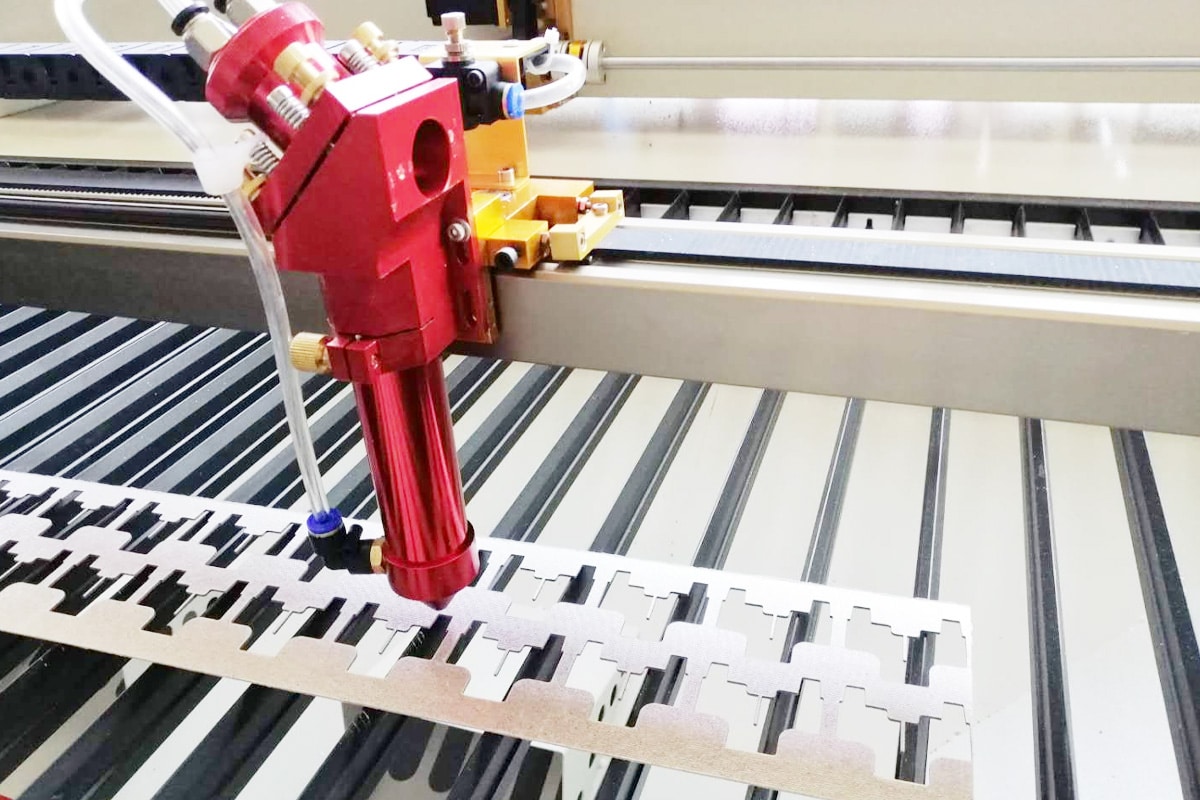
Factors to Consider When Installing Ventilation and Exhaust Systems for CO2 Laser Cutting Machines
CO2 laser cutting machines are mostly used to cut non-metallic materials, such as plastics, wood, textiles, etc. The smoke produced may contain particulates, unpleasant gases, and potentially dangerous compounds, depending on the material being processed. To maintain the health and safety of the laser operator and the people around him, the harmful gases produced by the CO2 laser cutting machine must be exhausted, and a large number of smoke particles can also damage the laser optical components, resulting in frequent maintenance and increased downtime. Properly designed and maintained ventilation systems can help control smoke emissions, protect operators from harmful pollutants, and ensure compliance with regulatory requirements. It can also improve cutting efficiency and extend the life of the machine. Many customers want to know how to create an effective exhaust system. Next, we will take a closer look at this issue and gain an in-depth understanding of the factors that need to be considered when installing an exhaust system.
