
How Hot Is Laser Welding?
Laser welding is an efficient and precise welding technology. Its core lies in using a high-intensity laser beam to locally melt the material and achieve a strong connection through rapid cooling. Unlike traditional welding methods, the energy of laser welding is concentrated and controllable, and its operating temperature is extremely high, which can easily reach 6000℃ or even higher, which is enough to melt most metals and alloys. Temperature is a critical parameter in the laser welding process. It not only determines the melting speed and welding depth of the material but also affects the strength and surface finish of the welded joint. Due to the highly concentrated heat input of the laser beam, laser welding has obvious advantages in speed, precision, and heat-affected zone (HAZ) control, which makes it the preferred process in many fields.
Temperature control in laser welding also directly affects the suitability and final performance of the process. If the welding temperature is too high, the material may be overburned or welding defects may appear, such as pores and cracks; if the temperature is too low, the material may not be completely melted, resulting in problems such as incomplete welding penetration. In addition, various factors such as the type of welding material, laser power, beam focus, and welding speed will have a significant impact on the welding temperature. In actual operations, engineers usually optimize the welding effect by adjusting process parameters based on the melting point and thermal conductivity of the material. It is precisely because of this precise control of temperature that laser welding can be widely used in high-demand industries such as automobile manufacturing, aerospace, and medical equipment, and has demonstrated its superior performance and adaptability.
Table of Contents
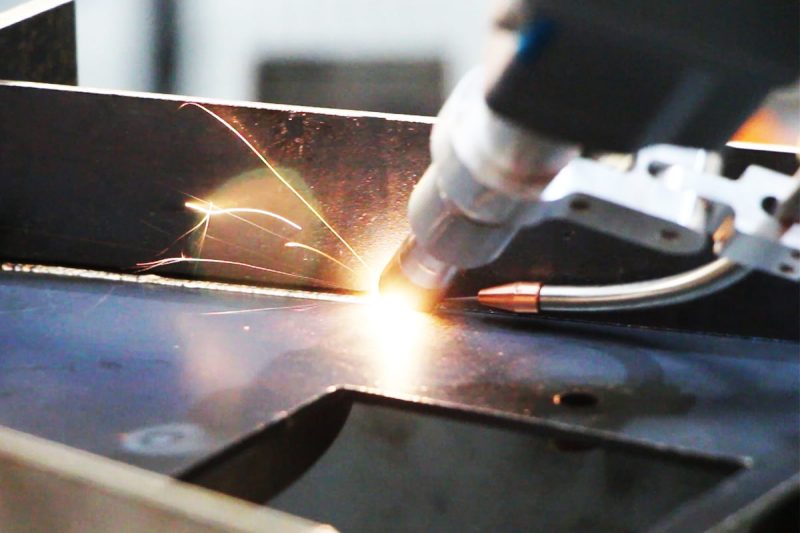
Understanding Laser Welding Temperatures
The Principle of High Temperature Involved in Laser Welding
material through the high energy density of the focused laser beam to form a strong welded joint. During the laser welding process, the focal temperature of the laser beam can be very high, usually exceeding 6000℃, and even up to 10000℃ in some cases. This high temperature is enough to melt almost all common metal materials, such as stainless steel, aluminum alloy, copper, and titanium alloy. The high-temperature characteristics of laser welding enable it to complete the melting and welding process in a short time, and due to the concentrated heat input, the heat-affected zone (HAZ) can be minimized, thereby reducing the risk of thermal deformation and residual stress.
Compared with traditional welding processes, laser welding has the following unique advantages:
- High energy density: The energy in the focus area of laser welding is concentrated, which can quickly melt the metal and is suitable for precision welding.
- High control accuracy: Laser power, beam focus, and other parameters can be accurately adjusted to provide highly controllable temperature distribution.
- Rapid heating: Laser welding can quickly melt metal in milliseconds, significantly increasing welding speeds.
Comparison of Laser Welding Temperature with Other Welding Processes
Compared with other traditional welding processes, laser welding has different temperature characteristics and heat-affected modes. The following is a temperature comparison between laser welding, arc welding, and resistance welding:
Laser Welding
- Temperature range: usually between 6000℃ and 10000℃, the temperature in the focal area can be very high.
- Temperature distribution: The temperature of laser welding is concentrated in the welding area, and almost no heat diffuses to the surrounding materials.
- Features: Due to the highly concentrated temperature and precise control, laser welding can complete melting in a very short time, with fast welding speed and a small heat-affected zone. It is suitable for scenes with extremely high requirements for welding accuracy and quality.
