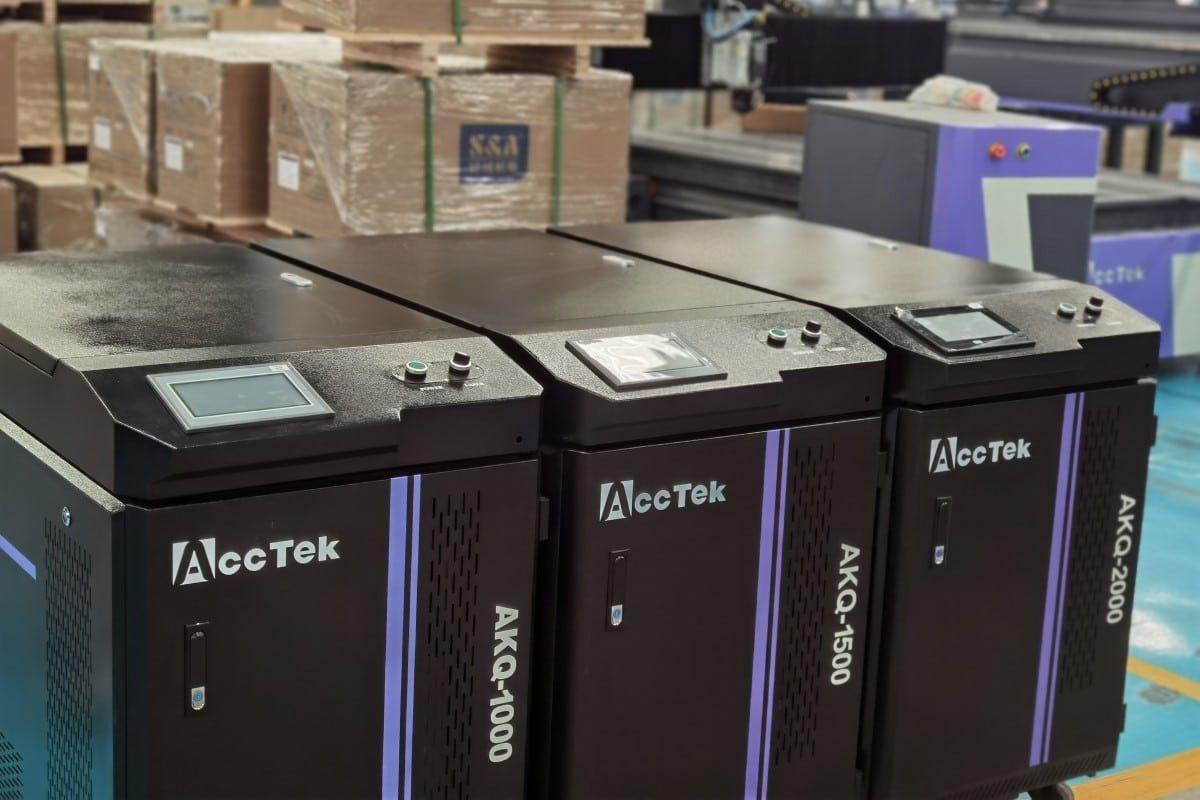
How Does Laser Cleaning Affect The Life And Durability of The Clean Surface?
Laser cleaning technology is a highly effective surface cleaning method that uses high-energy laser beams to remove dirt, coatings, and impurities. It has been widely used in many fields, including manufacturing, aerospace, the automotive industry, and cultural heritage protection. However, while laser cleaning offers many advantages, it can also have some impact on the longevity and durability of the surface being cleaned. This article will provide an in-depth look at the impact of laser cleaning technology on cleaning surfaces, including its potential benefits and challenges.
