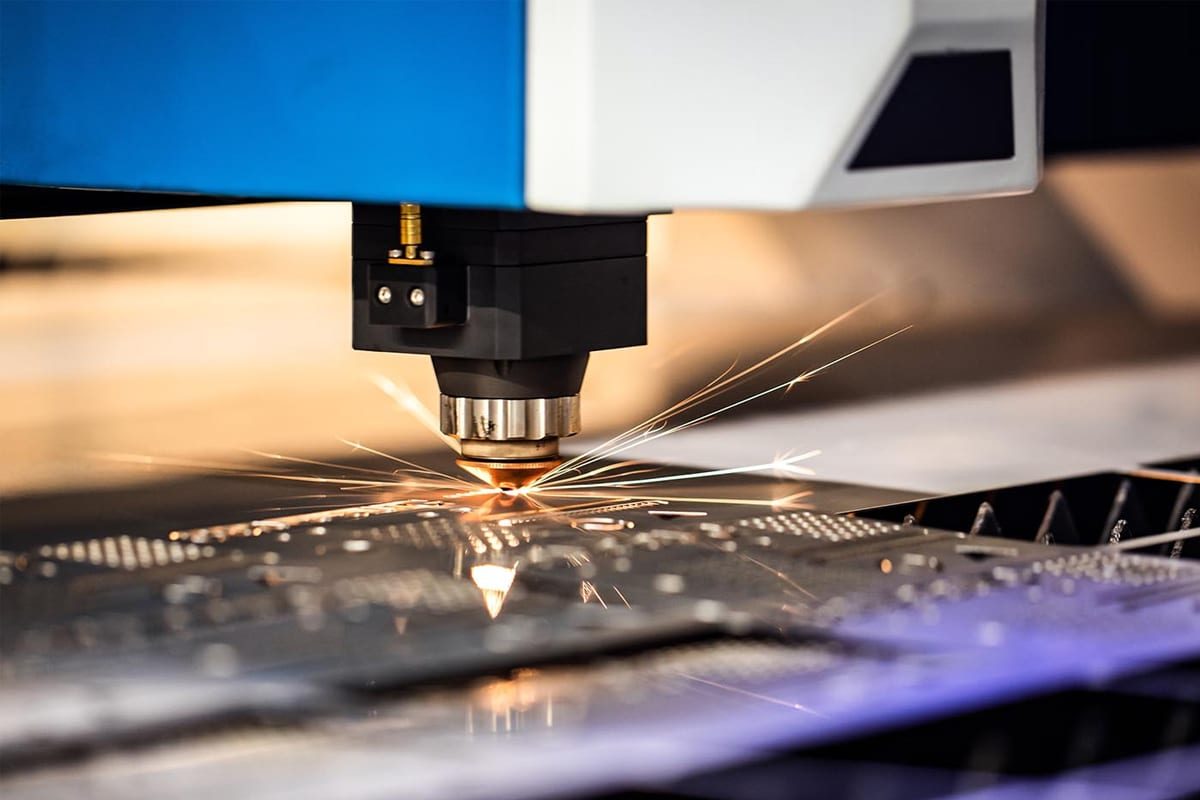
Fiber Laser Cutting VS Plasma Cutting
In the dynamic world of metal fabrication, choosing the right cutting technology helps achieve precision, efficiency, and cost-effectiveness. Fiber laser cutting and plasma cutting are two prominent methods that have revolutionized the industry. This article provides a comprehensive comparison of fiber laser cutting and plasma cutting, exploring their principles, advantages, limitations, and ideal applications. By delving into the specifics of each method, we aim to equip you with the knowledge to make informed decisions that align with your manufacturing needs and enhance your operational capabilities.