Table of Contents
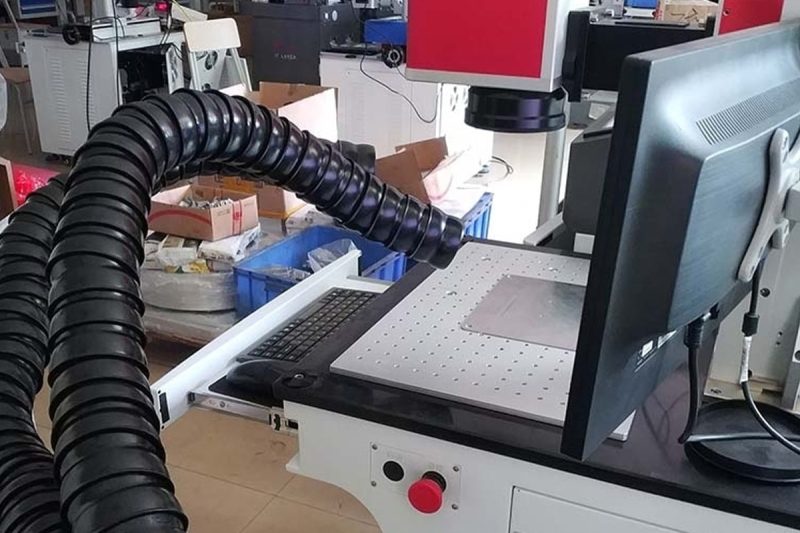
Importance of Ventilation and Exhaust Systems
A ventilation and exhaust system is essential for any laser engraver or cutter. Without it, operating the machine can pose serious health risks to both the worker and the machine itself.
Health and Safety
CO2 laser cutting machines are mostly used to process non-metallic materials. The wavelength of the CO2 laser generator is 10.6um, which is easily absorbed by non-metallic materials. CO2 laser cutting will produce smoke and harmful gases (such as carbon dioxide, nitrogen oxides, and volatile organic compounds). If these substances are not discharged in time, they will pose a threat to the health of the operator and may cause respiratory diseases, allergic reactions, and other problems. The design of the ventilation and exhaust system can effectively capture and filter these harmful substances to ensure the air quality of the working environment. In addition, everyone in the laser cutting industry should abide by safety protocols, whether it is a small laser machine enthusiast or a large laser cutting company.
Environmental Compliance
Depending on the location, the local government has a series of laws and regulations, and laser practitioners need to follow relevant regulations to properly discharge smoke. If necessary, smoke needs to be pre-treated and meet environmental standards before it can be discharged into the air. Many countries and regions have strict environmental regulations on industrial emissions. Using non-compliant exhaust systems may result in legal liability and fines. Choosing an efficient ventilation system can help companies comply with local environmental regulations, reduce environmental impact, and maintain a good corporate image.
Equipment Performance and Life
CO2 laser cutting machines are also affected by residual smoke. Without a proper exhaust system, smoke and particulate matter generated during the cutting process may be deposited on the internal components of the CO2 laser cutting machine, affecting the performance and service life of the equipment. A proper ventilation system can prevent pollutants from entering the interior of the equipment, reduce maintenance costs, extend equipment life, and improve production efficiency.
AccTek Laser CO2 laser cutting machines have different powers and functions to meet the needs of different customers. The fully enclosed design ensures that the laser beam and smoke gas are isolated inside the machine, thereby reducing the risk of accidental exposure to the operator. A reasonable ventilation system, can ensure the reasonable discharge of exhaust gas and protect the optical components of the machine.
