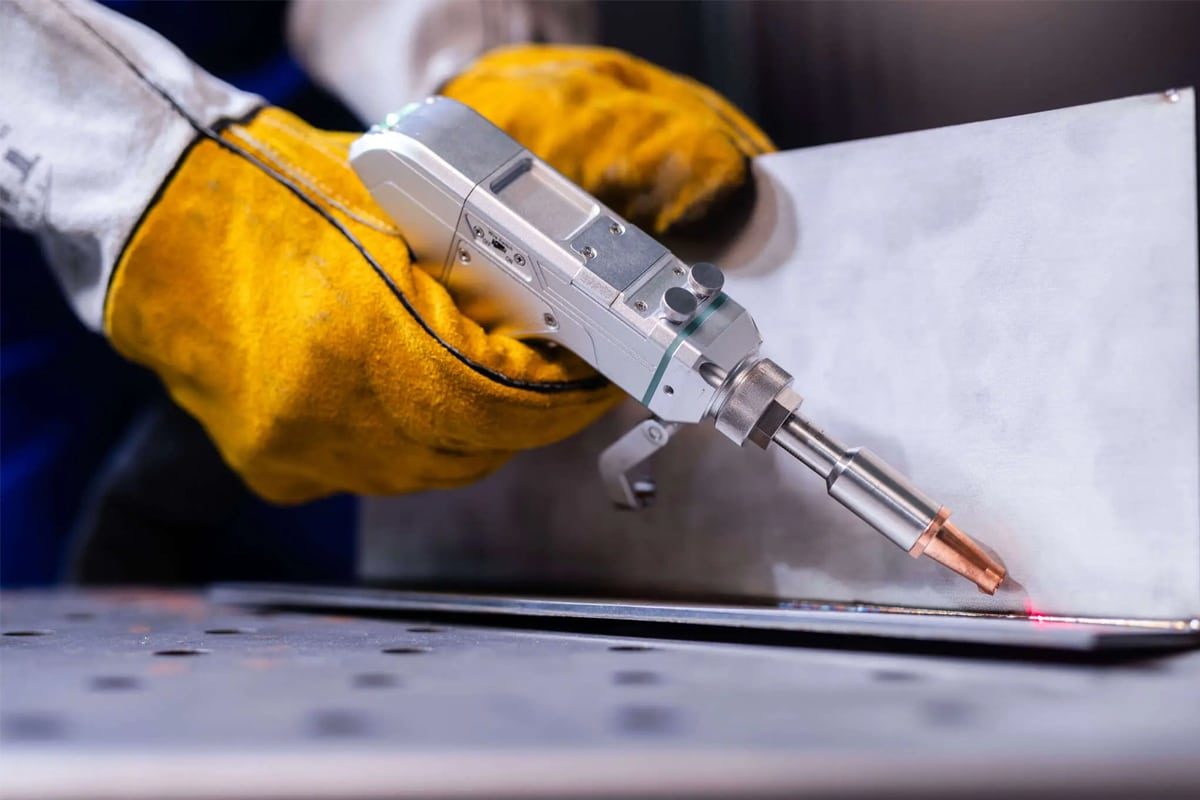
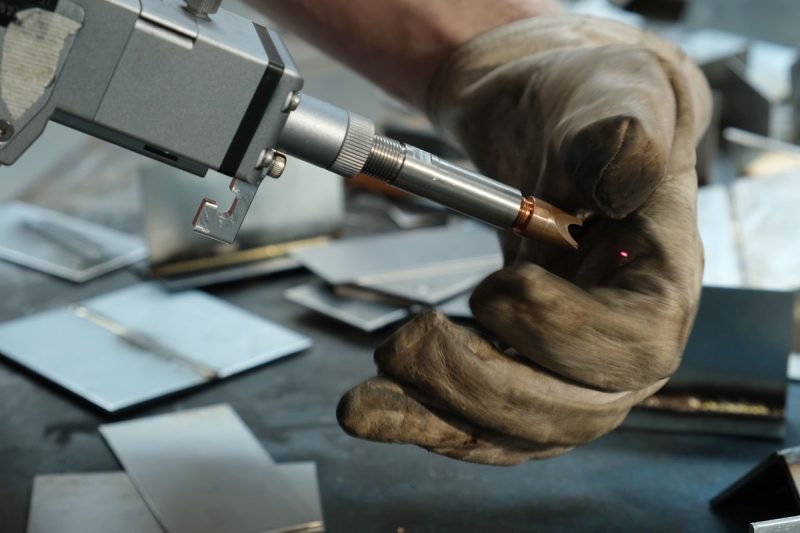
Cómo funciona la soldadura láser
Principios de la soldadura por láser
La soldadura láser funciona enfocando una luz láser de alta energía en una pequeña área del material. Esta energía concentrada calienta el material rápidamente, lo que hace que se derrita y se fusione. A diferencia de la soldadura tradicional, que a menudo se basa en zonas de calor más amplias, la soldadura láser se centra en crear zonas mínimas afectadas por el calor, lo que reduce la distorsión y proporciona uniones más limpias y de alta calidad. La fusión se produce en uno de dos modos principales: modo de conducción o modo de ojo de cerradura.
