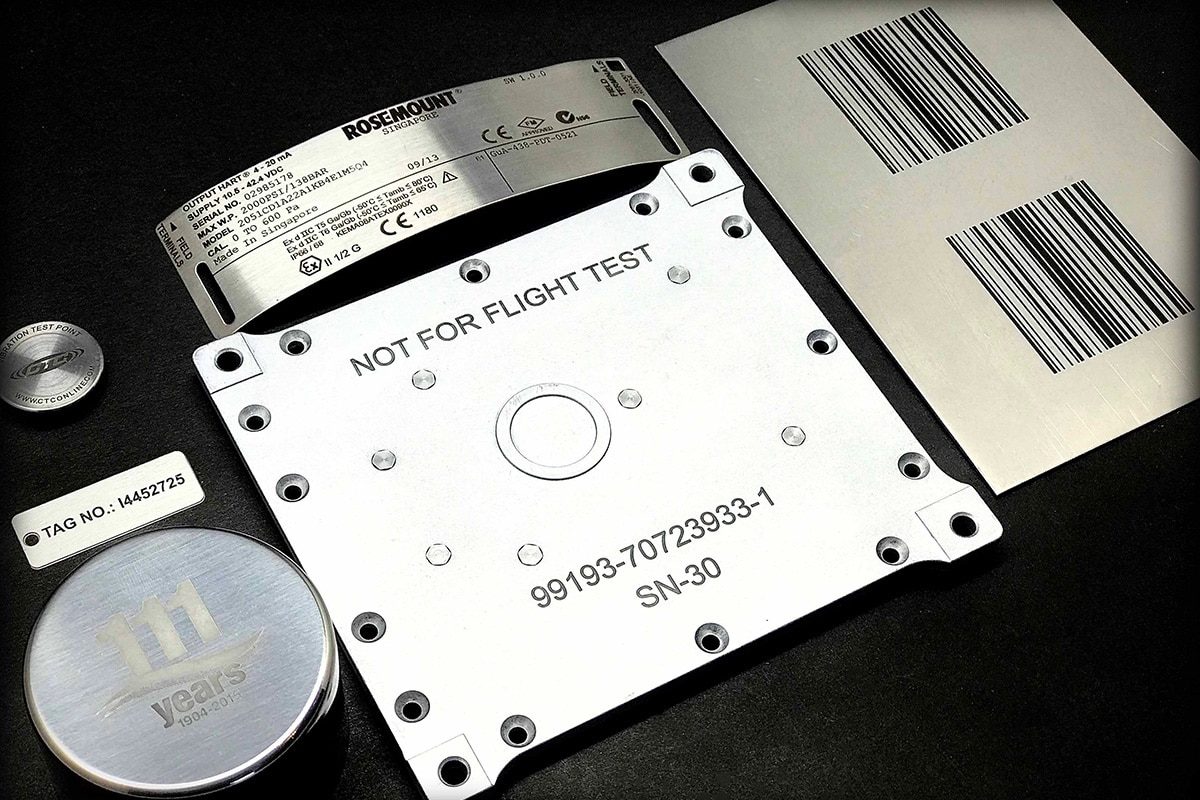
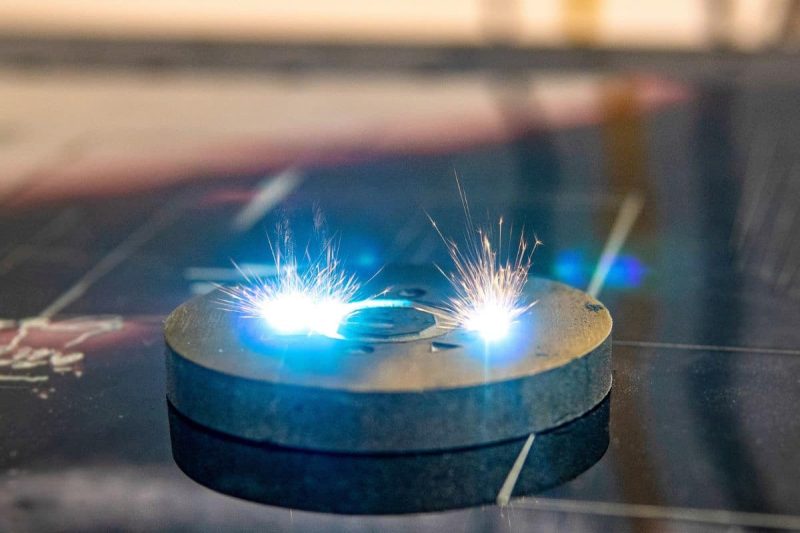
Laser Marking Basics
Laser Marking Processes and Applications
Laser marking is a versatile technology that can be used to create permanent marks on a variety of materials. The process involves directing a concentrated beam of light onto the surface of a material, causing a physical or chemical change that produces the desired mark. There are several types of laser marking, including:
- Annealing: Used primarily on metals, this process heats the material to create a mark without removing any material.
