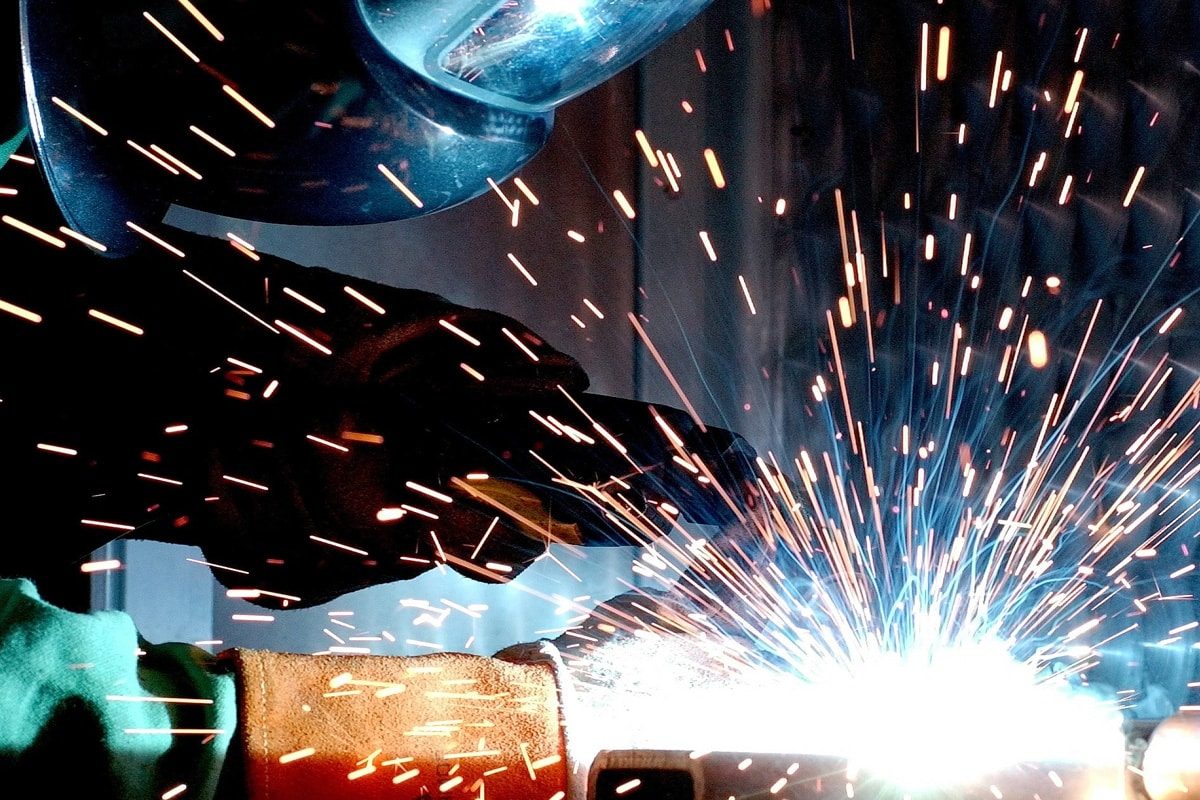
How Does the Focal Point of the Laser Beam Affect the Quality of the Weld?
Laser welding has become a highly accurate and effective process in modern manufacturing. Whether it is automotive manufacturing, aerospace, electronics manufacturing or the medical device industry, laser welding is widely used due to its high efficiency, low heat input and excellent weld quality. However, the quality of laser welds is greatly affected by the focus of the laser beam. The focus of the laser beam is a key factor that directly affects the efficiency and effectiveness of the laser welding process. In laser welding, the focus of the beam refers to the precise point where the laser energy is most concentrated, and the focus is critical to achieving the best weld quality. By carefully controlling the focus, manufacturers can tailor the welding process to meet specific requirements, such as ensuring sufficient penetration, minimizing defects and achieving consistent welds. Understanding the nuances of laser beam focusing can better control heat input, weld pool dynamics and overall process stability. This in turn can increase precision, reduce material waste and improve the structural integrity of welded components. As industries increasingly rely on the precision and efficiency of laser welding, mastering laser beam focusing technology is essential to producing high-quality welds in a variety of applications.
Table of Contents
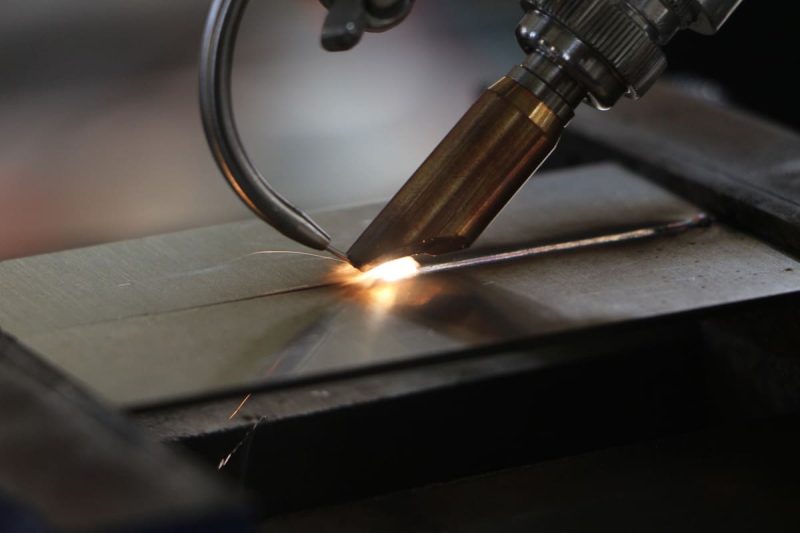
Understanding Laser Beam Focusing
Explanation of Laser Beam Focus and Its Role in Welding
The focus of a laser beam refers to the point in space where the laser beam is focused to the minimum diameter. This focus is a critical parameter in the laser welding process because it determines the distribution of the laser energy on the workpiece. The energy density of the laser beam is the highest after it is focused, which means that at the focus, the power of the laser is concentrated in a very small area, resulting in extremely high temperatures. It is this high temperature that allows the material to melt and fuse quickly in a short period of time to form a strong weld.