Table of Contents
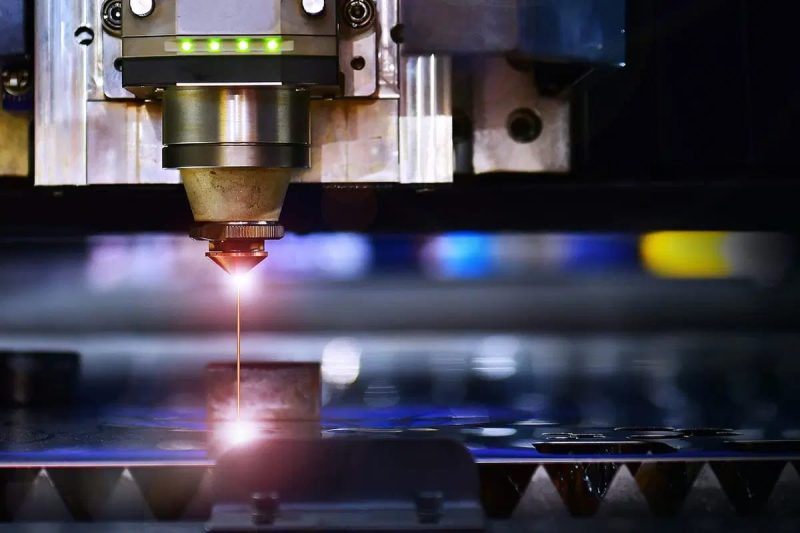
What is Fiber Laser Cutting?
Definition and Basic Principles
Fiber laser cutting is a modern manufacturing process that utilizes a high-powered fiber laser beam to cut and engrave materials with exceptional precision and speed. The technology is based on the amplification of light within optical fibers doped with rare-earth elements, resulting in a focused laser beam capable of melting, burning, or vaporizing material in a controlled manner. This method is widely recognized for its efficiency in cutting metals and offers superior edge quality compared to traditional cutting techniques.
How Fiber Lasers Work
At the core of fiber laser cutting is the fiber laser generator itself, which operates on the following principles:
- Laser Generation: A seed laser emits a low-power beam of light, which is then introduced into a fiber optic cable doped with rare-earth elements like ytterbium.
- Amplification: As the light travels through the doped fiber, it interacts with the rare-earth ions, causing them to emit additional photons of the same wavelength and phase—a process known as stimulated emission. This amplifies the light into a powerful laser beam.
- Beam Delivery: The amplified laser light is transmitted through flexible fiber optic cables to the cutting head without the need for complex mirrors or lenses.
- Focusing the Beam: The cutting head contains a lens that focuses the laser beam onto a very small spot on the material’s surface, achieving extremely high power density.
- Material Interaction: The concentrated energy melts or vaporizes the material at the focal point. Assist gases like nitrogen or oxygen are often used to blow away molten material, enhancing the cutting process and preventing oxidation.
- Controlled Movement: A computer numerical control (CNC) system directs the movement of the cutting head or the workpiece, following precise patterns to achieve the desired cut shapes.
Advantages
- High Precision and Quality: Fiber lasers produce a small focal diameter and high energy density, resulting in fine, clean cuts with minimal thermal distortion.
- Efficiency: They offer faster cutting speeds, especially on thin to medium-thickness materials, increasing productivity.
- Versatility: Capable of cutting a wide range of metals, including steel, stainless steel, aluminum, brass, and copper.
- Low Maintenance: Fiber laser generators have a solid-state design with no moving parts or mirrors in the light-generating source, reducing maintenance requirements and downtime.
- Energy Efficiency: They consume less power compared to traditional CO2 laser cutting machines and plasma cutting systems, leading to lower operational costs.
- Long Operational Life: The diodes in fiber lasers have a long lifespan, often exceeding 100,000 hours of operation.
- Compact Design: The fiber optic delivery system allows for a more compact machine footprint, saving valuable floor space.
Disadvantages
- High Initial Investment: The advanced technology and components result in higher upfront costs compared to other cutting methods like plasma cutting.
- Material Limitations: Fiber lasers are less effective on thicker materials (typically over 25 mm for steel) and are not suitable for non-metallic materials like wood or plastics.
- Reflective Material Challenges: Cutting highly reflective metals like copper and brass can pose challenges due to potential back-reflection damaging the laser source, though modern machines have features to mitigate this risk.
- Technical Expertise Required: Operators need specialized training to handle the equipment and optimize cutting parameters for different materials.
Applications
Fiber laser cutting is employed across various industries due to its precision and efficiency:
- Aerospace: For cutting complex components that require high precision and minimal thermal impact.
- Automotive: Manufacturing of parts like body panels, engine components, and intricate designs.
- Electronics: Cutting of small, precise parts used in electronic devices and circuitry.
- Medical Devices: Production of surgical instruments and medical equipment that demand high accuracy.
- Metal Fabrication: General fabrication work involving custom metal parts, enclosures, and structural components.
- Jewelry Making: Crafting intricate designs in precious metals with high precision.
