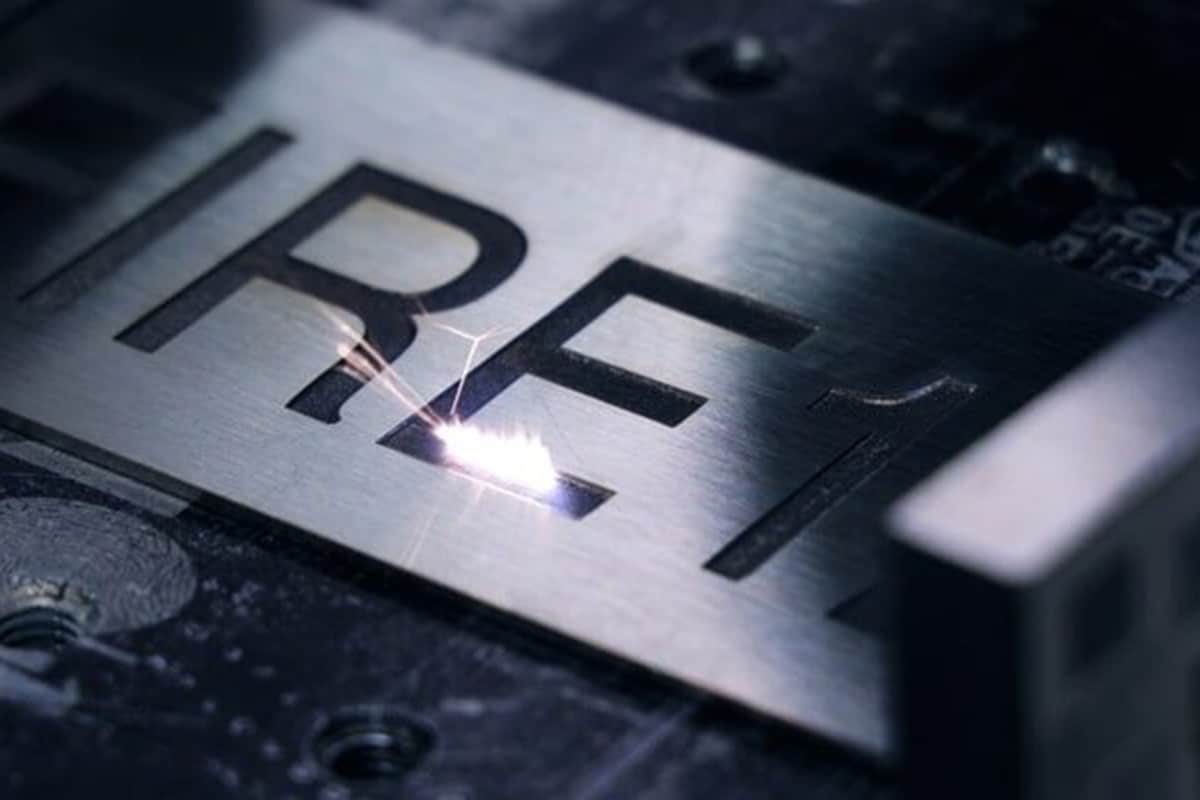
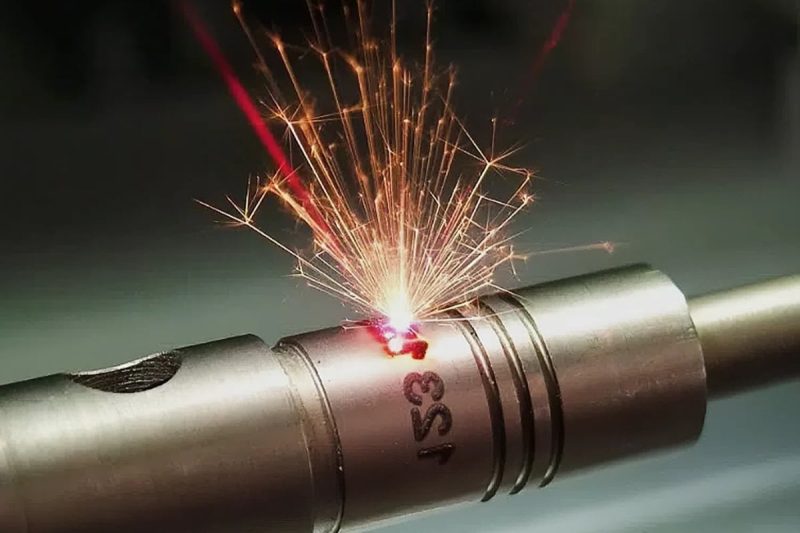
Laser Marking Introduction
Laser Marking Overview
Main Categories of Laser Marking Machines
Fiber Laser Marking Machine
CO2 Laser Marking Machine
UV Laser Marking Machine
Laser Marking Types
Laser Annealing
Laser Engraving
Laser Etching
Carbon Migration
Foaming
Color Change
Factors Affecting Laser Marking
Laser Parameters
Material Properties
Environmental Conditions
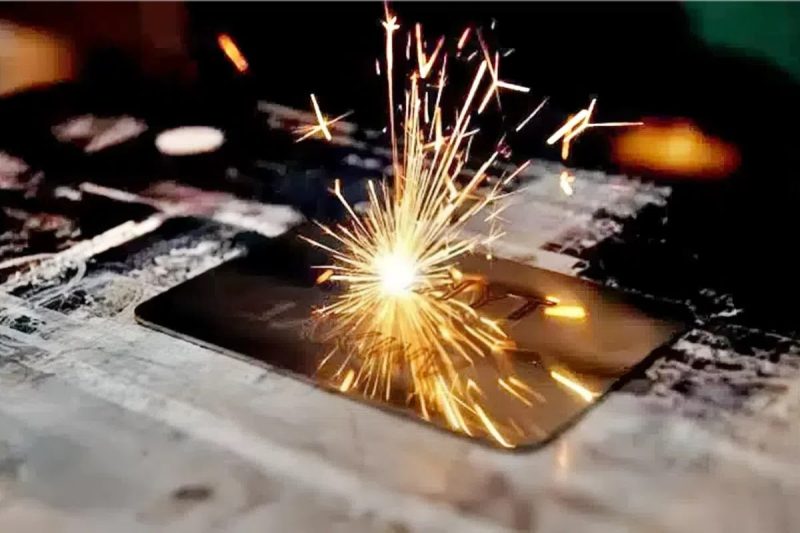
The Mechanism of Laser Marking on Metal
- Annealing marking: Annealing marking is the formation of an oxide layer on ferrous metals (iron, steel, high-quality steel) and titanium by local heating. Laser annealing is a marking technology that uses laser irradiation heat to induce local oxidation without significant material ablation.
- Laser etching: Laser etching uses a high-heat laser to melt only the surface of the metal material. Sometimes oxidation forms in the etched area, making the mark more clearly visible.
- Laser engraving: Laser engraving is the process of laser generating high heat during the engraving process to melt and vaporize the metal material. A visible and perceptible groove will be formed on the surface.
The Impact of Laser Marking on Different Metals
- Stainless steel: Stainless steel is widely used due to its good corrosion resistance and mechanical properties. Laser marking can form clear and durable marks on the surface of stainless steel, and it is not easy to wear. However, during the laser marking process, small white spots may appear, which is mainly caused by reasons such as too high laser power, too fast marking speed or unclean stainless steel surface.
- Aluminum: Laser marking on anodized aluminum is very simple because the laser removes the anodized layer to expose the metal underneath, providing high contrast. In addition, bare aluminum is aluminum, which is a lightweight, corrosion-resistant metal that can form clear marks on its surface. However, due to the high reflectivity and thermal conductivity of aluminum, the absorption rate of the laser beam on the aluminum surface is low, which may result in poor marking results or require higher laser power.