- Potencia y enfoque del láser: la densidad de potencia del láser y el tamaño del punto determinan la profundidad y el ancho de la soldadura. Las densidades de potencia más altas producen soldaduras más profundas, mientras que los ajustes de potencia más bajos se utilizan para soldaduras más finas y superficiales.
- Control de calor: La soldadura láser permite un control preciso sobre el aporte de calor, esencial para unir materiales sensibles al calor o piezas complejas.
Tipos de modos de soldadura láser
Soldadura por conducción
Características:
- Penetración de soldadura poco profunda, normalmente menos de 2 mm.
- Soldaduras lisas y anchas con mínima deformación superficial.
- Riesgo mínimo de formación de agujeros de cerradura, lo que reduce la probabilidad de porosidad o huecos.
Aplicaciones:
- Se utiliza comúnmente para materiales delgados y aplicaciones donde la calidad visual es crucial.
- Ideal para aplicaciones en joyería, dispositivos médicos y electrónica donde se requiere un acabado de superficie limpio.
Soldadura en modo ojo de cerradura
Características:
- Penetración de soldadura profunda (hasta varios centímetros) con ancho estrecho.
- Alta relación de aspecto, lo que da como resultado soldaduras fuertes y enfocadas.
- La eficiente absorción de energía debido a múltiples reflexiones dentro del ojo de la cerradura promueve una penetración más profunda de la soldadura.
Aplicaciones:
