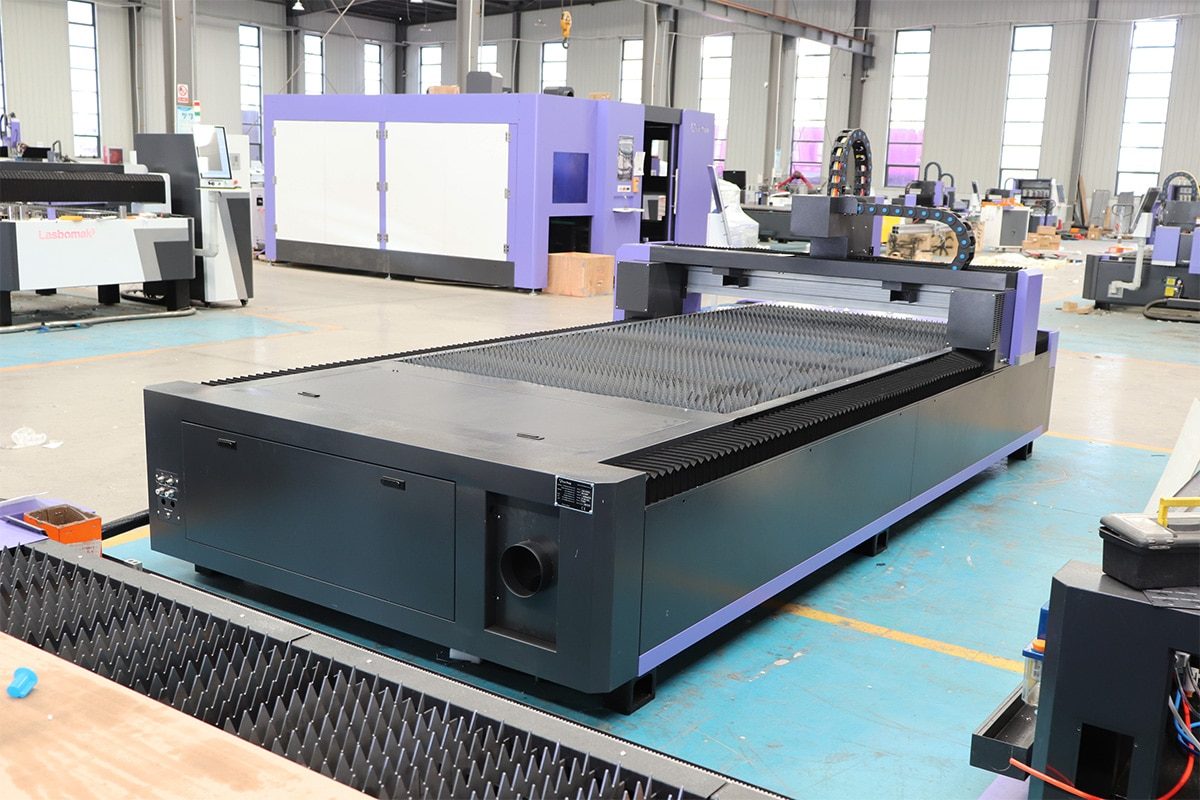
How to Choose the Fiber Laser Cutting Machine Bed Design?
Choosing the right fiber laser cutting machine bed design is crucial because it directly affects production efficiency, operational safety, and the diversity of material handling. Fiber laser cutting machines are generally available in two-bed designs, open and closed. The open bed design has the advantages of easy loading and unloading, support for large-size materials, and continuous processing, which is suitable for companies that require efficient processing; however, due to exposure, this design has some challenges in terms of safety, especially the operator needs protection to avoid the hazards of laser radiation. In contrast, the closed bed design completely encloses the working area, which can effectively shield laser radiation and reduce the impact of debris generated during the cutting process. The closed bed performs outstandingly in terms of precision and safety and is suitable for occasions with higher requirements for cleanliness and operating environment, but due to the relatively closed space, the convenience of loading large materials will be limited.
When choosing a bed design, users need to consider a variety of factors, including the size of the material to be processed, the output requirements, and the size of the workspace. The open bed design is suitable for environments with large production batches, variable material specifications, and higher flexibility requirements, while the closed bed provides better support for high-precision cutting, especially for industries with strict safety requirements. Understanding the advantages and disadvantages of the two designs and their respective application characteristics will help companies choose more matching laser cutting machines in different work scenarios, ensure the continuity and safety of production, and achieve higher benefits in long-term use.