In actual operation, the focus position of the laser beam is usually adjusted according to the specific welding needs. If the focus is on the surface of the workpiece, the laser energy is mainly concentrated on the surface of the material, which is usually suitable for welding thin materials and can achieve high-precision welding effects. When the focus is inside the workpiece, the laser beam can penetrate the surface of the material and penetrate deep into the material, thereby achieving deeper welding. This is especially important for thicker workpieces or applications that require high-strength joints.
In addition, the position of the laser beam focus not only affects the depth of the weld, but also the width of the weld, the size of the heat-affected zone, and the welding speed. Proper focus setting can reduce welding defects such as pores, cracks, and incomplete penetration while ensuring welding strength. On the contrary, if the focus position is incorrect and the laser energy is unevenly distributed, it may lead to poor welding quality, shallow penetration, overheating or inconsistent welding results.
In modern laser welding systems, precise control of the focus position has become one of the important means to improve welding quality. For example, adaptive optics technology can adjust the focus of the laser beam in real time during the welding process to adapt to the shape and material properties of the workpiece, ensuring that the laser energy is always concentrated on the most needed part. In addition, through beam analysis technology, the focus characteristics of the laser beam can be deeply analyzed to further optimize the welding parameters and improve the stability and consistency of the welding.In general, the focus of the laser beam plays a vital role in the welding process. By precisely controlling the focus position, the welding quality can be effectively improved to meet the needs of various complex applications. Whether in automotive, aerospace or electronic manufacturing, the correct focus setting is the key to achieving high-quality welding.
Focus Size and Its Relationship to Welding Quality
Focus size refers to the diameter of the laser beam at the focus point, usually measured in microns. The size of the focus directly affects the distribution of laser energy and the final effect of welding. In laser welding, the smaller focus size means that the laser energy is more concentrated and the energy density per unit area is higher. This high energy density quickly melts the material and increases the penetration of the weld, allowing for deeper welds. This has significant advantages in applications that require high strength and depth of welding, such as thick plate welding or welding of critical structural parts.
However, too small a focus size also has its limitations. Because the energy is so concentrated, the width of the weld can become very narrow, which may not be ideal for some applications that require a wider weld. In addition, too small a focus size may increase instability during the welding process, resulting in inconsistent weld quality, especially when the surface of the processed material is uneven or contains impurities.
On the other hand, a larger focus size will distribute the laser energy over a larger area, reducing the energy density per unit area. While this may reduce the penetration depth of the weld, for applications requiring a wider weld bead, such as surface joining or seal welding, a larger focus size is more suitable. In this case, although the depth of the weld may be reduced, the coverage of the weld is larger, ensuring the integrity of the surface connection of the materials.
Therefore, the choice of focus size is closely related to the welding quality and must be optimized according to the specific welding needs. In practical applications, welding engineers need to select the appropriate focus size based on the material, thickness, shape, and welding requirements of the workpiece to achieve the best balance between weld width, depth, and strength. Through reasonable focus size settings, welding stability can be improved, defects reduced, and ultimately the overall quality of welding improved.
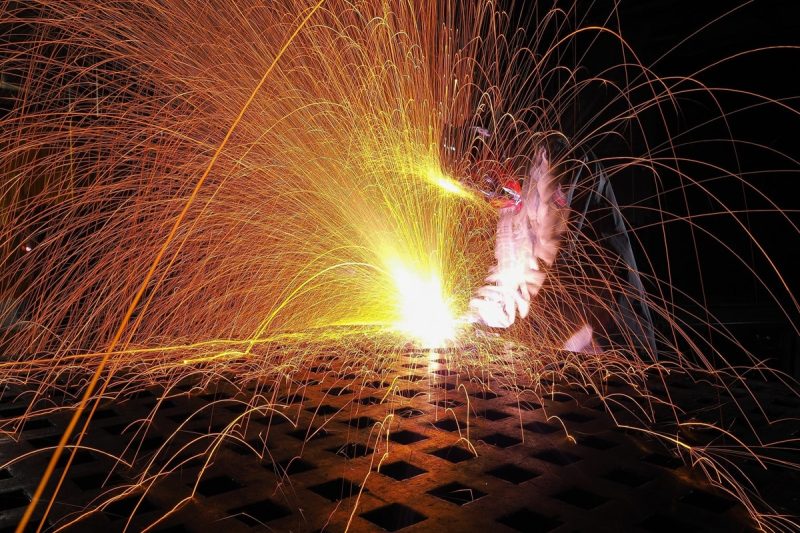
Factors Affecting Laser Beam Focusing
Laser beam focusing is a crucial step in laser welding, which directly determines the effect and quality of welding. Factors affecting laser beam focusing include lens selection, beam diameter, focal length, and beam quality. Correctly understanding and optimizing these factors can effectively improve welding performance and accuracy.