Arc Welding
- Temperature range: generally between 3500℃ and 6000℃, depending on the arc type and welding conditions.
- Temperature distribution: Arc welding has a wide temperature distribution, and the temperature will spread over a larger area, which may lead to a larger heat-affected zone.
- Features: Arc welding is usually used for welding thicker materials. Although the temperature is higher, it may cause more thermal deformation and stress due to the large heat input, and the control accuracy is relatively poor.
Resistance Welding
- Temperature range: The temperature of resistance welding is usually below 3000℃ and concentrated at the contact point.
- Temperature distribution: The temperature of resistance welding is mainly concentrated where the two electrodes contact the material, forming local heating.
- Features: Resistance welding is suitable for welding thin plate materials. The low temperature and concentrated welding area help avoid overheating, but its application range is narrow.
Laser welding is suitable for high-precision welding tasks that require fine control of welding temperature and small heat-affected zone due to its high temperature and concentrated heat input characteristics. Compared with traditional arc welding and resistance welding processes, laser welding provides higher energy density, a faster welding process, and a smaller heat-affected zone, making it widely used in aerospace, automobile manufacturing, electronic equipment, and other fields. The differences in temperature control and welding quality of different welding processes also make them have their advantages and limitations in different materials and industrial needs.
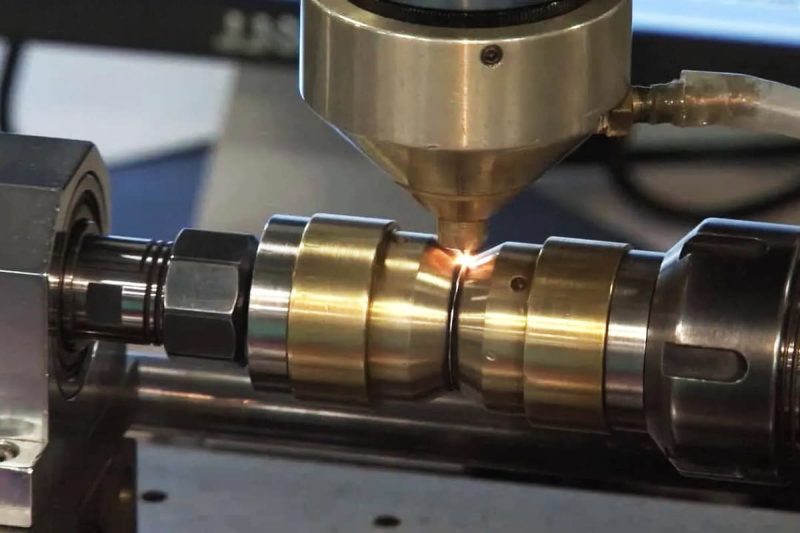
Factors Affecting Welding Temperature
Laser welding is a precision welding technology, and its welding temperature is affected by many factors. These factors are directly related to the welding effect, welding quality, and the performance of the final product. Next, we will discuss in detail how several major factors affect the temperature of laser welding.
Laser Power
The output power of the laser is one of the most critical factors affecting the laser welding temperature. The higher the power, the greater the energy emitted by the laser beam and the thicker the material that can be melted, but it may also cause problems such as overburning and thermal damage.
- High-power laser: used for thicker materials, can quickly provide enough energy to melt the material. The power of industrial-grade laser welding machines is usually between 500W and 6000W. According to different needs, the power can be adjusted to adapt to the thickness and type of different materials. Higher-power laser welding is suitable for thick materials and large-scale production, but it is also more likely to cause heat accumulation, resulting in thermal deformation or uneven welding.
- Low-power laser: suitable for thin materials, capable of fine welding with controlled heat input. Low-power laser welding can reduce the thermal impact on the material, but if the power is too low, it may not fully melt the material, resulting in insufficient strength of the weld joint.
Beam Focus
The focus of the beam is one of the key factors that determine the temperature distribution of laser welding. The degree of focus of the laser beam directly affects the energy density, which in turn determines the temperature during the welding process.
- Precise focus: The more precisely the laser beam is focused, the higher the energy density and temperature, which can quickly melt the material and complete the welding. Precise focusing can ensure uniform heat distribution during welding and good welding results.
- Focus offset: If the laser beam focus is offset or the focus is not precise enough, the energy distribution is uneven, and the temperature of the welding area will also be uneven, which may lead to poor strength of the welded joint or even quality problems such as cold welding and cracks.
Material Type
The thermal conductivity properties and melting point differences of different materials determine the required welding temperature. The thermal conductivity, melting point, and reflectivity of the material can significantly affect the results of laser welding.
