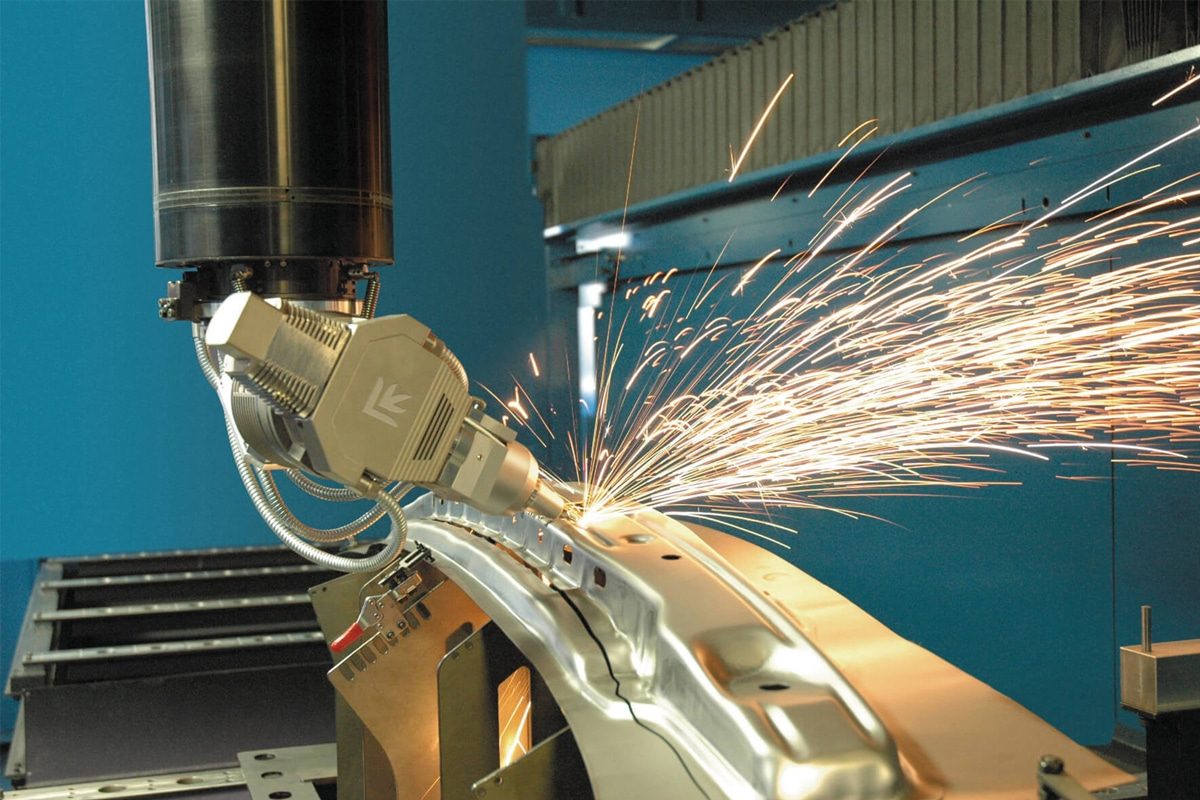
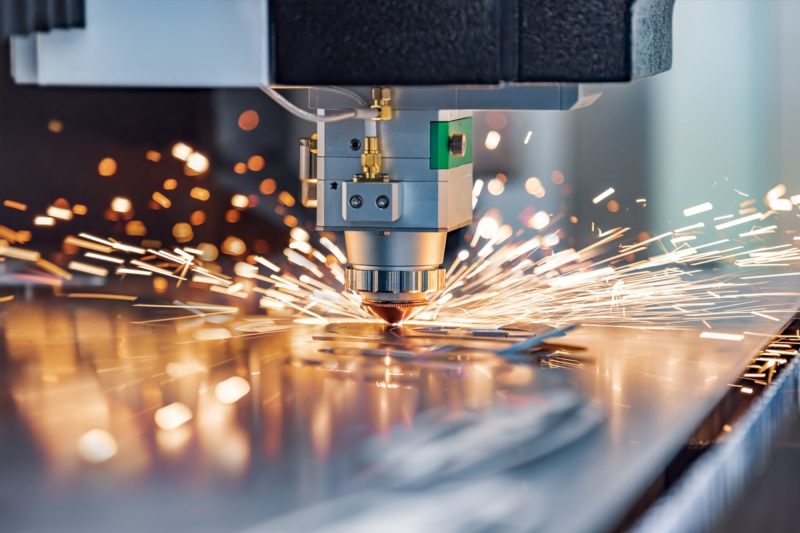
Overview of Fiber Laser Cutting Machines
What is a Fiber Laser Cutting Machine?
