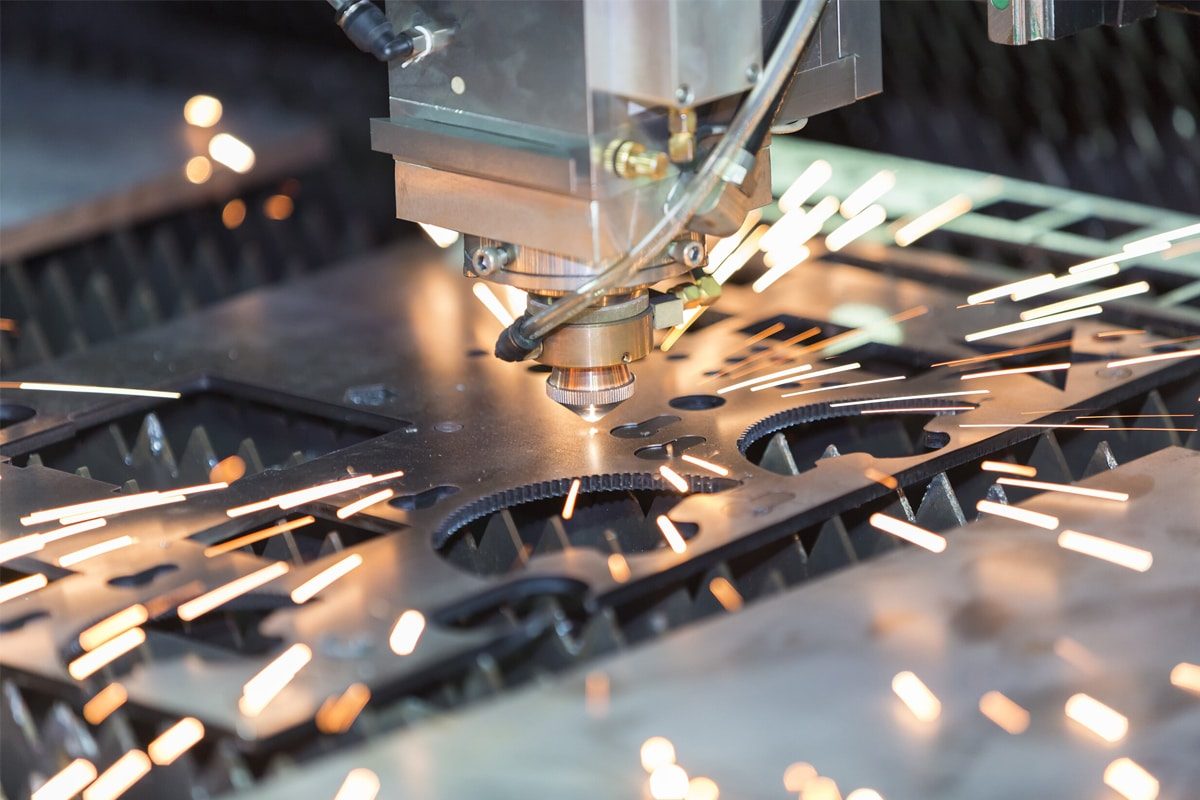
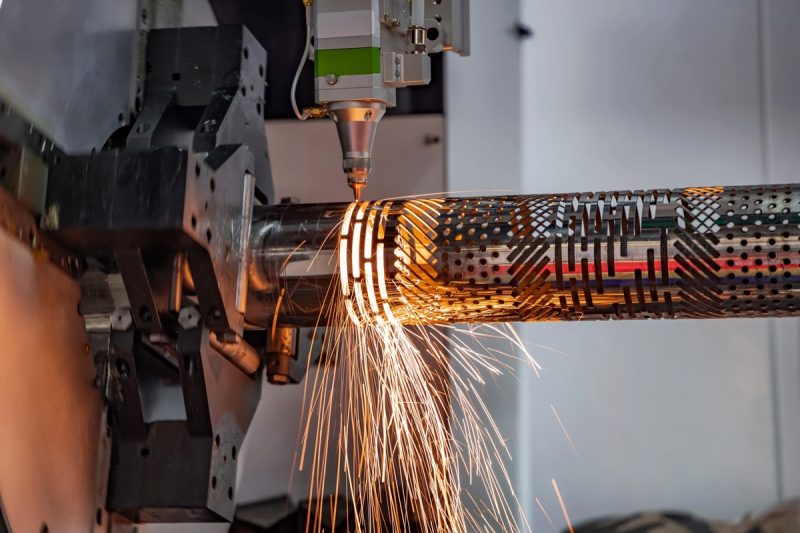
Comprendre la puissance du laser
Qu'est-ce que la puissance laser ?
Comment la puissance du laser affecte le processus de découpe
La puissance du laser joue un rôle clé dans le processus de découpe laser, affectant plusieurs aspects clés :
- Vitesse de coupe : une puissance laser plus élevée permet des vitesses de coupe plus rapides. En effet, une plus grande quantité d'énergie est disponible pour faire fondre, vaporiser ou brûler le matériau, ce qui permet une coupe plus rapide. Pour les applications industrielles où une productivité élevée est essentielle, le choix d'une puissance laser plus élevée peut réduire considérablement le temps de production.
- Qualité des bords : la qualité du bord de coupe est affectée par la puissance du laser. Le réglage de puissance optimal produit un bord lisse et propre tout en minimisant les bavures et la distorsion thermique. Cependant, une puissance trop élevée peut entraîner des brûlures sur les bords, une fusion excessive et une zone affectée par la chaleur (ZAT) plus large, ce qui peut compromettre la qualité des bords.
