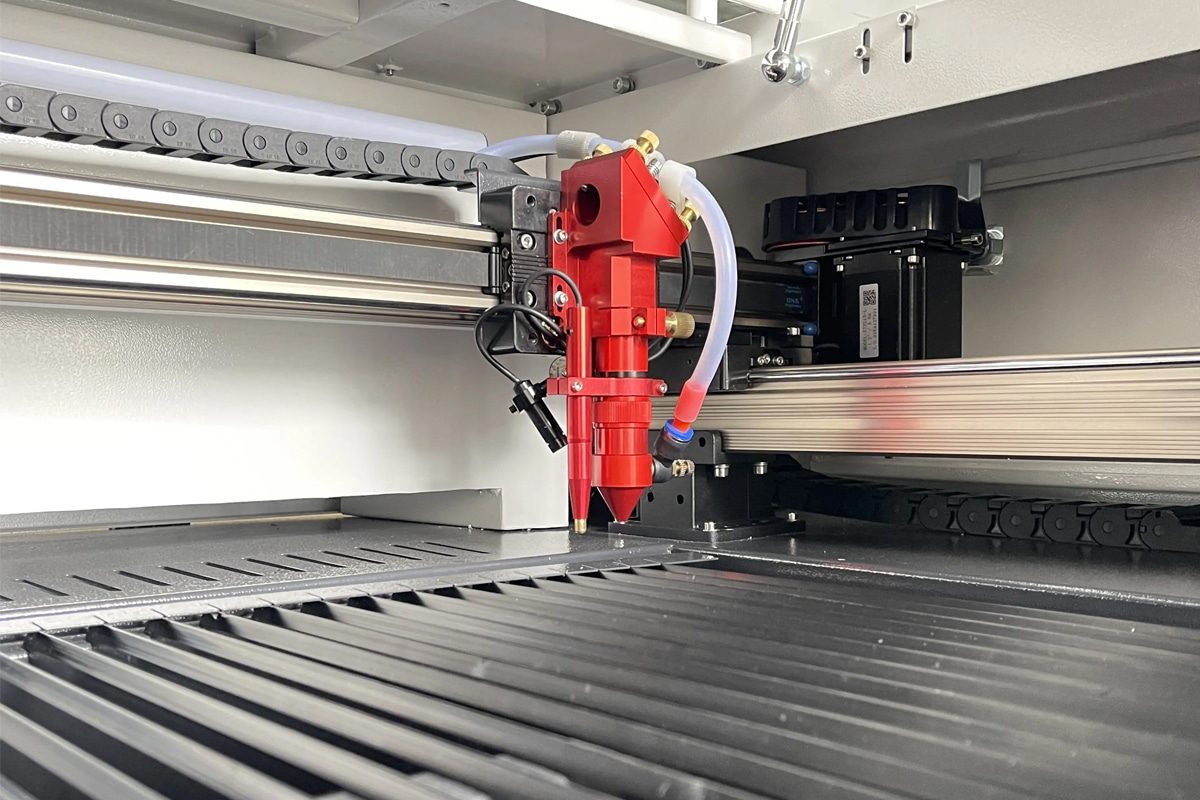
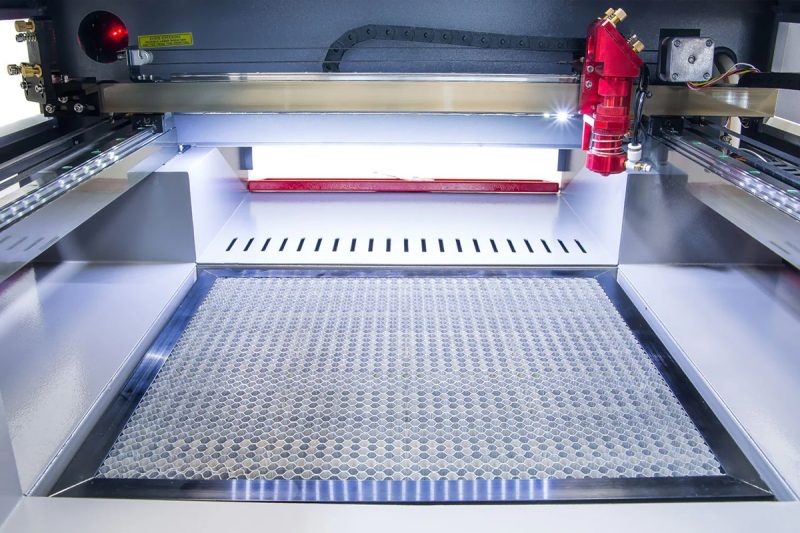
Basics of Laser Technology
What is a Laser?
Properties of Lasers
Lasers possess several unique properties that differentiate them from other light sources and make them indispensable for industrial applications, including:
- Coherence: Laser light waves are coherent, meaning they have a constant phase relationship. Unlike ordinary light, where the emitted waves are out of sync, the light waves produced by lasers are in phase. This coherence enables the laser beam to maintain its focus over long distances, delivering high precision in cutting and marking processes.