- Brass: Brass is a copper-zinc alloy with good processing performance and aesthetics. Laser marking can form clear and delicate marks on the surface of brass, and it is easy to control the engraving depth. However, too high laser power may cause ablation or deformation of the brass surface.
- Copper: Copper is a highly conductive and thermally conductive metal. It is prone to reflection problems during laser marking, which affects the marking effect. In addition, surface oxidation of copper may also affect the marking effect.
- Titanium: Titanium is a high-strength, corrosion-resistant metal. Laser marking can form high-quality marks on its surface. However, due to the high thermal conductivity of titanium, the heat-affected zone of the laser beam on the titanium surface may be large, and the laser parameters need to be precisely controlled to avoid material damage.
Common Challenges and Solutions
Reflectivity
- Metals with high reflectivity (such as aluminum and copper) may cause the laser beam to be reflected during laser marking, thus affecting the marking effect.
- Use anti-reflective coating.
- Adjust the laser angle.
Thermal conductivity
- Metals with high thermal conductivity (such as aluminum and titanium) may cause rapid heat diffusion during laser marking, increasing the heat-affected zone and the risk of material damage.
- Overheating may cause the metal to bend or discolor.
- To control heat, use a pulsed laser or adjust the power and speed of the laser.
- Cooling the metal between each process can also help solve the problem.
Oxidation
- Some metals (such as copper) are prone to oxidation when exposed to air for a long time, forming an oxide layer, which may affect the effect of laser marking.
- Clean and deoxidize the metal surface before marking.
- Select appropriate laser parameters to penetrate the oxide layer and form a clear mark on the metal substrate.
