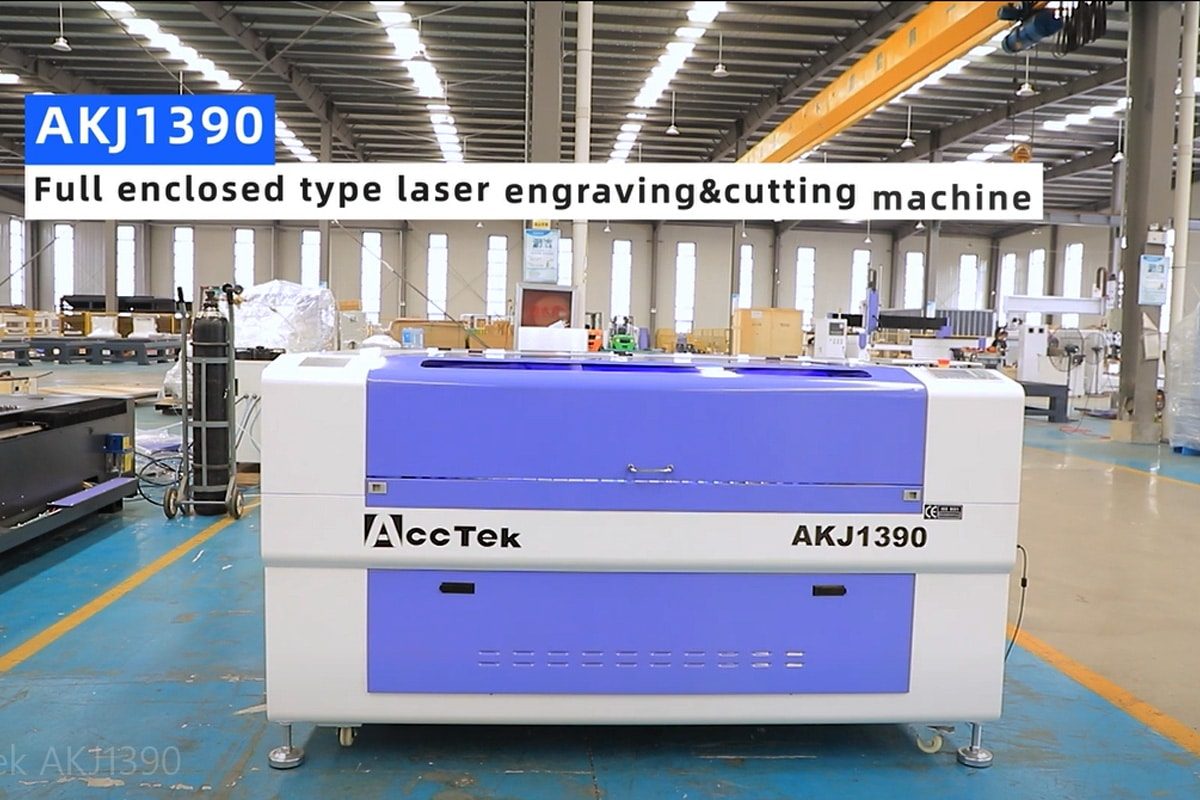
How to Choose Auxiliary Gas in CO2 Laser Cutting
CO2 laser cutting technology is widely used in the cutting of various materials such as metal, plastic, wood, etc. due to its advantages of high precision and high speed. In this process, the selection and setting of auxiliary gas is crucial, which directly affects the cutting quality, speed, and stability of the overall process. By scientifically selecting suitable auxiliary gas, it can not only effectively improve the cutting quality and reduce the thermal deformation of the material, but also optimize the cutting speed and improve the overall processing efficiency. The basic principle of the CO2 laser cutting machine is mainly to focus the laser beam on the surface of the material to generate a high temperature to melt or vaporize the material, and the auxiliary gas plays multiple roles in this process, including promoting the discharge of molten material, protecting the cutting edge from oxidation, and cooling the cutting area to reduce the heat affected zone.
Different types of auxiliary gases have different characteristics. For example, oxygen is suitable for cutting carbon steel. It can speed up the cutting speed through oxidation reaction, but it will produce oxides at the edge. Nitrogen effectively inhibits oxidation and ensures smooth edges. It is very suitable for materials with high surface quality requirements such as stainless steel. Air is a low-cost option and is suitable for applications with low precision requirements. In actual applications, the purity, pressure, and flow rate of the auxiliary gas also need to be adjusted according to the specific materials and cutting requirements. This article will analyze the advantages and disadvantages and applicable scenarios of auxiliary gases such as oxygen, nitrogen, and air based on the characteristics of different materials, to help you better understand the role of auxiliary gases and achieve more efficient and precise cutting results.