Applications in Various Industries
Due to their adaptability and precision, fiber laser cutting machines have a broad spectrum of applications across multiple industries:
- Automotive Industry: Fiber lasers are essential for creating complex car components, such as body panels, exhaust systems, and engine parts, with high precision. Their speed and efficiency improve production rates and reduce lead times.
- Aerospace Industry: Known for the stringent quality standards in aerospace, fiber laser cutting machines produce lightweight, high-strength components such as turbine blades, airframe sections, and brackets that meet exacting tolerances.
- Electronics Industry: With the growing demand for miniaturized electronic components, fiber lasers provide the accuracy needed to cut intricate circuit boards, metal enclosures, and battery elements essential for electronic devices.
- Medical Industry: Fiber laser cutting machines play a crucial role in manufacturing precision medical tools, implants, and surgical instruments. The non-contact nature of laser cutting also minimizes contamination, which is critical in medical applications.
- Jewelry and Arts: For intricate jewelry designs, fiber lasers offer unparalleled detail in cutting precious metals like gold and silver, allowing for customization and creativity in design. The machines are also used in decorative arts for engraving and fine detailing.
- Construction and Architecture: Fiber laser machines are frequently employed to cut structural elements, decorative panels, and facade components in the construction and architecture fields. They can create complex shapes and designs with precision, supporting both aesthetic and functional requirements.
Advantages Over Other Cutting Technologies
Fiber laser cutting machines offer several benefits over other cutting technologies, such as CO2 lasers, plasma cutting, and traditional mechanical cutting methods.
- Superior Precision and Speed: Fiber lasers produce a more focused and intense beam, allowing for higher cutting speeds and greater accuracy. This translates to cleaner edges, reduced rework, and more intricate designs without sacrificing speed.
- Energy Efficiency: Fiber lasers are more energy-efficient compared to CO2 lasers, as they convert a higher percentage of input energy into usable laser light. This efficiency reduces operational costs and supports sustainable production practices.
- Low Maintenance Requirements: Fiber laser cutting machines require minimal maintenance. Unlike CO2 lasers, they lack mirrors and moving parts within the laser source, making them less prone to alignment issues and component wear.
- Material Versatility: Fiber lasers excel in cutting a variety of metals and reflective materials, such as aluminum, brass, and copper, which are challenging for CO2 lasers. This versatility allows them to serve multiple sectors without the need for extensive machine adjustments.
- Extended Lifespan: The diodes in fiber lasers have a longer lifespan than those in other laser types, such as CO2 lasers. This longevity, along with fewer consumable parts, further reduces maintenance costs and machine downtime.
- Enhanced Safety: Fiber lasers often incorporate safety features, such as enclosed systems that protect operators from harmful laser exposure. Additionally, fiber lasers produce less fume and smoke compared to plasma or flame cutting, which contributes to a safer workplace environment.
