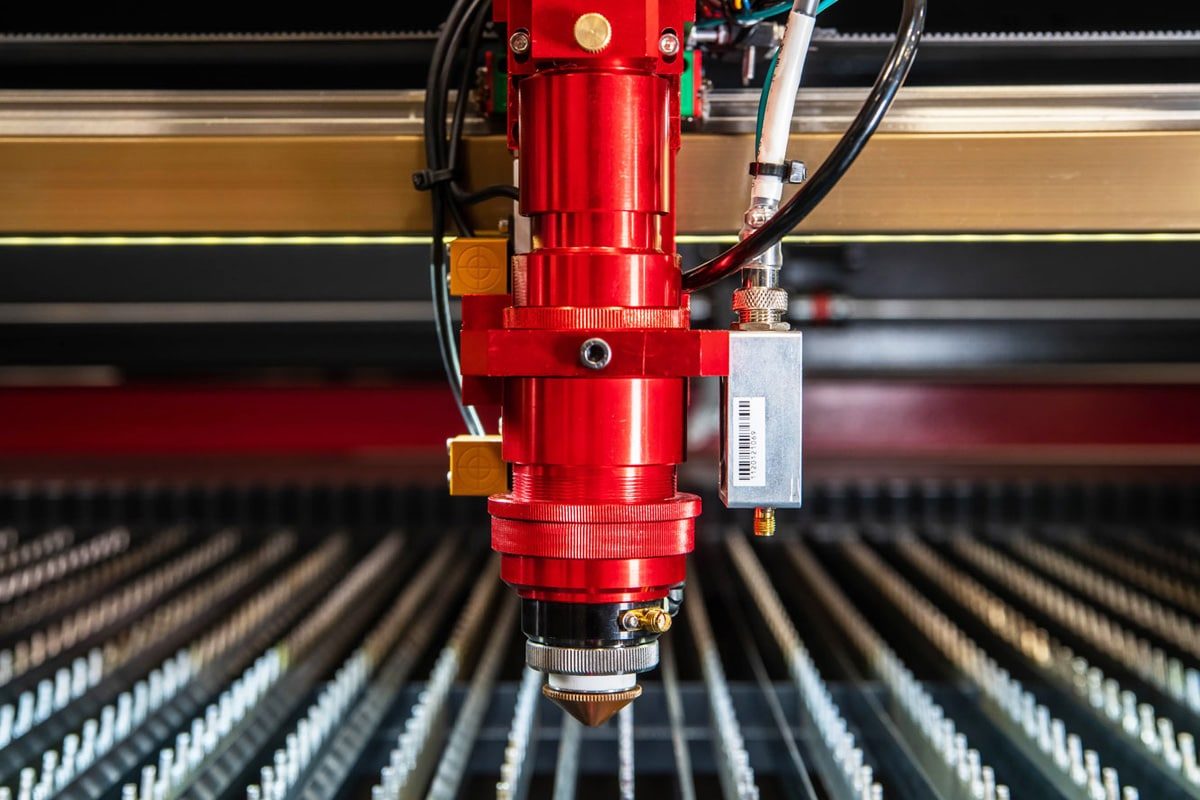
How Does the Gas Supply System of a CO2 Laser Cutting Machine Work?
CO2 laser cutting machines are widely used in modern manufacturing for their high precision and high efficiency, and have become the preferred equipment in many industries. During its working process, the gas supply system is an important part to ensure the cutting quality and efficiency. The system consists of auxiliary gases (such as oxygen, nitrogen or air), which assist the laser beam to achieve precise cutting by adjusting the flow and pressure of the gas. Different gases are selected according to the material properties and cutting requirements, which can not only increase the cutting speed, but also prevent the material from oxidizing and extend the life of the equipment. This article will discuss the gas supply system of the CO2 laser cutting machine in detail, including its composition structure, working principle, gas supply requirements and safety precautions.
Table of Contents
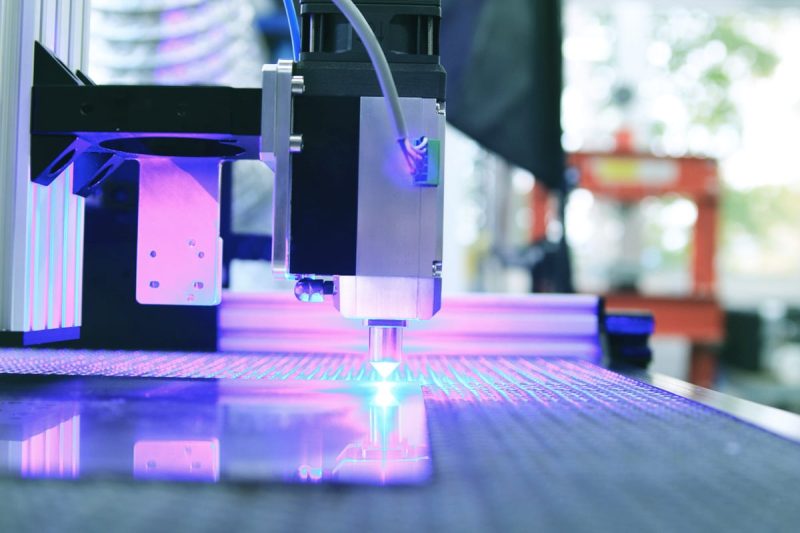
Basic Components of a CO2 Laser Cutting Machine
Laser Source
The laser source is the core component of the CO2 laser cutting machine, which generates a high-intensity laser beam. The CO2 laser generator is a gas laser generator that mainly uses carbon dioxide gas as a gain medium. Under the excitation of electrical energy, the electrons in the CO2 gas molecules are excited to a higher energy level and then release light of a specific wavelength, namely laser. CO2 lasers usually operate in the infrared band of 10.6 microns, which has a high absorption rate in materials and is therefore very suitable for cutting and engraving various metal and non-metal materials. The power of the laser source determines the cutting thickness and speed, and CO2 laser generators of different powers can be used for other materials and applications. The power ranges from tens to thousands of watts, which is suitable for efficiently processing thin metals, plastics, wood, fabrics, paper, and other materials.
