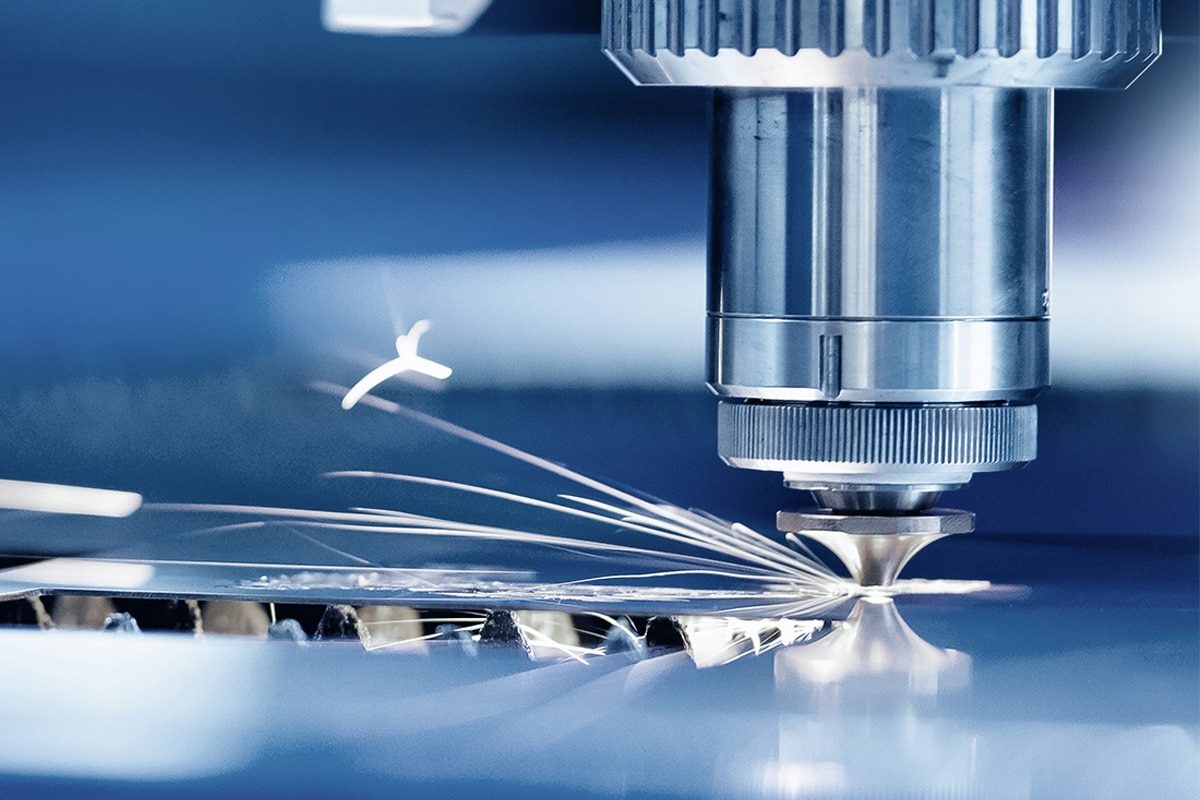
How Does a Fiber Laser Cutting Machine Handle Reflective Materials?
The cutting process of highly reflective materials is often challenging and difficult to solve for many fiber laser cutting equipment manufacturers. However, common highly reflective materials such as copper and aluminum need to be processed frequently in daily production. This article will explore how fiber laser cutting machines can handle these reflective materials and introduce some advanced technologies and best practices.
