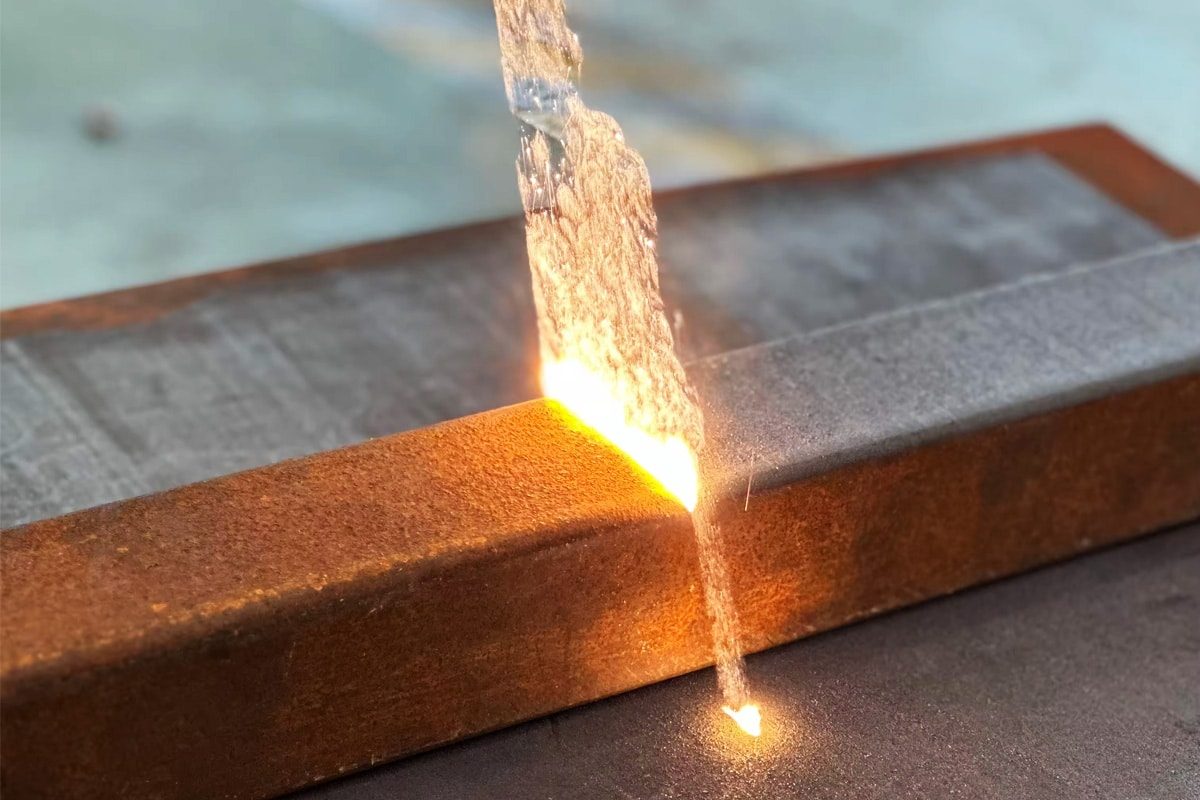
How to Choose a Suitable Laser Cleaning Machine
Laser cleaning technology is rapidly gaining popularity in many industries due to its high efficiency, precision, and environmental protection. As a non-contact surface cleaning technology, laser cleaning can remove surface contaminants through strong beam irradiation, avoiding the chemicals and mechanical wear involved in traditional cleaning methods. Whether it is the daily maintenance of industrial equipment or the high-precision requirements of specific processes, laser cleaning technology can provide unparalleled advantages. With the continuous advancement of technology, laser cleaning machines have achieved remarkable results in the surface cleaning of various materials such as metals, plastics, and ceramics, and have become an ideal choice for improving efficiency and reducing costs in many industries.