- Adecuado para aplicaciones de servicio pesado que requieren uniones fuertes y duraderas, como en componentes automotrices y aeroespaciales.
- Eficaz para materiales gruesos y metales de alta resistencia donde se requiere una fusión profunda.
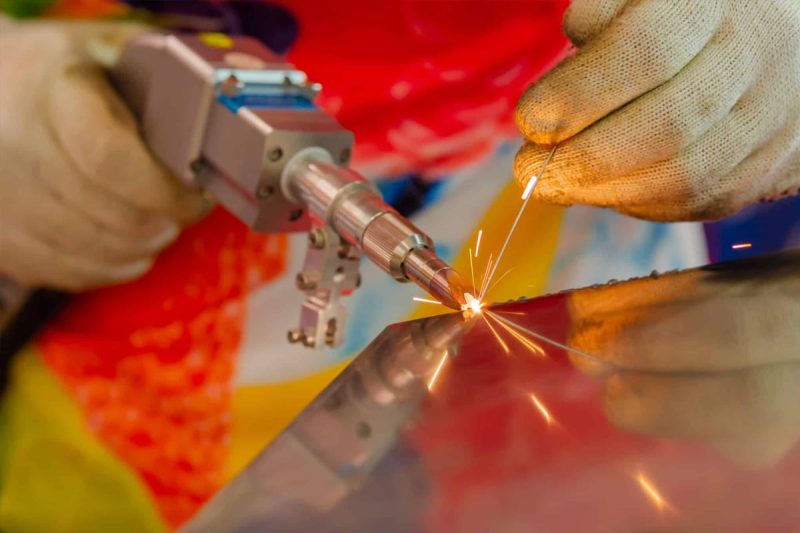
Ventajas de la soldadura láser
Precisión y exactitud
Alta velocidad de soldadura
Proceso sin contacto
Penetración profunda y soldaduras estrechas
Capacidad para soldar materiales difíciles
Distorsión mínima y zonas afectadas por el calor
Soldaduras limpias y estéticas
Bajos costos de mantenimiento y operación
Eficiencia energética
Automatización y flexibilidad
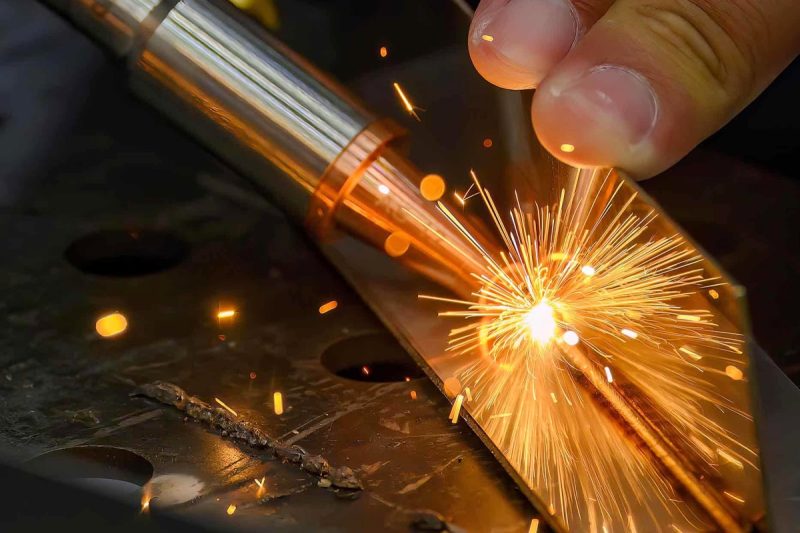
Desventajas de la soldadura láser
Alta inversión inicial
Soldadura de espesor limitado
Sensibilidad al ajuste de las articulaciones
Preocupaciones de seguridad
Problemas de reflectividad
Complejidad técnica
Sensibilidad del equipo
Uso de campo limitado
Requiere operadores capacitados
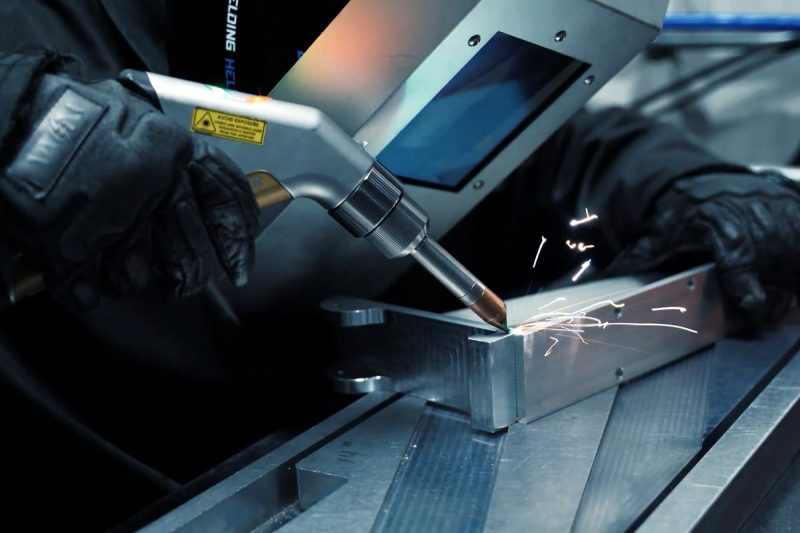
Aplicaciones de la soldadura láser
Industria automotriz
Aplicaciones en automoción:
- Paneles de carrocería y piezas en bruto a medida.
- Componentes del motor, incluidas las piezas de transmisión.
- Las carcasas de los airbags requieren precisión y fiabilidad.
- Los sistemas de escape necesitan soldaduras que puedan soportar altas temperaturas y presiones.
Industria aeroespacial
Aplicaciones en el sector aeroespacial:
- Los sistemas de combustible y las líneas hidráulicas requieren soldaduras a prueba de fugas.
