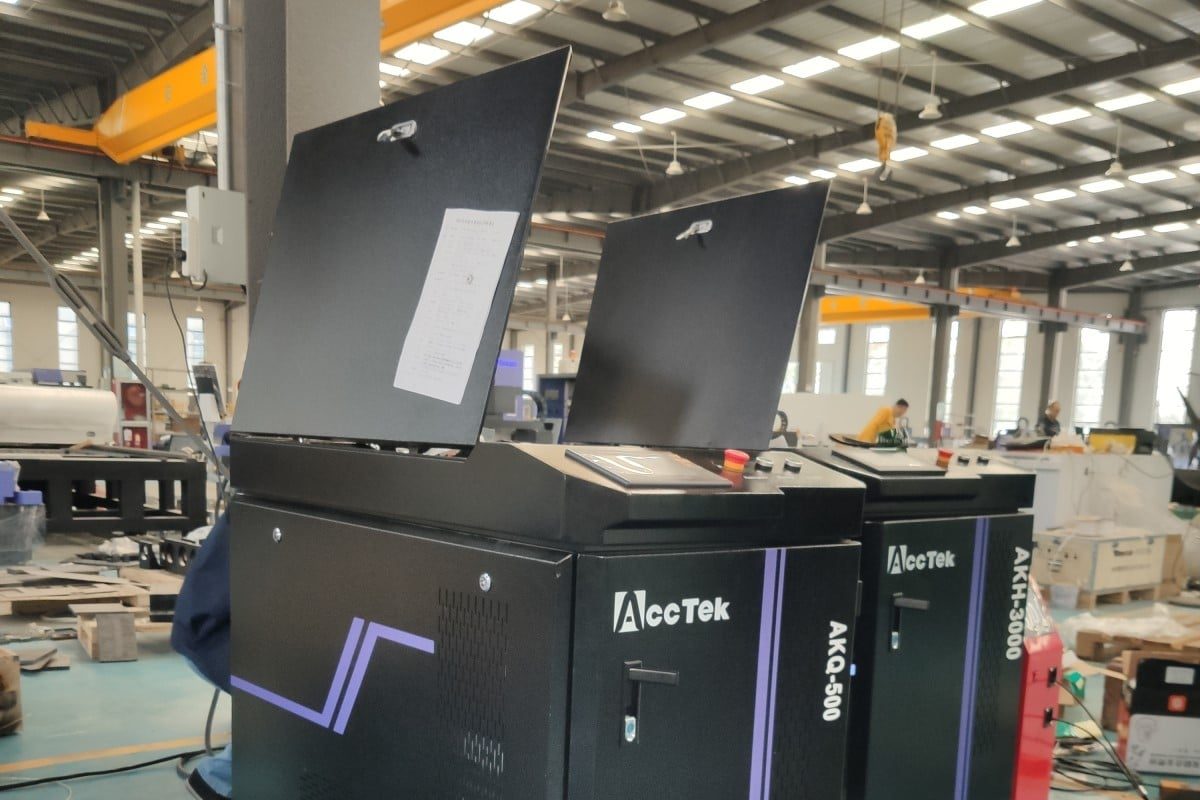
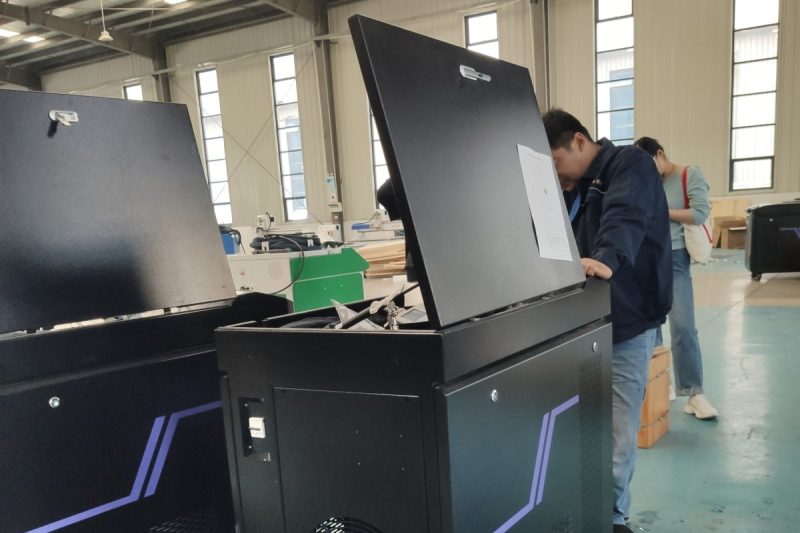
Learn the basics of laser cleaning
Laser cleaning process
Laser cleaning machine parts
A typical laser cleaning machine consists of several key components, including:
- Laser generator: This is the heart of the laser cleaning machine and generates a high-energy laser beam for cleaning. Different types of laser modalities are available, such as fiber laser generators, pulsed laser generators, and continuous wave (CW) laser generators.
