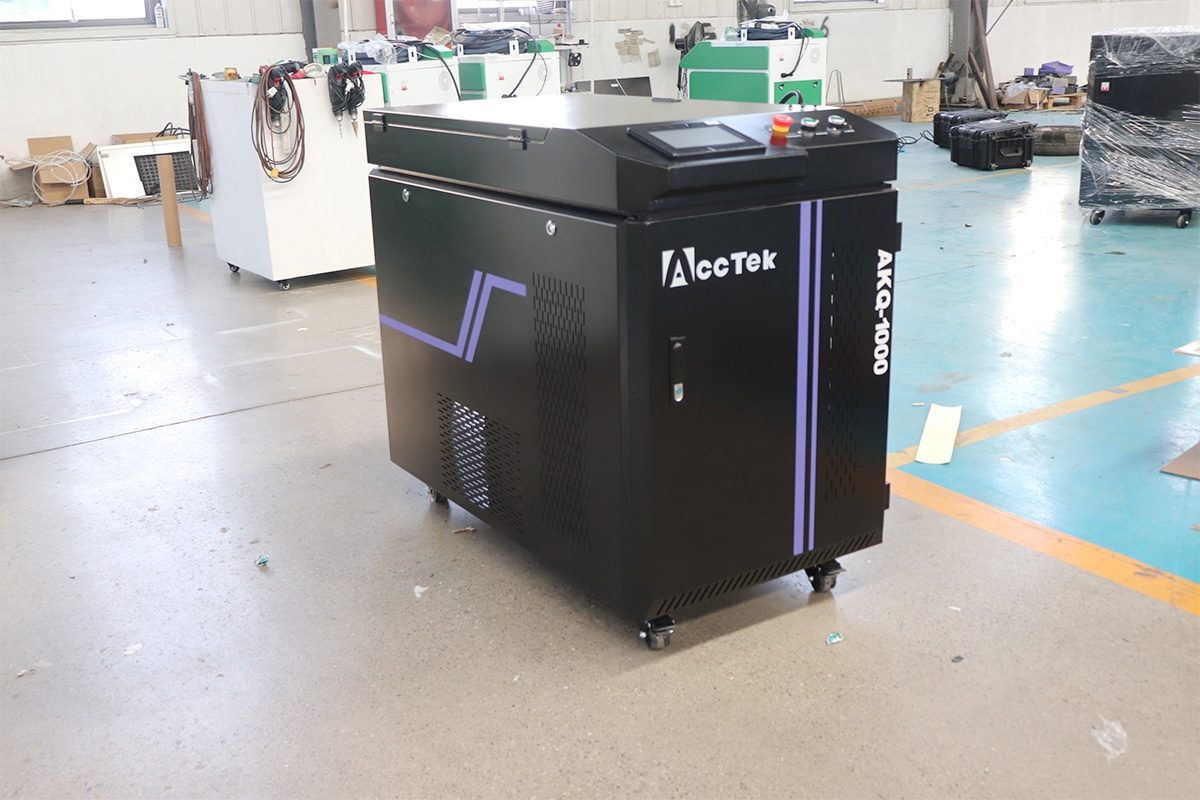
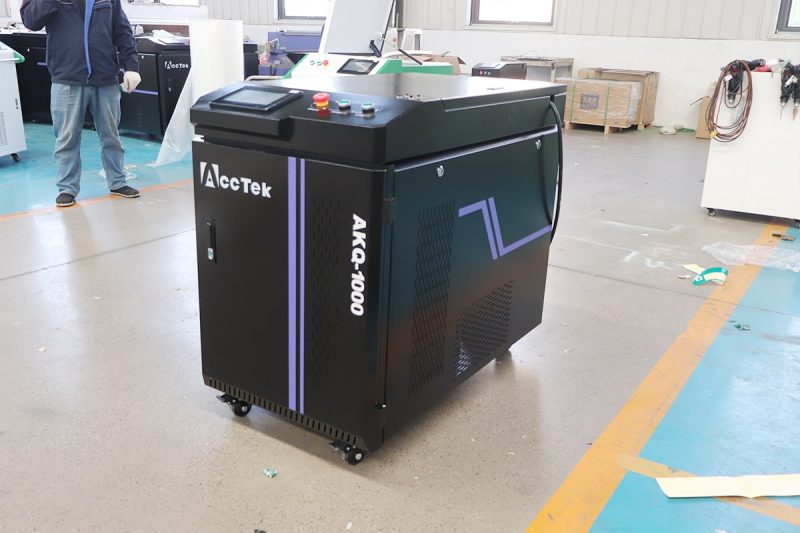
Laser Cleaning Basics
Basic Principles of Laser Cleaning
- Photon Absorption: Laser cleaning begins with the absorption of laser energy by surface contaminants. Different materials absorb laser energy differently depending on their optical properties and the laser wavelength. Effective cleaning occurs when the contaminant absorbs enough energy to facilitate its removal.
