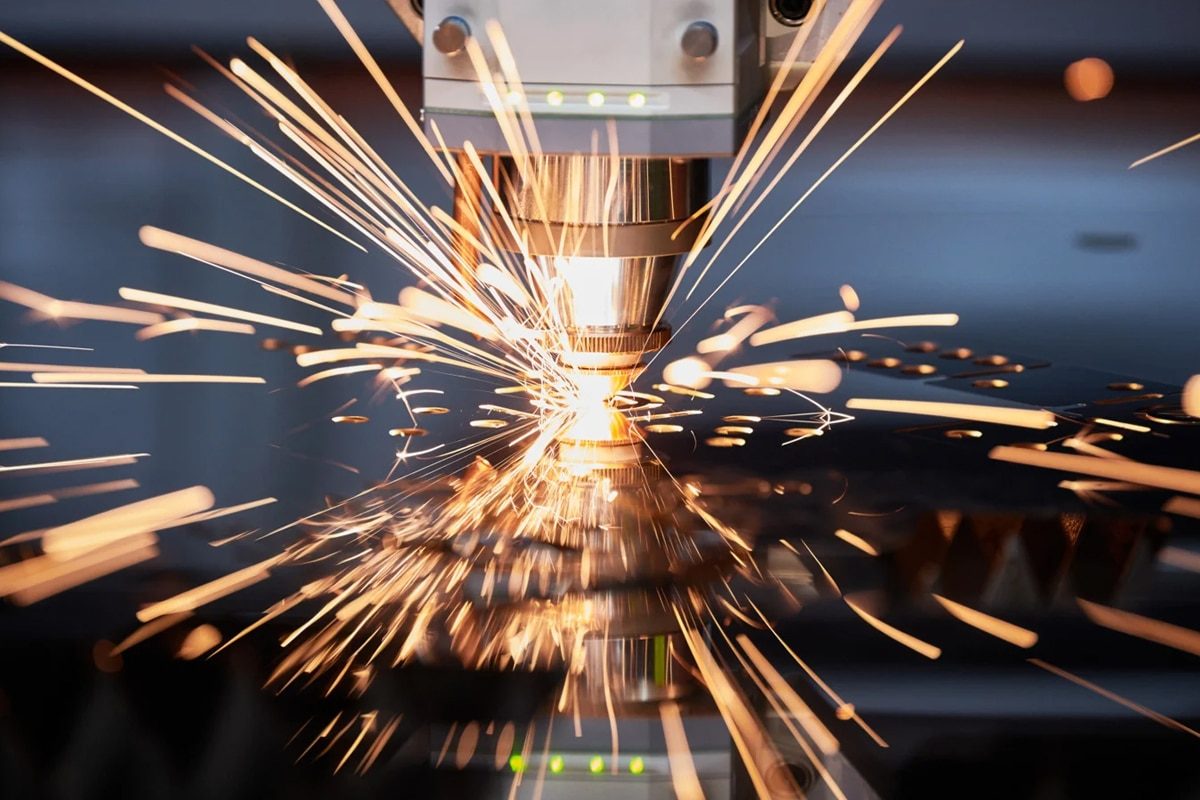
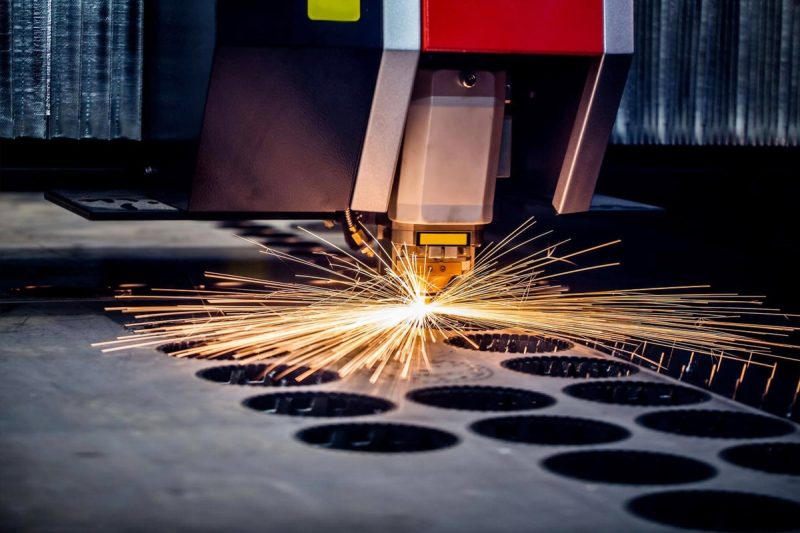
Présentation de la découpe laser
Comment fonctionne la découpe laser
La découpe au laser est un procédé thermique sans contact qui utilise un faisceau laser focalisé pour faire fondre, brûler ou vaporiser un matériau, ce qui permet d'obtenir un bord de coupe net et précis. Voici une description étape par étape du processus :
- Source laser : un faisceau laser est généré en stimulant un milieu laser, généralement du CO2, une fibre ou du YAG, dans une chambre scellée.