- Scanner and optics: These components control the direction and focus of the laser beam, thereby determining the area that the laser cleans with each pass.
- Contaminant removal system: Laser cleaning machines are often equipped with an exhaust system to remove particles and contaminants emitted during the cleaning process.
- Cooling system: High-power laser generators generate heat, so a cooling system helps maintain optimal working conditions.
- Control unit: The user interface and control unit allow the operator to configure laser settings and monitor the cleaning process.
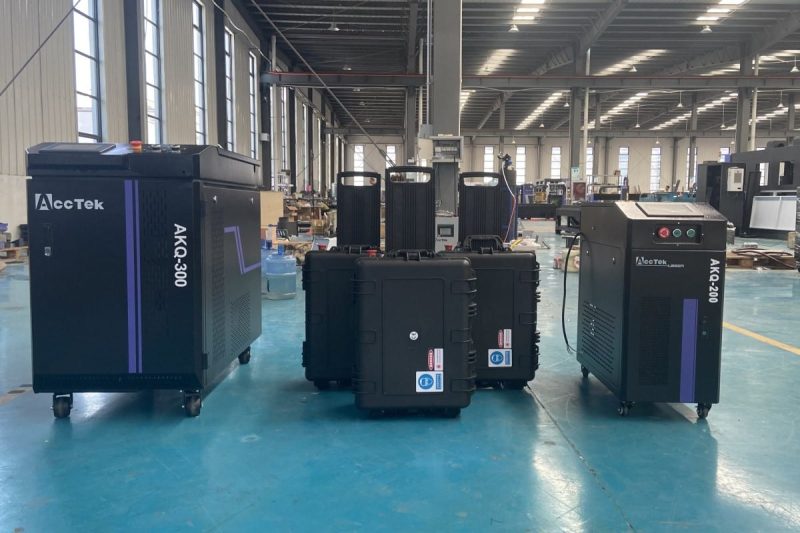
Noise generation in laser cleaning
Noise generation in laser cleaning is an important aspect to consider when utilizing laser technology for surface treatment and cleaning tasks. Understanding the sources and factors that generate noise during the operation of laser cleaning machines can help ensure safe production and improve production efficiency. Let’s take a closer look at the noise produced during laser cleaning.
- Laser ablation noise: One of the major sources of noise in laser cleaning is the laser ablation process. When high-intensity laser beams hit surfaces and interact with contaminants or coatings, they can cause them to vaporize, ablate, or explode. These rapid transitions generate shock waves and acoustic emissions that contribute to overall noise.
- Recoil noise: Recoil noise occurs when the momentum of expelled material causes vibrations and sound waves. When contaminants are forcibly removed from a surface, this recoil creates sound waves that affect the overall noise level of the cleaning process.
- Airborne particles and plume noise: The laser cleaning process produces airborne particles, gases, and smoke. The movement and interaction of these particles through the air can create noise, especially when they collide with each other or other surfaces near the cleaning area.
- Cooling system noise: Laser cleaning machines usually use a cooling system to maintain the optimal operating temperature of the laser generator. These systems produce noise, especially from the fans or pumps used to circulate the coolant. Cooling system noise may vary depending on its design and efficiency.