- Monochromaticity: A laser emits light of a single wavelength or color, known as monochromatic light. This contrasts with traditional light sources that produce a wide spectrum of colors. The monochromatic property of lasers makes them highly effective for focusing energy on a specific wavelength, resulting in greater control over how the light interacts with various materials.
- Directionality: Lasers emit light in a highly directional beam, with minimal divergence compared to conventional light sources. This means that laser beams can travel long distances with very little spread, concentrating the beam’s energy and enabling precise cuts and intricate patterns.
- High Intensity: The ability to focus light energy to a small point gives lasers a high power density, making them capable of melting, vaporizing, or ablating materials. This high intensity allows for fast, efficient material processing with minimal heat-affected zones, preserving the structural integrity of the surrounding material.
- Polarization: Laser light can be polarized, meaning the direction of its electric field oscillations can be controlled. This property is beneficial for various applications, including laser welding, where the polarization of light can influence the absorption and behavior of materials.
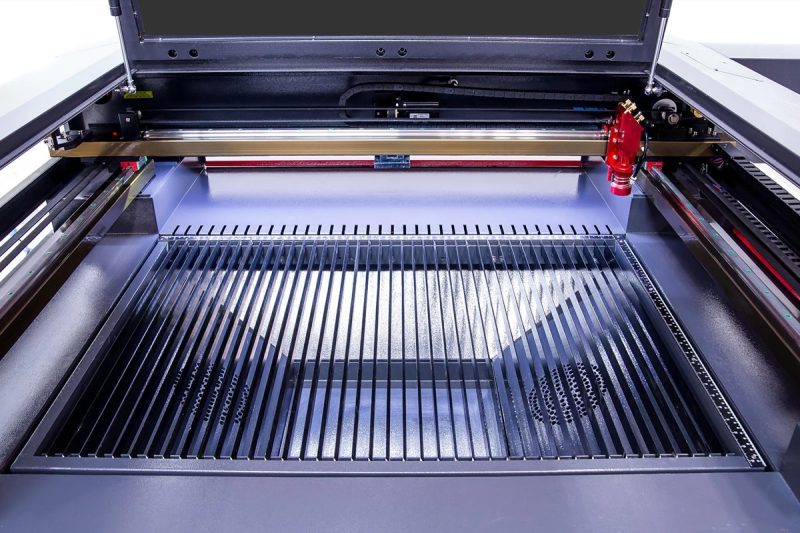
Fundamentals of CO2 Lasers
Characteristics of CO2 Laser Beams
CO2 lasers produce light in the far-infrared region, making them ideal for heating and cutting a wide variety of materials, including metals, plastics, textiles, wood, and more. The following characteristics make CO2 lasers particularly effective for industrial cutting:
- High Power Output: CO2 lasers can achieve continuous wave (CW) output with powers ranging from a few watts to several kilowatts, making them suitable for high-speed precision cutting.
- Monochromatic Light: The laser emits light at a specific wavelength (typically 10.6 µm), which ensures efficient energy absorption by a broad range of materials.
- Good Beam Quality: The beam can be focused to a small spot size, achieving a high power density necessary for precise and intricate cuts.
- High Efficiency: CO2 lasers offer relatively high electrical-to-optical conversion efficiency compared to other laser types.
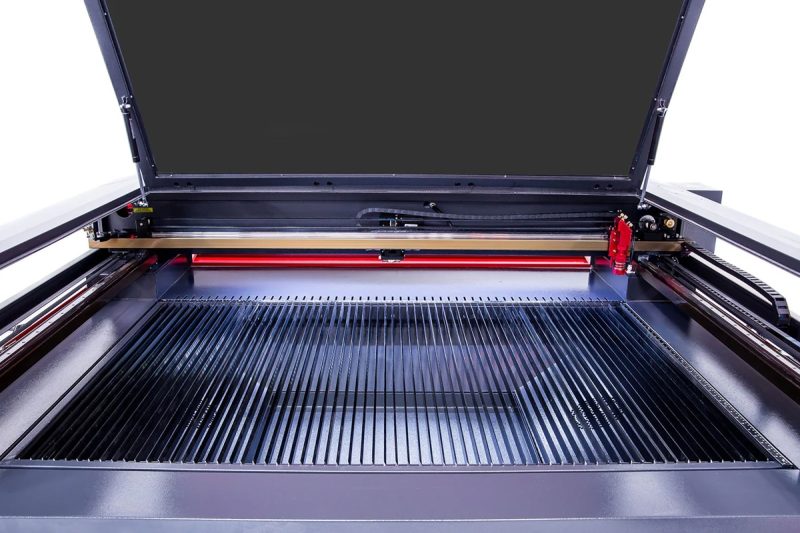
Components of CO2 Laser Cutting Machines
Laser Resonator
Cutting Head and Focusing Lens
Assist Gas System
An assist gas is supplied through the nozzle of the cutting head and flows coaxially with the laser beam. The assist gas plays a vital role in enhancing the cutting process by:
- Removing Molten Material: It blows molten material out of the kerf (cutting gap) to produce clean cuts.