Table of Contents
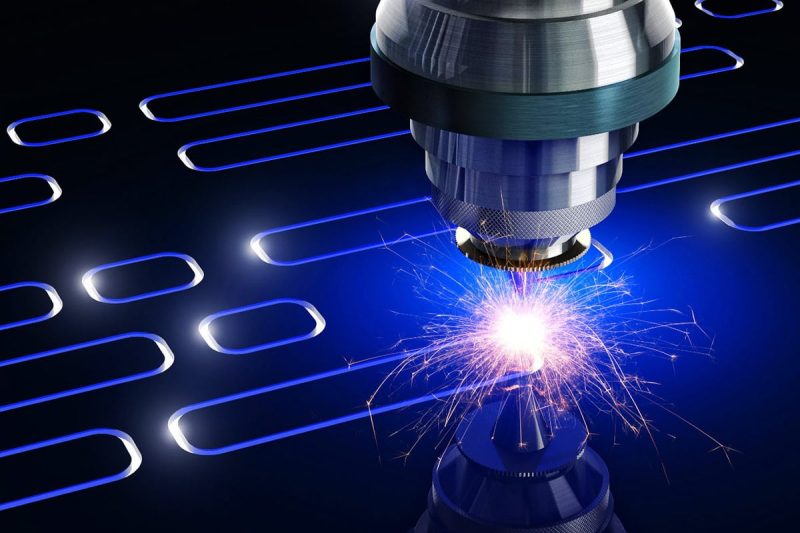
The Basic Principle of CO2Laser Cutting
Explanation of the Working Principle of CO2 Laser Cutting
CO2 laser cutting is based on the high energy concentration characteristics of the laser beam. By focusing the laser beam on the surface of the material to form an extremely high temperature, the material is partially melted or vaporized, and the auxiliary gas blows the melt or gasification product away from the cutting area. The laser beam forms a tiny perforation on the surface of the material and then moves along a preset trajectory to achieve precise cutting. The cutting process relies on the high heat energy transfer of the laser. The laser beam is continuously concentrated on the surface of the material to maintain a sufficient temperature so that the material can stably reach a melting or vaporization state. At the same time, the role of the auxiliary gas ensures that the cutting port remains clean to avoid residue accumulation. The synergistic effect of the laser beam and the auxiliary gas ensures the continuity, accuracy, and edge quality of the cutting.
CO2 Laser Cutting Process Overview
The entire CO2 laser-cutting process is the result of the cooperation of laser energy and auxiliary gas. The auxiliary gas not only helps to remove molten materials or steam, but also plays a protective role. For example, the auxiliary gas can prevent the debris and smoke generated during the cutting process from contacting the optical lens, so as not to affect the cutting accuracy. At the same time, in the cutting of certain materials, choosing a suitable auxiliary gas can also avoid oxidation reactions, thereby improving the finish of the cutting edge and the cutting quality. The type, purity, pressure, and flow rate of the auxiliary gas should be determined according to the characteristics of different materials and the specific requirements of cutting.
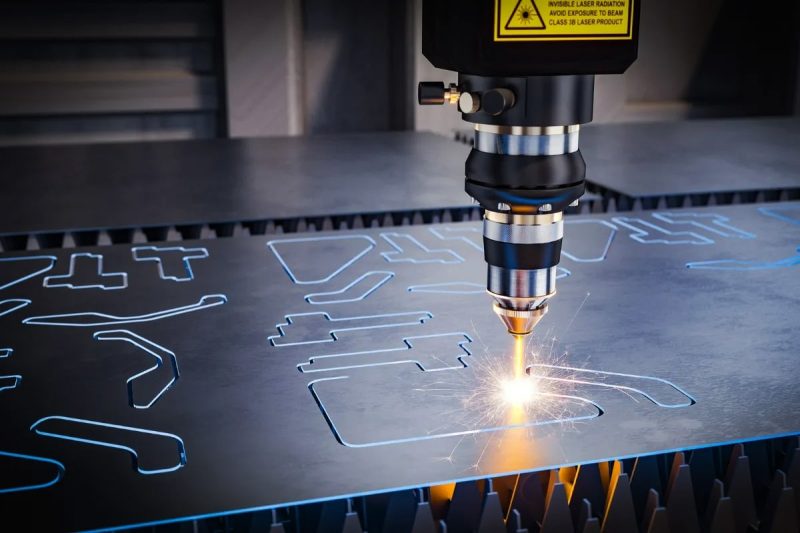
The Role of Auxiliary Gas in CO2 Laser Cutting
In CO2 laser cutting, the role of auxiliary gas is crucial. Choosing the right auxiliary gas can not only improve cutting efficiency but also improve cutting quality and reduce process defects. The following are the main functions and importance of auxiliary gas in CO2 laser cutting.
Ensure Cutting Efficiency
The auxiliary gas removes the melt and vapor in time during the cutting process, ensuring that the laser beam can act on the material surface stably and continuously, thereby maintaining high cutting efficiency. In particular, auxiliary gases such as oxygen will release additional heat through oxidation reactions, further increasing the cutting speed and greatly affecting production efficiency.
Improve Cutting Quality
The correct selection of auxiliary gas is crucial to the quality of the cutting edge. For example, nitrogen can effectively inhibit oxidation reactions, ensure smooth edges, no oxidation residue, and reduce burrs and scum. Choosing the appropriate auxiliary gas can significantly improve the smoothness of the cutting surface and meet the needs of applications that require high cutting accuracy and aesthetics.
