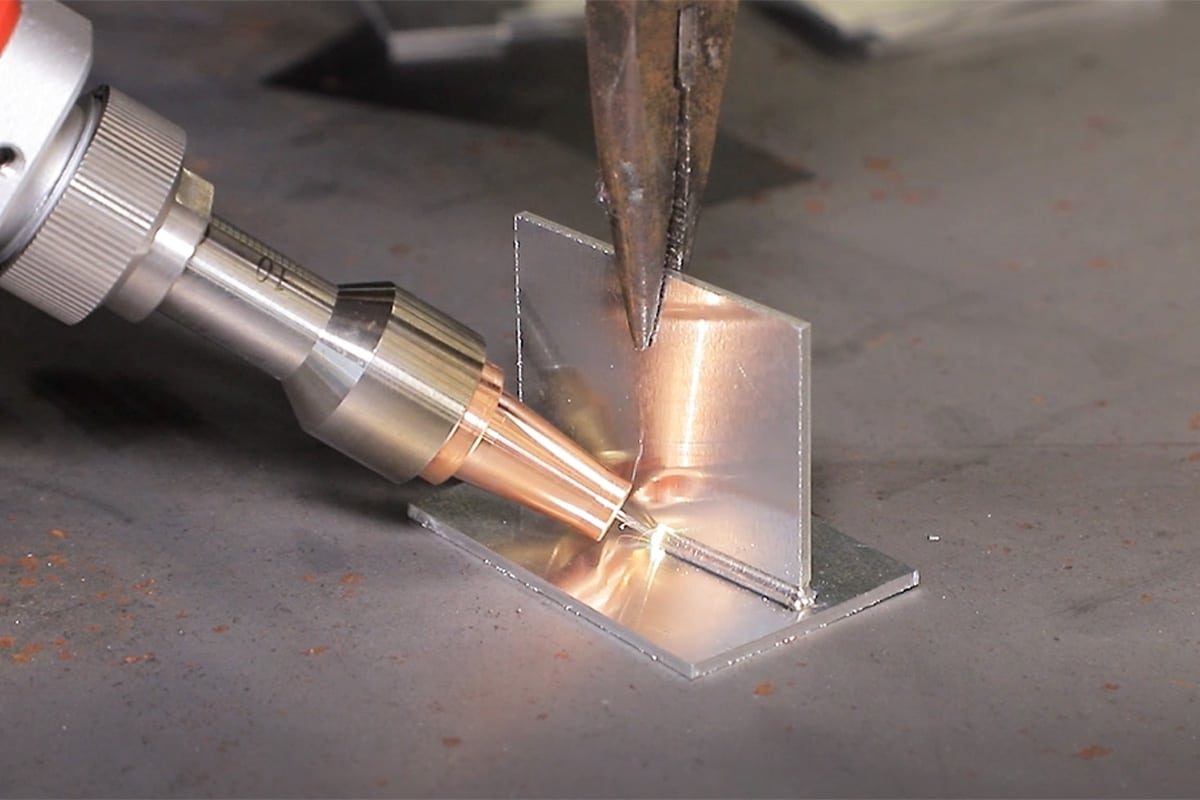
Guide to Laser Welding Stainless Steel
Stainless steel is widely used in many fields of modern manufacturing, such as automobiles, aerospace, medicine, and construction, due to its excellent corrosion resistance, high strength, heat resistance, and easy cleaning. In these industries, stainless steel is used to produce components that withstand high temperatures and corrosive environments, such as automotive exhaust systems and medical devices. Compared with other materials, stainless steel’s high strength and oxidation resistance make it particularly suitable for maintaining long-term stability and functionality in extreme environments, making stainless steel products an indispensable part of daily life and high-end manufacturing.
However, stainless steel welding also brings some specific challenges, mainly in terms of material deformation, weld oxidation, and heat input control during welding. Due to the low thermal conductivity of stainless steel, it is easy to deform due to local high temperatures during traditional welding, affecting welding accuracy and weld quality. In addition, stainless steel is very easy to oxidize at high temperatures, and an undesirable oxide layer may form on the surface of the weld, affecting the appearance and corrosion resistance. Laser welding has successfully overcome these difficulties with its advantages of high precision, low heat impact, and high efficiency, becoming an ideal solution for stainless steel welding. It not only reduces the heat-affected zone and reduces the risk of deformation, but also achieves efficient and high-quality welding results.