Optical System
The main function of the optical system is to transmit and focus the laser beam so that its energy is highly concentrated on the surface of the cutting material. The optical system is composed of multiple optical components, including reflectors, focusing lenses, and transmission optical fibers. The reflector is used to guide the laser beam from the laser source to the processing head, while the focusing lens is responsible for focusing the laser beam to an extremely small point to ensure that the laser energy is concentrated on a small area during cutting, thereby achieving fine cutting. The accuracy of the optical system has a direct impact on the cutting effect. The cleanliness, quality, and focusing ability of the lens will affect the shape of the laser beam and the efficiency of energy transfer. Therefore, regular maintenance and cleaning of optical components is essential to ensure the efficient operation of the CO2 laser cutting machine.
Control System
The control system manages the entire cutting process through preset computer software. It converts the design drawings into cutting paths and precisely controls the movement of the laser beam, power output, speed, and flow of auxiliary gas. Common control systems are usually CNC (computer numerical control) systems, where users can set the cutting path and parameters of the material by programming or loading CAD/CAM files. The control system not only ensures that the laser beam moves along the specified trajectory, but also adjusts the cutting speed in real-time to meet the requirements of different thicknesses and materials, thereby ensuring cutting accuracy and efficiency. In addition, advanced control systems can monitor the status of the machine, provide automation functions and fault diagnosis, and further improve production efficiency.
Air Supply System
The air supply system is an important auxiliary device of the CO2 laser cutting machine, which is responsible for providing auxiliary gases such as oxygen, nitrogen, or air to the cutting area. These gases act on the material surface simultaneously with the laser beam through the nozzle, helping to remove the slag, smoke, and debris generated during the cutting process, preventing heat accumulation, and improving the cutting accuracy and edge quality. Different auxiliary gases play different roles in the cutting of different materials:
- Oxygen: Mainly used for cutting carbon steel, it can increase cutting speed and promote material oxidation, thus forming a smooth cutting edge.
- Nitrogen: Commonly used for cutting stainless steel and aluminum materials, it prevents oxidation of the material edge, so that the cut remains bright and colorless.
- Air: An economical choice, suitable for cutting some materials that do not require high edges.
The pressure and flow of the auxiliary gas need to be precisely adjusted according to the material type and thickness to ensure the cutting quality and stable operation of the machine. In addition, the air supply system can prevent the optical lens on the laser head from being contaminated and extend the service life of the machine.
In summary, these basic components of CO2 laser cutting machines work together to ensure efficient and precise cutting performance in the manufacturing industry. The laser source provides the energy required for cutting, the optical system transmits and focuses the laser beam, the control system manages the cutting process, and the air supply system improves the cutting quality and efficiency through auxiliary gas. The precise coordination of each component is the key to achieving high-quality cutting results.
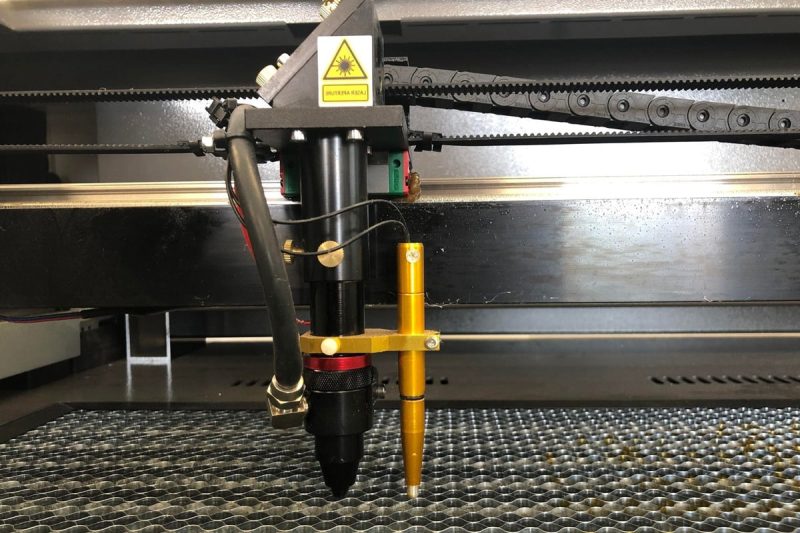
Working Principle of CO2 Laser Cutting
CO2 laser cutting is a technology that uses carbon dioxide gas to generate a high-energy laser beam to cut materials. Its working principle can be divided into the following key steps:
Laser Generation
Inside a CO2 laser generator, a gas mixture consisting mainly of carbon dioxide (CO2), nitrogen (N2), and helium (He) is enclosed in a closed laser cavity. When a power supply provides a high voltage, these gases are excited to form a plasma. The excited gas molecules collide with each other and release energy, generating laser photons. The laser photons are reflected in the laser cavity and amplified by the gain medium (i.e., the excited gas), ultimately forming a powerful CO2 laser beam.
