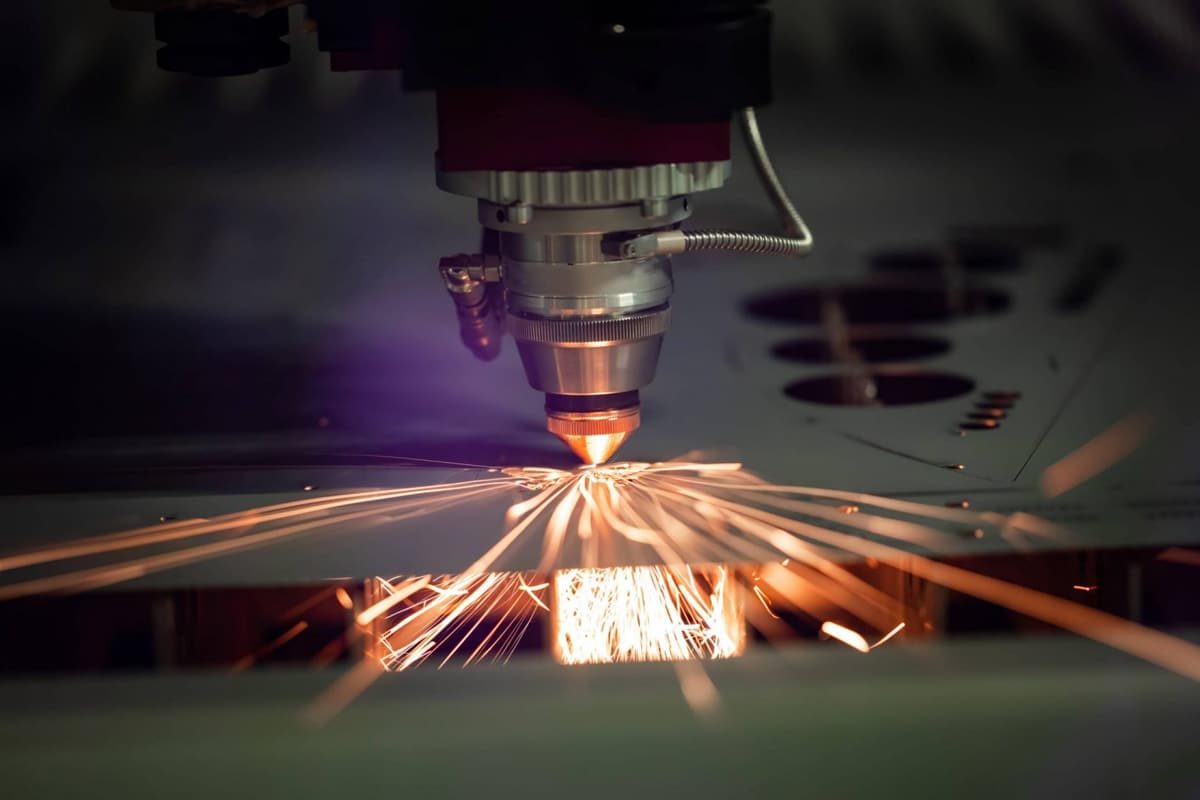
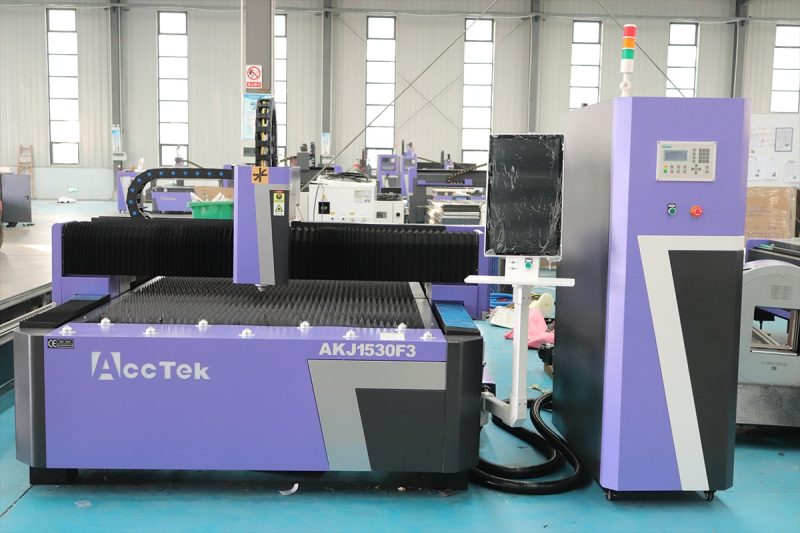
What Is a Fiber Laser Cutting Machine?