Table of Contents
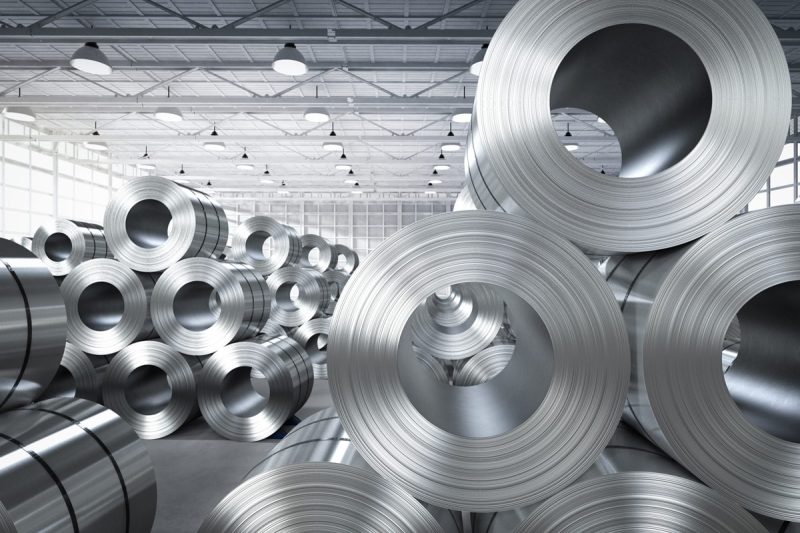
Characteristics of Stainless Steel
Stainless steel is an alloy based on iron, chromium, and nickel that is widely used in the manufacturing industry for its excellent corrosion resistance and high strength. Due to the different requirements of different application environments, the composition and characteristics of stainless steel will also vary accordingly. These differences make stainless steel excel in harsh environments, especially in places that need to withstand temperature fluctuations, humidity changes, and chemical corrosion.
Stainless Steel Performance Overview
- Corrosion resistance: When the chromium element in stainless steel comes into contact with oxygen, a dense passivation film will form on the surface, greatly enhancing the corrosion resistance of the material. This feature allows stainless steel to be used in humid or corrosive chemical environments.
- Heat resistance: Stainless steel can maintain high strength and stability in high-temperature environments. Different types of stainless steel can withstand operating environments ranging from hundreds of degrees to higher temperatures based on differences in composition design.
- Easy to clean: Stainless steel has a smooth surface and a self-cleaning effect, making it easy to clean and maintain, which is particularly important in industries with high hygiene requirements such as food and medicine.
Stainless Steel Types and Composition
Stainless steel can be classified according to its microstructure, composition and mechanical properties. The main types include:
- Austenitic stainless steel: It is composed of chromium, nickel, and a small amount of carbon, and has good toughness and plasticity. Austenitic stainless steel usually contains more than 8% nickel, which makes it have excellent oxidation resistance and corrosion resistance. It is widely used in food processing, medicine, building decoration, and other industries.
- Ferritic stainless steel: It mainly contains chromium and almost no nickel. It has good corrosion resistance and magnetism. Ferritic stainless steel has a simple composition and low cost. It is suitable for low-stress occasions such as automobile exhaust systems that require corrosion resistance.
- Martensitic stainless steel: It contains chromium and has a high carbon content. It is suitable for applications that require high strength and wear resistance, such as knives, turbine blades, etc. Due to its high hardness, martensitic stainless steel is suitable for occasions that need to withstand mechanical impact, but its corrosion resistance is slightly lower than that of austenitic stainless steel.
Challenges of Welding Stainless Steel
Although stainless steel has many advantages, it also faces some challenges during welding, and special attention should be paid to the following issues:
- Crack formation: Stainless steel is prone to hot cracks or cold cracks during welding, especially during rapid heating or cooling. These cracks can significantly reduce the strength and reliability of the weld.
- Deformation control: The thermal conductivity of stainless steel is low. During the welding process, the heat is more concentrated near the weld, resulting in higher local temperatures. It is prone to deformation after cooling, affecting the dimensional accuracy of the workpiece.
- Weld color change: The oxidation tendency of stainless steel is obvious during the welding process of stainless steel, and oxidative discoloration will occur on the surface of the weld, resulting in the color of the weld ranging from blue, and brown to black. This not only affects the appearance of the weld but may also reduce the anti-corrosion performance of the weld.