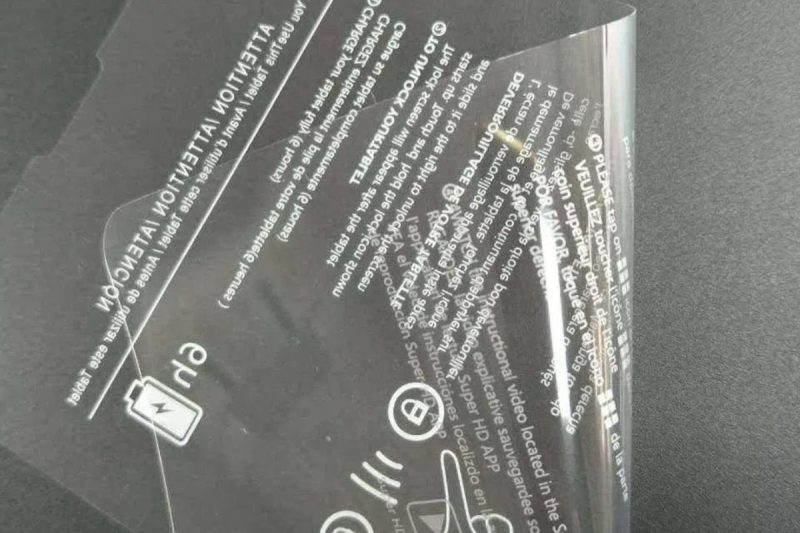
Mechanism of Laser Marking on Plastics
- Foaming/discoloration:The carbon in the plastic is destroyed and evaporated due to local heating, oxidized to form carbon dioxide, which is released from the plastic and forms a layer of foam, and then these materials cool to hard foam. Depending on the composition, the discoloration is lighter or darker. Dark plastics change color to white at the place to be marked, while light plastics change color to gray or black.
- Carbonization:In the case of laser carbonization, the plastic breaks and the carbon in it is released. The color of the marked material always becomes darker, and the resulting discoloration ranges from gray to blue-gray and black. Carbonization is used for light-colored plastics and organic materials (paper, packaging materials, wood and leather), where the color changes from light to dark.
Effects of Laser Marking on Different Plastics
Polycarbonate (PC)
- Characteristics: Polycarbonate is a plastic with high strength, high light transmittance and high heat resistance.
- Laser marking effect: Polycarbonate can be carbonized during laser marking, even under low-intensity laser beam irradiation, thus producing clear marks. This is because polycarbonate has a high absorption rate for lasers and is prone to physical or chemical changes under the action of lasers. It should be noted that the selection of laser parameters (such as power, frequency, scanning speed, etc.) is crucial to the marking effect. Too high or too low parameters may lead to poor marking results or damage to the material.
Acrylonitrile Butadiene Styrene (ABS)
- Characteristics: Acrylonitrile butadiene styrene (ABS) is a thermoplastic with excellent comprehensive properties, excellent mechanical properties, wear resistance and processing performance.
- Laser marking effect: Acrylonitrile butadiene styrene (ABS) has good responsiveness to lasers and can achieve clear and lasting marking on laser marking machines. Optimization of laser marking process parameters (such as current intensity, frequency, step length, etc.) is crucial to improving marking effects. For example, under appropriate parameters, foaming can occur on the surface of acrylonitrile butadiene styrene (ABS), thereby obtaining a marking effect with higher brightness.
Polyethylene (PE)
- Features: Polyethylene (PE) is a widely used thermoplastic with good low temperature resistance, chemical stability and electrical insulation.
- Laser marking effect: The laser marking machine can engrave clear and lasting marks on polyethylene (PE) pipes, such as production date, batch number, specification model, etc. These marks are essential for product traceability and quality control. Since the absorption rate of polyethylene (PE) material to laser is relatively low, higher laser power or longer processing time may be required to achieve the ideal marking effect.
Polypropylene (PP)
- Characteristics: Polypropylene (PP) is a non-toxic, odorless, low-density, high-strength, rigid and heat-resistant plastic.
- Laser marking effect: Laser marking machines are often used in the production line of polypropylene (PP) plastic products, such as basins, barrels, fresh-keeping boxes, furniture, films, woven bags and other products. UV lasers are particularly suitable for ultra-fine marking of plastics such as PP due to their extremely small focused spot and small heat-affected zone. UV laser marking can achieve high-speed and high-precision processing without causing thermal damage to the material.
Polyvinyl chloride (PVC)
- Characteristics: Polyvinyl chloride (PVC) is a polymer formed by a free radical polymerization mechanism, with excellent chemical resistance, insulation and flame retardancy.
- Laser marking effect: Polyvinyl chloride (PVC) materials can also produce clear marks during laser marking. However, due to the special properties of polyvinyl chloride (PVC) materials (such as heat sensitivity, easy decomposition, etc.), it is necessary to select appropriate laser parameters and processing strategies to avoid material damage or the generation of harmful gases. Ultraviolet lasers are widely used in the marking of polyvinyl chloride (PVC) materials because of their simple operation, difficult to erase marks, and environmental protection and pollution-free.
Challenges and Solutions
Thermal Damage
- We can choose to lower the machine power to avoid excessive carbonization of the material caused by high-intensity laser irradiation.
- Use cold processing marking equipment: UV laser marking machine.
Additives
- When laser marking on some plastic products, the laser marking machine cannot engrave or is unclear; such as common resins, ABS, PP, PE and other materials. In addition, during laser marking, bubbles may be generated on the surface of the plastic, resulting in unclear marking.
- We can add laser powder (laser engraving powder or laser additives) to the raw materials. The main function of laser powder is to absorb laser energy, convert the laser beam into heat energy, produce heat, carbonization, evaporation and chemical reactions caused by the discoloration of the additive itself, and form a marking pattern on the surface of the product.