- Componentes estructurales, incluidas piezas del fuselaje y tren de aterrizaje.
- Álabes de turbinas y otras partes del motor, donde la resistencia y la resistencia a la temperatura son fundamentales.
- La electrónica aeroespacial necesita soldaduras precisas y limpias para garantizar la confiabilidad a largo plazo.
Fabricación de dispositivos médicos
Aplicaciones en la fabricación de dispositivos médicos:
- Instrumentos quirúrgicos, donde la resistencia a la corrosión y la limpieza son esenciales.
- Los implantes médicos, como las carcasas de marcapasos y los dispositivos ortopédicos, requieren soldaduras herméticas y biocompatibles.
- Los catéteres y endoscopios necesitan soldaduras finas y precisas en componentes pequeños.
- Carcasas de baterías para dispositivos médicos, donde la integridad de la soldadura es fundamental para el uso a largo plazo.
Industria electrónica
Aplicaciones en Electrónica:
- Las conexiones de placas de circuito proporcionan soldaduras finas y precisas sin dañar los componentes cercanos.
- Las carcasas de los sensores y las conexiones de la batería requieren uniones fuertes y duraderas.
- Cajas para componentes electrónicos sensibles, garantizando la protección frente a factores ambientales.
- Microsoldadura en la fabricación de semiconductores, donde la precisión y la limpieza son cruciales.
Industria de la joyería
Aplicaciones en joyería:
- Reparaciones de joyas existentes, como cambiar el tamaño de anillos o arreglar cadenas rotas.
- Engaste de piedras, que permite realizar soldaduras seguras cerca de piedras preciosas sin daños por calor.
- Trabajos intrincados en metal en diseños de joyería personalizados, donde se requieren soldaduras detalladas y delicadas.
- Creación de diseños de metales mixtos, como unir oro y platino, con costuras de soldadura limpias e invisibles.
Sector Energético
Aplicaciones en Energía:
- Fabricación de baterías, donde la soldadura láser crea conexiones duraderas entre celdas y terminales.
- Las pilas de combustible y los componentes de los paneles solares se benefician de soldaduras limpias y precisas.
- Tuberías de petróleo y gas, donde las soldaduras de alta resistencia son esenciales para la seguridad bajo alta presión.
- Los componentes de las turbinas eólicas, incluidas las piezas estructurales, deben soportar la exposición a la intemperie y a tensiones mecánicas.
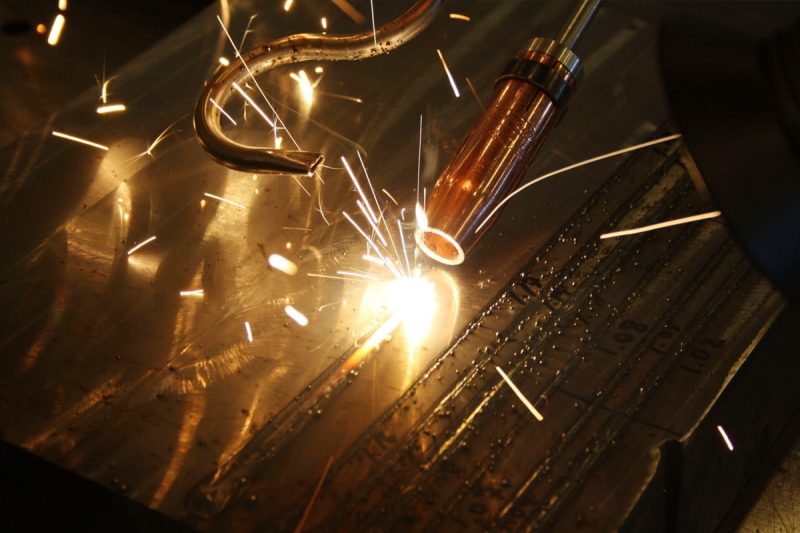
Comparación con los métodos de soldadura tradicionales
Soldadura láser vs. soldadura TIG
- La soldadura con gas inerte de tungsteno (TIG) es conocida por producir soldaduras limpias y de alta calidad en una amplia gama de metales, incluidos el aluminio, el acero inoxidable y el cobre. La soldadura TIG utiliza un electrodo de tungsteno para crear un arco entre el electrodo y la pieza de trabajo, fundiendo el metal y, a menudo, requiriendo un material de relleno.