- Etching/Engraving: This involves removing material to create a mark with depth, and it works well on metals and plastics.
- Ablation: This process removes layers of material to reveal a contrasting underlying layer, and is often used for anodized aluminum.
- Foaming: Used primarily on plastics, this process creates bubbles within the material that reflect light and create a raised mark.
- Carbonization: This process darkens the material by increasing the carbon concentration, and is often used on organic materials such as wood or leather.
Key Parameters Affecting Marking Capability
Wavelength
The wavelength of a laser determines how it interacts with different materials.
- Fiber lasers (~1064 nm) are ideal for metals and some plastics.
- CO2 lasers (~10.6 µm) are effective for non-metals such as wood, glass, and plastics.
- UV lasers (~355 nm) excel at marking delicate and heat-sensitive materials with high precision.
Pulse Duration
The duration of each laser pulse affects the marking process.
- Continuous wave (CW) lasers provide a stable beam suitable for deep engraving and cutting.
- Pulsed lasers deliver energy in short pulses, minimizing thermal effects and increasing precision. It is ideal for fine details and sensitive materials.
Power
The power of a laser affects the depth and speed of the mark.
- Higher-power lasers allow for deeper marks and faster processing times.
- Lower-power lasers are suitable for delicate applications that require minimal material destruction.
Focus Size
The size of the laser beam focus affects the precision of the mark.
- Smaller spot sizes allow for fine and detailed marks.
- Larger spot sizes are used for wider, less detailed marks.
Beam Quality
The quality of a laser beam is often quantified by the M² factor, which affects the accuracy and consistency of the mark.
- Lower M² values indicate a higher beam quality, resulting in finer, more consistent marks.
Scanning Speed
The speed at which the laser beam travels through the material affects marking time and quality.
- Higher scanning speeds increase marking efficiency but may reduce mark depth and quality.
- Lower scanning speeds allow for deeper, clearer marks.
Importance of Selecting the Correct Laser Type
Choosing the right laser type for a specific marking application helps achieve the best results. The right laser ensures high-quality marking, efficiency, and cost-effectiveness. Here are some reasons why choosing the right laser type is important:
- Material Compatibility: Different lasers interact differently with various materials. Fiber lasers work best with metals, CO2 lasers excel with non-metals, and UV lasers work best with sensitive materials. Using the wrong laser type can result in poor marking quality, material damage, or inefficiency.
- Marking Accuracy: Applications that require fine detail and high precision, such as electronics and medical devices, benefit from the small spot size and high beam quality of UV and fiber lasers. Conversely, CO2 lasers are better suited for wider, less detailed marks on materials such as wood and glass.
- Efficiency and Speed: Production speed and efficiency are critical in industrial applications. Fiber lasers are known for their high-speed marking capabilities and are ideal for high-throughput environments, while CO2 lasers offer a balance of speed and versatility for non-metallic materials.
- Heat Impact: Sensitive applications, such as marking electronics or medical devices, require lasers with minimal heat impact to avoid damaging materials. UV lasers and their cold marking process are ideal for these applications.