Smoke
- The smoke generated by the laser marking machine is determined by the workpiece. Some metal products are difficult to release smoke. If it is a simple metal product, these fumes are almost odorless. If it is a plastic product or other products, it may produce an odor. Therefore, the smell and smoke of the laser marking machine are caused by the volatilization of the workpiece during the laser processing. The laser marking machine’s laser itself does not release smoke, so the source of the smoke belongs to these workpieces.
- The operator can wear a gas mask. In addition, the laser marking machine can be equipped with an exhaust system, which can effectively deal with the smoke generated during the laser marking process. You can also choose AccTek Laser’s fully enclosed laser marking machine, which can prevent dust and smoke from entering the working environment, thereby ensuring the safety of workers. The machine automatically exhausts the smoke generated during the marking process, thereby minimizing the risk of inhalation and contamination. The fully enclosed design also helps prevent accidents during the marking process, making it an excellent choice for many industries.
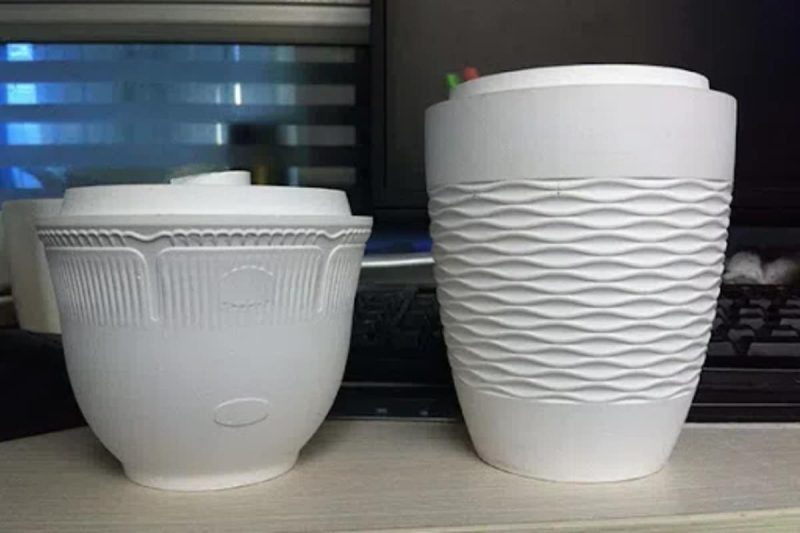
Mechanism of Laser Marking on Ceramics
The Impact of Laser Marking on Different Ceramics
The impact of laser marking on different ceramics varies due to their material properties and laser parameters. The following is a detailed analysis of several common ceramics such as alumina ceramics, zirconia ceramics, and glass ceramics:
- Alumina: Laser marking can produce clear, durable marks on alumina ceramics. Due to the high energy density of the laser, it can be irradiated locally on the ceramic surface, causing the surface material to vaporize or change color, forming obvious marks.
- Zirconium oxide: Laser marking technology uses laser beams to form clear graphics or text marks on the surface of zirconia ceramics. Since zirconia ceramics have the characteristics of high hardness and high wear resistance, laser marking can achieve high-precision marking on these materials, ensuring the clarity and durability of the marks.
- Glass ceramics: Laser marking uses high-energy-density laser beams to perform physical and chemical changes such as surface oxidation reaction or evaporation on glass ceramic materials to achieve marking patterns or text. This technology produces clear, detailed marks on glass ceramics that are extremely durable and resistant to wear or fading.
Challenges and Solutions
Brittleness
- Optimize laser parameters: By adjusting the laser power, pulse width, scanning speed and other parameters, reduce the thermal shock and mechanical stress on the ceramic material and reduce the risk of cracks.
- Use low-stress laser marking technology: such as ultraviolet laser marking technology, its short pulse and high energy density characteristics can reduce the heat-affected zone of ceramic materials, thereby reducing the possibility of cracks.
- Select suitable ceramic materials and processes: When possible, select ceramic materials with less brittleness and better processing performance, and optimize the preparation process of ceramics, such as grain refinement and pore reduction, to improve its crack resistance.
Surface Finish
- Pre-treat the ceramic surface: Clean and polish the ceramic surface before marking to remove surface defects and dirt and improve surface finish.
- Use high-precision laser marking equipment: Select laser marking equipment with high precision, such as equipment using a precision galvanometer scanning system, which can achieve fine marking on the ceramic surface and improve the clarity and edge accuracy of the mark.
- Control the quality of the laser beam: Ensure that the laser beam has good beam quality and stability to avoid diffusion or deformation of the laser beam during transmission, thereby affecting the marking effect.
Material Variability
- Strengthen raw material quality control: Strictly control the quality of ceramic raw materials to ensure that the raw material content, particle size distribution and other parameters meet the standard requirements and reduce material variability.
- Establish a laser marking process database: Through a large number of experiments and data analysis, establish a laser marking process database for different ceramic materials to provide reliable process parameters and reference basis for actual production.
- Real-time monitoring and adjustment: Real-time monitoring of laser marking effects during the production process, and timely adjustment of laser parameters and process conditions according to actual conditions to ensure the consistency and stability of the marking effect.
