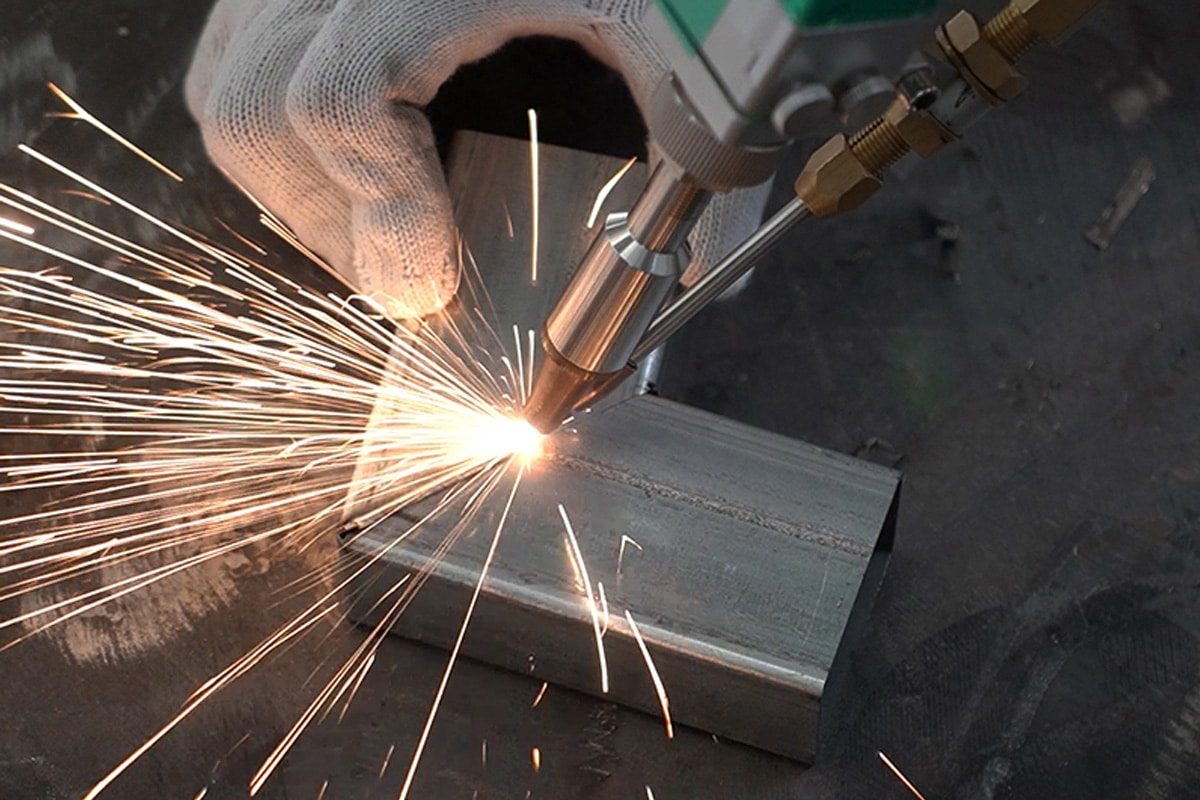
As an efficient and precise welding technology, laser welding has been widely used in modern manufacturing. It uses a laser beam as a heat source, and the laser generator emits a high-energy-density laser beam to melt and connect materials. Compared with traditional welding methods (gas metal arc welding (GMAW/MIG), gas tungsten arc welding (GTAW/TIG), shielded metal arc welding (SMAW) and flux-cored arc welding (FCAW)), laser welding has many unique advantages, such as high precision and high efficiency of the welding process and a smaller heat-affected zone. However, the effect and quality of laser welding are affected by many factors, among which material thickness is a key factor. This article will explore how material thickness affects the selection of laser welding machine parameters and provide optimization methods for different material thicknesses.
