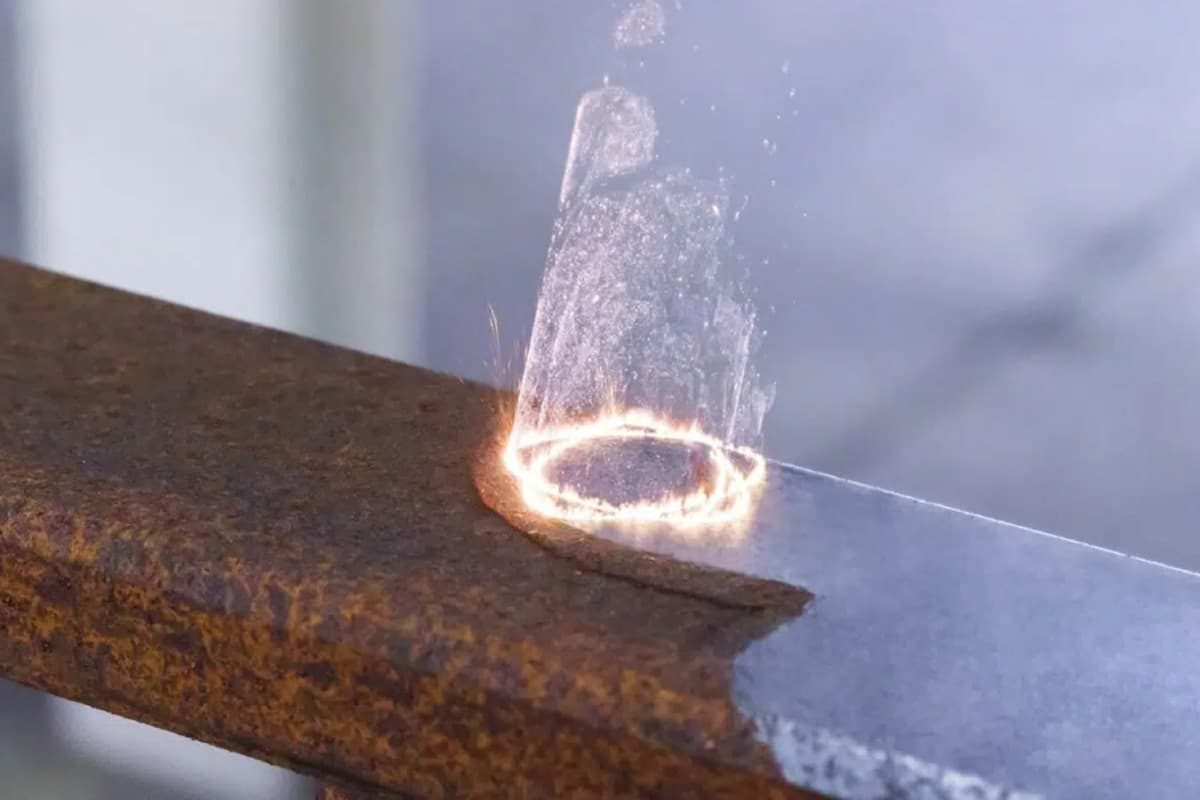
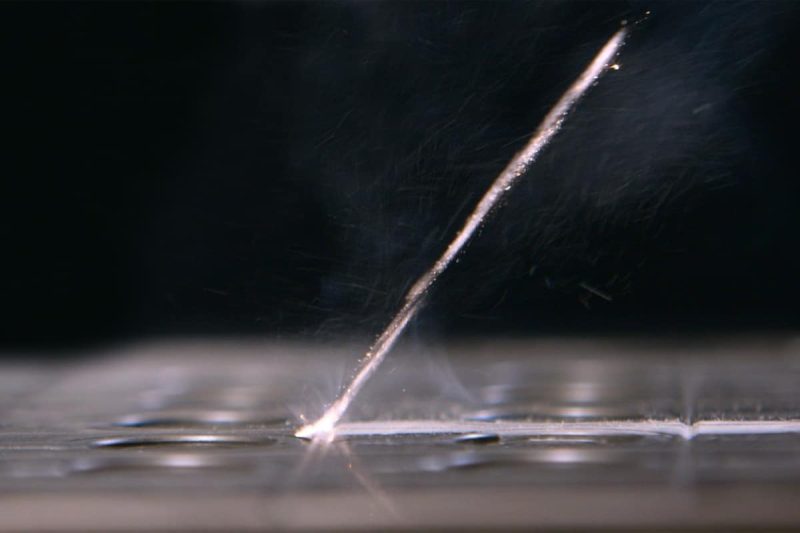
Understanding Surface Roughness and Cleanliness
Surface Roughness
Surface Cleanliness
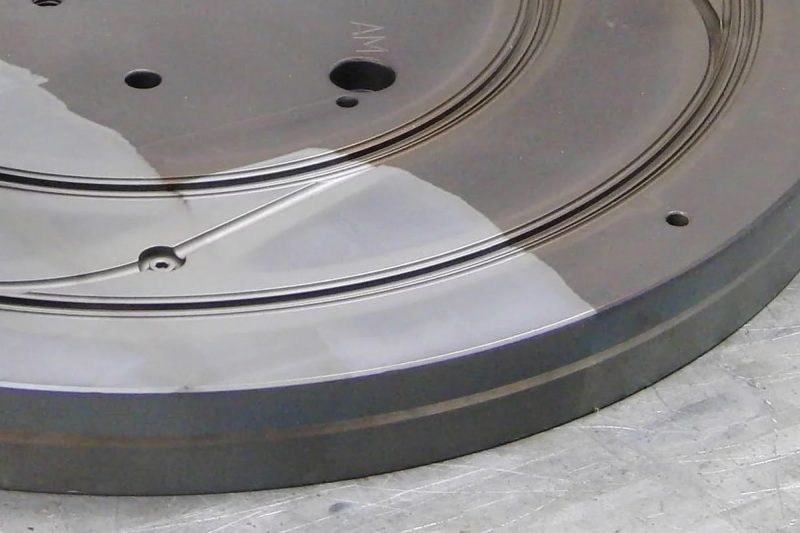
Effect of Laser Cleaning on Surface Roughness
Cleaning Mechanism
Ablation
Thermal Effects
Laser Parameters
Pulse Duration
- Shorter pulse duration: Short-pulse lasers (such as nanosecond lasers) often allow more precise control of the release of energy, thereby reducing the thermal impact on the substrate. This short pulse helps reduce thermal diffusion and overheating of the material surface, thereby reducing damage to the substrate and the increase in roughness. In this case, the laser energy is mainly concentrated on the contaminants and can more effectively remove surface contamination without significantly changing the microstructure of the substrate surface.
- Longer pulse duration: Longer pulses (such as microseconds or longer) may cause greater heat diffusion, thereby increasing the heat-affected area on the substrate surface. This may cause the formation of a molten layer, vaporization or ablation on the material surface, leading to an increase in surface roughness. Long pulses may also cause excessive material removal or uneven thermal effects, thereby increasing surface roughness.
Pulse Smoothness
- High pulse smoothness: means that the energy output of the laser pulse is more uniform and stable, which usually reduces the thermal impact and local over-removal in the surface treatment of the material, and obtains a smooth surface and lower roughness.