- Pénétration du matériau : la puissance du laser détermine la capacité à découper différentes épaisseurs de matériau. Les matériaux plus épais nécessitent des puissances plus élevées pour garantir que le faisceau laser puisse pénétrer toute la profondeur du matériau. Pour les matériaux fins, des réglages de puissance plus faibles sont souvent suffisants et peuvent éviter une accumulation de chaleur inutile et des dommages matériels.
- Taux d'enlèvement de matière : Le taux d'enlèvement de matière est affecté par la puissance du laser. Des puissances plus élevées entraînent des taux d'enlèvement de matière plus élevés, ce qui est bénéfique pour les matériaux plus épais, mais peut entraîner une fusion excessive ou une brûlure des matériaux plus fins.
- Précision et détails : pour les motifs complexes et les détails fins, des puissances laser plus faibles constituent souvent un meilleur choix. Cela permet un contrôle précis du faisceau laser, réduit le risque de surdécoupe et garantit que les détails sont restitués avec précision.
- Effets thermiques : une puissance laser excessive peut entraîner des effets thermiques notables, tels qu'une déformation ou une décoloration, en particulier sur les matériaux sensibles à la chaleur. Un calibrage de puissance approprié peut minimiser ces effets indésirables.
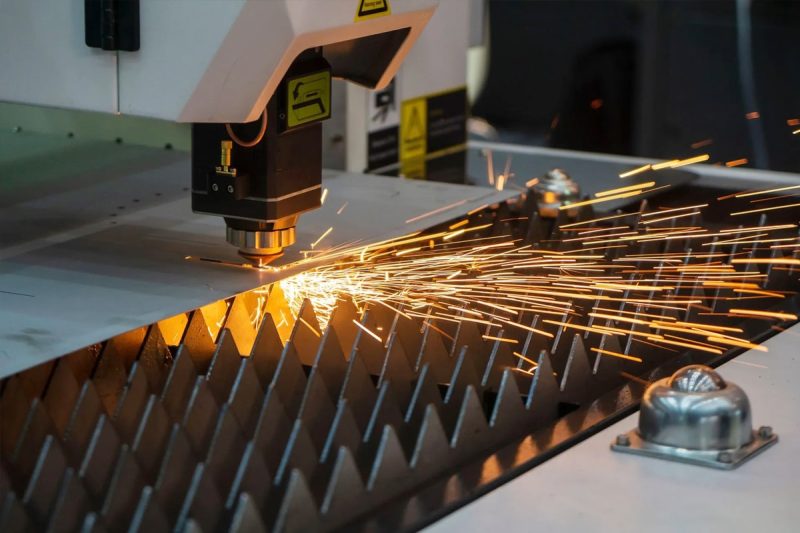
Types de machines de découpe laser
Machine de découpe laser à fibre
Caractéristiques principales
- Longueur d'onde : généralement d'environ 1,06 micron, ce qui la rend idéale pour la découpe des métaux.
- Efficacité : Efficacité électro-optique élevée, généralement supérieure à 30%, entraînant des coûts d'exploitation et une consommation d'énergie inférieurs.
- Qualité du faisceau : La qualité supérieure du faisceau permet une coupe plus fine et plus précise, en particulier sur les matériaux minces.
- Maintenance : Comme il n’y a pas de pièces mobiles dans la source laser, les besoins de maintenance sont faibles.
Applications
- Matériau : Idéal pour couper les métaux, notamment l'acier, l'acier inoxydable, l'aluminium, le laiton et le cuivre.
- Épaisseur : Convient pour la découpe de haute précision de matériaux fins à moyennement épais.
- Industries : Largement utilisé dans les industries aérospatiales, automobiles, électroniques et de fabrication de métaux.
Avantages
- Vitesse : Vitesses de coupe plus rapides par rapport aux lasers CO₂ et Nd, en particulier lors de la découpe de matériaux minces.
- Précision : Haute précision et haute qualité de bord grâce au faisceau fin.
- Efficacité électro-optique élevée : efficacité supérieure, entraînant une consommation d'énergie et des coûts d'exploitation inférieurs.
- Rentabilité : longue durée de vie et faibles besoins d’entretien.
Désavantages
- Coût initial : Investissement initial plus élevé par rapport aux générateurs laser CO2.
- Limitations matérielles : Moins efficace sur les matériaux non métalliques tels que le bois et le plastique.
Machine de découpe laser CO2
Caractéristiques principales
- Longueur d'onde : environ 10,6 microns, idéale pour couper une large gamme de matériaux, y compris les non-métaux.
- Efficacité : L’efficacité électrique est inférieure à celle des lasers à fibre.
- Qualité du faisceau : Bonne qualité de faisceau, adaptée à une large gamme de tâches de découpe et de gravure.
- Entretien : Nécessite un entretien régulier, y compris le remplissage en gaz et l'étalonnage du miroir.
Applications
- Matériaux : Capable de couper une large gamme de matériaux, notamment les métaux, le bois, l'acrylique, le verre, les textiles et les plastiques.
- Épaisseur : Efficace pour couper des matériaux fins et épais.
- Industries : Utilisé dans les industries de la signalisation, de l’emballage, du travail du bois, de l’automobile et du textile.
Avantages
- Polyvalence : Peut couper une large gamme de matériaux, en plus des métaux.
- Coût : Coût initial inférieur par rapport aux lasers à fibre.
- Disponibilité : Technologie mature, disponible dans une variété de modèles et de configurations.