Beam Delivery and Focusing
The generated laser beam is transmitted and focused through a series of optical lenses and lens systems. The main function of the optical system is to focus the laser beam to a very small point to increase the energy density of the beam. Through precise optical design, the laser beam can be focused to a point with a diameter of only a few microns, so that the surface temperature of the material rises rapidly to meet the cutting requirements.
Material Interactions
When a laser beam is focused onto the surface of a material, the high energy of the laser causes the material to quickly heat up to its melting or boiling point. The thermophysical properties of different materials affect this process:
- Melting: For some metal materials, the heat of the laser causes them to melt at the cutting edge, forming liquid metal.
- Evaporation: For some non-metallic materials (such as plastic or wood), the laser can quickly heat the surface to the evaporation point, causing the material to turn directly into gas.
At this stage, the interaction of the laser with the material creates a cut or hole and the cutting process begins.
Cutting Process
During the cutting process, the laser beam moves along a preset path. This process is usually achieved by a computer-controlled numerical control (CNC) system to ensure accurate and repeatable cutting. CO2 laser cutting machines can cut a variety of materials at high speeds and precision to form the desired shapes and patterns. The cutting quality of laser cutting depends on several factors, including laser power, cutting speed, material thickness, beam focus position, and the use of gas assist (such as oxygen or nitrogen). Using appropriate gas assist can improve cutting quality and efficiency, for example, oxygen can accelerate the combustion cutting of metals, while nitrogen can reduce the oxidation of materials.
CO2 laser cutting technology is an efficient and precise material processing method that uses the heat energy of the laser to quickly melt or evaporate the material to achieve cutting. Its superior cutting quality and wide range of applications make it an indispensable and important tool in modern manufacturing.
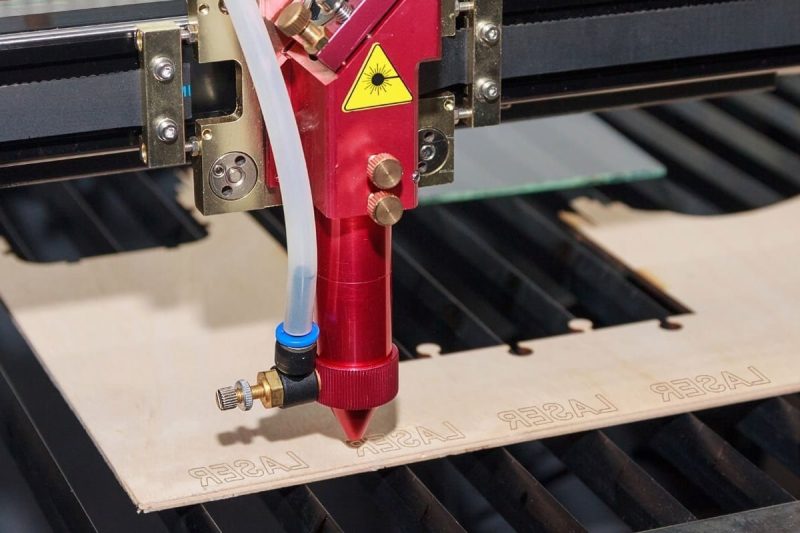
Gas Supply System in CO2 Laser Cutting Machine
The air supply system plays a vital role in CO2 laser-cutting machines. By selecting and using appropriate auxiliary gas, cutting efficiency and cutting quality can be significantly improved. The following is a detailed description of the air supply system.
The Role of Air in Laser Cutting
Air plays an important role as an auxiliary gas in the laser cutting process, which is mainly reflected in the following aspects:
- Remove slag: During the laser cutting process, the material is instantly heated to a molten or vaporized state by the high-energy laser. The slag and vapor generated will affect the cutting quality and cause the cut to be rough. By introducing air as an auxiliary gas, these slags can be effectively removed, keeping the cutting area clean and ensuring that the laser beam can cut the material smoothly.
- Reduce the heat-affected zone: The flow of air helps to remove heat from the cutting area, thereby reducing the heat-affected zone (HAZ) of the material. A smaller heat-affected zone can prevent the material from deforming or scorching during the cutting process, especially in thin materials or heat-sensitive materials such as plastics and wood.
- Improve cutting quality: The appropriate airflow and pressure can help improve the edge quality of the cut, make the cut smoother, and reduce the generation of burrs. At the same time, the effect of air can make the cutting speed faster and improve production efficiency.
- Optimize cutting performance: By selecting different auxiliary gases, the cutting speed and cutting effect can be optimized for the characteristics of specific materials. For example, oxygen can accelerate the combustion of metals and increase cutting speeds, while nitrogen can reduce oxidation reactions when cutting non-metallic materials.