For those who are new to laser cleaning technology or companies that plan to upgrade their equipment, choosing a suitable laser cleaning machine is crucial. Different models of laser cleaning machines differ in power, wavelength, cleaning range, and ease of operation. Only by choosing equipment that meets your actual needs can you maximize the technical advantages and achieve ideal cleaning effects. In the purchase process, in addition to the technical parameters of the equipment, understanding its industry applications and market feedback is also a key factor. This article will explore in depth the basic principles of laser cleaning, key points for purchase, and its wide application in various industries to help you make wise decisions when choosing a laser cleaning machine.
Table of Contents
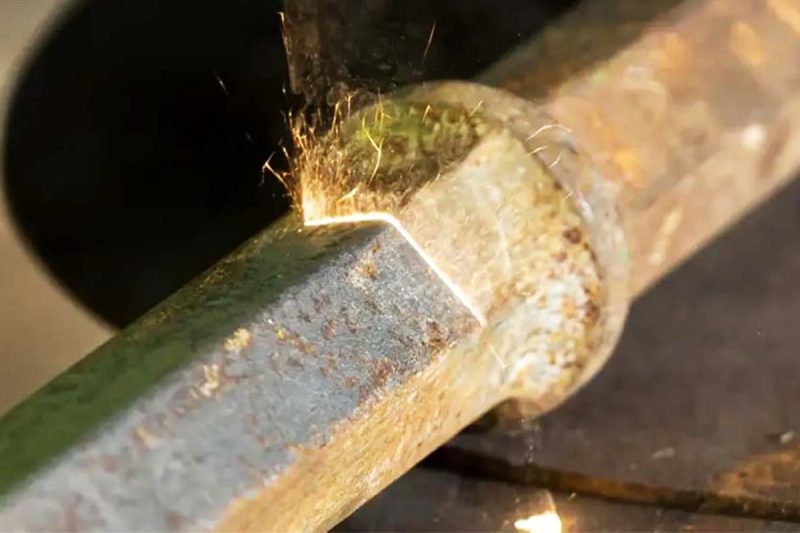
Learn About Laser Cleaning Technology
Laser cleaning technology focuses the laser beam on the target surface and uses the high-energy instantaneous ablation effect of the laser to remove surface pollutants, rust, oil, or coatings while maintaining the integrity of the substrate. The energy of the laser instantly evaporates or peels off pollutants during the cleaning process without causing any damage to substrates such as metals and plastics. Therefore, this technology is widely used in precision manufacturing and high-demand surface cleaning tasks.
Type of Laser Used
Continuous Wave (CW) Laser: This laser type outputs energy in a continuous beam, making it ideal for rapid cleaning of large areas, especially when removing heavy dirt, rust, or coatings. It can evenly cover larger surface areas, making cleaning more efficient and working faster.
Pulsed Laser: Pulsed lasers emit high-energy laser pulses in a short period of time, with the ability to precisely control the energy and duration of each pulse, making them ideal for cleaning delicate or sensitive surfaces. This laser technology is often used for high-precision cleaning, such as decontamination of electronic components or small parts, to ensure that fine structures are not damaged.
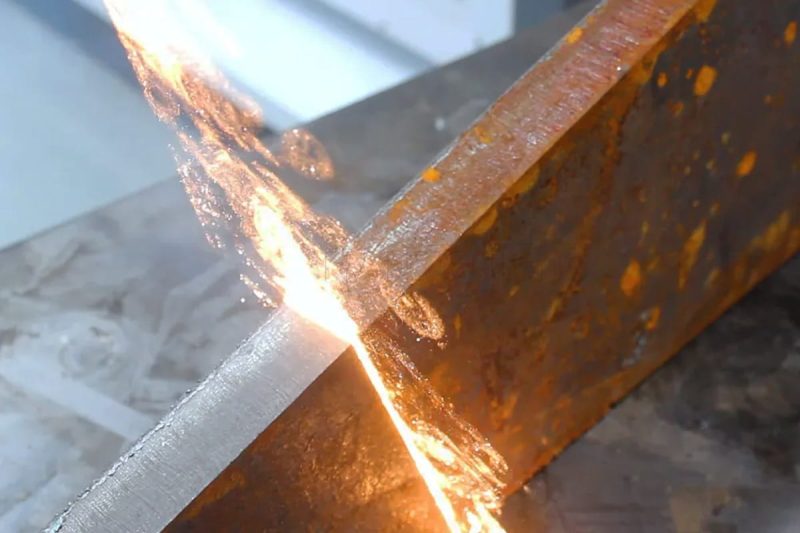
Key Factors to Consider When Choosing a Laser Cleaning Machine
Laser Type: Pulsed and Continuous Wave Lasers
Pulse laser: Pulse laser generator releases high-energy laser pulses in a short period, which is suitable for precise and demanding surface cleaning. It can quickly and accurately clean the surfaces of different materials, especially when dealing with sensitive surfaces or parts with complex shapes. Pulse laser is often used to remove rust, oil, coatings, etc., and can accurately control the pulse energy to avoid damage to the substrate. It is widely used in electronics, aviation, automotive and other industries.