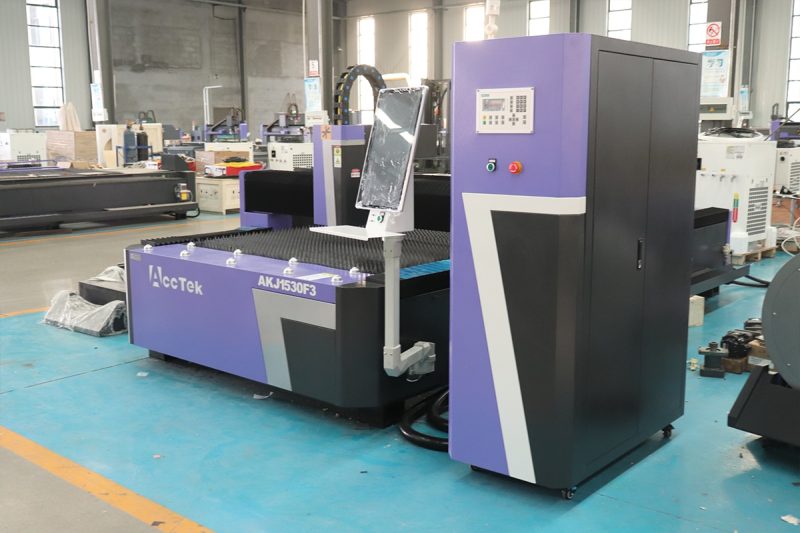
How Does a Fiber Laser Cutting Machine Work?
Laser Generation
The laser beam is generated inside the laser source, typically using rare-earth-doped optical fibers (like ytterbium).
- Diode Lasers pump energy into the fiber, stimulating electrons to higher energy states.
- When these electrons return to their normal state, they release photons, generating a coherent laser beam through stimulated emission.
- This beam is then amplified within the fiber until it reaches the desired power output, ranging from a few hundred watts to several kilowatts, depending on the application.
Beam Delivery
Once generated, the laser beam travels through fiber optic cables directly to the cutting head.
- Unlike CO2 lasers, which require mirrors to deliver the beam, fiber lasers use optical fibers, making the system more reliable with minimal maintenance.
- Fiber optic delivery ensures flexible movement of the laser head, enabling high-precision cuts on complex geometries.
Beam Focusing
At the cutting head, the laser beam passes through collimating lenses and focusing lenses, which align and concentrate the beam to a fine focal point on the material.
- The focal point can be as small as 0.1 mm, creating an intense power density.
- A height sensor adjusts the position of the cutting head in real time to maintain the ideal focal distance from the material, ensuring consistent cut quality.
Interaction with Material
When the focused laser beam hits the material, it heats it to its melting or vaporization point, depending on the cutting mode:
- Melting: For materials like stainless steel, the laser melts the material.
- Vaporization: For thinner materials or plastics, the laser evaporates the material directly.
Assist Gas Application
An assist gas is applied through a nozzle alongside the laser beam to improve the cutting process. The type of gas used depends on the material and the cut’s requirements:
- Oxygen: Used for cutting mild steel, where it reacts with the material to speed up the cutting process.
- Nitrogen: Ideal for stainless steel or aluminum, as it prevents oxidation and leaves a clean edge.
- Air: Can be used for cutting non-metals or thinner metals as a low-cost alternative.
Motion Control
The cutting head or the workpiece moves according to pre-programmed patterns using a CNC (Computer Numerical Control) system.
- Linear Motors or Servo Motors drive the motion, ensuring smooth and precise movements along the X, Y, and Z axes.
- Guide rails help stabilize the cutting head during operation, maintaining high accuracy.
Cutting Process
There are several methods of laser cutting, depending on the material and desired outcome:
- Fusion Cutting: Used for metals like stainless steel, where the material is melted, and high-pressure nitrogen removes the molten material.
- Flame Cutting: Common for carbon steel, where oxygen helps create an exothermic reaction to enhance the cutting speed.
- Sublimation Cutting: The material vaporizes directly, often used for non-metals or thinner materials.
Feedback and Monitoring
Advanced fiber laser cutting machines include real-time monitoring systems to ensure optimal performance:
- Height Sensors maintain the correct distance between the cutting head and the material surface.
- Vision Systems or cameras detect the material edges and align the laser accordingly.
- Laser Power Monitors track the output, ensuring the laser beam maintains consistent power throughout the cut.
Cooling and Safety Systems
To prevent overheating and maintain optimal performance, fiber laser machines incorporate cooling systems and advanced safety measures:
- Water Chillers: Used to cool the laser source, optical components, and cutting head to avoid heat buildup.
- Temperature Sensors: Continuously monitor the system to prevent overheating and ensure stable operation.
