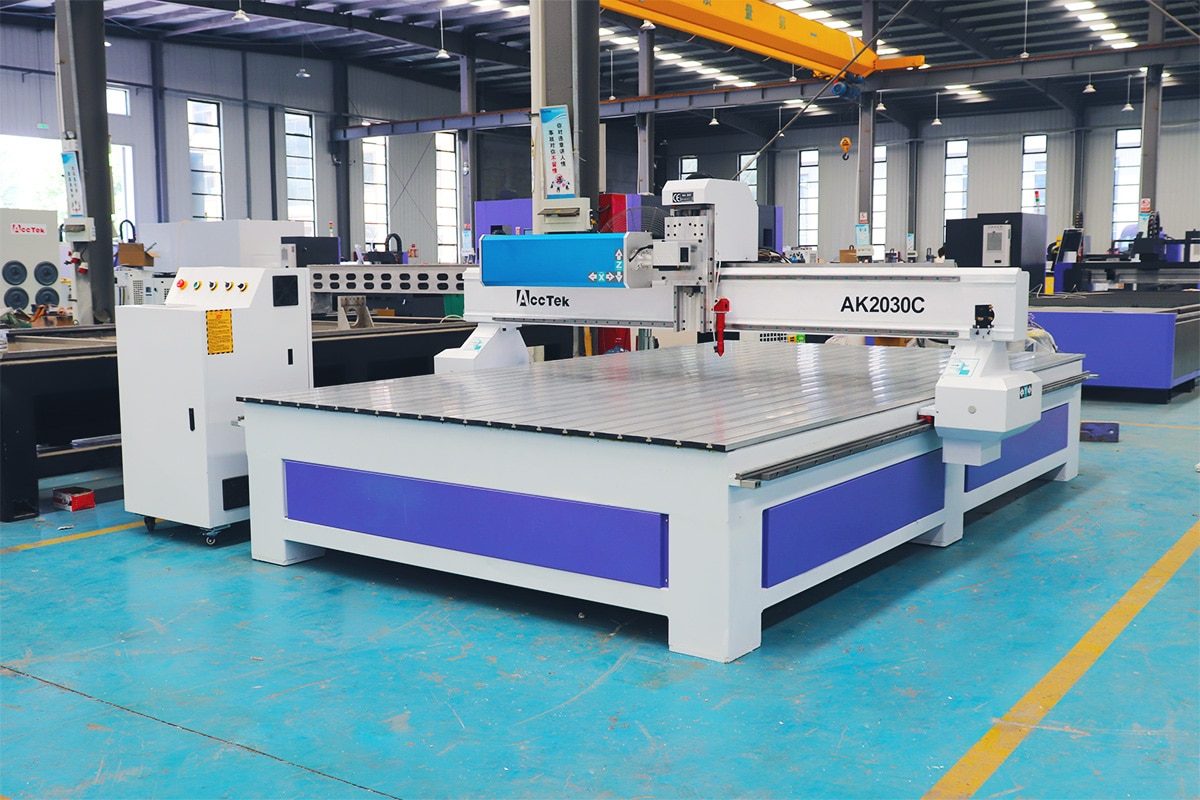
How to Choose the Power of a CO2 Laser Cutting Machine: A Comprehensive Guide
CO2 laser cutting technology is widely used in the manufacturing industry for its high precision and high efficiency. Laser power is one of the key factors affecting the cutting effect, which determines the cutting speed, depth, and material adaptability. Choosing the right power can not only improve production efficiency but also ensure cutting quality. Different materials and thicknesses have different power requirements, so it is important to understand the basic concepts and selection principles of laser power. This article will explore the basic principles of CO2 laser cutting, the relationship between power and material thickness, the factors that affect power selection, and how to choose the right laser power for different materials, helping you optimize the cutting process and achieve the best results.