- Distribution du faisceau : Le faisceau laser est dirigé à travers des miroirs ou des fibres optiques et focalisé sur le matériau à l'aide d'une lentille, ce qui produit une source de chaleur hautement concentrée.
- Tête de focalisation et de découpe : Le faisceau laser est dirigé à travers une tête de découpe, qui contient également une buse émettant un gaz d'assistance (inerte ou réactif) pour faciliter la découpe et l'élimination du matériau.
- Contrôle CNC : Le mouvement de la tête laser et du matériau est contrôlé par un système CNC, qui guide précisément le chemin laser selon une conception programmée.
- Processus de coupe : Le faisceau focalisé interagit avec le matériau, soit en le faisant fondre, en le brûlant ou en le vaporisant, tandis que le gaz d'assistance souffle les débris et le matériau fondu de la zone de coupe.
Avantages de la découpe laser
- Haute précision et exactitude : la découpe laser permet de découper des formes complexes et complexes avec des tolérances serrées, réduisant ainsi le besoin de traitement secondaire.
- Polyvalence : Il peut couper une large gamme de matériaux, y compris métaux, plastiques, bois, céramique et plus encore, ce qui le rend hautement adaptable à tous les secteurs.
- Déchet de matériau minimal : la saignée laser étroite (largeur de coupe) garantit un gaspillage de matériau minimal, optimisant ainsi le rendement et réduisant les coûts.
- Coupes nettes et finition réduite : la découpe au laser produit des bords nets avec un minimum de bavures, éliminant ou réduisant souvent le besoin de post-traitement.
- Traitement à grande vitesse : par rapport aux méthodes traditionnelles, la découpe laser peut accomplir les tâches plus rapidement, améliorant ainsi la productivité et réduisant les délais.
- Procédé sans contact : Comme le faisceau laser ne touche pas physiquement le matériau, le risque de déformation est moindre, en particulier pour les matériaux fins ou délicats.
- Compatibilité d'automatisation : les systèmes de découpe laser peuvent être facilement intégrés à des solutions automatisées, améliorant ainsi l'efficacité et la cohérence de la production.
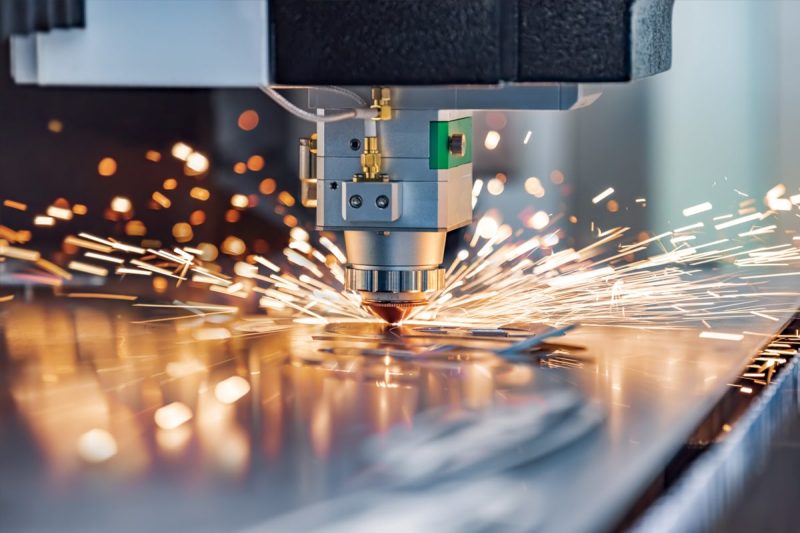
Les trois principaux types de découpe laser
Découpe par fusion (fusion et soufflage)
Explication du processus
Les étapes clés de la découpe par fusion sont :
- Fusion : Le faisceau laser concentre une énergie intense sur une petite zone, chauffant et faisant fondre rapidement le matériau.
