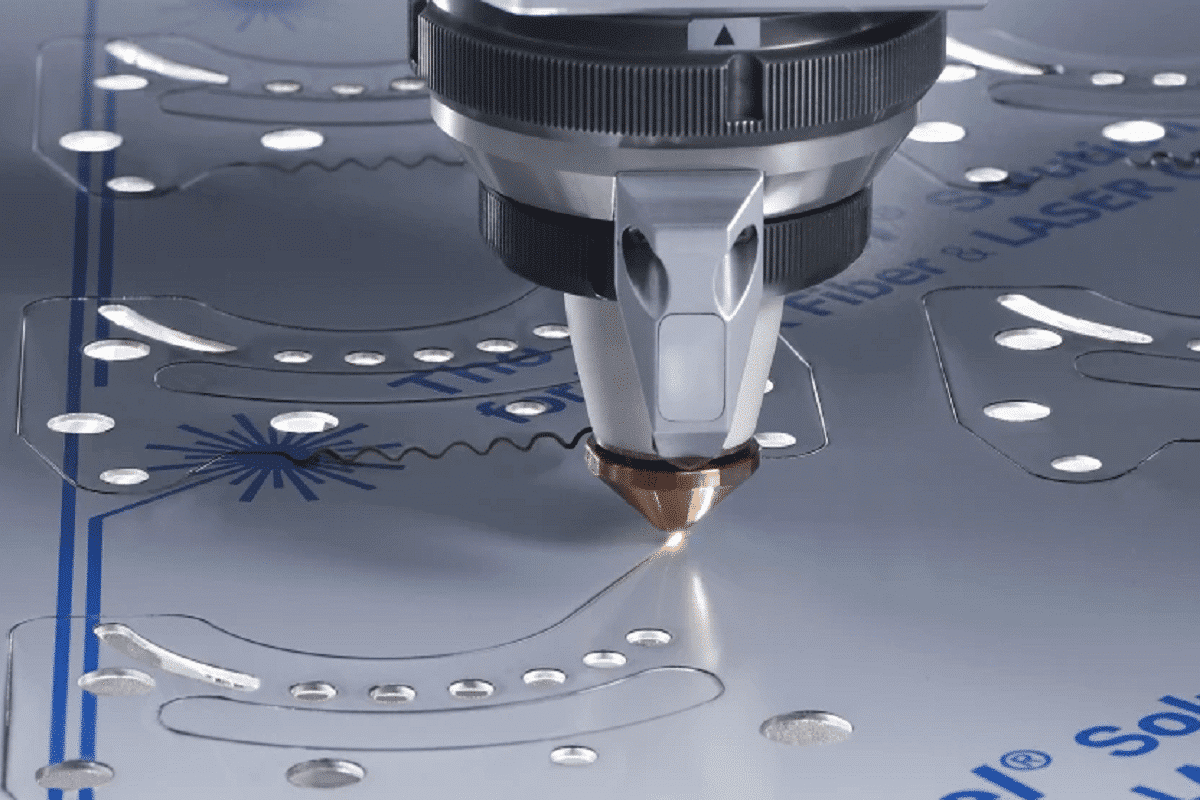
Guide to Optimizing CO2 Laser Cutting Speed
With the development of the manufacturing industry, CO2 laser cutting technology has attracted increasing attention in the field of material processing. CO2 laser cutting, with its high precision and high efficiency, shows great potential in the field of cutting non-metallic, plastic, and other materials. However, to fully exploit the advantages of CO2 laser cutting, optimizing cutting speed becomes a crucial task.
This article will discuss the method of optimizing cutting speed in CO2 laser cutting, taking into account multiple aspects such as laser power, cutting gas selection, cutting speed, and cutting head design. By scientifically and rationally adjusting these key factors, the cutting speed can be maximized and production efficiency improved.