- Signage and Decorative Arts: Creating detailed metal signs, art pieces, and decorative elements.
By leveraging the strengths of fiber laser cutting, manufacturers can achieve superior quality, reduce production times, and expand their capabilities to meet the demanding needs of modern industries.
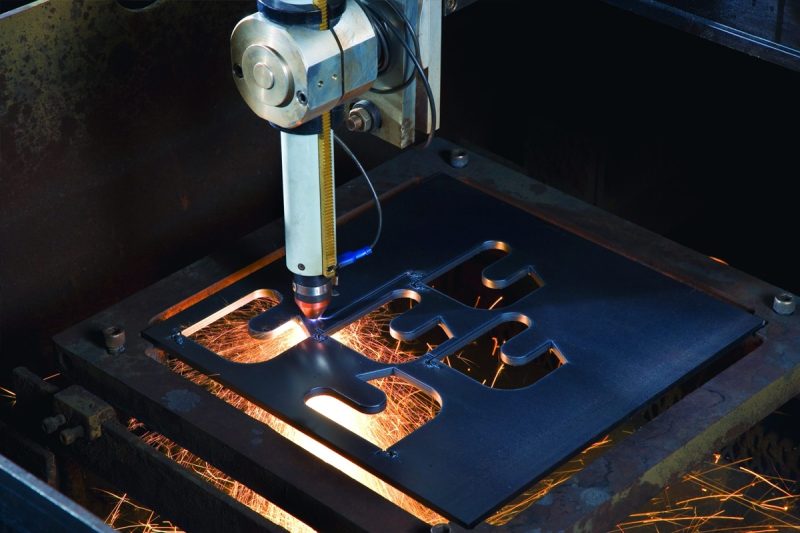
What Is Plasma Cutting?
Definition and Basic Principles
Plasma cutting is a thermal cutting process that employs a high-velocity jet of ionized gas, known as plasma, to melt and sever electrically conductive materials. The process involves generating an electrical arc that passes through a gas, transforming it into plasma capable of reaching temperatures up to 30,000℃ (54,000℉). This intense heat melts the metal, while the kinetic energy of the high-velocity gas removes the molten material, creating a clean cut. Plasma cutting is widely used for its efficiency in cutting thick metals and its ability to work on a variety of conductive materials.
How Plasma Cutting Works
The plasma-cutting process operates on the following principles:
- Initiation of the Arc: An electrical power source creates a direct current (DC) arc between an electrode (negative charge) inside the plasma torch and the workpiece (positive charge).
- Gas Ionization: Compressed gas (such as air, nitrogen, argon, or oxygen) is forced through a narrow nozzle at high speed into the arc. The intense energy of the arc ionizes the gas, converting it into plasma.
- Formation of Plasma Jet: The plasma exits the nozzle as a focused, high-velocity jet of ionized gas. The narrow nozzle constricts the arc, increasing its temperature and velocity.
- Material Melting: The plasma jet reaches extremely high temperatures, melting the material at the point of contact.
- Material Removal: The high-velocity plasma and secondary gases blow the molten metal away from the cut, leaving a narrow kerf.
- Controlled Movement: The plasma torch is guided along the desired cutting path, either manually or via a computer numerical control (CNC) system, to achieve precise cuts.
Advantages
- Capability to Cut Thick Materials: Plasma cutting excels at cutting thick metal plates, often up to 80 mm (3 inches) or more, depending on the power of the plasma system.
- Versatility: Effective on all electrically conductive metals, including carbon steel, stainless steel, aluminum, copper, brass, and cast iron.
- High Cutting Speeds: Faster than oxy-fuel cutting for materials less than 50 mm thick, improving productivity in metal fabrication tasks.
- Lower Initial Investment: Generally lower upfront costs compared to fiber laser cutting systems, making it accessible for small to medium-sized businesses.
- Ease of Use: Simpler setup and operation, with less technical expertise required compared to laser cutting systems.
- Portability: Plasma cutting equipment can be relatively compact and portable, suitable for on-site repairs and construction work.
Disadvantages
- Lower Precision: Plasma cutting produces a wider kerf (cut width) and less precise cuts compared to fiber laser cutting, which may require additional finishing.
- Heat-Affected Zone (HAZ): Generates a larger HAZ, which can alter the metal’s properties near the cut edge and may lead to warping or distortion.