- Oxide layer protection: During high-temperature welding, an oxide layer is easily formed on the surface of stainless steel, weakening the corrosion resistance of the weld. Therefore, it is necessary to use argon, nitrogen and other protective gases to cover the welding area to prevent oxygen from contacting the weld surface and ensure the quality of the weld.
These challenges require optimizing welding parameters, selecting appropriate welding processes, and taking effective protective measures when welding stainless steel.
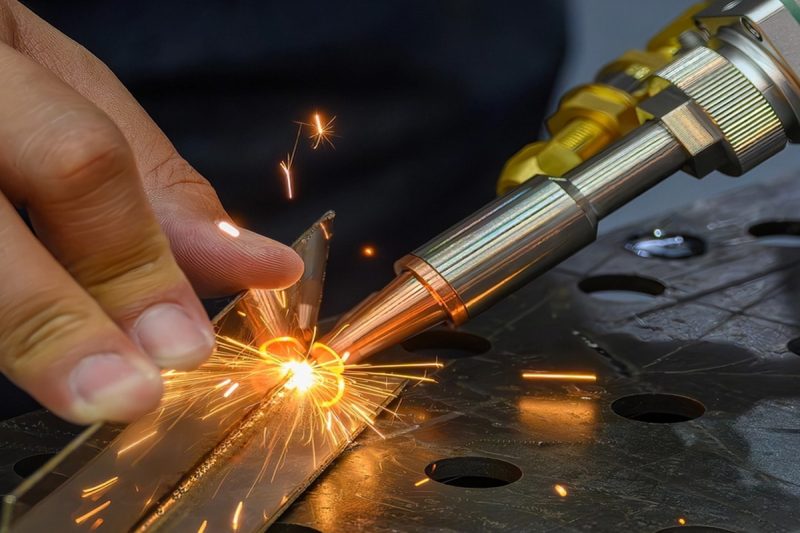
The principle of laser welding of stainless steel
Laser welding is an efficient and precise welding technology that uses a focused high-energy laser beam to melt stainless steel materials and achieve a stable connection through rapid cooling. Laser welding is particularly suitable for welding applications of heat-sensitive materials such as stainless steel due to its small heat-affected zone and high precision. According to the different welding thickness and application requirements, laser welding is mainly divided into two modes: thermal conduction welding and deep penetration welding, which are suitable for the connection of thin and thick stainless steel plates.
Laser Welding Process
- Thermal welding: The energy of thermal welding is concentrated on the surface of the material and diffused into the material through heat conduction. It is usually used to weld thinner materials. This welding mode has high requirements for the smoothness and fineness of the weld surface and is suitable for welding electronic components and precision instruments.
- Deep penetration welding: Deep penetration welding allows the laser to melt rapidly on the surface of stainless steel, forming a small molten pool and penetrating the material. The high temperature generated by the laser beam forms a small channel (called a “keyhole”) in the weld, and the laser energy is concentrated in the channel, making the welding depth greater. This welding method is suitable for thicker stainless steel plates and is widely used in high-strength welding occasions such as automobile manufacturing and pressure vessels.
Interaction of Laser with Stainless Steel
- Energy penetration: When the laser beam interacts with stainless steel, its high energy density quickly penetrates the surface of the stainless steel, instantly heating the local material to the melting point or even the vaporization temperature. The molten stainless steel metal forms a liquid in the molten pool and works together with the small hole structure generated by the laser to ensure a high-strength welding effect.
- Molten pool formation: Under the action of the laser, the metal molten pool is continuously heated by the laser to form a liquid metal area. The liquid metals will penetrate each other during the welding process to produce a strong joint area. The liquid metal inside the molten pool cools to form a solid weld that can withstand high mechanical stress.
- Weld quality: Due to the high energy density and small hole effect of laser welding, high-density connection of the weld can be achieved, and the weld strength is close to the strength of the parent material. In addition, due to the small heat-affected zone of laser welding, the deformation of the workpiece after welding is small, which reduces the oxidation loss of stainless steel materials under high temperature.
Key Parameters Affecting Welding
In the process of laser welding stainless steel, the welding effect is affected by several key parameters:
- Laser power: Laser power determines the amount of welding heat, which directly affects the welding depth and weld width. Higher laser power can deepen the welding penetration and is suitable for welding thick plate materials, but it is necessary to avoid excessive power causing over-melting of the material or cracking.
