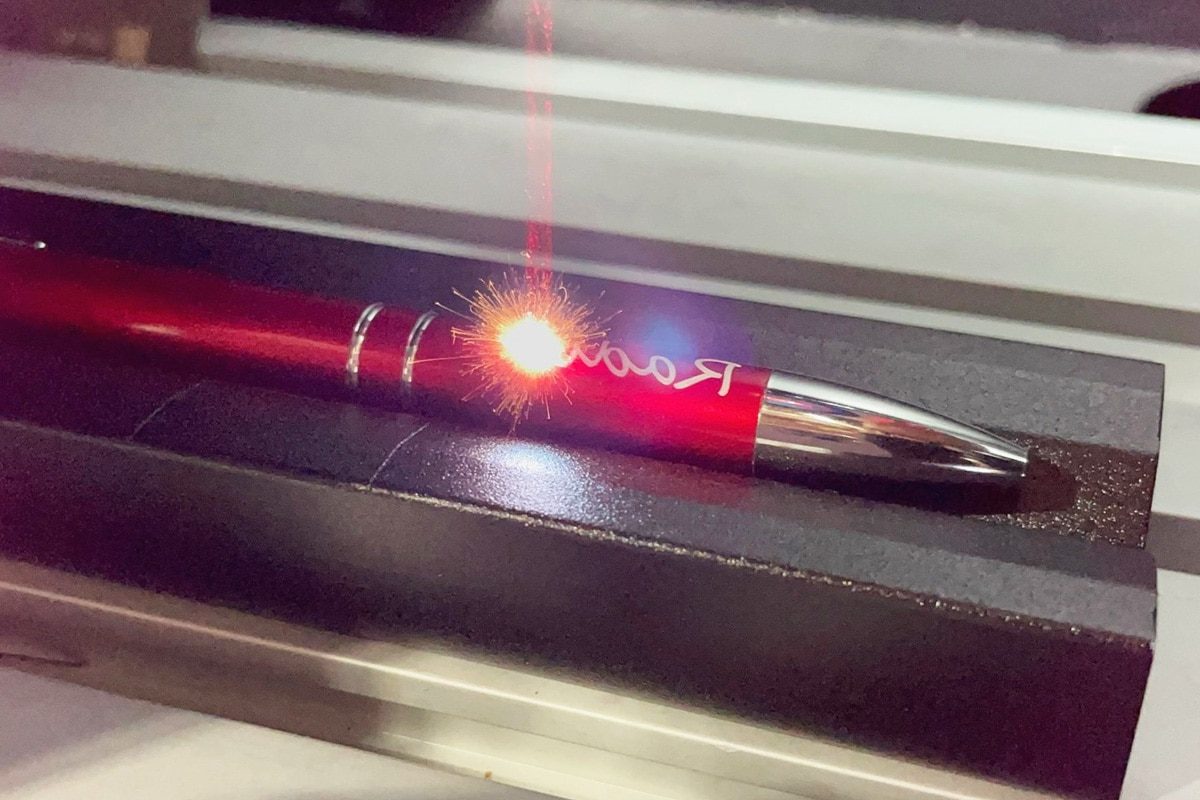
How Does Laser Beam Quality Affect Marking Results?
The quality of the laser beam is crucial to the marking effect, directly affecting the precision, speed, and adaptability of a variety of materials. Beam quality is not only an expression of beam concentration and stability but also a core indicator for measuring laser processing performance. By analyzing key factors such as beam diameter, divergence angle, uniformity, and M2 factor, we can fully understand the distribution of the beam at the focus, thereby determining the clarity, depth, and overall consistency of marking. These quality indicators are not only related to visual effects but also significantly affect production efficiency, so they are crucial to the final effect of laser marking.