Table of Contents
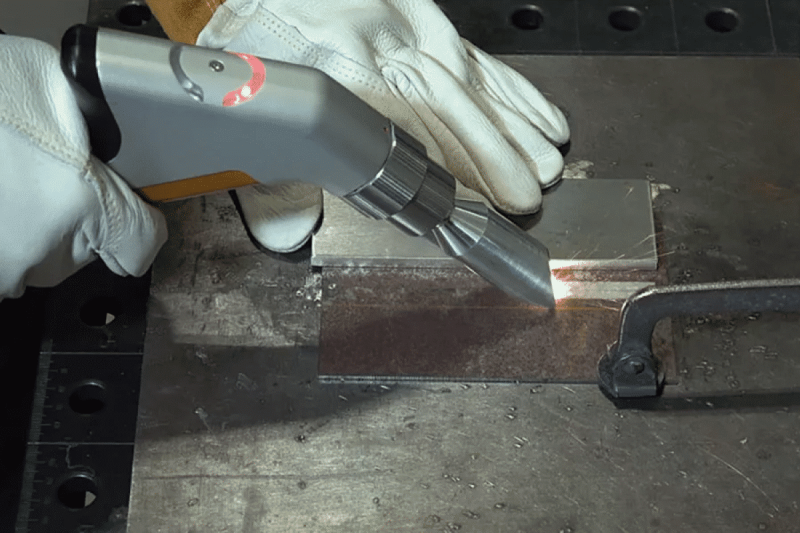
The principle of laser cleaning
Before we dive into how laser cleaning affects surface life, we first need to understand how laser cleaning works. Laser cleaning is a non-contact cleaning method that uses the high-energy beam of a laser to focus it on the surface that needs cleaning. This high-energy beam heats dirt, coatings, or impurities to extremely high temperatures, causing them to evaporate, break down, or peel away, resulting in a clean, contamination-free surface. Due to the highly directional nature of the laser beam, it can precisely clean the target area without damaging the surrounding area.
There are many types of laser cleaning technologies, including laser ablation cleaning, laser explosion cleaning, and laser melting cleaning. Laser cleaning is efficient, chemical-free, produces little waste, and works on a variety of surfaces. The basic principle is similar: using a laser beam to heat dirt or coatings and remove them. However, each type of laser cleaning has its specific applications and suitability and will have different effects on various cleaned surfaces.
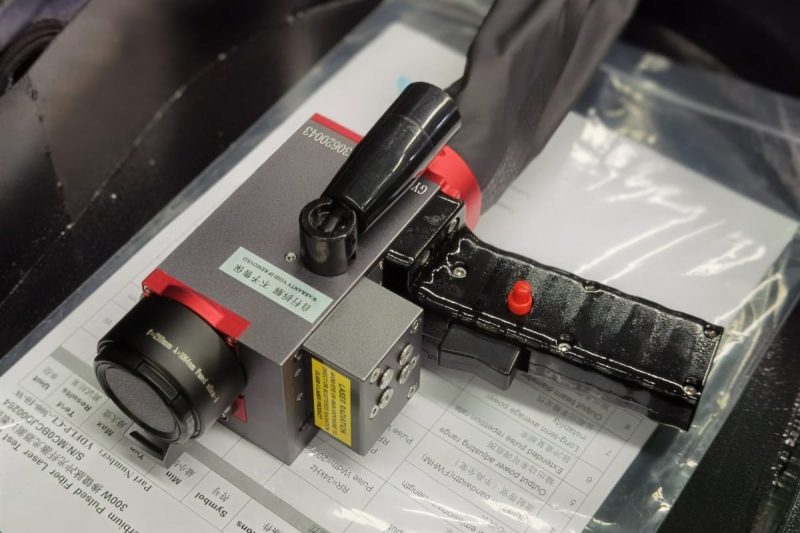
Possible impact of laser cleaning on surface life and durability
While laser cleaning offers many benefits, it may also have some impact on the longevity and durability of the surface being cleaned. Here are some potential influencing factors:
Improved surface quality
Laser cleaning improves the quality of surfaces by removing dirt, oxides, coatings, and other undesirable materials. This can extend the life of the surface because a cleaned surface is easier to maintain and maintain.
Scratches and dents
In some cases, laser cleaning can introduce tiny scratches or dents, especially when cleaning metal surfaces. These microscopic defects may cause the surface to be easily damaged during subsequent use, reducing its lifespan.
Chemical Reaction
Laser cleaning is usually performed in a high-temperature environment, and the laser beam triggers a chemical reaction as it cleans the surface. This may cause some chemicals to change or oxidize, affecting the corrosion resistance of the surface. Failure to properly control laser parameters or cleaning media may cause unexpected chemical reactions, accelerate surface corrosion, and reduce its service life.
Excessive cleaning
In some applications, a raw coating or protective layer may be present on the cleaned surface to prevent corrosion or abrasion. Excessive laser cleaning may strip the surface of its original coating or protective layer, making the surface more susceptible to erosion by the external environment. This can cause the surface to become more susceptible to rust, oxidation, or damage, shortening its life.
Thermal stress
Under the action of the high energy density of the laser beam, surface dirt, and coatings can quickly heat up and cool down quickly. This rapid thermal cycling can cause tiny thermal stresses that create tiny depressions or bumps in the surface. These microscopic-level changes may affect the optical properties, roughness, and mechanical properties of the surface to some extent. Especially for some high-precision and optical applications, such as lasers and optical lenses, this microscopic change may cause optical scattering and damage, reducing component performance and thus shortening its life.