Reduce Heat Affected Zone (HAZ)
The assist gas helps cool the cutting edge, prevents overheating, and reduces the extent of the heat-affected zone, thereby protecting the physical properties and structural integrity of the material. This is especially important for precision machining and thin material cutting, helping to maintain the strength and hardness of the material.
Protect Equipment and Extend Service Life
The auxiliary gas not only protects the cutting area but also prevents smoke and debris generated during the cutting process from adhering to the laser optical lens, avoiding damage or contamination of the lens. The use of auxiliary gas can reduce the frequency of cleaning and maintenance of the equipment, ensuring the stability and durability of the laser cutting machine.
Generally speaking, auxiliary gas is not only an important auxiliary tool in CO2 laser cutting but also a key element in achieving efficient and high-quality cutting. Choosing the right gas according to the material type and cutting needs can significantly improve production efficiency, reduce costs, and ensure the smoothness of the cutting edge and cutting quality.
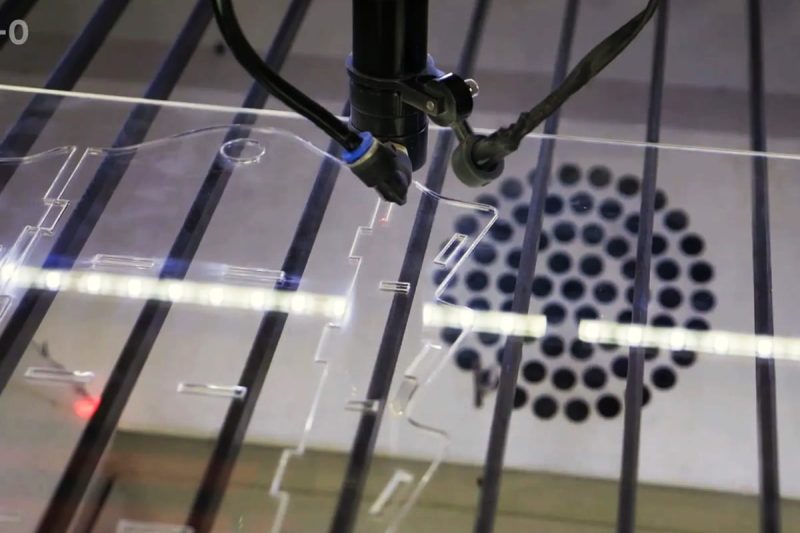
Common Auxiliary Gases for CO2 Laser Cutting
In the CO2 laser cutting process, the selection of auxiliary gas is crucial to the cutting effect. The following are common auxiliary gases and their functions:
Oxygen (O2)
Oxygen is one of the most commonly used auxiliary gases in CO2 laser cutting, especially suitable for cutting carbon steel. By reacting with the material being cut, oxygen generates additional heat, significantly increasing cutting speeds. This reaction process not only speeds up cutting but also reduces the residue of melt, ensuring higher cutting efficiency. However, there are some limitations to the use of oxygen. In cutting applications with high precision or strict requirements for oxidation, oxygen may form an oxide layer on the cutting edge, affecting the appearance and performance of the final product, so it should be used with caution in these situations.
Nitrogen (N2)
Nitrogen is an inert gas that is often used for stainless steel, aluminum, and other materials that require high-quality cutting. The main function of nitrogen is to prevent oxidation reactions from occurring, thereby ensuring that the cut edge remains smooth and clean. This makes nitrogen very suitable for applications that require high surface finish, such as the aerospace and electronics industries. By using nitrogen, slag, and burrs generated during the cutting process can be effectively reduced, improving the quality of the final cut part. In addition, the cost of nitrogen is relatively low, making it an affordable choice.
Air
Air is usually used as an auxiliary gas for low-cost cutting and is suitable for workpieces with low precision requirements. Since air contains about 21% oxygen, a certain oxidation reaction will occur during the cutting process. Although this reaction can provide some heat to help cutting, the cutting effect of air is slightly lower than that of pure oxygen. Nevertheless, the use of air can greatly reduce costs and is suitable for some applications that do not require high cutting quality, such as cutting or rough processing of building materials.
In summary, choosing the appropriate auxiliary gas is crucial to optimizing the CO2 laser cutting process. Oxygen, nitrogen, and air each have their own unique advantages and applicable scenarios. Proper selection and setting of auxiliary gases can significantly improve cutting efficiency and quality to meet the needs of different materials and applications.
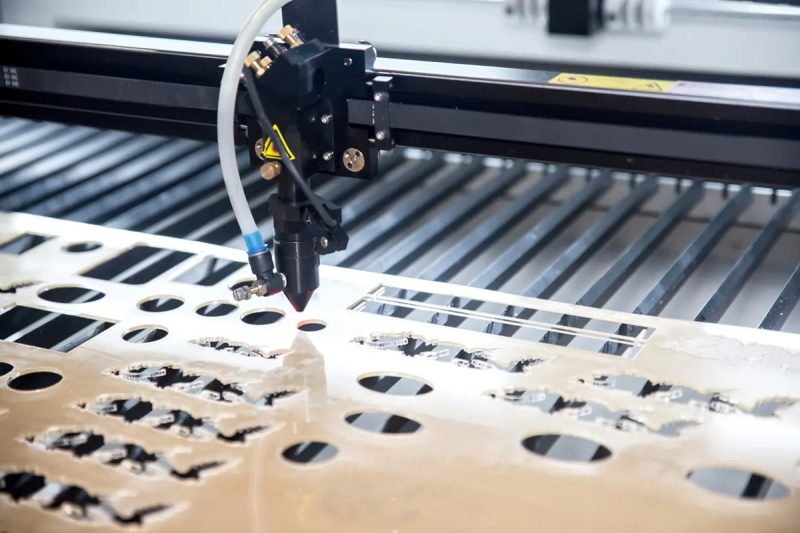
The Influence of Auxiliary Gas on Cutting Efficiency
Auxiliary gas plays an important role in the CO2 laser-cutting process. Its selection directly affects the cutting efficiency, which is mainly reflected in the cutting speed, material compatibility, and control of the heat-affected zone.