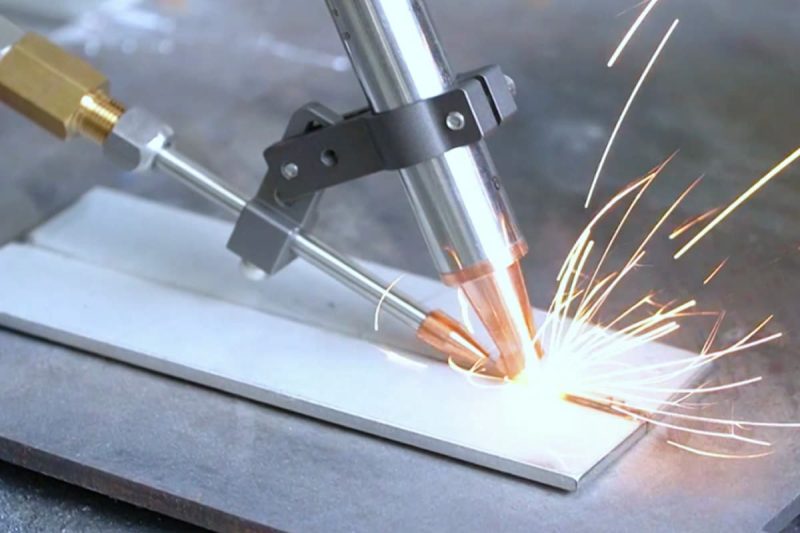
Laser Welding Basics
Laser Welding Process Description
Laser welding is a welding process that uses a laser beam as a heat source to melt and connect metals or other materials. The process includes the following steps:
- Laser beam focusing: The laser beam emitted by the laser generator is focused onto the welding head through an optical system.
- Material heating: The high energy density of the laser beam heats the material to its melting point, causing the material to melt or vaporize locally.
- Molten pool formation: The molten material forms a molten pool, and the continuous action of the laser beam keeps the molten pool liquid.
- Solidification and connection: When the laser beam moves or stops, the molten pool cools and solidifies, completing the welding process.
There are two types of laser welding processes, thermal conduction welding and keyhole welding.
- Thermal conduction welding: The laser beam heats the surface of the material above the melting point of the material, only produces melting on the welding surface, the inside of the workpiece is not fully penetrated, and basically no vaporization occurs. This process is mainly used to weld thin-walled materials. Thermal conduction welding produces smooth and beautiful welds.
- Keyhole welding: In keyhole welding, the laser beam heats the surface of the material to the vaporization point and penetrates into the material. The material evaporates to form a small hole. The hole filled with steam absorbs almost all the incident beam energy. The equilibrium temperature in the hole is about 2500℃. The heat is transferred from the outer wall of the high-temperature hole to melt the metal around the hole. The keyhole is filled with high-temperature steam generated by the continuous evaporation of the material under the irradiation of the beam. The laser beam continuously enters the hole, and the material outside the hole flows continuously. As the beam moves, the hole is always in a stable flow state. That is, the molten metal around the small hole and the hole wall moves forward at the speed of the beam. The molten metal fills the gap left by the movement of the small hole, and then condenses to form a weld.
Key Components of Laser Welding Systems
The key components of the laser welding system are:
- Laser generator: generates and emits laser energy. Common laser generators include fiber laser generators, gas laser generators, etc.
- Optical system: includes focusing lenses and mirrors for adjusting and focusing the laser beam.
- Laser transmission system: a system for transmitting the laser beam from the laser source to the welding position.
- Welding head: includes laser focusing mirror, collimating mirror and protective gas nozzle for actual welding operation.
- Control system: used to control various parameters of laser welding, such as laser power, welding speed, etc.
Advantages of Laser Welding over Traditional Welding Methods
Welding Quality
- The heat affected zone of laser welding is small, because the energy density of the laser beam is high, the heating time is short, and the heat loss is small, so the heat affected zone of the material is small, which can reduce the deformation, cracking, oxidation and other problems of the material.
- The depth-to-width ratio of the weld of laser welding is high, because the diameter of the laser beam is small and the energy is concentrated, so it can form a deep and narrow weld, which improves the strength and sealing of the welding.
- The weld of laser welding is smooth and beautiful, because the spot of the laser beam is stable, and the welding position and parameters can be accurately controlled, so it can form a smooth and beautiful weld, reducing the subsequent grinding and polishing.
- There are fewer welding defects in laser welding, because laser welding does not require the use of auxiliary materials such as electrodes, welding rods, and shielding gases, so it can avoid the generation of welding defects such as electrode contamination, pores, slag inclusions, and cracks.