- Éjection du matériau : le gaz d'assistance inerte souffle le matériau en fusion loin de la coupe, empêchant la resolidification et garantissant un bord lisse.
- Découpe continue : lorsque le laser se déplace le long du chemin désigné, ce processus se répète, créant une coupe continue.
Matériaux adaptés à la découpe par fusion
La découpe par fusion est idéale pour les matériaux qui nécessitent des bords de haute qualité, sans oxydation. Les matériaux appropriés comprennent :
- Acier inoxydable:Généralement coupé à l'azote pour éviter la formation d'oxyde.
- Aluminium et ses alliages : Nécessite une puissance laser plus élevée en raison de la réflectivité et de la conductivité thermique élevées.
- Alliages de titane et de nickel : bénéfiques pour les applications aérospatiales et médicales où l’intégrité des matériaux est essentielle.
- Métaux non ferreux : tels que laiton et cuivre, bien qu'ils puissent nécessiter des lasers spécialisés en raison de la réflectivité.
Avantages de la découpe par fusion
- Bords sans oxyde : l’utilisation de gaz inerte empêche l’oxydation, éliminant ainsi le besoin d’élimination de l’oxyde après la coupe.
- Haute précision et qualité : produit des coupes lisses et nettes avec une distorsion thermique minimale.
- Post-traitement minimal : réduit le besoin d’opérations de finition secondaires.
- Convient aux géométries complexes : peut couper avec précision des formes complexes et des détails fins.
Applications de la découpe par fusion
- Industrie aérospatiale : Fabrication de composants nécessitant précision et finitions de haute qualité.
- Fabrication de dispositifs médicaux : production d'instruments chirurgicaux et d'implants répondant à des normes d'hygiène strictes.
- Electronique : Découpe de pièces pour appareils électroniques où la précision est primordiale.
- Industrie Automobile : Fabrication de pièces nécessitant des bords de haute qualité pour l'assemblage et l'esthétique.
Considérations techniques
- Puissance laser : Une puissance adéquate est nécessaire pour faire fondre le matériau efficacement, en particulier pour les sections plus épaisses.
- Pression du gaz d’assistance : un gaz inerte à haute pression est essentiel pour l’élimination efficace du matériau en fusion.
- Position de mise au point : une mise au point précise garantit une concentration d'énergie optimale et une efficacité de coupe.
- Conception de la buse : une sélection appropriée de la buse peut améliorer le flux de gaz et améliorer la qualité de coupe.
- Réflectivité du matériau : les matériaux hautement réfléchissants comme l'aluminium peuvent nécessiter des lasers ou des revêtements spécialisés pour empêcher la réflexion du faisceau.
Découpe au chalumeau (découpe par fusion réactive)
Explication du processus
Étapes clés de l'oxycoupage :
- Chauffage : Le faisceau laser chauffe le matériau jusqu'à sa température d'allumage.
- Réaction exothermique : l’oxygène réagit avec le métal chauffé, le brûlant et générant de la chaleur supplémentaire.
- Enlèvement de matière : L'oxyde fondu est emporté par le flux d'oxygène, créant ainsi la coupe.
Matériaux adaptés à la découpe au chalumeau
Le découpage au chalumeau est plus efficace sur les métaux ferreux qui peuvent s'oxyder, tels que :
- Acier Carbone:Le matériau principal pour le découpage au chalumeau en raison de sa nature réactive avec l'oxygène.
- Aciers faiblement alliés : Aciers contenant un faible pourcentage d’éléments d’alliage.
- Acier doux : couramment utilisé dans la construction et la fabrication.
Avantages du découpage au chalumeau
- Épaisseur de coupe : Capable de couper des matériaux plus épais par rapport à la découpe par fusion avec la même puissance laser.
- Besoin réduit en puissance laser : La réaction exothermique complète le laser, permettant une découpe efficace avec une puissance moindre.
- Vitesse de coupe accrue : particulièrement efficace sur les sections épaisses d'acier.