- Focus position: The focus position of the laser is crucial to the welding quality. The appropriate focus position can concentrate energy on the welding part and improve the welding strength and depth. Usually, the focus is slightly adjusted to the inside of the workpiece to achieve the best welding effect.
- Welding speed: The welding speed directly affects the welding efficiency and heat input. Too fast welding speed will result in incomplete welds or insufficient strength, while too slow speed may cause excessive heat input, material deformation or pores. Usually, the welding speed is optimized according to the material thickness and laser power to obtain an ideal weld.
- Shielding gas: When laser welding stainless steel, shielding gas (such as argon and nitrogen) must be used to cover the welding area to prevent the weld from contacting with oxygen in the air and avoid oxidation of the weld. The flow and selection of shielding gas will also affect the quality of the weld. The appropriate shielding gas can effectively prevent oxidation of the welding area and ensure the strength and appearance of the weld.
By optimizing these parameters, stable laser welding effects can be achieved and the quality and performance requirements of stainless steel in different application scenarios can be met.

Preparation for Laser Welding of Stainless Steel
Before laser welding stainless steel, reasonable preparation is a key step to ensure welding quality and efficiency. Material selection, joint design, and surface cleaning before welding will affect the strength, appearance, and durability of the final weld. Careful preparation can reduce welding defects and improve the stability of welding results.
Material Selection and Preparation
- Choose the right stainless steel material: The stainless steel material used for welding should have excellent heat resistance and corrosion resistance to reduce possible quality problems during welding. Commonly used stainless steel materials include austenitic stainless steel (such as 304, 316) and ferritic stainless steel (such as 430). Suitable materials can be selected according to welding application scenarios and composition requirements.
- Ensure material quality: Select high-quality stainless steel to ensure that the material surface is flat, crack-free, and pore-free to avoid excessive molten pool instability or crack expansion during welding. Materials with too many impurities should be avoided when selecting materials, otherwise the weld strength may be affected.
- Ensure uniform material thickness: Welding materials with uneven thickness will result in uneven laser energy distribution, affecting weld quality. Ensuring uniform material thickness helps to obtain consistent penetration depth and weld shape.
Connector Design Considerations
- Butt joint: Butt joints are suitable for parallel and adjacent material edges and are often used for thin stainless steel connections. Butt joints can provide higher weld strength, but require higher alignment accuracy to ensure weld continuity.
- Lap joints: Lap joints are suitable for overlapping material welding and are usually used for thick plates or heavily loaded parts. Lap joints can improve weld strength and toughness, but the size of the overlapping area needs to be appropriate to avoid excessive welding heat input causing deformation.
- Fillet joints: Fillet joints are used for welding two material edges at right angles and are widely used in structural parts and frame welding. Fillet joints need to consider the welding angle in stainless steel welding to ensure consistency in strength and appearance after welding.
- Welding gap and weld width: A properly designed welding gap and weld width can ensure uniform laser energy distribution and avoid excessive heat concentration causing material deformation or weld shrinkage. For thick stainless steel, a smaller welding gap is usually used to reduce thermal deformation.
Surface cleaning and pre-welding
The cleanliness of the stainless steel surface will significantly affect the stability and quality of laser welding. Uncleaned surfaces may produce impurities or oxides that affect the formation of the molten pool and the strength of the weld.
- Remove the oxide layer: Stainless steel often has an oxide layer on the surface, which will affect the effective absorption of the laser and reduce the welding effect. Laser cleaning or chemical cleaning agents can be used to remove the oxide layer to ensure that the laser energy can fully act on the surface of the material.
- Remove oil and impurities: Oil and impurities may cause uneven welding or pores. Anhydrous alcohol or special cleaning agents are required to remove surface contaminants. Pre-welding cleaning is particularly important when used for welding parts with high cleanliness requirements such as food and medical.
- Mechanical cleaning: For stubborn surface dirt, mechanical cleaning methods such as grinding or sandpaper treatment can be used to ensure a smooth surface. Mechanical cleaning should be cautious to avoid leaving scratches on the stainless steel surface, which will affect the beauty and strength of the welding.
- Use appropriate shielding gas: During pre-welding treatment, appropriate shielding gas (such as argon, and nitrogen) should also be selected according to the material properties. This will effectively prevent oxidation and pores during welding and ensure the quality and strength of the weld.
Through the above preparation work, the stability and welding effect of laser-welded stainless steel can be significantly improved, ensuring the durability and aesthetics of the weld in various application environments.
