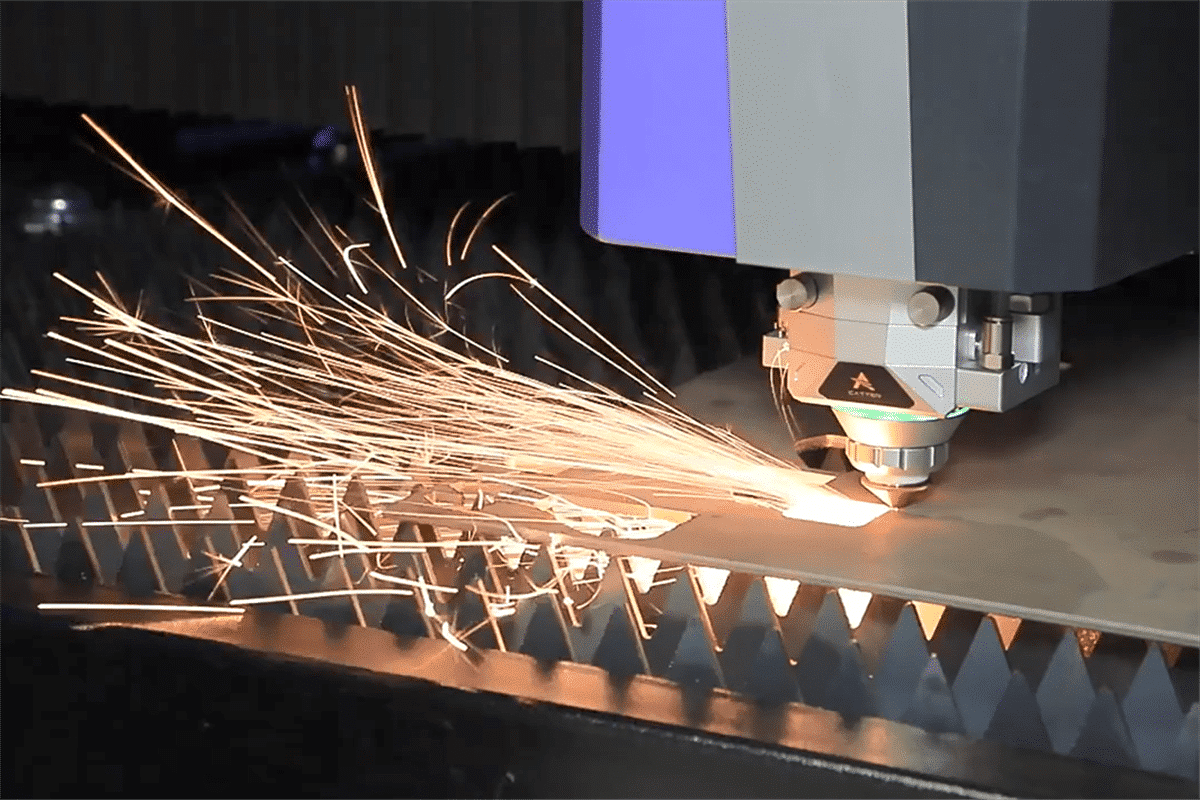
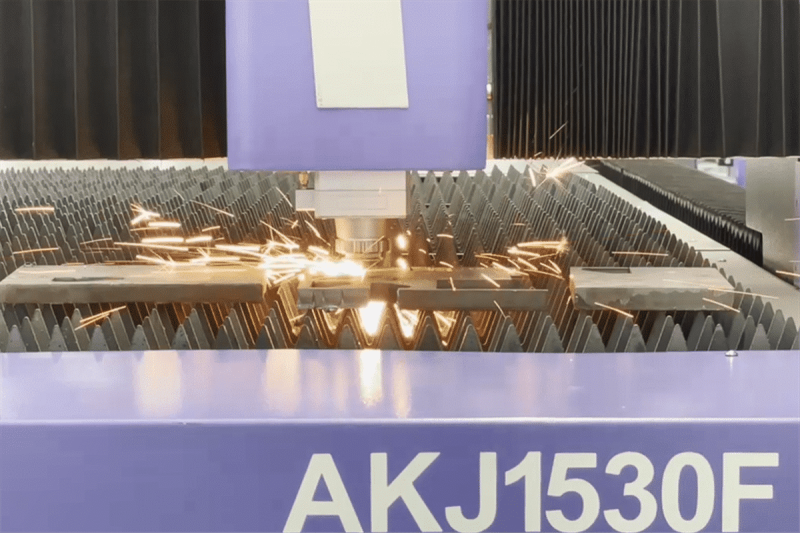
Understanding fiebr laser cutting technology
How does fiber laser cutting work?
What materials can be processed by fiber laser cutting process?
Fiber laser cutting machine is known for its high efficiency and versatility, especially in cutting various metal materials. The high power density of fiber laser cutting machine can cut these metals precisely and quickly:
- Stainless steel: Fiber laser can cut various grades of stainless steel with excellent edge quality and minimal thermal distortion, commonly used in automotive, aerospace, and construction industries.