Table of Contents
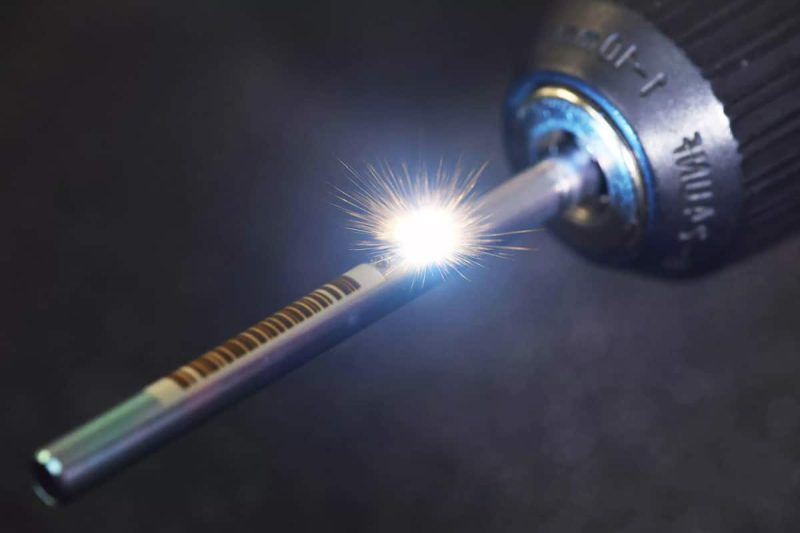
Understanding Laser Beam Quality
Laser beam quality is the core element of laser processing performance, which directly determines the accuracy, speed, and consistency of processing. In applications such as laser marking, cutting, and welding, the quality of the beam has a crucial impact on the final processing effect.
Definition of Laser Beam Quality
Laser beam quality mainly refers to the concentration, stability and uniformity of the beam. Concentration indicates the distribution of laser energy in space, stability reflects the consistency of the beam output at different times, and uniformity describes whether the light energy is evenly distributed on the beam cross section. A high-quality beam can focus on a smaller area and maintain a stable energy distribution, which is particularly important in scenarios that require fine and complex processing.
Factors Affecting Laser Beam Quality
Factors that affect beam quality include the type of laser generator, the configuration of optical components, the stability of the laser generator, and environmental conditions. The structure and design of the laser generator determine the original quality of the beam, such as the divergence angle and shape of the beam. The quality of optical components (such as lenses and reflectors) affects the uniformity and focusing ability of the beam. Environmental conditions (such as temperature and humidity) can also affect the stability of the beam and the consistency of the output. The beam quality can be effectively improved by optimizing the laser generator design, selecting high-quality optical components, and maintaining good environmental conditions.
Indicators for Evaluating Laser Beam Quality
- Beam diameter: The beam diameter refers to the width of the laser at the focal point. The smaller the diameter, the stronger the beam focusing ability and the higher the energy density, which can mark, cut, and other operations on materials more efficiently. The size of the beam diameter directly affects the resolution and marking accuracy of the focus.
- Beam divergence: The divergence angle describes the speed at which the laser spreads in space. A beam with a low divergence angle can maintain a focused state at a longer distance, improving processing accuracy. The smaller the beam divergence angle, the more concentrated the beam is, which is suitable for higher-precision laser applications.
- Beam uniformity: Beam uniformity refers to whether the light energy distribution of the laser is uniform on the cross section. A uniform beam ensures that there is no obvious difference in light and dark in the marking area, and the marking is clear and consistent. Beam uniformity is particularly important for applications that require high-quality marking or surface processing.
- M2 factor: The M2 factor is a metric used to evaluate how close the beam is to an ideal Gaussian beam. The closer M2 is to 1, the higher the beam quality and the stronger the beam focusing ability. A high-quality M2 factor means that the beam can concentrate energy on a smaller focal point, allowing for more sophisticated processing.