- Rentable : l’oxygène est moins cher que les gaz inertes comme l’azote ou l’argon.
Applications du découpage au chalumeau
- Fabrication lourde : Fabrication de composants structurels tels que des poutres et des plaques.
- Construction navale : Découpe de grandes sections d'acier pour coques et autres structures.
- Engins de chantier : Fabrication de pièces d'équipements lourds.
- Centres de services d'acier : Traitement de tôles et plaques d'acier pour diverses industries.
Considérations techniques
- Oxydation des bords coupés : Le processus produit des bords oxydés, ce qui peut nécessiter un post-traitement comme le meulage ou le sablage si un bord propre est nécessaire.
- Zone affectée thermiquement (ZAT) : ZAT plus grande par rapport aux autres méthodes de coupe, ce qui peut affecter les propriétés mécaniques du matériau à proximité de la coupe.
- Pureté du gaz d'assistance : l'oxygène de haute pureté améliore la consistance et la qualité de la coupe.
- Focalisation et alignement du laser : essentiels pour initier et maintenir la réaction exothermique.
- Épaisseur du matériau : Idéal pour les matériaux plus épais où la réaction exothermique offre le plus d'avantages.
Découpe par sublimation (découpe par vaporisation)
Explication du processus
Étapes clés de la découpe par sublimation :
- Vaporisation : Le faisceau laser chauffe rapidement le matériau jusqu’à son point d’ébullition, provoquant sa vaporisation.
- Éjection du matériau : Le gaz d’assistance expulse le matériau vaporisé de la zone de coupe.
- Découpe de précision : L’absence de matière fondue permet des coupes précises avec des effets thermiques minimes.
Matériaux adaptés à la découpe par sublimation
La découpe par sublimation est idéale pour les matériaux ayant un point de fusion bas ou ayant tendance à brûler ou à fondre difficilement. Les matériaux appropriés comprennent :
- Bois et Produits en papier : Pour la gravure et les découpes précises.
- Plastiques et polymères : tels que acryliques, polycarbonate, et d’autres thermoplastiques.
- Textiles et Tissus:Coupe sans effilochage ni endommagement du matériau.
- Céramiques et composites : matériaux fragiles ou ayant des points de fusion élevés.
- Métaux minces : lorsqu'une précision extrême est requise.
Avantages de la découpe par sublimation
- Haute précision et détail : idéal pour les conceptions complexes et les détails fins en raison de la largeur de trait minimale.
- Coupes nettes : produit des bords lisses sans bavures ni résidus fondus.
- Dommages thermiques minimes : l’apport de chaleur réduit minimise la zone affectée par la chaleur.
- Polyvalence : Capable de traiter une large gamme de matériaux non métalliques.
- Procédé sans contact : élimine les contraintes mécaniques sur les matériaux délicats.
Applications de la découpe par sublimation
- Industrie électronique : Découpe et perçage de circuits imprimés (PCB).
- Signalisation et affichage : Découpe précise d'acryliques et de plastiques pour des affichages de haute qualité.
- Dispositifs médicaux : Fabrication de composants nécessitant des dimensions exactes et des bords nets.
- Mode et Textiles : Découpe de tissus pour vêtements et accessoires sans effilochage des bords.
- Art et artisanat : création de motifs détaillés en bois, papier et autres matériaux.
Considérations techniques
- Densité de puissance laser : une densité de puissance élevée est nécessaire pour obtenir la vaporisation, en particulier pour les matériaux avec des températures de vaporisation élevées.
- Épaisseur du matériau : particulièrement adapté aux matériaux fins ; les matériaux épais nécessitent beaucoup plus d'énergie.
- Sélection de gaz d'assistance : les gaz inertes empêchent les réactions chimiques indésirables et aident à éliminer les matières vaporisées.
- Exigences en matière de ventilation : La vaporisation produit des fumées qui peuvent nécessiter des systèmes d’extraction et de filtration appropriés.
- Propriétés des matériaux : Il est essentiel de comprendre les propriétés thermiques du matériau pour éviter les brûlures ou la carbonisation.