Type of Air Supply System
Gas supply systems can be divided into two main types based on application requirements:
- Auxiliary gas supply: This is a gas supply method mainly used to enhance the cutting effect. The auxiliary gas is usually compressed air, and its purpose is to remove slag and gasify materials. During the cutting process, the auxiliary gas will be sprayed in the path of the laser beam, effectively cleaning the cutting area and improving the cutting quality.
- Process gas supply: According to the cutting requirements of different materials, it is crucial to choose the right process gas.
Components of the Gas Supply System
The effective operation of the gas supply system depends on the coordinated work of multiple components, mainly including:
- Compressor: As the core equipment of the gas supply system, the compressor is responsible for providing the required gas pressure and flow. By adjusting the output of the compressor, the gas flow during the cutting process can be precisely controlled to ensure a stable gas supply during the cutting process.
- Dryer: In order to ensure the dryness of the gas and avoid the influence of moisture on the cutting effect, a dryer is usually configured in the gas supply system. The dryer can effectively remove moisture from the gas to prevent water vapor from reacting with the laser beam, resulting in a decrease in cutting performance.
- Filter: The filter plays a key role in the gas supply system. It can filter out impurities and particles in the gas to ensure the purity of the gas. Clean gas helps maintain the cutting quality and the long-term stable operation of the equipment and prevents dirt from damaging the cutting head and other components.
- Distribution system: The distribution system is responsible for evenly distributing the gas to the cutting head and other components. A reasonably designed distribution system can ensure that the gas flows stably throughout the cutting process and avoid the fluctuation of gas pressure and flow on the cutting effect.
The air supply system in the CO2 laser cutting machine has an important impact on the cutting effect and efficiency. Through reasonable selection and configuration of auxiliary gas, combined with efficient gas supply system components, the quality and productivity of laser cutting can be significantly improved, ensuring precision cutting of various materials.
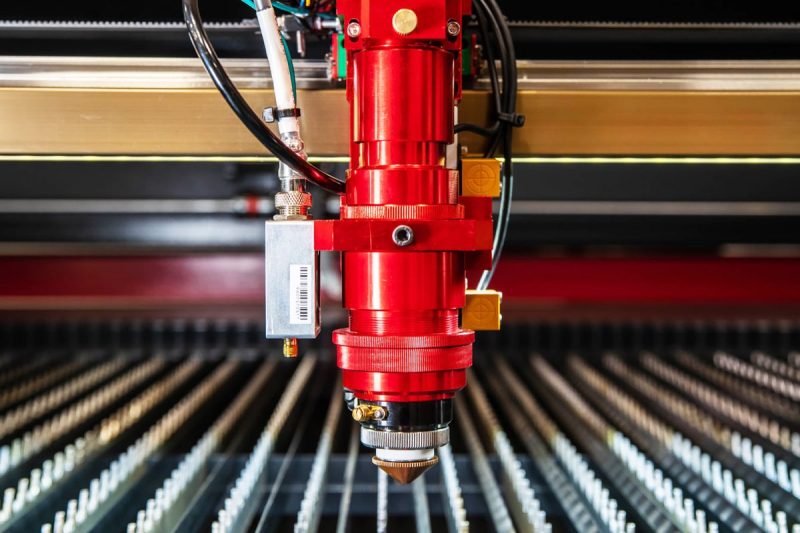
Specific Requirements for Gas Supply of CO2 Laser Cutting Machine
In the CO2 laser cutting process, the design and configuration of the gas supply system is critical to cutting quality and efficiency. The following are specific requirements for the gas supply system, covering gas purity, pressure and flow, as well as the compatibility of gas and material.
Gas Purity
Gas purity is one of the important factors affecting the quality of laser cutting. High-purity gas has the following advantages in laser cutting:
- Reduce interference from impurities: During the laser cutting process, if impurity-containing gases are used, unnecessary chemical reactions may occur during the cutting process, which may affect the cutting effect. Impurities may cause gas and laser scattering, reduce the energy density of the laser, and thus affect the cutting quality.
- Improve cutting effect: High-purity gas can ensure that the energy of the laser beam is concentrated on the cutting material, improving cutting speed and efficiency. For example, when using oxygen to cut metal, pure oxygen can fully react with the metal, improve thermal efficiency, and form a clearer incision.
- Extend equipment life: Using high-purity gas can reduce wear on laser cutting equipment, especially the cutting head and optical system. Impurities and contaminants may cause blockage or corrosion of the equipment, thereby shortening the service life of the equipment.
Pressure and Flow
Proper gas pressure and flow are key factors in ensuring the efficient operation of laser-cutting machines. Specific requirements include:
- Pressure: The gas pressure must be kept within the recommended range of the laser cutting machine. Too low a gas pressure will result in incomplete cutting and affect the cutting effect, especially when cutting on thicker materials; while too high a gas pressure may cause damage to the cutting head or burn-through of the material, resulting in rough cutting edges.
- Flow rate: The gas flow rate also needs to be precisely controlled according to the material type and cutting thickness. The appropriate flow rate can ensure the effective discharge of slag and gasified materials during laser cutting, preventing them from reattaching to the cutting edge and affecting the cutting quality. Too small a flow rate may result in insufficient material heating, and too large a flow rate may cause additional heat dissipation and deformation of the material.