- Protective Enclosures: Enclose the laser cutting area to protect operators from exposure to the laser beam and contain fumes and debris.
- Safety Interlocks: Prevent the laser from operating if safety features are not engaged.
- Fume Extraction Systems: Remove smoke, dust, and harmful gases from the cutting area to ensure a clean working environment.
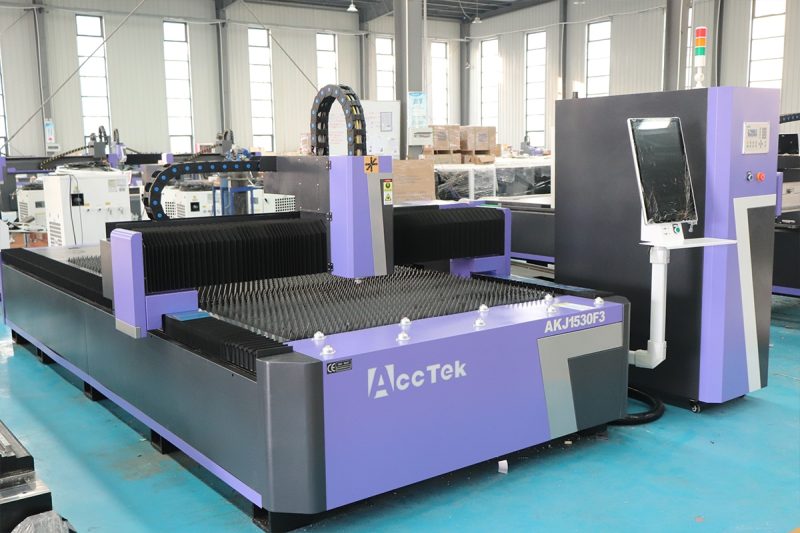
Components of a Fiber Laser Cutting Machine
Laser Source
The laser source is the heart of the machine, where the laser beam is generated. It determines the machine’s power and capability. Fiber laser sources use optical fibers doped with rare-earth elements such as ytterbium to amplify light and generate a powerful laser beam.
- Power Output: Fiber lasers typically range from 1500W to 30kW, with higher power levels used for cutting thicker materials.
- Beam Quality: A key factor affecting cut precision; better beam quality ensures finer cuts with less material waste.
- Lifespan: The diode modules used in fiber lasers have long lifespans, often exceeding 100,000 hours, reducing downtime and maintenance needs.
Fiber Optic Delivery System
The fiber optic delivery system transmits the laser beam from the laser source to the cutting head with minimal loss.
- Flexible Fiber Cables: These cables allow easy movement of the cutting head, increasing cutting precision and enabling complex cutting paths.
- Beam Integrity: Fiber delivery ensures the laser beam maintains consistent intensity and quality throughout the process.
- Low Maintenance: Unlike CO2 lasers, fiber optics do not require mirrors for beam guidance, reducing maintenance and alignment efforts.
Cutting Head
The cutting head is responsible for focusing the laser beam onto the material with high precision.
- Collimator and Focusing Lenses: The collimator aligns the laser beam, while the focusing lens concentrates it into a fine point for cutting.
- Nozzle: Directs the assist gas and laser beam onto the workpiece. Nozzles also help keep debris away from the optics.
- Height Sensor: Ensures that the correct distance between the nozzle and the material is maintained, optimizing the cut and preventing collisions.
- Protective Window: Shields the internal lenses from contamination, ensuring consistent performance.
Motion System
The motion system moves the cutting head or workpiece according to the cutting pattern programmed in the control system.
- Stepper Motors or Servo Motors: Provide precise and smooth motion along the X, Y, and Z axes.
- Guide Rails: Maintain stability and accuracy in the movement of the cutting head.
- Encoders and Feedback Systems: Track the exact position of the cutting head to ensure precise alignment and repeatability.
Control System
The control system manages the entire cutting process, ensuring smooth operation and precision.
- CNC Controller: Runs the machine’s software and executes cutting paths based on pre-programmed designs.
- User Interface: Allows operators to adjust parameters such as laser power, cutting speed, and assist gas flow.
- Real-Time Monitoring: Provides feedback during the cutting process, detecting errors and ensuring consistent performance.
- Nesting Software: Optimizes material usage by efficiently arranging multiple parts to be cut from the same sheet.
Assist Gas System
The assist gas system delivers gas through the nozzle to aid the cutting process.
- Oxygen: Speeds up the cutting of carbon steel by creating an exothermic reaction.
- Nitrogen: Prevents oxidation and creates a clean edge, ideal for stainless steel and aluminum.
- Air: A cost-effective option for cutting thin metals or non-metal materials.