Table of Contents
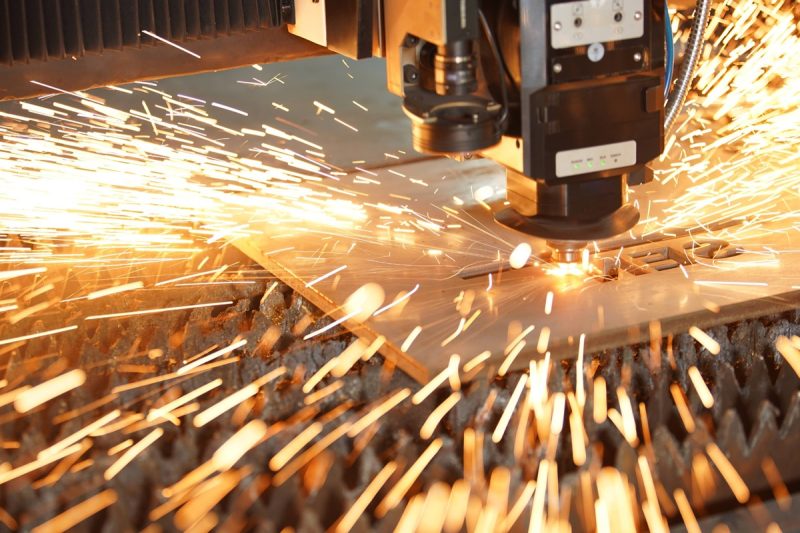
The Basic Principles of CO2 Laser Cutting
CO2 laser cutting machine uses CO2 laser as a cutting source. The laser beam generated by the CO2 laser generator is focused on the surface of the cutting material through an optical system to achieve high-temperature and high-energy laser beam concentration. The laser beam interacts with the surface of the material, and the material melts or vaporizes at high temperatures to form an incision. Laser power is one of the key factors in the cutting process, which determines the energy output of the laser beam, thereby affecting the cutting speed and depth. The incision during CO2 laser cutting is very narrow and smooth, which is suitable for high-precision processing of a variety of materials such as metal, wood, and plastic.
CO2 Laser Cutting Working Principle Description
CO2 laser generators generate lasers by converting electrical energy into light energy. The specific process is as follows:
- Excitation of CO2 gas: In CO2 laser generators, electrical energy is used to excite CO2 molecules into a high-energy state. This excitation is usually achieved by electrical discharge.
- Photon generation: When the excited CO2 molecules return to the ground state, they release photons. Due to the mirror system in the laser cavity, these photons are repeatedly reflected in the cavity, forming a light amplification effect, and finally producing a beam of high-intensity laser.
- Beam output: The laser beam is guided out of the laser cavity through a partially transmissive mirror, and is further focused into a high-energy density beam through a series of optical lenses and lenses.
- Focusing and cutting: The focused laser beam forms a high-temperature area on the surface of the material, causing the material to melt or vaporize rapidly. The cutting head is usually equipped with an auxiliary gas (such as oxygen or nitrogen) to blow away the molten material to form a precise cut on the workpiece.
Overview of the Cutting Process and Its Relationship to Laser Power
During CO2 laser cutting, the laser beam first contacts the surface of the material and forms a high-temperature area at the contact point. As the laser beam moves along the predetermined path, the material is melted, vaporized, or directly ablated under the high temperature of the laser, forming a cut. Laser power plays a vital role in the cutting process. It determines the energy output of the laser beam and directly affects the cutting speed, cutting depth, and cutting quality.
- Cutting speed: The higher the laser power, the faster the cutting speed. Higher power allows the laser to melt more material in a shorter time, thereby improving production efficiency. However, if the power is too high, it may cause the material surface to overheat and affect the cutting quality.
- Cutting depth: The laser power is proportional to the cutting depth. Higher laser power allows deeper cutting, but this may also increase the heat-affected zone at the cutting edge, causing deformation or slag at the edge.
- Cutting quality: The laser power setting needs to match the material characteristics. For thin materials, lower laser power can ensure the smoothness and precision of the cutting edge; for thick materials, higher power is required to ensure the integrity of the cutting.