Table of Contents
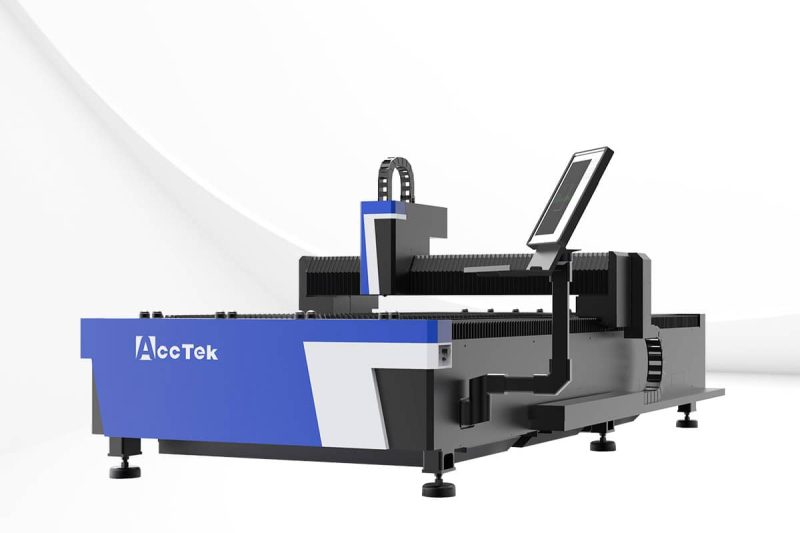
Learn About Open Bed Design
In the design of fiber laser cutting machines, the open bed is favored by many manufacturing industries for its simple and flexible structure. The open bed is not only convenient for loading and unloading, but also more suitable for processing large-sized workpieces, but there are also some special operating requirements. The following will introduce the definition, characteristics, advantages, and disadvantages of the open bed design in detail.
Definition and Characteristics of Open Bed Design
The open bed design is a fiber laser cutting machine bed form without a shell covering. Its open structure allows the workpiece to enter and exit freely from multiple directions. Compared with the closed design, the open bed structure is simpler and easier to load and process larger workpieces. This design is usually used in scenes with high space requirements and is suitable for cutting large or extra-long materials, such as industrial steel, pipes, and large-scale plates. In addition, the open bed has strong ventilation, which helps to reduce the accumulation of high temperature or smoke during the cutting process.
Advantages of Open Bed Design
Easy Material Loading and Unloading
The barrier-free structure of the open bed allows materials to be loaded and unloaded from multiple angles, reducing the time of loading and unloading. This feature is particularly evident when handling large, heavy, or extra-long workpieces, which not only improves operating efficiency but also reduces dependence on loading and unloading equipment. For example, in industries such as shipbuilding and construction, it is often necessary to cut extra-long steel. The open design facilitates direct operation and improves production efficiency.
Suitable for Larger Workpieces or Continuous Processing
Since there is no space restriction of the shell, the open bed can easily accommodate larger workpieces, thus achieving barrier-free processing. This design also allows operators to perform continuous processing, which is suitable for long-term production needs, especially for batch production and assembly line application scenarios. For tasks that require long-term continuous cutting, the open bed can provide operators with more processing flexibility.
Enhanced Ventilation
The open bed has good air circulation because it is not constrained by a closed shell, which helps to keep the working area clean and the temperature stable. The smoke and heat generated during the cutting process can be quickly discharged and are not easy to accumulate around the machine, thereby extending the service life of the equipment and improving the cutting environment. This design is particularly suitable for occasions that require long-term stable operation and can effectively reduce the maintenance requirements of the equipment.
Disadvantages of Open Bed Design
Exposure to Laser Radiation
Since there is no shielding of a closed shell, the open bed design exposes the laser radiation directly to the outside. The operator and the surrounding environment are therefore more likely to be exposed to laser radiation, increasing the safety risk during operation. Protective equipment such as laser protective glasses and protective clothing are usually required during operation to prevent direct contact with laser radiation. In addition, companies may need to set up protective measures such as shielding fences or enclosures to improve the safety of the work area.
Debris Accumulation Problem
The open design has no protective shell, and the debris and smoke generated during the cutting process are easy to accumulate directly around the machine. This not only affects the cutting accuracy, but also may pollute the working environment and increase the frequency of cleaning and maintenance. In addition, the accumulation of debris may interfere with the laser path, thereby affecting the quality of cutting. For this reason, additional fume exhaust equipment or cleaning measures are usually required to deal with the debris to ensure a smooth cutting process.
Inadequate Control over Small Parts and Debris
When processing smaller or lighter parts, the open bed lacks the control of fragments and small parts of the closed structure, which can easily cause the processed materials to scatter or be damaged. Especially when processing small metal parts or fragile materials, the open bed is prone to parts falling off or being lost, affecting the final cutting quality and material utilization. Therefore, the open bed is usually more suitable for processing large materials, and additional fixing measures are required if small items need to be processed.
The open bed design is suitable for large materials and continuous processing applications and has the characteristics of easy loading and unloading and good ventilation. However, its exposed structure brings certain safety hazards and is insufficient in controlling debris. Therefore, when choosing a fiber laser cutting machine, companies need to consider whether the production needs and operating environment are suitable for the open bed design.