- Thermal conductivity: Materials with high thermal conductivity (such as copper and aluminum) can quickly diffuse heat from the welding area to the surrounding area, which means that higher temperatures are required to melt these materials. In contrast, materials with low thermal conductivity (such as stainless steel and titanium) are more likely to accumulate heat in a local area, so it is relatively easy to reach the required welding temperature.
- Melting point: The difference in melting points of different materials also directly affects the welding temperature. For example, the melting point of stainless steel is 1450℃, while the melting point of aluminum alloy is lower, about 660℃. This means that welding stainless steel requires higher temperatures and stronger laser power while welding aluminum alloys can use lower temperatures.
Welding Speed
Welding speed is another important temperature-influencing factor. Welding speed determines the heat input of the material per unit time, which in turn affects the welding temperature.
- Higher welding speed: When the welding speed is faster, the laser beam passes through the weld for a shorter time and the heat input to the material is reduced. This will result in a lower temperature in the weld zone and less heat accumulation, which helps to reduce the heat affected zone, deformation and residual stress. However, welding speeds that are too fast may result in insufficient melting of the weld metal, leading to weld quality problems.
- Lower welding speed: Slower welding speeds allow the laser beam to stay in the weld zone for a longer time, allowing heat to accumulate, thereby increasing the temperature of the weld zone. This helps with welding thicker materials, but it may also lead to overheating, deformation, and expansion of the heat-affected zone.
The laser welding temperature is affected by many factors, including laser power, beam focus, material type, and welding speed. Each factor will affect the welding temperature to varying degrees, thus determining the effect and quality of welding. In actual operation, welding parameters need to be optimized according to material type, thickness, and process requirements to ensure a smooth welding process and obtain high-quality welded joints.
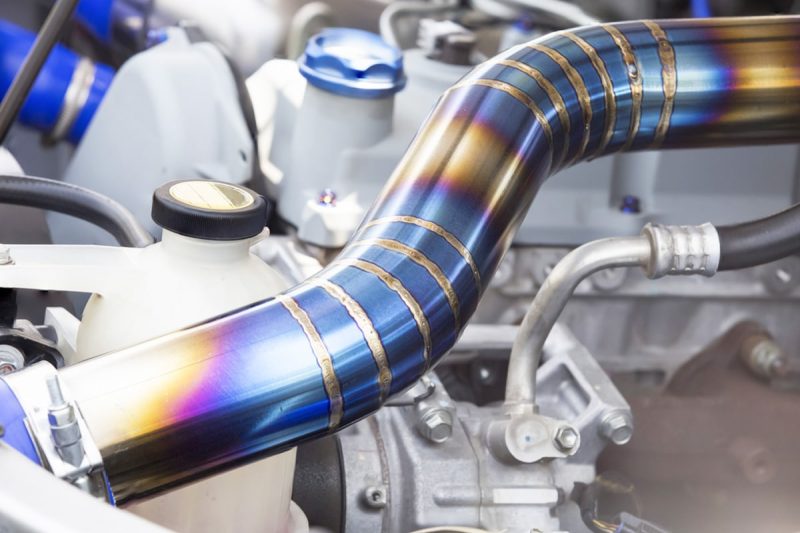
Temperature Range of Laser Welding
Laser welding is a high-precision welding process that heats the material with a concentrated energy laser beam. During the welding process, the temperature distribution range is wide, from the melting point of the material to the peak temperature of the weld zone. The control and management of temperature is critical to the quality of the weld. The following will discuss in detail the various aspects of temperature in laser welding, including the material melting point, the heat-affected zone (HAZ) temperature, and the peak temperature of the weld pool.
Material Melting Point
During the laser welding process, the laser beam must heat the material to above its melting point to melt the material and form a welded joint. Different materials have different melting points, which directly affects the temperature required for laser welding. The following are the melting point ranges of common materials:
- Steel: The melting point of steel is usually between 1200℃ and 1500℃. The melting point varies depending on the type of steel (such as carbon steel, alloy steel, etc.). The melting point of carbon steel is relatively low, while the melting points of alloy steel and stainless steel may be higher.
- Aluminum: The melting point of aluminum is relatively low, generally between 600℃ and 700℃. Due to its lower melting point, aluminum is easier to laser weld, but it is also more susceptible to overheating, resulting in thermal deformation.
- Titanium alloy: The melting point of titanium alloy is about 1660℃, which is higher than that of steel and aluminum. Therefore, when welding titanium alloy, the laser temperature needs to be controlled in a higher range to ensure melting and welding quality.
These melting point ranges determine the selection and adjustment of laser power and also impose requirements on thermal management during the welding process.