In summary, CO2 laser cutting technology achieves high-precision and high-speed cutting effects through the interaction between high-energy laser beams and materials. Laser power is one of the key parameters affecting the cutting process. Reasonable adjustment of power can achieve the best cutting effect.
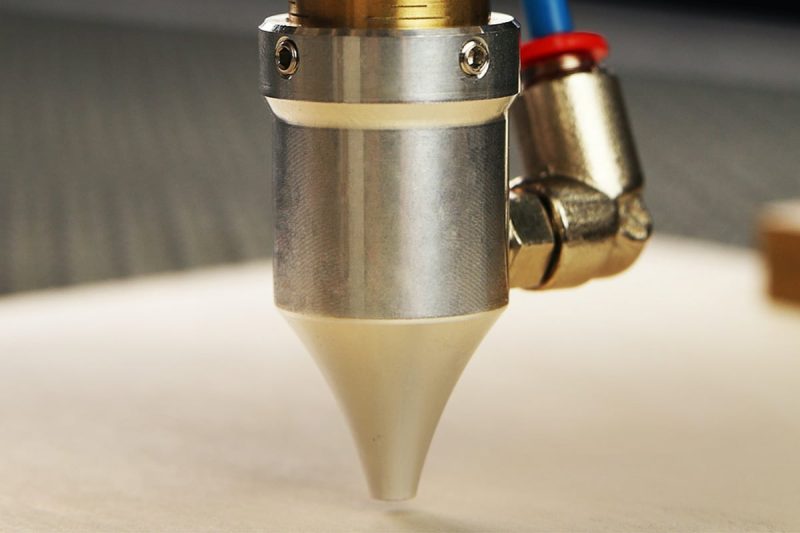
Understanding Laser Cutting Power
Laser cutting power is one of the most critical parameters in the laser cutting process, which determines the energy output of the laser beam, thus directly affecting the efficiency, depth and quality of cutting. Understanding laser cutting power not only helps to optimize the cutting process, but also improves production efficiency and reduces processing costs.
Definition of Laser Cutting Power
Laser cutting power refers to the energy intensity output by the laser during the cutting process, usually expressed in watts (W). This power value determines the energy density of the laser beam and directly affects the interaction between the laser and the material surface. During the laser cutting process, the laser converts electrical energy into light energy, and the generated laser beam is focused into a very small area through the optical system to form a high-energy-density spot. This spot generates extremely high temperatures on the surface of the material, causing the material to melt, vaporize, or ablate rapidly, thereby achieving cutting.The higher the power, the stronger the energy of the laser beam, which can melt or vaporize the material faster, so high-power lasers are usually used to cut thicker materials or increase cutting speeds. However, the higher the power, the better. Excessive power may cause the surface of the material to overheat, thereby affecting the cutting quality, such as causing rough cutting edges or excessive slag. Therefore, the selection of laser power should be adjusted according to the specific cutting requirements and material characteristics to achieve the best cutting effect.
Relationship Between Laser Power, Speed and Material Thickness
There is a close relationship between laser power, cutting speed and material thickness, which together determine the effect and efficiency of laser cutting.
- Laser power and material thickness: The thicker the material, the higher the laser power is required to ensure that the laser beam can penetrate the entire material thickness. For thin materials, using too high a power may cause excessive melting of the material or burnt edges, so medium and low power settings are usually selected. For thick materials, if the power is insufficient, the laser beam may not be able to completely cut through the material, resulting in failed or incomplete cutting.
- Material thickness and cutting speed: For thicker materials, it is usually necessary to reduce the cutting speed to ensure that the laser beam has enough time to penetrate the material thickness and make a thorough cut. Conversely, for thinner materials, the cutting speed can be increased, but it is necessary to ensure that the laser power is appropriate to avoid overheating the material or incomplete cutting.