- Thermal Effects: The absorbed laser energy causes rapid heating of the contaminant. This heating can cause the contaminant to thermally expand, melt, vaporize, or sublimate, depending on its thermal properties and the laser parameters. Thermal effects can help break the bonds between the contaminant and the substrate.
- Photomechanical Effects: In addition to thermal effects, laser cleaning can induce photomechanical effects, such as shock waves or sound waves. These effects are generated by the rapid heating and subsequent cooling of the contaminant, which creates mechanical stresses that help remove the contaminant from the surface.
- Photochemical Effects: In some cases, especially when using ultraviolet (UV) lasers, photochemical reactions occur. These reactions involve breaking molecular bonds within the contaminant through photon absorption, causing it to decompose or transform into compounds that are easier to remove.
Types of Laser Cleaning Processes
- Laser Ablation: Laser ablation involves the direct removal of material from a surface by vaporization or sublimation. The laser energy is focused on the contaminant, causing it to vaporize or sublimate without affecting the underlying substrate. This method is effective for removing coatings, paints, and thin layers of rust.
- Laser-Induced Breakdown Spectroscopy (LIBS): LIBS is a diagnostic technique that is often used in conjunction with laser cleaning. It involves the use of high-energy laser pulses to generate plasma on the surface of a material. By analyzing the light emitted by the plasma, the composition of the contaminant can be determined, which can aid in process control and optimization.
- Laser Shock Cleaning: Laser shock cleaning uses the mechanical forces generated by laser-induced shock waves to remove contaminants. This method is particularly useful for cleaning delicate surfaces where direct ablation may cause damage. The shock waves help lift and remove particles from the substrate.
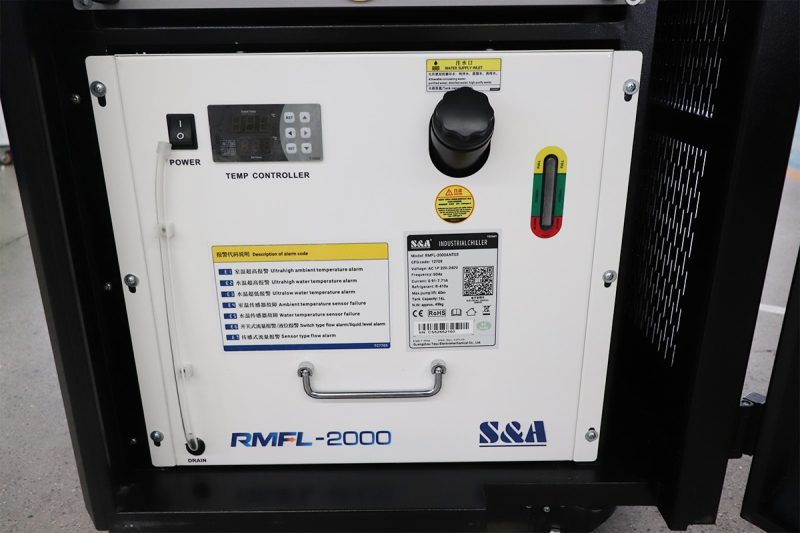
Key Laser Parameters Affecting the Cleaning Process
Wavelength
Definition
Impact on Cleaning
The wavelength determines how well the material being cleaned absorbs the laser energy. Different materials absorb different wavelengths to different degrees:
- Infrared Lasers (approximately 1064 nm): Infrared lasers are often used to clean metal surfaces because they are highly absorbed by metals. They are effective in removing rust, oxides, and coatings from metal surfaces.
