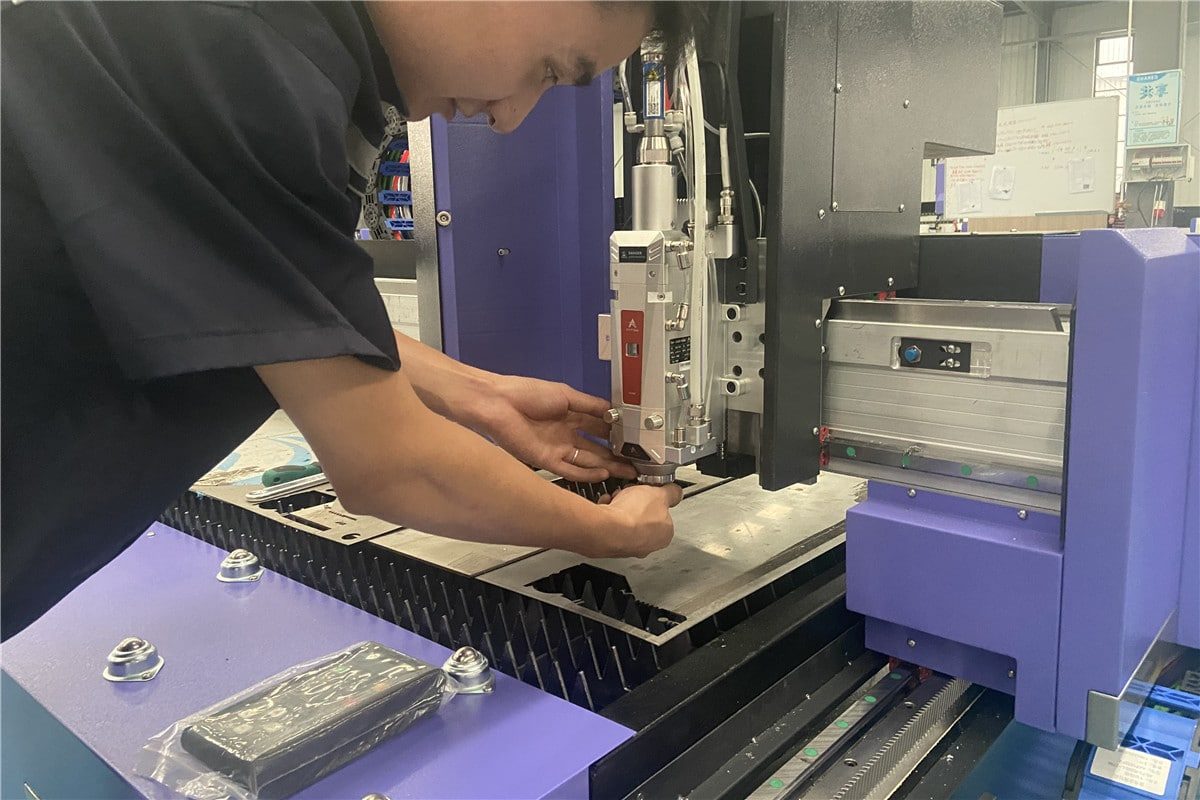
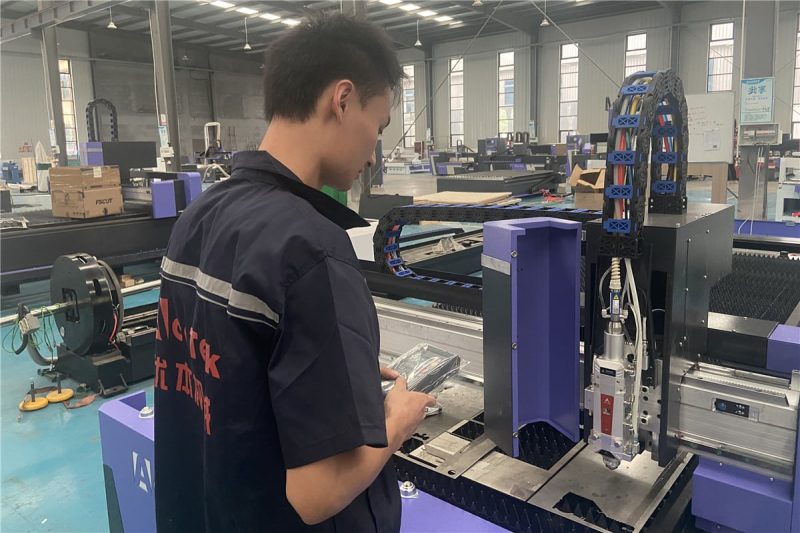
Fiber laser cutting machine operation precautions
Correct operation is the prerequisite to ensure the stable operation of the machine. The following points are the preparations before starting the fiber laser cutting machine. Users must strictly follow these safety precautions to avoid personal injury or machine damage.