Lens Selection
The lens plays a key role in the laser beam focusing process and is the main component that affects the beam convergence ability. Different lens designs and materials have a significant impact on the focusing performance of the laser beam. For example, a short focal length lens can focus the laser beam quickly, resulting in a smaller focal spot size. This high energy density focusing is suitable for welding tasks that require fine control, such as microelectronic component welding or high-precision thin plate welding. In these applications, the smaller the focus, the higher the welding precision and the narrower the weld.
However, the disadvantage of short focal length lenses is that they have limited penetration capabilities and are not suitable for thick materials or deep welding tasks. For this type of application, longer focal-length lenses are more suitable. Long focal length lenses focus the laser beam deeper, producing a larger focal spot size and longer depth of focus, thereby increasing welding depth. This lens is often used for welding tasks that require deep penetration, such as thick plate welding or structural parts in heavy industry.
In addition, the material of the lens will also affect the transmission efficiency and focus quality of the laser beam. High-quality lens material can reduce the energy loss of the laser when passing through the lens, ensuring that the focus of the laser beam is clearer and more stable. Choosing the appropriate lens material and design is the first step to optimizing laser beam focusing, which is directly related to the quality of welding.
Beam Diameter
Laser beam diameter is another important factor that affects focusing. It refers to the width of the laser beam when it is not focused. The size of the beam diameter determines the focal size of the laser beam after it is focused. A larger beam diameter generally results in a larger focal size, which is suitable for applications that require a wider weld. For example, in welding tasks that require covering a large contact area or making surface connections, a larger focal size can provide sufficient coverage to ensure a stable connection of the materials.
Conversely, a smaller beam diameter can form a smaller focal point, thereby providing higher energy density and welding accuracy. This is especially important for welding tasks that require fine control, such as micro-welding or precision machining. By adjusting the beam diameter, welding engineers can find the best balance between focal size and welding accuracy to optimize welding quality.
Focal Length
Focal length refers to the distance from the lens to the focal point of the laser beam and is an important parameter that determines the focusing ability of the laser beam. The choice of focal length directly affects the size of the focal point and the focusing depth of the beam. A short focal length lens enables the laser beam to be focused quickly over a shorter distance, forming a smaller focal size. This configuration generally provides higher energy density, allowing the laser to melt the material quickly, and is suitable for applications that require high precision and fast welding.
However, a short focal length may also limit the welding depth because the focus is concentrated on the surface of the material or close to the surface, making it difficult to achieve deep penetration. For tasks that require deeper welding, a long focal length lens is more suitable. A long focal length lens can focus the laser beam over a longer distance, forming a larger focal size, thereby providing deeper penetration capabilities. However, in this case, the energy density may decrease and the welding accuracy may also be affected. Therefore, the choice of focal length must be weighed according to the specific welding needs to achieve the best balance between penetration and welding accuracy.
Beam Quality
Beam quality is often expressed in terms of the M² factor, which is a key measure of the focusing ability of a laser beam. The closer the M² factor is to 1, the better the beam quality, and the laser beam can be focused better, creating a smaller, more concentrated focus. A high-quality beam means higher energy density and more precise control, suitable for demanding welding tasks, such as the welding of high-precision components or the welding of complex-shaped workpieces.
On the contrary, a laser beam with poor beam quality will cause the focus to become larger and the energy distribution to be uneven, thus reducing the welding accuracy and quality. Welds may appear uneven and even produce defects such as pores, cracks, or poor welding. Therefore, improving beam quality is an important means to improve welding quality. By optimizing laser generator design and using high-quality optics, welding engineers can significantly improve beam quality, thereby increasing welding reliability and consistency.
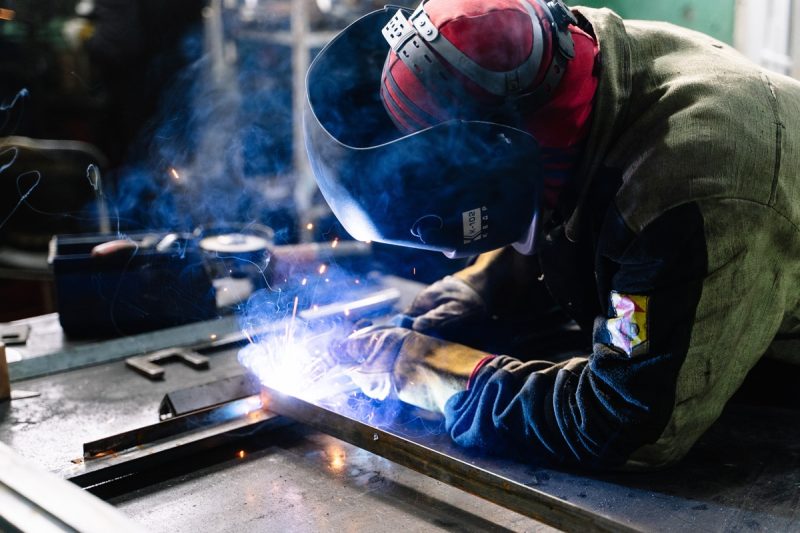
The Influence of Laser Beam Focusing on Welding Quality
The focus setting of the laser beam plays a vital role in the welding process, directly affecting several key parameters of welding, such as penetration depth, weld width, heat input, welding speed, and defect minimization. Through precise control of the focus of the laser beam, welding quality can be significantly improved to meet the needs of different applications.
