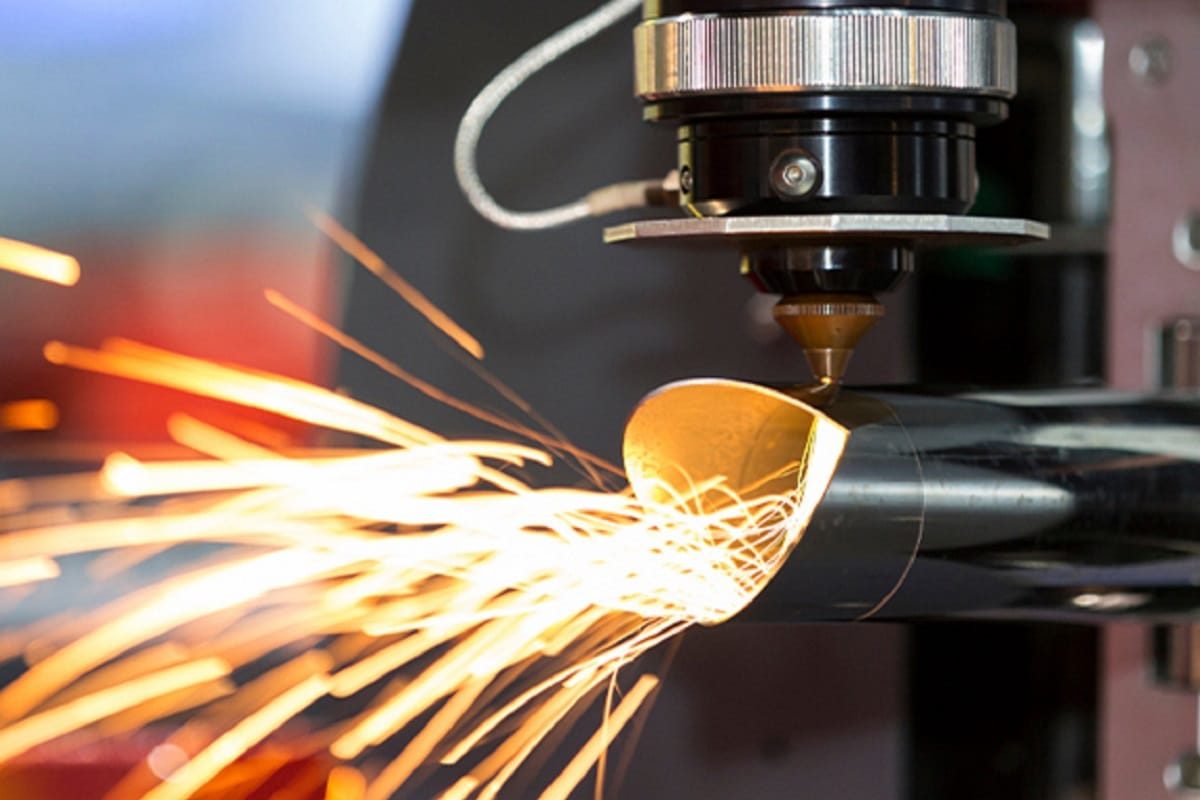
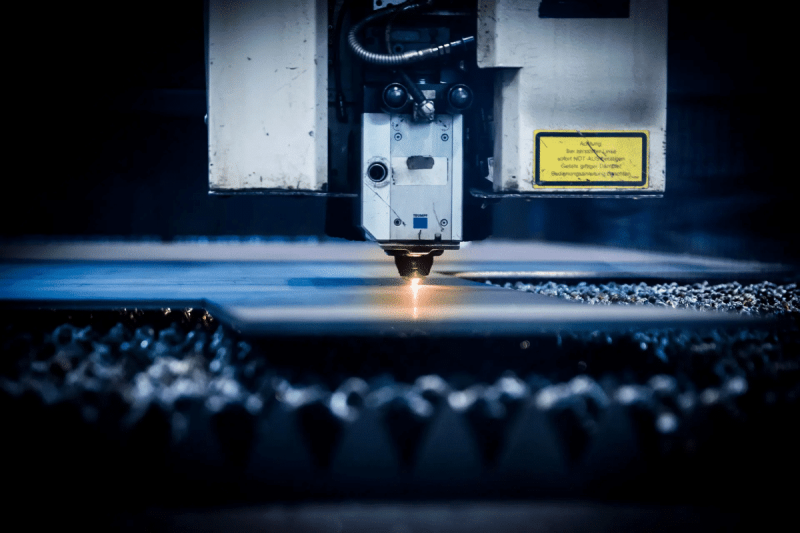
Laser Cutting Precision and Tolerances
Laser cutting is known for its exceptional precision, making it one of the most precise cutting methods in manufacturing and fabrication. This precision is the result of the unique characteristics of laser technology and the advanced control systems used in laser-cutting machines. Let’s take a look at the precision and tolerance levels of laser cutting.