- Cooling the Material: It cools the area around the cut, reducing thermal distortion.
- Reacting with the Material: For certain materials like mild steel, reactive gases such as oxygen create an exothermic reaction, increasing cutting speed. Alternatively, inert gases like nitrogen prevent oxidation and produce clean, oxide-free edges.
CNC Control System
Cooling System
Exhaust and Filtration System
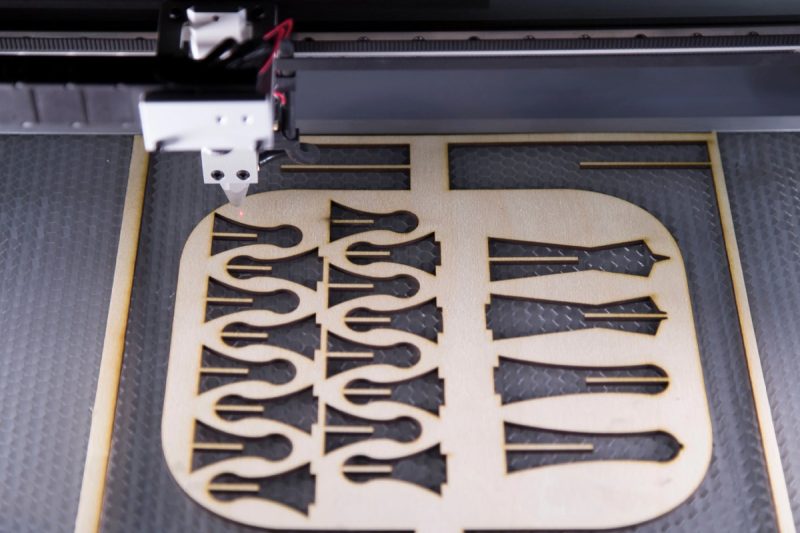
Generation of the Laser Beam
Stimulated Emission Process
Role of Gas Molecules
In a CO2 laser, the lasing medium is a gas mixture primarily composed of carbon dioxide (CO2), nitrogen (N2), and helium (He). Each gas plays a specific role in the laser generation process:
- Carbon Dioxide (CO2): The active lasing medium, responsible for emitting photons when excited. CO2 molecules can transition between vibrational energy states, releasing photons at a wavelength of 10.6 micrometers, which is suitable for industrial cutting applications.
- Nitrogen (N2): Acts as an energy transfer medium. When excited by an electrical discharge, nitrogen molecules reach a metastable state, meaning they hold their energy for an extended period. These excited nitrogen molecules collide with CO2 molecules, efficiently transferring their energy to elevate the CO2 molecules to an excited state.
- Helium (He): Facilitates the de-excitation of CO2 molecules and helps dissipate heat from the system, ensuring stable operation.
Achieving Population Inversion
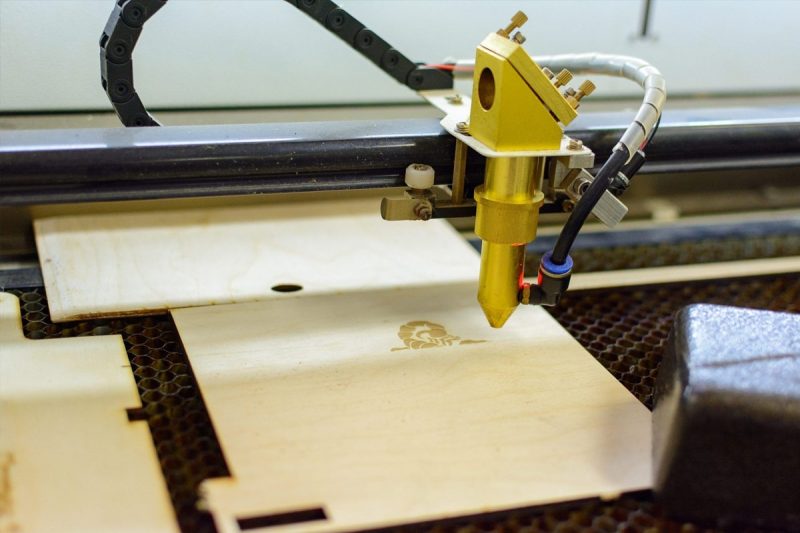
Beam Delivery and Focusing
Beam Path and Mirrors
Focusing Mechanism
Importance of Beam Quality
Beam quality is a critical factor that influences the performance of a CO2 laser-cutting machine. High beam quality ensures that the laser beam can be focused on a smaller spot size, increasing the power density and enhancing cutting precision. The key attributes of beam quality include:
- Coherence: The degree to which the light waves are in phase with one another. High coherence leads to a well-defined, concentrated beam.
- Beam Mode: Refers to the distribution of the beam’s energy across its cross-section. A TEM00 (transverse electromagnetic mode) beam has a Gaussian distribution and is considered ideal for precision cutting due to its symmetrical energy profile.
- Stability and Consistency: Consistent beam output is essential for achieving uniform cuts and minimizing material waste.