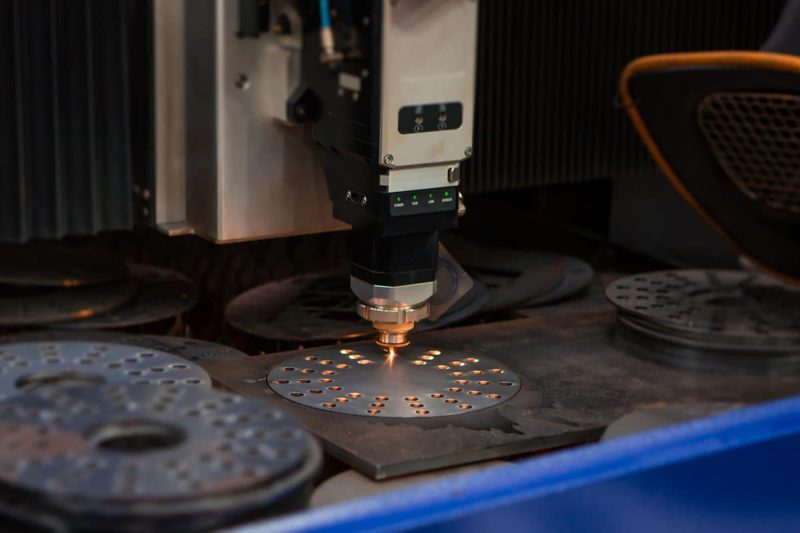
Operating Costs Overview
Definition of Operating Costs
Operating costs are the cumulative expenses required to run a fiber laser-cutting machine over time. Unlike the initial purchase or setup cost, operating costs are recurring, typically calculated over months or years, and are integral to the machine’s lifecycle expenses. For fiber laser cutting machines, operating costs include:
- Energy Consumption: The electricity required to power the laser source, cooling system, and other auxiliary equipment.
- Consumables: Components such as protective lenses, nozzles, and assist gases that wear out or are used up during operation.
- Maintenance and Repairs: Routine upkeep, part replacements, and repairs needed to maintain peak performance.
- Labor: Wages for operators, technicians, and any personnel involved in running and maintaining the machine.
- Downtime: Lost productivity due to scheduled or unscheduled maintenance, impacting both direct and indirect costs.
Importance of Understanding Operating Costs
Understanding operating costs is essential for businesses aiming to achieve high efficiency and profitability with fiber laser cutting machines. A clear picture of these costs enables companies to:
- Optimize Budgeting and Cost Control: Knowing where and how costs accumulate allows businesses to budget more accurately and allocate resources effectively, ensuring they stay within their operational budget.
- Maximize Return on Investment (ROI): By identifying areas where costs can be reduced—such as improving energy efficiency or optimizing consumable use—businesses can increase the ROI on their laser cutting machine.
- Improve Decision-Making for Cost Efficiency: Awareness of operating costs helps businesses make strategic decisions about factors such as machine usage, maintenance schedules, and consumable selection, ultimately enhancing overall cost efficiency.
- Enhance Competitive Edge: Lowering operating costs enables manufacturers to price their products competitively without sacrificing quality, making them more attractive to potential customers.
- Extend Machine Lifespan: Consistent maintenance and strategic use of consumables reduce wear and tear on the machine, contributing to its longevity and minimizing replacement costs.
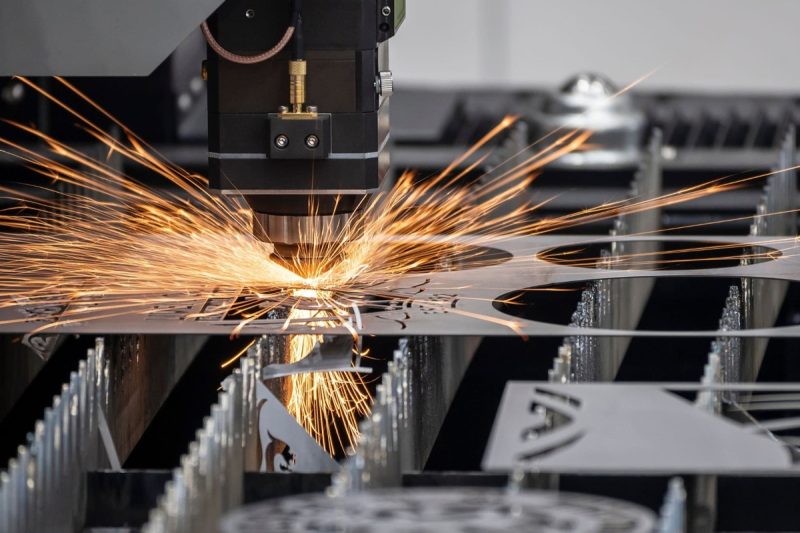
Factors Affecting Operating Costs
Energy Consumption
- Electricity Costs: Fiber laser cutting machines are energy-intensive, especially when operating at high power levels. Electricity costs can vary based on local utility rates, but it’s essential to consider daily and seasonal power fluctuations and even potential peak-time surcharges. Running the machine during off-peak hours, if feasible, can reduce electricity expenses. Additionally, choosing energy-efficient equipment or utilizing renewable energy sources can make a long-term impact on cost savings.