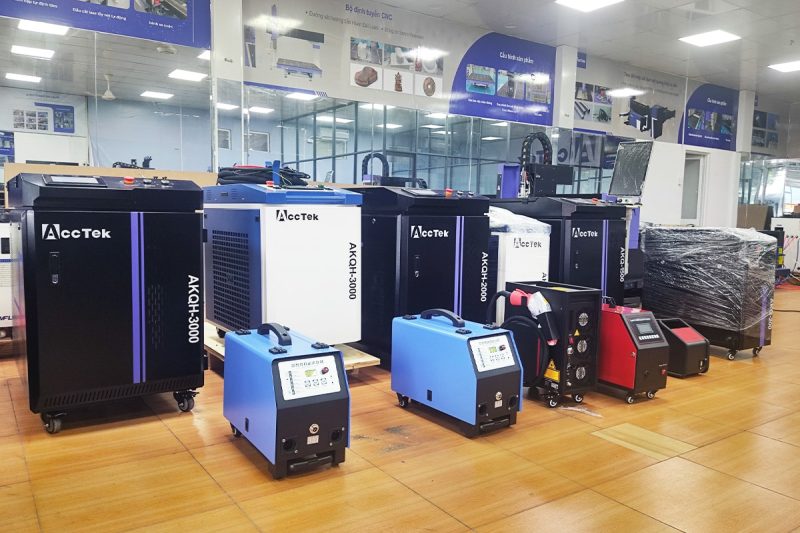
Stainless Steel Laser Welding Machine
Laser welding machines play a vital role in modern manufacturing, especially in welding applications of stainless steel. They provide efficient and precise welding solutions and are widely used in automotive, aerospace, medical equipment, and other industries. Choosing the right laser welding machine can significantly improve welding quality and production efficiency.
Types of Laser Welding Systems for Stainless Steel
There are two main types of laser welding systems on the market, each suitable for different welding needs of stainless steel.
Fiber Laser Welding Machine
- Fiber laser welding machines are widely used due to their high energy utilization and good beam transmission efficiency. Fiber laser generators can focus the laser beam precisely on the welding point, providing a stronger welding effect.
- This type of laser generator produces a smaller heat-affected zone during welding, reducing the risk of welding deformation and is suitable for precision welding and thin plate welding.
CO2 Laser Welding Machine
- CO2 laser welding machines are mainly suitable for welding thicker stainless steel plates. Although it is slightly less energy efficient than fiber laser welding machines, it is still an ideal choice for certain specific applications.
- The operation of this welding system requires higher control of gas flow and laser adjustment, which is suitable for large-scale production.
Laser Source and Parameter Selection
Selecting a suitable laser source and adjusting welding parameters are the key to ensuring the quality of stainless steel welding.
Laser Source Selection
- It is recommended to use a higher power fiber laser generator. Higher laser power can effectively increase the welding speed and depth, making the welding effect more ideal.
- When selecting a laser generator, it is necessary to consider the material thickness it is suitable for to ensure that it can meet the welding requirements of stainless steel of different thicknesses.
Parameter Adjustment
- Adjust the welding speed and laser power according to the thickness of the stainless steel plate. Thinner stainless steel plates require faster welding speeds and lower power to avoid deformation caused by excessive heat input.
- For thicker stainless steel plates, reducing the welding speed and increasing the laser power can ensure the depth and strength of the weld while maintaining a good weld appearance.
Auxiliary Equipment and Accessories
Auxiliary equipment and accessories play an important role in the laser welding process and can further improve the welding effect and quality.
Protective Gas
- Using argon or nitrogen as shielding gas can prevent oxidation and other adverse reactions during welding. The gas barrier formed by the shielding gas can protect the molten pool and ensure the cleanliness and quality of the weld.
- Reasonable selection of gas flow and type can help control the welding atmosphere and reduce the occurrence of weld defects.
Cooling System
- The cooling system is used to control the temperature generated during the welding process to prevent material deformation or weld degradation due to overheating.
- Proper cooling can extend the service life of the equipment and improve the stability and safety of the welding process.
Fixtures and Positioning Equipment
- The fixture and positioning equipment are used to fix the welding workpiece to ensure accurate docking and stability during the welding process. This is essential for high-precision welding.
- The flexible and adjustable fixture design can adapt to stainless steel workpieces of different shapes and sizes, improving production efficiency.