- Mild Steel: Fiber laser cutting is ideal for mild steel sheets and plates of various thicknesses, commonly used in various structural applications and general manufacturing.
- Aluminum: The fiber laser cutting process is ideal for cutting aluminum sheets and alloys, often used in aerospace and automotive applications.
- Copper: Copper is a highly conductive metal that can be effectively cut using a fiber laser generator, making it suitable for the production and processing of electrical components, pipes, and decorative components.
- Brass: Fiber lasers can precisely cut brass, a metal alloy known for its decorative applications.
- Galvanized Steel: Fiber laser generators can cut galvanized steel commonly used in construction and manufacturing.
- Titanium: Fiber laser generators can cut titanium, a lightweight yet strong metal used in the aerospace and medical industries.
- Other metal alloys: The fiber laser cutting process is capable of cutting various metal alloys used in specialized applications, expanding their application in various industries.
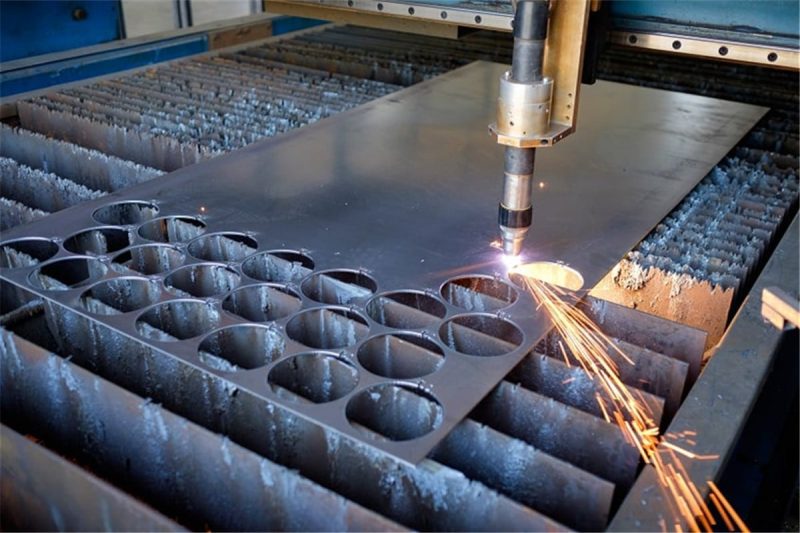
What are the traditional metal cutting processes?
Plasma Cutting
Waterjet Cutting
Waterjet cutting is a machining process that uses a high-pressure stream of water or a mixture of water and abrasive material to cut through a variety of materials. This technique is often used for precision cutting of materials that may be sensitive to high temperatures generated by other methods, such as laser or plasma cutting. There are two main types of waterjet cutting:
- Pure Waterjet Cutting: This method uses a focused stream of water to cut softer materials like rubber, foam, and certain plastics. Pure waterjet cutting is ideal for materials that do not require the added cutting power of abrasive particles.
- Abrasive Waterjet Cutting: In this process, abrasive particles (usually garnet) are mixed with the water stream to increase cutting power. This allows abrasive waterjets to cut through harder materials such as metal, stone, ceramics, and composites. The abrasive particles in the water jet serve to erode and cut through the material. In this article, we are talking about this type of abrasive waterjet cutting for metal cutting.
Flame Cutting
Flame cutting, also known as oxy-fuel cutting, is a thermal cutting process that uses the heat generated by the combustion of gas and oxygen to cut metal. It is particularly suitable for cutting ferrous metals and can be used manually or with a CNC system for automatic cutting. The flame-cutting process includes the following steps:
- Preheating: The metal is preheated to a temperature just below its melting point. This is done by directing the flame onto the metal surface. Preheating reduces the amount of oxygen required for the cutting process.
- Cutting: Once the metal is adequately preheated, a jet of oxygen is directed onto the preheated metal. The high-pressure oxygen jet reacts with the metal, forming iron oxide or slag. The exothermic reaction releases additional heat, melting the metal. The molten metal is then blown away by the force of the oxygen jet, creating a cut.
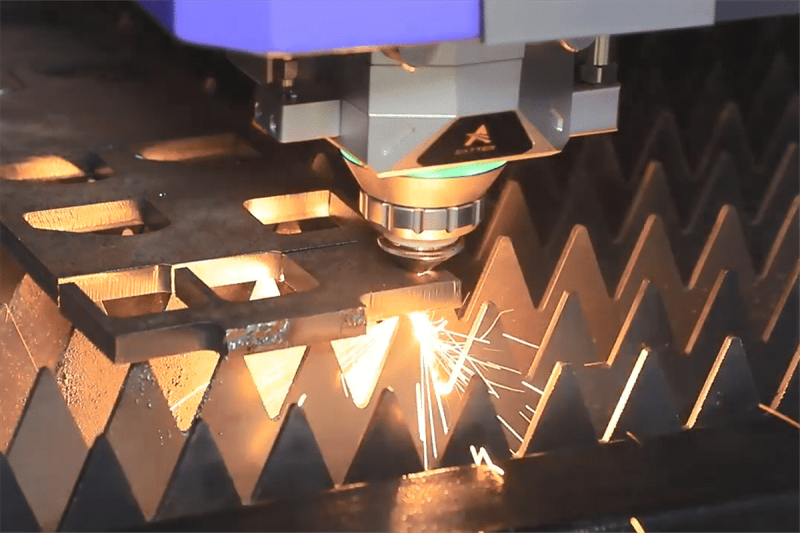
Fiber laser cutting VS traditional metal cutting processes
Principle of Operation
- Fiber Laser Cutting: This process involves using a high-power laser beam generated by a fiber laser source. The laser beam is focused and directed onto the material to be cut, melting or vaporizing it along the predetermined cutting path.