Cutting Speed
Oxygen, as an auxiliary gas, can significantly accelerate the cutting speed of carbon steel. This is because the oxidation reaction of oxygen with iron during the cutting process will release additional heat, thereby speeding up the cutting speed. However, oxygen does not significantly increase cutting speed on other materials such as aluminum or stainless steel. This is due to the chemical reactivity of oxygen, which can cause these materials to develop an oxide layer, which can adversely affect cut quality. In these cases, it may be more appropriate to use nitrogen as an assist gas. Although nitrogen itself will not speed up cutting, its inert properties can improve material compatibility and reduce problems that may arise during the cutting process, thus improving overall cutting efficiency.
Material Compatibility
Different materials have different requirements for assisting gases during cutting. Matching the assist gas to the material can effectively improve the cutting effect. For example, highly reflective materials such as aluminum and copper are more suitable for cutting with nitrogen because nitrogen can prevent surface oxidation and reduce the risk of laser reflection. For stainless steel, nitrogen is also preferred because it can provide a good cutting edge and reduce burrs. For low-alloy steel, oxygen is a suitable choice, which can cut quickly and improve efficiency. By properly selecting the assist gas according to the characteristics of the material, the cutting operation can achieve higher efficiency and better quality.
Reduce Heat Affected Zone
During the cutting process, the heat-affected zone (HAZ) is the area of the material where the heat from the laser is transferred to the surrounding area. A large HAZ may cause the edge of the material to deform and change the physical properties of the material. Using nitrogen and air as auxiliary gases can effectively reduce the size of the HAZ. Nitrogen cools the cutting edge to prevent it from overheating, while moisture and gas flow in the air also help to reduce the temperature. Reducing the HAZ not only protects the performance of the material but also ensures the flatness and finish of the cutting edge, ensuring the quality of the final product.
In summary, the selection of auxiliary gas has an important impact on the efficiency of CO2 laser cutting. Reasonable configuration of auxiliary gas can increase cutting speed, ensure material compatibility, and effectively reduce the heat-affected zone, thereby achieving higher-quality cutting results.
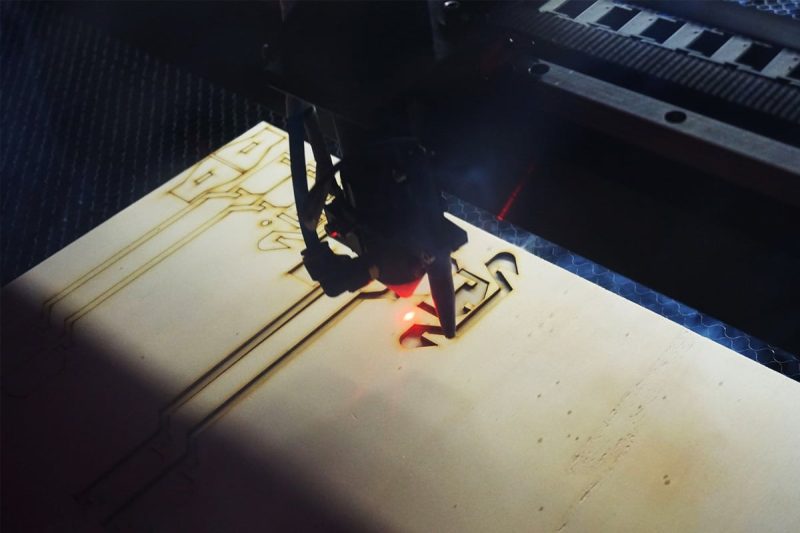
The Influence of Auxiliary Gas on Cutting Quality
In the CO2 laser cutting process, the auxiliary gas not only affects the cutting efficiency, but also plays a vital role in the cutting quality, which is mainly reflected in the surface finish, edge quality, and the reduction of burrs and dross.
Surface Finish
Nitrogen as an auxiliary gas can effectively prevent the occurrence of oxidation reactions during the cutting process, which is crucial to ensure the smoothness of the material surface. When cutting materials such as stainless steel and aluminum that have high requirements for surface finish, nitrogen can effectively inhibit surface oxidation, reduce the formation of oxide film, and ensure a smoother surface after cutting. In addition, a good surface finish can not only improve the aesthetics of the product but also avoid subsequent surface treatment in some applications, thereby saving cost and time. Therefore, nitrogen is an ideal choice for application scenarios with high precision requirements.