- Adjustment mechanism: Most laser cutting machines are equipped with a gas pressure and flow adjustment mechanism, which enables the operator to make real-time adjustments based on the actual cutting conditions and material characteristics to ensure the best effect of the cutting process.
Gas and Material Compatibility
Different materials have different requirements for assist gases. Choosing the right gas is critical to optimizing cutting results and ensuring material quality:
- Oxygen: Oxygen is a commonly used cutting gas, especially suitable for cutting carbon steel and some alloys. Oxygen reacts with metal during the cutting process to accelerate the cutting speed and improve thermal efficiency. However, when using oxygen, care should be taken to prevent material embrittlement caused by overoxidation.
- Nitrogen: Nitrogen is commonly used to cut stainless steel, aluminum, and some plastics and composite materials. Nitrogen can prevent oxidation reactions, maintain the original color of the material and smooth cuts, and is particularly suitable for products with high appearance requirements.
- Helium and carbon dioxide: In certain specific cases, helium or carbon dioxide can also be used as auxiliary gases, especially when cutting some special materials. Helium can be used to provide higher thermal conductivity, while carbon dioxide is suitable for cutting some non-metallic materials.
The specific requirements of the gas supply system directly affect the cutting quality and efficiency of the CO2 laser cutting machine. When designing and operating a laser cutting machine, it is important to ensure the use of high-purity gas, appropriate gas pressure, and flow, and select the appropriate auxiliary gas according to the material characteristics. The comprehensive optimization of these factors will help improve cutting results, reduce production costs, and extend the service life of the equipment.
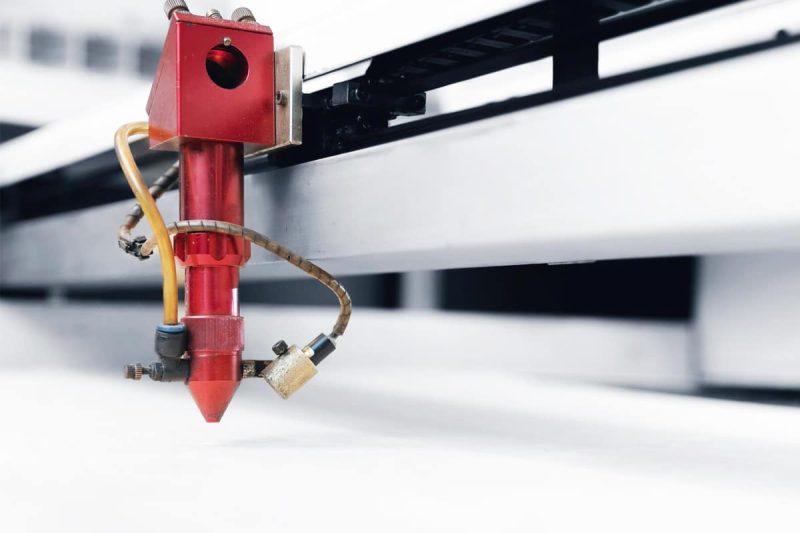
Auxiliary Gas in CO2 Laser Cutting
In the CO2 laser cutting process, the choice of auxiliary gas has an important impact on the cutting quality, efficiency, and the final effect of the material. Different types of auxiliary gases have their unique functions. The following are several commonly used auxiliary gases and their characteristics:
Oxygen (O2)
Oxygen is a powerful auxiliary gas, especially suitable for cutting metal materials. Its main functions include:
- Enhanced cutting speed: When laser cutting metal, oxygen not only helps remove slag, but also provides additional heat by reacting with the oxidation of the metal. This reaction makes the cutting process faster and more efficient, which can significantly increase cutting speed.
- Applicable Materials: Oxygen is primarily used for cutting carbon steel and certain alloys, especially thick sheet metal. By properly adjusting the oxygen flow, deeper cutting can be achieved to meet the processing needs of metals of different thicknesses.
- Note: Although oxygen can speed up cutting, its high temperature and chemical reactions can also cause material embrittlement and deformation. Therefore, when using oxygen, operators need to carefully adjust cutting parameters to prevent unnecessary material loss.
Nitrogen (N2)
Nitrogen is a non-reactive gas that is widely used for cutting high-quality non-metallic materials. Its advantages include:
- Prevent oxidation: Nitrogen can prevent oxidation reactions on the surface of materials during cutting, keeping the cutting edge smooth and clean. This is especially important for stainless steel, aluminum, and some composite materials, as oxidation can affect their appearance and performance.
- Improve cutting quality: Materials cut with nitrogen usually have higher cutting quality and no burrs, which is suitable for product processing with strict appearance requirements.
- Scope of application: Nitrogen is not only suitable for metal cutting but also for processing non-metallic materials such as plastics and wood. According to the different characteristics of the material, adjusting the flow and pressure of nitrogen can achieve the best cutting effect.
Air (compressed)
Compressed air is the most commonly used auxiliary gas and is suitable for general laser-cutting purposes. Its characteristics include:
- Economy: Air is the most readily available and economical auxiliary gas, suitable for most laser-cutting operations, especially in projects with strict cost control.
- Wide applicability: Compressed air is suitable for cutting a variety of materials, including wood, plastics, and some metals. Although its cutting effect may not be as good as oxygen or nitrogen, in many cases, compressed air can meet the basic requirements of cutting quality.