- Precisión y exactitud: tanto la soldadura láser como la soldadura TIG ofrecen una alta precisión, pero la soldadura láser tiene una ventaja debido a su haz enfocado, que puede crear soldaduras extremadamente estrechas con mínimas zonas afectadas por el calor (ZAT). La soldadura TIG requiere un mayor control manual y es más lenta, lo que la hace menos adecuada para soldaduras pequeñas e intrincadas en componentes sensibles.
- Entrada de calor y distorsión: la entrada de energía concentrada de la soldadura láser crea una ZAT mucho más pequeña en comparación con la soldadura TIG. Esto reduce el riesgo de distorsión térmica, lo que es particularmente importante para materiales delgados y aplicaciones sensibles al calor. La soldadura TIG, aunque controlada, genera más calor distribuido en un área más grande, lo que puede causar deformaciones en materiales más delgados.
- Velocidad: La soldadura láser es significativamente más rápida que la soldadura TIG, lo que la hace más adecuada para producciones de gran volumen. La soldadura TIG, si bien puede producir resultados de alta calidad, es más lenta debido a la operación manual y la precisión requerida, lo que la hace más adecuada para proyectos o reparaciones más pequeños.
- Aplicaciones: La soldadura TIG se utiliza a menudo en proyectos de pequeña escala y precisión, como piezas aeroespaciales y automotrices, pero generalmente tiene limitaciones en cuanto a velocidad y compatibilidad con la automatización. La soldadura láser es ideal para aplicaciones que necesitan velocidad y precisión, como componentes electrónicos, dispositivos médicos y automotrices de gran volumen.
Soldadura láser vs. soldadura MIG
- La soldadura con gas inerte metálico (MIG) es un método de soldadura común que se utiliza para unir materiales más gruesos, especialmente en aplicaciones donde la velocidad y el volumen de producción son prioridades. La soldadura MIG utiliza un electrodo de alambre alimentado de forma continua que se funde para formar una soldadura, lo que a menudo produce un área de soldadura más amplia y requiere un posprocesamiento para eliminar las salpicaduras.
- Penetración y ancho de soldadura: la soldadura láser puede lograr una penetración profunda con un cordón de soldadura estrecho, incluso en materiales gruesos, sin necesidad de material de relleno. La soldadura MIG produce una soldadura más ancha y menos precisa que, a menudo, requiere limpieza y acabado adicionales. Para aplicaciones que requieren soldaduras fuertes y estrechas, la soldadura láser es más adecuada.
- Zona afectada por el calor: la soldadura MIG genera más calor que la soldadura láser, lo que crea una ZAT más grande y aumenta el riesgo de distorsión térmica. El calor concentrado de la soldadura láser reduce la ZAT, preservando las propiedades mecánicas del material circundante y minimizando la distorsión posterior a la soldadura, especialmente en materiales delgados o sensibles al calor.
- Automatización y velocidad de producción: la soldadura láser es muy compatible con la automatización y puede funcionar a velocidades mucho más altas, lo que la hace ideal para entornos de producción de gran volumen. La soldadura MIG, si bien es más rápida que la TIG, generalmente es más adecuada para procesos manuales o semiautomatizados debido a la necesidad de alimentación de alambre y gas protector.
- Materiales: La soldadura MIG es eficaz para materiales más gruesos y metales de uso común, como el acero y el aluminio, pero tiene dificultades con materiales diferentes y muy delgados, donde se requiere precisión y bajo aporte de calor. La soldadura láser se destaca en la unión de metales delgados y diferentes, como el cobre y el acero inoxidable, debido a su control preciso de la energía.
Soldadura por láser frente a soldadura por haz de electrones
- La soldadura por haz de electrones (EB) es un proceso de soldadura de alta energía similar a la soldadura láser en su capacidad de producir soldaduras profundas y precisas. La soldadura EB utiliza un haz de electrones enfocado en el vacío para unir materiales, lo que la hace adecuada para aplicaciones exigentes que requieren una penetración muy profunda y un entorno controlado.
