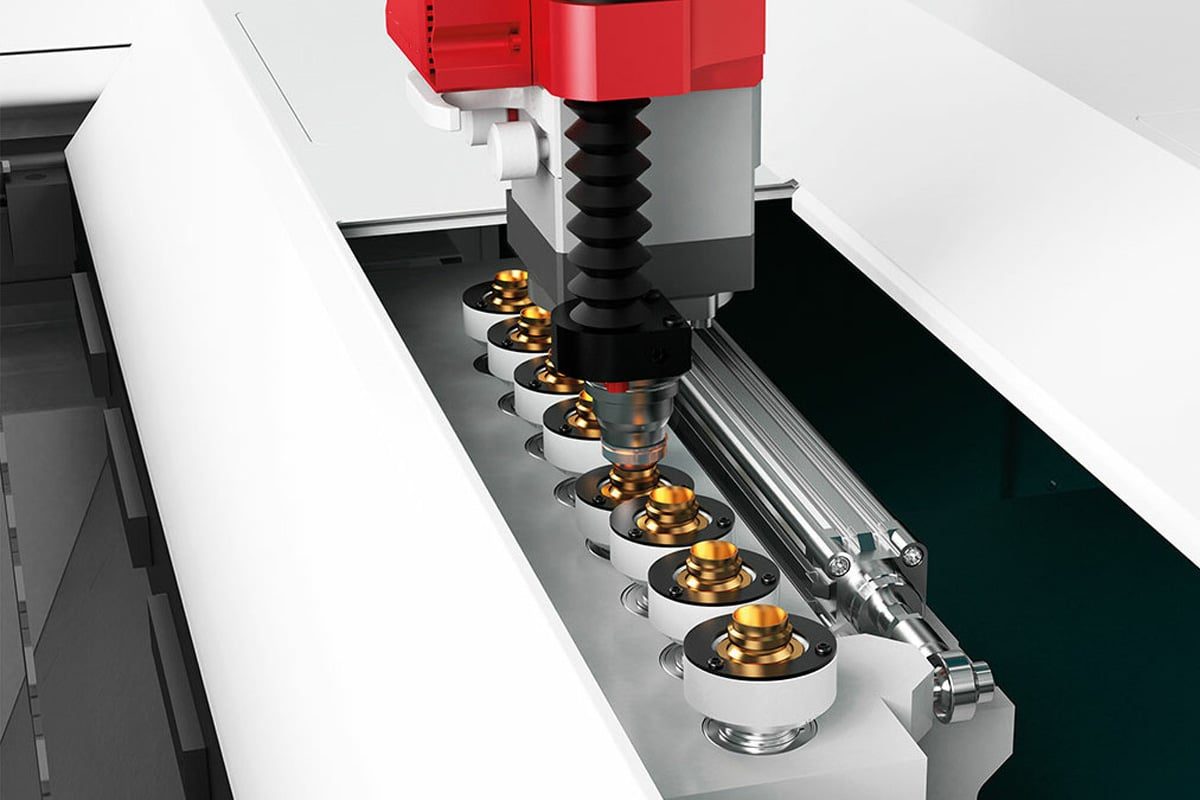
Advantages of Automatic Nozzle Changer in Fiber Laser Cutting Machine
The automatic nozzle changer is a core technology of modern machines de découpe laser à fibre. This function can efficiently replace nozzles of different types and sizes through programmed control to adapt to various processing materials and process requirements. This function greatly simplifies the complex process of traditional manual replacement and reduces the errors caused by human operation. At the same time, it can accurately select nozzle specifications according to the specific requirements of the cutting task to ensure the stability of processing quality. In addition, the automatic nozzle changer can save time, improve equipment utilization, and provide users with more efficient and intelligent production solutions. It is an indispensable tool for modern industry.