Edge Quality
Edge quality is another important indicator for evaluating cutting results. Although oxygen can speed up the cutting speed of carbon steel, it is easy to generate oxides during the cutting process, which may cause irregular and rough cutting edges. In contrast, the use of nitrogen can effectively improve edge quality and ensure that the cutting edge is neat and smooth. The inert properties of nitrogen suppress the oxidation reaction during the cutting process, thereby avoiding cutting defects caused by the generation of oxides. Therefore, the use of nitrogen is particularly important in cutting applications that have high requirements for edge quality.
Reduce Burrs and Dross
High-purity auxiliary gases, such as nitrogen, can effectively reduce the formation of burrs and dross during the cutting process. Burrs and dross not only affect the aesthetics of the cut piece but also increase the complexity and cost of subsequent processing. When using high-purity nitrogen, the molten material in the cutting process is quickly removed, thereby reducing the formation of burrs. In addition, nitrogen can also keep the cutting area clean, further reducing the generation of dross. By reducing the amount of burrs and dross, subsequent processing steps, such as deburring and cleaning, can be simpler, saving production time and improving efficiency.
In summary, the auxiliary gas has a significant impact on the quality of CO2 laser cutting. Selecting the appropriate assist gas can improve surface finish, optimize edge quality, and effectively reduce the formation of burrs and scum, thereby ensuring the high quality of the final cut part. This is critical to meeting increasingly stringent industry standards and customer demands.
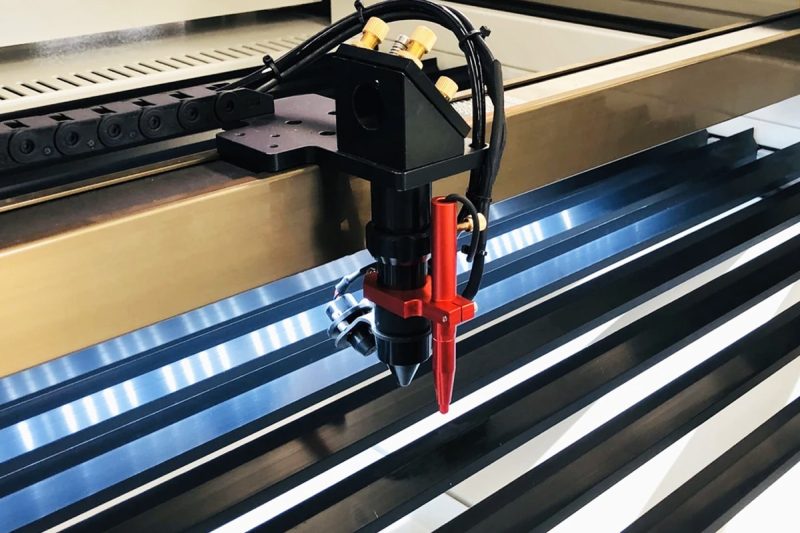
Specific Requirements and Precautions for Auxiliary Gas
When choosing the appropriate auxiliary gas during CO2 laser cutting, it is important not only to consider its type, but also to pay attention to its specific requirements and precautions, including purity level, pressure and flow settings, and safety instructions.
Purity Grade
The purity of the auxiliary gas directly affects the cutting effect, especially when cutting materials with strict requirements on surface quality. For example, the purity of nitrogen should reach more than 99.99% to ensure that it does not affect the surface of the material. Lower purity nitrogen may contain moisture and impurities, which will cause oxidation reactions during the laser cutting process, thus affecting the finish and quality of the cut edge. Similarly, oxygen, its purity should also be maintained at an appropriate level to avoid inducing unnecessary oxidation reactions. Therefore, the use of high-purity gas is an important prerequisite for ensuring cutting quality.
Pressure and Flow Settings
Gas pressure and flow settings are key parameters that affect cutting efficiency and quality. When cutting thick plates, a higher gas pressure is required to ensure that the molten metal can be effectively blown away, thereby maintaining the continuity and stability of the cutting process. Generally speaking, when cutting thicker materials, the pressure of oxygen is usually lower than that of nitrogen, because oxygen itself releases additional heat during the cutting process, reducing the need for pressure. Conversely, for thin plate cutting, lower gas pressure often achieves better cutting results and avoids overheating and deformation. Therefore, the specific flow and pressure settings should be adjusted accordingly according to the type and thickness of the cutting material to achieve the best cutting effect.
Safety Tips
When using high-purity gases, safety is an important factor that cannot be ignored. The sealing of the system is crucial, and it is necessary to ensure that there is no leakage in the gas pipelines and connectors to prevent potential safety hazards. Leaked gas may not only cause environmental pollution but also cause serious accidents such as fire or explosion. Therefore, when installing and using the auxiliary gas system, the equipment should be regularly inspected and maintained to ensure that it is in good condition. In addition, operators should receive necessary safety training and be familiar with emergency handling procedures to ensure that appropriate measures can be taken quickly in the event of abnormal situations, thereby minimizing risks.
In summary, when selecting and using auxiliary gas, attention must be paid to its purity level, pressure and flow settings, and safety precautions. Only by considering these factors comprehensively can the efficiency, safety, and quality of the CO2 laser-cutting process be ensured.