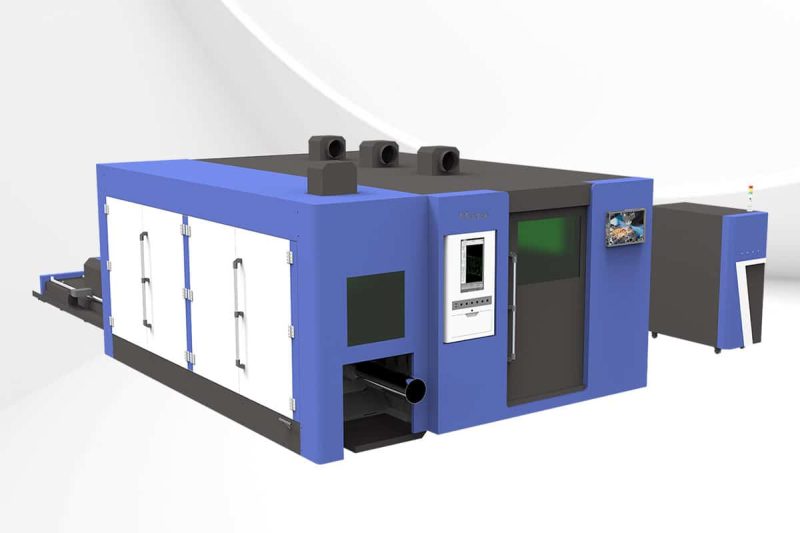
Understanding the Closed Bed Design
The closed bed design is widely used in fiber laser cutting machines, especially for scenes with high requirements for precision and safety. The closed shell isolates the cutting area from the outside world, providing higher safety and cutting stability, but also has certain loading and unloading restrictions. The following will introduce the definition, characteristics, advantages and disadvantages, and scope of application of the closed bed design in detail.
Definition and Characteristics of Closed Bed Design
The closed bed design is a type of fiber laser cutting machine bed that completely encloses the cutting work area in a safe shell. By isolating the external environment, the closed bed can effectively prevent external factors such as dust and airflow from interfering with the cutting process, while providing better laser radiation protection for operators. This design is usually used in situations where high-precision cutting is required and can provide more stable support for small or complex workpieces. The closed structure effectively improves the safety of the cutting process and ensures processing accuracy and stability. It is a common choice in precision industries such as medical devices and electronic manufacturing.
Advantages of Closed Bed Design
Laser Radiation and Debris Protection
The fully enclosed design of the enclosed bed can effectively shield laser radiation, prevent operators from being directly exposed to high-energy lasers, and ensure the safety of the use process. The enclosed structure also limits the diffusion of debris and smoke generated during the cutting process inside the machine, preventing debris from affecting the cutting quality and ensuring a clean operating environment. In addition, the enclosed design is usually equipped with a special exhaust or filtration system that can effectively remove internal smoke and harmful gases, providing additional protection for safe operation.
Solid Support for Small Workpieces
The closed bed structure design is more stable, which can provide better support for small or thin workpieces, ensuring that the material will not move due to vibration or airflow during high-precision processing. This stability makes the cutting process smoother, helps to maintain the accuracy of the cutting line, and reduces errors. In addition, the closed bed is also suitable for high-precision and meticulous processes, ensuring the uniformity and consistency of the final cutting effect, which is very suitable for the processing of small workpieces such as medical devices and precision electronic components.
Reduce External Influences
The closed structural design completely isolates the working area in the closed shell, significantly reducing the impact of dust, airflow, and other external factors on the cutting process. The stability of the cutting environment is greatly enhanced, helping to ensure stable focusing of the laser beam and reducing errors caused by airflow or dust interference. This feature gives the closed lathe a significant advantage in situations where high-quality, meticulous cutting is required and is especially suitable for production environments with high cleanliness requirements.
Disadvantages of Closed Bed Design
Difficult Loading/Unloading
The shell structure of the closed bed design limits the loading and unloading of materials to a certain extent, especially for larger or irregularly shaped workpieces, loading and unloading may become more cumbersome. Operators need to enter and exit materials through smaller openings, which may increase the difficulty of fixing and positioning the workpiece on some special occasions, affecting production efficiency. For this reason, many closed bed cutting machines are also equipped with automatic loading and unloading devices to facilitate more efficient material handling without opening the shell.
Limited Processing Space
The internal space of a closed bed is relatively limited. Due to the existence of the shell structure, it can usually only accommodate workpieces of a certain size. For tasks that require processing large-format materials or extra-long workpieces, the applicability of a closed bed is limited to a certain extent. Therefore, a closed bed is more suitable for processing smaller or standard-sized materials and is not suitable for scenarios that require large space operations. In addition, the closed nature of the shell also limits the diversity of materials, so when choosing a closed bed, it is necessary to fully evaluate the size and type of the processing material.
The closed bed design provides ideal support for machining tasks with high precision requirements due to its effective control of laser radiation, dust, and debris, and is especially suitable for precision machining of small or thin workpieces. However, due to the limitations of the closed shell, its limitations in loading and unloading and space are obvious. When choosing, enterprises should evaluate whether the closed bed design meets the operational requirements based on specific production needs and the characteristics of the processed materials to ensure cutting quality and production efficiency.