Penetration Depth
The correct setting of the laser beam focus has a direct impact on the penetration depth of the weld. The penetration depth refers to the depth at which the laser beam can effectively penetrate the material and form a strong joint. In laser welding, when the focus is set on the surface of the workpiece or inside it, the laser beam energy is concentrated at that location, allowing the laser to quickly melt and penetrate the material. This high energy density concentration enables deep welding, which is especially important for thicker workpieces. The correct focus setting ensures complete penetration of the weld and avoids the phenomenon of incomplete penetration, thereby ensuring the strength and reliability of the welded joint.
In some specific applications, such as welding thick plates or welding heavy industrial components, the penetration depth requirements are very high. By accurately adjusting the focus position, engineers can optimize the penetration depth and ensure that the internal structure of the welded joint is uniform and defect-free. This precise control not only improves the strength of the weld but also enhances the durability and safety of the joint in actual application.
Weld Width
The focus setting also has an important impact on the width of the weld. The weld width refers to the lateral width of the weld formed by the molten material during the laser welding process. Generally, a smaller focus size produces a narrower weld, which is suitable for applications that require fine welding. For example, in the welding of microelectronic components or the manufacture of precision instruments, a narrower weld can reduce material waste and enhance the aesthetics and functionality of the welded part.
In contrast, a larger focus size results in a wider weld, which is suitable for welding structural parts that require a larger contact area or higher strength. For example, in the construction of ships or the manufacture of large mechanical equipment, a wide weld can provide a larger welding contact area and improve the strength and stability of the welded part. Therefore, by adjusting the focus size of the laser beam, the weld width can be flexibly controlled to meet different welding requirements, thereby optimizing welding quality and process performance.
Heat Input
The focal position of the laser beam directly affects the heat input during the welding process. Heat input refers to the energy transferred by the laser to the material during the welding process, which directly determines the degree of melting of the material and the size of the heat-affected zone (HAZ). The heat-affected zone refers to the area of the material that is heated but not melted during the welding process, and usually thermal deformation or performance degradation occurs.
When the focus of the laser beam is concentrated on the welding area, the energy density is high and the heat input is concentrated, so the material can melt quickly and complete the welding. This precise heat control helps to reduce the size of the heat-affected zone, thereby reducing the risk of thermal deformation during welding and is particularly suitable for welding tasks that require high precision and low heat input, such as welding of thin-walled materials or complex structures. In these applications, minimizing the heat-affected zone can maintain the integrity and mechanical properties of the material and ensure the quality of the welded joint.
Welding Speed
The focus setting of the laser beam has an important influence on the welding speed. The welding speed refers to the speed at which the laser beam moves on the surface of the workpiece, usually measured in millimeters per second (mm/s). The correct focus setting can improve the utilization efficiency of the laser energy, allowing the laser beam to melt the material faster and more stably during the welding process, thereby speeding up the welding speed. Higher welding speeds not only improve production efficiency but also reduce the time the material is exposed to high temperatures, further reducing the risk of thermal deformation and material damage.
However, incorrect focus settings may cause energy dispersion and fail to fully focus on the welding area, thereby reducing the welding speed. The decrease in welding speed not only affects production efficiency but may also lead to unstable welding quality, such as uneven welds and difficult molten pool control. Therefore, by optimizing the focus setting, welding engineers can maintain consistency and reliability of welding quality while increasing welding speed.
Minimize Defects
Optimization of laser beam focus settings is critical to reducing welding defects. During the welding process, common defects include pores, cracks, incomplete penetration, and poor welding. These defects not only reduce the strength of the welded joint but may also lead to structural failure or safety hazards. By precisely adjusting the focus position of the laser beam, the occurrence of these defects can be effectively reduced.
Correct focus setting ensures uniformity and consistency of the weld and reduces the accumulation of internal stress, thus reducing the risk of cracks and pores during the welding process. In addition, the appropriate focus position can also improve the formation and solidification process of the molten pool and avoid the occurrence of poor welding. By optimizing laser beam focus settings, welding engineers can significantly improve the stability and reliability of welding quality, ensuring the durability of welded joints over long periods of use.