Désavantages
- Vitesse : Plus lent pour la découpe des métaux par rapport aux lasers à fibre.
- Entretien : Les besoins d'entretien sont élevés, notamment le remplissage de gaz et les réglages réguliers des rétroviseurs.
- Consommation d’énergie : La consommation d’énergie est élevée en raison de la faible efficacité électrique.
Machine de découpe laser Nd
Caractéristiques principales
- Longueur d'onde : environ 1,064 micron, similaire aux lasers à fibre, adaptée à la découpe du métal.
- Modes de fonctionnement : Peut fonctionner en mode onde continue (CW) et en mode pulsé, offrant une flexibilité pour les applications de découpe et de gravure.
- Qualité du faisceau : Qualité de faisceau élevée pour une découpe et un perçage de précision.
- Entretien : généralement peu d'entretien, conception robuste et longue durée de vie.
Applications
- Matériau : Convient pour couper les métaux, la céramique et certains plastiques.
- Épaisseur : Convient pour la découpe et le perçage de précision de matériaux minces.
- Industries : couramment utilisé dans l’électronique, la fabrication de dispositifs médicaux, la bijouterie et l’aérospatiale.
Avantages
- Précision : Haute précision, capable de produire des détails fins.
- Fonctionnement pulsé : Capable de fonctionner en mode pulsé, idéal pour le perçage et la gravure fine.
- Compatibilité des matériaux : Efficace pour une large gamme de matériaux, y compris les matériaux durs et cassants.
Désavantages
- Vitesse : Vitesses de coupe plus lentes par rapport aux générateurs laser à fibre.
- Coût : Coût initial plus élevé et efficacité inférieure par rapport aux lasers CO2.
- Exigences de refroidissement : Nécessite un système de refroidissement efficace pour gérer la dissipation de la chaleur.
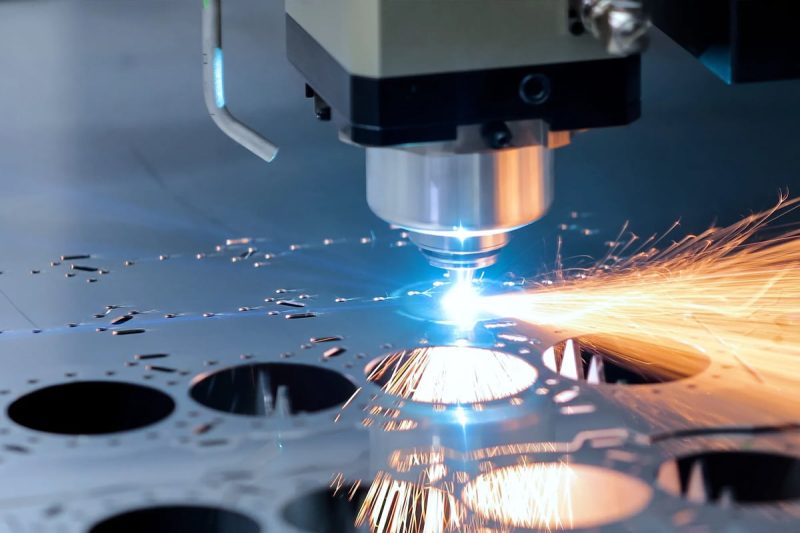
Facteurs affectant la puissance du laser
type de materiau
Les métaux
- Acier : en raison de son point de fusion élevé, il nécessite généralement des puissances laser plus élevées. L'acier doux, l'acier inoxydable et d'autres alliages d'acier peuvent avoir des besoins en puissance différents.
- Aluminium : En raison de sa réflectivité et de sa conductivité thermique élevées, il nécessite des puissances laser élevées.
- Cuivre et laiton : ces matériaux sont hautement réfléchissants et conducteurs et nécessitent des niveaux de puissance plus élevés ou des générateurs laser spécialisés, tels que des générateurs laser à fibre, pour garantir une découpe efficace.
Non-métaux
- Plastiques et acryliques : nécessitent généralement des puissances inférieures à celles des métaux. La puissance requise peut varier en fonction du type et de l'épaisseur du plastique.
- Bois : Une puissance modérée est requise, mais la puissance requise peut varier considérablement en fonction du type de bois et de son taux d'humidité.
- Tissu et papier : Ces matériaux étant fins et inflammables, ils nécessitent des puissances plus faibles lors de la découpe.
Épaisseur de matériau
L'épaisseur du matériau est directement proportionnelle à la puissance laser requise. Les matériaux plus épais nécessitent plus de puissance de coupe car le laser doit pénétrer plus profondément et retirer plus de matière.
- Matériaux fins (≤ 1 mm) : des niveaux de puissance inférieurs sont suffisants. Les puissances inférieures permettent une grande précision et des détails fins.
- Épaisseur moyenne (1-5 mm) : des niveaux de puissance moyens sont requis. La puissance exacte requise dépend du type de matériau et de la vitesse de coupe souhaitée.
- Matériaux épais (> 5 mm) : une puissance élevée est nécessaire pour assurer une pénétration complète et une découpe efficace. Pour les matériaux extrêmement épais, une approche multi-passes ou un générateur laser haute puissance spécialisé peut être nécessaire.
Exigences relatives à la vitesse de coupe
La vitesse de coupe souhaitée influence considérablement le choix de la puissance laser. Plus la vitesse de coupe est élevée, plus la puissance requise est généralement élevée pour maintenir la qualité de coupe et éviter les coupes incomplètes ou les bavures excessives.