- Flow Regulators and Pressure Sensors: Ensure the assist gas is delivered at the correct pressure for optimal cutting performance.
Cooling System
The cooling system prevents overheating by maintaining the optimal temperature of the laser source and optics.
- Water Chillers: Circulate cool water around the laser source and cutting head to dissipate heat.
- Temperature Control Sensors: Monitor system temperature and prevent overheating.
- Consistent Cooling: Ensures the machine operates at peak performance without interruption.
Protective Enclosure and Safety Systems
The protective enclosure and safety systems safeguard operators and ensure compliance with safety standards.
- Enclosures: Fully or partially enclose the cutting area to prevent accidental exposure to the laser beam.
- Interlock Systems: Automatically disable the laser if the enclosure is opened during operation.
- Emergency Stop Buttons: Allow operators to stop the machine immediately in case of emergencies.
- Fume Extraction System: Removes smoke, fumes, and debris generated during the cutting process.
- Laser Safety Glass: The Windows on the enclosure is made of glass that blocks harmful laser wavelengths, protecting operators.
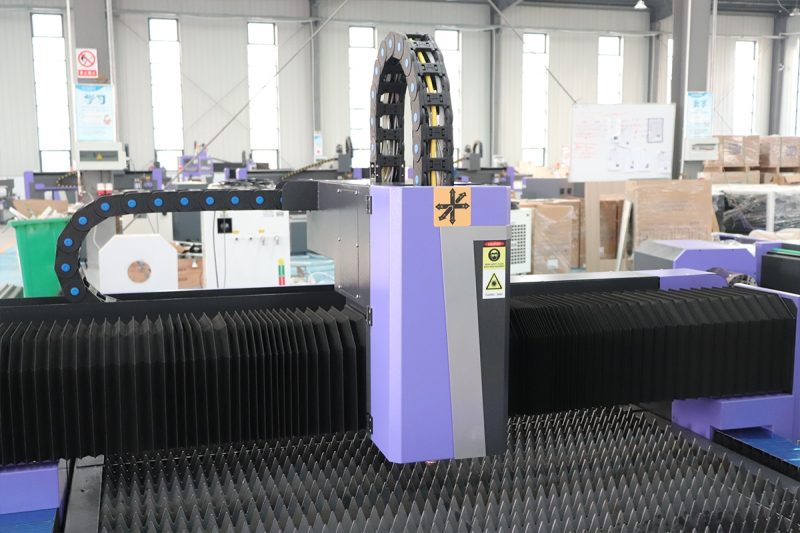
Advantages of Fiber Laser Cutting Machines
High Precision and Quality
Fiber laser cutting machines are known for delivering high precision, making them ideal for applications that require intricate and accurate cuts.
- Fine Beam Focus: The laser beam has a very small focal point, enabling precise cuts with minimal material waste.
- Minimal Heat Affected Zone (HAZ): Fiber lasers concentrate heat into a small area, reducing distortion and maintaining material integrity.
- Smooth and Clean Edges: The cutting process produces smooth edges with little to no burrs, often eliminating the need for secondary finishing operations.
High Cutting Speed
One of the standout features of fiber laser cutting machines is their speed.
- Faster Processing: Fiber lasers cut materials much faster than traditional cutting methods, particularly for thin metals.
- Increased Productivity: High cutting speeds reduce cycle times, allowing manufacturers to increase throughput and meet tight deadlines.
- Less Downtime: The faster processing speeds also reduce the time spent on each project, enhancing overall operational efficiency.
Low Maintenance
Fiber laser cutting machines require less maintenance compared to other laser systems, such as CO2 lasers.
- Solid-State Design: With no mirrors or lenses to adjust, fiber lasers have fewer components that wear out or require frequent maintenance.
- Long Lifespan: The laser diodes in fiber lasers have a long operational life, often exceeding 100,000 hours, reducing the need for replacement parts.
- Minimal Consumables: Fiber lasers use fewer consumables, leading to lower operating costs and simplified upkeep.
Versatility
Fiber laser cutting machines are highly versatile and capable of cutting a wide range of materials with ease.
- Wide Material Range: They can cut metals such as stainless steel, carbon steel, aluminum, brass, and copper. Their ability to cut reflective materials is a major advantage over other laser systems.
- Different Thicknesses: Fiber lasers can handle a broad range of material thicknesses, from thin metal sheets to thick plates, depending on the laser’s power.
- Adaptable for Various Applications: These machines can be used for tasks such as cutting, engraving, and perforating, offering flexibility across multiple industries.
Energy Efficiency
Fiber lasers are significantly more energy-efficient than other types of lasers, such as CO2 lasers.
- Higher Conversion Efficiency: Fiber laser generators can convert up to 30-35% of the electrical energy into laser light, compared to around 10-15% for CO2 laser tubes.