In actual application, the relationship between laser power, cutting speed, and material thickness is a dynamic balance. By adjusting these parameters, operators can optimize cutting results and ensure high-quality and efficient processing. The appropriate power setting can not only improve production efficiency but also reduce material waste and the need for subsequent processing, thereby improving overall productivity.
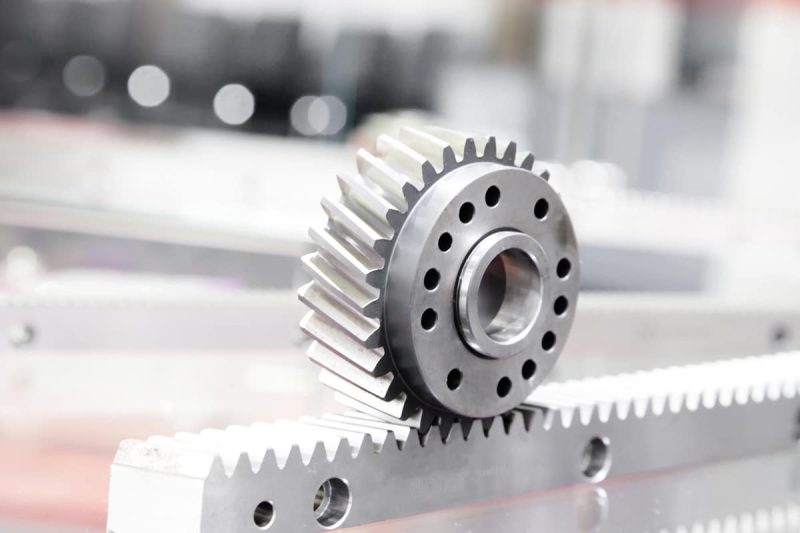
Factors Affecting Laser Cutting Power Selection
In the laser cutting process, choosing the right laser power is the key to ensuring cutting quality and efficiency. Multiple factors affect the choice of laser power, including the type and thickness of the material, the cutting speed requirements, the required cutting quality, and the machine capacity and lens configuration. The following is a detailed introduction to these factors and their impact on laser power selection.
Material Type and Thickness
The type of material is the primary factor that determines the laser cutting power. Different materials have different absorption and reflectivity to the laser, which directly affects the required power. For example:
- Metallic materials: Metals usually have a higher reflectivity to the laser beam, especially materials such as aluminum and copper. Therefore, these materials usually require higher laser power to achieve effective cutting. In addition, materials such as steel and stainless steel also require higher power to ensure cutting accuracy and speed due to their higher melting points and densities.
- Non-metallic materials: Such as wood, acrylic, plastic, etc., usually have a higher absorption rate to the laser, so they can be cut with lower laser power. However, these materials are easy to burn or melt, so when choosing the power, the thermal sensitivity of the material needs to be considered.
Material thickness is another important factor. Thick materials require higher laser powers to ensure that the cutting laser can penetrate the full thickness of the material. Thin materials can usually use lower powers, but you need to make sure the power is not too high to avoid excessive melting or burning of the edges of the material.
Cutting Speed Requirements
Cutting speed refers to the speed at which the laser cutting head moves across the surface of the material. There is a direct relationship between laser power and cutting speed: higher laser power can support faster cutting speeds because it can provide enough energy to quickly melt or vaporize the material.
However, the cutting speed requirement depends not only on production efficiency but also needs to match the characteristics and thickness of the material. If the cutting speed is too fast, the laser may not have enough time to completely cut through the material, resulting in rough cutting edges or incomplete cutting. On the contrary, although the cutting speed is too slow, it can ensure cutting quality, but it will reduce production efficiency. Therefore, when setting the cutting speed, the laser power must be adjusted according to the type and thickness of the material to find the best balance between speed and power.
Required Cutting Quality
Cutting quality is usually measured by the smoothness, precision, and edge clarity of the cut. Laser power directly affects these quality indicators:
- Smoothness and precision: Higher laser power can melt the material more quickly and reduce the heat-affected zone of the material, resulting in smoother cut edges and higher precision. However, too high power may cause excessive melting of the cut edge, affecting smoothness.