- Entorno y configuración: a diferencia de la soldadura láser, que puede funcionar al aire libre, la soldadura EB requiere una cámara de vacío para mantener el haz de electrones. Esta configuración de vacío hace que la soldadura EB sea más compleja, costosa y menos flexible que la soldadura láser, que se puede utilizar en una gama más amplia de entornos, incluidas salas blancas o líneas de producción semiautomatizadas.
- Profundidad y resistencia de penetración: la soldadura EB puede lograr una penetración más profunda que la soldadura láser, lo que la hace ideal para materiales gruesos o aplicaciones estructurales que requieren soldaduras muy fuertes. Sin embargo, para materiales moderadamente gruesos a delgados, la soldadura láser suele ser más eficiente y más fácil de implementar.
- Velocidad y automatización: la soldadura láser puede alcanzar velocidades más altas y es más fácil de integrar en líneas de producción automatizadas, lo que la hace adecuada para la producción de gran volumen. La soldadura EB, si bien es efectiva, generalmente es más lenta y menos adaptable a entornos de producción automatizados y de ritmo rápido debido a los requisitos de la cámara de vacío.
- Costo y mantenimiento: los sistemas de soldadura por electroerosión son costosos y requieren un mantenimiento especializado, en particular para el sistema de vacío. La soldadura láser requiere menos mantenimiento, lo que la hace más accesible y rentable para la fabricación habitual. Además, el tiempo de configuración y el mantenimiento de la soldadura por electroerosión pueden generar tiempos de inactividad más prolongados en comparación con la soldadura láser.
Comparación
- Soldaduras precisas y limpias: la soldadura láser supera a la soldadura MIG y TIG en precisión y compite con la soldadura EB por resultados limpios y precisos.
- Velocidad: La soldadura láser es más rápida que la soldadura TIG y MIG y generalmente es más adecuada para la producción automatizada de alta velocidad, especialmente donde se requiere precisión.
- Medio ambiente: La flexibilidad de la soldadura láser en entornos basados en aire la hace más versátil que la soldadura EB, que requiere vacío.
- Zona afectada por el calor: la mínima ZAT de la soldadura láser la hace ideal para materiales delgados y sensibles al calor, superando a la soldadura TIG y MIG en este aspecto.
- Costo y complejidad: La soldadura láser tiene un costo inicial elevado pero ofrece menores costos de mantenimiento y operación en comparación con la soldadura EB, que implica equipos y necesidades de mantenimiento más complejos.
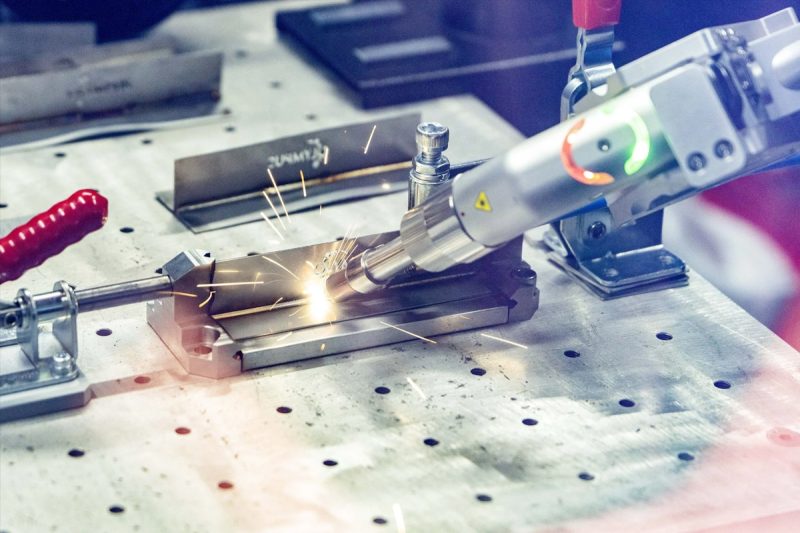
Factores que afectan la calidad de la soldadura láser
Parámetros del láser
Los ajustes y las características del láser desempeñan un papel crucial a la hora de determinar la calidad de la soldadura. Los parámetros clave del láser incluyen la potencia, el tamaño del punto focal, la velocidad de soldadura y la frecuencia de pulso (para láseres pulsados).