Continuous wave (CW) laser: Continuous wave laser provides stable laser output and is suitable for rapid cleaning of large areas. It is suitable for continuous cleaning of stains, rust, oil stains, etc. in a relatively wide area, and is often used for large-scale surface cleaning in industrial production lines. Due to its continuous laser output, it can improve efficiency and reduce cleaning time.
Material Compatibility
The choice of laser cleaning machine needs to take into account the type of material to be cleaned. Different laser wavelengths are suitable for different materials. For example, the cleaning requirements of metals, plastics, ceramics, stones, and other materials are different. Therefore, it is necessary to ensure that the wavelength of the laser cleaning machine matches the cleaning object. High-power lasers can handle harder metals and heavily rusted surfaces, while low-power lasers are more suitable for cleaning delicate materials such as plastics and coated surfaces.
Laser Power
Laser power directly affects cleaning efficiency and accuracy. Power is usually measured in watts (W), with a common range of 100W to 3000W. High-power lasers can quickly remove heavy contaminants or rust layers and are suitable for large-area cleaning in industrial production. Lower-power lasers are suitable for fine cleaning, such as removing minor stains or coatings. When choosing, you need to select the appropriate power based on the specific application requirements, the material of the cleaning object, and the cleaning target.
Beam Quality and Spot Size
The effect of laser cleaning is closely related to the beam quality and spot size. A high-quality beam can maintain good energy concentration, reduce energy scattering, and ensure efficient and precise cleaning. In addition, a laser generator with an adjustable spot size can adjust the size of the beam according to different cleaning requirements, thereby flexibly responding to various cleaning tasks, including large-area rapid cleaning and fine small-area cleaning.
Mobility and Portability
If the cleaning task needs to be performed on-site or on large equipment, portable laser cleaning machines are particularly important. Portable equipment is lightweight and easy to move, suitable for on-site cleaning of ships, steel structures, large mechanical equipment, etc. For companies that require cleaning in environments where it is inconvenient to move large equipment, it is more convenient to choose equipment with a wheeled base or that can be disassembled.
Cooling System
The cooling system of the laser cleaning machine is the key to ensuring stable operation of the equipment and extending its service life. High-power laser generators generate a lot of heat when working. Continuous cooling can prevent the equipment from overheating and ensure efficient operation of the equipment. Common cooling methods include water cooling and air cooling. The water cooling system is suitable for high-power equipment and can provide a more stable cooling effect to avoid overheating and damage to the laser generator.
Automation and Control Systems
Modern laser cleaning machines are usually equipped with advanced automated control systems and intelligent operation interfaces, which greatly improve the convenience of operation and cleaning efficiency. Users can set the automation mode according to different cleaning needs, such as automatically adjusting the laser power, pulse frequency, and cleaning trajectory, reducing manual intervention, and improving production efficiency. In addition, the intuitive and easy-to-use interface can help operators quickly master the use of the equipment.
Security Features
Laser cleaning machines generate high-energy laser beams during operation, so they must have good safety features. The equipment should be equipped with protective covers, laser safety windows, and emergency stop devices to ensure the safety of operators. In addition, the equipment should comply with international safety standards, such as laser safety standards (such as IEC 60825-1), to ensure that the laser beam during operation does not cause harm to personnel.