- Ultraviolet Lasers (approximately 355 nm): UV lasers are useful for cleaning delicate materials such as polymers and composites because they have a lower penetration depth and are more precise. UV lasers are also used to remove thin layers of contaminants without damaging the substrate.
- Green Lasers (approximately 532 nm): Green lasers strike a balance between fiber and UV lasers, with moderate absorptivity and precision. They are often used in cleaning applications that require efficiency and precision.
Pulse Duration
Definition
Impact on Cleaning
Pulse duration affects the interaction dynamics between the laser and the material:
- Femtosecond Laser: The extremely short pulses minimize heat diffusion, allowing precise material removal with minimal heat-affected zone. It is ideal for applications that require high precision and minimal substrate damage.
- Nanosecond Laser: The short pulses strike a balance between precision and efficiency, making them suitable for most industrial cleaning applications.
- Millisecond Laser: Longer pulses are used for bulk material removal, but can cause more significant thermal effects, which can damage delicate substrates.
Pulse Energy
Definition
Impact on Cleaning
Pulse energy directly affects the amount of material removed per pulse:
- High Pulse Energy: delivers more energy per pulse, allowing deeper penetration and faster removal rates, ideal for heavy contamination and thick coatings.
- Low Pulse Energy: provides finer control over the cleaning process, minimizing the risk of substrate damage, ideal for delicate surfaces and precision applications.
Repetition Rate
Definition
Impact on Cleaning
Repetition rate affects material removal rate and overall cleaning speed:
- High Repetition Rate: Increases cleaning speed by firing more pulses per second, suitable for cleaning large areas.
- Low Repetition Rate: Provides better control over the cleaning process, allowing for precise and targeted cleaning, suitable for complex and delicate surfaces.
Spot Size
Definition
Impact on Cleaning
Spot size determines the area affected by each laser pulse:
- Small Spot Size: Provides greater precision and is ideal for cleaning complex or delicate surfaces. It allows detailed cleaning of small areas without affecting surrounding materials.
- Large Spot Size: This covers a wider area and is suitable for bulk material removal and large-scale cleaning applications. However, this may reduce cleaning accuracy.
Scan Speed
Definition
Impact on Cleaning
Scan speed affects the exposure time of the laser on a specific point:
- High Scan Speed: reduces exposure time, minimizes thermal effects, and increases cleaning speed. It is suitable for cleaning large areas quickly with minimal risk of overheating.
- Low Scan Speed: increases exposure time, achieves deeper penetration and thorough cleaning, and is suitable for removing stubborn contaminants.
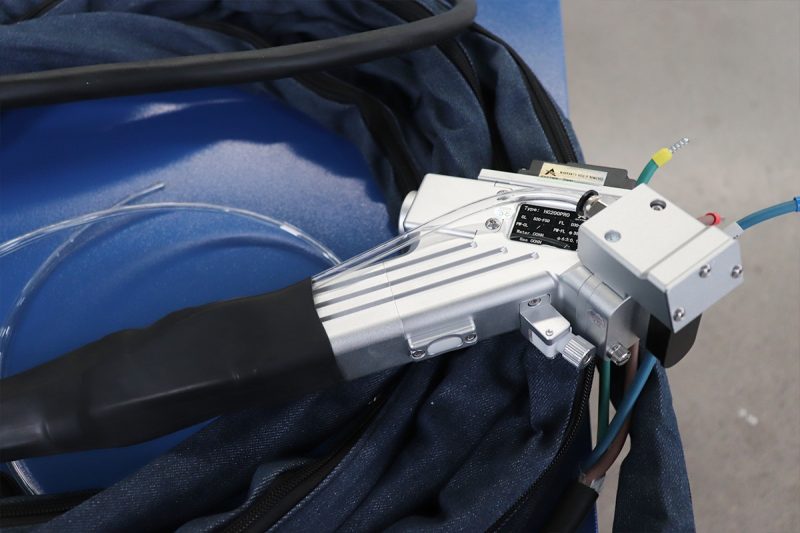
Interaction of Laser Parameters
Wavelength and Energy Density
Wavelength
Energy Density
Interaction
Pulse Duration and Repetition Rate
Pulse Duration
Repetition Rate
Interaction