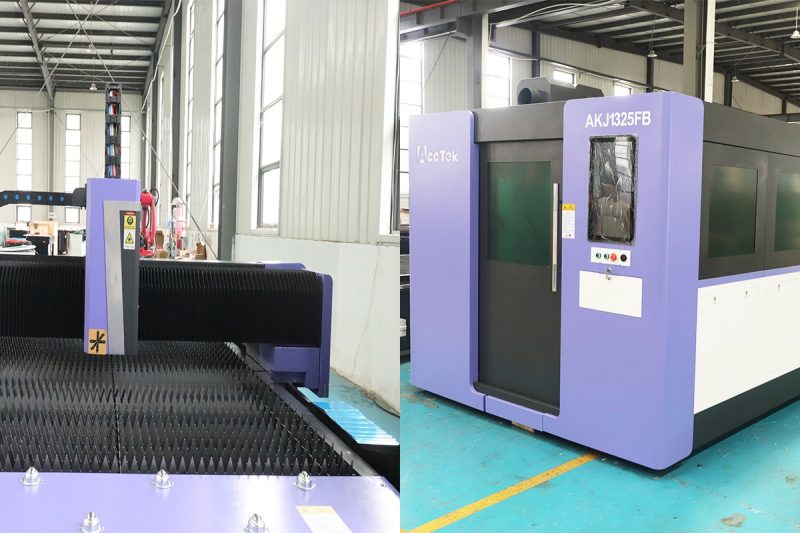
Comparison of Open and Closed Bed Designs
Different bed designs have a significant impact on the operating experience, cutting accuracy, safety, and applicability of fiber laser cutting machines. Open and closed lathes each have their advantages and disadvantages. The following will compare the characteristics and applicable scenarios of the two designs in detail from six aspects: cutting accuracy, material compatibility, throughput and efficiency, cost, versatility, and safety.
Cutting Accuracy
Closed Bed Guarantees Accuracy
The closed bed design isolates the cutting area through a closed shell, greatly reducing the interference of dust, airflow, and other external factors on cutting accuracy. This structure can effectively maintain the stability of the laser beam and prevent floating dust or temperature fluctuations in the processing environment from affecting laser focus, thus excelling in smaller parts or precision cutting. The closed bed is usually suitable for one-off production tasks that require extremely high precision, especially in manufacturing scenarios that require high precision and meticulousness.
Precision Challenges of Open Beds
The open bed is relatively weak in terms of protection and environmental control. Since there is no shell isolation, the cutting area is easily affected by factors such as airflow and debris accumulation. This design performs well in mass production with low precision requirements but may produce certain errors for tasks with high precision requirements. Therefore, the open bed is suitable for processing large workpieces that do not require extremely high precision but may be slightly insufficient in situations where precise cutting is required.
Material Compatibility
Material Suitability for Open Bed
The open bed design is suitable for processing large-sized workpieces, especially in the cutting of long plates or coils. Since the open structure can easily load materials from all directions, operators can place and position large workpieces more freely without being restricted by the space in the cutting area. This makes the open bed very suitable for cutting long materials of metal, wood, or plastic, which is particularly common in industrial production that requires large-area cutting.
Material Limitations of Closed Bed
The closed bed is slightly limited in terms of material compatibility. Due to the physical space limitations of the shell, it is usually only suitable for the processing of small and medium-sized workpieces. The closed design is mainly designed for small materials or complex parts with high precision and fineness requirements, and it is difficult to process large-sized materials. The closed bed is suitable for the production of small-sized precision parts, such as electronic components, medical device components, etc., whose material types and sizes are limited by internal space.
Throughput and Efficiency
High Efficiency with Open Bed
Due to the design characteristics of the open bed, the process of loading and unloading materials is simpler and more convenient, which allows the machine to quickly change processing materials and improve production efficiency. The open structure reduces the obstacles of manual material handling and is suitable for use in scenarios that require high-frequency loading and unloading. Therefore, the open bed is very suitable for batch production or assembly line processing, which can increase production throughput and reduce process changeover time.
Precision Production of Closed Bed
The loading and unloading process of the closed bed is slightly more inconvenient than that of the open structure, but its closed design can ensure the accuracy and consistency of processing. This structure helps to improve accuracy and processing consistency and is very suitable for production scenarios that require high quality and consistency of each batch of products. For example, in the field of precision electronics manufacturing, the closed bed can provide high-precision and high-consistency cutting effects to meet the needs of mass production of smaller workpieces.
Cost Considerations
Cost Investment of Closed Bed
The closed bed design has a higher manufacturing cost, so the price of the overall equipment is usually much higher than that of the open bed. The closed shell structure requires more complex design and manufacturing processes. In addition, to ensure the durability and stability of the shell, the material selection is usually more stringent. However, in the long run, the high precision and safety of the closed bed can reduce the rework rate in the production process and may bring cost savings in the high-end production field.
Economical Open Bed
The open lathe has a simple structural design and low manufacturing costs, making it suitable for companies with limited budgets but efficient production needs. The economical nature of the open lathe makes it more popular among budget-sensitive enterprises. Especially in areas with lower requirements for laser radiation protection, the open lathe can provide a more cost-effective option. In addition, the cost of subsequent maintenance and operation of the open structure is relatively low, so it has significant economic advantages in high-volume production scenarios.
Versatility
Flexibility of an Open Bed
The open bed is more flexible and can adapt to materials of different shapes and sizes. In terms of flexible deployment in the production environment, the installation and application of the open bed is relatively simple, and it is highly adaptable and suitable for use in a variety of industry environments. The versatility of the open structure makes it more widely used in different industries, such as furniture, decorative materials, and other fields that require large-size material processing.