- Cost Considerations: Different types of lasers have different initial investments and operating costs. While fiber laser marking machines have a higher initial cost, their long life and low maintenance costs can save you money in the long run. CO2 laser marking machines have a lower initial cost but may require more frequent maintenance.
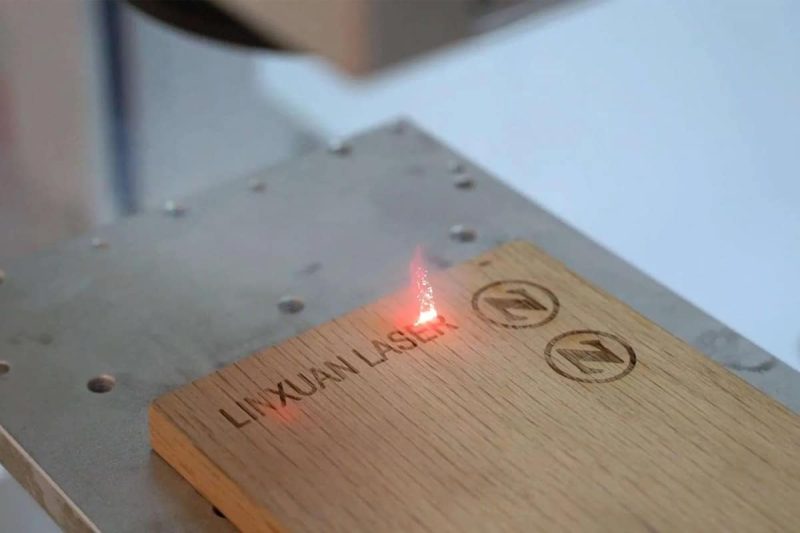
Types of Lasers Used in Laser Marking
Fiber Laser
Features
- Wavelength: Approximately 1064 nm (near infrared).
- Gain Medium: Fiber doped with rare earth elements such as ytterbium, erbium, or neodymium.
- Laser Type: Pulsed or continuous wave.
- Power Range: Typically from a few watts to hundreds of watts.
- Operation: High beam quality, continuous wave, and pulsed modes.
Performance
- Material Compatibility: Ideal for metals (stainless steel, aluminum, gold, silver), certain plastics, and ceramics.
- Depth and Precision: High accuracy and fine detail, capable of deep engraving on metals.
- Speed: High-speed marking capabilities for high-throughput environments.
- Beam Quality: Excellent beam quality for fine, detailed marking.
Applications
- Electronics: Marking circuit boards, microchips, and other electronic components.
- Jewelry and Watches: Engrave intricate patterns on precious metals.
- Automotive: Mark parts and components with serial numbers and barcodes.
- Medical Devices: Create precise and permanent marks on surgical instruments and medical implants.
Advantages
- High Precision and Quality: Produce fine marks with high accuracy.
- Speedand Efficiency: Mark quickly, ideal for high-volume production.
- Durability and Lifespan: Long lifespan, typically over 100,000 hours, with minimal maintenance.
- Energy Efficiency: More energy efficient than other types of lasers, reducing operating costs.
- Versatility: Able to mark a wide range of materials, especially metals.
Limitations
- Material Limitations: Less effective on non-metallic materials such as wood, glass, and some plastics.
- Initial Cost: Higher initial investment, but lower long-term operating costs.
- Complexity: More complex technology, requires expertise to operate and maintain.
- Cooling Requirements: Adequate cooling systems may be required to manage the heat generated during operation.
CO2 Laser
Features
- Wavelength: Approximately 10.6 µm (far infrared).
- Gain Medium: Gas mixture (CO2, nitrogen, helium).
- Laser Type: Continuous wave or pulsed.
- Power Range: Typically ranges from 10 watts to several hundred watts.
- Operation: High efficiency, continuous wave, and pulsed modes.
Performance
- Material Compatibility: Excellent for non-metals such as wood, glass, plastic, fabric, leather, and ceramics. Limited effectiveness on metals unless treated with specialized coatings.
- Marking Speed: Moderate, depending on the material and desired depth.