- Edge clarity: For some applications, such as high-precision electronic components or precision mechanical parts processing, very clear, burr-free cut edges are required. In this case, it may be necessary to precisely control the laser power to ensure that the quality of the cut edge does not become rough or irregular due to excessive temperature.
When considering the required cut quality, the choice of laser power also needs to be combined with the cutting speed and material thickness to achieve the desired effect.
Machine Capabilities and Lens Configuration
Machine capabilities include the maximum output power of the laser generator, stability, and the quality of the optical system. Different laser cutting machines have different power ranges, so when choosing a cutting power, the actual capabilities of the machine must be considered. If the required power exceeds the maximum output capacity of the machine, the cutting effect will not be as expected. In addition, the stability of the laser generator will also affect the continuity and accuracy of the cutting.
Lens configuration is also one of the important factors affecting the selection of laser power. The focal length and quality of the focusing lens determine the focusing ability of the laser beam, which affects the accuracy and depth of the cutting. Lenses with shorter focal lengths are suitable for cutting thinner materials and can provide higher focusing accuracy, but the power may need to be slightly adjusted. Conversely, lenses with longer focal lengths are suitable for cutting thicker materials and can provide deeper cutting, but higher laser power may be required to maintain cutting quality.
In actual applications, machine capabilities and lens configurations determine the available range of laser power. Operators need to reasonably adjust the laser power according to the specific machine configuration to ensure that the cutting effect reaches the best level.
Choosing the right laser cutting power requires comprehensive consideration of material type and thickness, cutting speed requirements, required cutting quality, as well as machine capabilities, and lens configuration. These factors are interrelated and together determine the final effect of laser cutting. In actual operation, reasonable adjustment of these parameters can help companies improve production efficiency, reduce costs, and ensure high-quality cutting results.
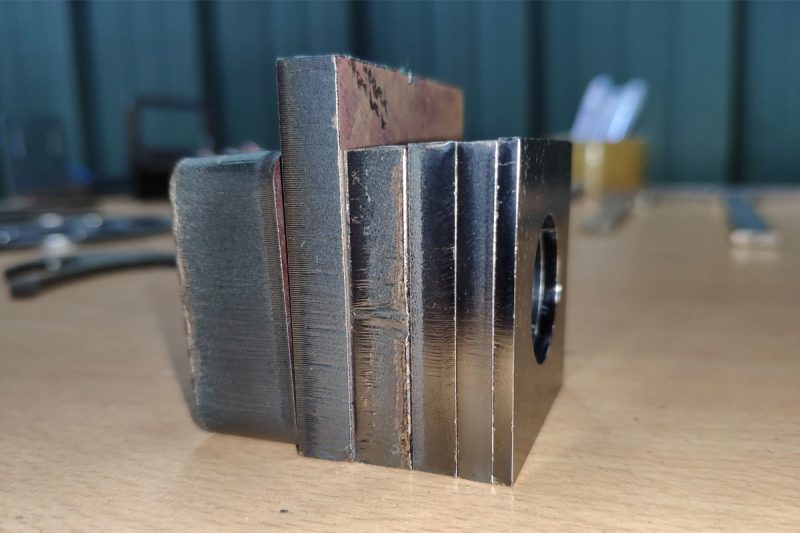
Power Selection Guide for Different Materials
During the laser cutting process, different materials have different absorption and reflection characteristics of lasers, so it is necessary to select the appropriate laser power according to the type and thickness of the material. The following is a guide to laser power selection for common materials, including metals, and non-metallic materials (such as acrylic, wood, and plastics), as well as composites and specialty materials.