- Plasma Cutting: Involves the use of a high-velocity jet of ionized gas (plasma) to melt and remove material. The plasma is generated by passing an electric arc through a gas.
- Water Jet Cutting: Water jet cutting utilizes a high-pressure stream of water (sometimes mixed with an abrasive material like garnet) to cut through materials. The abrasive water jet can cut through a wide range of materials by erosion rather than melting.
- Flame Cutting: Utilizes a high-temperature flame (typically oxy-fuel) to heat the material to its ignition point. A stream of oxygen is then directed at the heated material, causing it to oxidize and be blown away as slag.
Material Compatibility
- Fiber Laser Cutting: Versatile and suitable for cutting a wide range of materials, including metals like steel, aluminum, copper, and brass. It is especially effective for thin to medium-thickness metals.
- Plasma Cutting: Well-suited for a variety of conductive materials, including ferrous and non-ferrous metals. It is particularly effective for cutting thick materials.
- Water Jet Cutting: Versatile and can cut through a wide range of materials, including metals, plastics, composites, stone, glass, and ceramics.
- Flame Cutting: Commonly used for cutting thicker metals, particularly carbon steel. Less effective for cutting non-ferrous metals like aluminum and stainless steel.
Precision Capability
- Fiber Laser Cutting: Offers high precision and accuracy, especially for intricate and detailed cuts. The focused laser beam allows for fine control over the cutting process, enabling fine tolerances and producing smooth edges.
- Plasma Cutting: Generally provides good precision, but the cut quality may not be as high as that of laser cutting, particularly in terms of edge smoothness and detail.
- Water Jet Cutting: Provides good precision, especially for thicker materials, but the precision can be affected by factors like material thickness and the speed of cutting.
- Flame Cutting: Generally provides lower precision compared to laser cutting. Best suited for applications where precision is not a critical requirement, such as in structural steel fabrication.
Speed Capability
- Fiber Laser Cutting: Generally faster than many traditional methods, especially for thin to medium-thickness materials. Laser cutting speeds are influenced by factors like laser power and material type.
- Plasma Cutting: While it can be fast, especially in thick materials, plasma cutting may have limitations in terms of speed when compared to laser cutting.
- Water Jet Cutting: Slower than laser cutting, especially for thick materials. The cutting speed can be influenced by factors such as material type and thickness.
- Flame Cutting: Slower compared to laser cutting, especially for thicker materials. Cutting speed may vary depending on the thickness of the material.
Thickness Capability
- Fiber Laser Cutting: Effective for both thin and thick materials, but it may have limitations in extremely thick sections.
- Plasma Cutting: Well-known for its ability to cut through thick metals, making it a preferred choice for applications requiring high cutting power.
- Waterjet Cutting: It can effectively cut through thick metals, but the specific capabilities will depend on the material properties. Thicker materials may require slower cutting speeds to ensure proper penetration.
- Flame Cutting: Limited in terms of materials and is most effective for cutting thick carbon steel.
Heat Affected Zone (HAZ)
- Fiber Laser Cutting: Produces a smaller heat-affected zone compared to traditional methods, minimizing the risk of material distortion or warping.
- Plasma Cutting: Generally results in a larger HAZ, which can affect the material’s properties, particularly in thinner sections.
- Water Jet Cutting: Leaves a smooth edge, but the cut may have a slight taper. The process is considered cold cutting, resulting in minimal heat-affected zones.
- Flame Cutting: Generates a larger heat-affected zone, which can result in more significant thermal distortion.
Operating Costs
- Fiber Laser Cutting: This may have higher initial investment costs but generally lower operating costs in the long run due to energy efficiency and minimal consumables.
- Plasma Cutting: Usually has lower initial costs but may incur higher ongoing costs for consumables like electrodes and gases.
- Water Jet Cutting: This can be more expensive in terms of operating costs, particularly due to the high-pressure water pump and abrasive material.
- Flame Cutting: Lower initial investment, but operating costs may be higher due to the consumption of fuel gases.
Summarize
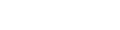
- [email protected]
- [email protected]
- +86-19963414011
- No. 3 Zone A, Lunzhen Industrial Zone,Yucheng City , Shandong Province.