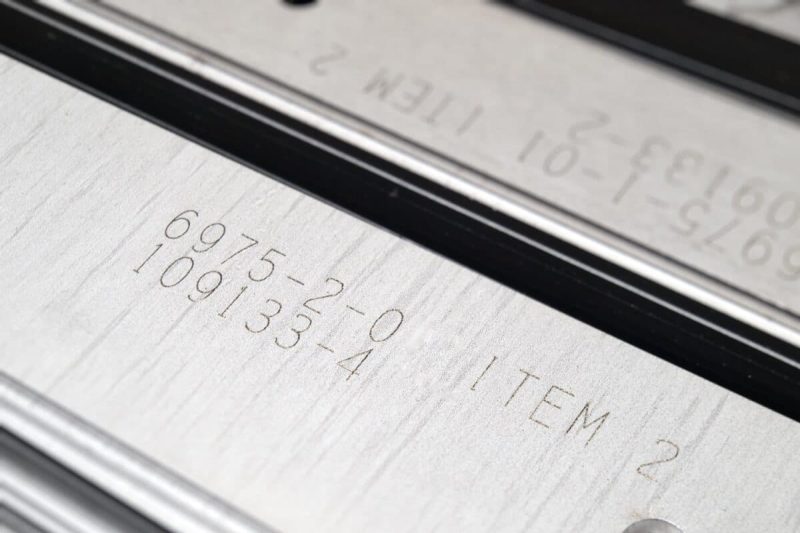
Types of Laser Marking Processes
Laser marking is a process that uses laser technology to mark or pattern the surface of a material. It mainly includes the following types:
Laser engraving
Laser engraving is the process of deeply engraving a material surface with a laser beam to create complex patterns and text. This process is suitable for a variety of materials, including metals and plastics. Laser engraving is highly accurate and long-lasting, and can be used to produce customized products, artwork, and commercial logos. Because the laser can precisely control the depth and range of the engraving, it can achieve detailed design effects.
Laser etching
Laser etching is a process that creates patterns by removing tiny layers of material, and is often used on metal surfaces. Compared with laser engraving, laser etching is usually shallower in depth and is mainly used to create patterns, text or logos, and can create fine details. This process is particularly suitable for metal materials such as stainless steel and aluminum and is widely used in industrial marking and decorative processing.
Laser annealing
Laser annealing uses lasers to heat the surface of a material to change its color without actually removing any material. This technology is suitable for metals such as stainless steel and can achieve beautiful color changes without affecting the material structure. Laser annealing is often used for product identification and decoration, and has the advantages of being efficient and non-destructive.
Laser ablation
Laser ablation is a process that uses high-energy lasers to remove layers of material, mainly used in high-precision applications. By focusing laser energy on the surface of a material, the material can be removed precisely, making it suitable for making complex patterns or shapes. Laser ablation has a wide range of uses in electronic component manufacturing, micro-device processing, and precision industrial applications. Its efficient energy utilization and minimal processing heat-affected zone make it ideal for high-precision processing.
These laser marking processes have their own characteristics and can meet the needs of different materials and application scenarios, so they have been widely used in modern industry.
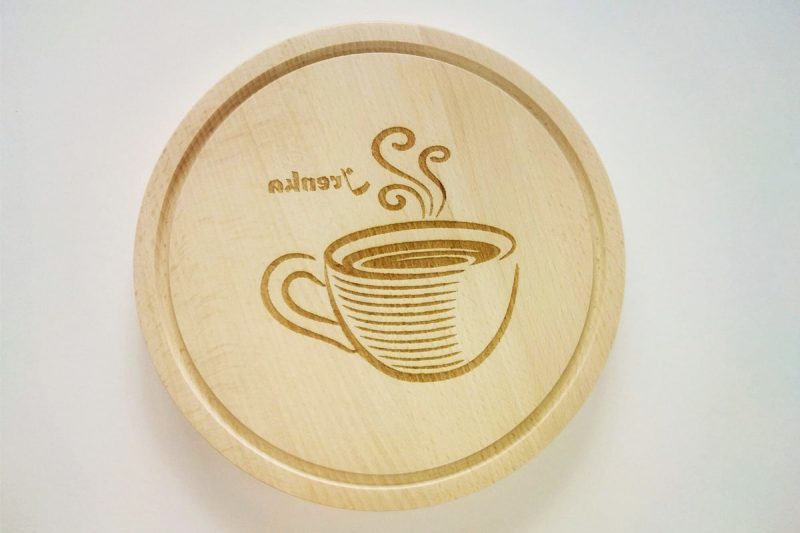
The Influence of Laser Beam Quality on Marking Results
Laser beam quality directly affects all aspects of laser marking. The following is a detailed analysis of several key factors:
Accuracy and Precision
The quality of the laser beam directly determines the accuracy and precision of the marking. A high-quality laser beam can produce a narrower line width, which usually means that the laser’s action area can be more accurately controlled during the marking process. This control is not only reflected in the line width but also ensures the consistency of the marking depth, further improving the edge quality. Good edge quality reduces blurry and jagged edges and improves the overall clarity of the marking pattern.