- Low pulse smoothness: may lead to unstable pulse energy, resulting in uneven heating of the material surface, more molten layers or vaporization, and increased roughness.
Spot Size
- For applications that require high precision and delicate processing (such as micromachining or precision cleaning), a smaller spot size will be more suitable.
- For large-area cleaning or processing (such as removing large areas of rust or pollution), a larger spot size may be more effective.
Beam Quality
- High beam quality: High beam quality means that the divergence angle of the laser beam is small and the energy distribution is uniform, which can provide more consistent processing results, reduce local overheating and melting, and thus reduce surface roughness. Higher beam quality helps to achieve more precise processing, can process small structures and features, and further reduce roughness.
- Low beam quality: Low beam quality may cause uneven energy distribution of the laser beam, resulting in larger spot size and more heat-affected area, which may lead to uneven surface treatment and higher roughness. Low beam quality affects the accuracy and detail performance of the processing, and increases the defects and roughness in the surface treatment.
Material Properties
Thermal Conductivity
- High thermal conductivity: Materials with high thermal conductivity can diffuse laser-induced heat from the laser action point to the surrounding area more quickly, reducing local heat accumulation. This can reduce the degree of local melting and vaporization, thereby reducing surface roughness. The high thermal conductivity of the material helps to distribute the laser energy more evenly and reduce surface unevenness caused by thermal gradients.