- Scanner and optics noise: The movement of scanners and optics within a laser cleaning machine can create mechanical noise. These components may produce vibrations and mechanical sounds as the laser beam is directed and focused on the target area.
- Exhaust and ventilation noise: Many laser cleaning machines are equipped with exhaust and ventilation systems to remove airborne contaminants and maintain a clean working environment. These systems create noise as air is circulated and exhausted.
- Control unit noise: Control units, including user interfaces and computer systems, can generate low levels of electronic noise. While this noise is usually not very loud, it can affect the overall soundscape near the machine.
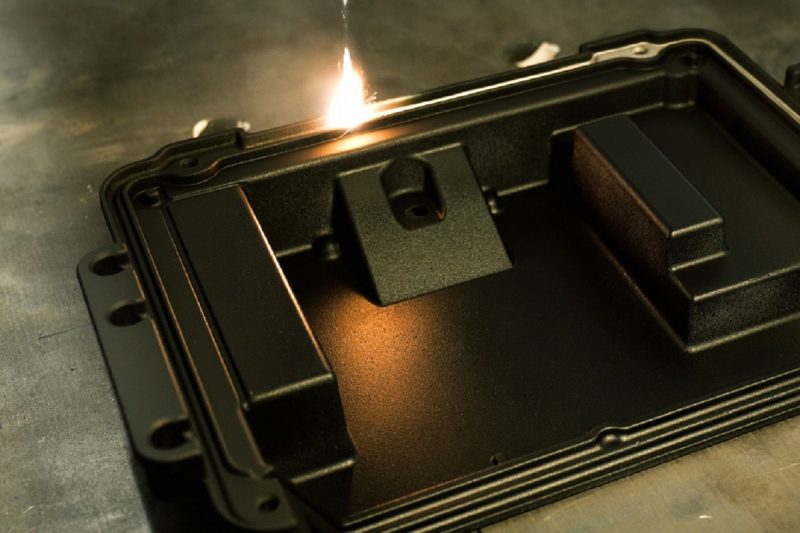
Factors affecting noise levels
The noise produced by laser cleaning machines is the result of the interaction of multiple complex factors, and understanding these factors can help manage and minimize noise in industrial environments. Several factors can affect noise levels:
- Laser power: One of the most important factors that affects the noise level of a laser cleaning machine is the laser power used. Higher-power laser generators, while more effective at removing contaminants, generally produce more noise due to the increased energy delivered to the surface. However, modern laser cleaning machines are designed and advanced to minimize noise as much as possible, even high-power laser cleaning machines.
- Material being cleaned: The properties of the material being cleaned play a vital role in determining the noise level during laser cleaning. Different materials react differently to laser cleaning and may produce varying levels of noise. Certain materials, especially metals, produce more noise when heated or ablated by a laser. In comparison, plastic and organic materials generally produce less noise.
- Machine design: The design and build quality of a laser cleaning machine play a key role in determining noise levels. Well-designed machines with noise-reduction features and high-quality components help reduce operating noise. When investing in a laser cleaning machine, it is recommended to choose one from a reputable manufacturer known for emphasizing noise reduction in their designs.
- Supporting equipment: In addition to the core components of the laser cleaning machine, auxiliary equipment such as exhaust systems and cooling mechanisms will also affect the overall noise level. While these components help maintain a safe and efficient cleaning process, they can also affect the noise produced, so they need to be considered when assessing the noise impact of a specific machine.