Table of Contents
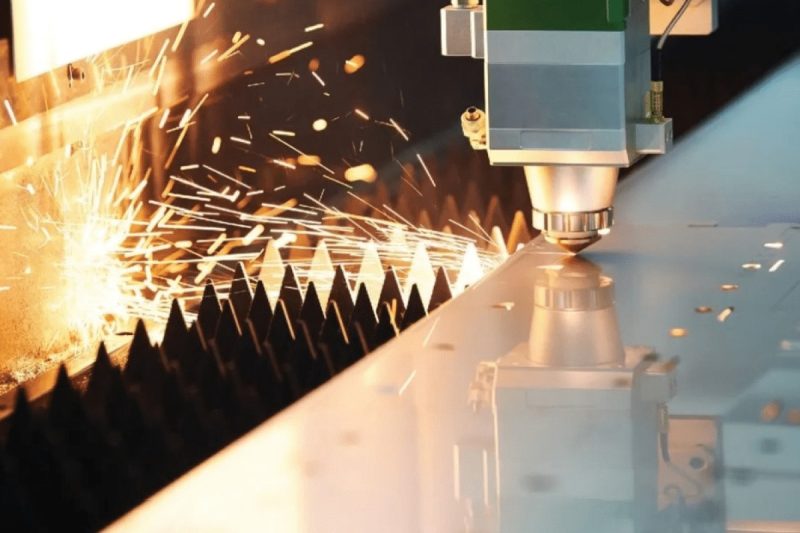
Introduction to Fiber Laser Cutting
Fiber laser cutting machine is a powerful tool that can do both flat cutting and bevel cutting with neat and smooth edges, suitable for fine cutting of metal and other materials in all walks of life. One of the key components of fiber laser cutting machine is the laser generator, which can produce a high-intensity laser beam, which is focused onto the surface of the material through a series of lenses and reflectors, and produces the cutting surface by melting, burning or evaporating the material.
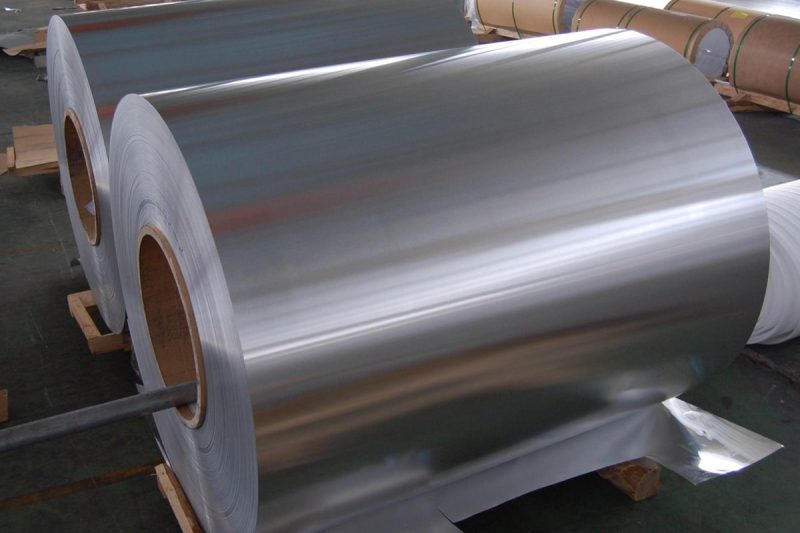
Understanding Reflective Materials
Reflective materials include copper, aluminum, brass, etc. These materials are highly reflective and may cause the beam to reflect back to the laser source during laser cutting, causing potential damage to the equipment. In addition, reflective materials will also affect the efficiency and quality of cutting.
- Copper: Copper has extremely high thermal conductivity and reflectivity, making it difficult to concentrate laser energy in the cutting area. Copper has a low absorption rate for laser beams, often less than 30%, which is equivalent to 70% of the laser being reflected, which not only causes energy loss and waste, but also easily causes damage to components such as processing heads, lenses, and laser generators.
- Aluminum: Aluminum is difficult to handle during laser cutting due to its high reflectivity and thermal conductivity. Pure aluminum is more difficult to cut than iron-based metals due to its low melting point and high thermal conductivity. Coating or alloying can improve cutting results, efficiency, and safety.