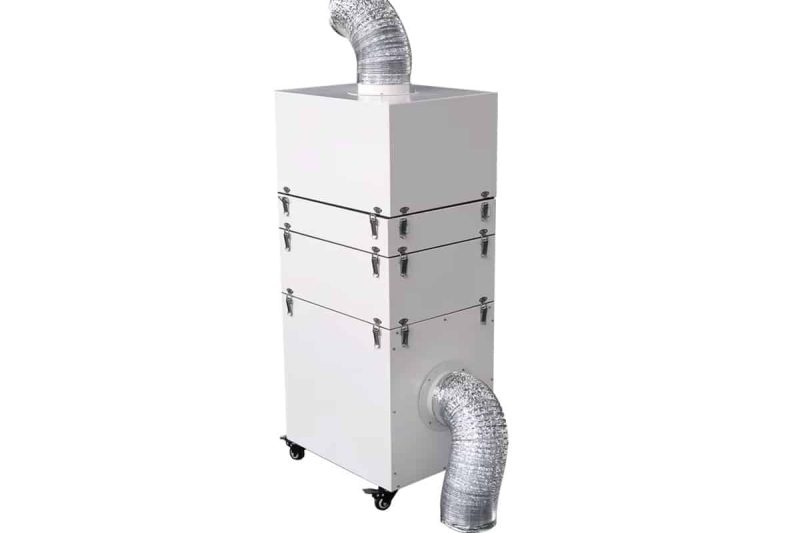
Factors to Consider When Selecting a Ventilation or Exhaust System
Air Volume
Air volume is a key parameter when selecting a ventilation system and needs to be determined based on the workload of the CO2 laser cutting machine, the size of the work area, and the type of processing material. Air volume is a crucial parameter and the selection of air volume should take into account the following factors to ensure that the system can effectively capture and exhaust all smoke and gases generated during the cutting process.
- Workload: The workload of the CO2 laser cutting machine directly affects the air volume required for the ventilation system. High-load cutting tasks usually produce more smoke and gases, so a larger air volume is required to ensure effective exhaust and filtration. Knowing the maximum workload of the machine can help determine the capacity of the ventilation system.
- Work area size: The size of the work area is also an important factor in determining air volume. Larger work areas require higher air volumes to ensure that pollutants in the air can be captured and exhausted promptly. If the air volume of the ventilation system is insufficient, it may cause pollutants to spread in the work area and affect the air quality.
- Type of processing material: Different processing materials will release different types and amounts of smoke and gases during the laser cutting process. For example, cutting plastics and synthetic materials may release more harmful gases, while cutting metals usually produce more smoke. Therefore, it is very important to adjust the air volume according to the type of processing material.
When choosing a ventilation system for a CO2 laser cutting machine, properly determining the air volume is key to ensuring operational safety and equipment performance. By combining factors such as workload, work area size, and type of processed materials, the most appropriate ventilation solution can be selected for the company, thereby improving production efficiency, protecting employee health, and complying with environmental regulations.
Filtration Efficiency
When choosing a ventilation and exhaust system for a CO2 laser cutting machine, filtration efficiency is a crucial consideration. An efficient filtration system can effectively remove various pollutants generated during the cutting process and ensure the air quality of the working environment. The type and efficiency of the filter (such as HEPA filter, or activated carbon filter) should be considered when selecting to effectively remove different types of pollutants. The following are some commonly used filters and their characteristics:
HEPA Filter
- Features: High-efficiency particulate air filter, can remove 99.97% of particles with a diameter of 0.3 microns or larger.
- Scope of application: Effectively remove fine particles, smoke, and tiny solid pollutants in the air.
Activated Carbon Filter
- Features: Remove gaseous pollutants and odors by using the adsorption characteristics of activated carbon.
- Scope of application: Suitable for removing volatile organic compounds (VOCs), odors, and harmful gases.
Electrostatic Filter
- Features: Remove particulate matter by the principle of electrostatic adsorption.
- Scope of application: Effectively captures smoke and tiny particles, but requires regular cleaning and maintenance.
Bag Filter
- Features: Adopts a multi-layer filter bag structure, which can accommodate a larger volume of dust and particles.
- Scope of application: Suitable for high dust environments, can capture larger particles.
Metal Mesh Filter
- Features: Filter larger particles through a metal mesh.
- Scope of application: Mainly used for primary filtration, usually used as a pre-filter in combination with other filters.
The above filters are often used in combination with each other. Metal mesh filters are generally used as primary filters, followed by bag filters, electrostatic filters, HEPA filters, and activated carbon filters. For regions and countries with very strict environmental protection requirements, it is very convenient to install a filter with a combination of multiple filters in the ventilation and exhaust system. The treated exhaust gas can meet safety standards for discharge. When installing the filter, take into account the type of waste generated by cutting and then choose the appropriate filter combination.