- Depth and Accuracy: Capable of deep engraving and high contrast marking on non-metals.
- Beam Quality: Provides good beam quality for precise marking.
Applications
- Signage and Advertising: Create intricate signs with acrylic, wood, and other materials.
- Packaging: Mark and cut packaging materials such as cardboard and plastics.
- Textiles and Fabrics: Engrave and cut patterns on fabric and leather.
- Glass and Ceramics: Engrave designs and messages on glass bottles, windows, and ceramic items.
Advantages
- Broad Material Compatibility: Works on a wide range of non-metal materials.
- Cost-Effectiveness: More affordable than fiber and UV lasers and can be used in a variety of applications.
- Flexibility: Capable of performing multiple tasks including cutting, engraving, and marking.
- Marking Depth: Suitable for deep engraving and applications requiring large amounts of material removal.
Limitations
- Lower Accuracy on Metals: Less effective on metals, requiring specialized coatings or additives.
- Maintenance Requirements: More frequent maintenance and parts replacement than fiber lasers.
- Material Compatibility: Excellent for non-metals such as wood, glass, plastic, fabric, leather, and ceramics. Limited effectiveness on metals unless treated with specialized coatings.
- Marking Speed: Moderate, depending on the material and desired depth.
- Depth and Accuracy: Capable of deep engraving and high contrast marking on non-metals.
- Beam Quality: Provides good beam quality for precise marking.
UV Laser
Features
- Wavelength: Approximately 355 nm (ultraviolet).
- Gain Medium: Solid-state or gas systems utilizing frequency tripling.
- Laser Type: Pulsed.
- Power Range: Typically ranges from a few milliwatts to several watts.
- Operation: High precision with short pulse durations.
Performance
- Material Compatibility: Suitable for a wide range of materials, including plastics, glass, ceramics, and metals.
- Depth and Precision: Ultra-fine marking with minimal thermal effects and high-contrast marking.
- Speed: Slower marking speeds but higher precision compared to fiber lasers.
- Beam Quality: Excellent beam quality for fine and detailed marking.
Applications
- Medical and Pharmaceutical: Marking of medical devices, instruments, and packaging with high precision and contrast.
- Electronics: Engraving of precision electronic components and microchips.
- Aerospace: Marking of sensitive materials used in aerospace parts.
- Consumer Products: Create high-quality marks on glassware, cosmetics, and other consumer products.
Advantages
- Precision: Ultra-fine marking with minimal thermal effects.
- Material Compatibility: Marking of a wide range of materials, including sensitive materials.
- Contrast and Quality: Provides high contrast and high-quality marking.
- Cold Marking Process: Reduces heat-affected zone, minimizing material damage.
- Non-Destructive: Ideal for applications that require minimal heat impact and no material deformation.
Limitations
- Lower Power: Typically have lower power output, limiting suitability for deep engraving or high-speed marking.
- Higher Cost: Initial investment and maintenance costs are higher.
- Limited Availability: Fewer manufacturers produce UV laser marking machines, resulting in limited availability and potentially longer lead times for parts and repairs.
- ShorterLifespan: UV lasers may have a shorter lifespan than fiber lasers.
- Speed: Marking speeds are slower compared to other types of lasers.