- Remove slag: During the cutting process, compressed air can effectively remove slag on the surface of the material, keep the cutting area clean, and improve cutting efficiency.
The Importance of Choosing the Right Assist Gas
Choosing the right auxiliary gas is crucial to improving the quality and efficiency of CO2 laser cutting. Appropriate auxiliary gas can not only reduce material loss but also optimize the cutting process and ensure the quality of the final product. Specifically:
- Improve cutting effect: By selecting the right gas, you can maximize the cutting performance of the laser, achieve faster cutting speed and more precise cutting effect, and reduce the need for post-processing.
- Reduce material loss: Improper use of auxiliary gas may lead to rough cutting edges, material damage, or incomplete cutting, increasing material waste. Choosing the right gas can effectively reduce these losses and improve material utilization.
- Enhance production efficiency: The right auxiliary gas can reduce cutting time, improve production efficiency, and thus enhance the competitiveness of the enterprise.
In the CO2 laser cutting process, the choice of auxiliary gas directly affects the cutting quality and efficiency. Oxygen, nitrogen, and compressed air each have their unique advantages. Choosing the right auxiliary gas is crucial to achieving high-quality cutting, reducing material loss, and improving production efficiency. Through reasonable gas configuration, companies can achieve better results in the field of laser cutting.
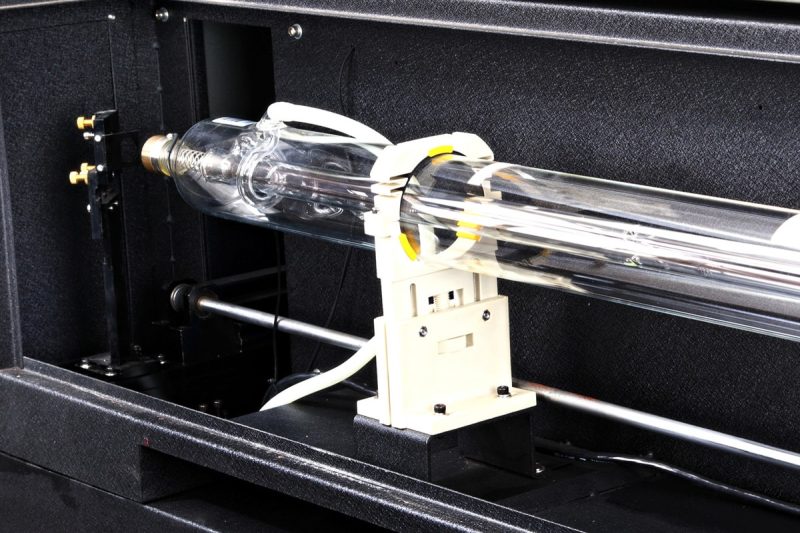
Safety Considerations for CO2 Laser Cutting Machines
When operating a CO2 laser-cutting machine, safety issues cannot be ignored. To ensure the safety of operators and reduce the risk of accidents, it is necessary to pay attention to the following safety considerations.
Gas Storage and Handling
Gas storage and handling are important aspects to ensure laser cutting safety, involving the following aspects:
- Safety of storage containers: Gas storage containers (such as oxygen cylinders, and nitrogen cylinders) should comply with relevant national and industry standards, and should be regularly inspected and maintained. Containers should be placed in well-ventilated areas away from heat sources and flammable materials to reduce the risk of gas leakage and explosion.
- Avoid gas leakage: When replacing gas cylinders, operators should ensure good sealing and use appropriate connectors and valves to avoid gas leakage. During use, regularly check gas pipelines and connections, and deal with problems in a timely manner.
- Follow safe operating procedures: All operators need to receive training on gas storage and handling, understand emergency handling procedures, and ensure that relevant safe operating procedures are followed. For example, when dealing with a leak, the operator should immediately evacuate the site and notify relevant personnel to handle it.
Pressure Regulation and Monitoring
Pressure regulation and monitoring are key to ensuring the normal operation of the gas supply system. Specific measures include:
- Set up an effective pressure regulation system: The laser cutting machine should be equipped with a professional pressure regulation device to keep the gas supply within a reasonable pressure range. Use a suitable pressure regulator to ensure stable gas pressure and avoid cutting problems caused by excessive or low pressure.
- Check the pressure gauge regularly: The operator needs to check the pressure gauge regularly to ensure its accuracy and normal working condition. If the pressure gauge is found to be faulty, it should be replaced immediately. Record the pressure changes so that the system can be adjusted in time to ensure normal gas supply during the cutting process.
- Emergency valve and alarm system: The laser cutting machine should be equipped with an emergency shut-off valve and a pressure alarm system to quickly cut off the gas supply in case of abnormal conditions to protect the safety of equipment and personnel.
Ventilation and Extraction Systems
A good ventilation and exhaust system is an important measure to ensure the safety of operators. Specific requirements include:
- Effectively remove harmful gases: During the cutting process, the reaction between the laser and the material will produce harmful gases and smoke. The ventilation and exhaust system should have sufficient capacity to effectively remove these harmful gases and ensure the air quality of the operating environment.
- Reasonable layout of ventilation equipment: The layout of ventilation equipment should take into account the circulation of the working area to ensure that the air can flow smoothly. The ventilation system should be cleaned and maintained regularly to keep it operating efficiently.