Cost and Budget
When choosing a laser cleaning machine, you need to consider the initial purchase cost, long-term operating costs, and maintenance costs of the equipment. The price of laser cleaning machines varies greatly, depending on factors such as power, function, and brand. High-power, high-precision equipment is usually more expensive, but it can provide excellent cleaning results in demanding environments and is suitable for industrial production. In addition to the initial investment, the long-term costs of the equipment such as energy consumption, maintenance, and repair should also be considered to ensure the cost-effectiveness of the equipment throughout its life cycle.
To sum up, when choosing a laser cleaning machine, we should not only pay attention to the technical parameters of the equipment but also comprehensively consider multiple factors such as usage scenarios, budget, maintenance, and safety to ensure that the equipment can provide efficient cleaning while meeting the production needs of different companies.
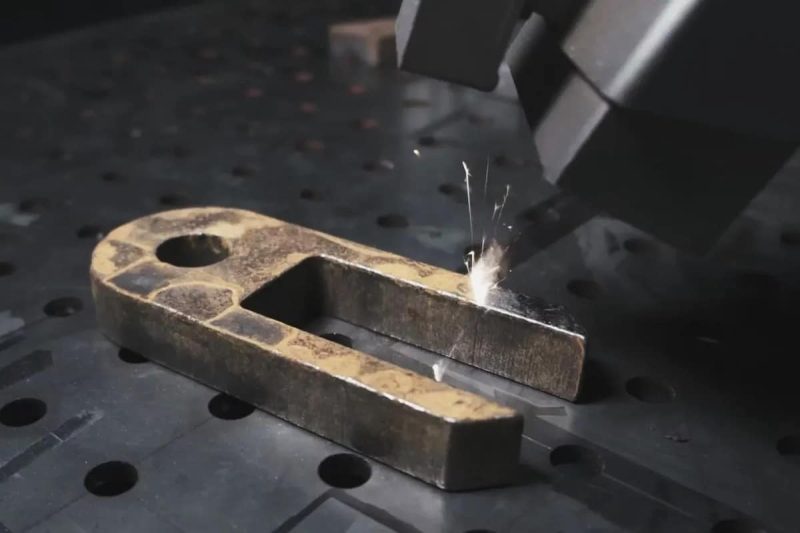
Advantages of Laser Cleaning
Environmental Friendly
- No chemical cleaners: Laser cleaning technology does not rely on chemical cleaners, solvents, or any harmful substances. Instead, it directly removes surface contaminants through lasers, which not only reduces the use of chemicals but also avoids possible environmental pollution. Traditional cleaning methods often require a large amount of solvents, which may sometimes pollute water sources and soil, while laser cleaning completely avoids this problem and meets the needs of modern green, and environmentally friendly production.
- Reduce waste: Traditional cleaning methods may generate a large amount of waste, including cleaning agents, cleaning cloths, brushes, etc., which require additional treatment. However, there is no chemical waste or solid residue in the laser cleaning process. The pollutants after cleaning will evaporate or peel off directly, and almost no waste will be generated, thus greatly reducing the pressure of post-cleaning waste treatment.
- Low energy consumption: Laser cleaning technology has lower energy consumption than traditional cleaning methods, especially in large-scale cleaning tasks. Laser cleaning provides an efficient solution to help companies reduce energy consumption in the production process while reducing carbon emissions, which meets the global requirements for energy conservation and emission reduction.
Efficiency
- Fast cleaning: Laser cleaning is much more efficient than traditional methods (such as manual cleaning, sandblasting cleaning, etc.). Laser beams can quickly remove rust, oil, or coatings from metal surfaces, especially in industrial production environments that require extensive cleaning. For large-area cleaning, laser cleaning can significantly increase processing speed, save a lot of time, and improve the efficiency of the production line.
- Reduce labor costs: Since laser cleaning is an automated operation, manual intervention is greatly reduced, especially in working environments that require high-frequency cleaning, which can effectively save labor costs. Traditional cleaning methods usually require manual cleaning and supervision, while laser cleaning can be completed through automated equipment, which not only saves manpower but also reduces the occurrence of human errors.