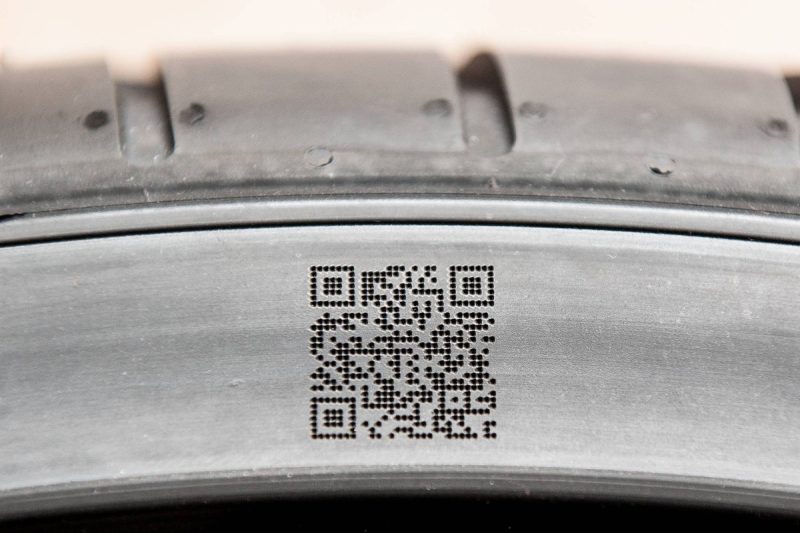
Comparison of Laser Types in Laser Marking
Marking Speed and Efficiency
Fiber Laser
- Speed: Fiber lasers are known for their high-speed marking capabilities. It can achieve fast marking rates, making it suitable for high-throughput production environments.
- Efficiency: Fiber lasers have excellent energy efficiency, converting a high percentage of input energy into usable laser light. This can reduce operating costs and reduce energy consumption.
CO2 Laser
- Speed: CO2 lasers offer moderate marking speeds. While not as fast as fiber lasers, they are adequate for many industrial applications, especially those involving non-metallic materials.
- Efficiency: CO2 lasers are generally less efficient than fiber lasers due to the nature of the gas medium, but they still offer reasonable efficiency for many applications.
UV Laser
- Speed: UV lasers are slower to mark than fiber lasers. Their speed is limited by the need for high precision and minimal thermal effects.
- Efficiency: UV lasers are less efficient in terms of energy use due to their lower output power, but they excel in precision applications where speed is less important.
Precision and Quality of Marking
Fiber Laser
- Precision: Fiber lasers offer high precision and fine detail, making them suitable for intricate marking on metals and some plastics.
- Quality: Marking quality is excellent, with sharp lines, minimal thermal distortion, and consistent results on a wide range of materials.
CO2 Laser
- Precision: CO2 lasers offer good precision for non-metallic materials, but are less accurate on metals without special coatings.
- Quality: Marking quality on non-metals is high, creating deep, visible engravings.
UV Laser
- Precision: The UV laser has the highest precision of the three lasers due to its short wavelength and minimal thermal effects. It can create extremely finely detailed marks.
- Quality: The quality of UV laser marking is excellent, with high contrast and clarity. The cold marking process ensures minimal damage to the material.
Versatility and Compatibility with Different Materials
Fiber Laser
- Versatility: Fiber lasers are very versatile and can mark a wide range of materials, including metals, plastics, and ceramics.
- Compatibility: It excels at marking metals such as stainless steel, aluminum, gold, and silver, as well as certain plastics used in industrial applications.
CO2 Laser
- Versatility: CO2 lasers are also very versatile, but are more focused on non-metallic materials. It can mark, engrave, and cut a wide range of substances.
- Compatibility: It is particularly effective on wood, glass, acrylic, plastic, fabric, leather, and ceramics, but is less effective on metals unless special treatments are used.
UV Laser
- Versatility: UV lasers are very versatile and are particularly useful in applications that require high-precision processing of delicate materials.
- Compatibility: It can mark a wide range of materials, including plastics, glass, ceramics, and metals. UV lasers are ideal for sensitive materials that require minimal heat effects.
Cost-Effectiveness and Maintenance Considerations
Fiber Laser
- Cost-Effectiveness: While the initial investment in a fiber laser marking system can be high, its long life and low maintenance requirements make it cost-effective in the long run.
- Maintenance: Fiber lasers have minimal maintenance requirements and typically run for more than 100,000 hours with minimal downtime. This reduces maintenance costs and production interruptions.
CO2 Laser
- Cost-Effectiveness: CO2 laser marking machines are generally more affordable initially, but may incur higher long-term costs due to frequent maintenance and parts replacement.
- Maintenance: Regular maintenance is required, including gas refills and mirror replacements, which can increase operating costs over time.
UV Laser
- Cost-Effectiveness: UV laser marking machines have the highest initial and operating costs due to their specialized technology and lower power output.