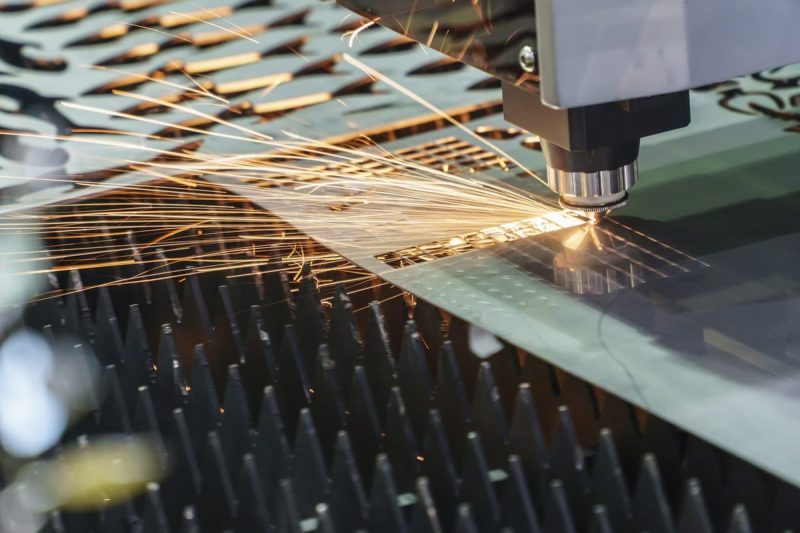
Comparaison des trois méthodes de coupe
Mécanisme de processus
- Découpe par fusion (fusion et soufflage) : cette méthode consiste à faire fondre le matériau à l'aide d'un laser et à souffler le métal fondu avec un gaz d'assistance inerte (par exemple, de l'azote ou de l'argon). Elle produit des bords nets et sans oxyde et est idéale pour la découpe de précision.
- Découpe au chalumeau (découpe par fusion réactive) : la découpe au chalumeau utilise l'oxygène comme gaz d'assistance, qui réagit avec le matériau chauffé pour créer une réaction exothermique qui ajoute de la chaleur au processus, permettant ainsi une découpe efficace de matériaux épais comme l'acier au carbone. Cependant, elle laisse un bord oxydé.
- Découpe par sublimation (découpe par vaporisation) : ce procédé vaporise directement le matériau à l'aide de la chaleur du faisceau laser, avec un gaz inerte utilisé pour expulser le matériau vaporisé. Il est particulièrement adapté aux découpes précises sur des matériaux fins et non métalliques.
Compatibilité des matériaux
- Découpe par fusion : convient à une large gamme de matériaux, en particulier les métaux tels que l'acier inoxydable, l'aluminium et les métaux non ferreux. Elle permet des coupes de haute qualité, sans oxydation.
- Découpe au chalumeau : principalement utilisée pour la découpe de métaux ferreux tels que l'acier au carbone et les aciers faiblement alliés en raison de sa dépendance à une réaction oxydante.
- Découpe par sublimation : idéale pour les matériaux fins, notamment le bois, les plastiques, les textiles, la céramique et certains métaux, où des coupes précises et complexes sont nécessaires.
Qualité des bords
- Découpe par fusion : produit des bords nets et lisses avec un minimum de bavures et aucune oxydation, réduisant ainsi le besoin de post-traitement.
- Découpe au chalumeau : produit des bords oxydés qui peuvent nécessiter une finition supplémentaire, comme le meulage, pour éliminer la couche d'oxyde si une surface propre est souhaitée.
- Découpe par sublimation : produit des bords exceptionnellement nets, avec une distorsion thermique ou des bavures minimales, ce qui le rend idéal pour les applications où la qualité des bords est primordiale.
Capacité de vitesse et d'épaisseur de coupe
- Découpe par fusion : efficace pour les matériaux minces à moyennement épais avec une grande précision, mais sa vitesse de coupe diminue à mesure que l'épaisseur du matériau augmente.
- Découpe au chalumeau : Offre des vitesses de coupe élevées pour les matériaux épais grâce à la réaction exothermique avec l'oxygène, ce qui la rend efficace pour la fabrication lourde et les composants structurels.
- Découpe par sublimation : particulièrement adaptée aux matériaux fins en raison de la grande énergie nécessaire à la vaporisation. Bien qu'elle offre une grande précision, elle peut ne pas être efficace pour les sections plus épaisses.