- Large Area Cleaning: Laser cleaning shows great advantages when a large number of surfaces or large areas of contamination need to be treated. Laser cleaning can quickly cover and clean the entire surface by adjusting parameters such as beam size and power, significantly improving the efficiency of cleaning operations. It is especially suitable for surface cleaning of metal structures, steel surfaces, large equipment, etc.
Versatility
- Applicable to a variety of materials: Laser cleaning technology has a wide range of applicability and can clean the surfaces of various materials, including metal, plastic, stone, composite materials, etc. Whether it is high-strength metal materials or fragile plastics and ceramics, laser cleaning can provide an ideal solution. For different materials, the laser wavelength and power can be flexibly adjusted to ensure a balance between cleaning effect and surface protection.
- Removal of various pollutants: Laser cleaning can not only remove rust, but also effectively remove various types of pollutants such as oil, paint, oxide layer, coke, etc. Whether in mechanical manufacturing, aerospace or automotive industry, laser cleaning can cope with a variety of different pollutants and meet the industry’s high requirements for cleaning effects.
- Adapt to complex shapes: Laser cleaning is suitable for workpieces with complex shapes or fine structures. Traditional cleaning methods may have difficulty covering all details when cleaning precision parts, while laser cleaning can clean irregular shapes or complex surfaces through its high-precision beam, especially suitable for surface cleaning of high-precision equipment such as electronic components and precision instruments.
Precision and Control
- High-precision cleaning: The high focusing characteristics of the laser beam enable it to precisely clean the target surface at the micron level. This precision makes laser cleaning the preferred technology for many high-precision industries, such as aerospace, semiconductors, optical instruments, etc., where laser cleaning can ensure the thorough removal of contaminants without damaging the substrate.
- Precise control of energy: The energy output of laser cleaning can be precisely adjusted, including pulse width, frequency, and laser power, which allows laser cleaning to be optimized according to different cleaning needs. For example, when removing tiny stains on the surface, the laser power can be lowered, while when dealing with rust or heavy contaminants, the power can be increased. This controllability greatly improves the accuracy and effect of cleaning.
- Avoid damage to the substrate: During laser cleaning, the laser beam only acts on the contaminant layer and does not directly contact the substrate, which avoids scratches, wear, or corrosion on the material surface that may occur in traditional cleaning methods. Therefore, laser cleaning is particularly important for precision parts or fragile surfaces to ensure that the substrate is not physically damaged.
Non-Contact Process
- No physical wear: Laser cleaning is a non-contact process, which means that the laser beam does not come into direct contact with the cleaning surface, thus avoiding the physical wear and scratches that may be caused by traditional cleaning methods. This is especially important for precision equipment or delicate materials that need to maintain an intact surface.
- Reduced risk of contamination: Since laser cleaning does not contact the surface of the workpiece, there are no contact tools such as brushes and cloths during the cleaning process, which greatly reduces the risk of contamination that may be introduced during the cleaning process. This is especially critical for handling parts that require high cleanliness, such as electronic components and optical equipment.
- Suitable for precision parts: Laser cleaning is particularly suitable for surface cleaning of precision parts and micro-components. For example, in electronics manufacturing, medical equipment, and micro-machining industries, laser cleaning can efficiently and safely remove contaminants on tiny parts and avoid any damage to fine structures.
Cost-Effectiveness
- Low maintenance costs: Laser cleaning equipment generally requires less maintenance than traditional mechanical cleaning equipment. The laser generator has a long service life and does not require frequent replacement of parts or consumable materials like traditional equipment, which greatly reduces long-term operating costs.
- High efficiency and energy saving: Although the initial equipment investment of laser cleaning is high, due to its efficient cleaning ability, a large amount of work can be completed in a shorter time, saving energy and labor costs. For enterprises, the saved time and resources can be converted into higher productivity.
- Reduced consumables: Compared with traditional cleaning methods, laser cleaning does not require the use of any consumables such as cleaning agents, solvents, sandblasting particles, etc., which not only reduces operating costs but also reduces environmental burden.
- High return rate: Despite the high initial investment, the advantages of laser cleaning technology such as high efficiency, low energy consumption, and long life make its long-term use have a high return on investment. In large-scale cleaning operations, laser cleaning equipment can provide a quick return, especially suitable for industrial production lines or repetitive cleaning tasks.