- Maintenance: More frequent maintenance is required and the lifespan is shorter than with fiber laser marking machine However, its ability to make ultra-precision marks justifies the higher cost in applications where precision is critical.
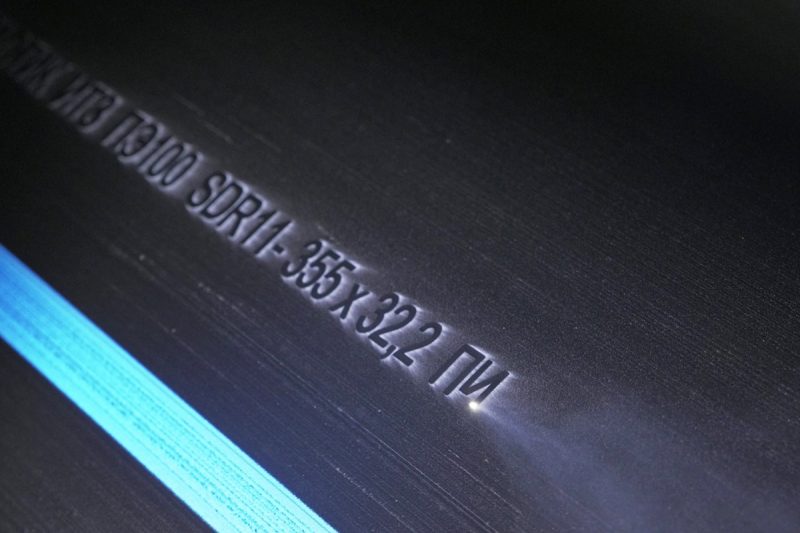
Factors Affecting Laser Type Selection
Material Type and Properties
The type of material being marked is one of the most critical factors in choosing the right laser type. Different lasers interact with the material in various ways, affecting the quality and efficiency of the marking process.
- Fiber Laser: For metals (steel, aluminum, copper, brass) and some plastics. Fiber lasers provide excellent marking quality on hard materials due to their high energy density and short wavelength.
- CO2 Laser: For non-metallic materials such as wood, glass, ceramics, plastics, leather, and textiles. CO2 lasers have a longer wavelength that these materials absorb well, making them ideal for cutting and engraving organic materials.
- UV Laser: For materials that require fine, detailed marking with minimal heat-affected zones. It is ideal for marking glass, ceramics, plastics, and some metals, especially in applications that require high precision and minimal heat effects.
Marking Requirements
Specific marking requirements, including depth, contrast, resolution, and durability, also affect the choice of laser type.
- Fiber Laser: Provides high contrast, abrasion- and corrosion-resistant permanent marking. For barcodes, serial numbers, and logos that require high clarity.
- CO2 Laser: Offers flexibility in marking a wide range of materials, especially where depth and texture are critical. Often used in engraving and cutting applications that require intricate designs.
- UV Laser: Produces high-precision marks with minimal heat impact, ideal for delicate materials and applications that require fine detail, such as electronics and medical devices.
Throughput and Speed Requirements
Throughput and speed requirements can determine the efficiency and suitability of a particular laser type for a particular application.
- Fiber Laser: Known for its high marking speeds and efficiency, it is suitable for high-volume production environments. Its ability to maintain high quality at fast speeds benefits industries such as automotive and aerospace.
- CO2 Laser: While versatile, it may not be able to match the speed of a fiber laser in certain high-volume applications. However, it excels in applications that require cutting and engraving non-metallic materials.
- UV Laser: Typically slower than fiber and CO2 lasers, but offers unmatched precision. It is best suited for applications where quality and detail are more important than speed, such as the electronics and medical industries.
Production Environment and Limitations
The operating environment and any potential limitations must be considered to ensure the selected laser type can function optimally.
- Fiber Laser: It is generally rugged, requires less maintenance, and is suitable for harsh industrial environments. They are compact in design and can be integrated into a variety of production lines.
- CO2 Laser: It requires a clean environment to prevent contaminants from affecting the laser optics. They may require more space due to the larger size of the laser tube and associated equipment.