- Découpe à grande vitesse : pour les applications où la vitesse est essentielle, comme la production en série, des puissances laser plus élevées sont nécessaires. Une puissance plus élevée garantit que le laser peut couper le matériau rapidement sans sacrifier la qualité.
- Découpe à vitesse moyenne : dans les scénarios où la vitesse de découpe n'est pas aussi importante, des réglages de puissance moyenne peuvent être utilisés. C'est souvent le cas pour la production en petites séries ou la fabrication sur mesure.
- Découpe à basse vitesse : pour des coupes très détaillées ou complexes, des vitesses de coupe et des réglages de puissance inférieurs peuvent être utilisés. Cela permet une plus grande précision et un meilleur contrôle.
Qualité de coupe requise
La qualité de coupe requise influe également sur le réglage de la puissance du laser. Les différentes applications ont des normes différentes en matière de qualité des bords, de précision et de finition.
- Découpe de haute qualité : pour les applications qui nécessitent des bords lisses, une qualité élevée et un post-traitement minimal, des puissances laser plus élevées et des vitesses de découpe plus lentes sont généralement requises. Cela garantit une coupe nette avec un minimum de scories et de bavures.
- Découpe de qualité standard : Pour les applications où des imperfections mineures sont acceptables, des niveaux de puissance moyens sont suffisants. C'est souvent le cas dans les applications industrielles lourdes où la vitesse prime sur la qualité esthétique.
- Découpe grossière : lorsque la vitesse est la principale préoccupation plutôt que la qualité des bords, des puissances plus élevées et des vitesses de coupe plus rapides peuvent être utilisées. Cette approche est souvent utilisée dans les étapes de découpe préliminaires ou pour les matériaux qui subiront un traitement ultérieur.
Complexité de la conception
La complexité du motif ou du motif à découper influe également sur la puissance laser requise. Les motifs complexes et détaillés nécessitent généralement un contrôle plus précis du laser, ce qui influe sur le réglage de la puissance.
- Motifs complexes : les motifs complexes avec des angles vifs, des petits trous et des détails détaillés nécessitent un contrôle précis de la puissance du laser. Des réglages de puissance plus faibles combinés à des vitesses plus lentes permettent d'obtenir une grande précision et d'éviter la surchauffe ou la déformation du matériau.
- Motifs moyens : les motifs de complexité moyenne peuvent être découpés avec des réglages de puissance équilibrés. Ces motifs peuvent inclure des courbes et des épaisseurs de ligne variables, mais ne nécessitent pas une précision extrême.
- Conceptions simples : des coupes simples avec un minimum de détails, telles que des formes simples et des lignes droites, peuvent être réalisées avec des réglages de puissance plus élevés et des vitesses plus rapides.
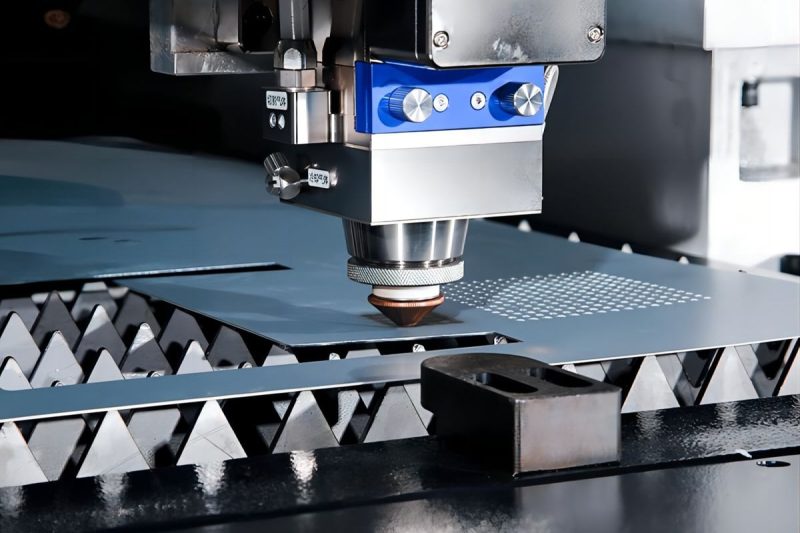
Plages de puissance laser pour différents matériaux
Les métaux
Acier doux
- Plaque mince (jusqu'à 3 mm d'épaisseur) : 1 000 à 2 000 watts
- Épaisseur moyenne (3-6 mm) : 2 000-4 000 watts
- Plaque épaisse (6-12 mm) : 4 000-8 000 watts
- Plaque extra épaisse (plus de 12 mm d'épaisseur) : 8 000 à 12 000 watts
Acier inoxydable
- Plaque mince (jusqu'à 2 mm d'épaisseur) : 1 000 à 2 000 watts
- Épaisseur moyenne (2-5 mm) : 2 000-4 000 watts
- Plaque épaisse (5-10 mm) : 4 000-6 000 watts
- Plaque extra épaisse (plus de 10 mm d'épaisseur) : 6 000 à 12 000 watts
Aluminium
- Plaque mince (jusqu'à 2 mm d'épaisseur) : 1 000 à 2 000 watts
- Épaisseur moyenne (2-6 mm) : 2 000-4 000 watts
- Plaque épaisse (6-10 mm) : 4 000-8 000 watts