- Reduced Power Consumption: The higher energy efficiency leads to lower electricity usage, cutting down on operational costs.
- Less Heat Generation: Fiber lasers produce less heat than other laser types, which reduces the energy needed for cooling systems.
Compact Design
Fiber laser cutting machines are more compact and space-efficient than other laser systems.
- Smaller Footprint: The compact design allows for easier integration into production facilities with limited space.
- No Mirrors or Complex Optics: The fiber optic delivery system eliminates the need for bulky mirrors and lenses, simplifying the machine’s design.
- Easy to Relocate: Some models offer a modular design, allowing them to be moved more easily within the production facility if needed.
Stability and Reliability
Fiber laser cutting machines are known for their stability and reliability, ensuring consistent performance over long periods.
- Consistent Beam Quality: The fiber laser’s beam quality remains stable over time, ensuring uniform cutting results.
- Environmental Tolerance: Fiber lasers are less sensitive to environmental factors like dust, humidity, and temperature changes, which can affect the performance of other laser systems.
- Real-Time Monitoring: Advanced control systems provide real-time feedback, helping to detect any potential issues before they impact the cutting process.
Environmental Benefits
Fiber laser cutting machines offer several environmental advantages over traditional cutting methods.
- Lower Energy Usage: Higher energy efficiency reduces the machine’s carbon footprint, making it an environmentally friendly choice.
- Minimal Waste: The precision of fiber lasers results in less material waste, contributing to more sustainable production processes.
- Cleaner Operation: Unlike some other cutting methods, fiber lasers produce fewer harmful emissions and don’t require the use of toxic chemicals.
- Eco-Friendly Assist Gases: The use of nitrogen and air as assist gases in fiber laser cutting reduces environmental impact compared to other gas types.
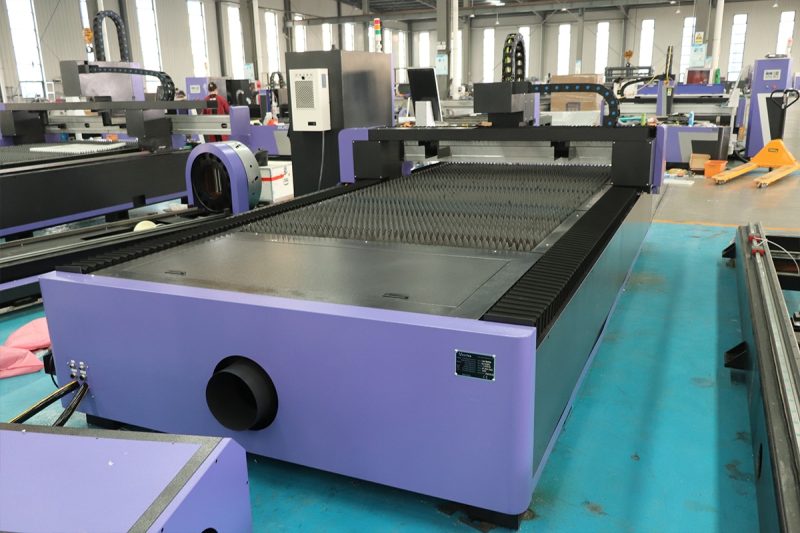
Applications of Fiber Laser Cutting Machines
Automotive Industry
The automotive industry relies heavily on fiber laser cutting machines for manufacturing components with precision and speed.
- Component Manufacturing: Fiber lasers cut complex parts like gears, exhaust systems, engine components, and body panels with high precision.
- Prototyping: Rapid prototyping of vehicle parts helps manufacturers test new designs efficiently.
- Customization: Fiber lasers enable precise cutting of aftermarket parts and custom automotive modifications.
Aerospace Industry
The aerospace sector demands high precision and reliable cutting for critical components. Fiber laser cutting machines excel in meeting these requirements.
- High-Performance Materials: Fiber lasers can cut aerospace-grade alloys like titanium and Inconel with minimal thermal distortion.
- Complex Components: Laser cutting allows for intricate designs used in aircraft structures, turbines, and exhaust systems.
- Weight Reduction: Fiber lasers facilitate lightweight component fabrication without compromising strength, essential for aerospace applications.
Electronics Industry
Fiber lasers are vital in the electronics industry, where small, intricate components are needed.
- Circuit Boards: Precision cutting and drilling of printed circuit boards (PCBs) improve the efficiency of electronic devices.
- Device Enclosures: Metal casings for smartphones, tablets, and laptops are often cut using fiber lasers.
- Microfabrication: Fiber lasers support the creation of tiny parts required for sensors and other electronic components.