Laser cleaning technology is becoming an important technology in the field of industrial cleaning due to its advantages of environmental protection, high efficiency, versatility, high precision, non-contact, and cost-effectiveness. With the continuous development and application of laser technology, more and more industries are beginning to adopt laser cleaning to improve production efficiency, reduce operating costs, and achieve a more sustainable production model. When choosing a laser cleaning machine, companies should consider their own cleaning needs and budgets and choose the right equipment to ensure that the advantages of laser cleaning technology are maximized.
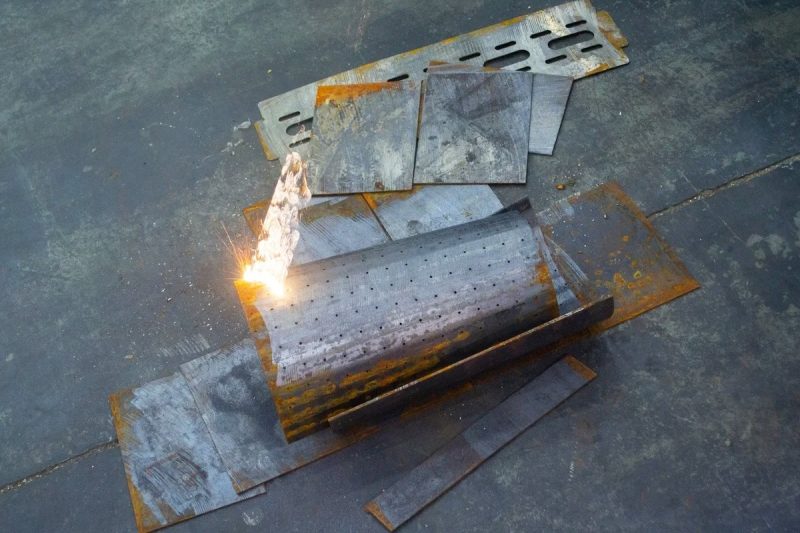
Specific Applications and Industry Requirements
Laser cleaning technology is an advanced process that uses high-energy laser beams to remove surface pollutants, rust, or coatings. It is efficient, environmentally friendly,y and precise. As a non-contact cleaning method, laser cleaning can not only effectively remove various stains, but also maintain the integrity of the substrate and avoid physical damage. Widely used in many industries such as automobiles, aerospace, electronics, and cultural heritage protection, laser cleaning is gradually replacing traditional cleaning methods and becoming an indispensable tool in modern industry and cultural heritage protection.
Auto Industry
- Rust removal: Laser cleaning can effectively remove rust from automotive metal parts without damaging the substrate.
- Coating removal: Laser cleaning accurately removes surface coatings or paint, providing an ideal clean surface for painting and welding.
- Surface pretreatment: Before assembly or painting, laser cleaning can effectively remove oil and impurities, ensure a clean surface for parts, and improve the subsequent process effect.
Aerospace Industry
- Precision cleaning: used to clean aviation parts, remove oil, oxide coatings, etc., while avoiding damage to high-precision parts.
- No risk of damage: Laser cleaning is a non-contact process, avoiding surface damage that may be caused by traditional cleaning methods, and ensuring the safety of parts.
Electronics Industry
- Precision component cleaning: Laser cleaning is used for precision cleaning of electronic components such as circuit boards and connectors to ensure no damage and remove tiny contaminants.
- Surface contamination-free: Through non-contact cleaning, the risk of contamination of sensitive components is reduced, ensuring the reliability and performance of electronic components.
Cultural Heritage Protection
- Surface cleaning of cultural relics: Laser cleaning can safely remove dirt, dust, and old coatings on the surface of cultural relics, protecting historical relics.
- Non-destructive cleaning: Laser cleaning does not contact the surface, ensuring that cultural relics and artworks are not physically damaged during the cleaning process.