By rationally selecting laser welding machines and their auxiliary equipment, efficient and high-quality welding effects can be achieved in stainless steel welding to meet the needs of modern manufacturing.
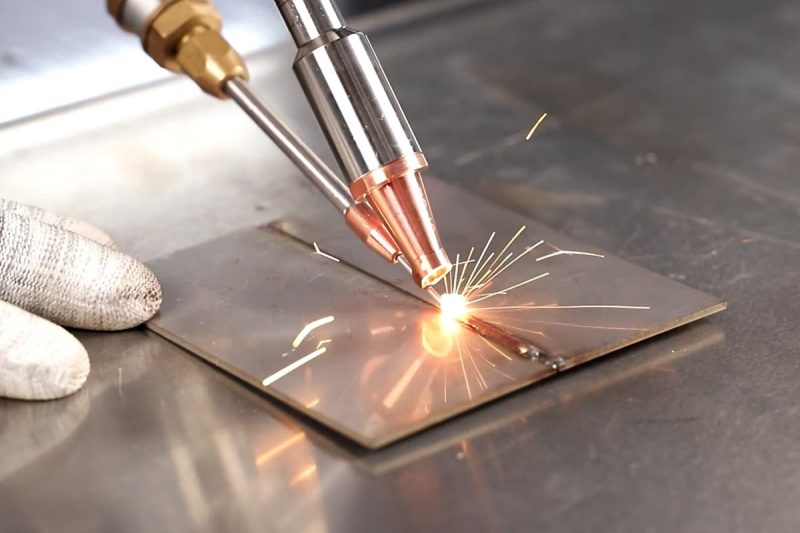
Application of Laser Welding of Stainless Steel
Laser welding technology has been widely used in many industries due to its superior welding effect and wide applicability. The following are the main application areas of laser welding of stainless steel, as well as their respective advantages and characteristics.
Automotive Industry
Application Areas
In the automotive industry, laser welding is widely used in the welding of automobile exhaust systems, fuel tanks, body structures, seat frames, and various accessories. The welding of these parts requires high strength and corrosion resistance to ensure the performance of the car under various driving conditions.
Advantages
- High-strength welds: Laser welding provides strong weld joints that withstand high pressure and impact forces, ensuring structural integrity under harsh conditions.
- Corrosion resistance: Stainless steel itself has excellent corrosion resistance, and laser welding welds can also effectively resist corrosion, extending the service life of the car and reducing maintenance costs.
- Lightweight design: The precision of laser welding and the small size of the weld allow designers to design stronger structures without adding weight, thereby improving the fuel efficiency of the car.
Aerospace
Application Areas
In the aerospace industry, laser welding is used to weld aircraft fuselages, turbine blades, engine components, and other complex structures. Since these components must withstand extreme conditions and high strength requirements, laser welding is an ideal choice.
Advantages
- High precision: Laser welding can achieve micron-level welding accuracy, which is critical for aerospace components and can ensure performance under high load and high-stress environments.
- Small heat-affected zone: Due to the small heat-affected zone during laser welding, the deformation and stress of the material are reduced, which can effectively avoid the problem of deformation after welding.
- Small and neat welds: Laser welding welds are smaller and more beautiful than traditional welding, which can reduce additional surface treatment processes.
Medical Devices
Application Areas
Components that often need to be welded in medical devices include surgical knives, implants, medical device housings, etc. These components need to meet strict hygiene and performance standards.
Advantages
- Clean welds: Laser welding can be performed in a pollution-free environment, and the welds are smooth and defect-free, meeting the strict cleanliness requirements of the medical industry.
- High precision: The high precision of laser welding can ensure the manufacturing accuracy of medical devices and improve the safety and effectiveness of use.
- Personalization and customization: Laser welding is suitable for welding of various complex shapes and sizes, and can meet the needs of personalized medical equipment.
Food and Beverage Industry
Application Areas
In the food and beverage industry, stainless steel welding is widely used in the welding of tanks, conveyors, storage tanks, and processing equipment. These welds must meet high hygiene standards to ensure food safety.
Advantages
- Corrosion resistance: Stainless steel materials can effectively resist various corrosions and ensure the long-term safe operation of food processing equipment.
- Easy to clean: The welds of laser welding are flat and smooth, which reduces the risk of bacterial growth, makes the equipment easy to clean, and meets food hygiene standards.
- High-quality welds: The welds provided by laser welding are high in strength and beautiful in appearance, which can improve the overall quality and market competitiveness of the equipment.