Table des matières
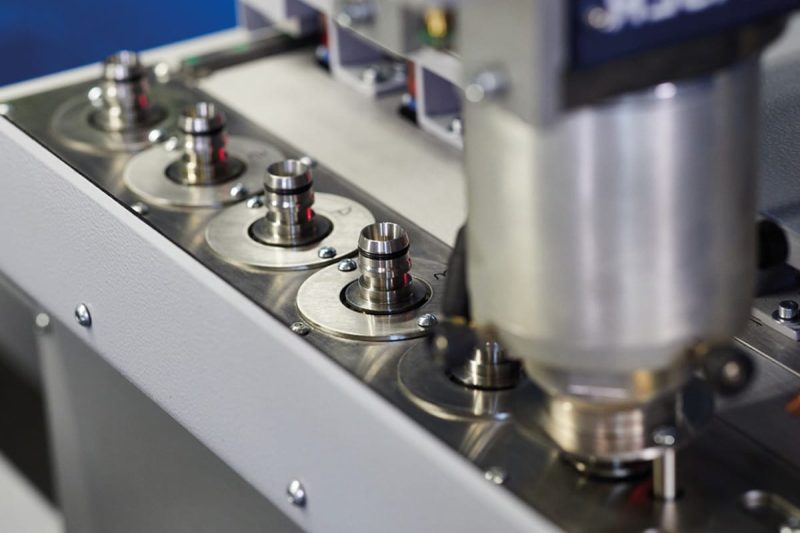
Learn About the Automatic Nozzle Changer
The automatic nozzle replacement device is an intelligent auxiliary device, whose core function is to replace the nozzle through programmed control quickly. The replacement process usually includes the system identifying the current nozzle status, automatically moving to the nozzle replacement position, completing the nozzle unloading and installation, and finally calibrating to the optimal cutting state. This process does not require manual intervention, is accurate and efficient, and provides convenience for cutting different materials and meeting diverse processing needs.
Functional Description
The automatic nozzle replacement device is an intelligent module integrated into the fiber laser cutting machine, designed to achieve efficient and accurate nozzle replacement. Its core functions include automatic identification of the current nozzle model, selection of an adaptive nozzle according to the processing material or task requirements, and real-time monitoring of the nozzle status to ensure replacement. Through programmed control, the device can meet the needs of different cutting processes, reduce manual operation time, and improve equipment operation efficiency and stability.
Nozzle Replacement Procedure Overview
The process of replacing the nozzle mainly includes the following steps:
- Identification phase: The system scans the current nozzle model and status to determine whether it needs to be replaced.
- Movement phase: The laser head moves to the replacement device position, and the old nozzle is unloaded by the robot or fixture.
- Installation phase: The new nozzle is automatically assembled to the cutting head to complete the installation.
- Calibration phase: The system calibrates the nozzle position and cutting parameters to ensure optimal cutting performance.
The entire process does not require manual intervention and is accurate and efficient, greatly reducing the time waste and errors that may be caused by manual operation, and significantly improving the overall efficiency and stability of the production line. This intelligent operation mode not only ensures the high-quality completion of processing tasks but also adapts to a variety of materials and complex cutting requirements, providing users with more reliable and flexible processing solutions to meet the requirements of modern industrial production for high precision and high efficiency.