Medical Industry
The medical sector benefits from the high precision of fiber laser cutting machines for producing instruments and devices.
- Surgical Instruments: Scalpel blades, scissors, and forceps are manufactured using fiber laser cutting.
- Medical Implants: Precision cutting of materials used in implants, such as bone plates and dental prosthetics.
- Medical Devices: Components for diagnostic equipment and other medical devices are cut with tight tolerances.
Jewelry and Arts
Fiber lasers offer the precision and flexibility required to create intricate designs in jewelry and decorative arts.
- Fine Jewelry: Fiber lasers cut precious metals like gold, silver, and platinum, enabling detailed designs.
- Customization: Engraving and cutting personalized jewelry pieces with names or intricate patterns.
- Artistic Creations: Laser cutting is used to create metal sculptures and intricate decorative elements.
Construction and Architecture
Fiber laser cutting machines are essential for producing structural and decorative elements in construction and architectural projects.
- Structural Components: Beams, supports, and brackets for buildings and infrastructure are cut with high accuracy.
- Decorative Panels: Laser-cut metal panels are used for facades, partitions, and interior design elements.
- Customized Fixtures: Production of architectural lighting fixtures, railings, and furniture.
Energy Sector
The energy industry relies on fiber laser cutting machines for fabricating essential components used in power generation and distribution.
- Oil and Gas Equipment: Cutting pipes, valves, and machinery components for oil and gas applications.
- Renewable Energy Systems: Production of parts for wind turbines, solar panel frames, and battery enclosures.
- Power Plants: Fabrication of boilers, turbines, and heat exchangers.
Signage and Advertising
The signage and advertising industry takes advantage of fiber laser-cutting machines to create eye-catching designs.
- Metal Signs: Precise cutting of letters and logos from stainless steel, aluminum, and other metals.
- Display Stands: Fabrication of custom display stands and promotional fixtures.
- Art Installations: Creation of large-scale metal artworks and installations for advertising and branding.
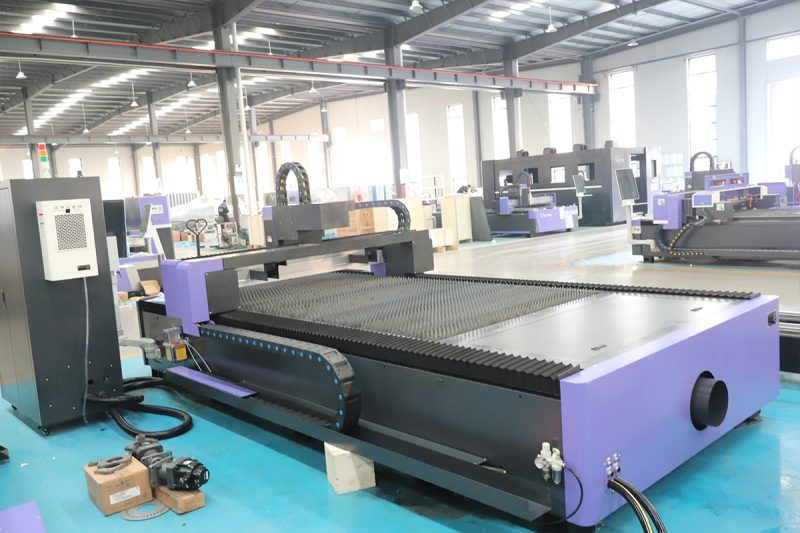
Factors to Consider When Choosing a Fiber Laser Cutting Machine
Laser Power
The laser power determines the machine’s ability to cut various materials and thicknesses efficiently.
- Material Type: Thicker and denser materials like steel require higher laser power (e.g., 4kW to 12kW).
- Production Volume: Higher power lasers offer faster cutting speeds, ideal for mass production environments.
- Future Needs: If you plan to expand into new materials or increase production, choosing a higher-power laser may provide flexibility.
Machine Size and Configuration
The size and configuration of the machine should match the type and volume of materials you plan to cut.
- Work Area Size: Ensure the cutting bed is large enough to accommodate your materials. Common sizes range from 1,500mm x 3,000mm to larger formats.
- Compact or Gantry Designs: Compact designs are suitable for smaller workshops, while gantry systems offer more flexibility for large-scale operations.
- Material Handling Options: Machines with automatic loading and unloading systems or exchange worktables improve efficiency.
Cutting Speed and Accuracy
The balance between speed and precision is essential for maximizing productivity without sacrificing quality.
- High-Speed Cutting: For industries requiring fast turnaround, look for machines with rapid cutting capabilities for thin materials.
- Accuracy Requirements: If your products demand intricate details or tight tolerances, prioritize machines with precise control systems.