- UV Laser: It is sensitive to environmental conditions and generally requires a cleanroom environment for optimal performance. Its precision makes it ideal for applications in controlled environments, such as semiconductor manufacturing.
Budgetary Limitations and Cost Considerations
Cost is always an important factor in choosing the right laser type. This includes initial investment, operating costs, and maintenance.
- Fiber Laser: generally have a higher initial cost, but have lower operating costs due to their energy efficiency and long service life. They offer a good return on investment for high-volume applications.
- CO2 Laser: It is generally more affordable initially, especially for lower-power systems. However, operating and maintenance costs may be higher due to the need for make-up gases and more frequent maintenance.
- UV Laser: It is generally the most expensive due to its complexity and precision. They are cost-effective for specialized applications where precision and minimal material impact are critical.
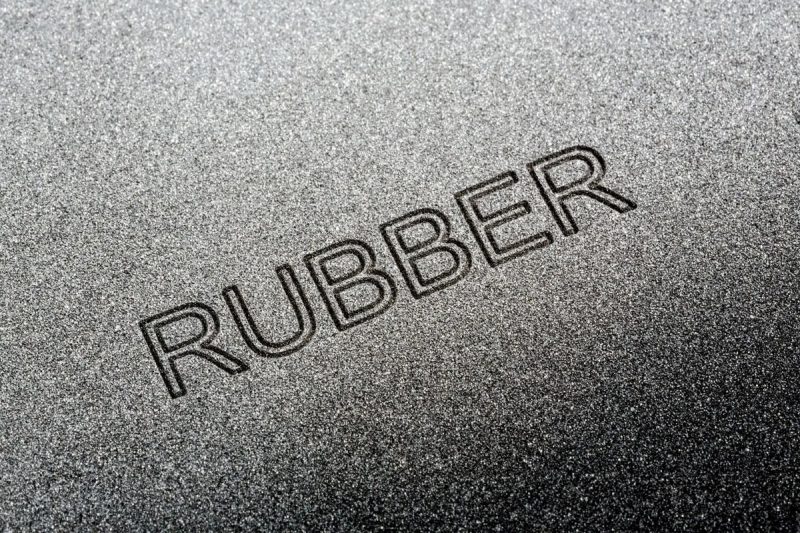
Best Practices for Selecting the Right Laser Type
Evaluate Material Compatibility and Marking Requirements
The first step in selecting the right laser type is to evaluate the materials you will be using and your specific marking requirements.
- Material Compatibility: Determine the types of materials you need to mark. Fiber lasers are well suited for metals and certain plastics, CO2 lasers are suitable for non-metals such as wood and glass, and UV lasers are ideal for delicate, sensitive materials. Test sample materials to observe how each laser type interacts with them.
- Marking Requirements: Define marking specifications such as depth, contrast, resolution, and durability. For example, if you need high-contrast, detailed markings on delicate surfaces, a UV laser is appropriate. For deep, permanent markings on metals, a fiber laser is the best choice. If you have high-volume production requirements, please consider marking speed.
Consult Laser Manufacturers and Experts
Taking advantage of the knowledge and experience of laser manufacturers and industry experts can provide valuable insights.
- Manufacturer Consultation: Contact laser manufacturers to discuss your specific needs. They can provide detailed information on the capabilities of different types of lasers and recommend the most appropriate options based on your material and marking requirements.
- Expert Advice: Consult industry experts who have experience in a variety of laser marking applications. They can provide practical insights and recommendations based on actual applications and performance.
Consider Long-Term Operating Costs and Maintenance Requirements
It is important to consider the long-term operating costs and maintenance requirements of your laser system to ensure cost-effectiveness.
- Initial Cost and Operating Costs: While fiber lasers may have a higher initial cost, they generally have lower long-term operating costs due to their durability and minimal maintenance needs. CO2 lasers may require more frequent maintenance and replacement of consumables, which can affect overall costs.