Piping and Exhaust Configuration
Reasonable duct design and exhaust configuration can help improve the efficiency of the system. The duct should be as short as possible with minimal bends and long distances to reduce airflow resistance. At the same time, the exhaust outlet should be set in a suitable position to prevent impact on the surrounding environment and buildings.
Pipeline Settings
- Reduce bends: Each elbow will increase airflow resistance, and straight pipes should be used as much as possible. If a turn is necessary, use a large radius elbow to reduce resistance.
- Shorten length: Shorten the pipe length as much as possible to reduce wind resistance and energy consumption.
- Pipe diameter matching: The pipe diameter should match the output of the fan and the amount of gas processed. Too small a diameter will increase resistance, while too large a diameter may lead to reduced efficiency.
- Reduce friction: Choose a pipe material with a smooth inner wall to reduce airflow friction and increase airflow speed and efficiency.
Exhaust Outlet Position Setting
- Away from the inlet: The exhaust outlet should be set away from the fresh air inlet to prevent polluted air from re-entering the system.
- Avoid sensitive areas: The exhaust outlet should be away from the office area, air inlet, or adjacent buildings to reduce the impact on the crowd and the surrounding environment.
- Raise the exhaust outlet: Set the exhaust outlet at a higher position to ensure that the exhaust gas can diffuse quickly and reduce the impact on the ground and surrounding buildings.
Noise Level
The ventilation and exhaust systems of CO2 laser cutting machines may generate noise during operation, which may not only affect the physical and mental health of operators but also interfere with the surrounding working environment. Therefore, it is necessary to select low-noise equipment or install silencers to reduce the impact on operators and the surrounding environment.
- Select low-noise equipment: When purchasing ventilation and exhaust systems, give priority to equipment that has been designed with noise reduction treatment in mind. These equipment usually use noise reduction technologies such as low-noise fans and shock-absorbing pads, which can keep noise at a low level while ensuring performance.
- Install silencers: For installed ventilation and exhaust systems, if the noise level is high, consider installing silencers. Silencers such as silencers and soundproof covers can effectively absorb or isolate the spread of noise, thereby reducing the impact of noise on the surrounding environment.
Energy Efficiency
Energy-efficient ventilation systems can not only reduce operating costs but also reduce energy consumption. Choosing energy-efficient systems will help achieve long-term economic and environmental benefits.
- Prioritize energy-efficient fans when purchasing ventilation systems. Running the fan at full speed all the time, regardless of the actual workload, will produce more air than is needed, resulting in energy waste and wear on the filter. Adjusting the fan speed according to the actual air volume required for the work is essential to reduce energy consumption and costs. Variable speed drives (VSD) with pressure control, also known as variable frequency drives (VFD) or inverters, help control the fan air volume changes. The pressure of the duct system is controlled and the fan speed can be optimized according to the actual required air volume to achieve the best dust removal capacity.
- Use fans with back-curved blades.
Maintenance and Suitability
- The system should be designed to facilitate daily maintenance and operation, the filters should be easy to replace, and the equipment failure rate should be low to reduce downtime. Choose a system that is suitable for the specific application scenario and ensure that it can meet the requirements of different materials and processes.
Comply with Regulations and Standards
- Ensure that the selected ventilation and extraction systems meet local and international safety, health, and environmental standards, such as ISO, CE certification, etc. This not only helps to comply with legal regulations but also improves the credibility of the company.
Cost and Budget
- When choosing a ventilation system, you need to consider the initial investment, operating costs, and maintenance costs. Choose a cost-effective system within your budget to achieve the best economic benefits.
Integration with Machine Control
- Choosing ventilation equipment that can be integrated with the CO2 laser cutting machine control system can achieve automated control and improve the response speed and safety of the system. This allows the ventilation system to automatically turn on when the cutting machine starts and automatically turn off when it is turned off.