Table Of Contents
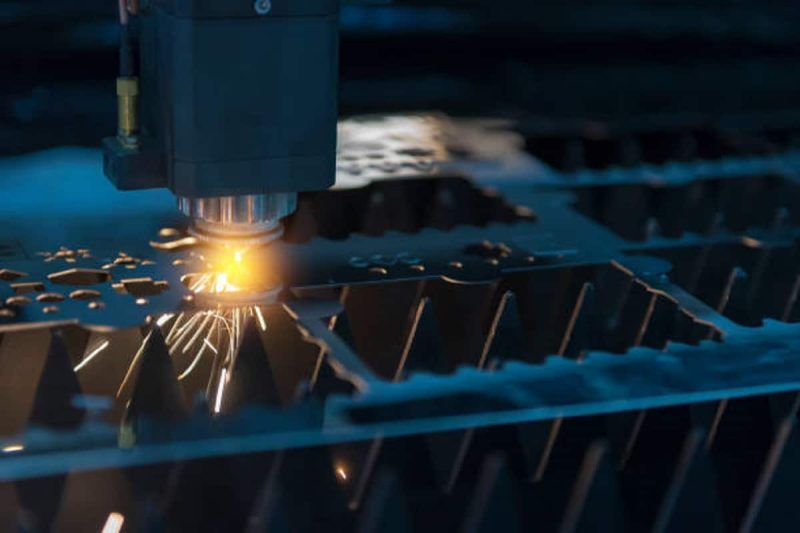
Overview of CO2 laser cutting technology
CO2 laser cutting is a cutting process that uses high-energy laser beams to locally heat the workpiece to melt it and blow away the melted material through gas blowing. Understanding the process principles of CO2 laser cutting is crucial to optimizing cutting speed.
- Laser generator: The core component of the CO2 laser cutting machine is the laser generator, which usually uses CO2 gas to excite laser light. During the excitation process, gas molecules are excited by energy and produce laser light.
- Optical system: The optical system consists of lenses, mirrors, etc. Their function is to maintain a high degree of focus on the laser beam to form a small spot with high energy density on the surface of the workpiece.
- Cutting head: Usually, the cutting head includes a lens with adjustable focal length to adjust the focus point position of the laser. The auxiliary gas is sprayed onto the surface of the workpiece through the cutting head to cool and remove material in the cutting area.
- Auxiliary gas system: Commonly used auxiliary gases include oxygen, nitrogen, etc. They are sprayed onto the surface of the workpiece through the cutting head, which can not only accelerate the gasification of the material but also remove the molten material from the cutting area to improve the cutting speed and quality.
- Control system: The control system is responsible for adjusting and controlling various parts of the laser cutting machine, including laser power, cutting speed, auxiliary gas flow, and other parameters. The advanced control system can realize automatic control and improve production efficiency and cutting quality.
Taken together, the working principle of CO2 laser cutting technology and its equipment is a complex and efficient system. Understanding the process principles of CO2 laser cutting technology is of great help in optimizing its cutting speed.
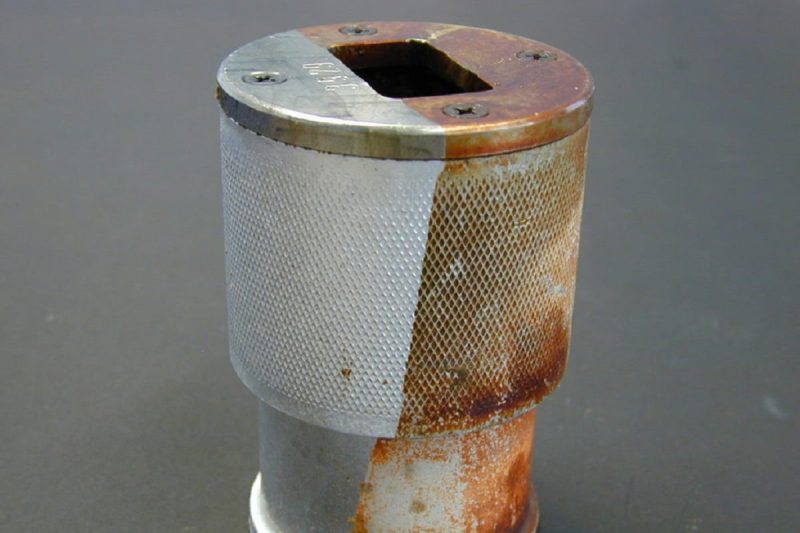
The impact of cutting speed on production efficiency
Cutting speed has a significant impact on production efficiency in CO2 laser cutting. Production efficiency is a comprehensive indicator, which is affected by cutting speed and is mainly reflected in the following aspects:
- Improved production output: The increase in cutting speed directly leads to the completion of more cutting tasks per unit of time, thereby increasing production output. This is particularly critical for industries with large-scale production and high output requirements, helping to meet market demand and improve the competitiveness of enterprises.