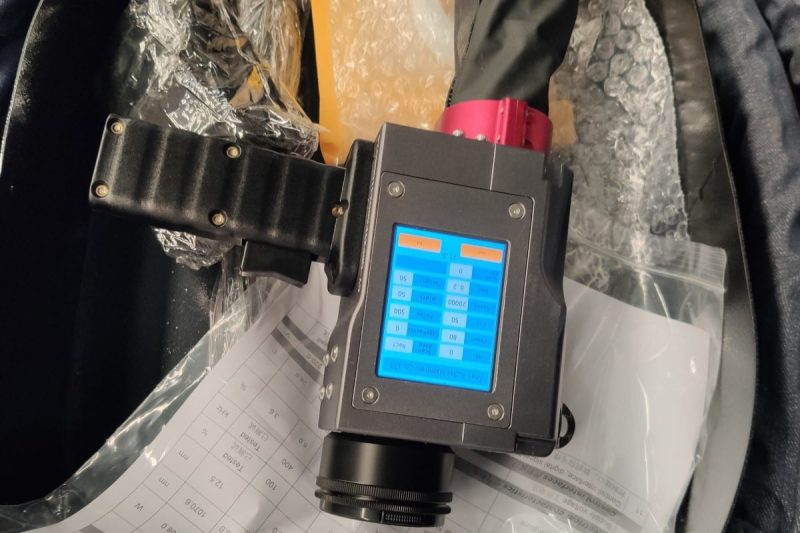
Noise measurement and assessment
To accurately quantify and compare the noise levels produced by different laser cleaning machines, sound pressure level (SPL) measurements are required. SPL measurements are usually expressed in decibels (dB). Lower dB values indicate quieter operation, while higher values correspond to a noisier process. Understanding how noise is measured can help evaluate the noise emissions from laser cleaning machines.
The noise level generated during the operation of a laser cleaning machine typically ranges from approximately 65 to 85 dB. To better understand this, here are some common noise level comparisons:
- Normal conversation: 60-70 decibels
- Urban traffic: 85-90 decibels
- Jackhammer: 100-120 dB
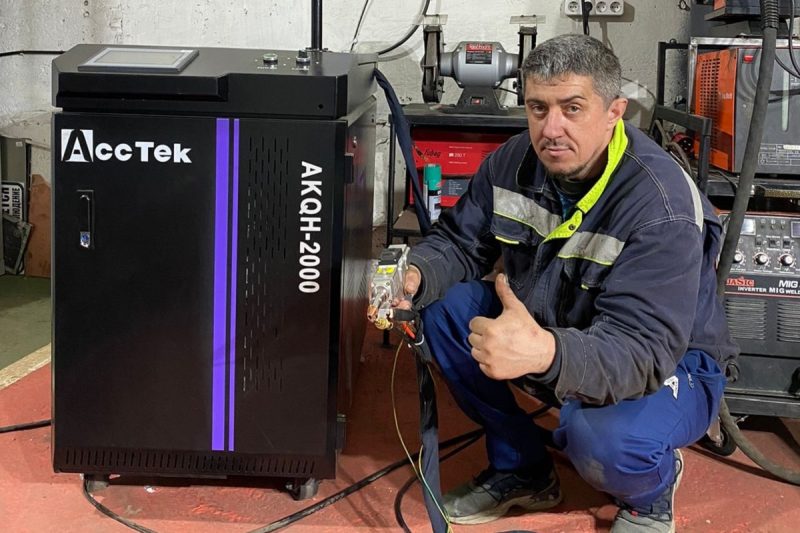
Noise reduction measures
If the noise generated by the laser cleaning machine remains a concern for the operator and the surrounding environment, several strategies and measures can be used to reduce noise levels:
- Choose a machine with noise reduction: Choose a laser cleaning machine that is designed with noise reduction in mind. Reputable manufacturers often invest in research and development to create quieter, more efficient machines. Look for features like improved case design, sound insulation, and advanced cooling systems for quieter operation.
- Provide hearing protection: Although laser cleaning machine noise levels are within acceptable limits, it is still prudent to equip operators with appropriate hearing protection, such as earplugs or earmuffs. This helps ensure their safety and comfort during long periods of machine operation.
- Optimize machine settings: Adjusting laser power and machine settings can help reduce noise levels while still achieving effective cleaning results. Reducing laser power or adjusting scan speed can make operation quieter, but may make cleaning less effective, so find the right balance between power and noise.