- Brass: Brass is a type of alloy mainly composed of copper and zinc, but because it contains zinc, it releases toxic fumes during cutting and requires special treatment. Brass is a highly reflective metal material with extremely low absorption rate for common wavelength lasers. It also has good thermal conductivity. The absorbed heat will quickly spread to the surrounding area of the processing area, affecting the processing quality.
- Stainless steel: Although the reflectivity of stainless steel is lower than that of aluminum and copper, stainless steel will show reflective properties after polishing. Its surface finish and oxide layer may make cutting more difficult and easily cause problems such as sheet burns.
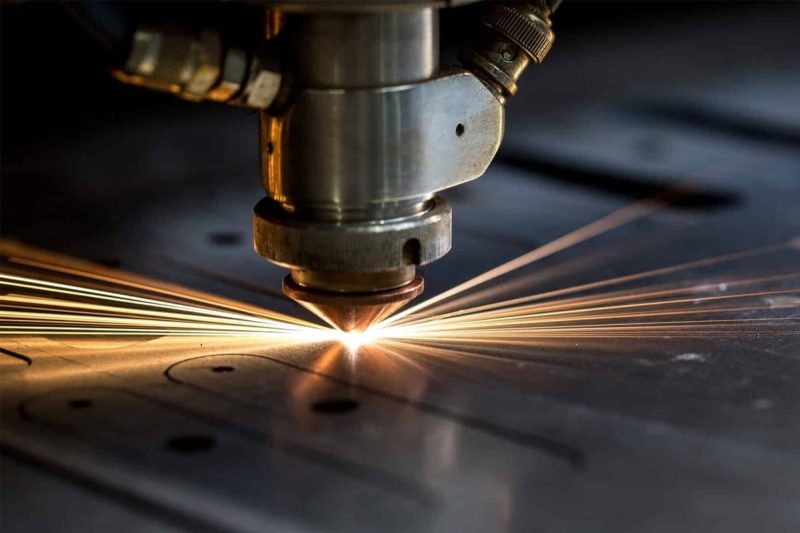
Challenges of Cutting Reflective Materials
When cutting reflective materials, fiber laser cutting machines do need to overcome a series of challenges, which mainly include beam reflection, heat dissipation issues, cutting quality, oxidation, and surface contamination. The following is a detailed analysis of these challenges:
Beam Reflection
Challenge
Reflective materials Metal materials such as aluminum and stainless steel have high reflectivity. They will reflect part of the laser beam back to the laser source, which not only reduces the cutting efficiency but also causes damage to the laser generator, especially the laser lens and reflector system.
Countermeasures
- Use special coatings to cover the surface of reflective materials. These coatings can absorb laser beams and reduce laser beam reflection.
- Choose a fiber laser cutting machine equipped with a self-protection system, which can automatically shut down the laser source when laser beam reflection is detected to prevent equipment damage.
- Compared to CO2 laser cutting machines, fiber laser cutting machines use optical fibers to transmit laser beams, reducing complex reflector systems and thus reducing the risk of beam reflection.
Heat Dissipation
Challenge
Materials with high thermal conductivity, such as copper, will dissipate heat quickly during the laser cutting process, making it difficult to concentrate the laser energy on the cutting area, resulting in insufficient cutting depth or reduced cutting speed.
Countermeasures
- Optimize laser cutting parameters, such as increasing laser power, reducing cutting speed, etc., to ensure that sufficient laser energy is concentrated in the cutting area.
- Use auxiliary gases (such as nitrogen, argon, etc.) for cutting. These gases can not only help blow away the molten metal but also reduce heat conduction to a certain extent.
- Preheat the material before cutting to reduce the thermal conductivity of the material, reduce heat loss, make it easier to concentrate laser energy in the cutting area, and improve cutting efficiency.
- Use short pulse or ultrashort pulse laser technology to reduce heat accumulation and improve cutting quality.
Cutting Quality
Challenge
Due to its high reflective properties, reflective materials will affect the cutting accuracy and quality to a certain extent.