- Potencia del láser: una mayor potencia aumenta la profundidad de penetración y permite una soldadura más rápida, pero puede generar un calor excesivo si no se controla adecuadamente. Una potencia excesiva puede provocar salpicaduras o quemaduras, mientras que una potencia insuficiente puede dar lugar a soldaduras débiles o incompletas.
- Velocidad de soldadura: la velocidad a la que se mueve el láser sobre la pieza de trabajo afecta la calidad de la soldadura. Las velocidades de soldadura altas pueden reducir la entrada de calor, lo que minimiza la zona afectada por el calor (ZAT) y reduce la distorsión. Sin embargo, las velocidades demasiado altas pueden impedir la fusión completa de los materiales, lo que da como resultado uniones débiles. Las velocidades más lentas permiten una penetración más profunda, pero pueden aumentar la acumulación de calor, lo que puede causar distorsión térmica.
- Tamaño del punto de enfoque: un punto de enfoque más pequeño concentra la energía en un área diminuta, lo que permite realizar soldaduras finas y estrechas. El tamaño del punto de enfoque debe coincidir con el ancho de la junta; si es demasiado grande, puede causar calor excesivo y distorsión. Si es demasiado pequeño, es posible que no penetre lo suficientemente profundo para materiales más gruesos.
- Frecuencia de pulso (láseres pulsados): para aplicaciones que requieren láseres pulsados, ajustar la frecuencia de pulso ayuda a controlar la cantidad de energía que se suministra a la soldadura. Las frecuencias de pulso más altas pueden proporcionar soldaduras más uniformes y continuas, mientras que las frecuencias más bajas proporcionan ráfagas de energía intermitentes, útiles para aplicaciones que necesitan un aporte mínimo de calor.
Propiedades materiales
El material que se suelda influye en la forma en que el láser interactúa con la superficie y penetra el metal. Factores como la reflectividad, la conductividad térmica y la composición de la aleación afectan la calidad de la soldadura.
- Reflectividad: los materiales con alta reflectividad, como el aluminio y el cobre, pueden reflejar una parte importante de la energía del láser, lo que reduce la absorción. El uso de longitudes de onda láser más bajas o el tratamiento previo de los materiales reflectantes pueden ayudar a aumentar la absorción y mejorar la calidad de la soldadura.
- Conductividad térmica: los materiales con alta conductividad térmica, como el cobre, disipan el calor rápidamente, por lo que requieren una mayor potencia del láser o parámetros ajustados para lograr una penetración adecuada. Los materiales con baja conductividad, como el titanio, retienen el calor, lo que permite realizar soldaduras más profundas con menos potencia.
- Composición de la aleación: Las aleaciones suelen tener distintos puntos de fusión y pueden requerir diferentes configuraciones del láser para lograr soldaduras uniformes. Algunas aleaciones también producen más salpicaduras o requieren diferentes frecuencias de pulso para evitar el agrietamiento, en particular aquellas con elementos que pueden evaporarse a temperaturas de soldadura.
- Estado de la superficie: la limpieza y el acabado de la superficie del material influyen en la absorción del haz láser. Los óxidos, los aceites o los contaminantes de la superficie pueden alterar el proceso de soldadura y debilitar las uniones. La limpieza o la preparación de la superficie antes de soldar pueden ayudar a mejorar la consistencia y la resistencia de la soldadura.
Diseño y montaje de juntas
El diseño de la unión y la calidad del ajuste afectan significativamente la calidad final de la soldadura. Un diseño de unión adecuado y un ajuste perfecto garantizan que el láser pueda fusionar los materiales con precisión sin espacios ni desalineaciones.
- Diseño de juntas: los distintos tipos de juntas (como juntas a tope, juntas traslapadas y juntas de filete) requieren configuraciones y enfoque de láser específicos para garantizar resultados óptimos. Por ejemplo, las juntas a tope pueden necesitar una penetración más profunda, mientras que las juntas traslapadas pueden ser menos profundas, pero requieren control para evitar una propagación excesiva del calor.