Heat Affected Zone (HAZ) Temperature
The heat-affected zone (HAZ) refers to the area where the material temperature rises due to the laser beam heating during the welding process but does not reach the melting point. In this area, although melting does not occur, the microstructure of the material will change due to the increase in temperature, which may affect the mechanical properties of the material.
- Temperature range: The temperature of the heat affected zone is usually lower than the melting point of the material, but sufficient to cause changes in the lattice structure of the material, usually ranging from 500°C to 1000° For some high-strength materials, these temperatures are sufficient to cause hardness changes and may even cause embrittlement.
- Influencing factors: The temperature of the heat affected zone is affected by many factors, including laser power, beam focus, welding speed, and thermal conductivity of the material. The greater the laser power and the slower the welding speed, the larger the heat affected zone and the higher the temperature.
Controlling the HAZ temperature is crucial to ensuring the quality of the welded joint. Excessive HAZ temperature may lead to a decrease in material performance and even affect the overall weld strength and fatigue life.
Peak Weld Pool Temperature
The weld pool is the area of liquid metal formed by the molten metal during the laser welding process. The peak temperature of the weld pool is the most concentrated temperature during the welding process and is usually located in the center of the weld zone. The temperature of the weld pool is usually between 3000℃ and 6000℃, which is enough to melt most metals and is the key to forming a strong weld joint.
- Weld pool temperature range: The temperature of the weld pool can vary depending on the material and laser parameters. For high melting point materials (such as titanium alloys, stainless steel, etc.), the temperature of the weld pool can reach over 3000°C, while for low melting point materials (such as aluminum alloys), the temperature is relatively low, usually between 3000°C and 4500°
- Effect of temperature on welding quality: The weld pool temperature directly determines the depth and width of the molten pool, as well as the shape of the final weld joint. Too high a weld pool temperature may cause the molten pool to be too deep, increasing the risk of thermal deformation, while too low a temperature may result in insufficient welding and insufficient joint strength.
During laser welding, the temperature ranges from the melting point of the material to the peak temperature of the weld pool. The melting point determines the minimum temperature that the laser needs to reach, while the temperature of the heat-affected zone and the peak temperature of the weld pool affect the depth of the weld, the strength of the joint, and the final properties of the material. Different materials, welding parameters, and process settings will affect the temperature distribution during welding, so in actual operation, the temperature needs to be precisely controlled to ensure the quality of the weld and the reliability of the welded joint.
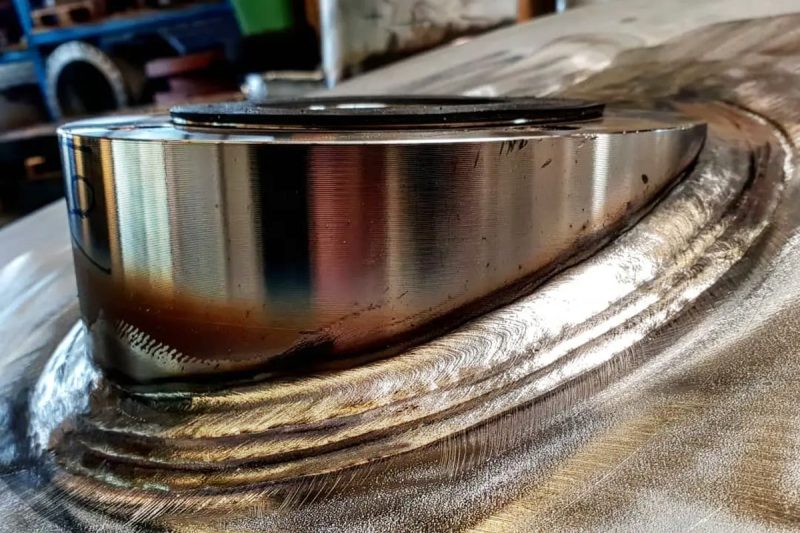
Effect of Temperature on Welding Quality and Performance
Temperature is a critical factor in the laser welding process, affecting weld quality, material properties, and the performance of the final workpiece. Laser welding requires that the material be heated to a sufficient temperature so that it melts and combines, but temperatures that are too high or too low will have a negative impact on weld quality and material properties. The following discusses in detail the specific effects of temperature on weld quality and performance.
Material Properties
During the welding process, temperature changes will cause changes in the microstructure of the material, which will directly affect the mechanical properties of the welded joint.
