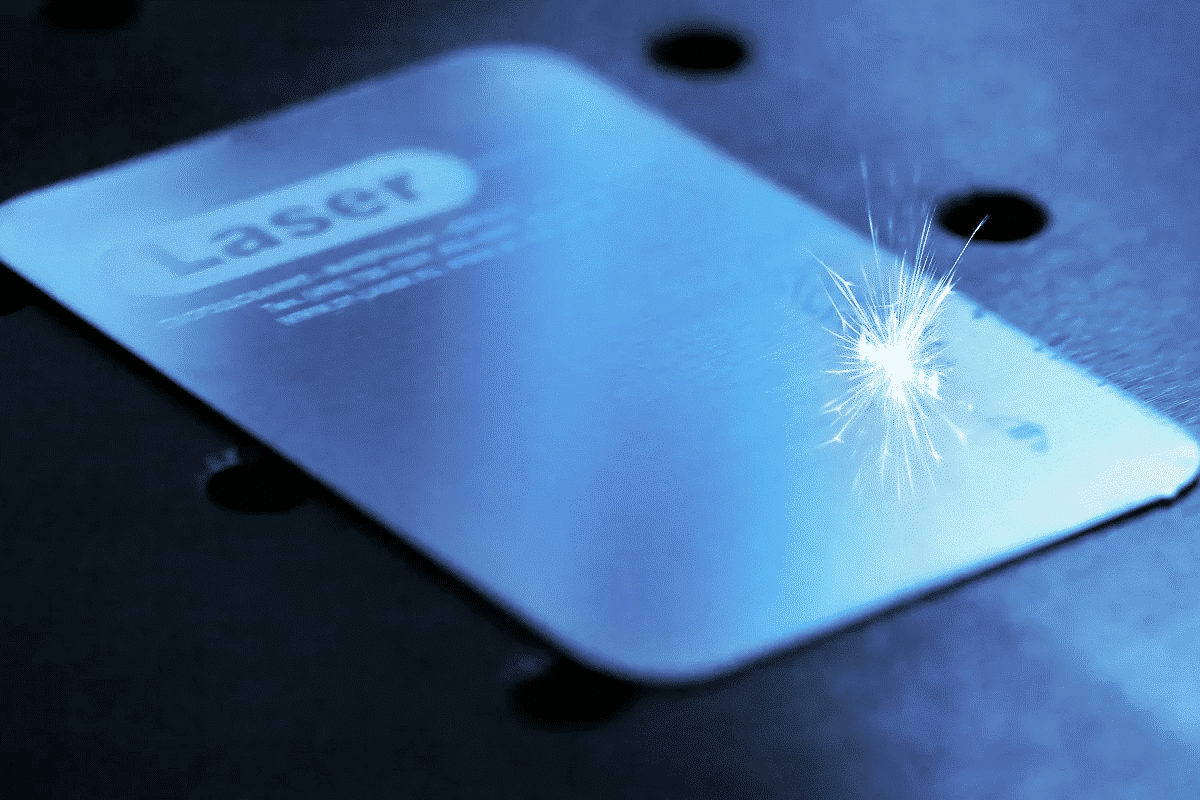
Guide to Optimizing Laser Marking Speed
Laser marking technology is a high-precision, non-contact marking method widely used in industrial manufacturing, medical equipment, electronic products, and other fields. With the continuous development of the manufacturing industry, the requirements for laser marking speed are also increasing. In practical applications, how to optimize the marking speed in laser marking has become a matter of great concern. This article will delve into the key factors that affect laser marking speed and propose some optimization strategies to meet the needs of different industries for efficient marking.