- Precisión de ajuste: la alineación precisa entre las piezas es esencial para lograr una calidad de soldadura uniforme. Cualquier espacio o desalineación puede provocar una fusión incompleta, lo que crea puntos débiles en la soldadura. Los ajustes ajustados garantizan que la energía del láser se absorba de manera efectiva en toda la unión, lo que minimiza la posibilidad de defectos. Para aplicaciones que requieren tolerancias extremadamente estrechas, se pueden utilizar sistemas de sujeción y fijación para sujetar las piezas de manera segura durante la soldadura.
- Compatibilidad de espesores: El espesor de la junta también afecta la resistencia de la soldadura. Al soldar materiales gruesos, los parámetros del láser deben ajustarse para penetrar completamente sin sobrecalentar el material circundante. Los materiales delgados, por el contrario, requieren ajustes de potencia más bajos para evitar deformaciones o quemaduras.
Gas protector
El uso de gas de protección ayuda a proteger el área de soldadura de la contaminación y la oxidación, que pueden afectar la calidad y el aspecto de la soldadura. La elección y el flujo del gas de protección desempeñan un papel importante para lograr soldaduras de alta calidad.
- Tipo de gas: Los gases de protección más comunes son el argón, el helio y el nitrógeno. El argón proporciona una atmósfera estable y se utiliza ampliamente para una variedad de metales. El helio se utiliza a menudo para una penetración profunda debido a su alta conductividad térmica, pero es más caro. El nitrógeno se utiliza a veces para materiales específicos, como el acero inoxidable, pero puede provocar nitruros en algunos metales, lo que podría afectar a la resistencia.
- Caudal de gas: el caudal del gas de protección debe ajustarse según el material y los parámetros de soldadura. Un caudal demasiado alto puede alterar el baño de soldadura y generar turbulencias, mientras que un caudal demasiado bajo puede no proteger completamente la soldadura, lo que permite la oxidación y provoca decoloración o porosidad.
- Método de suministro: El gas de protección se puede suministrar directamente a través de una boquilla cerca del cabezal del láser o, en algunos casos, a través de una línea de gas secundaria para una mayor cobertura. El suministro adecuado de gas garantiza una distribución uniforme, lo que protege la soldadura de la exposición al aire y promueve un acabado de soldadura limpio y estético.

Resumen
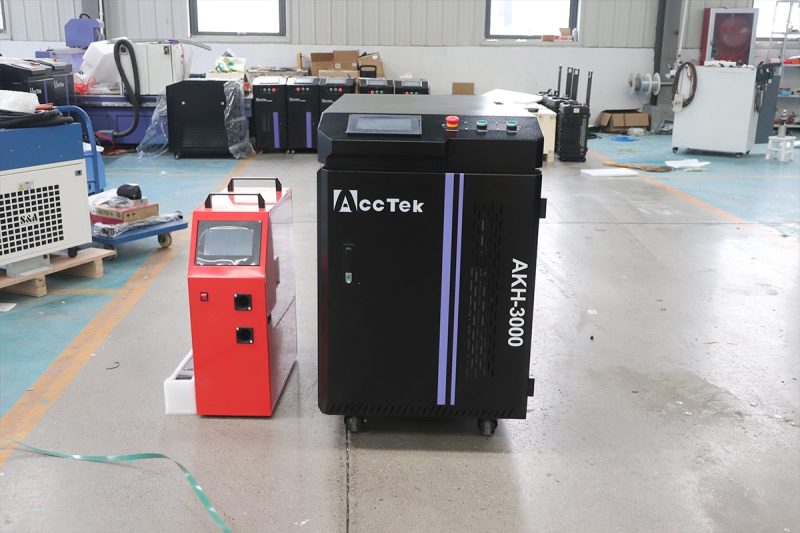
Obtenga soluciones de soldadura láser
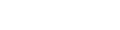
- [email protected]
- [email protected]
- +86-19963414011
- No. 3 Zona A, Zona Industrial de Lunzhen, Ciudad de Yucheng, Provincia de Shandong.