- Make sure that all parts of the machine are grounded completely and reliably. It is strictly forbidden to start the machine without a ground wire.
- Every time the machine is turned on, the water pump must be checked for lack of water. Do not start work without water.
- Check whether the cooling water circulation is normal and ensure that the water quality is clean and free of debris. It is recommended to use pure water and replace circulating water every month.
- Before starting the machine, carefully check the pressure of the laser auxiliary gas. When the air pressure is insufficient, it needs to be replaced in time.
- Check whether there are leaks in the air pipe interface of the laser cutting head and the cooling water to ensure the normal supply of auxiliary gas and cooling water.
- It is strictly prohibited to keep flammable and explosive items near the laser cutting machine to prevent fire.
- During the operation of the machine, the operator is strictly prohibited from leaving without authorization to avoid unnecessary losses.
- To ensure the normal operation of the machine, operators need to be trained before taking up their posts.
- During the operation of the machine, the operator needs to observe the working condition of the machine at any time. When the plate cannot be cut through, slag discharges, burrs occur, or the machine makes abnormal sounds, the machine should be stopped and inspected to troubleshoot the fault to avoid serious damage to machine parts.
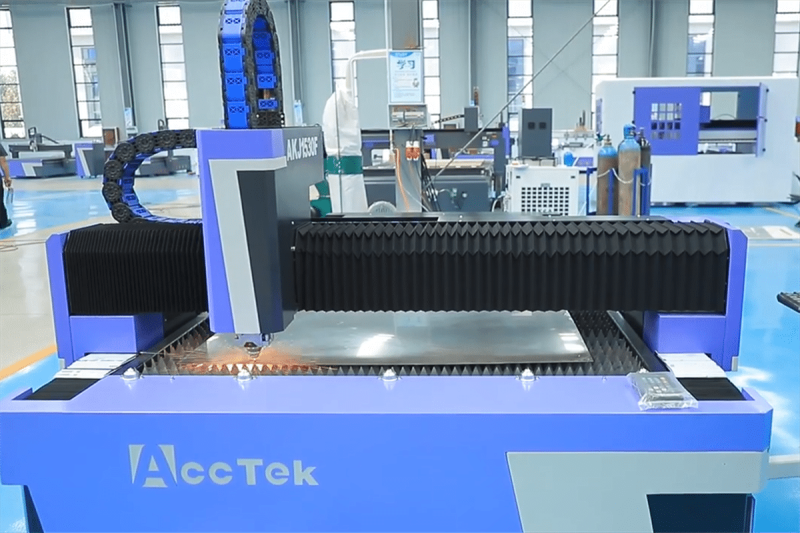
Daily cleaning of fiber laser cutting machine
To extend the service life of the fiber laser cutting machine, the simplest maintenance method is to do daily cleaning. Operators must clean the machine after each job. Although this is a simple task, it can prevent serious problems in the future.
- When you’re done cutting for the day, empty any drawers containing waste. If workers do not clean the drawer after using it, the drawer will eventually become stuck, which will greatly affect the operation of the workbench.
- Workers must clean the work surface after cutting. Only by clearing the debris on the table can you ensure that the next time you place the cutting board, it will be flat and not tilted.
- Please check whether the laser cutting head is clean. When contaminants are found, the operator can use a clean towel to clean the laser cutting head. The laser cutting head is the core component of the machine. If it fails, it will directly affect the cutting effect and cause economic losses. Therefore, workers should clean the outside of the laser cutting head, nozzles, connecting cables, and protective windows. A clean laser cutting head helps achieve the most precise laser cutting.
- It is also important to keep the environment around the machine clean. Scrap materials scattered around machines are safety hazards, and workers can trip over them and injure themselves. Therefore, after completing a day’s cutting tasks, clean and inspect the work area to ensure a safe and tidy workplace.