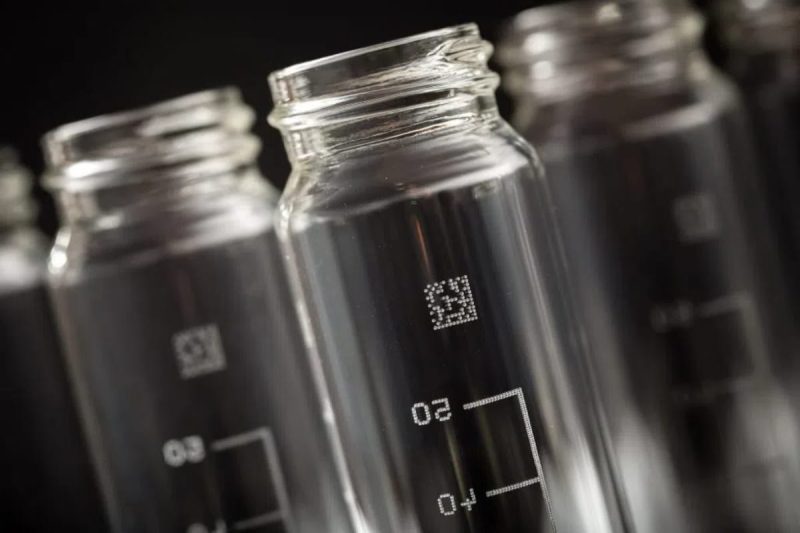
Mechanism of Laser Marking on Glass
Laser marking uses high-energy-density lasers to irradiate the local surface of glass. The two main types of marking are engraving and surface modification. Different types present different effects, and we can adjust the laser according to the effects we need.
- Engraving:The engraving process in which the laser beam is precisely controlled on the surface or inside of the glass to form the desired pattern or shape.
- Surface modification: The surface modification process in which the laser beam irradiates the glass surface to change its surface properties.
The Impact of Laser Marking on Different Glasses
Soda-lime glass
- Features: Soda-lime glass is the most common form of glass, accounting for about 90% of all glass production. Soda-lime glass, also known as SLS glass, consists of about 70% S (silicon dioxide), 15% S (sodium oxide) and 9% L (calcium oxide), as well as small amounts of other compounds used as clarifiers or to control color.
- Laser marking effect: Glass laser marking can be done by heating the glass surface with a CO2 laser. This will produce a series of surface microcracks, forming a uniform mark with a frosted appearance. Compared with other glass marking methods, laser marking of glass can produce more delicate and complex design effects.
Borosilicate glass
- Features: Borosilicate glass is a type of glass that is resistant to high temperatures and has high strength. Its chemical and thermal stability are better than ordinary soda-lime glass.
- Laser marking effect: The laser can form a clear, crack-free mark with moderate protrusion height on the glass surface. This processing method can keep the optical and physical properties of the glass intact. Commonly used in the manufacture of laboratory utensils, cookware, optical components, etc.
Tempered glass
- Characteristics: Tempered glass is a type of glass made by heating and rapid cooling, with high heat resistance and impact resistance. A compressive stress layer is formed on its surface, and a tensile stress layer is generated inside, which improves the strength and stability of the glass.
- Laser marking effect: Laser marking can form clear and durable marks on tempered glass. These marks will not affect the physical properties and strength of tempered glass. At the same time, the laser marking imprint has a high degree of anti-counterfeiting and traceability, and is suitable for application scenarios that require high security.
Challenges and Solutions
Cracking
- Adjust laser energy: According to the thickness and density of the glass, reasonably set and adjust the laser energy to ensure that the laser does not damage the material during the engraving process. If the laser energy is too high and causes the glass to crack, the laser energy can be appropriately reduced.
- Choose suitable glass material: Avoid using too thin glass, and choose thicker glass to improve its ability to resist laser damage.
- Optimize pattern design: Design simple patterns and avoid overly complex and delicate engraving to reduce damage to the glass material.
Surface Reflection
- Surface treatment: Roughen the glass surface, such as grinding with sandpaper or corroding with chemical reagents, to reduce the reflectivity. You can also consider coating the glass surface with a layer of light-absorbing material, such as black paint or special coating.
- Adjust laser parameters: Improve the reflection problem by adjusting the power, speed, frequency and other parameters of the laser marker. Appropriately increasing the power, reducing the marking speed, and increasing the frequency can reduce light reflection and improve the accuracy of marking.
- Clean the lens: Clean the lens of the laser marker regularly to prevent dust and other impurities from affecting the reflectivity.
Consistency
- Select high-precision equipment: Select high-precision and stable laser marking equipment to ensure the stability and accuracy of the marking process.
- Optimize the operation process: Develop standardized operation procedures, provide professional training for operators, and ensure that each marking operation is carried out in accordance with the standard process.
- Environmental control: Maintain the stability of the marking environment, such as temperature, humidity, light, etc., to reduce the impact of environmental factors on the marking results.
- Regularly calibrate equipment: Regularly calibrate and maintain laser marking equipment to ensure the accuracy and stability of the equipment.