Contrast and Readability
The uniformity of the laser beam is critical to the contrast and legibility of the marking. A uniform beam ensures that the laser can provide a high-contrast marking effect during the marking process, which makes the marked pattern or text visible against a variety of backgrounds. Whether it is used for product identification or security labels, good legibility is an important factor in ensuring that information is conveyed.
Material Compatibility
High-quality laser beams have better material compatibility and can achieve consistent marking effects on a variety of materials. For example, different materials such as metals, plastics, and ceramics react differently to laser beams, but high-quality beams ensure that the marking effect remains consistent regardless of the material type. This compatibility makes laser marking technology widely used in multiple industries to meet the needs of different customers.
Speed and Efficiency
The focusing accuracy and stability of the laser beam directly affect the speed and efficiency of marking. A high-quality beam can focus on the target area more quickly, increasing the processing speed. This efficiency improvement not only shortens the production cycle but also reduces energy consumption and improves overall productivity. An efficient marking process is particularly important for large-scale production and can meet the dual requirements of speed and accuracy in modern industry.
In summary, laser beam quality is an important factor affecting the results of laser marking, from accuracy, and contrast to material compatibility and marking speed. By optimizing the quality of the laser beam, companies can improve the marking quality and production efficiency of their products, thereby gaining a competitive advantage in the market.
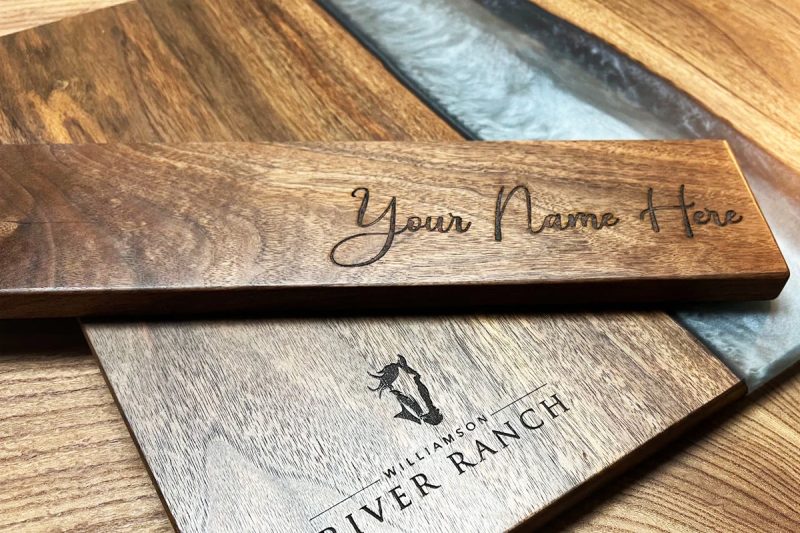
Optimizing Laser Beam Quality
Optimizing the quality of the laser beam is crucial to improving the effect of laser marking. Here are a few key optimization strategies:
Calibration and Maintenance
Regular calibration and maintenance of the laser system is the basis for ensuring beam quality. Optical components, such as lenses and mirrors, may affect beam quality due to dust, dirt or damage. Therefore, clean these optical components regularly to maintain their optimal performance. At the same time, regularly check the focusing ability of the beam to ensure that the system is in the best working condition. This not only improves the accuracy of marking but also extends the service life of the equipment.
Choosing the Right Laser System
It is crucial to select a laser system that is suitable for the application. Different application scenarios have different requirements for laser light sources and optical configurations. For example, solid-state laser generators, fiber laser generators, and CO2 laser generators each have different characteristics and are suitable for different materials and marking requirements. When selecting a laser system, the properties of the target material, the level of detail of the marking, and production efficiency should be considered to ensure that the selected system can meet actual needs.