The Suitability of the Closed Bed for Specific Occasions
The closed bed design is more advantageous in situations where high precision and cleanliness are required, such as in the medical, aerospace, and other industries. Its closed structure can provide a stable cutting environment to ensure that the workpiece surface is not contaminated or damaged by the outside world. In these fields, the special advantages provided by the closed bed can meet the strict precision and quality control requirements and are very suitable for specific situations with high precision and high requirements.
Safety
Safety Protection of Closed Bed
The fully enclosed shell structure of the closed lathe has significant advantages in terms of safety. It can effectively isolate laser radiation and debris generated by cutting, and protect the operator from laser and debris. The closed structure can also prevent the spread of smoke and dust and ensure the air quality of the operating environment. Therefore, the closed bed design is more suitable for production environments with higher safety requirements and can protect the health and safety of workers. It is especially suitable for high-power cutting machines where laser cutting is more dangerous.
Safety Risks of Open Bed
Compared with the closed structure, the open bed design lacks the isolation protection of the shell, so laser radiation and debris are easily exposed directly in the operating area. This design has certain safety risks during use, especially in high-power laser applications, which may cause the operator to be affected by laser radiation or cutting debris. Therefore, for the application scenarios of the open bed, additional safety protection equipment and protective facilities are often required to reduce operational risks.
In general, open and closed bed designs have their advantages. The open bed has higher flexibility and cost advantages in terms of material compatibility and production efficiency, while the closed bed performs well in terms of precision, safety, and specific use scenarios. When choosing a bed design, companies need to consider production needs, budget, safety, processing accuracy, and other aspects to find the bed type that best suits their application.
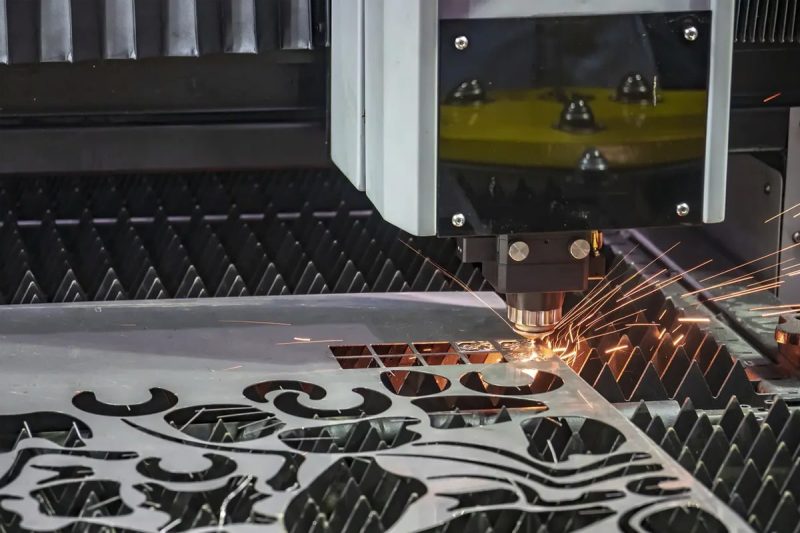
Application Considerations for Two Bed Designs
The application of open and closed beds in laser cutting equipment has its characteristics. To ensure safety and achieve the best cutting effect, the following will introduce in detail the operating precautions for using open and closed bed designs.
Application Considerations for Open Bed Design
Operator Protection
In an open bed cutting environment, operators need to pay special attention to protective measures because the laser beam and debris are exposed. Operators should be equipped with special safety gear, such as laser safety glasses, protective masks, and work gloves, to effectively reduce the impact of high-energy laser radiation on the eyes and skin. In addition, to reduce the risk of exposure to dust and debris, consider adding protective fences or barriers, especially when high-power laser equipment is running.
Cleaning and Maintenance of Cutting Area
Since the open bed design makes the cutting area completely exposed, debris and dust are easily generated during the cutting process. If this debris accumulates for a long time, it may interfere with the path of the laser beam or affect the laser focus, thereby reducing the cutting quality. Therefore, it is necessary to formulate operating procedures for regular cleaning of the cutting area, especially in a high-frequency continuous production environment. Keeping the area free of debris accumulation and well-ventilated can help improve processing accuracy and equipment life.
Applicable Materials and Workpiece Sizes
The open bed design is very suitable for processing large-sized or long materials, such as metal sheets, coils, etc. Because the bed is open, the operator can easily place and position the material, which facilitates the cutting of large workpieces. In addition, the open bed design can meet the needs of rapid switching of multiple materials, so it is particularly suitable for occasions where large quantities of irregular-sized materials need to be processed, such as continuous production processes in industries such as construction and automotive manufacturing.
Noise and Air Flow Management
Since the open bed has no closed structure, the noise generated during the cutting process is more obvious. Therefore, noise management in the open work area is also an aspect worthy of attention, especially in long-term processing, which has a greater impact on the surrounding environment and operators. In addition, in the case of poor ventilation or large air flow, the stability of cutting may be affected. A proper exhaust and dust removal system can help reduce the interference of airflow on the laser cutting path.