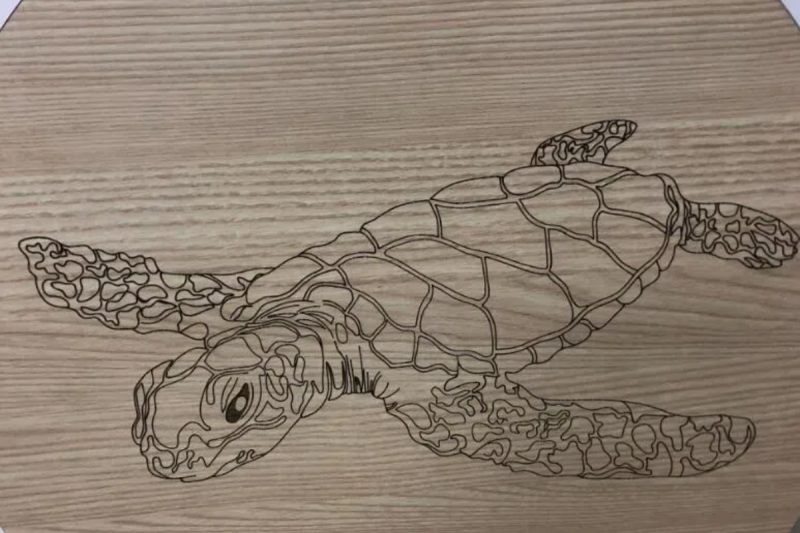
Mechanism of Laser Marking on Wood
The Impact of Laser Marking on Different Types of Wood
Hardwood
- Characteristics: Hardwood has high hardness and density.
- Laser marking effect: Laser marking can form clear and lasting marks. The laser beam can accurately remove the material on the surface of hardwood, leaving fine graphic marks. High-precision laser marking machines (such as UV lasers) can achieve finer patterns and text printing on hardwood, improving the beauty and recognition of products.
Cork
- Characteristics: Cork has low density and soft texture.
- Laser marking effect: The laser beam can more easily remove its surface material. The marking process is relatively fast and the marking quality is good. It is also suitable for various cork materials, such as pine, fir, etc. Its flexible processing method can meet the marking needs of cork products of different shapes and sizes.
Plywood
- Characteristics: small deformation, large format, convenient construction, no warping, good cross-grain tensile mechanical properties, etc.
- Laser marking effect: The effect of laser marking on plywood is similar to that on solid wood. The laser beam can penetrate the surface of the plywood and mark the internal materials. It should be noted that the engraving depth should not be too deep to avoid damaging the internal structure of the plywood. The laser marking machine is suitable for various types and thicknesses of plywood. Its efficient processing method can meet the marking needs of mass production of plywood.
Medium Density Fiberboard (MDF)
- Characteristics: Compared with solid wood, the processing performance of medium-density fiberboard is more stable and is less prone to problems such as deformation or cracking.
- Laser marking effect: Laser marking has good effect on medium density fiberboard. The laser beam precisely removes material from its surface, creating clear, long-lasting marks. Laser marking machines are widely used for medium density fiberboard products of various types and thicknesses. Its efficient processing method can meet the marking needs of medium-density fiberboard mass production.
Challenges and Solutions
Burning and Carbonization
- The operator must pay close attention to the settings of the laser, including the laser power and cutting speed. The correct laser settings, especially the speed and power settings, help to strike the right balance between accuracy and preventing carbonization.
- Adequate ventilation helps to dissipate the fumes generated during cutting, reducing the chance of burns and ensuring a safer working environment.
- In addition, the choice of materials is crucial when using. Selecting wood with a lower resin content can help reduce the risk of igniting volatile compounds in the wood.
Inconsistent Texture
- Pre-treat the wood: Before laser marking, pre-treat the wood by grinding and polishing to make the surface flatter and smoother, which helps to achieve a more consistent marking effect.
- Adjust laser parameters: According to the texture characteristics of the wood, adjust the laser power, speed, scanning path and other parameters to adapt to the texture changes in different areas.
- Use image processing technology: Introduce image processing technology in the laser marking software to identify and analyze the texture of the wood, and automatically adjust the laser parameters to match the texture changes.
Adhesives
- Choose the right adhesive: When manufacturing products such as plywood, choose an adhesive that has less impact on laser marking.
- Adjust laser parameters: For wood products containing adhesives, appropriately adjust the laser power, speed, scanning path and other parameters to reduce the impact of the adhesive on the marking effect.
- Post-processing: After laser marking, post-process the marked area, such as grinding, cleaning, etc., to remove possible bubbles or blurred edges and improve the marking quality.