Countermeasures
- Choose a high-precision fiber laser cutting machine to improve cutting accuracy and quality by precisely controlling the focus and movement path of the laser beam.
- Use appropriate auxiliary gas and cutting parameters during the cutting process.
Oxidation and Surface Contamination
Challenge
Materials such as aluminum are easily oxidized to form compounds such as aluminum oxide, which will adhere to the surface of the material and the cutting edge, affecting the cutting effect.
Countermeasures
- Pre-treat the material before cutting to remove oxides and surface impurities to improve the cutting effect.
- Use inert gas (such as nitrogen) as a protective gas during the cutting process to reduce the occurrence of oxidation reactions.
- Select cutting parameters and process methods with anti-oxidation properties, such as pulsed laser cutting.
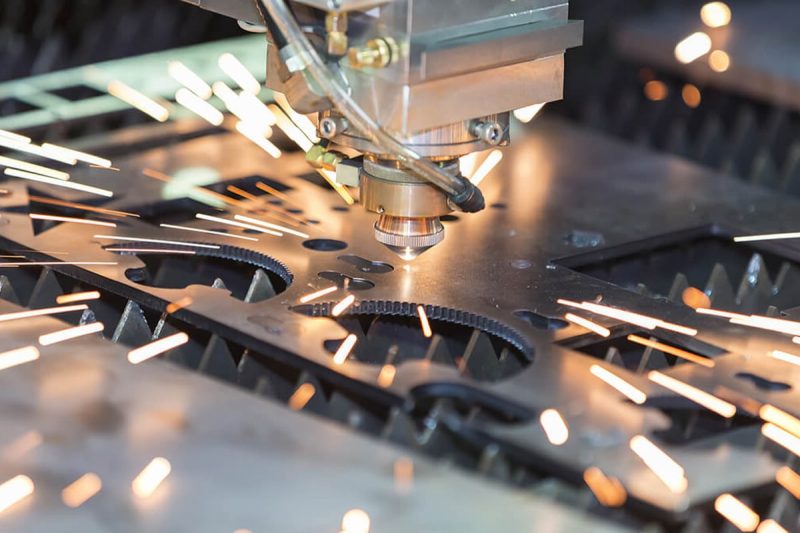
Technology and Process for Cutting Reflective Materials
Anti-Reflection Measures
- Protective coating: Pre-coating a layer of anti-reflective coating on the surface of highly reflective materials can significantly reduce the reflectivity of the laser beam, allowing more laser energy to be absorbed by the material, thereby improving cutting efficiency and effects. This coating needs to have good properties such as high temperature resistance and corrosion resistance to ensure stability during the laser cutting process.
- Beam cutoff: Beam cutoff technology interrupts the light path before the laser beam is reflected to the laser source, which can effectively prevent damage to the laser generator by reflected light. By installing a beam trap, the reflected light can be captured to ensure that the laser energy mainly acts on the material and reduces the damage to the equipment caused by reflection.
Higher Power Laser Generators
- Increase power output: Using a higher-power laser generator is a direct way to deal with highly reflective materials. Higher power means stronger penetration and deeper cutting depth, which can more effectively overcome the reflectivity of the material.
- Power modulation: By dynamically adjusting the power output of the laser, it can be precisely controlled according to the reflectivity and cutting requirements of the material. This adjustment ensures that the laser energy is always kept in the best state during the cutting process, improving cutting quality and efficiency.
Pulse Modulation
- Controlled pulse: Using controlled pulse technology, a continuous laser beam can be divided into a series of short and strong pulses. This pulse mode can reduce the accumulation of heat in the material and prevent the material from deforming or melting due to overheating, thereby improving cutting accuracy and edge quality.
- Short pulse: Short pulse laser has higher peak power and shorter duration, which can heat and evaporate materials more quickly and achieve more precise cutting. At the same time, short pulses can also reduce the heat-affected zone and protect the structure around the material from damage.