- Efficiency of the Laser Source: Fiber lasers are typically more efficient than other laser types, like CO2 lasers, converting more electrical energy into the laser beam itself and reducing wasted energy as heat. High-quality fiber laser sources from reputable manufacturers often provide higher efficiency, improving cut quality and speed, thus lowering overall power usage per cut. Choosing the correct power level for your application (e.g., a 3kW laser for thinner materials instead of a 6kW) avoids excess energy consumption.
- Standby Energy Consumption: Fiber laser machines often consume energy even in standby mode, running systems like cooling and internal electronics. Standby consumption can add up, especially in high-use environments. Automated power-off features during idle periods and ensuring efficient standby energy management systems are active can reduce these unnecessary costs.
Maintenance and Consumables
- Laser Source Maintenance: The laser source, the machine’s core component, requires regular inspection and calibration to maintain peak performance. Cleaning the laser head, checking alignment, and preventing dust buildup can enhance its lifespan. Some laser sources also benefit from occasional alignment and recalibration, which requires skilled technicians and impacts both labor and operational costs.
- Replacement Parts: Optical components like lenses, mirrors, and protective glass are especially prone to wear and damage from debris or reflectivity of certain materials (e.g., aluminum). High-quality replacement parts might have a higher upfront cost but offer longer life spans, improving cut quality and lowering the frequency of replacements. Tracking and sourcing replacement parts from reputable suppliers or directly from the machine’s manufacturer can help prevent machine downtime.
- Consumable Items: Consumables, including lenses, nozzles, filters, and assist gases, directly impact both cost and cut quality. Protective lenses, for example, prevent material debris from damaging the laser optics but need to be inspected and replaced regularly to avoid cut quality issues. Opting for higher-quality consumables, which typically last longer, can offset the overall cost by requiring less frequent replacement.
- Cooling System Maintenance: Cooling systems prevent the machine from overheating, preserving the integrity of the laser source and other sensitive parts. Regularly inspecting coolant levels, cleaning filters, and maintaining the chiller system prevents overuse of power and reduces the risk of unexpected malfunctions. Changing coolant fluids periodically and monitoring the cooling system’s efficiency is critical to maintain optimal machine temperature and avoid heat-related damage.
Gas Consumption
- Assist Gases: Assist gases, such as oxygen, nitrogen, and compressed air, are necessary to optimize the cutting process. Each gas has different cutting effects on various materials. For instance, oxygen is typically used for cutting carbon steel, creating an exothermic reaction that speeds up the cutting process, while nitrogen provides a cleaner edge on stainless steel. Understanding which gases work best for different materials and investing in bulk purchasing or high-capacity gas tanks can lower long-term gas expenses.
- Gas Purity and Pressure: The purity and pressure of assist gases significantly impact cut quality, especially for metals like stainless steel and aluminum. High-purity nitrogen or oxygen ensures cleaner cuts with minimal oxidation, but purer gases are more expensive. Adjusting pressure levels based on material thickness and required cut quality can help control costs without sacrificing performance. Regular calibration of gas flow rates and investing in pressure regulators can also improve efficiency.
- Impact on Cutting Quality and Speed: The right choice of assist gas and optimal gas flow directly affect cutting speed, quality, and post-processing needs. Using lower-purity gas may save costs initially, but it can compromise cut quality, potentially requiring more post-cut processing, which adds additional labor and material handling costs. Finding the balance between gas purity and cutting requirements can help maintain high productivity with controlled costs.