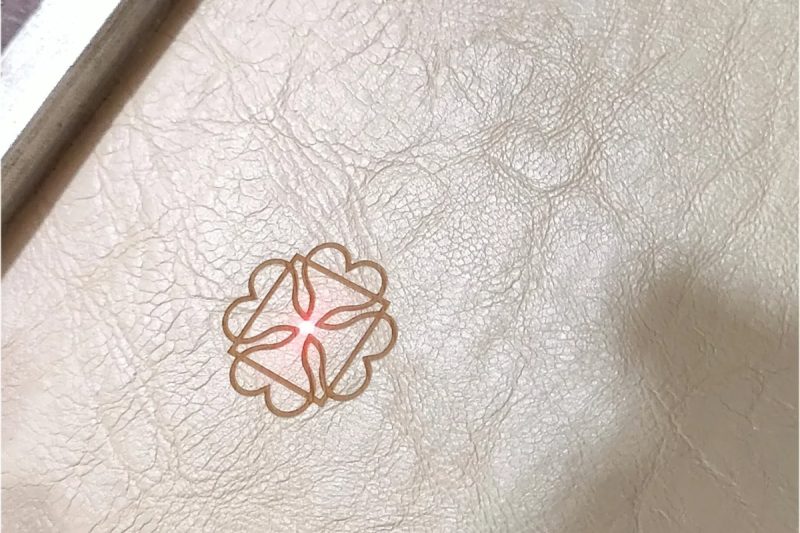
Mechanism of Laser Marking on Textiles
Depending on the laser intensity and material properties, we can cut the textiles, produce pattern engravings with a certain depth, and also change the pattern by simply changing the color of the textiles.
- Color change: Some textiles change color or hue when exposed to a CO2 laser beam, but the surface appearance changes without any material being removed. Laser marking can be used to produce visible patterns and designs on the surface of textiles.
- Engraving: Both natural and synthetic textiles readily absorb the energy of a CO2 laser beam. The high-energy laser beam generated by the laser can cause the textile to melt instantly or even vaporize. The power of a CO2 laser beam can be limited so that it removes (engraves) material to a specified depth.
- Cutting: If the laser power is high enough, the laser beam will completely penetrate the textile. When cut with a laser, most textiles vaporize quickly, resulting in a smooth and straight edge with a small heat-affected zone. In some cases, laser cutting seals the edge, preventing the textile from unraveling.
The Impact of Laser Marking on Different Types of Textiles
Natural Fibers
Natural fibers such as cotton, linen, silk, and wool have their own unique physical and chemical properties.
- Cotton fiber: Cotton fiber has a strong absorption capacity for lasers, and it is easy to form clear marks on the surface during laser marking. However, due to the flammability of cotton fibers, the energy density needs to be strictly controlled during laser processing to prevent excessive burning or carbonization.
- Hemp fiber: Hemp fiber is similar to cotton fiber and is also sensitive to laser response. Laser marking can form obvious patterns or text on the surface of hemp fiber, but it is also necessary to prevent burning.
- Silk fiber (such as silk): The surface of silk fiber is smooth and delicate. Laser marking can form fine marks without damaging the fiber structure. However, the heat resistance of silk fiber is relatively poor, so the selection of laser parameters needs to be more precise.
- Wool fiber (such as wool): The laser marking effect of wool fiber depends on its specific type and treatment method. Some wool fibers may produce a slight burnt smell or smoke under the action of laser, but reasonable laser parameter settings can reduce this effect.
Synthetic Fibers
Synthetic fibers such as polyester, nylon, spandex, etc. have excellent physical properties and chemical stability.
- Polyester: Polyester fibers respond well to lasers, and laser marking can form clear and lasting marks on their surfaces. Polyester has good heat resistance and is not easy to burn or deform.
- Nylon: Nylon fibers are similar to polyester and also have good laser processing performance. Laser marking can form fine patterns or text on the surface of nylon, and the marking quality is stable.
- Spandex: Spandex is an elastic fiber that is often used in the elastic part of clothing. The effect of laser marking on spandex is relatively small, but it is necessary to control the laser energy to prevent damage to the elastic properties of the fiber.
Blended Fibers
Challenges and Solutions
Burning and Melting
- Precisely control laser parameters: According to the material, thickness and required marking depth of the textile, accurately adjust the laser power, wavelength, pulse width and other parameters to ensure that the laser energy is within a controllable range.
- Introduce a cooling system: Equip the laser marking machine with a cooling system, such as a water cooling or air cooling device, to dissipate the heat generated during the laser marking process in a timely manner and reduce the temperature of the textile surface.
- Optimize the marking path and speed: By optimizing the movement path and marking speed of the laser beam, the laser residence time on the textile surface is reduced, thereby reducing the risk of burning and melting.
Wear and Tear
- Choose a suitable laser: According to the material and characteristics of the textile, choose a suitable laser wavelength and power to reduce the wear and tear on the textile surface.
- Adjust the marking depth: Control the depth of laser marking to avoid damage to the internal structure of the textile and surface wear caused by too deep marking.
- Use auxiliary materials: Before laser marking, a layer of auxiliary materials, such as a high temperature resistant and wear resistant coating or film, can be applied to the textile surface to protect the textile surface from wear and tear.
Color Consistency
- Sample testing: Before marking, test the sample with laser marking to determine the best laser parameters and marking effect. By comparing the marking effects under different parameters, select the solution with the best color consistency for production.
- Color management: Establish a color management system to perform color calibration and color matching on the laser marking machine to ensure color consistency of marking at different times and on different devices.
- Select the appropriate laser type: According to the color characteristics and marking requirements of the textile, select the appropriate laser type (such as fiber laser, CO2 laser, etc.) to obtain better color consistency and marking effect.