- Monitor air quality: Air quality monitoring instruments can be installed in the working area to monitor the concentration level of harmful gases in real-time. Once the concentration exceeds the safety standard, the system should promptly alarm and take necessary emergency measures to ensure the health and safety of the operator.
In the operation of CO2 laser cutting machines, safety issues involve many aspects, including gas storage and handling, pressure regulation and monitoring, and the effectiveness of ventilation and exhaust systems. By implementing strict safety measures, regular inspections, and maintenance of equipment, operators can be ensured to work in a safe environment, thereby reducing potential risks and accidents. Safety is the top priority of cutting operations, and companies need to attach great importance to it.
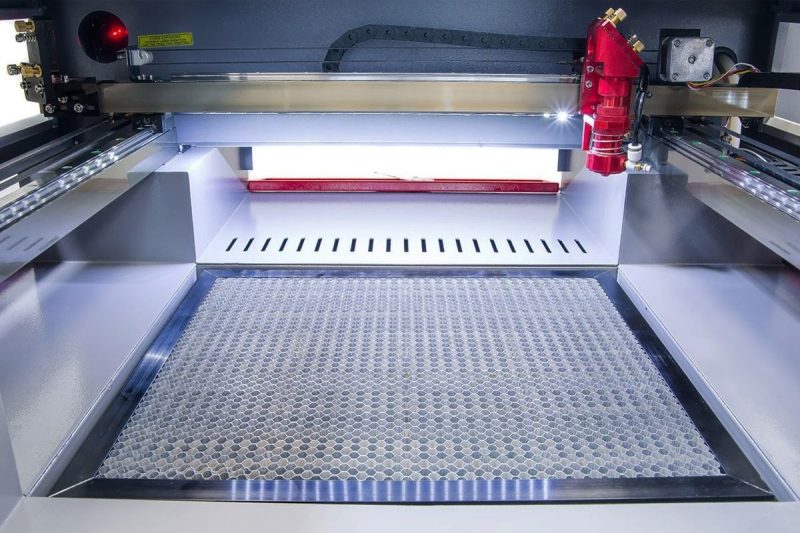
CO2 Laser Cutting Machine Maintenance and Troubleshooting
To ensure the normal operation and optimal performance of the CO2 laser cutting machine, regular maintenance and troubleshooting are essential. Through systematic maintenance and timely troubleshooting, the service life of the equipment can be extended, the cutting quality can be improved, and downtime can be reduced.
Regular Maintenance Practices
Regular maintenance is the basis for maintaining efficient operation of the laser cutting machine. Maintenance includes:
- Clean the filter: The filter in the gas supply system is responsible for removing impurities and moisture from the gas and keeping the gas pure. It is recommended to clean or replace the filter regularly every month to ensure that the gas flow is unobstructed. Dirty filters will cause insufficient gas flow, which will affect the cutting quality.
- Check the gas pipeline: Regularly check the connection and sealing status of the gas pipeline to ensure that there is no gas leakage. You can use a gas leak detector to check and repair or replace damaged pipelines in time to prevent gas leakage from causing safety hazards.
- Maintain the compressor and dryer: Regularly lubricate and maintain the compressor to ensure that it operates properly. At the same time, check the working status of the dryer to ensure that it can effectively remove moisture from the gas to prevent moisture from affecting the cutting effect.
- Adjust and calibrate the laser cutting machine: Regularly check the optical path system, focusing lens, and reflector of the laser cutting machine to ensure that they are clean and intact. Calibrate the equipment to ensure that the energy and focal position of the laser beam meet the cutting requirements.
Common Problems and Solutions
When using a CO2 laser cutting machine, you may encounter some common problems. Here are the solutions:
Insufficient Gas Flow
- Problem analysis: Insufficient gas flow may be caused by filter blockage, gas supply system failure or gas pipeline leakage.
- Solution: First check whether the gas supply is normal and confirm whether the pressure of the gas bottle is sufficient. Then, clean or replace the filter to ensure that the filter is clean and unobstructed. Finally, check the connection and sealing status of the gas pipeline and repair any leaks in time.
Poor Cutting Quality
- Problem analysis: Poor cutting quality may be related to the settings of gas type, pressure, or flow, or it may be related to the characteristics of the material and the state of the machine.
- Solution: According to the requirements of the cutting material, adjust the gas type (such as oxygen, nitrogen, or air) appropriately to ensure that the appropriate auxiliary gas is selected. At the same time, check and adjust the gas pressure and flow to keep it within the recommended range. In addition, ensure that the optical system of the laser equipment is clean, and adjust the cutting speed and laser power according to the characteristics of the material.
Importance of Professional Inspection
While regular maintenance and troubleshooting can resolve many common issues, regular inspections by a professional technician are essential. Specific reasons include:
- Comprehensive inspection of potential problems: Professional technicians can conduct a comprehensive inspection of the laser cutting machine and promptly identify potential faults and safety hazards. They can use professional equipment and experience to identify details that operators may overlook.
- Improve equipment reliability: Regular professional inspections, can ensure that each component of the equipment operates in the best condition, reduce the probability of sudden failures, and improve the overall reliability and stability of the equipment.
- Extend the service life of the equipment: Regular professional inspections and maintenance can not only deal with problems in a timely manner but also effectively extend the service life of the equipment and reduce long-term operating costs.