- Cutting accuracy: Laser cutting is very precise and can achieve cutting accuracy on the order of microns (μm) or even smaller. Accuracy mainly depends on the type of laser generator used, the quality of the optical system, and the accuracy of the motion control system. In many cases, laser-cutting machines can consistently cut with an accuracy within the range of ±0.05 to ±0.2 mm (0.002 to 0.008 inches). This level of accuracy is critical for applications requiring complex designs and tight tolerances.
- Tolerance: Tolerance in laser cutting refers to the allowed deviation from expected dimensions. Laser-cutting machines can typically achieve tight tolerances within ±0.1 mm (0.004 inches) or less. This means that the actual size of the cut usually deviates from the expected size by no more than 0.1 mm in either direction. In some cases, even tighter tolerances can be achieved with advanced equipment and skilled operators.
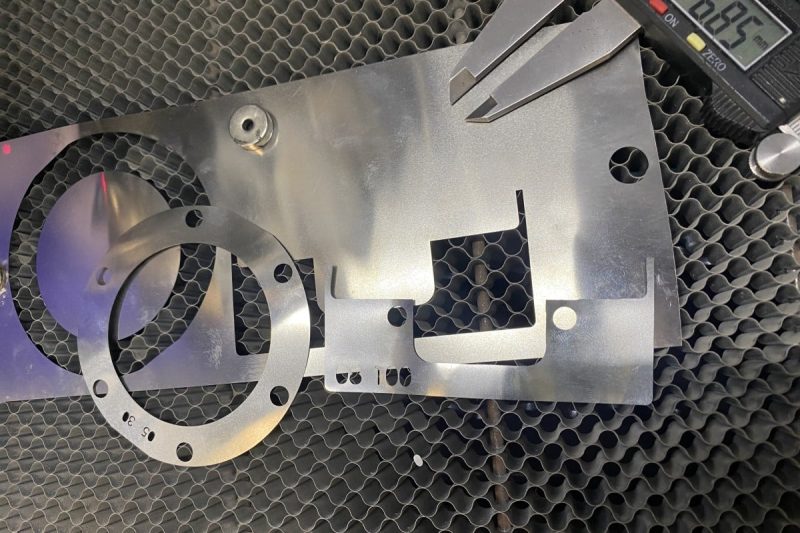
What factors make laser-cutting machines so precise?
Laser cutting is a highly advanced and versatile cutting method that utilizes a focused laser beam to cut a variety of materials with exceptional precision. The process begins with a computer-controlled laser system that directs a high-intensity laser beam onto the surface of the material. The laser’s energy is focused on a tiny, extremely hot spot, causing the material to melt, vaporize, or burn away, leaving a precise, clean-cut edge. The following are the factors that affect the cutting accuracy of laser-cutting machines:
- Focused laser beam: Laser cutting machines use a highly concentrated laser beam that can be focused to a very small spot size, typically as fine as 0.1 mm (0.004 inches). This focused beam enables extremely precise cutting, ensuring accuracy down to the micron level.
- Computer numerical control (CNC): Laser cutters are equipped with a CNC system that controls the movement of the laser head with incredible precision. Operators can program these systems to follow a precise cutting path, ensuring precise and repeatable cuts.
- Non-contact cutting: Unlike traditional cutting methods that require physical contact between the cutting tool and the material, laser cutting is a non-contact process. This eliminates the risk of tool wear, reduces the need for frequent tool changes, and ensures consistent accuracy over time.
- Minimal heat-affected zone (HAZ): Laser cutting produces the smallest heat-affected zone (HAZ) compared to traditional cutting methods such as plasma or flame cutting. The reduced heat-affected zone means that the surrounding material is exposed to very little heat during the cutting process, reducing the risk of material deformation, warping, or damage.
- Material handling and securing: Proper material handling and securing techniques ensure that the workpiece is securely positioned during the cutting process, minimizing the risk of misalignment or deformation.
- Precise control: One of the main reasons laser cutting stands out in terms of precision is its unparalleled control over cutting parameters. Operators can adjust the laser’s power, speed, and focus in micrometers. This level of control allows for accurate and consistent cuts, ensuring minimal material waste.
- Advanced beam control: Modern laser cutting machines are equipped with advanced optics and beam control systems such as beam shaping and adaptive optics. These technologies optimize the quality and consistency of the laser beam, improving cutting accuracy.
- Operator expertise: Skilled operators play a vital role in maintaining the accuracy of your laser cutting machine. They are responsible for programming the machine, selecting appropriate settings, and monitoring the cutting process to ensure optimal results.
- Quality control measures: Implementing quality control measures, such as regular machine maintenance, calibration, and inspections, can help ensure that your laser cutting machine continues to maintain high accuracy over time.