Labor Costs
- Operator Skill Level: Skilled operators who understand the technical nuances of fiber laser cutting can achieve faster, more precise cuts, reducing waste and improving productivity. While higher wages may be associated with skilled operators, the investment often pays off through better machine handling, fewer errors, and greater output quality. Well-trained operators are also capable of performing minor troubleshooting, reducing reliance on external technical support.
- Training Costs: Training is crucial to ensure operators are up-to-date with the latest machine functions, software updates, and safety practices. While initial training represents an upfront cost, it reduces material waste, machine damage, and operational errors over time. Continuous training, especially as new software or machine features become available, ensures that operators can maximize machine performance.
- Automation and Its Impact on Labor: Automation, such as automated loading/unloading systems and software-driven cutting processes, reduces the need for manual handling and intervention. Automated systems often improve consistency and efficiency, allowing operators to focus on machine monitoring rather than handling. Although initial automation setup can be costly, the long-term reduction in labor hours can make it a cost-effective solution.
Material Costs
- Types of Materials Being Cut: Different materials require varied laser settings and assist gases, affecting energy consumption, gas use, and machine wear. For example, cutting harder materials, like steel or titanium, demands higher power settings and may require specific gases to optimize cut quality. Lower-cost, easier-to-cut materials, like mild steel, incur less wear and tear, reducing consumables and extending machine life.
- Material Thickness: Thicker materials require slower cutting speeds and higher power levels to penetrate fully, increasing both energy and gas usage. Additionally, thicker materials can cause greater wear on nozzles and other consumables, adding to replacement costs. Optimizing settings based on thickness and material type is essential for managing these expenses effectively.
Machine Downtime
- Scheduled Maintenance: Planned maintenance keeps machines in peak condition, reducing the likelihood of unexpected breakdowns. Scheduling maintenance during low-demand periods minimizes the impact on productivity, helping to maintain production schedules and reduce downtime costs.
- Unexpected Breakdowns: Unexpected failures can lead to costly downtime and affect productivity. Preventive measures, such as predictive maintenance software, allow for real-time monitoring of machine health and early detection of potential issues. Prompt access to technical support and maintaining an inventory of essential spare parts can minimize downtime during unforeseen breakdowns.
- Impact on Production Schedules: Downtime disrupts production timelines, potentially affecting delivery schedules and customer satisfaction. For high-demand periods, having backup machines or the ability to reassign production loads to other equipment helps maintain productivity and meet deadlines.
Software and Programming
- CAD/CAM Software Costs: CAD/CAM software is crucial for creating cutting paths and optimizing machine functionality. Many software options require licenses, subscriptions, or regular updates, which contribute to long-term costs. Choosing software that offers both cost-effectiveness and advanced features helps reduce operating expenses.
- Nesting Efficiency: Efficient nesting software arranges cut parts on the material with minimal waste, maximizing usage and reducing material costs. Advanced nesting algorithms allow for tight arrangements, cutting down scrap material and lowering the cost per part.
- Software Updates and Support: Regular software updates provide access to new features, better nesting algorithms, and improved machine performance. However, updates may come with additional fees. Access to timely support also ensures minimal downtime if issues arise, reducing potential delays and lost productivity.
Environmental Factors
- Ambient Temperature and Humidity: Extreme temperatures or high humidity levels can impact machine performance and lifespan. Maintaining stable room conditions reduces the burden on the cooling system and prevents condensation, which can lead to electrical issues or component degradation.
- Dust and Cleanliness of the Working Environment: Dust and debris can contaminate optics and affect cut quality. A clean workspace reduces the frequency of cleaning cycles, maintenance requirements, and replacement parts, all of which contribute to cost savings.
- Impact on Machine Performance: Controlled environmental conditions extend the life of machine components and maintain consistent performance. Implementing air filtration and regular cleaning protocols further minimizes the risk of component wear due to environmental factors.