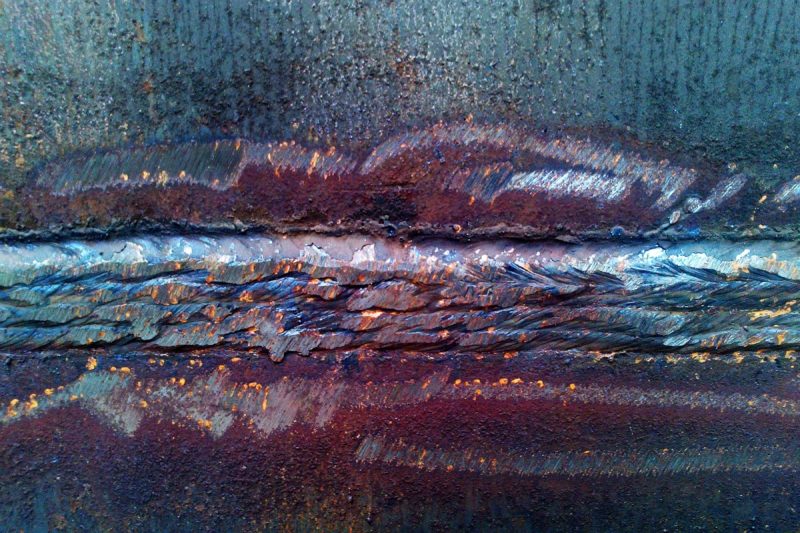
Effects of Incorrect Focus Setting
In the laser welding process, accurate focus setting is crucial. However, if the focus is not set correctly, it will have a series of negative effects on welding quality and production efficiency. The following are some specific problems that may be caused by incorrect focus setting:
Shallow Penetration
When the focus of the laser beam is not set correctly, especially when the focus position is too high or too low, the laser beam may not be able to effectively penetrate the workpiece. In this case, the laser energy cannot be fully concentrated in the area to be welded, resulting in insufficient welding depth. This shallow penetration phenomenon directly affects the strength and firmness of the welded joint. Shallow penetration welded joints may not be able to withstand stress during use, resulting in early failure or fracture of the structure, and cannot meet the requirements of practical applications, especially in industrial applications that require high strength and high reliability, such as aerospace, automotive manufacturing, and heavy machinery. Therefore, shallow penetration not only reduces the performance of the welded joint but may also bring serious safety hazards.
Excessive Heat Input
Incorrect focus setting may also lead to excessive heat input, especially when the focus is too concentrated on the surface of the material. In this case, the energy of the laser beam cannot be effectively dispersed into the deep layer of the material but is concentrated on the surface, resulting in excessive accumulation of heat in local areas.
This will cause several problems: First, the heat-affected zone (HAZ) is enlarged, and the material structure may undergo adverse changes, such as grain coarsening or phase transformation, which in turn affects the mechanical properties of the material. Secondly, excessive heat input will induce thermal deformation of the workpiece, resulting in a decrease in the dimensional accuracy of the workpiece, especially in manufacturing processes that require high precision and small tolerances, such as welding of electronic components and precision instruments. In addition, excessive heat may also cause problems such as surface oxidation and burning of the material, further reducing the quality and aesthetics of the weld. Therefore, controlling heat input is crucial to maintaining the structural integrity of the material and the quality of the weld.
Inconsistent Welding Quality
Improper focus setting can lead to inconsistency in welding quality, which is a serious problem in actual production. When the laser beam focus cannot be precisely aligned with the welding path, the width, depth, and morphology of the weld can vary significantly on the same workpiece. This inconsistency results in uneven mechanical properties of the weld, which affects the overall strength and durability of the welded joint. In addition, the inconsistency of welds can also affect the appearance quality of the product, especially in applications that require high visual quality, such as consumer electronics and medical device manufacturing, where the smoothness and uniformity of welds are critical. Inconsistent welding quality may also increase the complexity of subsequent processing, such as requiring additional grinding, repair, and inspection steps, thereby increasing production costs and time.
Reduced Efficiency
Incorrect focus settings can significantly reduce welding efficiency. When the laser beam cannot fully focus on the critical area of the workpiece, the energy utilization rate decreases and the welding speed decreases. As the welding speed slows down and the production cycle is extended, this not only reduces the overall efficiency of the production line but also increases the production cost per unit time. Especially in large-scale production, reduced efficiency can hurt a company’s production capacity and delivery times, which can lead to order delays and reduced customer satisfaction. In addition, rework rates may increase due to welding defects that may arise from improper focus settings, further increasing production costs and wasted time. Therefore, ensuring that focus settings are correct is critical to maintaining an efficient production process and controlling production costs.
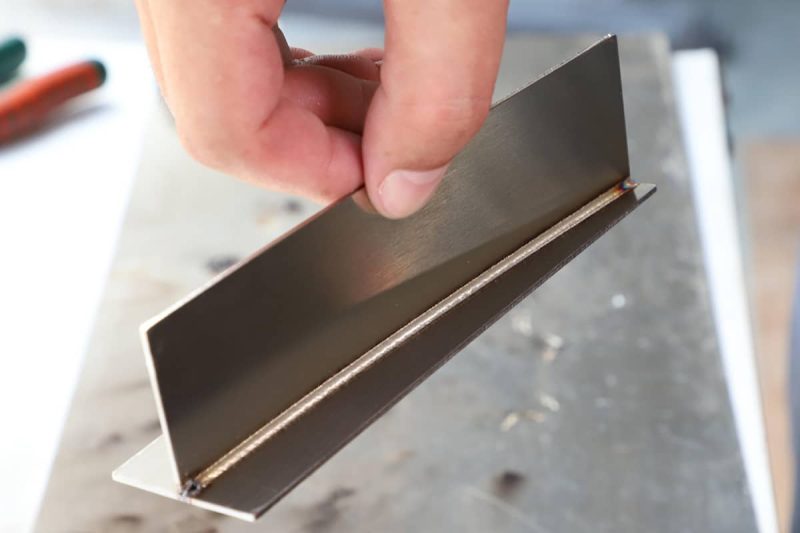
Optimize Laser Beam Focusing for High-Quality Welding
To achieve high-quality welding results during laser welding, the focusing performance of the laser beam must be optimized. Optimizing the focusing of the laser beam involves many aspects of technology, including beam analysis, process parameter adjustment, and advanced adaptive optics. These methods complement each other and help ensure the effective use of laser beam energy, thereby improving welding quality and production efficiency.