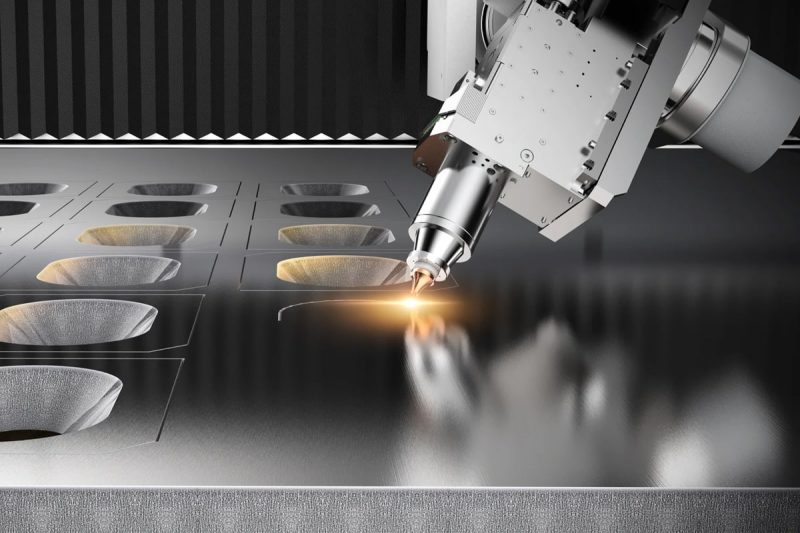
Improve Efficiency
In modern manufacturing, improving production efficiency and reducing equipment downtime are the keys to increasing output value and competitiveness. The application of automatic nozzle replacement systems in the laser cutting industry has gradually become a core solution to improve efficiency and reduce downtime. Through automated design, the nozzle replacement time is significantly shortened, the production line can maintain efficient operation, and reduce the cost caused by downtime.
- Improve efficiency and reduce downtime: Traditional nozzle replacement requires manual operation, which usually takes a long time and affects production efficiency. The automatic nozzle replacement system can complete nozzle replacement in a few seconds, reduce downtime, ensure production line continuity, and significantly improve production efficiency, especially in high-intensity production environments.
- Simplified operation, lower technical requirements: The automated system simplifies the operation process and reduces the operator’s skill requirements. Compared with manual replacement, automatic nozzle replacement reduces the risk of human error, operation is more stable and consistent and reduces the cost of training and operating errors.
- Improve productivity and increase capacity: The nozzle replacement speed is increased, and the equipment can quickly resume work, avoiding long pauses. This fast switching increases the capacity per unit time, especially suitable for production lines that require long-term continuous operation.
The automatic nozzle replacement system optimizes the production process, improves efficiency and productivity, and reduces human errors. As automation technology advances, it will continue to provide continuous productivity support for the manufacturing industry.
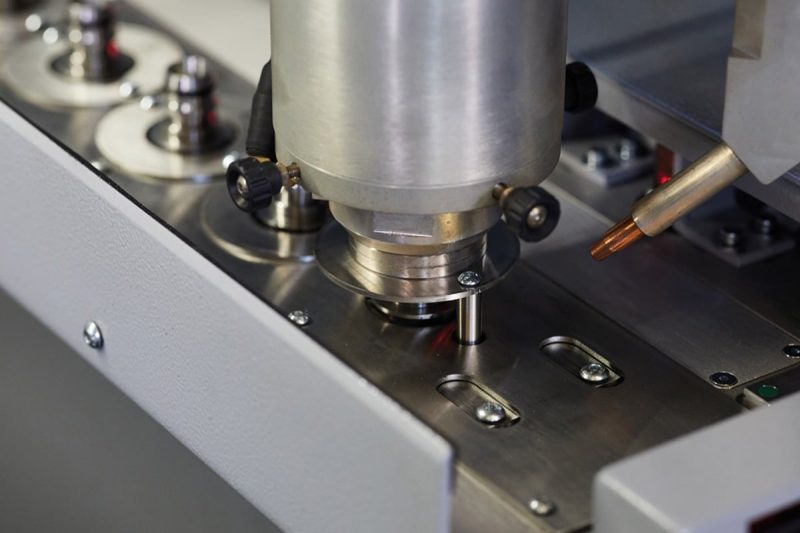
Enhanced Versatility
The automatic nozzle changer improves the versatility and application flexibility of laser cutting machines, especially when processing different materials and performing multiple tasks. This technological innovation enables laser cutting machines to adapt to different work requirements more efficiently, improving production efficiency and equipment utilization.
- Material compatibility: The automatic nozzle changer can automatically adjust to the cutting requirements of different materials (such as stainless steel, aluminum alloy, and carbon steel), avoiding the time waste and errors of manual nozzle replacement. It can quickly select the appropriate nozzle according to the material type, ensuring the best cutting effect and improving work efficiency.