Depreciation and Financing Costs
- Initial Investment Cost: The purchase price influences the overall cost structure. Investing in a high-quality machine may require a larger upfront investment, but it often results in lower ongoing costs and greater longevity.
- Depreciation Over Time: The machine’s value decreases with age and use. Proper maintenance slows depreciation, preserving the machine’s value, and improving its potential resale value. Accounting for depreciation helps in financial planning and determining the machine’s true operating costs over time.
- Interest on Financing: If the machine is financed, interest payments become part of the operating costs. Securing favorable financing terms or paying down loans early can reduce long-term expenses, easing the overall financial burden.
Regulatory Compliance
- Safety Regulations: Adhering to safety regulations minimizes risk, protecting employees and reducing liability. Investing in safety features, such as protective enclosures, emergency stops, and safety sensors, ensures regulatory compliance and workplace safety.
- Environmental Regulations: Regulations on emissions and waste disposal can add compliance costs, such as installing fume extraction systems or handling material waste responsibly. Compliance avoids fines and supports a more sustainable, environmentally friendly operation.
- Costs Associated with Compliance: Regular audits, training, and certification for regulatory compliance may be costly initially but prevent penalties and improve workplace safety, ultimately supporting long-term business growth.
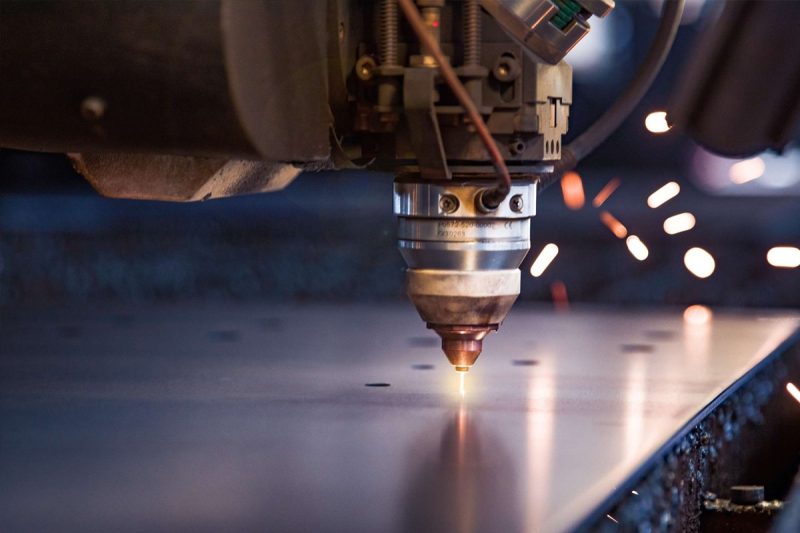
Strategies to Optimize Operating Costs
Regular Maintenance Schedules
Establishing a regular maintenance schedule is one of the most effective ways to reduce costs associated with unexpected breakdowns, ensuring that the machine consistently operates at peak efficiency.
- Preventive Maintenance: Routine checks on components like optics, nozzles, and cooling systems prevent gradual wear and tear from becoming major issues. Scheduling regular cleanings and inspections helps avoid costly repairs and prolongs the machine’s lifespan.
- Predictive Maintenance Tools: Utilizing monitoring systems that predict wear or imminent failures based on data can further enhance maintenance efforts. These systems alert operators to potential issues, allowing for repairs before they lead to costly downtime.
- Maintenance During Off-Peak Hours: Scheduling maintenance during non-peak hours ensures that production is not interrupted, allowing businesses to maintain a steady workflow and meet delivery timelines.
Investing in Energy-Efficient Machines
Energy consumption is a significant component of operating costs, so investing in an energy-efficient fiber laser machine can yield substantial savings over time.
- Choosing High-Efficiency Laser Sources: Fiber lasers are inherently more efficient than CO2 lasers, converting more electricity into laser energy with less heat wastage. Selecting machines with high-quality, energy-efficient laser sources reduces electricity consumption and overall costs.
- Power Management Systems: Look for machines that offer power-saving modes or automated standby features. These can cut power to non-essential components when the machine is idle, reducing unnecessary energy use.