Metal
In laser cutting, CO2 laser cutting machines are usually suitable for thinner metal sheets, but are less recommended for thicker metal sheets. For metals smaller than 3mm like carbon steel and stainless steel, a 600W CO2 laser cutting machine can cut efficiently and even achieve high-quality cutting edges. However, as the metal thickness increases, the cutting speed and efficiency decrease significantly, resulting in poor results. Therefore, for thicker metal sheets, fiber laser cutting machines are a more suitable choice.
Non-Metallic: Acrylic
Acrylic is a commonly used laser cutting material with good laser absorption and low melting point:
- Thin acrylic (5-12mm): Smooth cutting edges can usually be achieved using a low power (60W-80W) laser generator. Lower power can reduce material deformation and edge burning.
- Thick acrylic (12-30mm): For thicker acrylic, slightly higher power (80W-180W) is required, but the power should still be selected carefully to avoid overheating the edge, causing material deformation or slag.
Non-Metal: Wood
Wood has a relatively low power requirement for laser cutting. The power selection during cutting should be adjusted according to the type and thickness of the wood:
- Thin wood (5-12mm): A low-power (60W-100W) CO2 laser generator is usually sufficient to ensure cutting accuracy and smooth edges while avoiding wood burning.
- Thick wood (12-25mm): A medium-power (100W-180W) CO2 laser generator is required to ensure cutting depth and speed. However, the power and cutting speed still needs to be controlled to prevent excessive burning or deformation of the wood.
Non-Metallic: Plastics
There are many types of plastics, and different types of plastics react differently to lasers, so the power selection needs to be careful:
- Thin plastics (5-9mm): Usually low power (60W-100W) can be used for effective cutting, and the quality of the cutting edge is guaranteed to avoid material melting or deformation.
- Thick plastics (9-18mm): slightly higher power (100W-180W) is required, but the cutting speed should be slower to ensure the cutting effect while reducing the generation of slag and deformation of the edge.
Composite Materials and Specialty Materials
The laser power requirements for cutting composite and specialty materials depend on the specific composition and properties of the material. Such materials usually include multi-layer structures, which may combine multiple components such as metal, plastic, fiberglass, etc., so the selection of laser power requires special attention to avoid material delamination or damage.
- Composite materials: For multi-layer composite materials with a thickness of no more than 3mm, CO2 laser cutting machines can be used for cutting. For thicker composite materials, higher-power laser equipment is recommended.
- Special materials: Such as ceramics, carbon fiber, etc., CO2 laser cutting machines are only suitable for cutting very thin specialty materials (<2mm). For thicker or more difficult specialty materials cutting, higher-power laser equipment is usually required.
Different materials have different requirements for laser power, and choosing the right laser power is crucial. The power setting not only affects the cutting speed and efficiency but is also directly related to the cutting quality and edge smoothness. By properly adjusting the laser power, companies can improve production efficiency, reduce material waste, and ensure high-quality output of products.
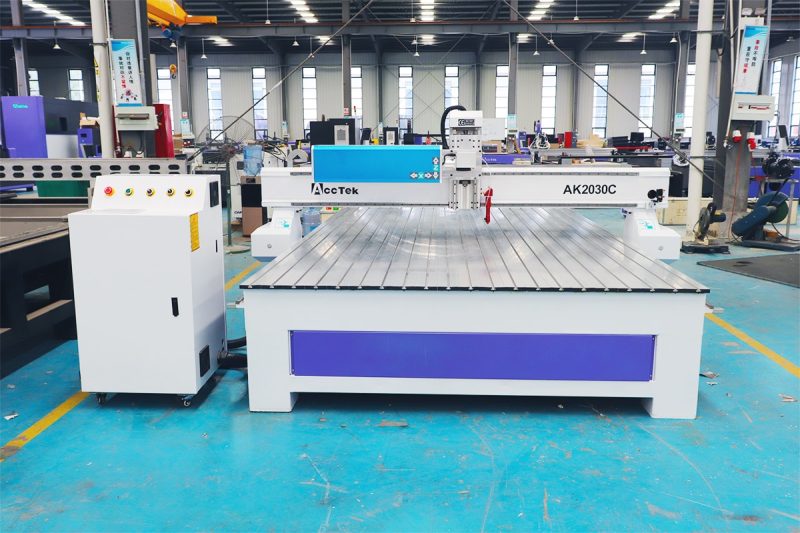
Testing and Experimentation for Selecting CO2 Laser Power
When selecting CO2 laser power, testing and experimentation are key steps to ensure cutting quality and efficiency. Through experiments, the impact of different power settings on cutting effects can be accurately evaluated, and reliable data support can be provided for actual operation.