- Application flexibility: The automatic nozzle changer supports a variety of cutting tasks, expanding the application range of the machine à découper au laser. Whether it is fine cutting, deep cutting, or thick plate processing, the automation system can quickly switch according to needs, improving the versatility and flexibility of the equipment.
The automatic nozzle changer improves the adaptability and efficiency of laser cutting machines in cutting different materials and various application tasks, broadens its application range, and is a key technology for improving productivity and equipment flexibility.
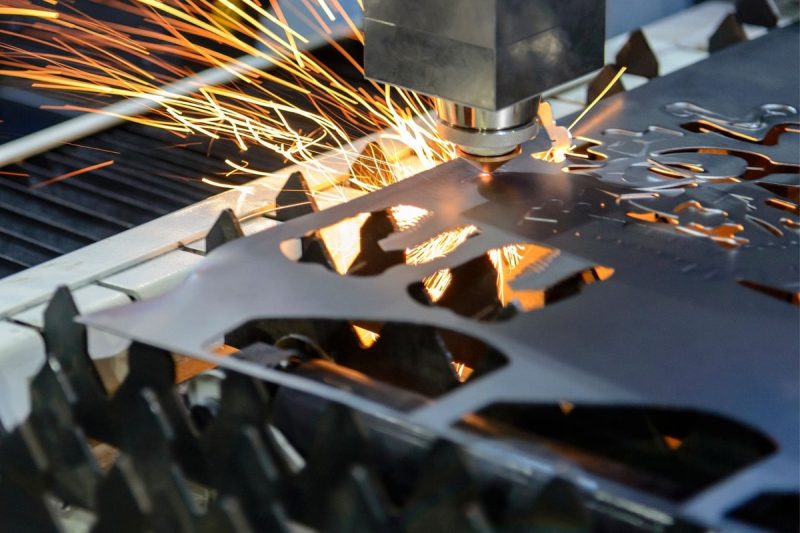
Accuracy and Consistency
In the laser cutting process, it is very important to maintain cutting quality and improve processing accuracy. The automatic nozzle replacement system not only improves production efficiency but also ensures the consistency and accuracy of cutting, reducing the errors caused by human operation. This system can effectively improve the processing quality and accuracy through precise nozzle control, ensuring that each cutting can meet the expected standards.
- Maintain cutting quality: Traditional manual nozzle replacement may lead to improper operation or inaccurate nozzle selection, which will affect the cutting quality. The automatic nozzle replacement system can automatically select the most suitable nozzle according to different materials and cutting requirements. This ensures that the best nozzle is always used for each cutting, maintaining a high level of cutting quality and avoiding uneven cutting or quality fluctuations caused by incorrect nozzle selection.
- Improved accuracy: When manually adjusting the nozzle, the operator may be inexperienced or careless, resulting in an inaccurate nozzle position, which will affect the cutting effect. The automatic nozzle replacement system ensures that the nozzle is always in the best working condition through high-precision positioning and selection, reducing the error caused by manual adjustment. The system can control the precise position of the nozzle in real-time, which significantly improves the accuracy of the cutting process and avoids the occurrence of errors.
The automatic nozzle changing system not only improves production efficiency but also provides higher precision and consistency in the cutting process. Always maintaining cutting quality and reducing errors caused by manual operation, ensures that every cut is made with the best results. This improvement in precision and consistency makes laser-cutting machines more competitive when handling high-precision and high-demand jobs.