Construction and Decoration
Application Areas
Stainless steel is widely used in the construction and decoration industries, and laser welding technology is used in the welding of stainless steel railings, doors and windows, furniture, and other decorative parts.
Advantages
- Smooth welds: Laser welding ensures a smooth weld surface, avoiding common defects in traditional welding and improving overall aesthetics.
- Aesthetics: Less surface treatment after welding makes stainless steel products more attractive to customers in appearance and meets the high aesthetic requirements of architectural design.
- Durability: Stainless steel materials are corrosion-resistant and wear-resistant, and the robustness of laser welding ensures the long-term use of buildings and decorations in various environments.
The widespread application of laser welding stainless steel technology has not only improved the quality and performance of products in various industries but also continuously promoted the advancement of manufacturing technology. Through precise and efficient laser welding technology, it can meet the urgent needs of the modern manufacturing industry for high quality and high efficiency.
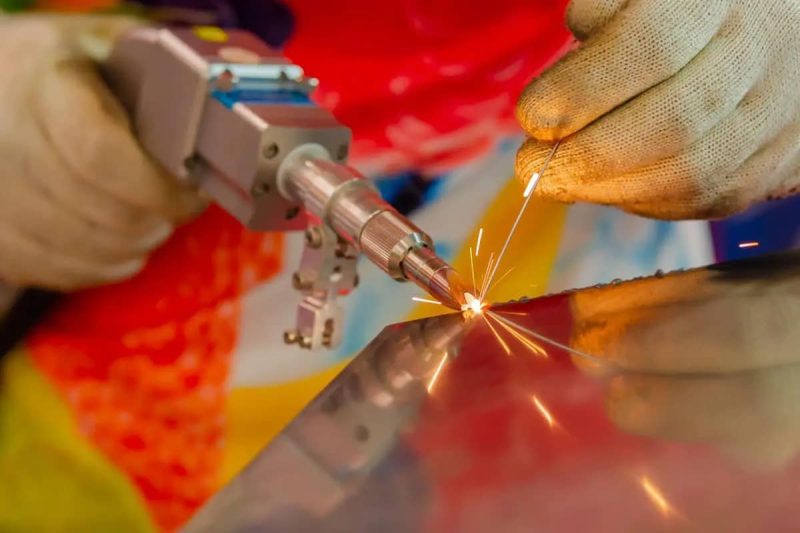
Best Practices and Tips
When laser welding stainless steel, it is important to follow best practices and tips to not only improve weld quality but also ensure a smooth welding process. Here are some key best practices and tips for your welding process.
Proper Handling and Storage of Stainless Steel Materials
Material Storage
- Stainless steel materials should be stored in a dry, ventilated environment to avoid moisture and contamination.
- Use wooden racks or plastic pads to avoid direct contact with the ground to prevent moisture intrusion.
- Use coverings (such as plastic film) to protect the surface of stainless steel, but make sure the material is breathable to prevent moisture accumulation.
Material Handling
- Before welding, check the surface of the stainless steel material to ensure that there are no scratches, rust, or other defects.
- Use a lint-free cloth and an appropriate cleaner (such as alcohol or special cleaner) to thoroughly clean the surface to remove oil, oxides, and impurities to ensure welding quality.
- Avoid using tools that may contaminate the stainless steel surface, such as wire brushes or iron tools.
Optimization of Welding Parameters
Laser Power and Welding Speed
- Optimization of welding power and speed is critical for stainless steel plates of different thicknesses. Thicker stainless steel plates (e.g., more than 3 mm) generally require higher laser power and slower welding speeds to ensure adequate melting and penetration.
- The best welding speed and laser power combination can be experimentally determined, and parameter settings can be optimized through small-scale testing.
Focus Position
- When welding, the focal position of the laser beam also affects the quality of the weld. The focal point should be placed slightly below the workpiece surface to ensure the best welding effect.
- Regularly check and adjust the laser focus to ensure that it always remains in the best position to avoid poor welding.
Post-Weld Processing and Finishing Technology
Post-Weld Processing
- After welding, the weld may be left with oxides and dirt, and post-weld treatment should be performed. Common treatment methods include grinding, polishing, and pickling.
- Grinding: Use a grinder and appropriate abrasives to gently polish the weld to remove surface defects and ensure the smoothness of the weld.
- Pickling: Use pickling liquid to remove oxides on the surface of the weld, restore the gloss of the stainless steel, and improve its appearance and corrosion resistance.