Material Considerations
The type and characteristics of the material have a direct impact on the laser marking effect. Therefore, it is crucial to adjust the laser parameters according to the reaction characteristics of different materials. For example, metals and plastics have different absorption rates and thermal conductivity to lasers, and the laser power, pulse frequency, and marking speed need to be adjusted accordingly. By accurately adjusting the laser parameters, the clarity and consistency of the mark can be improved, thereby achieving higher marking quality.
Optimizing laser beam quality requires a combination of calibration and maintenance, selection of the appropriate laser system, and material properties. These measures can significantly improve the accuracy and efficiency of laser marking and provide enterprises with higher-quality product marking solutions.
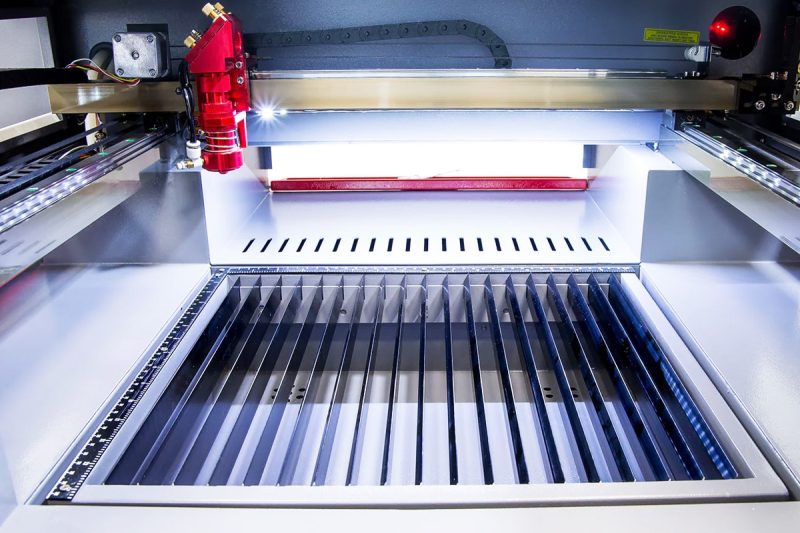
Challenges and Limitations
Although improving laser beam quality brings many benefits, it also faces many challenges and limitations in actual operation. First, improving beam quality usually requires high-end laser equipment and continuous maintenance. These devices are not only expensive but also require professional personnel to operate and maintain them to ensure the stability and consistency of their performance.
Secondly, the characteristics of the laser generator may be affected by environmental factors such as temperature, humidity and dust. Environmental changes may cause the focusing ability and output stability of the laser beam to decrease, thus affecting the marking effect. Therefore, the stability requirements for the equipment are relatively high, and it needs to be operated in a suitable environment to reduce the interference of external factors.
Finally, the production process of high-quality laser beams is relatively complex and requires higher skills from operators. This makes it more difficult to maintain consistent laser beam quality in large-scale production, especially in the case of fast production lines. Companies need to invest additional resources and time to train employees to ensure that they can properly operate and maintain the laser system to achieve the best marking results.

Summarize
Laser beam quality is crucial in the laser marking process, which directly affects the processing speed, marking accuracy, and material applicability. A high-quality laser beam can achieve a more detailed marking effect, improve the consistency and clarity of the marking, and thus enhance the overall visual effect of the product. At the same time, optimizing the beam quality can also effectively improve production efficiency, and reduce resource waste and rework rate, thereby providing companies with greater competitive advantages in the fierce market competition. Therefore, when selecting and maintaining laser systems, companies must pay attention to improving beam quality to achieve efficient and high-quality production.
Laser beam quality directly affects the effect, accuracy, and production efficiency of marking. It is crucial to choose the right laser system and optimize the beam quality, which not only improves the visual effect of the product but also improves the overall production efficiency. Working with experienced suppliers can obtain tailored solutions and continuous technical support. By using advanced laser marking machines, companies can achieve higher energy efficiency, reduce operating costs, and promote sustainable development. Together with AccTek, light up your future! Experience high efficiency, improve productivity, and create a greener tomorrow! Learn about our laser solutions now and discover solutions to improve your business!
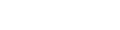
Contact information
- [email protected]
- [email protected]
- +86-19963414011
- No. 3 Zone A, Lunzhen Industrial Zone,Yucheng City , Shandong Province.
Get Laser Solutions