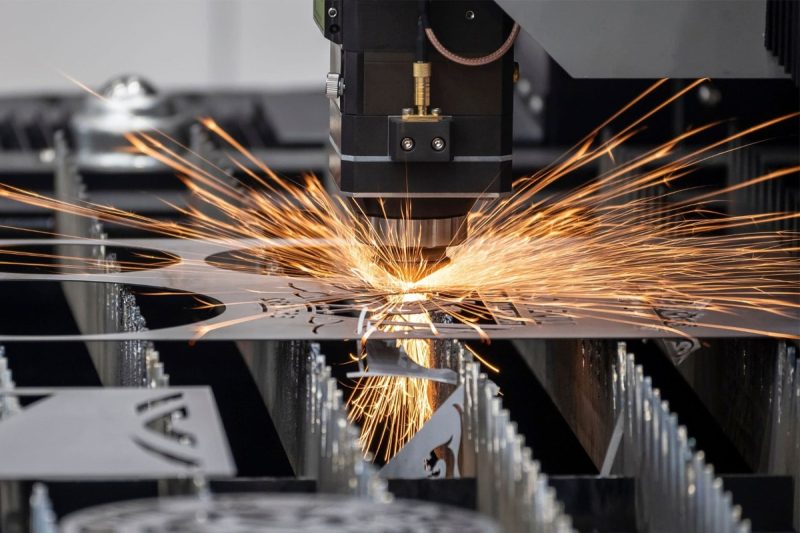
Cost Savings
In the laser-cutting industry, cost control is an important factor in improving profitability. The automatic nozzle replacement system effectively reduces operating costs by optimizing operating processes and reducing unnecessary downtime. By reducing manual operations and errors, companies not only save labor costs but also improve the efficiency of equipment use, thereby achieving significant cost savings in long-term operations.
- Reduce operating costs: Manual operation not only increases personnel costs but also easily leads to operational errors, which in turn causes downtime and repair costs. The automatic nozzle replacement system reduces the need for human intervention through automated control, reducing downtime and repair costs caused by human errors. The equipment can operate efficiently and stably, optimize resource allocation, improve overall operational efficiency, and help companies reduce operating costs in the fierce market competition.
- Extend the life of the nozzle: The nozzle is an important consumable part of the laser cutting machine. Frequent incorrect operation and improper use often accelerate the wear of the nozzle. The automatic nozzle replacement system can accurately select the appropriate nozzle according to actual needs, avoiding unnecessary wear and replacement. By optimizing the use of the nozzle and reducing excessive operation, the system can extend the service life of the nozzle and reduce the frequency of replacement, thereby saving the cost of maintenance and replacement of the nozzle.
- Increase machine uptime: Equipment idle time is the enemy of enterprise production efficiency, especially in the process of manual operation, due to personnel changing nozzles or improper adjustment, which often leads to equipment downtime. The automatic nozzle replacement system significantly reduces equipment idleness caused by manual operation by increasing the speed of nozzle replacement. Each nozzle replacement can be completed quickly, and the equipment can be quickly restored to working condition, maximizing its uptime, improving production efficiency, and reducing non-productive time.
The automatic nozzle replacement system effectively helps companies save operating costs by reducing manual intervention, extending nozzle life, and improving machine operating efficiency. Its efficient replacement mechanism not only reduces equipment idleness and maintenance costs but also optimizes resource allocation, providing companies with a higher return on investment. With the continuous development of automation technology, this system will continue to bring more cost savings and benefits to the manufacturing industry.