- Grain refinement or coarsening: During laser welding, the material undergoes rapid heating and cooling, and temperature changes may lead to grain refinement or coarsening. The size of the grains directly affects the strength and toughness of the material. Too high a temperature may lead to grain coarsening, reducing the strength of the welded joint. Conversely, lower welding temperatures may lead to too many fine grains, which may weaken the toughness of the welded area.
- Phase change: Some materials undergo phase changes during heating, such as steel changing from ferrite to austenite at high temperatures. This phase change may cause changes in the mechanical properties of the material. Different heat treatment processes (such as annealing, quenching) may also occur at different welding temperatures, affecting the hardness, tensile strength, and fatigue resistance of the material.
Welding Quality
Temperature has a direct impact on the quality of welded joints, especially in terms of joint integrity and stability.
- Too high temperature: Too high temperature may cause a series of welding defects, including pores, cracks, overburning, etc. At high temperatures, the metal molten pool is too large, and gas can easily enter the molten pool, resulting in the formation of pores. In addition, high temperatures may also cause oxidation or brittle phases on the surface of the material, increasing the risk of welding cracks. Too high temperature may also cause overburning of the material, causing the welding area to become over-molten, and ultimately resulting in reduced strength of the joint.
- Too low temperature: When the welding temperature is too low, the metal cannot be completely melted, which may result in incomplete penetration. Incomplete penetration refers to the fact that the molten part of the weld joint is not completely combined, resulting in a decrease in joint strength. In addition, lower welding temperatures may also cause uneven surfaces of welded joints, cold cracks, or reduced tensile strength.
Residual Stress and Deformation
In laser welding, due to the influence of high temperature, thermal expansion, and contraction will occur in the welding area, which will cause residual stress and thermal deformation.
- Residual stress: During high-temperature welding, the metal will experience expansion and contraction, and the thermal expansion of the welded area is usually greater than that of the unwelded area, which will produce residual stress. Excessive residual stress may cause the material to deform during use, and even cause the joint to rupture or fatigue failure. The presence of residual stress may also cause crack propagation in the welded part, affecting the reliability of the overall structure.
- Thermal deformation: The high temperature of laser welding may cause thermal deformation of the material, especially in thin materials. The degree of thermal deformation depends on factors such as welding temperature, thermal expansion coefficient of the material, and welding speed. Thermal deformation may cause inaccurate dimensions of parts, thereby affecting the assembly and function of parts. Especially in some precision manufacturing industries, such as aerospace and electronics manufacturing, excessive thermal deformation may cause parts to fail to meet tolerance requirements.
Post-Weld Heat Treatment and Correction
To control and reduce the residual stress and thermal deformation generated during welding, appropriate heat treatment or correction is usually required after welding.
- Heat treatment: After welding, materials often need to be annealed, normalized or quenched to eliminate residual stress, optimize the microstructure of the material, and improve mechanical properties. By controlling the heating and cooling process, the adverse effects caused by excessively high or low temperatures can be effectively reduced.
- Correction: For larger thermal deformations, mechanical correction or the use of laser leveling technology is usually required to correct the shape and size deviations of the workpiece. This helps to restore the original shape of the welded part and ensure its accuracy and stability during use.
Temperature has a profound impact on the quality and performance of laser welding. From the microstructural changes of the material to the strength and stability of the welded joint, to the residual stress and thermal deformation during the welding process, temperature control is the key to ensure welding quality. Too high or too low temperature may cause welding defects and affect the performance and reliability of the final product. Therefore, in the laser welding process, precise temperature control and reasonable management of welding parameters are essential to obtain high-quality welded joints.
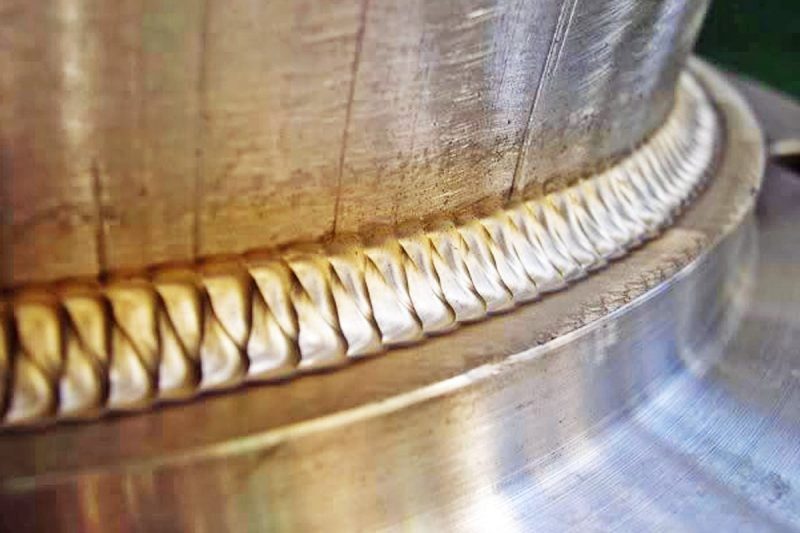
Controlling Laser Welding Temperature
To ensure high-quality welding results, it is essential to accurately control the temperature of laser welding. The welding temperature directly affects the strength of the welded joint, the microstructure of the welded area, and the performance of the final product. The following are some commonly used strategies for controlling temperature, which help optimize the welding process and ensure the stability and consistency of welding quality.