Welding Efficiency
- Laser welding has a fast welding speed. Because the energy density of the laser beam is high and the heating time is short, the welding process can be completed quickly, which improves production efficiency.
- Laser welding has high welding flexibility. Because the laser beam is a non-contact heat source, it can be transmitted and controlled by optical fiber, reflector, robot, etc., so it can adapt to various complex welding positions and shapes, improving production flexibility.
- Laser welding has a high degree of welding automation. Because laser welding can be accurately controlled and adjusted by computer or CNC system, it can achieve a high degree of automation and intelligence, reducing manual intervention and errors.
Welding Applications
- Laser welding has strong material adaptability, because the heat source of laser welding is a non-contact heat source, which can weld various metal or non-metal materials, and even weld different types of materials to achieve the connection of dissimilar materials.
- Laser welding has strong industry adaptability, because the heat source of laser welding is an efficient heat source, which can achieve high-quality, high-speed, and highly automated welding, so it can be applied to various high-end industries, such as aerospace, automobile, electronics, medical, etc.
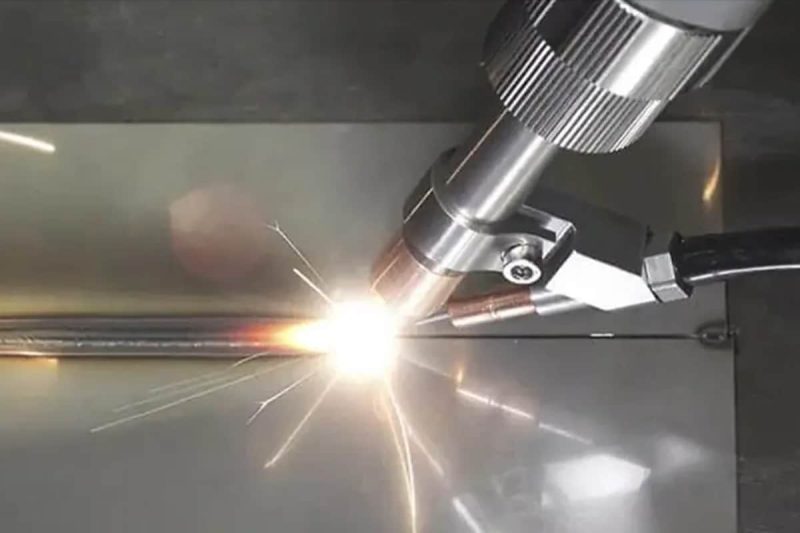
Effect of Material Thickness on Welding Parameters
Laser Power
Pulse Duration and Frequency
Welding Speed
Focus Position
Beam Diameter
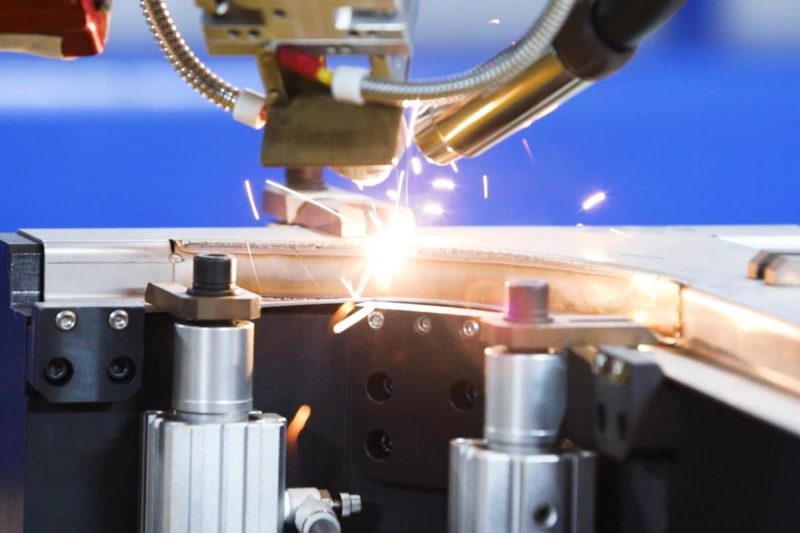
Optimizing Laser Welding Parameters for Different Material Thicknesses
Thin Materials (<1mm)
- Laser power: A lower laser power should be selected to avoid overheating and excessive melting. It is usually selected in the range of tens of watts to hundreds of watts.