The importance of post-processing
After laser cleaning, proper post-processing is important to restore or enhance the performance and durability of the surface. If post-treatment is not done properly or this step is ignored, the surface may become more susceptible to corrosion, abrasion, or other damage. Appropriate post-treatment may include recoating, anti-corrosion treatment, polishing, or other restorative measures.
Characteristics of surface materials
Different types of materials respond differently to laser cleaning. Materials such as metals, plastics, and ceramics may require different cleaning strategies. For example, metal surfaces are generally better suited for laser cleaning than plastic or ceramics because metals can withstand thermal stress better. Therefore, the material properties of the surface need to be considered when choosing a cleaning method. to minimize adverse effects on their lifespan.
Applicability and options
In some cases, laser cleaning may not be the best option. When considering cleaning methods, the type of material, application requirements, and suitability for laser cleaning need to be considered to ensure minimal impact on surface life.
Laser cleaning technology has great potential in many applications, but its potential impact on surface durability needs to be carefully considered when using it. Finding best practices and precautions can help minimize these potential impacts, ensuring that cleaned surfaces maintain their performance and durability over time.
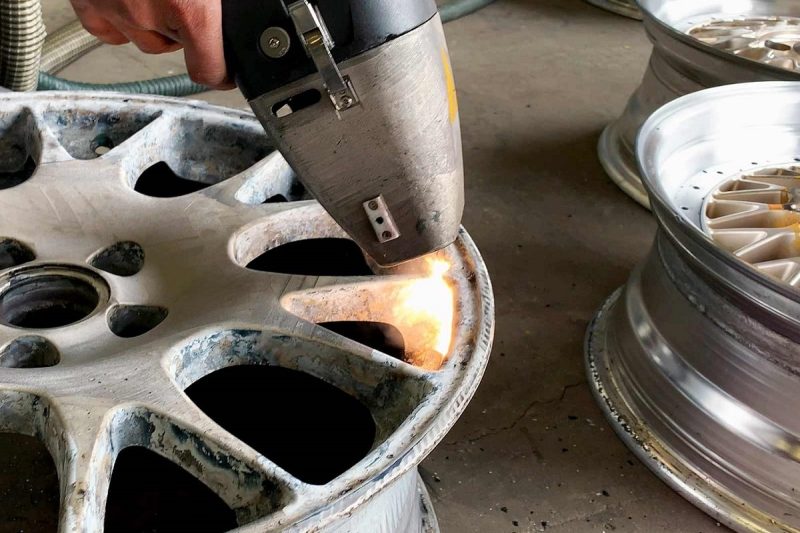
How to reduce the potential impact of laser cleaning on surface life and durability
To reduce the potential impact of laser cleaning on surface life and durability, here are some key measures and best practices:
Select appropriate laser parameters
Laser cleaning machines usually have multiple parameter setting options, including laser power, pulse frequency, beam diameter, cleaning speed, etc. Correct selection of these parameters is crucial for different types of surfaces. Here are some guidelines:
- Power Control: Avoid using too high a laser power as this may cause overheating and damage to the surface. Start with lower power and gradually increase to get the desired cleaning effect.
- Pulse frequency: Pulse frequency affects the cleaning effectiveness and surface impact of laser cleaning. Higher frequencies generally provide more uniform cleaning but also require higher laser power. Appropriate frequencies need to be chosen based on material properties to balance effectiveness and power requirements.
- Beam diameter: Beam diameter determines the size of the laser spot, thereby affecting the scope and depth of cleaning. Adjust the beam diameter to suit different cleaning tasks and surface types.
Surface quality assessment
Before proceeding with laser cleaning, it is important to fully evaluate the surface. This can help determine if any defects or damage are present and if special handling is required. Here are some assessment steps:
- Surface Inspection: Using visual inspection or other inspection methods to check surfaces for defects, coatings, or corrosion, which can help determine the appropriate method for cleaning.
- Material Type: Different materials may require different treatments, and understanding the material type of the surface being cleaned is critical to determining the suitability for laser cleaning.
Proper post-processing
After laser cleaning, appropriate post-processing steps may be required to maintain or improve the performance and durability of the surface. Here are some post-processing methods:
- Recoating: If the surface being cleaned requires a protective coating, ensure the quality and uniformity of the recoat will prevent further corrosion or damage.