- Plaque extra épaisse (plus de 10 mm) : 8 000 à 12 000 watts
Cuivre et Laiton
- Plaque mince (jusqu'à 1 mm d'épaisseur) : 1 000 à 2 000 watts
- Épaisseur moyenne (1-3 mm) : 2 000-4 000 watts
- Plaque épaisse (3-6 mm) : 4 000-6 000 watts
- Plaque extra épaisse (plus de 6 mm) : 6 000 à 8 000 watts
Non-métaux
Plastiques (par exemple polycarbonate, polypropylène, PVC)
- Feuilles minces (jusqu'à 2 mm d'épaisseur) : 25-40 watts
- Épaisseur moyenne (2-5 mm) : 40-100 watts
- Feuilles épaisses (5-10 mm) : 100-150 watts
- Feuilles extra épaisses (plus de 10 mm d'épaisseur) : 200-600 watts
Acrylique
- Feuilles minces (jusqu'à 2 mm d'épaisseur) : 60-100 watts
- Épaisseur moyenne (2-5 mm) : 100-200 watts
- Feuilles épaisses (5-10 mm) : 200-400 watts
- Feuilles extra épaisses (plus de 10 mm d'épaisseur) : 400-600 watts
Bois (par exemple contreplaqué, MDF, bois dur)
- Feuilles minces (jusqu'à 3 mm d'épaisseur) : 100-150 watts
- Épaisseur moyenne (3-6 mm) : 150-300 watts
- Feuilles épaisses (6-12 12 mm) : 300-500 watts
- Feuilles extra épaisses (plus de 12 mm) : 500-600 watts
Textiles et Cuirs
- Épaisseur fine et moyenne : 60-150 watts
- Matériaux épais : 150-300 watts
Matériaux composites
Polymère renforcé de fibres de carbone (PRFC)
- Feuille mince (jusqu'à 1 mm d'épaisseur) : 100-200 watts
- Épaisseur moyenne (1-3 mm) : 200-400 watts
- Feuille épaisse (3-6 mm) : 400-600 watts
Polymère renforcé de fibres de verre (GFRP)
- Feuille mince (jusqu'à 1 mm d'épaisseur) : 100-200 watts
- Épaisseur moyenne (1-3 mm) : 200-400 watts
- Feuille épaisse (3-6 mm) : 400-600 watts
Autres composites (par exemple, Kevlar, composites au bore)
- Feuille mince (jusqu'à 1 mm d'épaisseur) : 100-200 watts
- Épaisseur moyenne (1-3 mm) : 200-400 watts
- Feuille épaisse (3-6 mm) : 400-600 watts
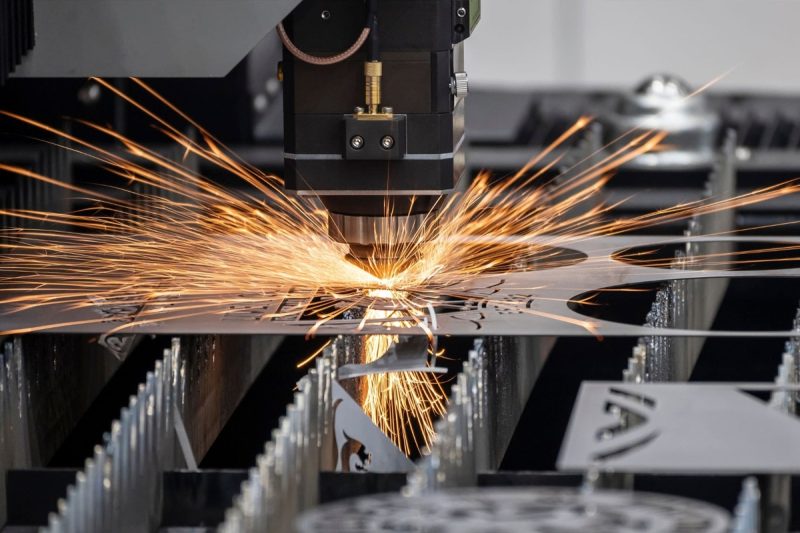
Méthodes de détermination de la puissance laser
Tableaux de compatibilité des matériaux
Les tableaux de compatibilité des matériaux sont une ressource précieuse qui fournit des conseils généraux sur les paramètres de puissance laser requis pour différents matériaux.
- Objectif : Ces tableaux aident les utilisateurs à identifier rapidement les paramètres de puissance de démarrage pour divers matériaux en fonction du type et de l'épaisseur du matériau.
- Structure : Les tableaux de compatibilité répertorient généralement les matériaux dans une colonne, suivis des paramètres de puissance recommandés, des vitesses de coupe et d'autres paramètres pertinents.
- Sources : Ces tableaux peuvent être trouvés dans les manuels d’utilisation, les logiciels de découpe laser et les sites Web des fabricants.
Avantages
- Référence rapide : fournit des conseils immédiats sans nécessiter de calculs ou d’expérimentation approfondis.
- Paramètres standardisés : fournit des paramètres d’alimentation standardisés basés sur les meilleures pratiques du secteur.
Désavantages
- Informations générales : Ces informations peuvent ne pas tenir compte des variations spécifiques de la qualité des matériaux ou des conditions environnementales.
- Point de départ uniquement : cela doit servir de base pour d’autres ajustements et optimisations.
Essais de matériaux
Les tests de matériaux impliquent la réalisation de tests réels pour affiner les paramètres de puissance laser pour des matériaux et des applications spécifiques.
- Configuration initiale : commencez par les paramètres recommandés figurant dans un tableau de compatibilité des matériaux ou dans le guide du fabricant.
- Réglage progressif : ajustez progressivement la puissance du laser, la vitesse et d’autres paramètres tout en surveillant les résultats.
- Évaluation : Évaluez la qualité de la coupe, la douceur des bords et tout signe de dégradation du matériau ou de surchauffe.