Scan Speed and Energy Density
Scan Speed
Energy Density
Interaction
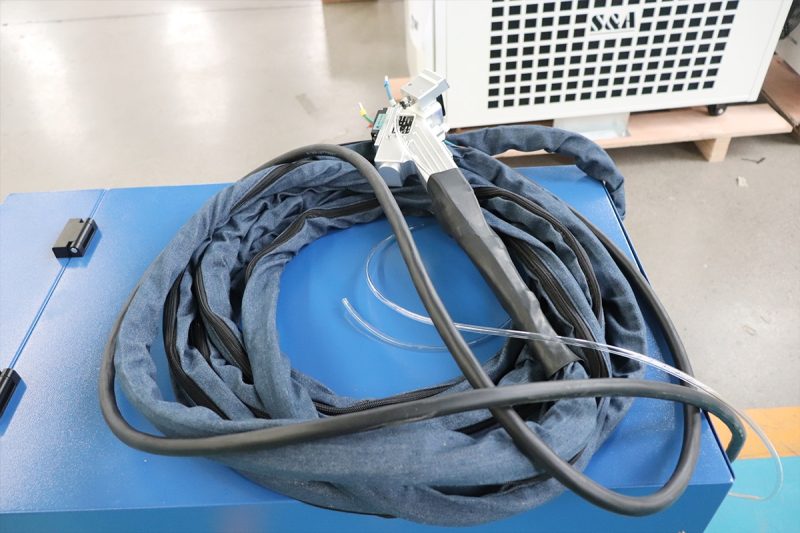
Advantages and Challenges of Laser Cleaning
Advantages of Laser Cleaning
Non-Contact Process
Laser cleaning is a non-contact method, which means that the laser beam does not come into physical contact with the surface being cleaned. This offers several advantages:
- Minimized Damage: There is no mechanical wear or physical stress on the substrate, which reduces the risk of damage, especially on delicate surfaces.
- Consistency: The cleaning process is highly consistent and repeatable, ensuring uniform cleaning results for different parts and surfaces.
Environmentally Friendly
Laser cleaning is an environmentally friendly alternative to traditional cleaning methods that often rely on chemical solvents and abrasive materials:
- No Chemicals: It eliminates the need for chemical solvents and detergents, reducing the release of hazardous substances into the environment.
- Reduced Waste Generation: The process generates minimal waste, which is generally limited to the contaminants removed, which can be easily managed.
Precision and Control
One of the outstanding features of laser cleaning is the high level of precision and control it provides:
- Selective Cleaning: Laser parameters can be finely adjusted to target specific contaminants without affecting the underlying material, allowing for selective cleaning.
- Adjustable Parameters: The ability to adjust parameters such as wavelength, pulse duration, energy density, and scanning speed allows operators to precisely control the cleaning process, allowing customization for a variety of applications.
Reduced Waste
Laser cleaning produces significantly less waste than traditional methods:
- Minimal Residue: The process typically leaves only evaporated or sublimated contaminants, which can be safely collected and disposed of.
- No Secondary Waste: Unlike sandblasting or chemical cleaning, there is no secondary waste such as spent media or residual chemicals.
Versatility
Laser cleaning is versatile and can be applied to a wide range of materials and contaminants:
- Multi-Material Compatibility: It is effective on metals, ceramics, polymers, composites, and more, and is used in a variety of industries such as automotive, aerospace, heritage conservation, and electronics.
- Various Contaminants: It can remove rust, oxides, coatings, grease, and other contaminants to meet different cleaning needs.
Challenges of Laser Cleaning
Cost
The initial investment in laser cleaning technology can be a significant barrier:
- Equipment Cost: High-quality laser systems are expensive, which can be a barrier for small and medium-sized businesses.
- Maintenance and Training: Ongoing maintenance and the need for skilled operators to manage and optimize the equipment can increase overall costs.
Safety
Laser cleaning involves high-intensity laser beams, which pose safety risks:
- Laser Radiation: Direct exposure to laser radiation can cause harm to human skin and eyes. Proper safety measures, including protective glasses and shields, are necessary to mitigate these risks.