- Quickly respond to market needs: In a rapidly changing market environment, quick response to customer needs is a key factor for enterprises to remain competitive. High cutting speed enables companies to adjust production plans more quickly, meet customers’ personalized and fast delivery needs, and improve market agility.
- Reduce production costs: High cutting speed can process more workpieces per unit of time, effectively reducing the production cost of each workpiece. Although the investment and operating costs of laser cutting equipment are high, by improving production efficiency, fixed costs can be better allocated, thereby reducing unit output costs.
- Reduced production cycle time: The increase in cutting speed shortens the production cycle, helping to speed up product launch and order delivery. This is crucial for companies to remain competitive in the market and improve customer satisfaction.
- Improve equipment utilization: High cutting speed reduces the idle time of equipment during the cutting process and improves equipment utilization. By making fuller use of laser cutting machines, companies can increase production capacity without increasing the number of equipment, further improving production efficiency.
Overall, cutting speed is an important factor directly related to production efficiency in CO2 laser cutting. Through scientific and reasonable cutting speed selection and adjustment, enterprises can maximize the advantages of laser cutting technology and improve production efficiency.
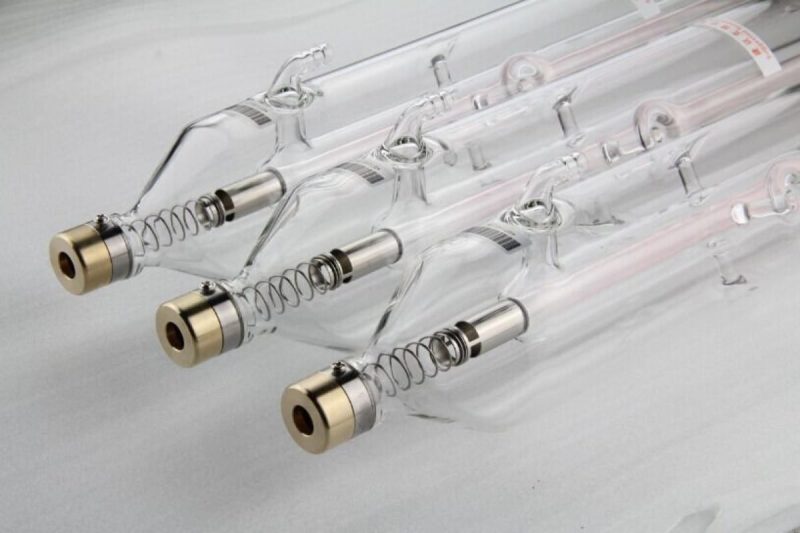
What are the key factors to consider when optimizing cutting speed for CO2 laser cutting?
The widespread application of CO2 laser cutting technology has made remarkable achievements in industrial manufacturing. However, to give full play to its advantages and achieve the best production results, the optimization of cutting speed has become a crucial research direction. In the process of optimizing cutting speed in CO2 laser cutting, the following key factors need to be considered:
Laser power
Laser power is one of the decisive factors in CO2 laser cutting speed. Increasing laser power can significantly increase cutting speed, but too high laser power may lead to problems such as reduced cutting quality and expansion of the heat-affected zone of the material. Therefore, laser power needs to be precisely adjusted based on material type and thickness to achieve the best balance of cutting speed and quality.
Cutting gas selection
Cutting gas plays an important role in CO2 laser cutting, both cooling the workpiece surface and purging melted material. Selecting the appropriate cutting gas, such as oxygen or nitrogen, and adjusting the gas flow and pressure are critical to achieving optimal cutting speeds..
Cutting speed and material thickness
There is a complex relationship between cutting speed and material thickness. Generally speaking, increasing the cutting speed can increase production efficiency, but for materials of different thicknesses, the cutting speed needs to be accurately adjusted to ensure cutting quality. Excessive cutting speed may lead to reduced seam quality and edge deformation.
Focus position and spot shape
The shape of the spot and the position of the focus have a significant impact on the distribution of laser light on the workpiece. By adjusting the spot shape and focus position, more uniform energy distribution can be achieved, improving cutting speed and quality.
Cutting head design
The cutting head is a key component of the laser cutting machine, and its design directly affects the cutting effect. Reasonable cutting head design can improve cutting accuracy and speed. Some advanced cutting heads also have the function of automatically adjusting focus and ejecting auxiliary gas to further optimize the cutting process.
Material properties
Different materials have different responses to laser light, including reflectivity, absorptivity, etc. When optimizing cutting speed, it is necessary to consider these characteristics of the material and select appropriate process parameters to achieve the best cutting effect.