- Rougher Edge Quality: Edges may have more dross (residual slag) and roughness, necessitating secondary processing for applications requiring high-quality finishes.
- Limited Fine Detail Capability: Not ideal for cutting intricate patterns or small holes due to the size of the plasma arc and kerf width.
- Higher Energy Consumption: Generally consumes more electricity than fiber laser systems, leading to increased operational costs over time.
- Safety Hazards: Produces intense light, noise, and fumes, requiring appropriate safety measures like eye protection, hearing protection, and proper ventilation.
Applications
Plasma cutting is widely used in industries and applications where cutting of thick, conductive metals is required:
- Construction and Infrastructure: Cutting structural steel components for buildings, bridges, and infrastructure projects.
- Shipbuilding: Fabricating large steel sections for ships and offshore platforms.
- Automotive Repair and Manufacturing: Cutting and repairing chassis components, frames, and body parts.
- Metal Fabrication Shops: General fabrication of heavy-duty metal parts, custom assemblies, and repair work.
- Manufacturing of Agricultural and Heavy Equipment: Producing components for tractors, excavators, and industrial machinery.
- Scrap Metal Recycling: Cutting large metal items into smaller pieces for recycling purposes.
- Maintenance and Repair Operations: On-site cutting and modification of metal structures and equipment in various industries.
Understanding the fundamentals of plasma cutting allows manufacturers to assess its suitability for their specific needs. While plasma cutting offers advantages in cutting thick materials and lower initial costs, it may not match the precision and edge quality provided by fiber laser cutting systems.
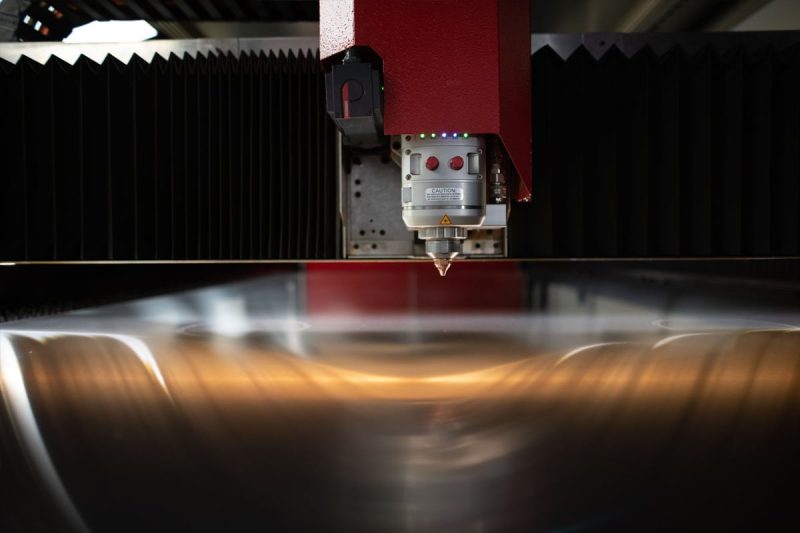
Comparison Between Fiber Laser Cutting and Plasma Cutting
When deciding between fiber laser cutting and plasma cutting, it’s essential to understand how each method performs across various criteria. Below is a detailed comparison that highlights the strengths and weaknesses of both technologies.
Cutting Quality
Fiber Laser Cutting
- Edge Quality: Produces superior edge quality with smooth, clean cuts and minimal dross (residual slag).
- Heat-Affected Zone (HAZ): Smaller HAZ due to the concentrated laser beam, reducing the risk of thermal distortion.
- Precision Cuts: Ideal for intricate designs and tight tolerances, making it suitable for applications requiring high precision.
Plasma Cutting
- Edge Quality: Generally produces rougher edges with more dross, which may require secondary finishing processes.
- Heat-Affected Zone (HAZ): Larger HAZ due to the broader plasma arc, increasing the potential for warping and distortion.
- Coarse Cuts: Better suited for less detailed work where ultra-fine precision is not critical.
Cutting Speed
Fiber Laser Cutting
- Thin to Medium Materials: Offers faster cutting speeds on thin to medium-thickness metals (typically up to 25 mm for steel).
- Efficiency: High-speed processing increases productivity and reduces lead times.
Plasma Cutting
- Thick Materials: Generally faster when cutting thicker materials (above 25 mm), where the laser’s efficiency decreases.