- Repeatability: Machines with stable motion systems and advanced sensors ensure consistent results over time.
Software and Control Systems
Advanced software plays a critical role in operating the machine efficiently and ensuring high-quality output.
- User-Friendly Interface: Choose a machine with an intuitive control panel that reduces operator errors.
- Nesting Software: Features that optimize material usage help reduce waste and improve profitability.
- Remote Monitoring and Diagnostics: Systems with remote access allow operators and technicians to monitor performance and detect issues in real-time.
- CAD/CAM Compatibility: Ensure the machine supports the software you use for design and production.
Maintenance and Support
Ongoing maintenance and manufacturer support are crucial for minimizing downtime and ensuring long-term performance.
- Reliable Manufacturer Support: Choose a reputable manufacturer like AccTek Laser, known for providing excellent technical assistance and after-sales service.
- Service and Maintenance Plans: Look for machines with preventive maintenance programs to extend operational life.
- Training Programs: Access to operator training ensures your staff can use the machine efficiently and safely.
Cost Considerations
The cost of the machine should align with your budget and expected return on investment (ROI).
- Initial Investment: Machines with higher power and advanced features may have higher upfront costs.
- Operating Costs: Consider energy consumption, maintenance, and consumables when evaluating the machine’s overall cost.
- ROI Analysis: Assess how the machine will impact production efficiency, product quality, and profitability over time.
Safety Features
Safety is paramount when working with powerful laser machines, and compliance with safety standards is essential.
- Protective Enclosures: Ensure the machine has fully enclosed cutting areas to protect operators from laser exposure.
- Interlock Systems: Safety interlocks prevent operation if the enclosure is opened during use.
- Emergency Stop Functions: Machines should have accessible emergency stop buttons to quickly halt operation in case of emergencies.
- Fume Extraction Systems: Proper ventilation ensures a safe working environment by removing harmful fumes and particles.
Customization and Upgrades
Customization options allow you to tailor the machine to meet your specific production needs.
- Modular Design: Machines with modular components can be upgraded easily as your production requirements evolve.
- Automation Integration: Consider systems that allow integration with robotic arms or material handling systems to increase efficiency.
- Additional Features: Machines with extra functions like tube-cutting capabilities or dual worktables offer more flexibility.
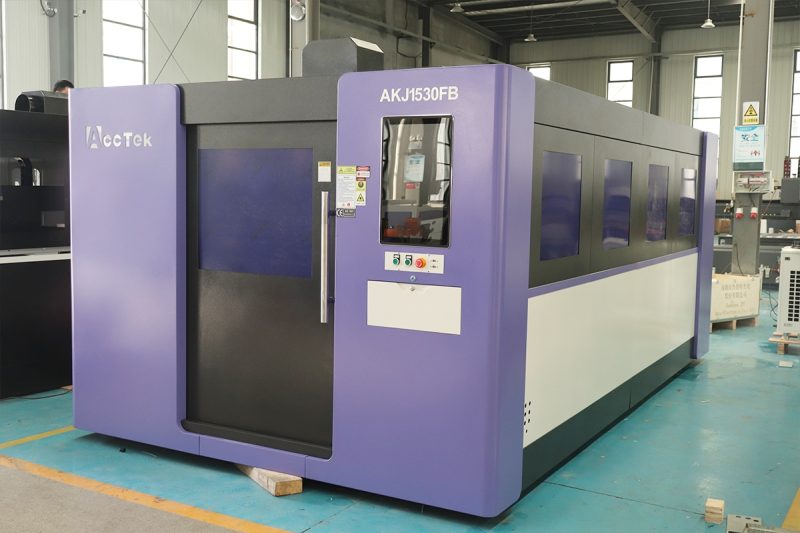
Maintenance and Safety Considerations
Maintenance Practices
Regular maintenance is critical to keeping the machine running efficiently and preventing unexpected downtime.
- Cleaning Optics: Regularly inspect and clean lenses, mirrors, and protective windows to prevent dust buildup and maintain beam quality.
- Alignment Checks: Ensure that the laser beam is properly aligned to avoid cutting errors and performance issues.
- Lubricating Moving Parts: Apply the recommended lubricants to guide rails, motors, and other moving parts to prevent friction and wear.
- Software Updates: Keep the control system’s software up to date for optimal performance and access to the latest features and security patches.
- Scheduled Inspections: Perform routine inspections to identify worn parts, such as belts or bearings, before they fail.
Consumables Management
Effective management of consumables helps maintain cutting quality and reduces operational costs.
- Nozzles and Lenses: Regularly check and replace nozzles, lenses, and protective windows to avoid contamination and maintain beam focus.
- Assist Gas Supply: Monitor the levels of assist gases (oxygen, nitrogen, or air) to ensure smooth operation without interruptions.