- Energy-Efficient Cooling Systems: High-quality, energy-efficient chillers and cooling systems keep the laser source at an optimal temperature while consuming less power. Monitoring and maintaining these systems is essential for consistent performance.
Training Operators
A well-trained operator can make a significant difference in reducing waste, increasing productivity, and lowering maintenance costs. Training should be ongoing to ensure operators stay proficient with the latest equipment and software updates.
- Basic Troubleshooting Skills: Providing operators with basic troubleshooting skills allows them to address minor issues, reducing the need for external technical support and minimizing downtime.
- Advanced Programming and Machine Handling: Training operators in advanced machine handling and programming can lead to more efficient use of materials and better cut quality. Skilled operators are also more likely to use optimal machine settings, reducing wear on consumables and maximizing the machine’s potential.
- Safety and Maintenance Training: Training operators on safe practices and basic maintenance procedures minimizes the risk of accidents and ensures that the machine is kept in good condition.
Effective Material Management
Materials can be one of the most significant costs in fiber laser cutting operations. Efficient material use reduces waste, lowers costs, and increases profitability.
- Optimized Nesting Software: Advanced nesting software arranges parts on sheets for optimal material usage, reducing scrap and waste. Improved nesting efficiency also allows for faster cutting times and reduced setup times.
- Material Inventory Management: Maintaining an accurate inventory helps prevent overordering, which ties up resources, and underordering, which disrupts production. Automated inventory systems ensure materials are available when needed, minimizing downtime and wasted resources.
- Scrap Recycling and Waste Reduction: Implementing recycling strategies for scrap metal and other waste materials can recover some costs. Additionally, reusing leftover material, when feasible, can further reduce expenses.
Utilizing Automation and Advanced Software
Automation and modern software solutions can streamline operations, minimize manual labor, and improve machine performance. Though initial costs may be high, the long-term savings are often substantial.
- Automated Loading and Unloading Systems: Automation for material handling reduces the time operators spend manually loading and unloading, allowing for faster, continuous cutting with less labor.
- Real-Time Monitoring and Diagnostics: Many modern fiber laser machines come with monitoring systems that provide real-time data on machine health and performance. These systems enable predictive maintenance and help prevent unplanned downtime.
- Optimized Cutting Path Software: Software that automatically optimizes the cutting path saves time and reduces machine wear. This software minimizes unnecessary movements and cuts, improving efficiency and prolonging machine life.
Investing in Quality Consumables
Quality consumables may have a higher upfront cost but often last longer and perform better, reducing the frequency of replacement and improving cut quality.
- Optics and Protective Glass: Investing in high-quality optics and protective glass extends the lifespan of these components, maintaining cut quality and reducing downtime. Cheap or poorly made optics may wear out faster, increasing costs in the long term.
- Durable Nozzles and Lenses: Using durable nozzles and lenses that are resistant to wear and contamination leads to fewer replacements and more consistent cutting. Regularly cleaning these components and following manufacturer recommendations for care prolongs their life.
- Consumables Tracking and Management: Keeping track of consumables usage allows for timely replacements, preventing wear-related quality issues. Many machines also offer alerts for consumable replacement, which can improve maintenance efficiency.
Choosing Appropriate Assist Gases
Assist gases are necessary for the cutting process, and selecting the right type and purity can optimize both cost and cut quality.
- Selecting the Right Gas: Different materials require different gases. For instance, nitrogen is preferred for clean cuts on stainless steel, while oxygen is used for carbon steel to accelerate the cutting process. Choosing the correct gas for each job reduces gas waste and enhances cut quality.
- Adjusting Gas Purity and Flow Rate: High-purity gases produce better-cut quality, but they come at a higher cost. Adjusting the purity based on the job’s quality requirements helps balance cost and quality. Monitoring flow rates and optimizing them for each material type also reduces gas consumption without compromising performance.
- Bulk Purchasing and Efficient Storage: Bulk purchasing of assist gases and efficient storage practices help reduce gas costs. Ensuring that gas tanks are correctly stored and managed can prevent leaks and other issues that lead to waste.