- Speed vs. Quality Trade-off: While capable of high speeds, increased speed may further reduce cut quality.
Material Compatibility
Fiber Laser Cutting
- Metallic Materials: Excels at cutting a variety of metals including carbon steel, stainless steel, aluminum, brass, and copper.
- Non-Metals: Not suitable for cutting non-metallic materials due to the laser’s wavelength absorption characteristics.
- Reflective Metals: Modern fiber lasers can handle reflective metals like copper and brass with appropriate technology to prevent back-reflection damage.
Plasma Cutting
- Conductive Metals: Can cut all electrically conductive metals, including steel, stainless steel, aluminum, copper, brass, and cast iron.
- Non-Metals: Ineffective on non-conductive materials like plastics, glass, or wood.
Thickness Capabilities
Fiber Laser Cutting
- Optimal Thickness Range: Highly efficient on thin to medium-thickness materials, typically up to 25 mm for steel.
- Limitations on Thick Materials: Cutting thicker materials may require significantly more power and can result in decreased cut quality and speed.
Plasma Cutting
- Thick Material Cutting: Capable of cutting thicker materials effectively, often up to 80 mm or more depending on the plasma system’s power.
- Thin Materials: Can cut thin materials but may cause excessive heat input, leading to warping or reduced cut quality.
Precision and Accuracy
Fiber Laser Cutting
- High Precision: Achieves extremely tight tolerances and intricate cuts with accuracy levels often within ±0.1 mm.
- Small Kerf Width: The laser beam’s narrow focus results in a minimal kerf, preserving material and allowing for detailed designs.
Plasma Cutting
- Moderate Precision: Suitable for applications where precision is less critical, with tolerances typically within ±0.5 mm to ±1 mm.
- Wider Kerf Width: The plasma arc produces a wider cut, which can limit the ability to cut fine features or closely spaced components.
Operational Costs
Fiber Laser Cutting
- Initial Investment: Higher upfront costs due to advanced technology and equipment.
- Operating Costs: Lower ongoing costs are attributed to higher energy efficiency and reduced consumable usage.
- Energy Consumption: More energy-efficient, leading to lower electricity costs over time.
Plasma Cutting
- Initial Investment: Lower purchase price makes it accessible for businesses with budget constraints.
- Operating Costs: Higher operational costs due to greater energy consumption and frequent replacement of consumables like electrodes and nozzles.
- Consumables: Ongoing expenses for consumables can add up, increasing the total cost of ownership.
Maintenance
Fiber Laser Cutting
- Low Maintenance Requirements: Solid-state design with fewer moving parts reduces maintenance needs.
- Component Longevity: Key components like diodes have a long operational life, often exceeding 100,000 hours.
- Downtime: Less frequent maintenance leads to higher machine availability and productivity.
Plasma Cutting
- Higher Maintenance Needs: Consumable parts like electrodes and nozzles require regular replacement due to wear.
- Machine Wear and Tear: The intense heat and electrical arcs can lead to more frequent servicing and parts replacement.
- Downtime: Increased maintenance can result in more machine downtime, affecting productivity.
Safety Considerations
Fiber Laser Cutting
- Laser Radiation: Requires strict safety measures to protect operators from laser exposure, including protective eyewear and enclosures.
- Fume Extraction: Cutting metals can produce fumes and require proper ventilation or extraction systems.
- Noise Levels: Generally quieter operation compared to plasma cutting.
Plasma Cutting
- Electric Shock Risk: High voltage and current pose a risk of electric shock if safety protocols are not followed.
- UV and Infrared Radiation: Generates intense UV and IR radiation, necessitating protective clothing and eye protection.
- Fume and Noise Emission: Produces significant fumes and high noise levels, requiring hearing protection and effective ventilation systems.
Environmental Impact
Fiber Laser Cutting
- Energy Efficiency: More energy-efficient, reducing the overall carbon footprint of operations.
- Reduced Emissions: Generates fewer fumes and emissions compared to plasma cutting.
- Assist Gases: Uses inert gases like nitrogen, which have minimal environmental impact.
Plasma Cutting
- Higher Energy Consumption: Less efficient energy usage contributes to a larger environmental footprint.
- Fume Generation: Produces more fumes and particulate matter, which can affect air quality if not properly managed.
- Consumable Waste: Frequent replacement of consumables adds to waste generation.