Adjust Process Parameters
During the welding process, process parameters such as laser power, welding speed, and beam mode are key factors affecting the welding temperature. Accurately adjusting these parameters helps to achieve the desired temperature control.
- Laser power: Laser power directly determines the amount of energy input, which affects the temperature of the molten pool. Higher power is suitable for welding thick materials but may cause overburning or thermal damage. Lower power is suitable for welding thin materials but may cause incomplete penetration. The power should be adjusted according to the thickness of the material and the welding requirements.
- Welding speed: The welding speed is inversely proportional to the heat input. Faster welding speeds can reduce heat input and thus lower welding temperatures, which is suitable for thin materials or situations where less heat is required. Slower welding speeds can provide more heat input, which is suitable for thick materials or situations where stronger welds are required.
- Beam mode: The focusing mode of the laser beam (such as circular, rectangular or linear mode) affects the energy density of the beam and thus the temperature distribution. Accurate beam focusing can concentrate the laser energy into a small area and heat the material quickly. And the extended beam mode can evenly distribute the heat and reduce the risk of local overheating.
Preheating and Postheating
Certain materials are very sensitive to heat, especially materials such as aluminum alloys and high-strength steel. Strategies to control heat input include preheating and post-heating, which can help reduce cracks, thermal deformation, and residual stresses.
- Preheating: Preheating refers to heating the material to a certain temperature before welding. For low melting point materials such as aluminum alloys and magnesium alloys, preheating can reduce the thermal stress and crack risk caused by rapid cooling of the material during welding. Preheating can also reduce thermal shock during welding and avoid cracks caused by excessive temperature differences.
- Post-heating: Heating (or annealing) after welding helps to reduce residual stress in the welding area, reduce the risk of thermal deformation, and improve the mechanical properties of the welded joint. Post-heating is usually achieved by controlling the cooling rate after welding, especially in the welding of high-strength steel or other heat-sensitive materials.
Monitoring and Feedback System
Modern laser welding equipment is usually equipped with high-precision temperature monitoring systems, which can monitor the welding temperature in real-time and adjust the process parameters according to real-time data. These systems not only improve the accuracy of the welding process but also ensure the consistency of welding quality.
- Temperature sensor: The temperature sensor can measure the temperature of the welding area in real time and feedback on the temperature change information to the control system. Commonly used sensors include infrared temperature sensors and laser spectrum sensors, which can monitor the temperature of the welding area without contact.
- Automatic feedback adjustment system: The temperature monitoring system can be linked with the laser power control system and the welding speed control system to dynamically adjust the laser power and welding speed according to the actual welding temperature to keep the temperature within the required range. Such an automatic feedback system not only improves the stability of welding but also reduces the error of human operation.
Other Temperature Control Strategies
In addition to the above methods, other technologies can be combined in laser welding to further control the temperature.
- Laser pulse control: By adjusting the frequency and duration of the laser pulse, the heat input can be precisely controlled. Short pulses can achieve lower temperature input and are suitable for heat-sensitive materials, while long pulses are suitable for welding tasks that require higher temperatures.
- Multi-beam welding: Using multiple laser beams working in parallel during the welding process helps to evenly distribute the heat in the welding area, avoiding local overheating, thereby improving the welding quality.
Laser welding temperature can be effectively controlled by precisely adjusting process parameters, preheating and post-heating, effective cooling strategies, and advanced temperature monitoring and feedback systems. These controls help ensure that the temperature during welding remains within the optimal range, resulting in high-quality welded joints, reduced risk of defects, and optimized performance of the final product.