Utilisation du gaz d'assistance
- Découpe par fusion : des gaz inertes comme l’azote ou l’argon sont utilisés pour empêcher l’oxydation et produire un bord de coupe net.
- Découpe au chalumeau : elle utilise l’oxygène, qui réagit avec le métal pour améliorer le processus de découpe grâce à une réaction exothermique.
- Découpe par sublimation : utilise souvent un gaz inerte ou aucun gaz, selon le matériau, pour expulser le matériau vaporisé.
Zone affectée par la chaleur (ZAT)
- Découpe par fusion : produit une zone affectée par la chaleur relativement petite en raison de sa concentration sur la fusion sans réactions supplémentaires.
- Découpe au chalumeau : cela crée une zone affectée par la chaleur plus large en raison de la réaction exothermique, ce qui peut altérer les propriétés du matériau près du bord coupé.
- Découpe par sublimation : minimise la zone affectée par la chaleur grâce à une vaporisation rapide, préservant l'intégrité du matériau environnant.
Applications
- Découpe par fusion : idéale pour les applications où une haute précision et des bords sans oxydation sont essentiels, comme dans les secteurs de l'aérospatiale, de la médecine et de l'électronique.
- Découpe au chalumeau : couramment utilisée dans la fabrication lourde, la construction, la construction navale et d'autres applications nécessitant la découpe de sections d'acier épaisses.
- Découpe par sublimation : idéale pour les travaux détaillés sur des matériaux fins ou délicats, comme dans les secteurs de l'électronique, du textile, de l'art et du design.
Considérations relatives aux coûts et à l’efficacité
- Découpe par fusion : nécessite une puissance plus élevée et des gaz inertes plus chers, mais offre une qualité de bord et une précision supérieures.
- Découpe au chalumeau : plus rentable pour la découpe d'acier au carbone épais en raison de l'utilisation d'oxygène, mais le post-traitement peut entraîner des coûts supplémentaires.
- Découpe par sublimation : consomme beaucoup d'énergie pour les matériaux plus épais, ce qui la rend plus adaptée aux applications spécialisées avec des matériaux fins.
Tableau récapitulatif
Fonctionnalité | Découpe par fusion | Découpage à la flamme | Découpe par sublimation |
Mécanisme de processus | Fait fondre le matériau, le gaz inerte élimine la masse fondue | Utilise l'oxygène pour une réaction exothermique | Vaporise le matériau |
Matériels | Les métaux comme l'acier inoxydable, l'aluminium | Acier au carbone, aciers faiblement alliés | Métaux minces, non-métaux, plastiques |
Qualité des bords | Propre, sans oxyde | Oxydé, peut nécessiter une finition | Propre, précis |
Épaisseur de coupe | Fin à moyen | Matériaux épais | Matériaux fins |
Gaz d'assistance | Gaz inerte (par exemple, azote, argon) | Oxygène | Gaz inerte ou aucun |
Zone dangereuse | Petit | Grand | Minimal |
Applications | Aérospatiale, électronique, médical | Composants structurels, fabrication lourde | Électronique, textile, art |
Rentabilité | Coût plus élevé, haute précision | Économique pour les coupes épaisses | Haute précision, matériaux fins |
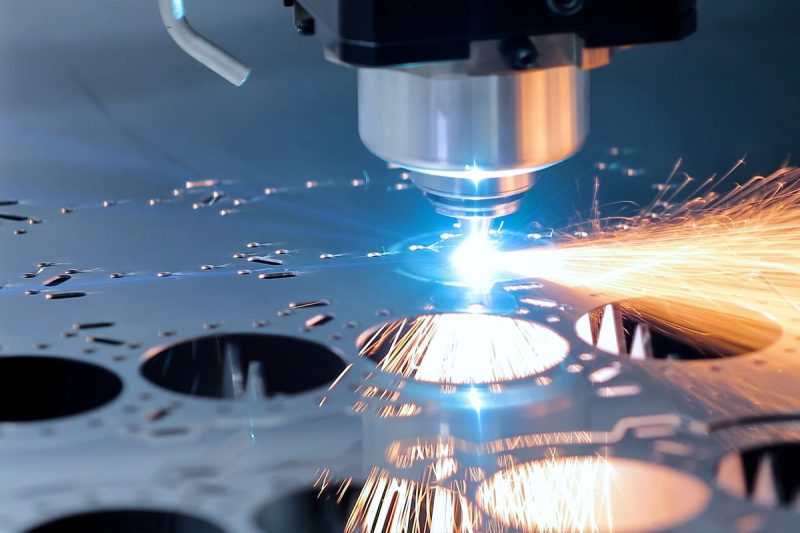
Choisir le bon type de méthode de coupe
Type de matériau et propriétés
- Matériaux métalliques : pour les métaux tels que l'acier inoxydable, l'aluminium et d'autres métaux non ferreux qui nécessitent des bords nets et sans oxyde, la découpe par fusion est souvent la meilleure option. L'utilisation de gaz inertes empêche l'oxydation, ce qui permet des coupes précises et de haute qualité.