Beam Analysis
Beam analysis is the first step to optimize the focusing performance of the laser beam. By measuring and analyzing the key parameters of the laser beam in detail, you can gain a deeper understanding of how the laser beam behaves during the welding process. Beam analysis usually includes the following important aspects:
- Beam diameter measurement: Measuring the diameter of the laser beam at different positions can help determine how the laser beam is focused after passing through the lens. A smaller beam diameter generally means higher energy density, which is critical for achieving deep penetration and high-precision welding.
- Focus position measurement: By measuring the position of the laser beam focus, you can ensure that the laser beam is accurately focused on a specific part of the workpiece. Precise control of the focus position helps optimize welding depth and weld quality, avoiding problems such as shallow penetration or excessive heat input.
- M² factor analysis: The M² factor is an important indicator of laser beam quality, which reflects the focusing ability of the laser beam. By analyzing the M² factor, you can evaluate whether the laser beam has good focusing performance. A lower M² factor generally indicates that the laser beam is of better quality and can be focused more effectively, thereby improving welding accuracy and quality.
Beam analysis provides a scientific basis for laser welding, allowing operators to optimize adjustments based on specific welding needs. Through-beam analysis, potential problems such as focus shift or beam quality degradation can be identified and resolved, ensuring that the laser beam is always in optimal condition, thereby improving the overall quality of the weld.
Process Parameters
In addition to the optimization of the beam itself, the correct setting of welding process parameters is also an important factor in ensuring the focusing effect of the laser beam. Process parameters include laser power, welding speed, shielding gas flow, etc., which together determine the energy input and transmission efficiency of the laser beam. The following are some key optimization points for key process parameters:
- Laser power: Laser power directly affects the energy input during welding. Too high power may lead to excessive heat input, causing workpiece deformation or material burnout; too low power may lead to incomplete welding or shallow penetration. Therefore, accurate adjustment of laser power is the key to ensuring welding quality according to the characteristics of the material and welding requirements.
- Welding speed: The welding speed is closely related to the laser power, which determines the residence time of the laser beam on the workpiece. Slower welding speed can increase the penetration depth, but may cause the heat-affected zone to expand; faster speed helps to reduce thermal deformation and improve production efficiency. The best welding effect can be achieved by balancing the welding speed and laser power.
- Shielding gas flow: During laser welding, the use of shielding gas such as argon or nitrogen can prevent oxidation and contamination of the welding area. The regulation of shielding gas flow is essential to maintain the quality of the weld. Too high or too lowa gas flow may affect the formation and quality of the weld, so it needs to be accurately adjusted according to the material and process requirements.
By optimizing the process parameters, it is possible to ensure that the energy of the laser beam is fully utilized, thereby reducing welding defects such as pores, cracks and incomplete penetration, and improving the strength and consistency of the welded joint.
Process Parameters
Adaptive optics is an advanced optical adjustment technology that can optimize the focal position and beam shape of the laser beam in real-time. Adaptive optics dynamically adjust the laser beam during the welding process to ensure that the laser beam is always at the optimal focal position to cope with different workpieces and welding conditions. The following are specific applications of adaptive optics in laser welding:
- Real-time focus adjustment: Adaptive optics can monitor the focal position of the laser beam in real-time and adjust it according to the surface morphology of the workpiece and the welding path. This dynamic adjustment capability enables the laser beam to maintain high-precision focus during complex welding tasks, especially when dealing with workpieces with irregular shapes or varying thicknesses.
- Beam morphology optimization: In addition to the focal position, adaptive optics technology can also adjust the morphology of the laser beam, such as changing the spot shape or energy distribution of the beam. This adjustment can help optimize the morphology and quality of the weld and reduce welding defects, especially in the welding of multi-layer materials or composite materials.
- Automatic correction system: Adaptive optics systems are usually equipped with automatic correction functions that can detect and compensate for beam deviations caused by changes in optical components or the environment. This function ensures the stability and consistency of the laser beam, maintaining high-quality welding results even under long-term welding or complex process conditions.
The introduction of adaptive optics technology has greatly improved the flexibility and precision of laser welding, making it possible for laser welding to adapt to more complex and diverse application scenarios. For example, in automobile manufacturing, adaptive optics technology can be used to weld body structural parts, and in the aerospace industry, it can handle the welding needs of joints of different materials and thicknesses. Therefore, adaptive optics not only improve welding quality but also improve production efficiency and process stability.