Auxiliary Gas
- Oxygen: When cutting metals such as steel, oxygen as an auxiliary gas can increase the cutting speed. Oxygen reacts chemically with high-temperature metals to produce an oxidation exothermic effect, which further accelerates the cutting process of the material.
- Nitrogen: Nitrogen is very useful when cutting easily oxidized materials such as aluminum. It can prevent the material from being oxidized during the cutting process and maintain the finish and precision of the cutting edge. In addition, nitrogen can also reduce the emission of smoke and harmful gases during the cutting process.
- Argon: Argon is suitable for cutting materials such as brass. It has good inertness and can protect the material from oxidation during the cutting process. At the same time, argon can also reduce the generation of smoke and harmful gases during cutting and improve the working environment.
In summary, by adopting these advanced technologies and processes, fiber laser cutting machines can effectively meet the cutting challenges of reflective materials and improve cutting efficiency, accuracy, and quality.
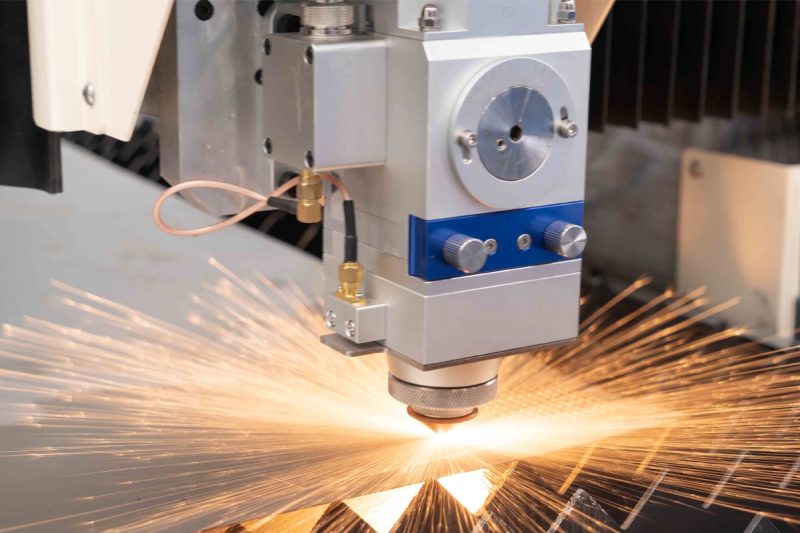
Advanced Technology of Fiber Laser Cutting
Adaptive Optics
- Real-time adjustment: Adaptive optics technology can monitor the focus status of the laser beam in real time and make real-time adjustments based on feedback signals to ensure that the laser beam is always in the optimal focus state.
- Auto-focus: By optimizing the focusing system, adaptive optics technology can significantly improve the focusing accuracy and energy density of the laser beam, thereby improving cutting quality and efficiency.
Adaptive optics dynamically optimizes the focus of the laser beam by adjusting the optical system in real-time, ensuring better adaptability to materials of different thicknesses or reflections during cutting. This adjustment can reduce the reflection loss of the laser beam and enhance cutting accuracy and efficiency.
Beam Shaping
- Customized beam profile: Beam shaping technology can customize the profile of the laser beam according to different cutting requirements, thereby optimizing the energy distribution of the laser beam and improving cutting efficiency and quality.
- Improve power utilization: The shaped laser beam can better match the absorption characteristics of the cutting material, improve the utilization of laser energy, and reduce energy waste.
Beam shaping technology allows the shape of the laser beam to be customized. The laser beam is shaped through specific optical elements (such as beam shapers, microlenses, etc.) to convert it from the original Gaussian distribution to the desired shape (such as a circle). , rectangle, square, etc.). To adapt to different cutting needs. This technology can improve energy utilization, especially when processing highly reflective materials, and has a significant effect, helping to improve processing efficiency and quality.