Surface Treatment
- For products with higher requirements, additional surface treatments such as polishing and sandblasting can be performed to improve aesthetics and corrosion resistance.
- Regularly inspect and maintain welded parts to ensure that they maintain good performance and appearance for a long time.
Common Challenges and Troubleshooting
Weld Oxidation
- If oxidation occurs in the weld during welding, it may be due to insufficient or improper shielding gas flow. You can try to adjust the argon flow to increase the coverage of the shielding gas and ensure the cleanliness of the weld.
- You can also consider using a higher-purity shielding gas to reduce the risk of oxidation.
Welding Deformation
- Deformation during welding is usually related to excessive laser power or too fast welding speed. The welding parameters should be re-evaluated, and the laser power should be appropriately reduced or the welding speed should be increased.
- Consider welding in sections or using appropriate fixtures to fix the workpiece to reduce the risk of deformation during welding.
Insufficient Weld Strength
- Insufficient weld strength may be caused by too fast welding speed or insufficient laser power. This can be remedied by adjusting the welding parameters.
- Perform weld tensile and shear tests regularly to ensure that the weld quality meets the expected standards and re-weld if necessary.
By following the best practices and tips above, the welding process can effectively improve the quality and efficiency of stainless steel laser welding, reduce the probability of common problems, and ensure the long-term reliability of the welded structure.
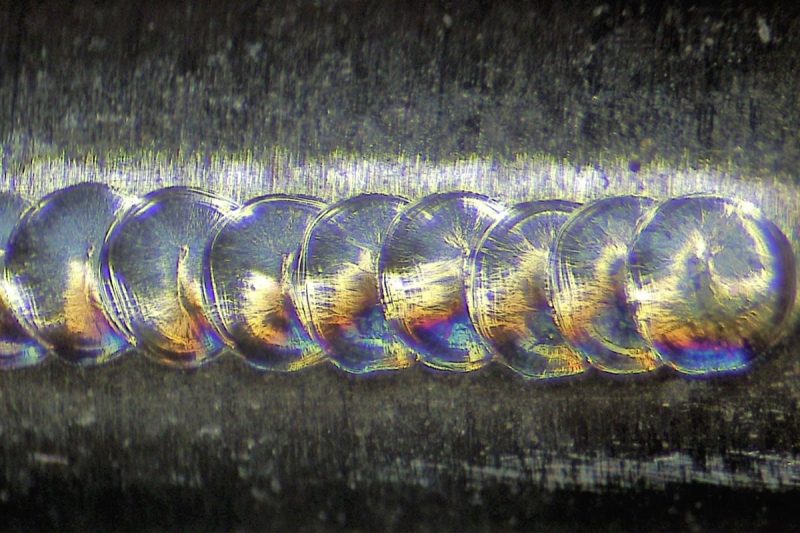
Summarize
Laser welding of stainless steel is a revolutionary technology that provides reliable welding solutions for all types of manufacturing industries. This welding method uses precise control of high-energy laser beams to quickly melt stainless steel materials during welding and form high-strength and beautiful welds. Compared with traditional welding methods, laser welding has the advantages of small thermal impact, less deformation, and high efficiency, making it the first choice for precision manufacturing. Because of this, laser welding is increasingly used in modern industry, covering many fields such as automobiles, aerospace, and medical equipment.
When welding stainless steel, selecting appropriate materials, accurately controlling welding parameters, and performing necessary post-weld treatments are key factors to ensure welding quality. Before welding, ensure that the material surface is clean and dry to avoid welding defects; during the welding process, appropriately adjusting the laser power and welding speed can significantly improve the strength and appearance of the weld. After welding, proper treatment and finishing, such as grinding and pickling, can remove oxides and improve the smoothness and corrosion resistance of the weld, thereby extending the service life of the product.
As an industry-leading laser equipment manufacturer, AccTek provides laser welding machines suitable for various industries, aiming to meet the diverse needs of customers. Our machines are known for their excellent performance and durability, and we also provide comprehensive after-sales service to ensure that customers receive timely support and assistance during use. Welcome to contact us to learn more about our laser welding equipment to help your manufacturing needs and improve production efficiency!
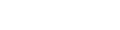
Contact information
- [email protected]
- [email protected]
- +86-19963414011
- No. 3 Zone A, Lunzhen Industrial Zone,Yucheng City , Shandong Province.
Get Laser Solutions