- Anti-corrosion treatment: For metal surfaces, anti-corrosion treatment is the key to maintaining service life. Proper anti-corrosion treatment can prevent oxidation and corrosion.
- Polishing and surface restoration: For scratches or dents that appear after cleaning, polishing or surface restoration can be performed to improve the finish and quality of the surface.
Cleaning process control
Controlling how you operate during cleaning is important to reduce potential impacts:
- Maintain proper cleaning distance and angle: Make sure the laser beam hits the surface at the proper distance and angle to avoid over-cleaning or under-cleaning.
- Movement speed: Control the movement speed of the laser cleaning machine to ensure that the beam adequately treats dirt or coatings while avoiding excessively long exposure times.
- Monitor temperature: Surface temperatures need to be monitored during the cleaning process to ensure that the maximum temperature tolerance of the material is not exceeded.
Application-specific research and testing
Different applications and surface types may require different cleaning strategies. Before using laser cleaning technology, conduct adequate research and testing to determine the best cleaning methods and parameters.
Through the selection of appropriate laser parameters, surface quality assessment, appropriate post-processing and cleaning process control, the negative effects of laser cleaning can be reduced while ensuring maximum cleaning effectiveness and surface life.
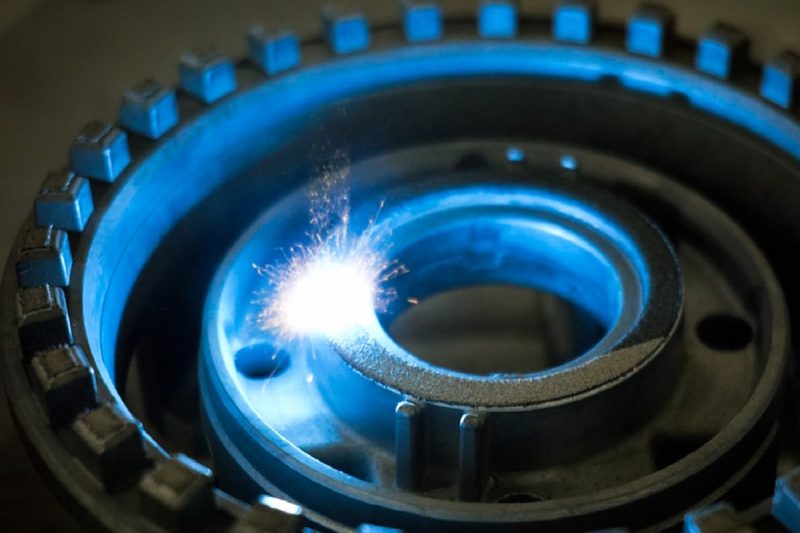
Benefits of using laser cleaning
Efficient cleaning
Laser cleaning effectively removes a variety of dirt and coatings, including paint, rust, coatings, and oxides. It is often faster and more thorough than traditional cleaning methods.
Contactless
Laser cleaning is a non-contact cleaning method that does not require physical contact with the surface, thus eliminating potential scratches or abrasions.
Precise control
Laser cleaning allows precise control of the cleaning process by adjusting laser parameters such as power, pulse frequency, and beam diameter to suit different types of surfaces and applications.
Environmental protection
Laser cleaning is generally more environmentally friendly than some traditional cleaning methods because it does not require the use of chemical cleaners or the generation of waste.
Versatility
Laser cleaning can be used on a variety of different types of surfaces, including metals, plastics, ceramics, stone, etc., and in a variety of applications such as industrial manufacturing, construction, cultural heritage protection, etc.
Less maintenance
Because laser cleaning is a non-contact method, there is less wear and tear on equipment and tools, requiring relatively few maintenance and replacement parts, which reduces operating costs.
Summarize
Laser cleaning technology can provide an efficient and precise cleaning method, but it requires special care when used to minimize its potential impact on the life and durability of the cleaned surface. Proper laser parameter settings, surface evaluation, appropriate post-processing, and application-specific research are all key factors in ensuring the long-term performance of cleaned surfaces.
Only through careful planning and practice can laser cleaning technology reach its full potential, providing efficient cleaning solutions for a variety of applications. Ultimately, the use of laser cleaning technology requires a combination of factors to achieve optimal cleaning results and maintenance of surface life.
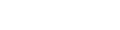
Contact information
- [email protected]
- [email protected]
- +86-19963414011
- No. 3 Zone A, Lunzhen Industrial Zone,Yucheng City , Shandong Province.
Get Laser Solutions