Real-Time Monitoring
- Process control: Real-time monitoring technology can obtain various parameters in the cutting process (such as temperature, speed, power, etc.) in real-time, and dynamically adjust according to the preset process requirements to ensure the stability and controllability of the cutting process.
- Quality assurance: Through real-time monitoring of cutting effects (such as slit width, roughness, etc.), possible quality problems can be discovered and corrected in time to ensure the quality of the cut products.
Real-time monitoring technology monitors and controls the entire cutting process through sensors and monitoring systems integrated into the fiber laser cutting machine, ensuring automatic adjustment of parameters during the cutting process and ensuring quality stability. This technology can prevent incorrect operations, maintain cutting accuracy, and improve overall production efficiency.
In summary, advanced technologies such as adaptive optics, beam shaping, and real-time monitoring combine to enable fiber laser cutting machines to provide higher precision, more efficient performance, and a more stable operating experience when processing reflective metals and other materials.
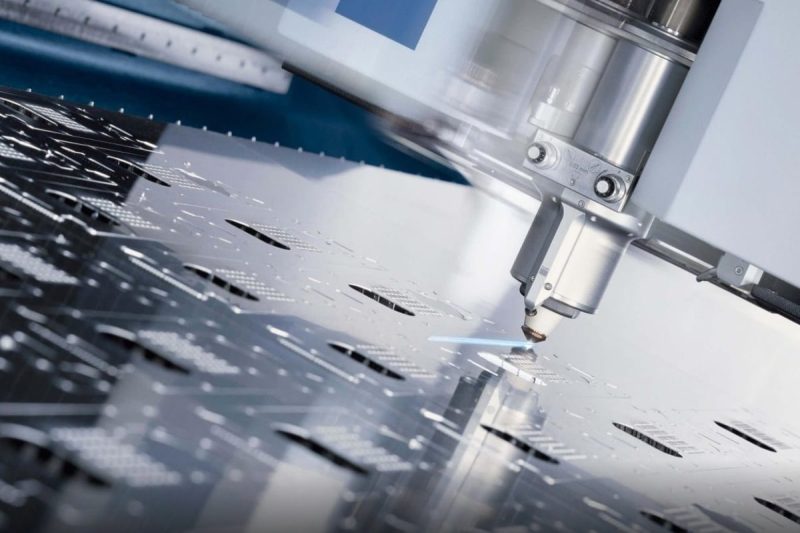
Best Practices for Cutting Reflective Materials
Machine Calibration
- Regular maintenance: To ensure the stability and efficient operation of the laser cutting machine, it is very important to clean and maintain the machine regularly. This can avoid the degradation of cutting performance due to the accumulation of dust or contaminants.
- Optical alignment: The alignment of the optical system determines the accuracy of the laser beam. Ensuring that the laser beam is focused in the correct position can reduce the impact of reflective materials during the cutting process and improve the accuracy and quality of the cutting.
Parameter Optimization
- Cutting speed: Properly adjusting the cutting speed can balance the cutting quality and efficiency. Too fast speed will result in incomplete cutting, while too slow speed may generate too much heat and affect the quality of the cutting edge.
- Power setting: According to the reflectivity and thickness of the material, set the laser power reasonably. Highly reflective materials usually require higher power, but overheating caused by excessive power should be avoided.
Safety Precautions
- Protective equipment: When cutting reflective materials, ensure that the operator wears appropriate protective equipment, such as goggles and gloves, to avoid injuries caused by laser reflection.
- Safety protocol: Strictly abide by the safety protocol, regularly check the equipment, and ensure that the working environment meets the relevant safety standards to prevent laser equipment failure and accidents.
Taken together, these best practices can help improve laser cutting efficiency for reflective materials, maintain cut quality, and ensure operator safety.