Application Considerations for Closed Bed Design
Inspection and Maintenance of Closure Devices
When using laser cutting equipment with a closed bed, the sealing and integrity of the closed shell must be checked before operation. The closed device must remain intact to prevent the laser beam from leaking out and ensure the safety of the operator during operation. If the closed device is found to be damaged or not tightly sealed, it should be repaired or replaced immediately to ensure the safety of the cutting environment. In addition, the operator must also pay attention to checking the tightness of the shell to ensure that the beam will not leak into the external environment during the cutting process.
Cleaning and Maintenance Inside the Shell
Although the cutting area of the closed bed design is isolated, a certain amount of dust, debris and cutting smoke will accumulate inside the shell during long-term use. These impurities may interfere with the propagation path of the laser beam and affect the cutting accuracy. Therefore, to ensure the cutting effect, the operator needs to clean the inside of the shell regularly, especially in situations where high precision is required. Keeping the inside clean is the key to ensuring cutting quality. Use dust-free cloth or special tools when cleaning to avoid damaging the equipment or leaving secondary contamination.
Suitable for Precision Machining
The closed bed design is more suitable for precision machining occasions with extremely high cutting quality requirements due to its closed structure. This type of design is very suitable for small parts and workpieces with complex shapes, ensuring consistency and accuracy during the cutting process. In addition, the closed structure reduces the interference of dust and airflow in the external environment on cutting, which is an ideal choice for occasions that require a highly clean environment (such as medical device manufacturing, electronic equipment production, etc.).
Safety Monitoring and Ventilation System
In the closed bed design, since the cutting area is in a confined space, special attention must be paid to the temperature and airflow conditions inside the shell during operation. The ventilation and dust removal system in the shell should be checked regularly to ensure safety in a closed environment. Harmful gases or high temperatures may be generated during the cutting process. It should be ensured that the shell has good exhaust equipment to discharge the smoke and dust generated by cutting in time to maintain the normal operation of the equipment and ensure the health and safety of the operator.
Real-Time Monitoring of the Cutting Process
The closed bed structure limits the ability to directly observe the cutting process, so in some cases, it is necessary to install a monitoring camera or observation window to monitor the progress of the cutting process in real-time. Ensure that possible abnormal situations, such as cutting path deviation, spark abnormality, etc., can be quickly detected and identified. This not only helps to ensure the quality of cutting but also reduces the incidence and loss of machine failures.
Whether it is an open or closed bed design, it has its own unique operating precautions and maintenance requirements. The open bed design focuses on the convenience of operation and material compatibility, but has higher requirements for operator protection and regular cleaning; the closed bed design emphasizes safety and cutting accuracy but requires strict maintenance of the shell structure. When selecting and using laser cutting machines, enterprises must follow the above precautions according to production requirements and safety needs to ensure the stability of equipment performance and the safety of the operation process.
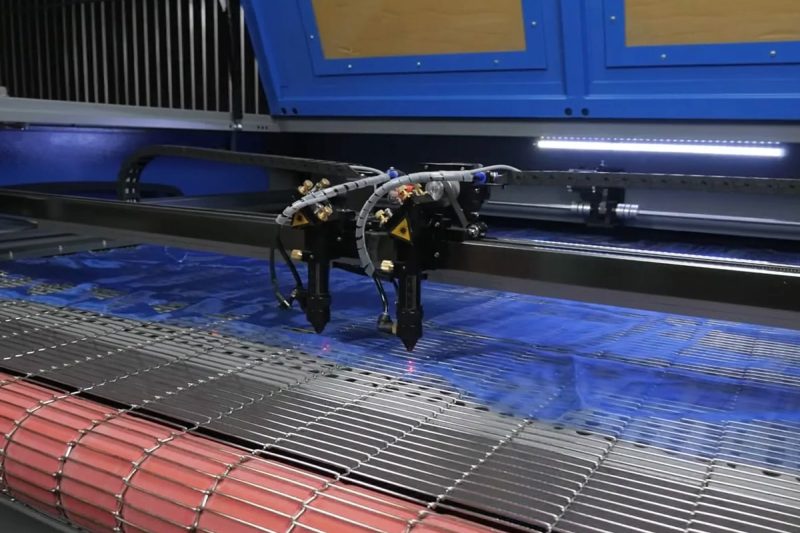
How to Choose the Right Bed Design
Choosing the right laser-cutting machine bed design can help companies maximize efficiency and minimize costs in a specific production environment. The following discusses in detail how to make the best choice from four aspects: material type and size, production volume and workflow requirements, available space and facility layout, budget constraints, and long-term goals.
Material Type and Size
Applicability for Large Sizes and Long Materials
The open bed design is more adaptable to large-sized and long materials. Since there is no restriction of a closed shell, the loading and positioning of materials is very convenient, especially suitable for scenes that require processing large pieces of metal sheets or long coils. The open structure allows the operator to access the material from multiple directions and easily adjust the position when necessary. Large structural parts such as building components, ship parts, and large equipment housings often require open-bed cutting machines to ensure a smooth cutting process.
Applicability for Small Precision Parts
The closed bed is more suitable for small and high-precision parts. The closed structure provides a stable cutting environment, which can effectively reduce the interference of external airflow and dust on the cutting path. This is especially important for precision processing occasions that require high precision and consistency, such as the production of electronic components, medical devices and small equipment parts. For these occasions, the design of the closed bed ensures that the laser cutting machine achieves ideal accuracy when processing small-sized materials.