Laser cleaning technology has become an ideal surface cleaning solution in many industries due to its environmental protection, high efficiency, precision, and versatility. From the automotive industry to the aerospace, electronics industry, and cultural heritage protection, laser cleaning can efficiently remove various pollutants without damaging the substrate, greatly improving production efficiency and reducing environmental impact. With the continuous advancement of technology, laser cleaning will show its unique application potential in more fields, providing more sustainable and economical cleaning solutions for various industries.
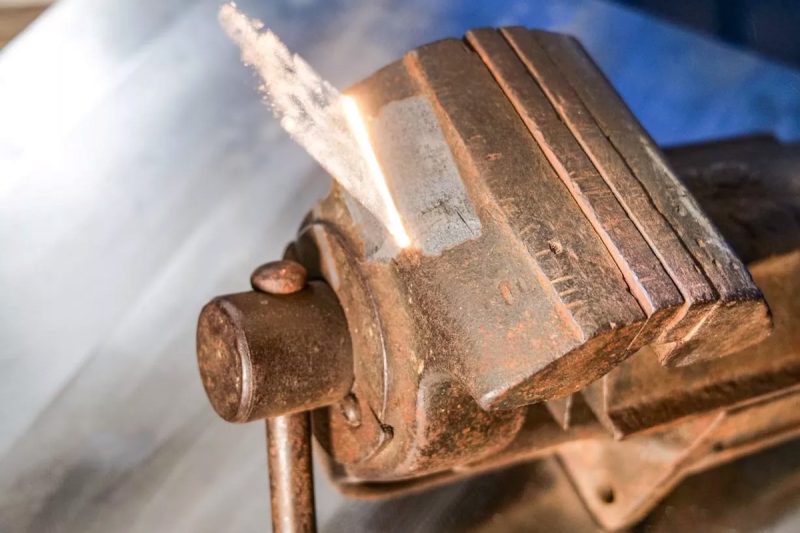
Evaluating Laser Cleaning Machine Suppliers
Choosing the right laser cleaning machine supplier is crucial to ensuring the performance and long-term use of the equipment. When evaluating suppliers, pay attention to key factors such as their market reputation, after-sales support, customization options, and warranty and service agreements. By comprehensively considering these factors, you can ensure that you get high-quality laser cleaning equipment that suits your needs, and enjoy long-term and stable technical support and service guarantees.
Supplier Reputation
- Market reputation: Choose suppliers with good reputations and successful cases to ensure reliable equipment quality and performance.
- Industry experience: Experienced suppliers can provide professional advice and customized solutions to ensure that the equipment meets specific needs.
- Customer feedback: Understand the supplier’s customer feedback to help evaluate its product reliability and service level.
After-Sales Support
- Technical support: Suppliers should provide timely technical support to ensure that equipment failures are resolved quickly.
- Maintenance services: Regular maintenance and inspections can improve equipment stability and service life.
- Upgrades and training: Ensure that suppliers provide equipment upgrades and operation training to ensure long-term and efficient use of equipment.
Customization Options
- Personalized needs: Choose suppliers that support customized solutions to meet the needs of different working environments.
- Flexibility and scalability: Suppliers should provide adjustable and scalable equipment configurations to cope with future changes in demand.
Warranty and Service Agreement
- Warranty: Pay attention to the warranty period provided by the supplier to ensure that the equipment can be repaired free of charge in the event of a failure.
- Service agreement: Check the repair response time and cost terms in the service agreement to ensure that the equipment can be repaired efficiently and economically.
- Additional protection: Consider whether there is an extended warranty or additional service protection to reduce long-term risks.
Through the evaluation of these aspects, you can more clearly choose a reliable laser cleaning machine supplier.