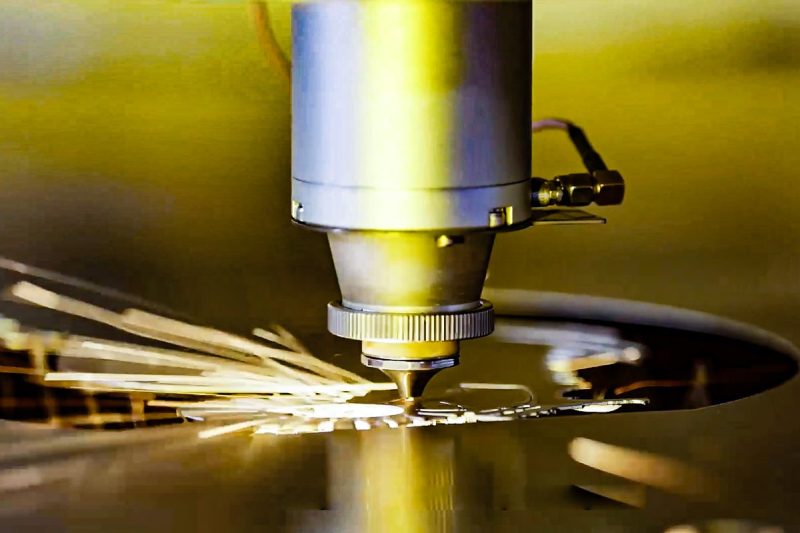
Safe and Easy to Use
In industrial production, safety and ease of use are always important considerations in equipment design. The automatic nozzle replacement system not only improves production efficiency but also greatly improves the safety of the working environment by reducing operator intervention and simplifying the operation process. The system uses automation technology to reduce human interference, reduce operating risks, and make operations more intuitive and safe.
- Reduce operator intervention: Traditional nozzle replacement operations require a lot of manual intervention. Operators need to manually install and adjust nozzles, which not only increases the difficulty of operation but also poses certain safety hazards, such as operation in a high-temperature environment or equipment failure. The automatic nozzle replacement system significantly reduces the need for operator intervention through automation functions, reducing the safety risks associated with nozzle replacement. Operators no longer need to frequently contact equipment parts, reducing accidents and injuries caused by improper operation, and ensuring the safety of operators.
- Simplified operation: The operating interface and program design of the automatic nozzle replacement system are very user-friendly, and the entire replacement process is intuitive and efficient. The operator only needs to make simple settings, and the system can automatically complete the nozzle replacement task. Automated program control and simplified interface make the entire process unnecessary and reduce the operating threshold. Even novice operators can quickly understand and master the use of this system, greatly reducing training costs and operating difficulties. This simplified operation method improves overall production efficiency and ensures long-term stable operation of the equipment.
The automatic nozzle replacement system not only improves work efficiency but also enhances operational safety by reducing operator intervention and simplifying the operation process. The system’s automation and humanized design make the nozzle replacement process more intuitive and simple, reducing potential safety risks and the occurrence of human errors, and ensuring the safety and reliability of the production process. As the technology continues to improve, the automatic nozzle replacement system will continue to promote the development of safe and efficient automated production models.
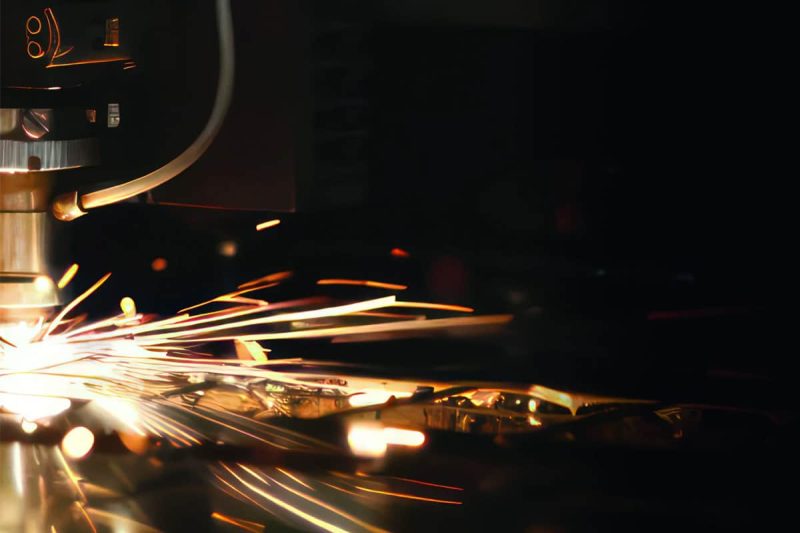
Résumer
The application of automatic nozzle changers in fiber laser cutting machines significantly improves the overall efficiency, flexibility, and cost-effectiveness of the production line. This technology reduces downtime, optimizes operating procedures, and ensures the continuity of the production line through automated processes, thereby greatly improving production efficiency. The automatic nozzle changer not only improves cutting accuracy and consistency but also can quickly switch the appropriate nozzle according to different production needs, expanding the scope of application of the equipment. Its precise nozzle selection and efficient replacement speed ensure that each cut can maintain high quality and avoid errors and inconsistencies that may occur in manual operation.