By examining these critical factors, it becomes evident that both fiber laser cutting and plasma cutting have distinct advantages and limitations. Fiber laser cutting is the preferred choice for applications demanding high precision, superior cut quality, and efficiency on thin to medium-thickness materials. In contrast, plasma cutting is advantageous for cutting thicker materials where ultra-fine precision is less critical and initial investment costs are a consideration.
Choosing the right technology depends on factors such as the types of materials being processed, the required thickness range, desired cut quality, operational cost considerations, and environmental and safety priorities. By leveraging the strengths of each method, manufacturers can optimize their production processes, reduce costs, and improve overall product quality.
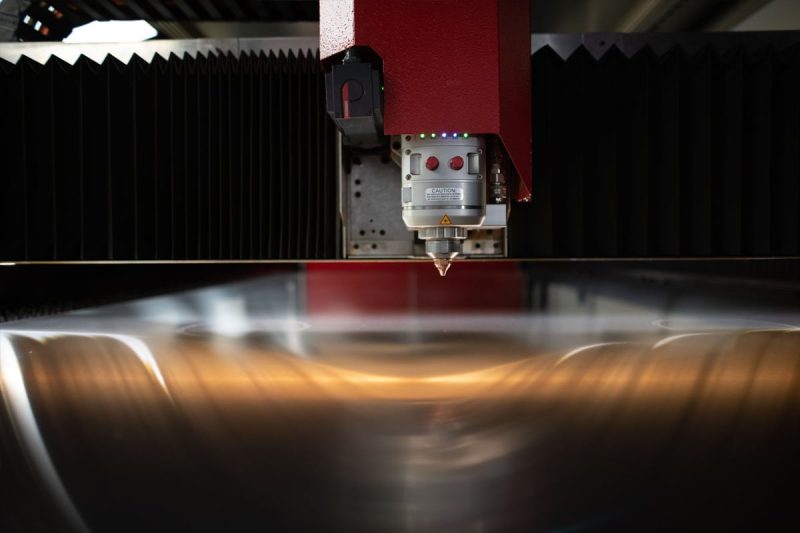
Choosing Between Fiber Laser and Plasma Cutting
Selecting the appropriate cutting technology for your manufacturing needs is a critical decision that can significantly impact your production efficiency, product quality, and overall operational costs. Both fiber laser cutting and plasma cutting offer unique advantages and are suited for different applications.
Factors to Consider
Material Type and Thickness
- Material Compatibility: Fiber laser cutting is ideal for metals like carbon steel, stainless steel, aluminum, brass, and copper. Plasma cutting is effective on all electrically conductive metals but may struggle with non-ferrous metals in terms of cut quality.
- Thickness Capabilities: Fiber lasers excel at cutting thin to medium materials (up to 25 mm), offering high precision and speed. Plasma cutters handle thicker materials (up to 80 mm or more) effectively but with less precision.
Cutting Precision and Quality
- Precision Requirements: If your projects demand high accuracy with minimal edge roughness, fiber laser cutting is the superior choice.
- Edge Quality: Fiber lasers produce smoother edges with a smaller heat-affected zone (HAZ), reducing the need for secondary finishing. Plasma cutting may result in rougher edges and a larger HAZ.
Production Volume and Speed
- Cutting Speed: For thin materials, fiber lasers offer faster cutting speeds, enhancing productivity for high-volume production runs. Plasma cutters may be faster on thicker materials but are generally slower on thinner ones.
- Repeatability: Fiber lasers provide consistent results, which is crucial for mass production where uniformity is essential.
Operational Costs
- Initial Investment: Fiber laser cutting machines have a higher upfront cost due to advanced technology. Plasma-cutting machines are less expensive initially.
- Operating Expenses: Consider energy consumption, maintenance, and consumables. Fiber lasers are more energy-efficient and have lower long-term maintenance costs.
Complexity of Design
- Intricate Cuts: Fiber lasers can handle complex and detailed designs with high precision. Plasma cutters are less suitable for intricate work due to a wider kerf.
Maintenance and Downtime
- Machine Reliability: Fiber lasers have fewer moving parts and require less frequent maintenance, resulting in less downtime.
- Consumables: Plasma cutting machines require regular replacement of electrodes and nozzles, increasing maintenance needs.
Safety and Environmental Impact
- Safety Measures: Fiber lasers require precautions against laser radiation, while plasma cutting involves risks from high temperatures, UV radiation, and fumes.