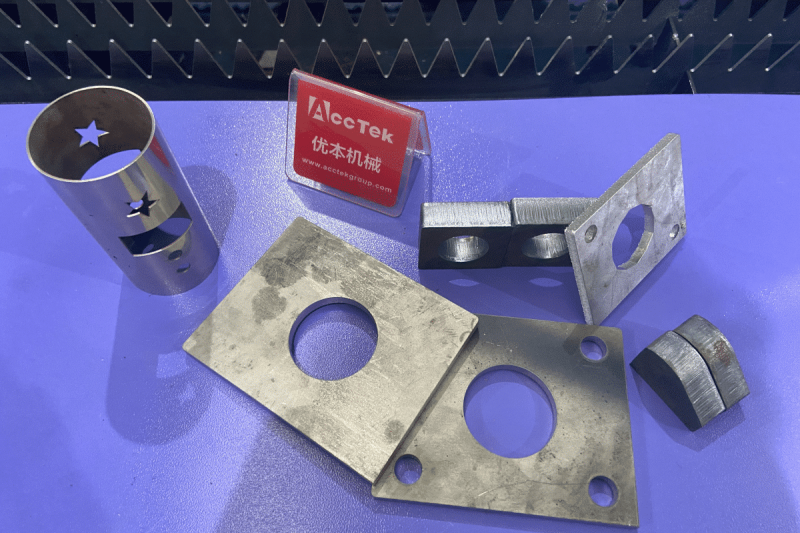
How to maintain the cutting accuracy of a laser cutting machine?
Maintaining the cutting accuracy of your laser cutting machine helps ensure consistent and precise results during your manufacturing or manufacturing process. Here are key steps to help you maintain cutting accuracy:
- Regular cleaning and inspections: Keep your machine clean by regularly removing dust, debris, and residue from the work area, optics, and other critical components. Dirty or damaged optics can scatter or absorb the laser beam, resulting in reduced accuracy. Also, check the machine for any loose or damaged parts and resolve them promptly.
- Alignment and calibration: Perform regular alignment and calibration procedures according to the manufacturer’s guidelines to ensure the laser beam is properly aligned with the cutting head. Proper alignment ensures the laser beam is directed accurately to the cutting point.
- Check and adjust focus: Verify that the laser beam is properly focused on the material being cut. Incorrect focus can cause variations in cut quality and accuracy, so the focus should be set accurately. In addition, the focal length should be adjusted according to the needs of different material thicknesses.
- Beam quality check: Continuously monitor and maintain beam quality to ensure it meets the manufacturer’s specifications. Maintaining proper beam quality helps achieve accurate cuts, and any deviations should be addressed immediately.
- Replace consumables regularly: Check and replace consumable parts such as nozzles, lenses, and focusing optics regularly. These components can degrade over time and affect the quality and accuracy of your cuts. It is recommended to follow the manufacturer’s recommended replacement schedule.
- Monitor the auxiliary gas supply: Ensure a continuous, clean supply of auxiliary gas (such as oxygen, nitrogen, or air) to the cutting head. Inconsistent gas flow can affect cut quality and cause inaccuracies, so gas pressure and flow need to be monitored to maintain cut quality and prevent accuracy deviations.
- Inspect and maintain machine structures: Regularly inspect the machine’s structural components, including frames, rails, and gantry, for any signs of wear, damage, or misalignment. Lubricate moving parts according to the manufacturer’s recommendations. Proper lubrication of moving parts helps prevent friction-related errors.
- Material handling and support: Inspect the material being cut for any defects or warping, ensuring the material being processed is properly supported and secured to the cutting table. During the cutting process, even slight material movement can affect cutting accuracy.
- Temperature and environment control: Maintain a stable and controlled operating environment for the laser cutting machine. Fluctuations in temperature and humidity will also affect cutting accuracy.
- Keep your work area clean: Contaminants in your work area can affect cutting accuracy. You need to ensure that the workspace around your laser cutter is clean and free of debris or materials that could interfere with its operation.
- Operator training and skills: Make sure machine operators understand the intricacies of the laser cutting process and how to maintain cutting accuracy. Skilled operators can optimize machine settings and make real-time adjustments to maintain accuracy during cutting.
- Optimize cutting parameters: Continuously fine-tune and optimize cutting parameters (including laser power, cutting speed and assist gas pressure) to match the specific material and thickness being processed. Using the correct laser parameters helps improve cutting precision and accuracy.
- Quality control and testing: Implement quality control processes including regular testing and inspection of cut parts. Use calibration standards to verify cutting accuracy and make adjustments as needed.
- Log and document maintenance: Keep detailed records of maintenance activities, including dates, procedures performed, and any problems encountered. This documentation can help identify trends and patterns that may affect cutting accuracy.
Summarize
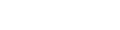
- [email protected]
- [email protected]
- +86-19963414011
- No. 3 Zone A, Lunzhen Industrial Zone,Yucheng City , Shandong Province.