- Fan cleaning. After the machine is used for a long time, a large amount of dust will accumulate in the fan, which not only makes the fan make a lot of noise but is also not conducive to the heat dissipation of the machine. Therefore the fan should be cleaned regularly. First, turn off the power, remove the air inlet duct and air outlet duct from the fan, and clean them. Then turn the fan upside down and clean the blades until they are clean.
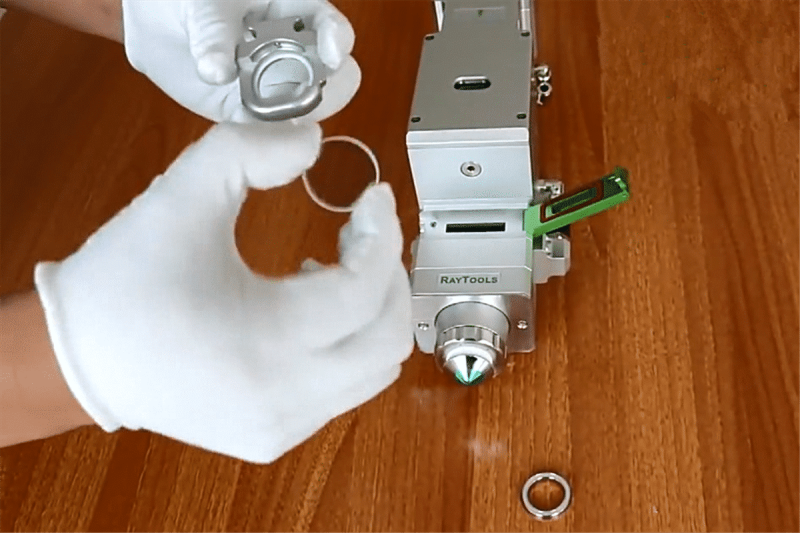
Optical lens maintenance
The optical lens of the fiber laser cutting machine is located in the laser cutting head. The protective lens is used to block spatter generated by metal cutting and protect optical components such as focusing lenses and electronic sensors. As a consumable product, protective lenses can extend their service life through regular cleaning, thereby reducing loss costs. However, when the protective lens is damaged, it needs to be replaced in time to ensure that other optical components are not damaged and to ensure the quality of laser cutting. To extend the service life of optical lenses, you can refer to the following maintenance methods:
- The protective lens of the laser cutting machine is easily affected by smoke and dust, and it is recommended to clean it once a day.
- Do not directly touch the surface of optical devices such as the focusing lens, protective lens, and QBH laser head to avoid scratching or corroding the lens.
- When the surface of the lens is stained with dust, dirt, and water vapor, it will seriously affect the use of the lens, and the lens should be cleaned in time.
- It is strictly prohibited to use water and detergents to clean the lens surface. Because the surface of the lens is coated with a special film, water, and detergent will damage the surface of the lens. Lenses can be cleaned using a cotton swab dipped in alcohol.
- Do not place the lens in a dark and humid place, otherwise it will cause the lens surface to age.
- When installing or replacing the reflector, focusing mirror, and protective mirror, do not use excessive force, otherwise, the lens may be deformed and the beam quality may be affected.
- Optical lenses should be stored properly to keep the quality of the lenses intact. The storage environment temperature is 10~30℃. Do not put the lenses in the freezer or similar environment, otherwise, frost will condense on the lenses when they are taken out, thus damaging the lenses.
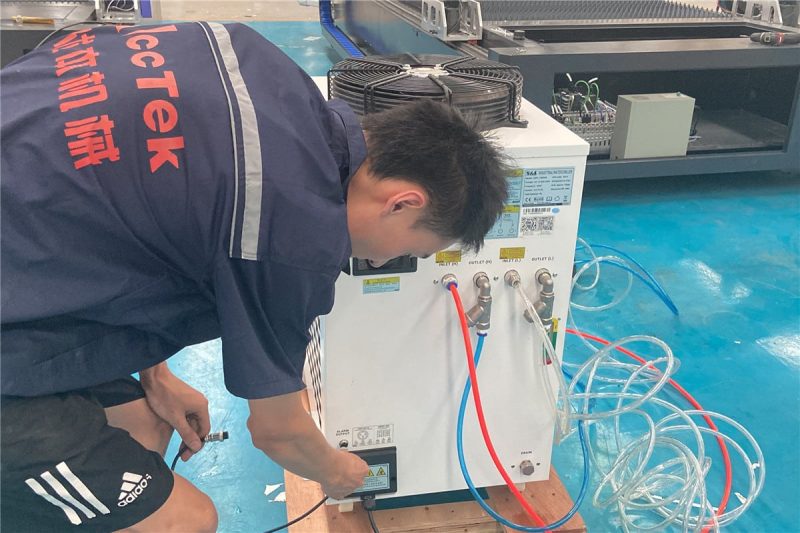
Water chiller maintenance
The water chiller is responsible for cooling the laser generator and laser cutting head and is an important part of the fiber laser cutting machine. To ensure the stable operation of the fiber laser cutting machine, we also need to perform regular maintenance on the chiller. If you encounter a fault, be sure to ask professional technicians to repair it, and remember not to disassemble the machine by yourself. The following aspects should be paid attention to in the daily maintenance of the fiber laser cutting machine chiller:
- Clean the heat sink regularly. The cleaning method is as follows: carefully scrub the heat sink with a brush, and then blow clean with compressed air.