Table Of Contents
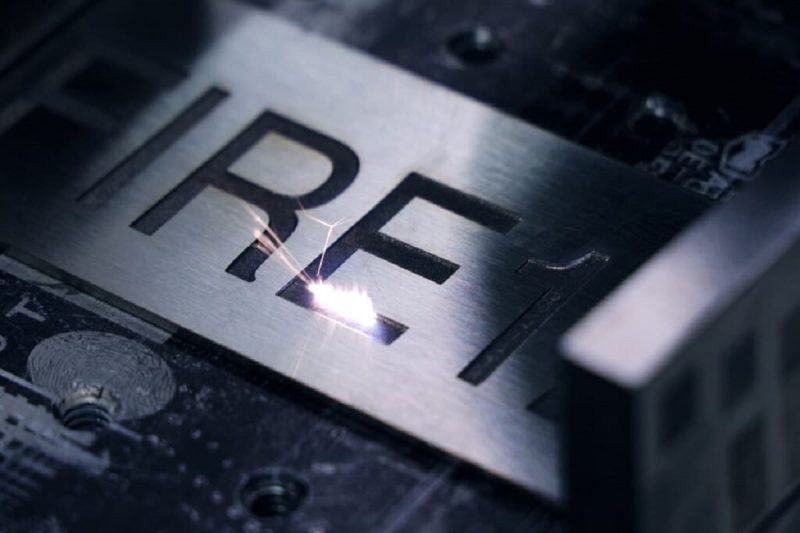
Working principle of laser marking machine
A laser marking machine is a device that uses a laser beam to mark the surface of an object. Its working principle involves multiple key steps such as laser generation, regulation, and focusing. The working principle of the laser marking machine is as follows:
- Generation of laser: The laser used in laser marking machines is generally generated by a laser generator. In this process, the laser gas or laser medium is excited to generate photons. By adjusting these optical elements, the required laser beam diameter, shape, and focusing effect can be obtained.
- Control of laser beam: Use optical components such as lenses or gratings to adjust, focus, and split the laser beam. By adjusting these optical components, the desired laser beam diameter, shape, and focus can be obtained.
- Positioning and control of laser beam: The laser marking machine is equipped with a sophisticated control system to accurately control the movement position of the laser beam in three-dimensional space. This enables the laser beam to move accurately on the working plane to achieve precise marking of objects.
- Material-laser interaction: The laser beam interacts with the material on the surface of the object, including the absorption, scattering, and conduction of laser energy. Different materials react differently to the laser, which also determines the quality of the final marking effect.
- Material marking process: The laser marking machine can evaporate, vaporize, or change the color of the object by finely controlling the intensity and time of the laser beam to achieve markings of different depths and colors.
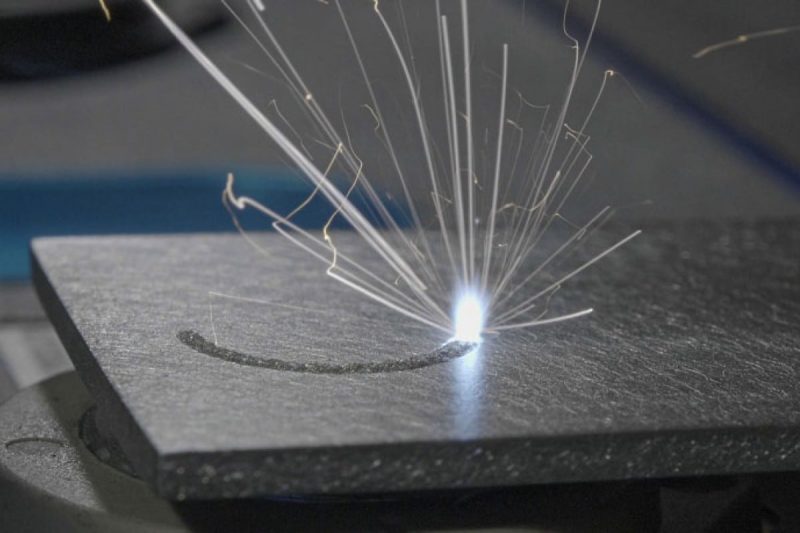
What are the key factors to consider when optimizing marking speed in laser marking
Optimizing the marking speed in laser marking is a key part of improving production efficiency and reducing production costs. To optimize laser marking speed, a series of factors need to be considered, which involve the performance of the laser system, material properties, control systems and software, and environmental factors.
Laser System Performance
- Laser power: Laser power is one of the core factors that affect laser marking speed. Higher laser power can provide more energy and speed up the marking process of materials. However, a balance needs to be found between power and marking quality to prevent overheating and material damage.
- Laser beam quality: Laser beam quality is directly related to the size and shape of the focus, which in turn affects the accuracy and speed of marking. A high-quality laser beam can achieve a smaller focus and improve the precision of marking, while also helping to increase marking speed.
- Scan head performance: The scan head is responsible for controlling the movement of the laser beam, so its performance is critical to laser marking speed. The fast and accurate scanning head can effectively improve marking efficiency and reduce marking time.
Material properties
- Absorption coefficient: The absorption coefficient of a material determines the degree of laser absorption in the material. For materials with higher absorption coefficients, the laser can be more efficiently converted into heat energy, thereby increasing marking speed.
- Thermal conductivity: The thermal conductivity of the material directly affects the transfer speed of heat energy during the laser marking process. Materials with high thermal conductivity dissipate heat faster, helping to prevent overheating and thus increase marking speed.