- Fume Generation: The process produces fumes and particulate matter, requiring adequate ventilation and filtration systems to ensure a safe working environment.
Material Compatibility
Not all materials are suitable for laser cleaning:
- Substrate Sensitivity: Some materials can be sensitive to laser radiation and can be damaged if parameters are not properly controlled. This is especially true for certain plastics, composites, and delicate artwork.
- Absorption Characteristics: The effectiveness of laser cleaning depends on the material’s absorption characteristics of the laser wavelength. Some materials may not absorb the laser energy effectively, resulting in poor cleaning results.
Process Optimization
Achieving optimal cleaning results requires careful tuning of laser parameters:
- Complex Interactions: The interactions between wavelength, pulse duration, energy density, and other parameters can be complex and require expertise to optimize.
- Trial and Error: Developing the ideal settings for a specific application can require a period of trial and error, which can be time-consuming and resource-intensive.
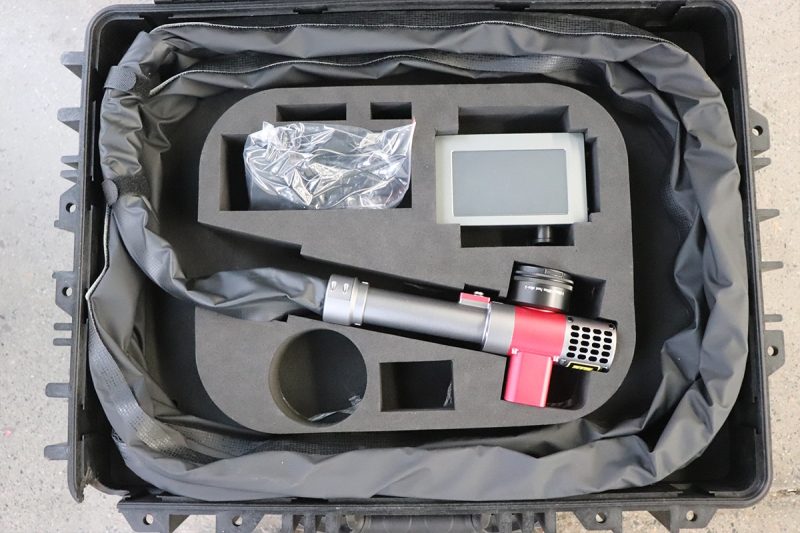
Summary
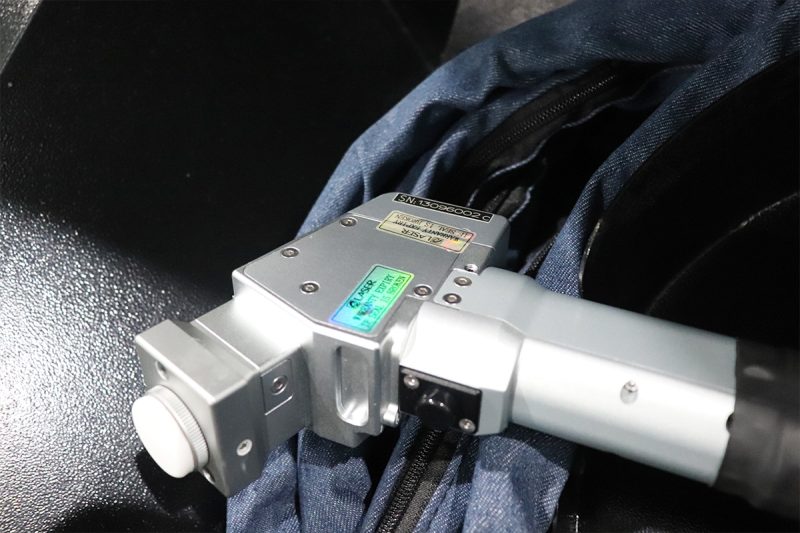
Get Laser Cleaning Solutions
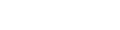
- [email protected]
- [email protected]
- +86-19963414011
- No. 3 Zone A, Lunzhen Industrial Zone,Yucheng City , Shandong Province.