Avantages
- Précision : permet un étalonnage précis en fonction des propriétés spécifiques du matériau et des exigences de coupe.
- Optimisation : permet un réglage précis pour des performances de coupe optimales, améliorant ainsi l'efficacité et la qualité.
Désavantages
- Prend du temps : nécessite du temps et des ressources pour effectuer plusieurs tests et évaluations.
- Déchet matériel : implique l'utilisation de certains matériaux pendant les tests.
Recommandations du fabricant
Suivre les recommandations du fabricant est une méthode essentielle pour déterminer la puissance de découpe laser appropriée.
- Source : Les recommandations peuvent être trouvées dans les manuels d'utilisation, les documents d'assistance technique et les communications officielles des fabricants de machines de découpe laser.
- Contenu : Ces guides incluent généralement des paramètres de puissance détaillés, des vitesses de coupe et d'autres paramètres basés sur des tests approfondis et des applications réelles.
Avantages
- Fiabilité : Les recommandations du fabricant sont basées sur des tests complets et sont adaptées aux capacités spécifiques de la machine de découpe laser.
- Assistance : Une assistance technique est disponible auprès du fabricant pour toute question ou préoccupation.
Désavantages
- Recommandations générales : Bien que ces recommandations soient fiables, elles peuvent encore nécessiter d'être affinées en fonction de cas d'utilisation et de conditions matérielles spécifiques.
- Dépendance : une dépendance excessive aux recommandations du fabricant peut limiter l’exploration de paramètres optimisés pour des applications uniques.
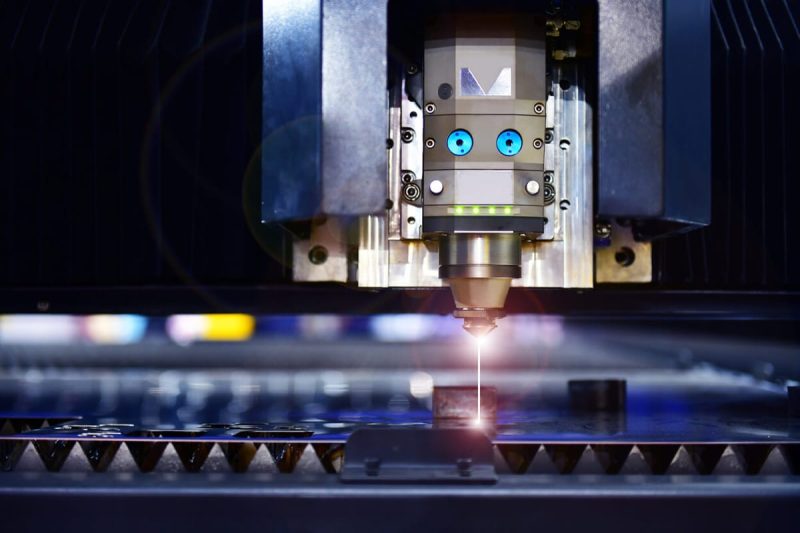
Considérations pratiques pour la sélection de la puissance de découpe laser
Spécifications de la machine
Puissance de sortie maximale et minimale
- Portée : Assurez-vous que votre machine peut gérer les paramètres de puissance requis pour votre matériau. Les lasers à fibre vont généralement de 1 000 à 12 000 watts (pour les métaux), tandis que les lasers CO2 vont de 60 à 600 watts (pour les non-métaux).
- Flexibilité : Les machines avec une large plage de puissance offrent une plus grande flexibilité pour couper différents matériaux et épaisseurs.
Qualité du faisceau
- Taille du foyer : La qualité du faisceau laser affecte la précision de la découpe. Une qualité de faisceau élevée et une taille focale plus petite permettent des découpes plus fines et plus précises.
- Stabilité : la qualité constante du faisceau garantit des coupes uniformes et réduit le besoin de réglages fréquents.
Vitesse de coupe et accélération
- Capacité de vitesse : une puissance laser plus élevée permet des vitesses de coupe plus rapides, mais les composants mécaniques de la machine doivent prendre en charge ces vitesses sans compromettre la précision.
- Accélération : Une machine dotée de capacités d'accélération élevées peut gérer des changements rapides de direction de coupe, ce qui permet de réaliser des conceptions complexes.
Système de contrôle
- Logiciel : Un logiciel de contrôle avancé peut optimiser les chemins de coupe et les paramètres de puissance, améliorant ainsi l'efficacité et la qualité.
- Intégration : Assurez-vous que le système de contrôle peut être parfaitement intégré à d’autres équipements et logiciels de production pour simplifier le fonctionnement.
Coût et efficacité énergétique
Les coûts d'exploitation
- Consommation électrique : les réglages de puissance laser plus élevés consomment davantage d'électricité. Évaluez les besoins énergétiques et les coûts d'exploitation associés aux différents niveaux de puissance.
- Gaz auxiliaire : Le type et la quantité de gaz auxiliaire utilisé (par exemple, oxygène, azote, air comprimé) peuvent affecter le coût total. Des réglages de puissance plus élevés peuvent nécessiter davantage de gaz auxiliaire pour maintenir la qualité de coupe. Si vous souhaitez en savoir plus sur les gaz auxiliaires, consultez le «Effet de la sélection de gaz auxiliaire sur la découpe laser" article.
Investissement initial VS épargne à long terme
- Coût initial : une machine de découpe laser plus puissante nécessite généralement un investissement initial plus élevé. Cependant, elle peut permettre de réaliser des économies à long terme en augmentant la vitesse et l'efficacité de la découpe.