- Surface reflectivity: The surface reflectivity of a material affects the energy loss of the laser on the surface of the material. Lower surface reflectivity means more laser energy is absorbed, resulting in faster marking.
Control systems and software
- Control accuracy: The accuracy of the control system directly determines the degree of precise control of the laser beam. The high-precision control system can more accurately control the position and movement speed of the laser beam, thereby increasing the marking speed.
- Marking parameter optimization: Reasonable marking parameter settings can maximize the performance of the laser system, including optimization of laser power, scanning speed, focus size, and other parameters.
- Real-time monitoring and feedback: Real-time monitoring of the laser marking process and timely acquisition of feedback information can help adjust marking parameters, optimize marking speed, and prevent potential problems.
Environmental factors
- Temperature and humidity: The ambient temperature and humidity have a certain impact on the performance of laser marking equipment. Excessive or low temperature may affect the stability and marking speed of the laser system.
- Environmental dust: Dust may affect the spread of laser beams, cause energy loss, and also affect the heat dissipation effect of the equipment. Maintaining the working environment to clean it helps to improve the marking speed.
- Vibration and vibration: Vibration and vibration may affect the stability of the laser beam, so corresponding protection measures need to be taken to ensure that the equipment runs in a stable working environment.
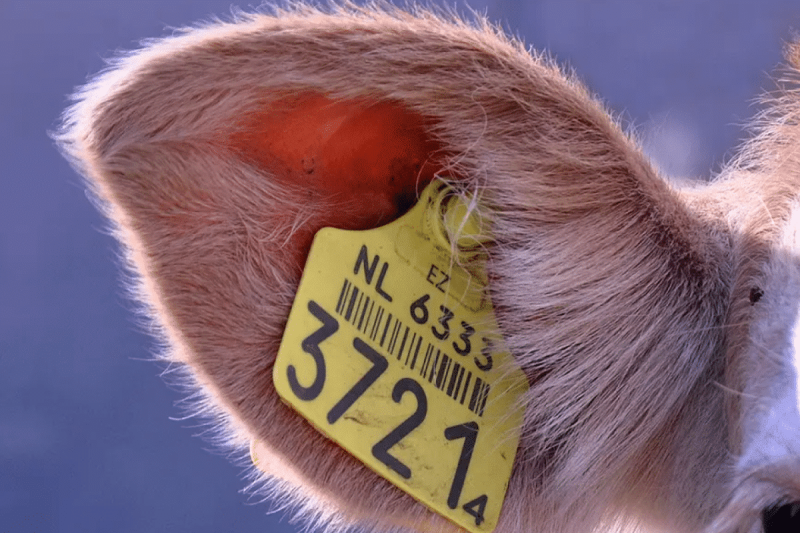
Optimize the importance of laser marking speed
Optimizing laser marking speed is of great significance for modern manufacturing and related fields. Its importance is reflected in multiple aspects
Improve production efficiency
The optimization of laser marking speed is directly related to the improvement of production efficiency. Fast marking speed means more marking tasks can be completed at the same time, thus speeding up the entire production process. This is particularly important for industries that produce large quantities of goods, as it can shorten the production cycle and increase production capacity.
Reduce production costs
An efficient laser marking process can reduce production costs per unit of product. By reducing marking time, companies can realize cost savings in labor, energy, and more. This is critical to remain competitive in a highly competitive market environment.
Improve product quality
Optimizing the laser marking speed can avoid problems such as overheating and deformation of materials caused by too long marking time, thereby improving the accuracy and consistency of marking. High-speed marking can help reduce the thermal impact on materials and ensure marking quality, which is especially important for some application fields that require high marking accuracy.
Adapt to diverse needs
Different industries and different products have different requirements for laser marking. By optimizing the laser marking speed, the equipment can better adapt to the marking needs of different materials, shapes, and sizes. This makes laser marking technology more flexible and able to meet diverse market needs.
Improve production flexibility
High-speed laser marking technology makes the production line more flexible and able to respond quickly to market changes and changes in customer needs. This is crucial for the rapidly changing market environment and personalized customization needs and helps enterprises better adapt to dynamic changes in the market.
Promote scientific and technological innovation
The continuous pursuit of optimizing laser marking speed has promoted innovation in related technologies. With the continuous development of technology, the improvement of laser marking speed is not only a means to improve production efficiency but also a driving force for the continuous progress and innovation of the entire laser marking technology.