- Pulse duration and frequency: Shorter pulse duration and higher frequency help provide rapid heating and cooling cycles, reducing thermal effects.
- Welding speed: Higher welding speeds can be used to improve production efficiency and avoid overheating.
- Focus position: The laser focus should be set near the surface of the material for the best welding effect.
- Beam diameter: Use a smaller beam diameter to improve the accuracy and detail control of welding.
Medium Thickness Materials (1mm-5mm)
- Laser power: Moderate laser power needs to be selected to ensure welding depth and quality. Usually selected in the range of several hundred watts to kilowatts.
- Pulse duration and frequency: According to the specific material thickness, select medium pulse duration and frequency to balance the heating and cooling effects.
- Welding speed: Moderate welding speed should be selected according to the material thickness to ensure welding quality and production efficiency.
- Focus position: The laser focus should be set in the middle of the material to ensure welding depth and uniformity.
- Beam diameter: Select a moderate beam diameter to balance energy distribution and welding accuracy.
Thick Material (>5mm)
- Laser power: A higher laser power needs to be selected to provide sufficient heat input to ensure welding depth and quality. Usually selected in the range of several kilowatts.
- Pulse duration and frequency: Longer pulse duration and lower frequency can provide more sufficient heat input to melt thicker materials.
- Welding speed: A slower welding speed should be selected to ensure that the laser beam can effectively penetrate and melt the material.
- Focus position: The laser focus should be set inside the material to ensure that the laser beam can effectively penetrate and melt the material.
- Beam diameter: Use a larger beam diameter to provide sufficient energy density and welding depth.
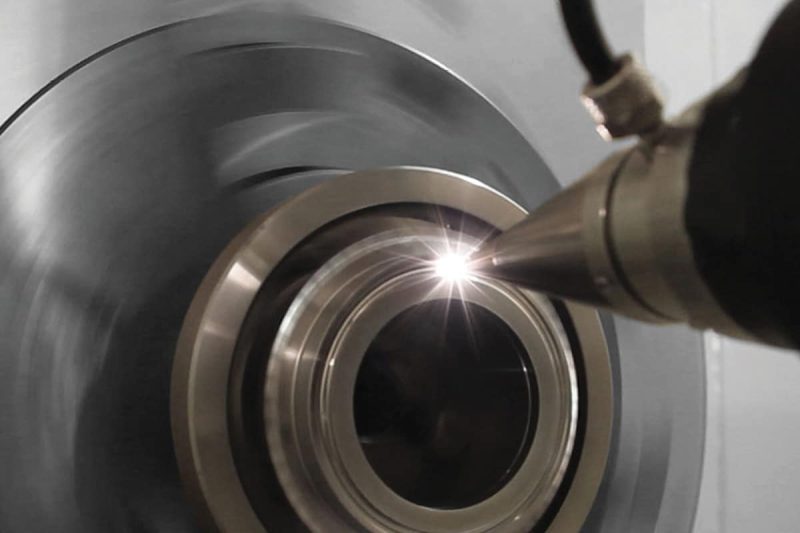
Summarize

Get Laser Solutions
Choosing the right laser welding machine can help optimize power consumption and achieve high operational efficiency. Working with a trusted supplier ensures access to advanced technology, tailored advice and ongoing support. At AccTek Laser, we offer a comprehensive range of laser welding equipment designed to meet a variety of industrial needs. Our experts can help you choose the most energy-efficient model and configuration, taking into account factors such as material type, thickness and production volume. We also offer cutting-edge features such as high-efficiency laser generators, intelligent cooling systems and energy management software to maximize performance and minimize energy use. In addition, our team provides regular maintenance services and technical support to keep your equipment at peak efficiency. By partnering with us, you can achieve significant energy savings, reduce operating costs and enhance your sustainability efforts. If you have any questions, please contact us in time, AccTek Laser is committed to providing every customer with perfect laser solutions!
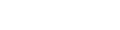
- [email protected]
- [email protected]
- +86-19963414011
- No. 3 Zone A, Lunzhen Industrial Zone,Yucheng City , Shandong Province.