- Gain d'efficacité : un laser plus puissant peut réduire le temps de découpe et augmenter le rendement de production, économisant ainsi des dépenses de main-d'œuvre et d'exploitation.
Efficacité énergétique
- Efficacité du laser : les générateurs laser à fibre sont généralement plus économes en énergie que les générateurs laser à CO2. Tenez compte de l'efficacité énergétique du type de générateur laser lors de la sélection d'un réglage de puissance.
- Système de refroidissement : Un système de refroidissement efficace peut réduire la consommation d’énergie et prolonger la durée de vie du générateur laser.
Maintenance et temps d'arrêt
Maintenance de routine
- Fréquence : des réglages de puissance plus élevés accélèrent l'usure des composants de la machine. Créez un calendrier de maintenance régulier pour inspecter et remplacer les pièces selon les besoins.
- Pièces : Les composants critiques tels que les lentilles, les miroirs et les buses nécessitent un nettoyage et un remplacement fréquents pour maintenir des performances optimales.
Gestion des temps d'arrêt
- Temps d'arrêt planifiés : planifiez les activités de maintenance pendant les temps d'arrêt planifiés afin de minimiser les perturbations de la production.
- Maintenance préventive : mettez en œuvre une stratégie de maintenance préventive pour identifier et résoudre les problèmes potentiels avant qu'ils ne provoquent une panne de la machine.
Assistance du fabricant
- Contrats de service : envisagez les contrats de service et les packages d'assistance proposés par les fabricants. Ils peuvent vous apporter une tranquillité d'esprit et réduire le risque de temps d'arrêt prolongé.
- Assistance technique : Garantissez l’accès au support technique pour dépanner et optimiser les performances de la machine.
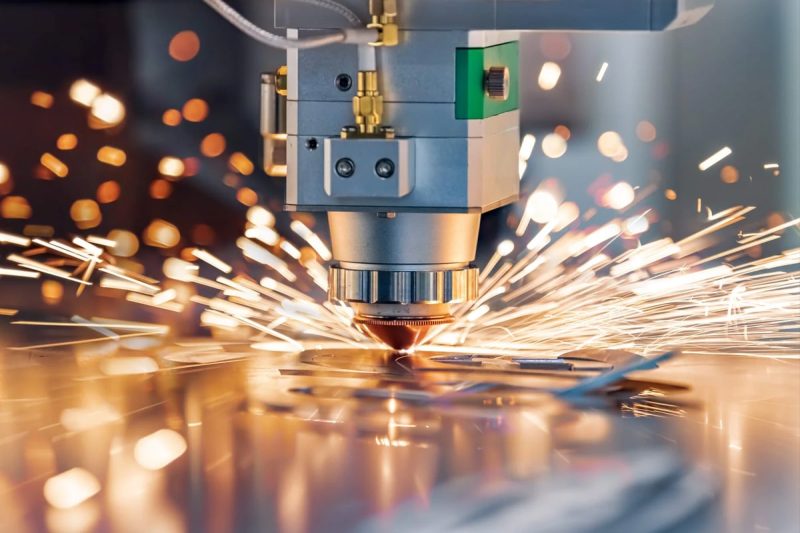
Dépannage des problèmes de puissance laser
Ne pas couper assez profondément
Puissance insuffisante
- Cause : Le réglage de la puissance du laser est peut-être trop faible pour couper le matériau.
- Solution : Augmentez progressivement la puissance du laser et effectuez des coupes d'essai jusqu'à atteindre la profondeur souhaitée. Assurez-vous que le niveau de puissance se situe dans la plage de fonctionnement sûre de la machine.
Vitesse de coupe trop élevée
- Cause : La vitesse de coupe peut être trop rapide, ne laissant pas suffisamment de temps au laser pour pénétrer complètement le matériau.
- Solution : Réduisez la vitesse de coupe pour concentrer davantage d'énergie sur le matériau. Équilibrez les réglages de vitesse et de puissance pour optimiser la profondeur de coupe.
Manque de concentration
- Cause : Le faisceau laser peut ne pas être correctement focalisé sur la surface du matériau, ce qui réduit l'efficacité de la coupe.
- Solution : Réglez la hauteur de mise au point pour vous assurer que le faisceau laser est correctement focalisé sur le matériau. Utilisez l'outil de mise au point de la machine ou ajustez manuellement si nécessaire.
Épaisseur de matériau
- Cause : Le matériau peut être plus épais que prévu, nécessitant plus de puissance ou plusieurs passages.
- Solution : Vérifiez l'épaisseur du matériau et ajustez le réglage de puissance en conséquence. Pour les matériaux très épais, envisagez plusieurs passages ou l'utilisation d'un laser plus puissant.
Brûlure ou fusion excessive
Puissance excessive
- Cause : Le réglage de la puissance du laser est peut-être trop élevé pour le matériau à couper.
- Solution : Réduisez progressivement la puissance du laser jusqu'à ce que le risque de brûlure ou de fusion soit réduit. Assurez-vous que le réglage de puissance est adapté au matériau.
Vitesse de coupe lente
- Cause : La vitesse de coupe peut être trop lente, ce qui provoque une accumulation excessive de chaleur et des brûlures.
- Solution : Augmentez la vitesse de coupe pour réduire le temps d'exposition à la chaleur. Trouvez le bon équilibre entre vitesse et puissance pour obtenir une coupe nette sans vous brûler.
Mise au point incorrecte
- Cause : La focalisation du laser peut être trop concentrée, provoquant une surchauffe dans une petite zone.