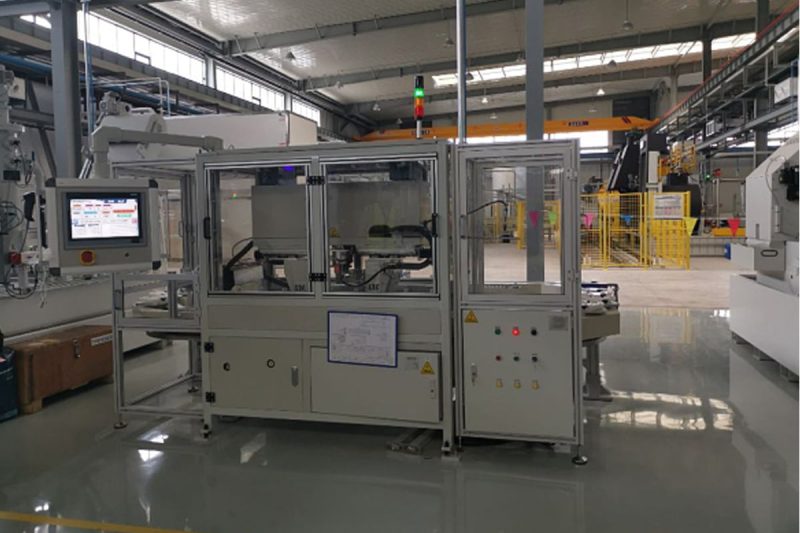
Environmental and Safety Considerations
Material safety
Smoke and particles
- Use the exhaust system to promptly discharge the generated smoke and particles from the work area.
- Regularly check and maintain the exhaust system to ensure its effective operation.
- Operators should wear personal protective equipment such as dust masks or respirators.
Thermal effect
- Accurately control laser parameters such as power, pulse width, etc. to avoid excessive energy input.
- Introduce a cooling system, such as water cooling or air cooling, to reduce the surface temperature of the material.
- Regularly check and maintain the cooling system to ensure its normal operation.
Laser safety
Laser level
- Before operation, you must understand the level and potential hazards of the laser equipment.
- Strictly abide by the safety operating procedures of the laser equipment.
Protective equipment
- Operators should wear appropriate personal protective equipment, including laser protective glasses and protective clothing.
- The laser marking machine should be set up in a dedicated working area to prevent unintentional contact by non-operating personnel.
- Regularly check and maintain the safety system of the laser marking machine.
Environmental impact
Energy consumption
- Choose a laser marking machine model with high energy efficiency.
- Arrange production plans reasonably to reduce the idle time of the equipment.
- Maintain and maintain the equipment regularly to ensure that it is in the best working condition.
Waste management
- Collect and treat the generated waste in a classified manner.
- Use environmentally friendly materials for marking to reduce the generation of hazardous waste.
- Comply with local environmental protection laws and regulations and send hazardous waste to designated treatment agencies for treatment.
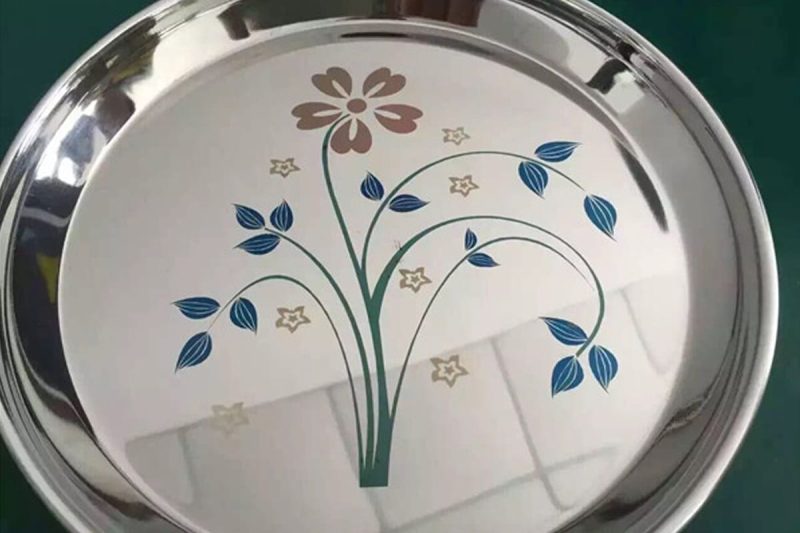
Summary
Get Laser Solutions
AccTek Laser is a leading supplier of professional laser marking technology, providing comprehensive solutions tailored to meet diverse industry needs. We place great emphasis on safety and efficiency, ensuring that each operator is fully trained to master the operation of its advanced laser cleaning equipment. Our training programs cover essential areas such as understanding laser technology, mastering machine components, and adhering to strict safety protocols. By partnering with AccTek Laser, companies gain access to cutting-edge laser marking technology, backed by expert training and support. This not only maximizes the effectiveness of the marking process, but also ensures operator safety and compliance with regulatory standards. Choose AccTek Laser for reliable, efficient, and safe laser marking solutions that meet the specific needs of your industry.
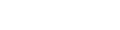
- [email protected]
- [email protected]
- +86-19963414011
- No. 3 Zone A, Lunzhen Industrial Zone,Yucheng City , Shandong Province.