Production Volume and Workflow Requirements
High Volume and Fast Turnaround Production
In a high-volume, fast-paced production environment, an open bed can provide greater operational flexibility. Operators can load, unload, and adjust materials more conveniently, greatly improving production efficiency. Therefore, the open bed design is particularly suitable for production lines that require frequent material changes, ensuring fast cutting and efficient turnover, such as automotive manufacturing, metal processing, and other industries that require large-scale production. For some long-term production of large workpieces, the open bed not only helps to speed up the production process but also supports multiple positioning operations.
High-Precision, Low-Volume Processing Requirements
The closed bed is more suitable for small-volume production with high precision requirements. The closed structure reduces the interference of external factors during the cutting process, helping the equipment to achieve higher precision. Therefore, for precision manufacturing and one-time small-batch orders with high requirements, the design of the closed bed can ensure the stability and consistency of the cutting results. In the fields of scientific research experiments, aerospace, and medical equipment, the high-precision advantages of the closed bed are particularly obvious, helping companies maintain high-quality product standards.
Available Space and Facility Layout
Open Bed for Spacious Workshops
Open bed design usually requires a larger floor space due to its open structure, especially when large materials need to be rotated or moved. Therefore, if the company has a spacious production workshop or factory, an open bed is a good choice. This layout also allows for a larger operating space, facilitating the arrangement of multiple machines and the movement of materials. In addition, the working area around the open bed makes it easier to arrange auxiliary equipment, such as material stacking, pre-processing, and post-processing workbenches.
Enclosed Bed for Compact Workspaces
For workshops with limited space, the compact structure of the enclosed bed is an ideal choice. The enclosed design not only saves space but also provides a safe cutting environment, effectively reducing the potential safety hazards caused by limited space. Especially in workshops with multiple workstations, the compact structure of the enclosed bed helps to make rational use of space and protect the safety of operators by reducing the leakage of laser radiation. The structural design of the enclosed bed is suitable for small, high-precision processing environments in the fields of electronic manufacturing, precision machinery, etc.
Budget Constraints and Long-Term Goals
Low-Cost Applicability of Open Bed
Open lathes are relatively low-cost to manufacture and maintain, making them ideal for start-ups or small businesses on a budget. The open design usually does not require complex housings and sealing devices, reducing the initial cost and subsequent maintenance costs of the equipment. For companies, this means more budget can be invested in expanding materials and production processes while achieving efficient production targets. Especially in industries that value cost-effectiveness, such as metal processing and furniture manufacturing, open lathes can help companies achieve significant production gains in the short term.
Long-Term Return on Investment for Closed Bed
Although the initial investment of the closed bed is high, in the long run, the closed design can provide higher precision and safety, thereby reducing the error rate and improving product quality. Therefore, if the company pursues the high-end market and focuses on the long-term development of brand and quality, the closed bed is more advantageous. Its stable cutting accuracy can bring higher market competitiveness to the company, especially suitable for industries with extremely high precision requirements such as aerospace and medical equipment manufacturing. In addition, the safety design of the closed bed can better protect the operator in long-term use, which helps the company establish a good reputation for safe production.
Choosing the right bed design depends on the company’s production needs, processing materials, space conditions, and budget. Open beds are suitable for high-volume production lines that require high flexibility and fast operation, especially when processing large-sized materials; while closed beds are suitable for production environments that require high precision and higher safety. Companies should consider current work needs and long-term development goals to choose a bed design that suits them.
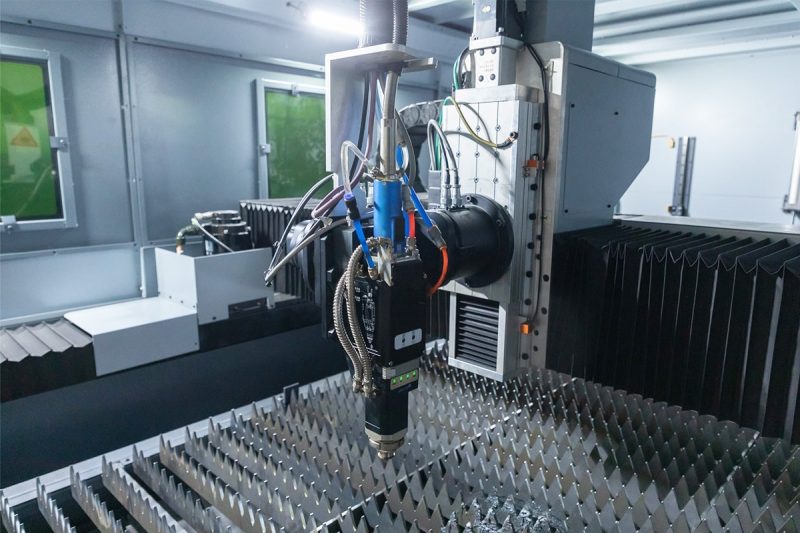
Summarize
When choosing a laser cutting machine, the bed design is a crucial factor. Different bed designs are suitable for different production needs, working environments, safety requirements and budgets. Therefore, companies need to consider these factors comprehensively to choose the most suitable equipment. As an industry-leading laser cutting machine supplier, AccTek provides a variety of bed designs, including open beds and closed beds, to meet the needs of various production scenarios, helping you improve efficiency, ensure safety, and optimize production costs.