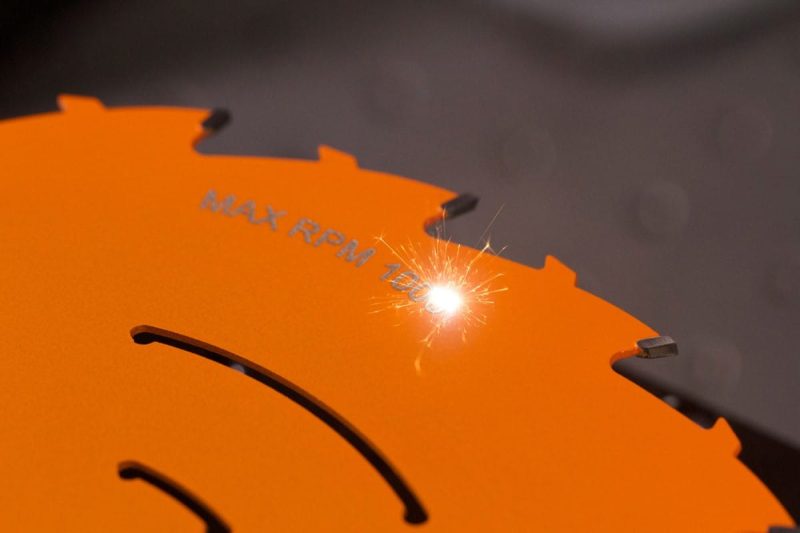
How to increase laser marking speed?
Increasing laser marking speed is the key to improving production efficiency and reducing costs, while also helping to adapt to rapidly changing market demands. Here are some suggestions to help increase laser marking speed:
Optimize laser system performance
- Increase laser power: Using a higher-power laser can accelerate the action of the laser beam on the material, thereby increasing the marking speed.
- Optimize laser beam quality: Ensure the quality and focus shape of the laser beam to improve marking accuracy and speed.
- Upgrade scanning head: Choose a more advanced and precise scanning head that can control the movement of the laser beam more quickly and accurately.
Adjust marking parameters
- Optimize scanning speed: By reasonably increasing the scanning speed, you can reduce the time for each mark and increase the overall marking speed.
- Moderately increase the laser power: Without affecting the marking quality, moderately increasing the laser power can speed up the marking process.
- Adjust focus size: According to material and marking requirements, adjust the focus size of the laser beam promptly to balance speed and quality.
Improve the performance of control systems and software
- Upgrade the control system: Choose a more advanced control system to improve the positioning accuracy and stability of the laser beam to support faster marking speeds.
- Optimized marking algorithm: Use advanced marking algorithms to make full use of the performance of the laser system to achieve more efficient marking.
- Real-time monitoring and feedback: Introduce a real-time monitoring system to detect and correct potential problems promptly and improve production efficiency.
Understand material properties and optimize processing
- Choose materials that are easy to mark: When possible, choose materials that are easy to absorb laser light to improve marking efficiency.
- Optimize laser parameters: Adjust laser power, pulse frequency, and other parameters for different materials to obtain the best marking speed and quality.
Create a suitable working environment
- Control temperature and humidity: Maintain appropriate temperature and humidity of the working environment to ensure the stability of the laser system.
- Dust-proof measures: Take effective dust-proof measures to keep the optical components clean to maintain the propagation effect of the laser beam.
- Reduce vibration and shock: Reduce the impact of vibration on laser marking through reasonable workplace layout or the use of vibration isolation equipment.
Summarize
As a high-precision and efficient marking method, laser marking technology plays an important role in modern manufacturing and other fields. Optimizing laser marking speed can not only improve production efficiency and reduce production costs, but also improve product quality, adapt to diverse needs, and improve production flexibility. This process involves the careful balancing of multiple key parameters such as laser system power, laser beam quality, and material absorption coefficient. It is necessary to find the best compromise point between different factors.
With the continuous advancement of science and technology, laser marking technology will surely usher in new development opportunities. More advanced laser systems, intelligent control systems, and marking processes more suitable for various materials will become important directions for technological innovation. If you would like to learn more about optimizing laser marking speed, please contact AccTek Laser. We offer stable, extensive manufacturing capabilities, including laser series machines and other custom services, for all your prototyping and production needs. Visit our website to learn more or request a free, no-obligation quote.
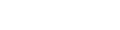
Contact information
- [email protected]
- [email protected]
- +86-19963414011
- No. 3 Zone A, Lunzhen Industrial Zone,Yucheng City , Shandong Province.
Get Laser Solutions