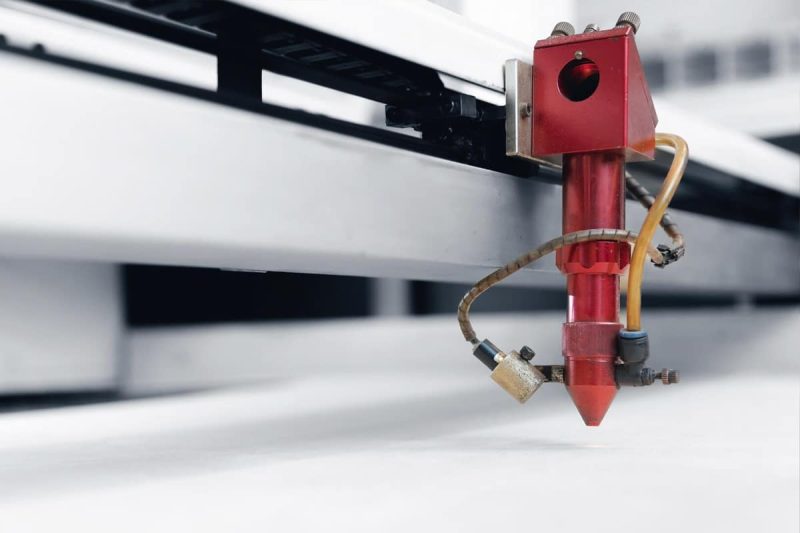
Interaction with Materials
Absorption of Laser Energy
Thermal Processes in Cutting
The absorbed laser energy is converted into heat, leading to a series of thermal processes that enable material cutting:
- Melting: The concentrated laser beam rapidly raises the temperature of the material, causing it to reach its melting point. In many cases, the laser beam heats a localized area, creating a molten pool.
- Vaporization: For some materials, the laser energy can be intense enough to vaporize the material directly, forming a narrow kerf or cut. This process is particularly useful for thin materials or applications requiring minimal material removal.
- Material Removal: Once the material has been melted or vaporized, it must be removed from the cutting area to complete the cut. This removal is facilitated by the assist gas, which blows away the molten or vaporized material from the cutting zone.
- Cooling and Solidification: After the cutting process, the surrounding material cools rapidly, solidifying the edges. The cooling rate and heat-affected zone (HAZ) can influence the quality of the cut, including edge smoothness and structural integrity.
Role of Assist Gases
The assist gas is an integral part of the CO2 laser-cutting process. It flows coaxially with the laser beam through a nozzle at the cutting head and plays several important roles:
- Material Removal: The assist gas helps expel molten and vaporized material from the kerf, ensuring a clean and continuous cut. This is especially important for thick or dense materials, where rapid removal of molten material prevents re-solidification and improves cut quality.
- Chemical Reactions: In some applications, reactive gases such as oxygen (O2) are used as the assist gas. Oxygen reacts with the material, creating an exothermic reaction that adds heat to the cutting process, enhancing cutting speed and efficiency. This is commonly used for cutting mild steel.
- Protection Against Oxidation: In contrast, inert gases such as nitrogen (N2) or argon (Ar) are used when oxidation must be minimized, such as when cutting stainless steel or aluminum. These gases create a protective atmosphere that prevents oxidation, resulting in clean, oxide-free edges.
- Cooling: The assist gas can also cool the material and surrounding area, reducing the size of the heat-affected zone (HAZ) and preventing thermal distortion.
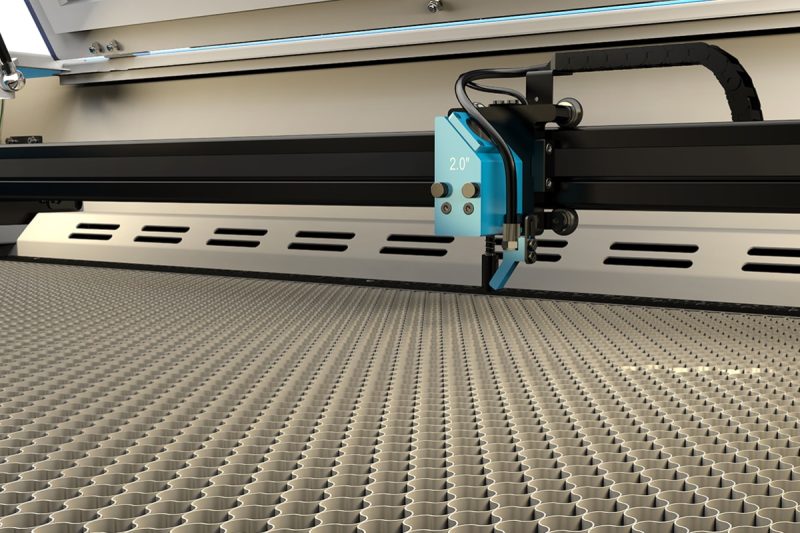
Cutting Process Control
CNC Programming
Key aspects of CNC programming in CO2 laser cutting include:
- Defining the Cutting Path: The CNC program specifies the precise path that the laser beam must follow to cut the material. This path is critical for achieving the desired shape and dimensions.