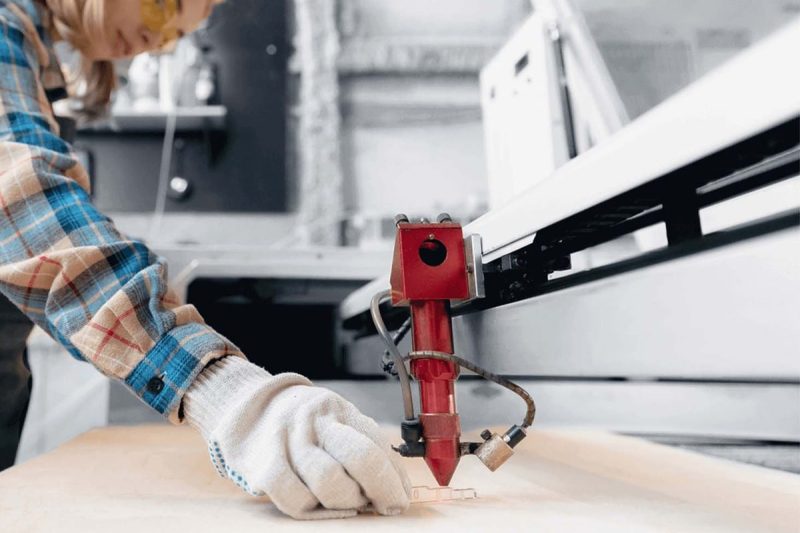
Comparative Analysis of Assist Gases
In the CO2 laser cutting process, the choice of auxiliary gas has a significant impact on cutting efficiency and quality. The following is a comparative analysis of commonly used auxiliary gases (oxygen, nitrogen, and air) covering performance comparisons, cost considerations, and application-specific recommendations.
Performance Comparison
- Oxygen (O2): Oxygen is superior in terms of cutting speed and is particularly suitable for cutting carbon steel. By reacting with the metal surface, oxygen releases additional heat, which speeds up the cutting process. However, the side effect of this reaction is that an oxide layer is formed on the cut edge, resulting in a decrease in the cut surface quality and a lower finish. Therefore, oxygen is more suitable for applications where the cutting speed is high but the cutting quality requirements are relatively loose.
- Nitrogen (N2): Nitrogen is superior in terms of cutting quality and surface finish. It can effectively prevent the oxidation of the material and ensure a smooth cut edge, especially for materials such as stainless steel and aluminum that require high surface quality. Although nitrogen is not as fast as oxygen in cutting speed, its excellent cutting quality makes it an ideal choice for high-precision cutting applications.
- Air: Air is a lower-cost auxiliary gas suitable for cutting occasions with lower precision requirements. Although the use of air can reduce cutting costs, due to its oxygen content, the cutting effect is often not as good as nitrogen and pure oxygen, so it is not suitable for applications that require high precision and finish.
Cost Considerations
- Oxygen: Compared to nitrogen, oxygen has a lower cost and is suitable for applications where high cutting speed is required but cutting quality is not so strict. This makes oxygen the gas of choice in many industrial applications, especially in large-scale production and processing.
- Nitrogen: Although nitrogen costs more than oxygen, its advantages in cutting quality and precision make it more competitive in high-end applications. Therefore, for industries with high requirements for cutting quality and precision, the additional cost of nitrogen is often worth it.
- Air: Air has the lowest cost of use and is suitable for projects with limited budgets and low-cost cutting needs. However, due to its limited cutting effect, it is recommended only for workpieces with lower precision requirements.
Application-Specific Recommendations
- Carbon Steel Cutting: For carbon steel cutting, oxygen is preferred. Its speed advantage can significantly improve production efficiency, especially when producing large quantities.
- Stainless Steel and Aluminum: Nitrogen is a better choice when cutting stainless steel and aluminum. It ensures smooth and oxidation-free cutting edges and is suitable for applications where surface quality is critical.
- Stainless Steel and Aluminum: Nitrogen is a better choice when cutting stainless steel and aluminum. It ensures smooth and oxidation-free cutting edges and is suitable for applications where surface quality is critical.
By comparing and analyzing the auxiliary gases, we can select the appropriate auxiliary gas for the cutting tasks of different materials, thereby improving the cutting efficiency and quality, and making reasonable decisions on the cost. Selecting the appropriate auxiliary gas can not only optimize the cutting effect but also reduce production costs in the long run and improve the competitiveness of the enterprise.