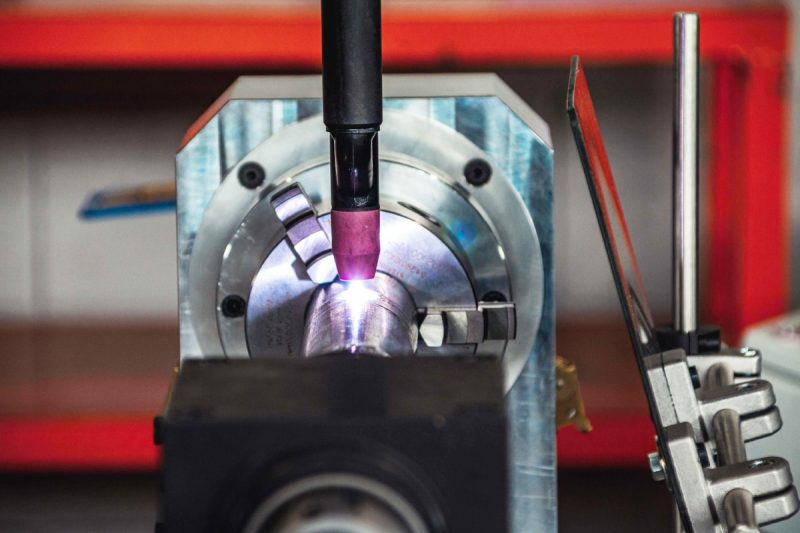
Temperature Considerations in Specific Applications
Laser welding technology is widely used in many industries, and there are significant differences in welding temperature requirements in different fields. When every industry uses laser welding, it is necessary to accurately control the welding temperature based on material properties, welding goals, and quality requirements. Here are some temperature control considerations for major industries.
Automotive Industry
In the automotive industry, laser welding is widely used in the welding of body structural parts, such as doors, roofs, chassis, etc. This industry has very high requirements for welding quality and efficiency, so temperature control is particularly critical.
- Welding strength: The body structure needs to have high welding strength to ensure driving safety. Therefore, the welding temperature needs to be high enough to ensure good fusion of the welding area and meet the high strength requirements. However, too high a temperature may lead to brittleness of the welded joint, so the heat input needs to be precisely controlled.
- Efficiency and production rate: The automotive manufacturing industry has high requirements for production speed. The temperature control during welding must not only ensure welding quality, but also take into account welding efficiency. Therefore, controlling the appropriate welding temperature can help increase the speed of the production line while maintaining high-quality welded joints.
- The heat-affected zone (HAZ): The body material is mostly high-strength steel or aluminum alloy, and the control of the heat-affected zone is particularly important. Excessive temperature will cause the heat-affected zone to soften and affect the mechanical properties of the material. Therefore, it is necessary to avoid excessively high welding temperatures to prevent material performance degradation.
Aerospace Industry
The aerospace industry has extremely strict requirements on the performance of materials, and temperature control during welding is particularly critical. Especially in the manufacture of aircraft structural parts and engine components, too high or too low welding temperature will have a significant impact on the performance of the material.
- Heat-affected zone control: Materials used in the aerospace industry, such as titanium alloys and high-temperature alloys, generally have high strength and corrosion resistance. During the welding process, the heat input must be precisely controlled to avoid an excessively large heat-affected zone (HAZ). Overheating can cause the material’s strength to decrease and even cause cracks, affecting the overall performance of the structural parts.
- Temperature accuracy: High-precision temperature control is a core requirement of the aerospace industry. Since the material is very sensitive to temperature changes, low-power lasers need to be used during welding to reduce heat input and ensure that the welded joint is not affected too much.
- Welding quality: In the aerospace field, welding quality is directly related to flight safety. Therefore, it is crucial to ensure that the temperature during welding is always kept within the optimal range to avoid uneven heating or overheating.
Electronics Manufacturing
In the field of electronics manufacturing, laser welding is used to connect small precision parts such as microcircuits, connectors, and components. Since these components are small and very sensitive to heat, temperature control is particularly important.
- Risk of overheating: The components and circuits of electronic assemblies are very sensitive to thermal rise. Excessive welding temperature may cause component damage or performance degradation, such as damage to the circuit board or welding failure of the component. Therefore, lower laser power needs to be used during welding to reduce heat input to avoid overheating.
- Use of low-power lasers: To reduce thermal damage to components, the electronics manufacturing industry usually uses low-power lasers and precisely controls the focus and welding time of the laser beam. Such low-power welding methods can achieve high-quality connections without damaging sensitive electronic components.
- Temperature rise monitoring: In order to ensure accurate temperature control during welding, the electronics manufacturing industry usually uses a temperature monitoring system to provide real-time feedback on the temperature during welding. By monitoring the temperature rise, the laser power or welding speed is adjusted to ensure that the welding temperature is always within a safe range.
Medical Device Manufacturing
In medical device manufacturing, precision welding technology is widely used to connect tiny parts, such as surgical tools, implants, and medical device housings. These applications have extremely high requirements for welding accuracy and non-contamination.