Negotiating Better Rates for Energy and Materials
Energy and material costs are two of the most significant contributors to operating costs. By negotiating better rates, businesses can achieve substantial savings.
- Bulk Material Discounts: For high-volume orders, many suppliers offer discounts on materials. Negotiating with suppliers for bulk discounts or loyalty-based pricing can lower costs over time.
- Energy Rate Negotiation: In regions where energy rates can be negotiated, securing a favorable rate or opting for long-term energy contracts can reduce electricity costs. Some manufacturers also explore options with renewable energy providers for cost stability and environmental benefits.
- Preferred Supplier Agreements: Forming partnerships with preferred suppliers for consumables, replacement parts, and assist gases can lead to better pricing and more reliable service. Long-term contracts may yield additional discounts and more flexible payment terms, reducing upfront cash flow burdens.
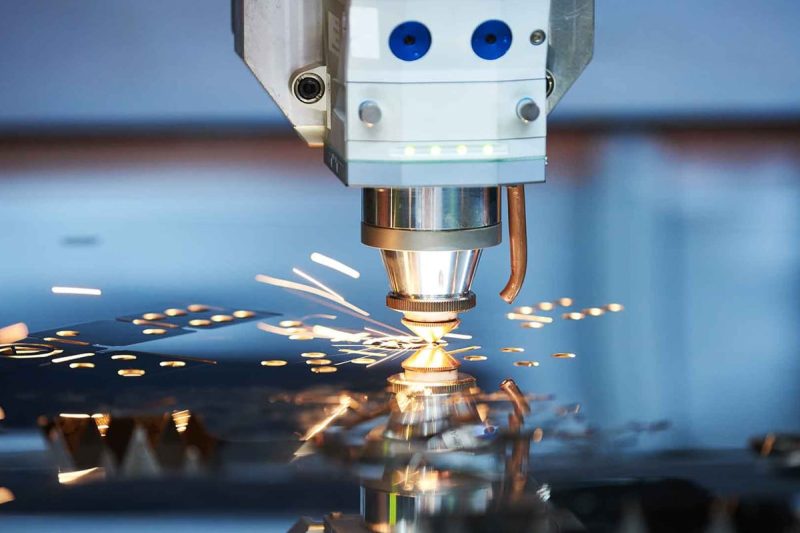
Summary
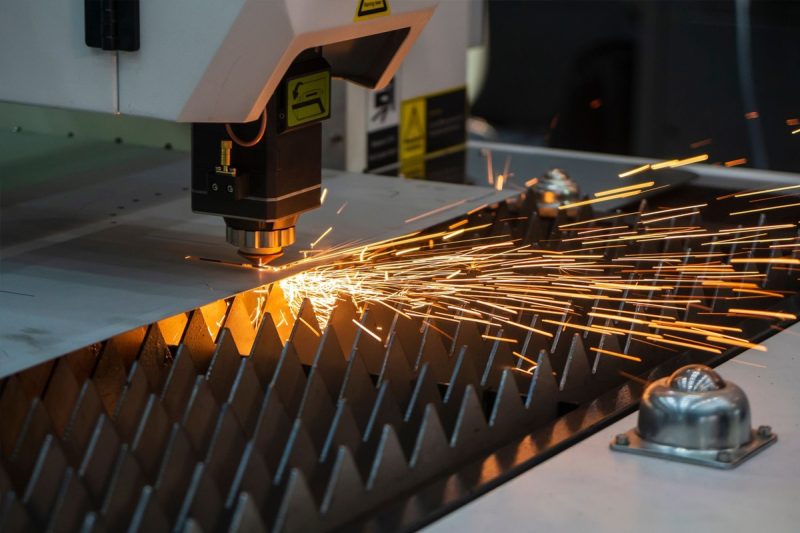
Get Laser Cutting Solutions
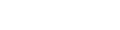
- [email protected]
- [email protected]
- +86-19963414011
- No. 3 Zone A, Lunzhen Industrial Zone,Yucheng City , Shandong Province.