- Environmental Considerations: Fiber lasers are more energy-efficient and produce fewer emissions, aligning with sustainable practices.
Application Examples
Automotive Manufacturing
- Fiber Laser Cutting: Used for precise cutting of body panels, intricate components, and custom parts where accuracy is crucial.
- Plasma Cutting: Suitable for cutting thicker structural components like frames and chassis parts.
Metal Fabrication
- Fiber Laser Cutting: Ideal for creating detailed metal artwork, signage, and components requiring high precision.
- Plasma Cutting: Effective for general fabrication of heavy-duty parts and equipment where fine detail is less important.
Construction Industry
- Fiber Laser Cutting: Used for cutting metal studs, brackets, and fittings that require precision.
- Plasma Cutting: Suitable for cutting large steel plates and beams used in building structures.
Shipbuilding and Heavy Machinery
- Fiber Laser Cutting: Applicable for cutting thinner materials used in certain ship components and machinery parts.
- Plasma Cutting: Preferred for cutting thick steel plates and heavy components in ships and industrial machinery.
Aerospace Industry
- Fiber Laser Cutting: Employed for precision cutting of lightweight metals and alloys used in aircraft components.
- Plasma Cutting: Limited use due to lower precision but may be used for cutting thicker support structures.
Cost-Benefit Analysis
Initial Investment
Fiber Laser Cutting:
- Costs: Higher initial purchase price due to sophisticated technology and components.
- Benefits: Investment leads to higher precision, better cut quality, and long-term operational savings.
Plasma Cutting:
- Costs: Lower upfront cost, making it more accessible for businesses with budget constraints.
- Benefits: Immediate capability to cut thick materials without significant capital expenditure.
Operating Costs
Fiber Laser Cutting:
- Energy Consumption: More energy-efficient, resulting in lower electricity bills.
- Maintenance: Lower maintenance costs due to fewer consumables and less frequent part replacements.
- Consumables: Minimal consumable costs, primarily limited to assist gases.
Plasma Cutting:
- Energy Consumption: Higher energy usage increases operating expenses.
- Maintenance: Higher maintenance costs due to frequent replacement of consumables like electrodes and nozzles.
- Consumables: Ongoing expenses for consumables can add up over time.
Productivity and Quality
Fiber Laser Cutting:
- Productivity: Faster cutting speeds on thin to medium materials enhance throughput.
- Quality: Superior edge quality reduces or eliminates the need for secondary finishing, saving time and labor costs.
Plasma Cutting:
- Productivity: Efficient on thicker materials but may require additional time for post-processing due to lower cut quality.
- Quality: This may necessitate grinding or sanding to achieve desired edge smoothness, adding to labor costs.
Return on Investment (ROI)
Fiber Laser Cutting:
- Long-Term Savings: Energy efficiency and low maintenance contribute to cost savings over time.
- Market Advantage: High precision and quality can lead to new business opportunities and higher customer satisfaction.
Plasma Cutting:
- Short-Term Affordability: Lower initial costs allow for quicker deployment.
- Limitations: Potentially higher long-term costs due to maintenance and lower efficiency.
The choice between fiber laser cutting and plasma cutting hinges on your specific operational requirements, budget, and long-term business goals. If your work primarily involves cutting thin to medium-thickness metals with a need for high precision and superior edge quality, investing in a fiber laser cutting machine is advantageous. The higher initial cost is offset by lower operating expenses and the ability to produce high-quality products that meet stringent industry standards.
Conversely, if your operations focus on cutting thicker materials where precision is less critical, and you need a cost-effective solution with a lower initial investment, plasma cutting may be the appropriate choice. It provides the capability to handle heavy-duty cutting tasks efficiently.