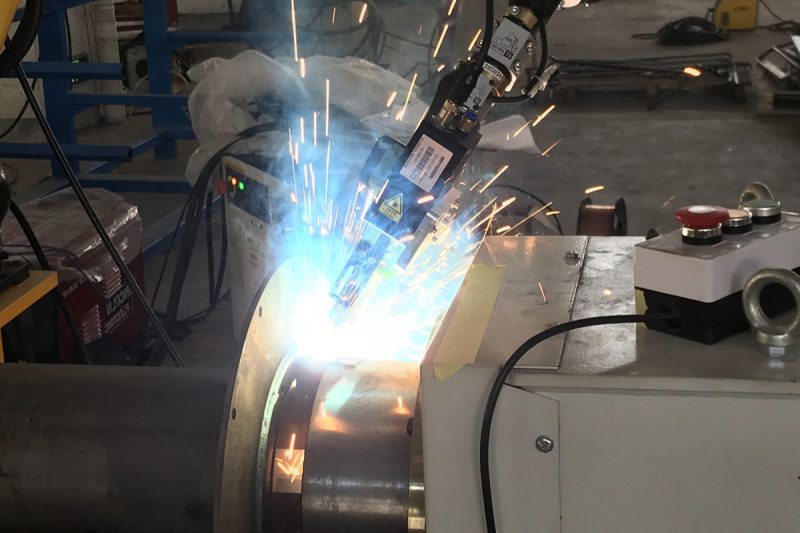
Application-Specific Considerations
Laser welding is widely used in multiple industries, each of which has its specific standards and challenges for welding quality and laser beam requirements. The following are specific considerations for different application areas:
Automotive Industry
In automobile manufacturing, laser welding is widely used to connect car bodies, chassis, and engine parts. Auto parts usually have complex shapes and strict strength requirements, so the accuracy and reliability of laser welding are crucial.
- Focus position and size optimization: The welding of automotive parts usually involves a variety of materials and thicknesses. The correct focus setting can ensure the strength and stability of the weld. The focus position needs to be precisely adjusted to meet the connection requirements of different parts. A smaller focus size can achieve high-precision welding, but it is also necessary to ensure that the depth and strength of the weld meet the safety standards of automotive manufacturing.
- Strength and aesthetics of the weld: The welds of automotive parts must not only have sufficient strength to withstand the operating load of the vehicle but also meet the aesthetic requirements of the appearance. The high precision of laser welding helps to reduce welding defects such as spatter and uneven welds, thereby improving the appearance and quality of automotive parts.
- Material compatibility: Automotive manufacturing involves the connection of many different materials, such as steel, aluminum, and composite materials. Laser welding can handle the welding tasks of these different materials, but the focus position and size of the laser beam need to be optimized for different materials to ensure the firmness and durability of the welded joint.
Aerospace Industry
The aerospace industry has extremely high requirements for welding quality, especially in the manufacture of engine and fuselage structural parts. When laser welding is applied in this field, special attention should be paid to the following points:
- Precise focus control: Aerospace components are often subjected to extreme environmental conditions such as high temperatures and high pressures. Therefore, the focus setting of laser welding must be very precise to ensure the quality and structural strength of the weld. Optimization of the focus position and size helps to avoid weld defects, thereby ensuring the safety and reliability of the welded joint.
- Beam analysis and adaptive optics: In aerospace manufacturing, it is often necessary to weld complex geometries and materials of different thicknesses. Advanced beam analysis and adaptive optics technologies can adjust the focus of the laser beam in real-time to ensure optimal performance during the welding process. These technologies help achieve high-precision welding and reduce flight safety hazards caused by welding defects.
- Material and environmental control: Aerospace components often use high-performance materials such as titanium alloys and high-temperature alloys. The welding of these materials requires special laser welding parameters and environmental control to ensure that the material properties are not affected during the welding process. Optimizing the focus position and size of the laser beam can reduce the heat-affected zone and ensure the structural integrity of the material.
Electronics Manufacturing
In electronics manufacturing, laser welding is mainly used to connect tiny components such as chips, wires, and connectors. Because these components are extremely sensitive to heat, laser welding requires special attention to the following aspects:
- Precise focus setting: Electronic parts are very small in size, so the focus setting of the laser beam must be very precise. Small focus size can provide high energy density, which helps to achieve fine welding. However, the focus control must be very precise to avoid excessive heat input to tiny parts, which can cause damage or performance degradation.
- High beam quality: Welding in electronic manufacturing requires extremely high uniformity and quality of welds. Laser welding with high beam quality can provide a stable focus, thereby achieving high-quality welded joints. Optimizing beam quality can reduce thermal deformation and joint defects caused by welding, and improve the overall reliability of electronic products.
- Heat management: In electronic manufacturing, the heat generated by laser welding must be strictly controlled to prevent overheating of sensitive electronic components. The focus setting of the laser beam needs to ensure precise control of heat input to protect parts from overheating damage while ensuring the firmness and stability of the weld.
Electronics Manufacturing
In medical device manufacturing, laser welding is used to connect high-precision materials such as stainless steel and titanium alloys. The welding of these materials is extremely demanding, involving the following key considerations:
- Precise focus position and size: Medical devices often involve high-precision components such as surgical instruments and implants. Optimization of the focus position and size of the laser beam is critical to ensure the accuracy and reliability of the welded joint. A smaller focus size helps achieve delicate welding, ensuring the safety and functionality of medical devices.
- Material properties: Medical devices often use high-performance alloys and stainless steels, which have very strict requirements for welding. The focus setting of the laser beam must take into account the thermal conductivity and thermal reactivity of the material to avoid thermal damage and structural changes during welding.