- Low thermal conductivity: Materials with low thermal conductivity can cause laser energy to concentrate in the surface area of the material, resulting in a larger heat-affected zone. This can cause local melting, vaporization, or ablation, thereby increasing surface roughness. Low thermal conductivity materials may also produce greater thermal stress, causing material deformation or cracking, further increasing roughness.
Absorption Coefficient
- High absorption coefficient: A high absorption coefficient means that the material can effectively absorb laser energy, thereby improving the local heating effect. Appropriate energy absorption helps to effectively remove contaminants, but too high absorption may cause excessive heating and increase roughness. A high absorption coefficient generally improves cleaning efficiency and makes contaminants more thoroughly removed, which helps to achieve a smoother surface, provided that the thermal effect is controlled.
- Low absorption coefficient: Materials with low absorption coefficients absorb lasers poorly, which may result in the laser energy not being effectively used to remove contaminants or surface treatment, reducing the cleaning effect and may require more energy or longer processing time. Low absorption coefficients may result in poor cleaning results and incomplete removal of contaminants, which affects surface quality and roughness.

Effect of Laser Cleaning on Surface Cleanliness
Selective Pollutant Removal
Cleaning for Specific Contaminants
No Residual Waste
Maintaining Substrate Integrity
Non-Destructive Cleaning
Minimum Heat Affected Zone
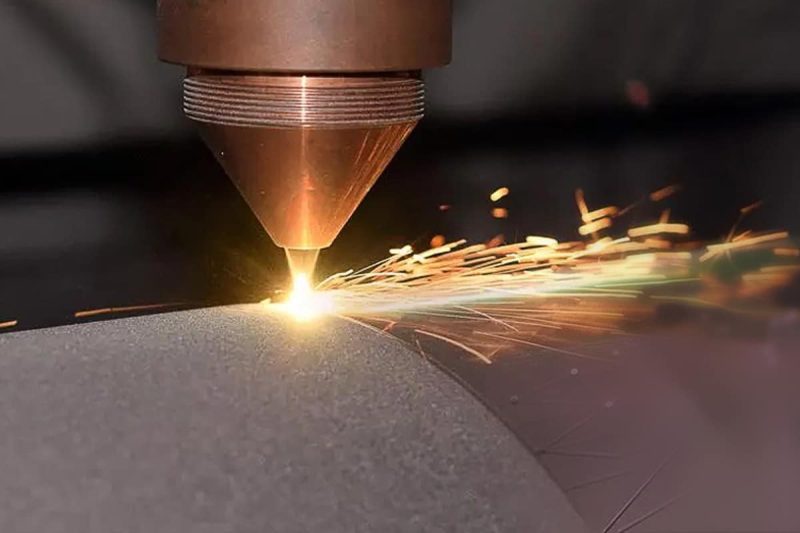
Optimizing Surface Roughness and Cleanliness for Laser Cleaning
Material Properties and Compatibility
- Material type: Understand the physical and chemical properties of the material to be cleaned, including melting point, thermal conductivity, reflectivity, absorption coefficient, etc., in order to select the appropriate laser type and parameters.
- Compatibility analysis: Evaluate the compatibility of the material with the laser cleaning process to ensure that the laser will not damage the material or change its surface properties.
Laser Parameter Optimization
- Laser wavelength selection: Select the appropriate laser wavelength according to the absorption characteristics of the material to improve cleaning efficiency and effect.
- Power and energy density: Adjust the laser power and energy density to ensure that contaminants can be effectively removed without damaging the material itself.
- Pulse width and frequency: Optimize the pulse width and frequency of the laser to achieve the best cleaning effect and surface roughness control.
- Scanning speed and overlap rate: Adjust the scanning speed and overlap rate of the laser beam to ensure uniform cleaning and improve surface finish.
Process Validation and Quality Control
- Experimental verification: Process verification is carried out under laboratory conditions to find the best cleaning solution by testing different parameter combinations.
- Quality inspection: Use optical microscopes, scanning electron microscopes (SEM) and other inspection methods to evaluate the surface roughness and cleanliness after cleaning.
- Standardized process: Establish standard operating procedures and quality control standards to ensure the repeatability and consistency of the cleaning process.
- Feedback and improvement: Continuously optimize and adjust the cleaning process based on quality inspection results and actual application feedback.
Operator Training and Skills Development
- Training plan: Develop a detailed training plan for operators to ensure that they understand the basic principles of laser cleaning and equipment operation.
