodos de prueba e interpretación de datos, y garantizar la confiabilidad de los resultados de la evaluación.
- Registrar resultados: Registre los datos de cada evaluación de limpieza en detalle, incluido el tipo de contaminante, el método de prueba, los parámetros del equipo y los resultados finales, para rastrear y analizar, optimizar el proceso de limpieza y cumplir con los requisitos de gestión de calidad.
Mediante estas mejores prácticas, las empresas pueden mejorar la precisión y la consistencia de las evaluaciones de limpieza y garantizar la confiabilidad de los procesos de limpieza láser, mejorando así la calidad del producto y la competitividad del mercado.
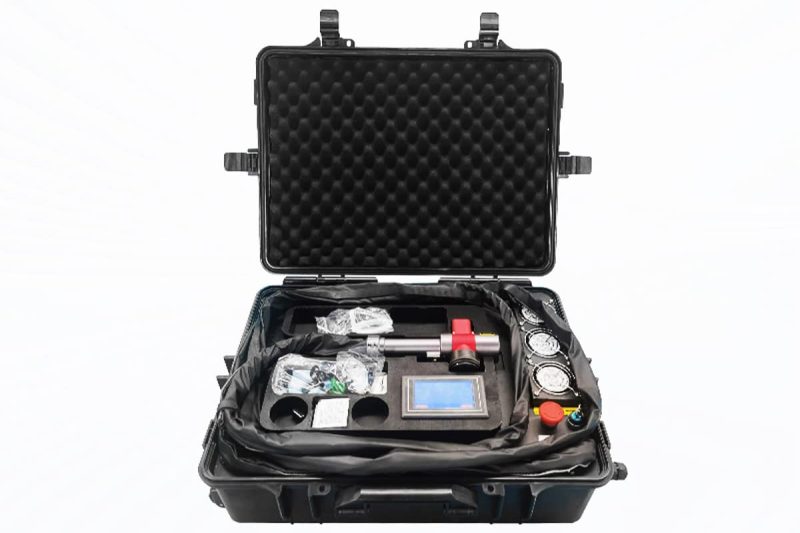
Resumir
La limpieza láser no solo consiste en eliminar contaminantes superficiales, sino que también es un componente importante para mejorar la calidad de fabricación y optimizar el flujo del proceso. Una superficie completamente limpia y normalizada garantiza el correcto desarrollo de los procesos posteriores de recubrimiento, soldadura, unión y otros, y evita defectos en el producto causados por contaminantes residuales. Mediante una evaluación precisa de la limpieza, las empresas pueden cuantificar el efecto de la limpieza láser y garantizar que cada pieza cumpla con los estándares de la industria, mejorando así la estabilidad y la vida útil del producto. Además, una gestión rigurosa de la limpieza ayuda a reducir las tasas de reprocesamiento y desperdicio, optimizar los costos de producción y mejorar la eficiencia general de la fabricación.
En un mercado altamente competitivo, el uso de tecnología de evaluación científica, procesos estandarizados y métodos de prueba eficientes no solo puede mejorar la calidad del producto, sino también fortalecer la reputación de la empresa en el mercado y la confianza de los clientes. Por lo tanto, la evaluación de la limpieza después de la limpieza láser no solo es un paso clave en el control de calidad, sino también una garantía importante para lograr la optimización de la fabricación a largo plazo y el liderazgo en la industria.
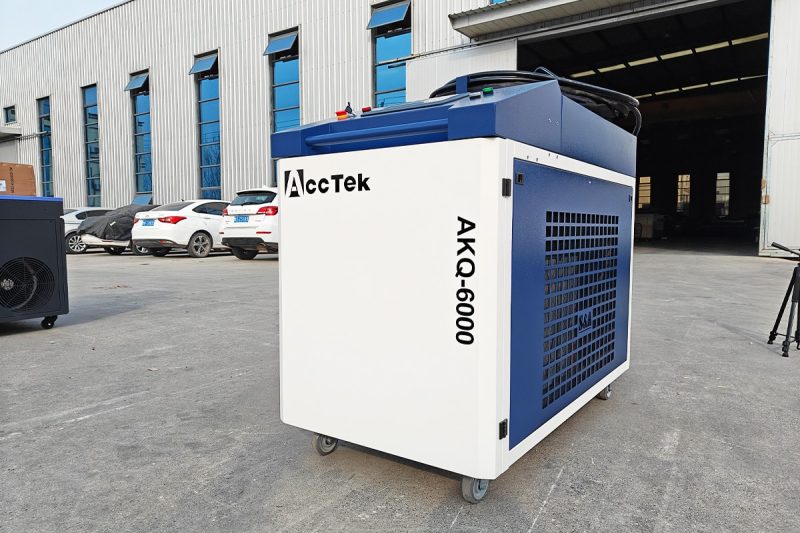
Obtenga soluciones láser
Láser AccTek se especializa en proporcionar máquinas de limpieza láser eficientes, precisas y seguras, que se utilizan ampliamente en muchos campos, como la fabricación de automóviles, la industria aeroespacial, la industria electrónica, el procesamiento de metales, la restauración de reliquias culturales, etc. Nuestra tecnología de limpieza láser puede eliminar eficazmente contaminantes de la superficie como capas de óxido, manchas de aceite, recubrimientos, óxido, etc., lo que garantiza un procesamiento de alta calidad de las piezas a la vez que es respetuoso con el medio ambiente y tiene un bajo costo de mantenimiento.
Si busca una solución confiable de limpieza láser, nuestro equipo de profesionales puede brindarle soluciones personalizadas según sus necesidades específicas para garantizar que el equipo se adapte perfectamente a su proceso de producción, mejore la eficiencia del trabajo y reduzca los costos operativos. Ya sea para aplicaciones industriales a gran escala o para la limpieza de piezas de precisión, AccTek Laser le ofrece soporte técnico avanzado y un servicio posventa excepcional.
Bienvenido a Contáctenos Para consultas profesionales, demostraciones de productos y soluciones técnicas detalladas, ¡deje que la tecnología de limpieza láser ayude a su empresa a avanzar hacia estándares de producción más elevados!
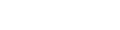
Información del contacto
- [email protected]
- [email protected]
- +86-19963414011
- No. 3 Zona A, Zona Industrial de Lunzhen, Ciudad de Yucheng, Provincia de Shandong.
Obtenga soluciones láser