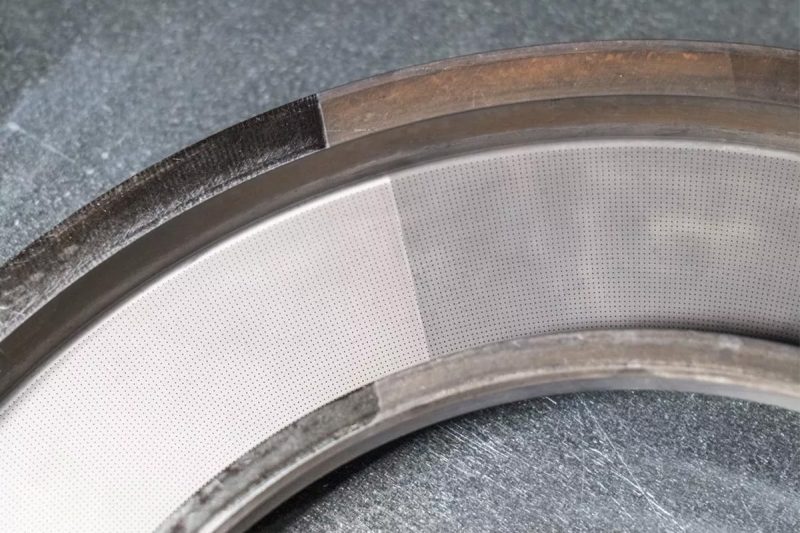
Summarize
When choosing a laser cleaning machine, you need to consider many factors, including technical requirements, operational goals, and budget constraints. First of all, clarifying the laser type (such as pulse or continuous wave), power, beam quality, and material compatibility is the key to ensuring that the equipment can meet specific cleaning needs. In addition, it is also crucial to choose a supplier that provides comprehensive after-sales service to ensure timely technical support and maintenance services during the use of the equipment.
By adopting advanced laser cleaning technology, you can not only significantly improve production efficiency, but also promote environmental protection and sustainable development while reducing the use of chemical cleaning agents. The efficiency and precision of laser cleaning make it the preferred solution for many industries, helping companies improve their competitiveness. When choosing equipment, carefully evaluate various factors and let the laser cleaning machine become a powerful helper for you to stand out.
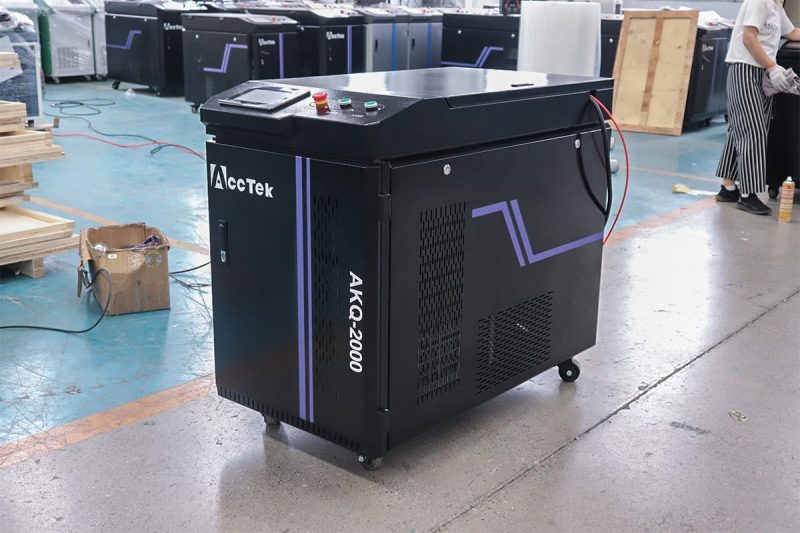
Get Laser Solutions
We provide advanced laser cleaning solutions to help customers in various industries improve production efficiency and cleaning effects. Whether it is used for rust removal, coating removal, or precision surface cleaning, our laser cleaning machines can provide customized solutions according to your specific needs. Our equipment has the advantages of high precision, environmental protection, and high efficiency, and is widely used in many fields such as automobiles, aerospace, electronics, and cultural heritage protection. By combining advanced industry technology and strong after-sales service, AccTek Laser is committed to providing you with high-quality and reliable laser cleaning equipment to help you stand out in the fierce market competition. Choose us to get the efficient laser cleaning solutions you need and let us provide strong support for your production and environmental sustainability.
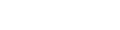
Contact information
- [email protected]
- [email protected]
- +86-19963414011
- No. 3 Zone A, Lunzhen Industrial Zone,Yucheng City , Shandong Province.
Get Laser Solutions