- Setting Cutting Parameters: The program controls various parameters, such as laser power, feed rate, focus position, and assist gas flow. These parameters can be adjusted based on the material type, thickness, and desired edge quality.
- Piercing Strategies: For thicker materials, the CNC system may employ specific piercing strategies to create an initial hole before continuing with the cut. This ensures efficient and clean cutting from the start.
Motion Control Systems
Key functions of the motion control system include:
- Synchronization: Coordinating the motion of the cutting head with the laser beam’s on/off state to ensure that cutting occurs only when necessary.
- Acceleration and Deceleration Control: Optimizing the speed of the cutting head to achieve smooth transitions during direction changes, preventing jerks, and maintaining consistent cut quality.
- Real-Time Adjustments: Adapting the speed and position of the cutting head based on cutting conditions, such as changes in material thickness or complex geometries.
Monitoring and Feedback
Examples of monitoring and feedback mechanisms include:
- Height Sensing: A height sensor continuously monitors the distance between the cutting head and the material surface. It adjusts the position of the cutting head to maintain the optimal focus distance, ensuring consistent cutting depth and edge quality.
- Laser Power and Beam Stability Monitoring: Sensors track the laser’s output power and beam stability, allowing for adjustments to maintain consistent energy delivery.
- Assist Gas Pressure and Flow Monitoring: Monitoring the pressure and flow rate of the assist gas ensures that the gas is delivered consistently, contributing to clean cuts and proper material removal.
- Thermal and Vibration Sensors: Detect excessive heat or vibrations that may impact cutting precision. The system can slow down or pause the cutting process to prevent defects or damage.
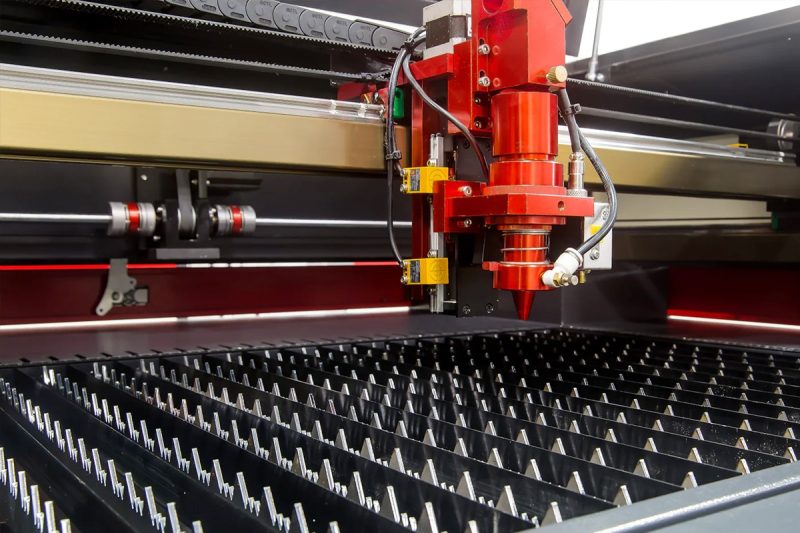
Suitable Materials for CO2 Laser Cutting
Non-Metallic Materials
CO2 lasers are especially effective for cutting non-metallic materials, which absorb the laser’s infrared wavelength more efficiently. This makes CO2 laser-cutting machines highly suitable for industries such as textiles, woodwork, and signage.
- Wood: CO2 lasers are widely used for cutting, engraving, and marking wood. They produce clean cuts and intricate designs, making them ideal for applications like furniture, decorative items, and model-making.
- Acrylic: Often used in signage and display manufacturing, acrylic cuts smoothly with CO2 lasers, creating polished, flame-finished edges without additional finishing steps.
- Plastics: Many types of plastics, such as polycarbonate, polyester, and polypropylene, can be cut with CO2 lasers. Laser cutting is used in the packaging, electronics, and automotive industries for custom plastic components.
- Leather and Fabrics: CO2 lasers offer precise cutting and minimal fraying on leather and synthetic or natural fabrics. They’re commonly used in the fashion, upholstery, and footwear industries.
- Rubber: Certain rubbers can be processed for gasket manufacturing and other industrial uses. The laser creates clean cuts with minimal residue.
Organic Materials
CO2 laser cutting machines can also cut a variety of organic materials, thanks to their ability to vaporize the material with minimal heat distortion. These materials include:
- Foam: Thin foam sheets can be cut to make packaging inserts, custom padding, and other precision foam products.
- Paper and Cardboard: CO2 lasers are highly effective for the precision cutting of paper products, making them suitable for packaging, invitations, and art applications.
Metals (with Limitations)
Though not the primary choice for metals, CO2 lasers can handle thin metal sheets and some coated metals when configured properly. These include:
- Mild Steel: Thin sheets of mild steel (up to about 2-3 mm) can be cut with a CO2 laser, especially when using oxygen as the assist gas to create an exothermic reaction, increasing cutting efficiency.