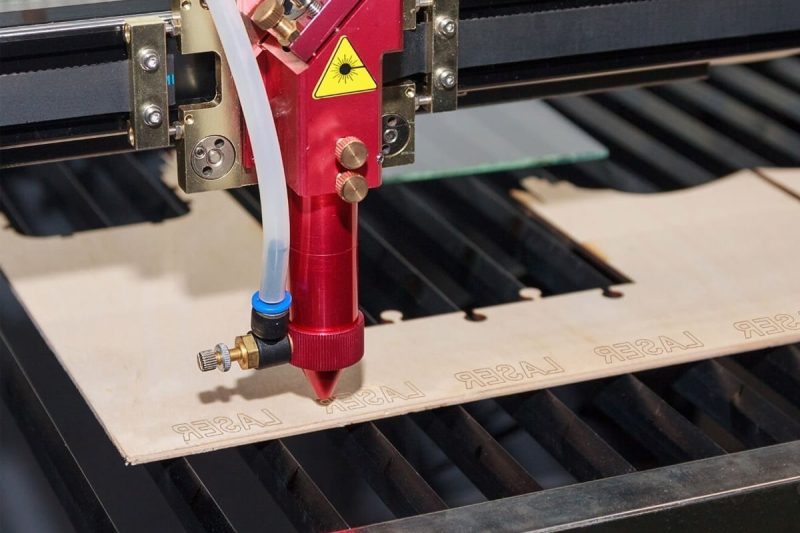
Optimize assist gas selection for different materials
In CO2 laser cutting, the selection of auxiliary gas is crucial to the cutting effect and quality. The characteristics of different materials require us to optimize the use of auxiliary gas according to their specific needs. The following are gas selection recommendations for metal materials, plastic materials, and composite materials.
Metal Materials
- Carbon steel cutting: For carbon steel cutting, oxygen (O2) is recommended as an auxiliary gas. Oxygen can release additional heat through oxidation reaction, thereby significantly increasing the cutting speed, which is suitable for large-scale production and occasions with high cutting efficiency requirements. However, oxygen may form an oxide layer on the cutting edge, so its impact on cutting quality needs to be considered when applying it.
- Stainless steel and aluminum: Nitrogen (N2) is a better choice when cutting stainless steel and aluminum. Nitrogen can prevent the occurrence of oxidation reactions, thereby maintaining the smoothness of the cutting edge and avoiding trouble in subsequent processing. Therefore, when cutting stainless steel and aluminum with nitrogen, higher surface quality can be ensured, especially in applications with high aesthetic and functional requirements.
Plastic Materials
- When cutting plastic materials, it is recommended to use nitrogen or air as auxiliary gas. The use of nitrogen can avoid thermal deformation or combustion caused by high temperature, ensuring the safety and quality of the cutting process. Although air is slightly inferior to nitrogen in effect, it is low in cost and suitable for plastic-cutting tasks that do not require high cutting accuracy. Therefore, according to the cutting requirements, choosing the right gas can effectively avoid damage to plastic materials during the cutting process.
Composite Materials
- For cutting composite materials, it is recommended to choose air or nitrogen according to specific needs. Composite materials are usually composed of different materials, and their cutting process may produce harmful gases, so it is crucial to choose the right auxiliary gas. Air as an auxiliary gas can reduce cutting costs, but may cause surface oxidation in some cases; while nitrogen can provide better cutting quality and safety, and is suitable for demanding cutting applications. According to the specific composite material characteristics and cutting requirements, customizing the appropriate gas selection can effectively reduce the generation of harmful gases and ensure the safety and environmental protection of the cutting process.
Customized Gas Selection for Specific Cutting Requirements
When selecting auxiliary gas, factors such as material properties, cutting speed, cutting quality, and cost need to be considered comprehensively to achieve the best cutting effect. By customizing gas selection for different materials, not only can the cutting efficiency be improved, but the cutting quality can also be effectively controlled to meet the different needs and application scenarios of customers. Selecting the right auxiliary gas will directly affect the smooth progress of the cutting process and the quality of the final product, and is an important part of improving production efficiency and reducing costs.
Nitrogen plays a vital role in laser cutting. To meet the cutting needs of demanding workpieces, AccTek also provides a professional nitrogen production machine that can produce high-purity nitrogen. This investment is very important for applications that require precise cutting, ensuring the smoothness of the material surface and the quality of the cut edge. With our nitrogen generator, you will get better cutting results and reliability, further improve production efficiency, and reduce cutting costs.
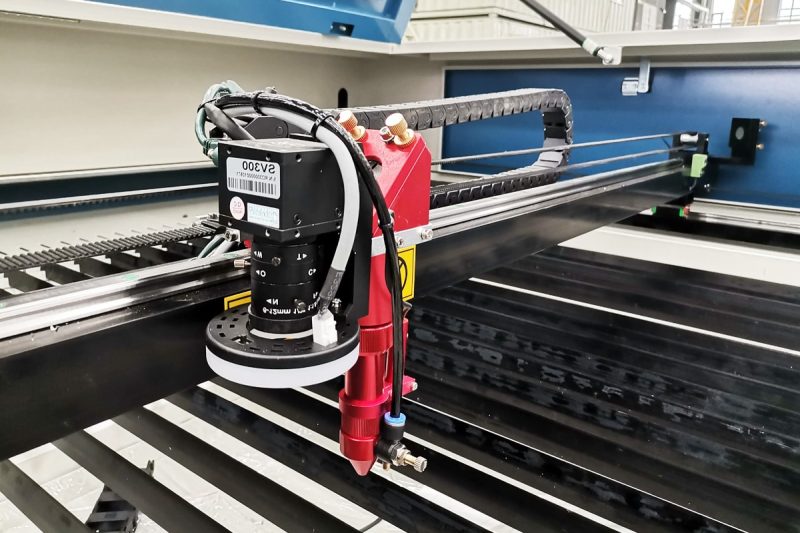
Common Challenges and Solutions
During the CO2 laser cutting process, companies often face challenges that, if not addressed promptly, may affect production efficiency and the quality of the final product. The following are some common problems and their corresponding solutions.