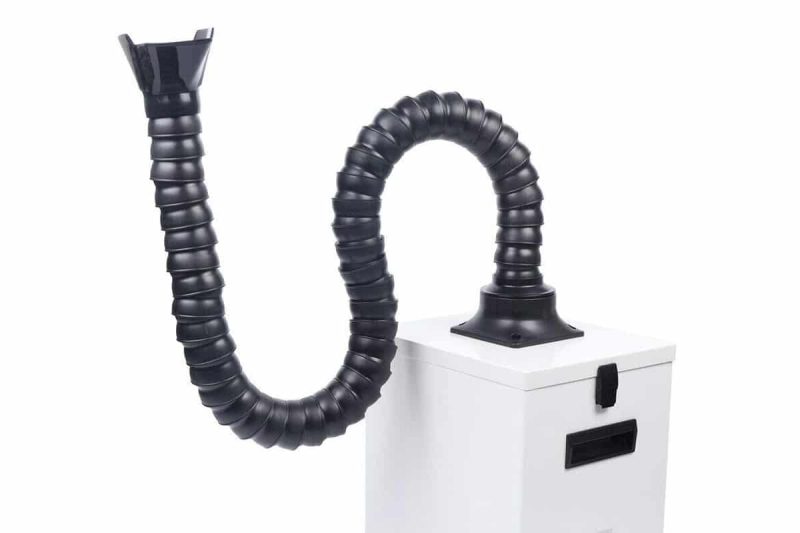
Summary
Choosing the right ventilation or extraction system is essential for the safe and efficient operation of CO2 laser cutting machines. Considering factors such as air volume, filtration efficiency, duct design, noise level, energy efficiency, ease of maintenance, regulatory compliance, cost, and integration with the machine can help companies maximize production efficiency while protecting operator health, extending equipment life, and complying with environmental regulations. Through reasonable planning and implementation, companies can create a safe, environmentally friendly, and efficient production environment.
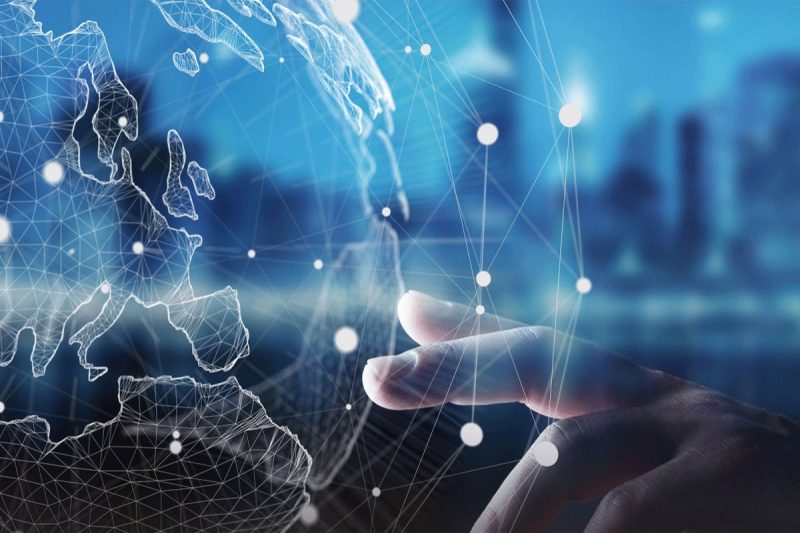
Get Laser Solutions
Choosing the right ventilation or exhaust system can help optimize power consumption and achieve high operating efficiency. Working with a trusted supplier ensures access to advanced technology, tailored advice and ongoing support. At AccTek Laser, we offer a comprehensive range of ventilation or exhaust system equipment designed to meet a variety of industrial needs. Our experts can help you choose the most energy-efficient model and configuration, taking into account factors such as material type, thickness and production volume. We also offer cutting-edge features such as high-efficiency laser generators, intelligent cooling systems and energy management software to maximize performance and minimize energy use. In addition, our team provides regular maintenance services and technical support to keep your equipment at peak efficiency. By partnering with us, you can achieve significant energy savings, reduce operating costs and enhance your sustainability efforts. If you have any questions, please contact us in time, AccTek Laser is committed to providing perfect laser solutions for every customer!
Energy-efficient ventilation systems can not only reduce operating costs but also reduce energy consumption. Choosing energy-efficient systems will help achieve long-term economic and environmental benefits.
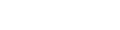
Contact information
- [email protected]
- [email protected]
- +86-19963414011
- No. 3 Zone A, Lunzhen Industrial Zone,Yucheng City , Shandong Province.
Get Laser Solutions