Automation control system
The advanced automated control system can monitor various parameters during the cutting process in real-time and automatically adjust process parameters according to the actual situation. Such a system can improve production efficiency, reduce the need for human intervention, and enable intelligent optimization of cutting speed.
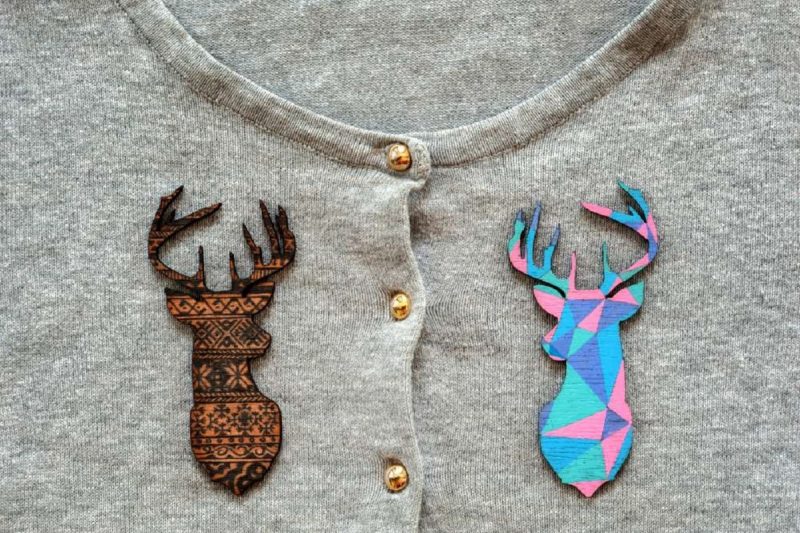
Challenges faced by CO2 laser cutting technology
Although CO2 laser cutting technology has achieved remarkable success in industrial applications, it still faces a series of challenges, which involve many aspects such as technology, process, and application.
Challenges in cutting speed and quality
With the continuous improvement of production efficiency requirements, the pursuit of higher cutting speed has become an urgent need. However, high-speed cutting may lead to problems such as reduced seam quality and expansion of the heat-affected zone, thus affecting the overall quality of the product.
Challenges in material type and thickness
There are still some limitations to the adaptability of CO2 laser cutting technology. Some special materials, such as high-reflectivity metals, composite materials, etc., may reflect or scatter the laser beam, making the cutting effect difficult to control. In addition, when cutting thicker materials, cutting speed and quality also face greater challenges due to the absorption and conductive properties of the material.
Environmental and safety challenges
CO2 laser cutting technology also faces some environmental and safety challenges. The smoke, gas, and other waste generated during the laser-cutting process may have an impact on the environment and workers’ health, and effective measures need to be taken to deal with and reduce these emissions.
Challenges related to the laser equipment itself
The cost of equipment is high and the maintenance and operation requirements for the equipment are high, which may make it unaffordable for some small and medium-sized enterprises. In addition, the size and complexity of the device may also limit its use in certain production environments.
In general, CO2 laser cutting technology still faces many challenges as it continues to advance. Solving these challenges requires technological innovation, process improvement, equipment upgrades, and collaborative efforts across the entire industry chain.
Summarize
Taking these factors into consideration, CO2 laser cutting can be optimized, thereby increasing the cutting speed and achieving an efficient and precise cutting process. At the same time, meticulous maintenance measures can ensure long-term and stable operation of the equipment. According to the characteristics and thickness of different materials, adjusting the corresponding parameters can make the cutting process more intelligent and customized. Therefore, comprehensive consideration and optimization of these key factors will help CO2 laser cutting technology play a greater role in industrial production, improve production efficiency, reduce costs, and promote the progress of industrial manufacturing.
As technology continues to advance, the speed of CO2 laser cutting will continue to be optimized, opening up new possibilities and applications in various fields. In a world where precision and productivity are paramount, CO2 laser cutting is a testament to human ingenuity and innovation in manufacturing and manufacturing. If you are looking for a CO2 laser cutting machine, you can contact us. AccTek Laser can provide you with customized solutions based on your specific application.
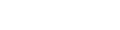
Contact information
- [email protected]
- [email protected]
- +86-19963414011
- No. 3 Zone A, Lunzhen Industrial Zone,Yucheng City , Shandong Province.
Get Laser Solutions