- Dust the condenser regularly.
- Check the water level of the chiller regularly and add pure water in time.
- Check whether the joints in the chiller system are leaking and whether the pipes are aging and replace them in time.
- If the quality of the cooling water becomes poor or turbid, all the deteriorated cooling water should be drained out in time and replaced with new cooling water.
- Remove impurities from the filter element. If the filter element is damaged, it should be replaced in time.
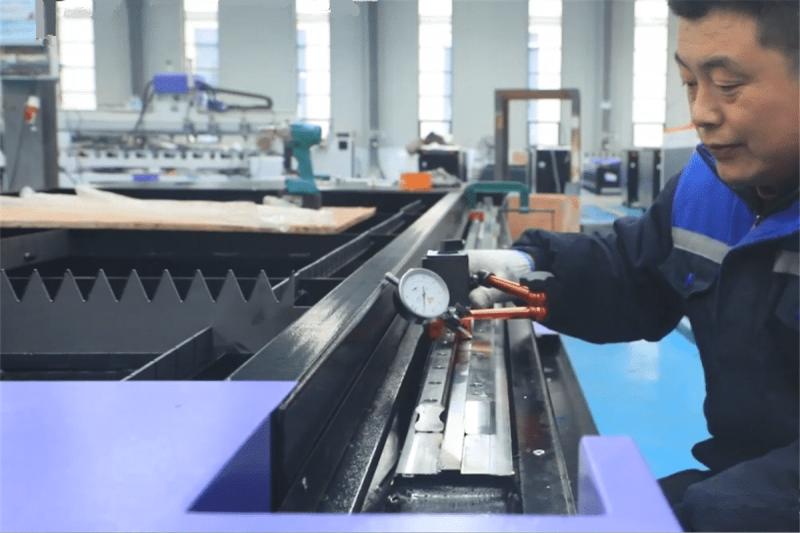
Guide rail maintenance
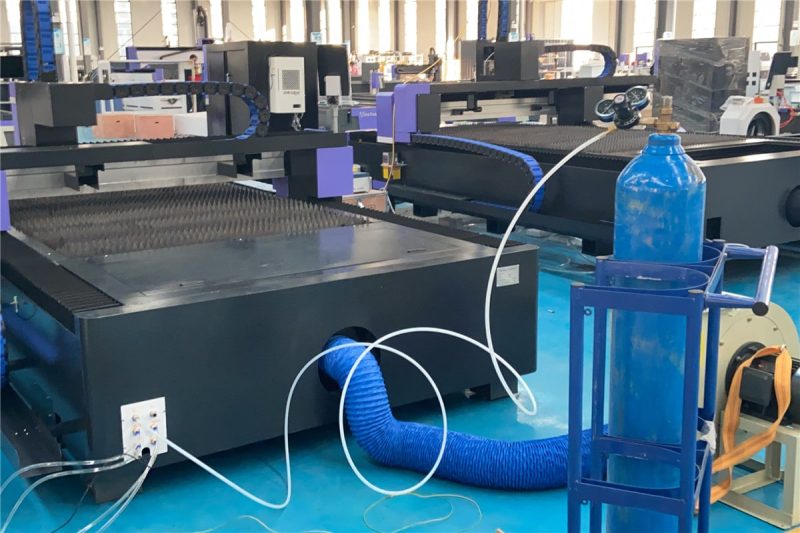
Check of auxiliary gas
Summarize
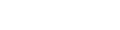
- [email protected]
- [email protected]
- +86-19963414011
- No. 3 Zone A, Lunzhen Industrial Zone,Yucheng City , Shandong Province.