- Skill improvement: Help operators master the skills of laser parameter adjustment and process optimization through practical operation and technical exchanges.
- Safe operation: Train operators to identify and prevent possible safety hazards and ensure the safe use of laser equipment.
- Continuing education: Regularly organize technical updates and training courses to keep the operator’s skill level in sync with technological progress.
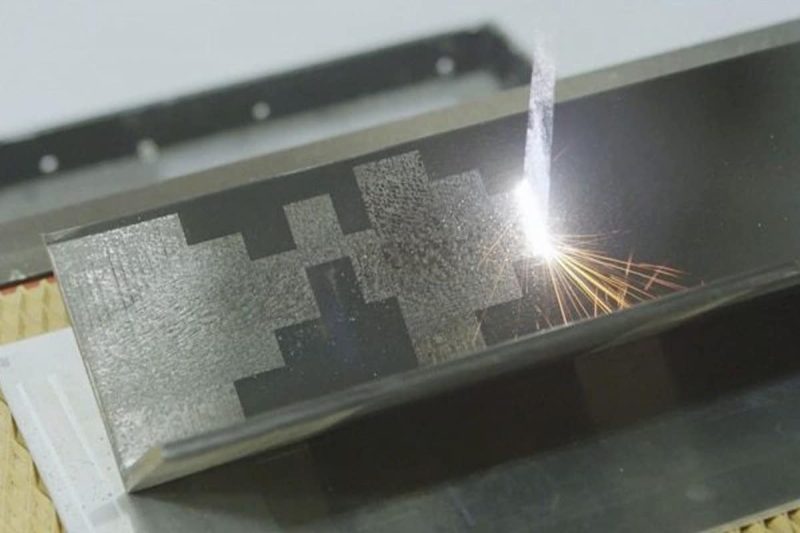
Summarize
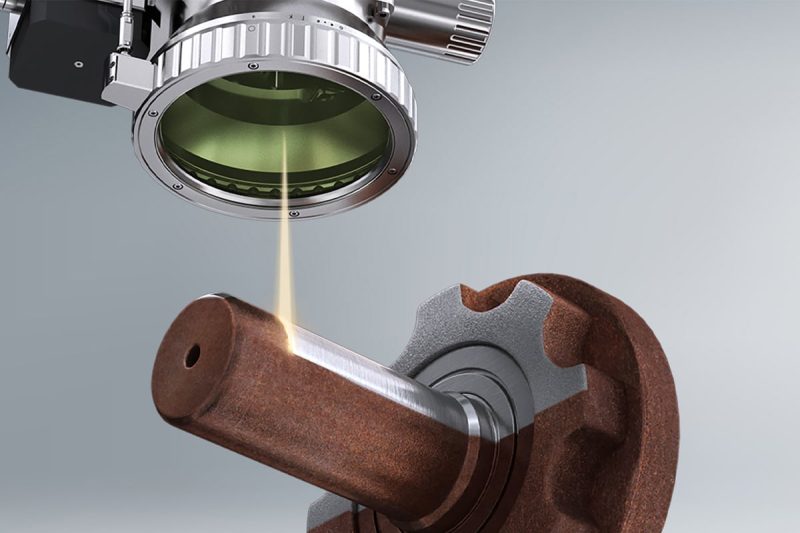
Get Laser Solutions
Choosing the right laser cleaning machine can help optimize power consumption and achieve high operational efficiency. Working with a trusted supplier ensures access to advanced technology, tailored advice and ongoing support. At AccTek Laser, we offer a comprehensive range of laser cleaning equipment designed to meet a variety of industrial needs. Our experts can help you choose the most energy-efficient model and configuration, taking into account factors such as material type, thickness and production volume. We also offer cutting-edge features such as high-efficiency laser generators, intelligent cooling systems and energy management software to maximize performance and minimize energy use. In addition, our team provides regular maintenance services and technical support to keep your equipment at peak efficiency. By partnering with us, you can achieve significant energy savings, reduce operating costs and enhance your sustainability efforts. If you have any questions, please contact us in time, AccTek Laser is committed to providing every customer with perfect laser solutions!
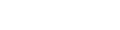
- [email protected]
- [email protected]
- +86-19963414011
- No. 3 Zone A, Lunzhen Industrial Zone,Yucheng City , Shandong Province.