- Precision requirements: The welding parts of medical devices are usually very small and delicate, so precise temperature control is required. Excessive temperature may cause overheating of the welding area, thereby damaging the material or causing the joint to fail. To avoid this, laser welding usually uses low power and accurately controls the beam focus to ensure uniform temperature at the welding point.
- Pollution-free requirements: The welding of medical devices requires to be carried out in a clean environment to avoid pollutants affecting product quality. The welding temperature must be strictly controlled to avoid metal oxidation or harmful gases caused by excessive temperature, which affects the safety and hygiene of the final product.
- Moderate temperature: In the precision welding of medical devices, the welding temperature usually needs to be controlled in a moderate range, which must ensure that the material is fully melted, but not overheated to cause a decrease in material performance. Proper temperature control helps the strength and durability of the welded joint, ensuring the reliability and long-term performance of the final product.
Laser welding has unique temperature control requirements in different application fields. The automotive industry focuses on welding strength and efficiency, the aerospace industry emphasizes the control of heat-affected zones, electronic manufacturing focuses on low-temperature welding to protect sensitive components, and medical device manufacturing requires precision welding and non-contamination. The welding temperature control strategy of each industry needs to be precisely adjusted according to the specific material properties and welding goals to ensure the quality and performance of the product.
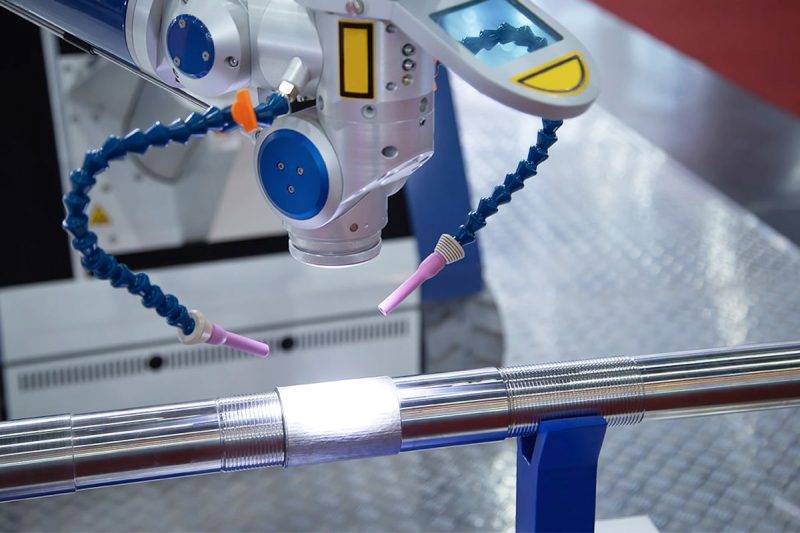
Summarize
Laser welding is a high-temperature, high-precision advanced process that is widely used in multiple industries, including automotive, aerospace, electronic manufacturing, and medical devices. The process uses a laser beam as a heat source with highly concentrated energy to quickly and efficiently melt materials and form a strong joint. The main advantages of laser welding are its high precision and high speed, which makes it widely used in many industries with strict requirements on welding quality. However, the success of laser welding depends not only on the output power of the laser beam and the material properties but also on the precise control of the temperature during the welding process. Too high or too low a temperature will hurt the quality of the welded joint, which may cause defects such as pores, cracks, overburning, and incomplete penetration. Therefore, temperature control is the core of ensuring welding quality. AccTek Laser’s laser welding machine, with its stable temperature control system, provides users with a more precise and reliable welding experience, helping them stand out in the industry competition.
In order to achieve high-quality laser welding, it is essential to optimize process parameters, select suitable equipment and implement a monitoring feedback system. By adjusting parameters such as laser power, welding speed and focus position, the heat input can be precisely controlled according to the characteristics of the material and welding requirements. In addition, modern laser welding equipment is usually equipped with a real-time monitoring system that can adjust parameters in time according to temperature changes during the welding process to ensure that the welding quality is always in the best state. With the continuous advancement of technology, the temperature control of laser welding will become more precise and can meet the needs of more and more high-end industries for welding quality and performance. In the future, as laser welding technology develops, it will provide more efficient and reliable welding solutions for more industries and promote the progress and innovation of the manufacturing industry.
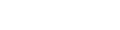
Contact information
- [email protected]
- [email protected]
- +86-19963414011
- No. 3 Zone A, Lunzhen Industrial Zone,Yucheng City , Shandong Province.
Get Laser Solutions