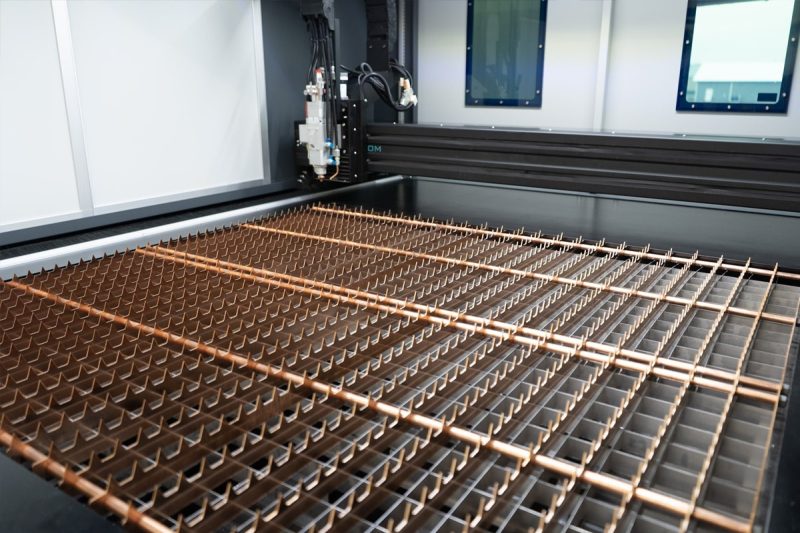
Summary
Choosing the right cutting technique can help achieve the best results in metal fabrication. Fiber laser cutting stands out for its high precision, superior edge quality, and efficiency in cutting thin to medium-thickness metals. It’s ideal for industries that require intricate designs and tight tolerances. On the other hand, plasma cutting excels in cutting thicker materials and offers a lower initial investment, though it may produce rougher edges that require additional finishing. Factors such as material type and thickness, required precision, operational costs, and specific application needs play a significant role in determining the most suitable method. By thoroughly evaluating these factors, manufacturers can choose the cutting technology that best aligns with their production goals and budget constraints.
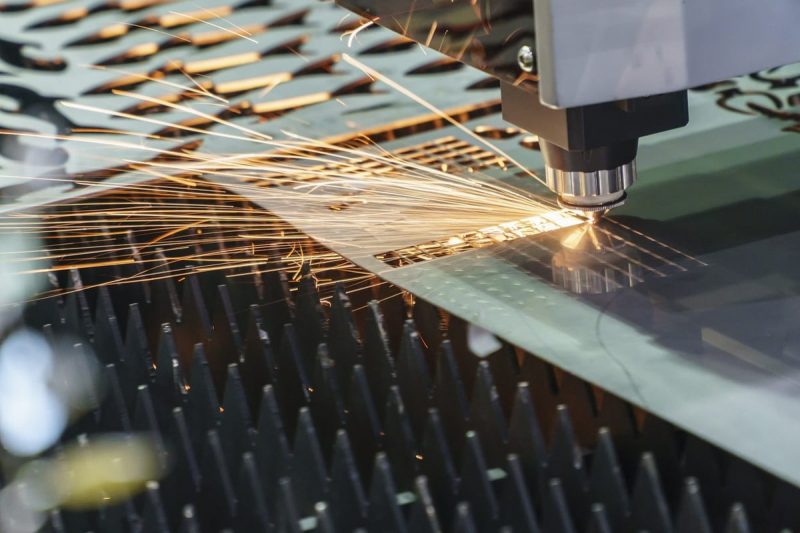
Get Laser Cutting Solutions
If you’ve determined that fiber laser cutting is the optimal choice for your manufacturing needs, AccTek Laser is ready to provide you with cutting-edge solutions. As a professional manufacturer of laser cutting machines, we specialize in delivering high-quality fiber laser cutting systems that combine precision, efficiency, and reliability. Our machines are designed to handle a wide range of materials and thicknesses, making them suitable for various industries such as aerospace, automotive, electronics, and metal fabrication.
At AccTek Laser, we offer personalized solutions tailored to your specific applications. Our expert team will work closely with you to understand your requirements and recommend the most suitable equipment from our extensive product lineup. We are committed to helping you enhance your production capabilities, reduce operational costs, and achieve superior cut quality.
In addition to laser cutting machines, we also provide laser welding machines, laser cleaning machines, and laser marking machines, offering a comprehensive suite of laser technologies to meet all your manufacturing challenges. By choosing AccTek Laser, you are investing in advanced technology that will give you a competitive edge in today’s fast-paced market.
Contact us today to explore how our fiber laser cutting solutions can transform your operations and drive your business forward. Let us partner with you in achieving excellence in precision metal fabrication.
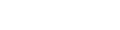
Contact information
- [email protected]
- [email protected]
- +86-19963414011
- No. 3 Zone A, Lunzhen Industrial Zone,Yucheng City , Shandong Province.
Get Laser Solutions