In addition, the automatic nozzle changer extends the service life of the nozzle, reduces wear and tear, and helps companies save maintenance and replacement costs. Since automated operation greatly reduces manual intervention, this not only reduces the technical requirements of the operator, but also reduces the risk of human error, and improves the safety and reliability of the production environment. More importantly, it enables the laser cutting machine to adapt to a variety of materials and cutting tasks more flexibly, broadens the application range of the equipment, increases production capacity, and reduces the manufacturing cost per unit product.
For production lines that pursue efficiency, precision, and flexibility, the automatic nozzle changer is undoubtedly a feature worth investing in. It not only brings significant economic benefits to enterprises but also helps improve productivity and market competitiveness. With the continuous advancement of automation technology, the automatic nozzle changer will play an increasingly important role in the future manufacturing industry and is one of the key technologies for enterprises to achieve sustainable development.
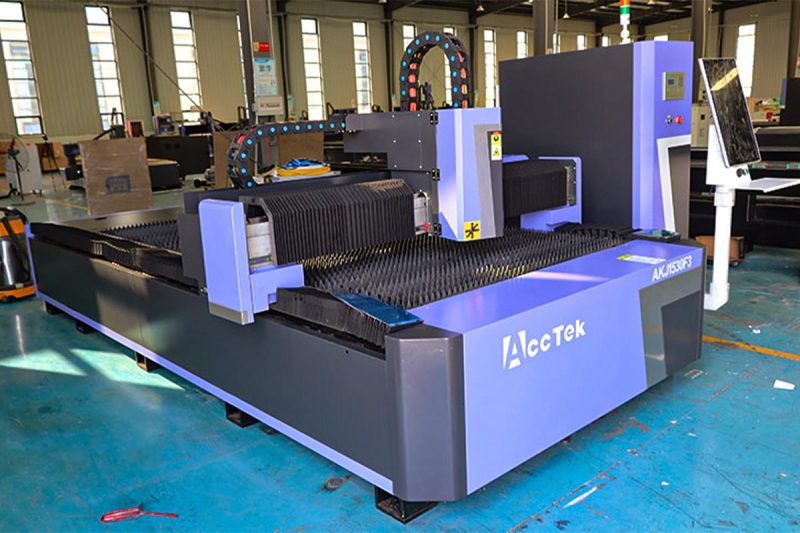
Obtenez des solutions laser
When you are looking for an efficient and precise laser cutting solution, the AccTek Laser fiber laser cutting machine is undoubtedly your ideal choice. Our equipment not only has excellent cutting accuracy but also is equipped with an advanced automatic nozzle replacement system, providing unprecedented flexibility and efficiency for your production line. With the automatic nozzle replacement function, you do not need to stop the machine for manual adjustment, which can greatly reduce downtime, improve production continuity, and ensure consistent high quality every time you cut.
Whether you are dealing with stainless steel, aluminum alloy, or carbon steel, our laser cutting machines can quickly and accurately change nozzles according to different materials and cutting tasks to ensure the best cutting results. With this innovative technology, our fiber laser cutting machines not only improve cutting accuracy, but also extend the life of the nozzle, reduce maintenance costs, and optimize production efficiency. Let Lasers AccTek laser solutions become your powerful partner to improve productivity, reduce operating costs, and help your business move toward greater success.
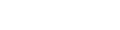
Coordonnées
- [email protected]
- [email protected]
- +86-19963414011
- No. 3 Zone A, zone industrielle de Lunzhen, ville de Yucheng, province du Shandong.
Obtenez des solutions laser