- Stainless Steel and Aluminum: Thin sheets can be cut, though fiber lasers are generally preferred for these metals. For CO2 lasers, inert gases like nitrogen are used to prevent oxidation and produce clean edges.
Composite Materials
Certain composite materials, such as laminates and coated textiles, can be processed with CO2 lasers. However, it’s essential to avoid materials that emit harmful fumes when laser cut, such as PVC and some fibrous composites.
- Laminate Sheets: CO2 lasers are often used for cutting laminate materials in industries such as furniture, interior design, and electronics, where high precision is needed.
- Coated Fabrics: Laser cutting can create intricate patterns on coated fabrics, often used in upholstery, outdoor gear, and custom clothing.
Unsuitable Materials for CO2 Laser Cutting
While CO2 lasers are versatile, some materials are unsuitable for laser processing due to the potential release of toxic fumes or excessive melting. These include:
- Fiberglass and Carbon Fiber: These materials tend to burn and release harmful fumes, making them unsuitable for CO2 laser cutting.
- Reflective Metals: Thick, highly reflective metals like copper and brass are not suitable for CO2 lasers as they reflect much of the laser energy, causing inefficient cuts and potential equipment damage.
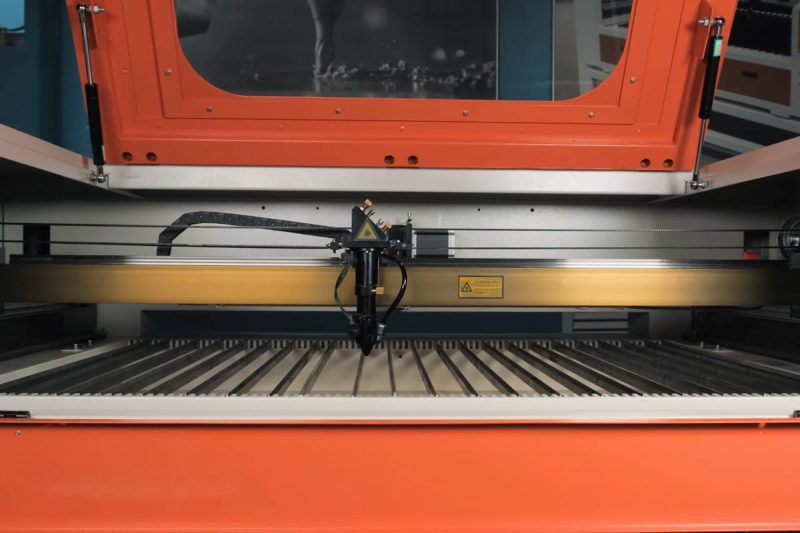
Advantages and Limitations of CO2 Laser Cutting
Benefits of CO2 Laser Cutting
- High Precision and Accuracy: CO2 laser cutting machines offer exceptional precision and accuracy, allowing for intricate and detailed cuts with tight tolerances. The laser beam can be precisely controlled, resulting in clean, sharp edges with minimal deviation from the intended cut path. This makes CO2 lasers ideal for industries that require complex geometries and fine details, such as signage, electronics, and automotive manufacturing.
- Smooth and Clean Cuts: CO2 lasers produce smooth and clean edges without the need for secondary finishing processes, such as deburring or grinding. The non-contact nature of laser cutting minimizes mechanical deformation and ensures high-quality finishes, even in materials that are prone to chipping or fraying.
- Versatility Across Materials: CO2 laser cutting machines are highly versatile and can process a broad range of materials, including wood, plastics, textiles, leather, glass, acrylic, and thin metals. This versatility makes them a valuable tool for industries spanning from manufacturing and fabrication to creative and artistic applications.
- High Cutting Speed: Compared to traditional cutting methods, CO2 lasers can achieve high cutting speeds, particularly for thin and non-metallic materials. This leads to greater productivity, shorter cycle times, and increased output in industrial settings.
- Non-Contact Process: Laser cutting is a non-contact process, meaning that there is no physical tool-to-material contact. This eliminates the risk of tool wear, reduces maintenance costs, and minimizes mechanical stress on the material. As a result, CO2 laser cutting is particularly advantageous for delicate or sensitive materials.
- Reduced Material Waste: CO2 laser cutting machines produce narrow kerf widths (the width of the cut), reducing material waste and maximizing the number of parts that can be cut from a single sheet of material. Advanced nesting software can further optimize material usage, contributing to cost savings.
- Automation and Integration Capabilities: CO2 laser cutting machines can be easily integrated into automated production lines, improving efficiency and reducing labor costs. Features such as automatic loading/unloading systems, CNC controls, and real-time monitoring enhance productivity and enable complex, large-scale manufacturing processes.
- Minimal Heat-Affected Zone (HAZ): The focused laser beam minimizes the heat-affected zone around the cut, reducing thermal distortion and preserving the material’s structural integrity. This is especially important for applications where precision and minimal deformation are critical.