- Maintenance Requirements: Evaluate the maintenance schedule and requirements for each laser type. Make sure you have the necessary resources and capabilities to perform regular maintenance to avoid downtime and ensure consistent performance.
- Energy Efficiency: Consider the energy consumption of each laser type, as this can significantly affect operating costs over time.
Regularly Evaluate and Optimize Your Marking Process
Continuously evaluating and optimizing your marking process can lead to increased efficiency and better results.
- Process Assessment: Regularly evaluate the performance of your laser marking system. Monitor parameters such as marking speed, quality, and consistency to identify any areas for improvement.
- Optimization Strategy: Implement an optimization strategy based on your assessment. This may include adjusting laser settings, upgrading components, or even switching to a different type of laser if marking needs improvement.
- Training and Development: Make sure your team is well-trained in operating and maintaining your laser system. Regular training sessions can help everyone stay up to date on best practices and new techniques to use the equipment more effectively.
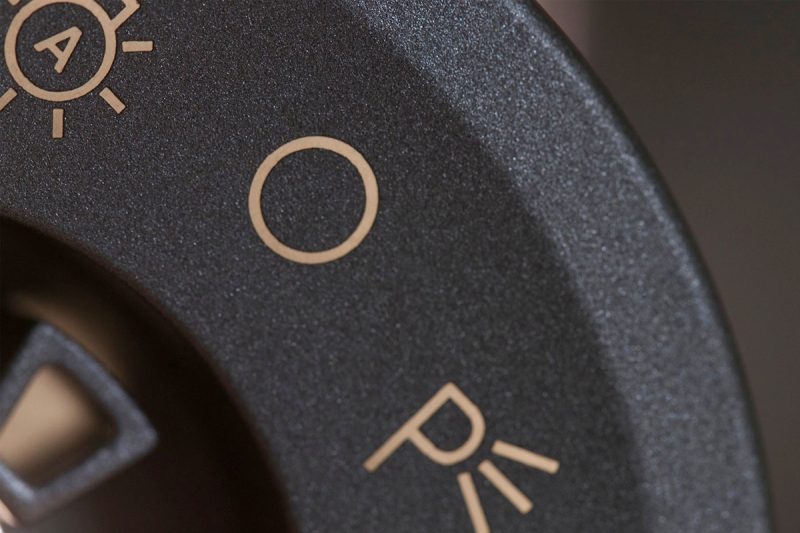
Summary
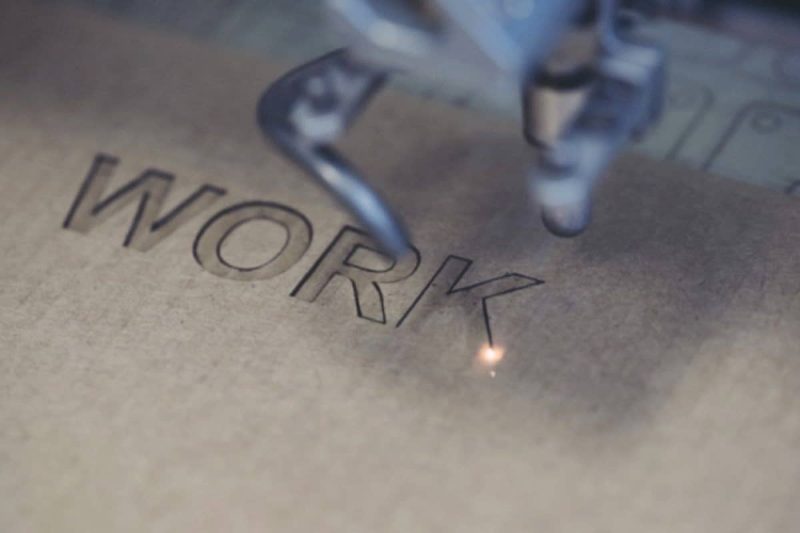
Get Laser Marking Solutions
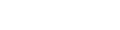
- [email protected]
- [email protected]
- +86-19963414011
- No. 3 Zone A, Lunzhen Industrial Zone,Yucheng City , Shandong Province.