- Métaux ferreux : si vous coupez de l'acier au carbone ou d'autres matériaux ferreux, la découpe au chalumeau offre d'excellentes performances grâce à l'utilisation d'oxygène pour créer une réaction exothermique. Cette méthode permet une découpe efficace de matériaux épais, mais peut entraîner des bords oxydés.
- Matériaux non métalliques et fins : la découpe par sublimation est idéale pour les matériaux non métalliques comme le plastique, le bois, la céramique et les textiles. Elle est particulièrement adaptée aux motifs complexes et aux coupes précises, en particulier pour les matériaux fins.
Qualité de bord souhaitée
- Bords propres et sans oxydation : si un bord propre et de haute qualité sans oxydation est essentiel pour votre application, la découpe par fusion est préférée en raison de l'utilisation de gaz inertes qui empêchent l'oxydation pendant le processus de découpe.
- Bords oxydés : dans les cas où une forte réaction exothermique est nécessaire et où les bords oxydés sont acceptables ou peuvent être post-traités, la découpe au chalumeau est une option appropriée.
- Haute précision et bords lisses : pour les applications qui exigent une précision extrême et des bords lisses avec une distorsion thermique minimale, telles que l'électronique et les beaux-arts, la découpe par sublimation est le bon choix.
Épaisseur de matériau
- Épaisseur fine à moyenne : la découpe par fusion excelle dans les matériaux d'épaisseur fine à moyenne, offrant des bords précis et de haute qualité.
- Matériaux épais : la découpe au chalumeau est mieux adaptée aux matériaux plus épais, car la réaction exothermique permet une découpe efficace avec des besoins en puissance laser inférieurs.
- Matériaux très fins : la découpe par sublimation est idéale pour les matériaux très fins et offre une grande précision pour les motifs et les formes complexes.
Vitesse et efficacité de coupe
- Production à grande vitesse : si la vitesse est une priorité, en particulier pour la découpe de plaques d'acier épaisses, la découpe au chalumeau est très efficace grâce à sa réaction exothermique à base d'oxygène.
- La précision plutôt que la vitesse : pour les applications où la précision est plus importante que la vitesse, la découpe par fusion et la découpe par sublimation offrent des résultats supérieurs.
- Production par lots ou travail personnalisé : tenez compte de la nature de votre production. La découpe par fusion est adaptée au traitement par lots de haute précision, tandis que la découpe par sublimation est idéale pour les travaux personnalisés nécessitant des détails complexes.
Considérations relatives aux coûts
- Coûts des gaz auxiliaires : la découpe par fusion utilise des gaz inertes tels que l'azote ou l'argon, qui peuvent être plus chers que l'oxygène utilisé dans la découpe au chalumeau. Cependant, elle offre une qualité de coupe supérieure.
- Consommation électrique : la découpe par sublimation peut être gourmande en énergie pour les matériaux épais, mais elle est efficace pour les sections fines. La découpe au chalumeau nécessite une puissance laser plus faible en raison de la chaleur générée par la réaction de l'oxygène, ce qui la rend rentable pour les coupes épaisses.
- Exigences de post-traitement : Le besoin de post-traitement (par exemple, l'élimination des oxydes lors du découpage à la flamme) peut augmenter les coûts globaux, ce qui doit être pris en compte dans la décision.
Exigences de candidature
- Applications critiques en matière de précision : pour les industries telles que l'aérospatiale, l'électronique et la fabrication de dispositifs médicaux où la précision et les bords nets sont essentiels, la découpe par fusion et la découpe par sublimation sont préférées.