Oxidation Problem
When cutting easily oxidized materials such as stainless steel, the formation of an oxide layer may significantly affect subsequent processing and the appearance quality of the product. To solve this problem, it is recommended to use nitrogen (N2) as an auxiliary gas during the cutting process. Nitrogen can effectively prevent oxidation reactions and ensure that the cutting edge is smooth and free of oxide layers. In this way, the quality of the cut is improved and the cleanup required in subsequent processing steps is reduced, thereby increasing overall productivity.
Heat Affected Zone Is Too Large
During the laser cutting process, a large heat-affected zone (HAZ) can cause deformation and performance degradation of the material at the cutting edge, affecting cutting accuracy. To this end, it is key to properly adjust the flow and pressure of the auxiliary gas. Lower flow and appropriate gas pressure settings can reduce heat transfer to the surrounding material, thereby reducing the heat-affected zone. At the same time, using higher-purity gases (such as nitrogen) can also help control heat and ensure a more uniform temperature distribution during the cutting process, thereby improving cutting accuracy and quality.
Gas Consumption Control
Gas consumption is not only related to cutting costs, but also to the overall economic efficiency of production. To more effectively control gas consumption, it is recommended that companies regularly monitor gas flow and pressure settings. By using gas flow meters and pressure sensors, operators can monitor gas usage in real-time and adjust parameters in time to suit different cutting needs. In addition, regular equipment maintenance and inspections can ensure the tightness of the gas system and reduce unnecessary leaks, thereby further saving costs and improving overall cutting efficiency.
By implementing corresponding solutions to the above challenges, companies can effectively improve the production efficiency and quality of CO2 laser cutting while reducing costs and risks. Effective gas management and adjustment can help companies maintain their advantages in the fierce market competition and meet the growing quality requirements of customers.
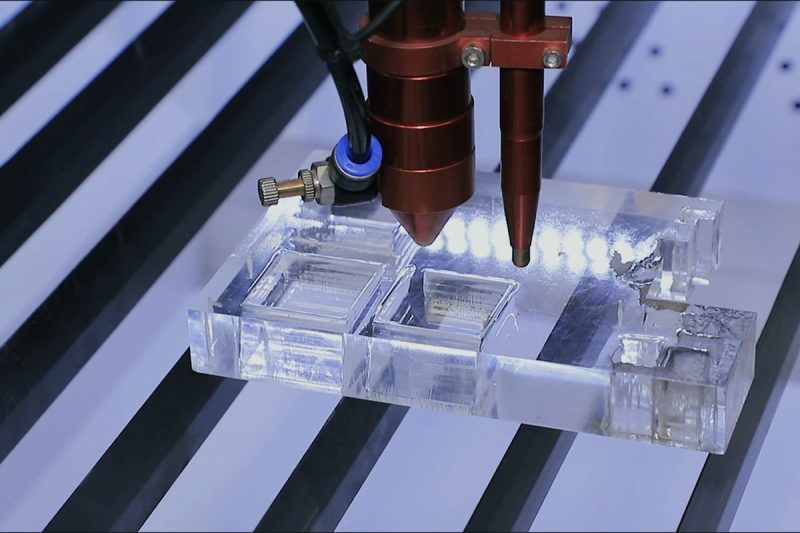
Summarize
The selection of auxiliary gas in a CO2 laser cutting system plays a vital role in cutting quality, speed, and cost. Different materials have different gas requirements during the cutting process. Reasonable selection of auxiliary gas can not only improve cutting efficiency but also ensure cutting quality and reduce overall production costs. For example, when cutting carbon steel, using oxygen as an auxiliary gas can significantly increase the cutting speed, while when cutting stainless steel and aluminum, nitrogen is a more ideal choice because it can prevent oxidation and ensure the smoothness of the cutting edge and accuracy.
In addition, the purity and setting parameters of the auxiliary gas also have a profound impact on the cutting effect. High-purity nitrogen can effectively reduce the generation of burrs and scum and improve the surface finish of the material. The appropriate flow and pressure settings can reduce the heat-affected zone, thereby improving cutting accuracy and material integrity. For different cutting applications, by continuously adjusting the gas type and parameter settings, companies can better meet increasingly diverse industrial needs.
In summary, accurate auxiliary gas selection and optimized cutting parameter settings are key factors in achieving efficient and high-quality CO2 laser cutting. This can not only improve production efficiency but also enhance the market competitiveness of products, enabling enterprises to gain an advantage in the fierce competition. Therefore, in the actual application of CO2 laser cutting, enterprises should pay attention to the selection and management of auxiliary gases to achieve higher production benefits and lower operating costs.
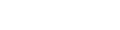
Contact information
- [email protected]
- [email protected]
- +86-19963414011
- No. 3 Zone A, Lunzhen Industrial Zone,Yucheng City , Shandong Province.
Get Laser Solutions