Potential Drawbacks of CO2 Laser Cutting
- Limited Metal Cutting Capabilities: While CO2 lasers can cut thin metals, they are generally less effective than fiber lasers for cutting thick or highly reflective metals like aluminum, brass, and copper. These materials may reflect the laser energy, leading to inefficient cutting and potential damage to the equipment.
- High Energy Consumption: CO2 lasers require significant electrical power to operate, which can lead to higher energy costs compared to other cutting technologies. Proper maintenance of the cooling and electrical systems is necessary to keep energy consumption in check.
- Maintenance Requirements: CO2 laser cutting machines involve more complex maintenance compared to solid-state lasers. The laser resonator, optics (mirrors and lenses), and assist gas system require periodic cleaning, alignment, and replacement to maintain optimal performance. This can lead to downtime and additional operational costs.
- Emission of Fumes and Gases: During the cutting process, certain materials can emit fumes, smoke, and potentially hazardous gases. Effective exhaust and filtration systems are required to ensure operator safety and compliance with environmental regulations. Improper ventilation or lack of filtration can lead to harmful exposure.
- Lower Cutting Efficiency for Thick Materials: When cutting thick materials, CO2 lasers may require slower speeds and higher power settings, which can reduce overall cutting efficiency. This is a significant drawback compared to fiber lasers, which typically provide faster and more efficient cuts on thick metals.
- Initial Investment Cost: The purchase and installation of a CO2 laser cutting machine involve a significant upfront investment. While the long-term benefits often outweigh the initial costs, smaller businesses may face financial barriers to adoption.
- Reflective Material Challenges: CO2 lasers can struggle with highly reflective materials like polished metals. These materials may reflect the laser beam into the optical components, potentially causing damage and reducing cutting efficiency. Specialized coatings, higher power levels, or alternative laser sources (e.g., fiber lasers) may be required.
- Complexity in Setup and Programming: Operating a CO2 laser cutting machine requires expertise in CNC programming, material selection, and parameter optimization. Complex jobs may need detailed programming and fine-tuning, which can increase setup times, particularly for custom or small-batch runs.
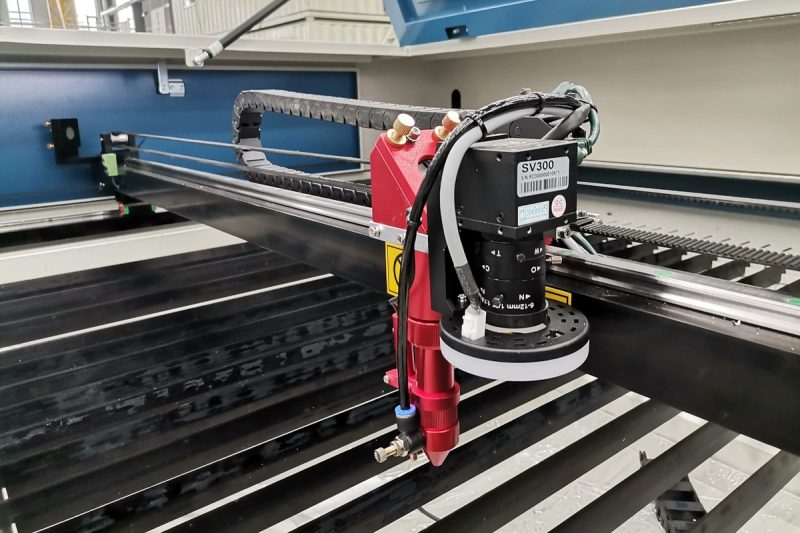
Safety Considerations
Laser Safety Measures
CO2 lasers produce high-powered beams capable of cutting through a variety of materials, making safety a top priority. The following measures help mitigate potential risks associated with laser operation:
- Laser Safety Goggles: Operators and personnel in the vicinity must wear appropriate laser safety goggles designed to protect against the specific wavelength of the CO2 laser (10.6 micrometers). This prevents eye damage caused by direct or reflected laser beams.
- Enclosed Work Areas: CO2 laser cutting machines often include fully enclosed or partially enclosed workspaces to contain the laser beam and prevent accidental exposure. Safety interlocks ensure that the machine will not operate if the enclosure is open.
- Laser Warning Signs: Proper signage must be displayed around the machine to indicate that a high-powered laser is in use. This alerts personnel to potential hazards and restricts unauthorized access to the laser area.
- Regular Beam Path Alignment Checks: Misalignment of the laser beam can lead to unintended reflections, which pose a significant hazard. Regular inspection and alignment of mirrors and optical components help mitigate this risk.
- Fire Safety Equipment: The high-energy laser beam generates heat, which may ignite flammable materials or dust. Fire extinguishers, fire blankets, and other fire safety equipment should be readily available. Operators should also maintain a clean workspace free of combustible materials.
- Ventilation and Fume Extraction: Cutting certain materials with CO2 lasers generates smoke, fumes, and potentially hazardous gases. A robust ventilation and fume extraction system is essential to remove these byproducts from the cutting area, ensuring operator safety and compliance with environmental regulations.