Maintenance and troubleshooting are important parts of ensuring the normal operation of CO2 laser-cutting machines. Through regular cleaning and inspection, timely resolution of common problems, and seeking the help of professional technicians, companies can improve the efficiency and safety of equipment, ensure cutting quality, and thus enhance production capacity and market competitiveness.
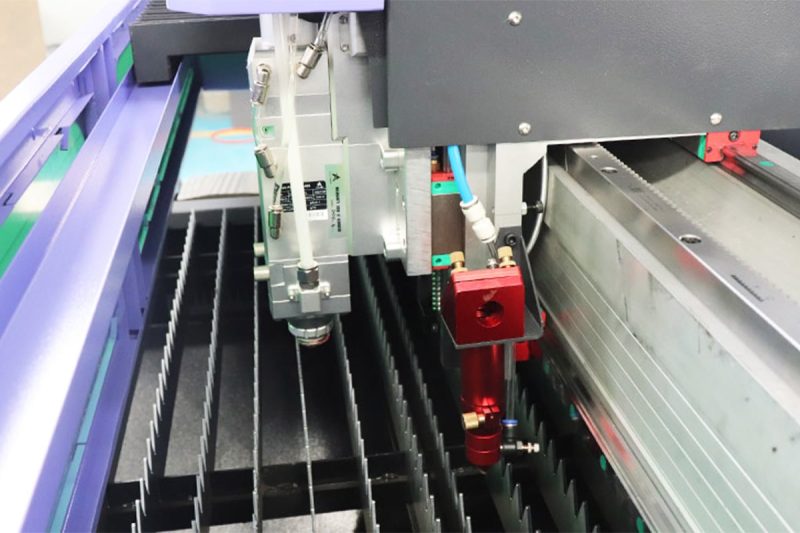
Summarize
The gas supply system of the CO2 laser cutting machine plays a vital role in ensuring cutting quality and efficiency. The gas supply system not only provides the necessary gas for the laser cutting process but also plays a key role in improving cutting accuracy and reducing material loss. Understanding its basic composition, working principle, and gas supply requirements can not only help optimize the cutting process, but also improve the safety and reliability of the equipment.
Basic Composition
The gas supply system is mainly composed of a compressor, a dryer, a filter, and a distribution system. The compressor is responsible for providing the pressure and flow of the gas to ensure the stability of the gas supply; the dryer removes moisture from the gas to avoid affecting the effect of the laser during the cutting process; the filter removes impurities from the gas to ensure the purity of the gas; the distribution system effectively delivers the gas to the cutting head and other key components.
At AccTek, our CO2 laser cutting machine is equipped with an efficient gas supply system to ensure that each cutting can achieve the best results and help users achieve higher production efficiency.
How It Works
The working principle of the air supply system involves multiple links. First, the laser source generates a laser beam through gas excitation, and the laser beam is focused and irradiated onto the material surface. At the same time, the auxiliary gas provided by the gas supply system plays a key role in the cutting process. Different types of assist gases (such as oxygen, nitrogen, and compressed air) can significantly affect the speed and quality of the cut.
Choosing the appropriate auxiliary gas can improve the cutting effect. For example, oxygen helps to enhance the cutting speed of metallic materials, while nitrogen is suitable for preventing oxidation of non-metallic materials. AccTek’s laser cutting machines flexibly support different types of auxiliary gases to meet various cutting needs and provide customers with better services.
Gas Supply Requirements
To ensure the high efficiency of laser cutting, the gas supply system has strict requirements on the purity, pressure, and flow of gas. High-purity gas can effectively reduce the interference of impurities in the reaction, thereby improving the cutting quality. Appropriate gas pressure and flow are the keys to ensuring the efficient operation of the laser cutting machine. Too low pressure and flow will lead to incomplete cutting, while too high pressure and flow may damage the material.
At AccTek, we provide users with detailed gas supply requirements guidelines to help them select the appropriate gas configuration and adjust the corresponding pressure and flow to ensure that the equipment is always in the best cutting state.
Regular Maintenance and Professional Inspections
Through regular maintenance and professional inspections, we ensure that the equipment is always in the best condition and provide reliable production support. Regularly cleaning filters, checking gas pipelines, and maintaining compressors and dryers can not only improve cutting quality but also prevent potential failures.
Regular inspections by professional technicians can timely discover potential problems with the equipment and avoid affecting production efficiency. AccTek advocates regular equipment inspection and maintenance services to ensure that customers’ laser-cutting machines are kept in the best condition, reduce the occurrence of failures, and improve production efficiency.
In short, the gas supply system of the CO2 laser cutting machine plays a core role in cutting quality and efficiency. By understanding its basic composition and working principles, users can better optimize the cutting process and ensure the safety and reliability of the equipment. At AccTek, we are committed to providing high-performance laser cutting solutions, and through regular maintenance and professional inspections, we ensure that customers’ equipment is always in the best working condition and provide strong production support. By choosing us, you can not only get high-quality equipment but also enjoy excellent customer service and technical support.
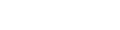
Contact information
- [email protected]
- [email protected]
- +86-19963414011
- No. 3 Zone A, Lunzhen Industrial Zone,Yucheng City , Shandong Province.
Get Laser Solutions