- Solution : Réglez la hauteur de mise au point de manière à ce que l'énergie laser soit répartie de manière plus uniforme sur la zone de coupe. Assurez-vous que le faisceau est correctement aligné et focalisé.
Sensibilité aux matériaux
- Cause : Certains matériaux sont plus sensibles à la chaleur et ont tendance à brûler ou à fondre.
- Solution : utilisez autant que possible des matériaux plus résistants à la chaleur. Pensez également à utiliser un gaz d'appoint tel que l'azote, qui peut aider à réduire les brûlures en déplaçant l'oxygène autour de la zone de coupe.
Résultats de coupe incohérents
Puissance de sortie variable
- Cause : La puissance de sortie du générateur laser peut fluctuer, ce qui entraîne des performances de coupe incohérentes.
- Solution : Vérifiez que le générateur laser ne présente aucun problème de stabilité et qu'il fonctionne correctement. Un entretien et un calibrage réguliers peuvent contribuer à maintenir une puissance de sortie constante.
Variations de matériaux
- Cause : Les variations dans les propriétés du matériau, telles que l’épaisseur ou la composition, peuvent entraîner une coupe incohérente.
- Solution : utilisez des matériaux uniformes de haute qualité pour garantir la cohérence du matériau. Effectuez des coupes d'essai sur différents lots de matériaux pour ajuster les paramètres selon les besoins.
Étalonnage incorrect de la machine
- Cause : La machine n'est peut-être pas correctement calibrée, ce qui affecte la précision et la cohérence de la coupe.
- Solution : étalonnez régulièrement la machine de découpe laser conformément aux instructions du fabricant. Vérifiez l'absence de problèmes mécaniques ou de désalignements susceptibles d'affecter les performances de découpe.
Optique sale ou endommagée
- Cause : Des optiques sales ou endommagées peuvent disperser le faisceau laser, ce qui entraîne des résultats de coupe incohérents.
- Solution : nettoyez régulièrement les optiques et inspectez-les pour détecter tout dommage. Remplacez les composants endommagés pour garantir une qualité et une cohérence optimales du faisceau.
Facteurs environnementaux
- Cause : Les changements de température ambiante, d’humidité ou de flux d’air peuvent affecter le processus de coupe.
- Solution : Maintenez un environnement contrôlé pour votre machine de découpe laser. Assurez des niveaux de température et d'humidité constants pour réduire l'impact des facteurs environnementaux sur le processus de découpe.
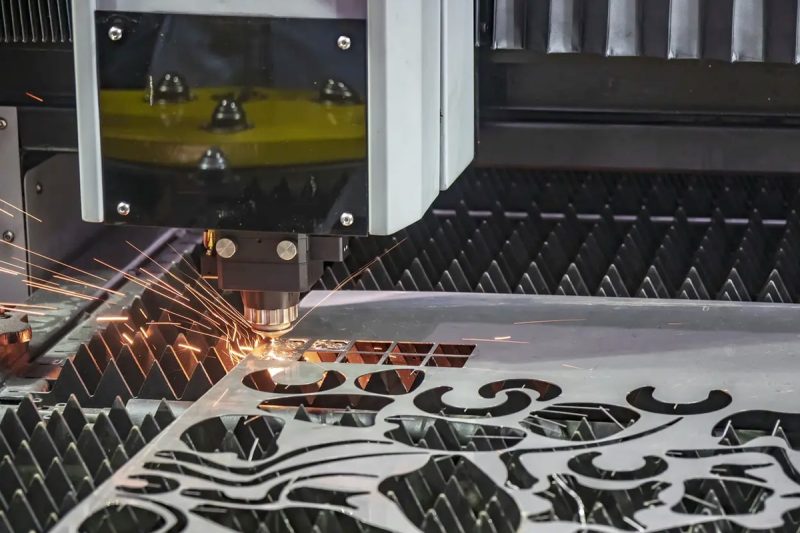
Résumé
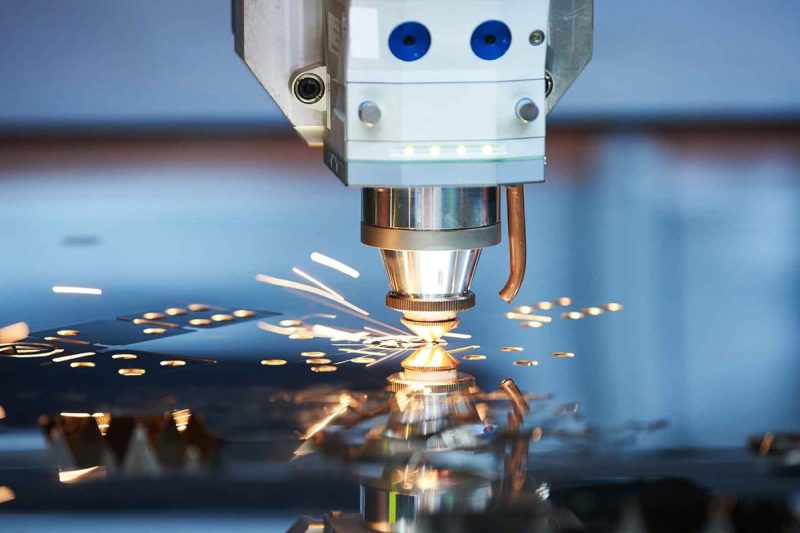
Obtenez des solutions de découpe laser
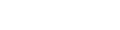
- [email protected]
- [email protected]
- +86-19963414011
- No. 3 Zone A, zone industrielle de Lunzhen, ville de Yucheng, province du Shandong.