Handling of Gases and Electrical Components
Handling of Gases
- Assist Gas Safety: CO2 laser cutting machines use assist gases, such as oxygen, nitrogen, and compressed air, to aid in the cutting process. It is crucial to handle these gases with care, as improper use or leaks can pose safety risks, including fire, explosion, and asphyxiation.
- Proper Storage: Gas cylinders should be stored securely in a well-ventilated area, away from heat sources, sparks, and direct sunlight.
- Pressure Regulation: Gas pressure must be monitored and regulated to prevent over-pressurization, which can damage equipment or create safety hazards.
- Leak Detection: Regularly inspect gas lines, valves, and connections for leaks using approved detection methods, such as soapy water or specialized gas detectors.
- Exhaust and Ventilation Systems: Ensure that exhaust systems are properly maintained and functional to remove toxic gases, fumes, and particulates produced during cutting. This prevents the accumulation of hazardous substances and maintains air quality in the workspace.
Handling of Electrical Components
- High-Voltage Safety: CO2 laser cutting systems operate at high voltages, making electrical safety critical. Only trained and qualified personnel should perform electrical maintenance, repairs, or adjustments.
- Lockout/Tagout (LOTO): Implement lockout/tagout procedures to ensure that electrical systems are de-energized and cannot be accidentally re-energized during maintenance.
- Electrical Inspections: Periodically inspect electrical connections, cables, and components for signs of wear, damage, or corrosion. Address any issues immediately to prevent electrical hazards.
- Grounding and Insulation: All electrical components should be properly grounded and insulated to prevent electric shocks or short circuits. Grounding helps safely redirect stray electrical currents.
- Control Panel Safety: Operators must be trained in the proper use of control panels, emergency stop buttons, and interlock systems. In case of an emergency, these systems allow for immediate shutdown of the laser to prevent injury or equipment damage.
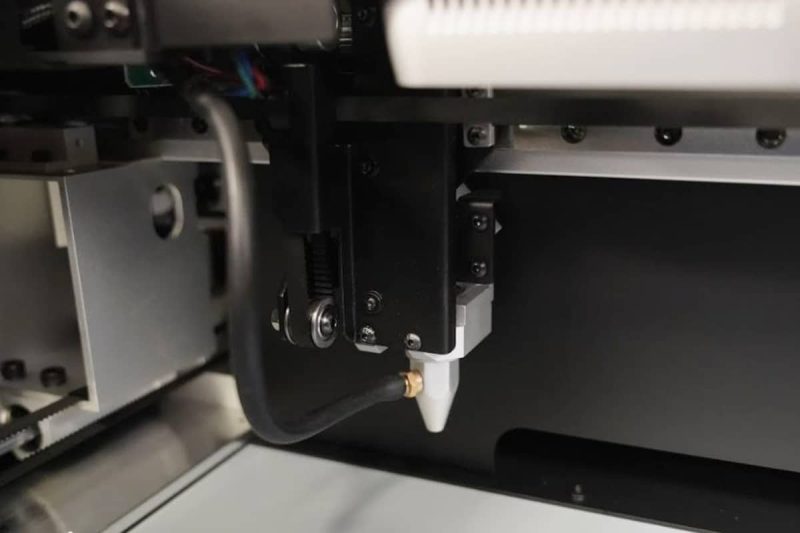
Summary
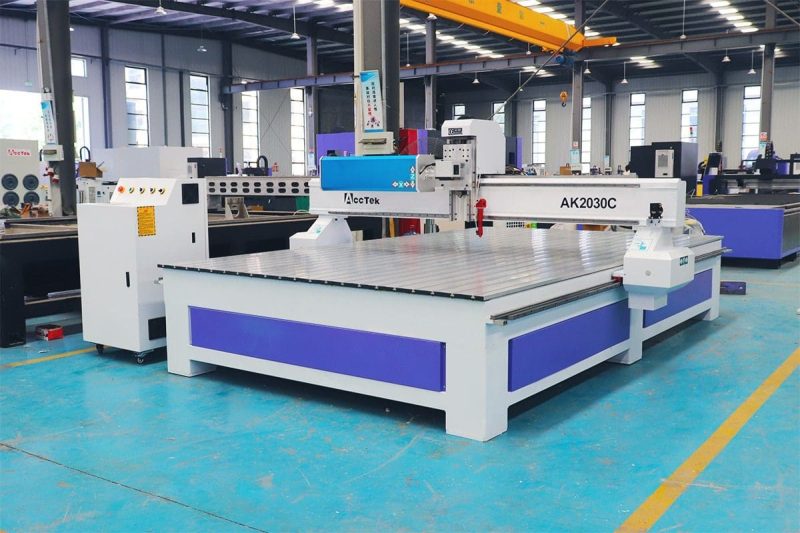
Get Laser Cutting Solutions
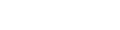
- [email protected]
- [email protected]
- +86-19963414011
- No. 3 Zone A, Lunzhen Industrial Zone,Yucheng City , Shandong Province.