- Hygiene requirements for welded joints: The welded joints of medical devices need to meet strict hygiene and sterility requirements. Precise control of the focus of the laser beam can reduce defects in welded joints and ensure the safety and hygiene of the product during use.
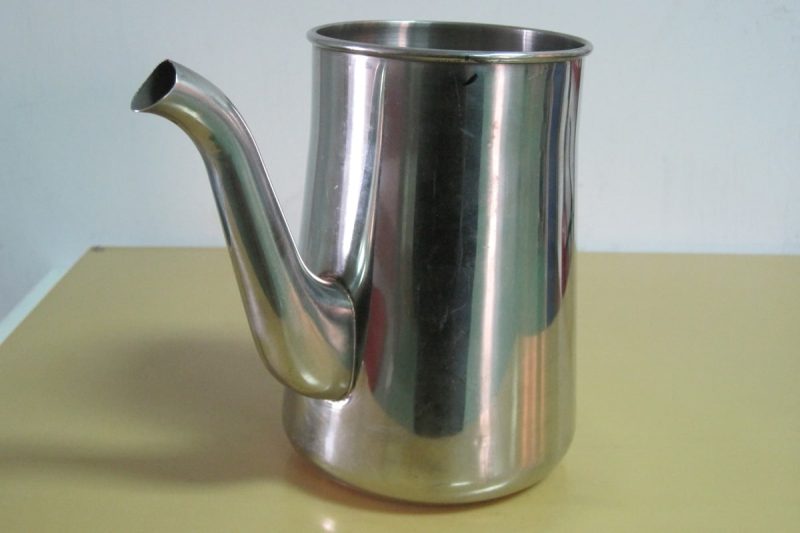
Summarize
The focus setting of the laser beam has a profound impact on welding quality. Proper selection of lenses, and adjustment of beam diameter, focal length, and beam quality can significantly improve the depth, width, and consistency of welds, thereby reducing welding defects. Through precise focus setting, not only can deeper penetration and wider welds be achieved, but the uniformity of the welding process can also be improved, ensuring consistent quality in every welded joint. This consistency is particularly important in applications that require high standards, such as aerospace and medical device manufacturing.
In addition, optimizing focus settings can effectively reduce welding defects such as porosity, cracks, and incomplete penetration. Precisely controlling the focus of the laser beam can reduce the size of the heat-affected zone and reduce thermal deformation, thereby improving the stability of welding quality. At the same time, accurate focus settings can help avoid overheating and material damage, ensuring the integrity and strength of welded joints. This optimization in the welding process not only improves welding quality but also improves production efficiency and reduces production costs.
As laser technology continues to advance, so does focus optimization technology. Advanced beam analysis, adaptive optics technology, and improvements in process parameters will further promote the application of laser welding technology. In the future, laser welding technology will be able to handle more complex welding tasks, meet the needs of more industries, and play an increasingly important role in the manufacturing industry. The continuous development of focus optimization technology will promote innovation and progress in the welding industry, achieving higher quality and more efficient production.
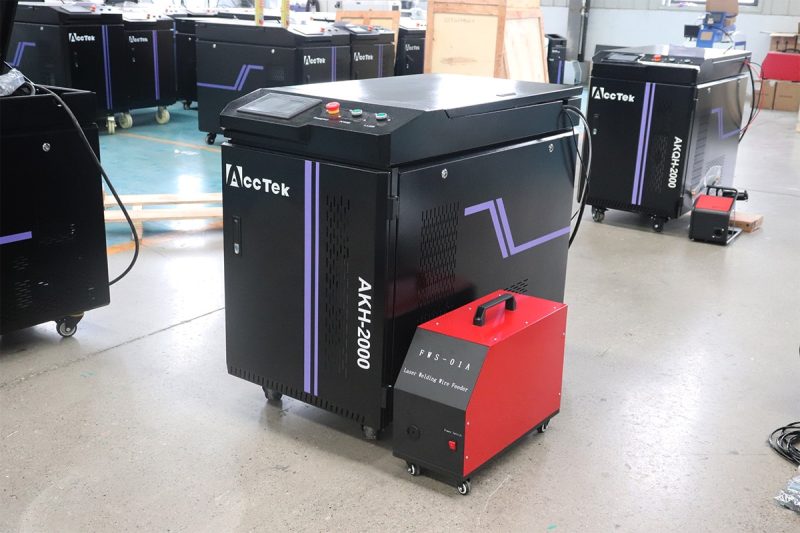
Get Laser Solutions
Choosing the right laser beam focus setting is key to optimizing welding quality. When working with a reliable supplier, you can get advanced technical support, professional advice, and continuous service. At AccTek Laser, we offer a diverse range of laser welding equipment for a variety of industry needs. Our experts will help you optimize focus parameters, ensure stable weld quality, and maximize production efficiency. We also provide advanced features such as precision focus adjustment and intelligent monitoring systems to ensure consistency and accuracy of welding. In addition, our technical team provides regular equipment maintenance and technical support to ensure that your equipment is always running at its best. By working with AccTek Laser, you will get efficient and stable welding quality, reduce production risks, and enhance competitiveness. Contact us now to learn more about our innovative welding solutions to help your business take off.
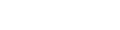
Contact information
- [email protected]
- [email protected]
- +86-19963414011
- No. 3 Zone A, Lunzhen Industrial Zone,Yucheng City , Shandong Province.
Get Laser Solutions