- Fabrication robuste : la découpe au chalumeau est idéale pour les composants structurels, les machines lourdes et d’autres applications nécessitant une découpe de métal épais.
- Motifs complexes : si des détails fins et des coupes complexes sont nécessaires, en particulier pour les matériaux non métalliques, la découpe par sublimation est la meilleure option.
Considérations relatives à l'équipement et à la configuration
- Puissance et type de laser : Assurez-vous que le système laser que vous choisissez possède une puissance adéquate et est compatible avec la méthode de découpe sélectionnée. Par exemple, les métaux hautement réfléchissants peuvent nécessiter des sources laser spécialisées dans la découpe par fusion.
- Disponibilité des gaz d'assistance : Tenez compte de la disponibilité et du coût des gaz d'assistance. Le découpage à la flamme utilise généralement de l'oxygène, tandis que le découpage par fusion nécessite des gaz inertes.
- Automatisation et intégration : si vous souhaitez intégrer la découpe laser dans une ligne de production automatisée, la découpe par fusion et la découpe par sublimation offrent souvent une meilleure compatibilité en raison de leurs capacités de précision.
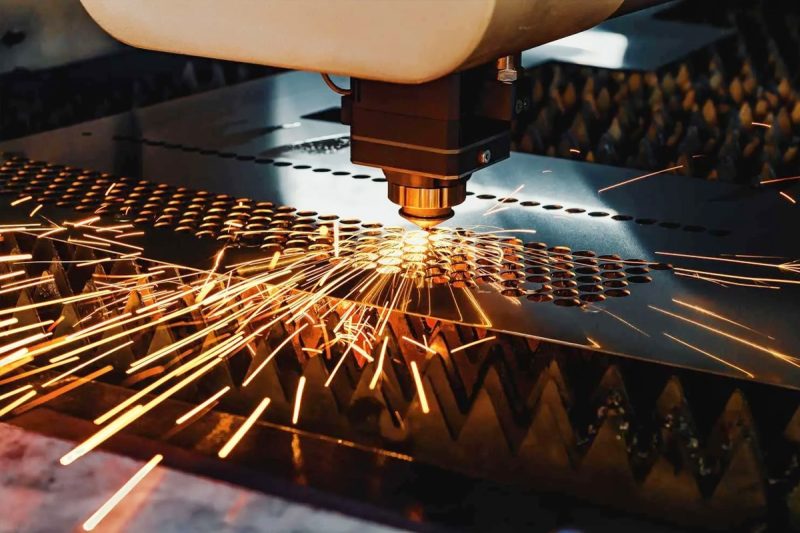
Résumé
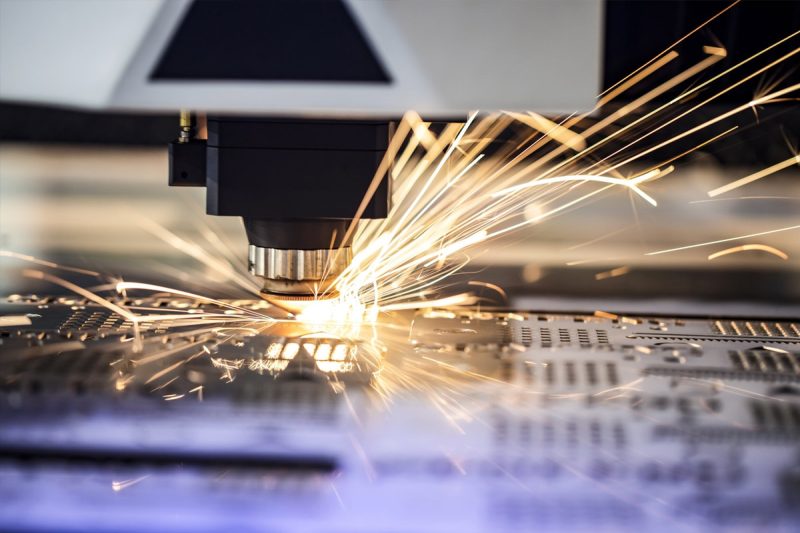
Obtenez des solutions de découpe laser
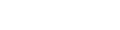
- [email protected]
- [email protected]
- +86-19963414011
- No. 3 Zone A, zone industrielle de Lunzhen, ville de Yucheng, province du Shandong.