Open Bed Design: Suitable for Large-Size Workpieces and Efficient Production
The open bed design is ideal for processing large-size materials and for environments that require fast and efficient production. Its open structure allows operators to easily load, unload, and adjust materials, greatly improving production efficiency. In production environments that require processing long plates or large-size coils, the open bed can provide more flexible operating space and is the first choice for mass production in industrial manufacturing, metal processing, and other fields.
In addition, the open bed design is suitable for continuous processing production lines, especially those factories that have a high demand for loading and unloading convenience. Whether it is cutting metal, plastic, wood, or other large-size materials, the open bed can easily cope with it. More importantly, the initial investment of the open bed is low, and it is a cost-effective choice for companies with limited budgets.
At AccTek, we provide efficient and reliable open-bed laser cutting machines to meet your needs for efficient production. Our equipment uses advanced technology to ensure stable and accurate cutting quality while providing an easy-to-use operating experience to help your company achieve fast production and efficient operation.
Closed Bed Design: Precision Machining and Safety Assurance
If your production environment has higher requirements for cutting accuracy, cleanliness, and employee safety, the closed bed design is your ideal choice. The closed bed can effectively prevent interference from the external environment, such as dust, airflow, etc., to ensure the consistency and stability of the precision during the laser cutting process. For precision parts, thin materials, and high-precision industrial applications, the closed bed can provide more reliable protection.
In addition, the closed structure design provides higher safety, can effectively prevent the leakage of laser radiation, and controls debris and smoke within the cutting area to ensure operator safety. Especially in high-end manufacturing industries such as precision machining, electronic manufacturing, and aerospace, the advantages of closed lathes are even more significant.
At AccTek, we understand the importance of precision and safety, especially in complex and demanding applications. Our enclosed bed laser cutting machines use cutting-edge design and technology to not only improve cutting accuracy but also ensure a safe and clean operating environment. Our equipment is suitable for a variety of high-precision processing tasks, helping you maintain leading production efficiency and excellent product quality.
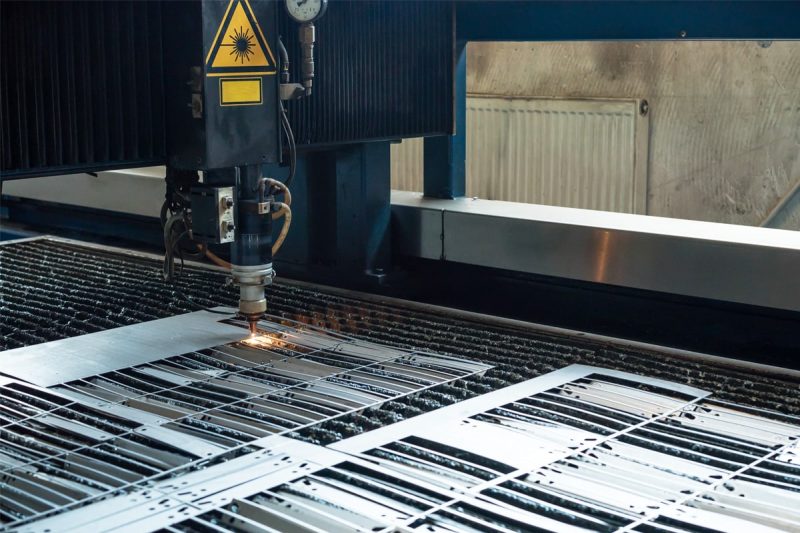
Why Choose AccTek's Laser Cutting Machine?
Whether you need an open bed or a closed bed, AccTek can provide high-quality laser-cutting machines to meet the diverse needs of different companies. Our equipment not only has efficient and precise performance but also excels in safety, durability, and maintenance convenience. We are committed to providing customers with advanced technology, high-quality services, and tailored solutions to help you increase productivity and reduce production costs.
By choosing AccTek’s laser cutting machine, you will experience:
- Efficient production: The open bed design provides fast loading and unloading, improving production efficiency.
- Excellent precision: The closed bed design ensures cutting accuracy and meets the needs of precision processing.
- Employee safety: The closed structure reduces laser radiation leakage and ensures the safety of the operator.
- Flexibility and reliability: Adapt to different production needs and provide long-term stable operation.
Our customers are all over the world, including leading companies in many industries. They all choose AccTek’s laser cutting machines as a powerful assistant to improve production efficiency and product quality. Whether you are a large-scale production company or a company pursuing high-precision, low-volume processing, we can provide you with the most suitable laser-cutting solutions.
Contact us to learn more about our laser cutting machines and help you make the best choice for your needs. Choose AccTek, we will be your reliable partner to improve production efficiency, ensure employee safety, and optimize production costs!
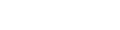
Contact information
- [email protected]
- [email protected]
- +86-19963414011
- No. 3 Zone A, Lunzhen Industrial Zone,Yucheng City , Shandong Province.
Get Laser Solutions