- Isolate the machine: Consider isolating the laser cleaning machine in a separate soundproof enclosure or room to contain noise. These enclosures are specifically designed to minimize the transmission of noise and can play a significant role in reducing the impact of noise on the surrounding environment.
- Maintenance and inspections: Frequent maintenance inspections will help ensure that all components of your laser cleaning machine are in optimal condition. Damaged or worn parts can cause increased noise levels, whereas a well-maintained machine is less likely to produce excessive noise.
- Proper operator training: Educating operators on machine operation and maintenance protocols can help reduce noise. A skilled operator can make adjustments and take precautions to maintain quieter operation.
- Implement proper exhaust and ventilation: Efficient exhaust and ventilation systems can help reduce noise by removing airborne contaminants and by-products produced during the laser cleaning process. A well-designed exhaust system also helps create a safer, more comfortable work environment.
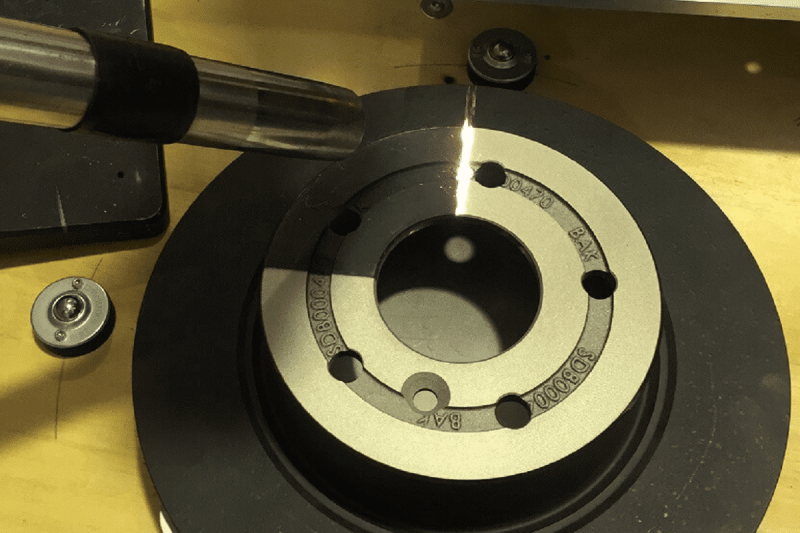
Practical applications of laser cleaning machines
To illustrate the practical applications and benefits of laser cleaning machines, let’s explore some industries and scenarios where they have proven to be of high value.
- Manufacturing and automotive: Laser cleaning machines are widely used in manufacturing plants and automotive facilities to remove rust, paint, and coatings from metal parts. This is particularly important in industries where surface treatment is a critical step in the production process. By using laser cleaning machines, manufacturers can increase the quality and longevity of their products while minimizing their impact on the environment.
- Cultural heritage restoration: Laser cleaning technology plays an important role in the restoration and preservation of historical and cultural relics. Fine art, sculptures, and architectural structures can be cleaned of contaminants and contaminants without damaging the original material. This application allows the restoration of cultural treasures with the utmost precision and care.
- Aerospace: In the aerospace industry, precision and safety are paramount. Laser cleaning machines are used to maintain the integrity of aircraft components by removing corrosion, paint, and coatings. The precision of laser cleaning ensures critical components remain in optimal condition while adhering to strict safety standards.
- Construction & renovation: In construction and remodeling projects, laser cleaning is a versatile and efficient method of restoring old buildings and structures. By removing layers of contaminants and aged coatings, the original appearance of architectural features can be restored. Additionally, laser cleaning reduces dust and debris, helping to maintain a clean work environment.
- Shipbuilding and marine: Marine applications benefit from laser cleaning machines that remove rust and dirt from hulls and equipment. This not only improves the vessel’s performance and fuel efficiency but also reduces environmental impact by preventing biofouling from spreading invasive species.
Summarize
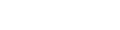
- [email protected]
- [email protected]
- +86-19963414011
- No. 3 Zone A, Lunzhen Industrial Zone,Yucheng City , Shandong Province.