- Filters and Extraction Systems: Replace filters in fume extraction systems to maintain air quality and prevent the buildup of harmful substances.
- Cooling Fluids: Monitor the coolant levels and replace the cooling fluid according to the manufacturer’s guidelines to prevent overheating.
Safety Protocols
Strict adherence to safety protocols is essential when operating high-powered laser equipment.
- Personal Protective Equipment (PPE): Operators should wear appropriate laser safety glasses and protective clothing.
- Laser Enclosures: Ensure the protective enclosure is closed and secured during operation to prevent laser exposure.
- Emergency Stop Functions: Familiarize operators with the machine’s emergency stop buttons and ensure they are easily accessible.
- Operator Training: Provide comprehensive training for all users to ensure they understand safety protocols and operating procedures.
- Fume Extraction and Ventilation: Ensure the fume extraction system is functioning properly to prevent inhalation of harmful gases.
Regulatory Compliance
Fiber laser cutting machines must comply with local and international safety and environmental regulations.
- Laser Safety Standards: Ensure compliance with standards such as ANSI Z136.1, which outlines safety requirements for laser systems.
- Occupational Health Regulations: Adhere to guidelines from agencies such as OSHA (Occupational Safety and Health Administration) to ensure workplace safety.
- Environmental Regulations: Dispose of waste materials, such as used filters and coolants, by environmental regulations.
- Machine Documentation: Maintain up-to-date records of maintenance, safety checks, and operator training to demonstrate compliance during audits.
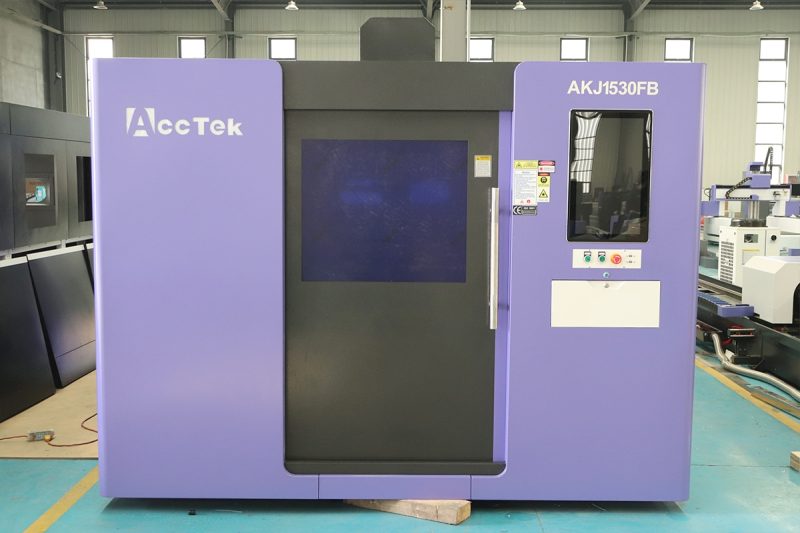
Summary
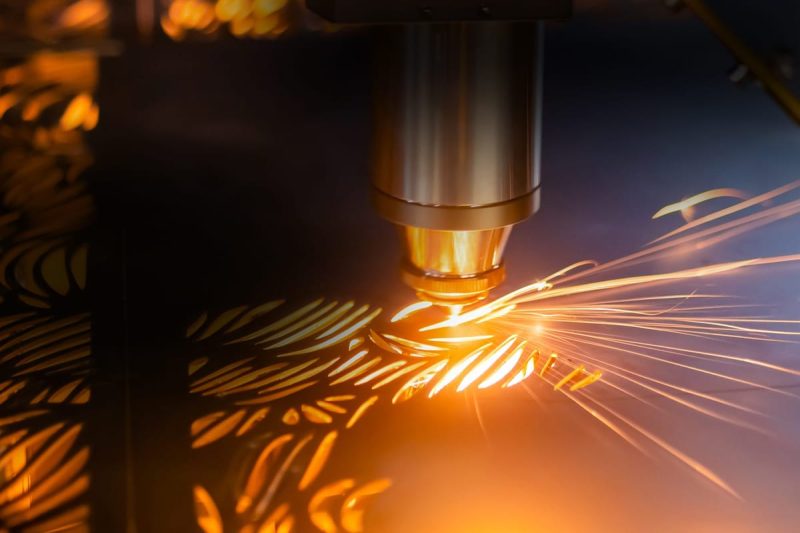
Get Laser Cutting Solutions
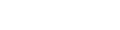
- [email protected]
- [email protected]
- +86-19963414011
- No. 3 Zone A, Lunzhen Industrial Zone,Yucheng City , Shandong Province.