Summarize
Fiber laser cutting machines face multiple challenges when processing reflective materials, including high reflectivity of the beam, energy loss caused by fast heat dissipation of the material, difficulty in controlling cutting quality, and possible oxidation and contamination problems on the surface of the material. To overcome these challenges, fiber laser cutting technology adopts a variety of strategies and advanced technologies.First, by applying anti-reflection measures, such as applying a protective coating on the surface of the material or using beam truncation technology, the beam reflection is effectively reduced and the energy absorption efficiency is improved. At the same time, equipped with a higher-power laser generator, combined with power modulation technology, it can output greater energy to penetrate the material, while pulse modulation technology optimizes the cutting effect by generating controlled short pulses. In addition, the selection of auxiliary gas is also crucial. Oxygen is often used to promote oxidation reactions and increase cutting speeds; nitrogen and argon are used to prevent oxidation and protect the quality of the cutting edge. Adaptive optical systems have also been introduced in the field of fiber laser cutting to adjust the beam in real-time to enhance focusing accuracy and stability, and beam shaping technology further improves cutting efficiency and quality by customizing the beam profile. In actual operation, it is crucial to follow best practices, including regular machine calibration to ensure accurate optical alignment, optimizing cutting speed and power settings for the best cutting results, strictly following safe operating procedures, using necessary protective equipment, and implementing safety protocols.In summary, fiber laser cutting machines effectively address the cutting challenges of reflective materials and achieve high-quality and efficient cutting operations by comprehensively using anti-reflection measures, high-power laser technology, pulse modulation, auxiliary gas selection, and advanced adaptive optics and beam shaping strategies.
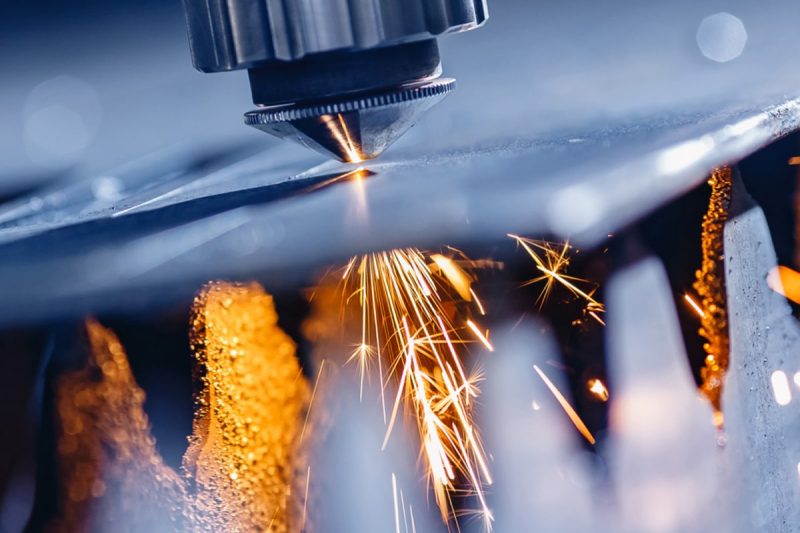
Get Laser Solutions
Choosing the right fiber laser cutting machine can help optimize power consumption and achieve high operational efficiency. Working with a trusted supplier ensures access to advanced technology, tailored advice, and ongoing support. At AccTek Laser, we offer a comprehensive range of laser-cutting equipment designed to meet a variety of industrial needs. Our experts can help you select the most energy-efficient model and configuration, taking into account factors such as material type, thickness, and production volume. We also offer cutting-edge features such as high-efficiency laser generators, intelligent cooling systems, and energy management software to maximize performance and minimize energy use. In addition, our team provides regular maintenance services and technical support to keep your equipment at optimal efficiency. By working with us, you can achieve significant energy savings, reduce operating costs, and enhance your sustainability efforts. If you have any questions, please contact us in time, AccTek Laser is committed to providing every customer with a perfect laser solution!
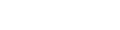
Contact information
- [email protected]
- [email protected]
- +86-19963414011
- No. 3 Zone A, Lunzhen Industrial Zone,Yucheng City , Shandong Province.
Get Laser Solutions