Material Testing
First, preliminary tests are conducted on the target material. Select representative material samples and cut them using different laser power settings. Record the results of each cut, including cutting speed, edge smoothness, slag conditions, and whether there are uncut parts. With these data, a preliminary judgment can be made on the required power range.
Cutting Parameter Adjustment
Based on the preliminary test, the laser power is gradually adjusted according to the cutting speed and quality requirements. Make sure to test the changes in cutting speed at different powers to find the best power setting that balances efficiency and quality. This process should include testing the complexity of the cutting path to ensure that the cutting effect can be maintained stably in actual production.
Repeatability Verification
To ensure the reliability and consistency of the selected power, multiple tests are required for the same material and different batches. Observe whether the cutting effect of different batches of materials at the same power is consistent, and ensure that the power setting can adapt to the slight differences in the material during production.
Actual Application Test
After determining the power setting in a laboratory environment, apply it to actual production conditions. Observe the performance of the power setting on the actual production line, and make necessary fine-tuning according to the on-site conditions (such as equipment status, and environmental factors). Ensure that in actual applications, the laser power can meet the requirements of cutting quality and production efficiency.
Safety and Cost Considerations
During the test process, the impact of power settings on the equipment must also be considered. Excessive power may accelerate equipment wear and increase maintenance costs. Therefore, in the selection of power, the cutting effect and the long-term use of the equipment should be balanced to achieve the best combination of economy and efficiency.
Through systematic testing and experiments, a scientific basis can be provided for the selection of CO2 laser power to ensure the best cutting effect in actual applications. These experiments not only help optimize cutting quality and speed but also protect the long-term use of the equipment.
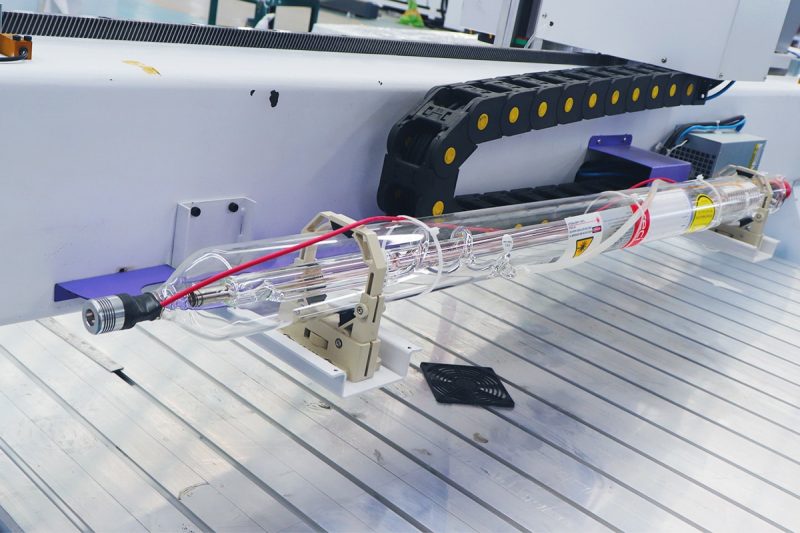
Calculating Power Requirements
In laser cutting, accurately calculating power requirements is the key to achieving efficient and precise cutting. The calculation of power requirements mainly considers material type and thickness, cutting speed, and required cutting quality.
Material Type and Thickness
The type and thickness of the material are the primary factors that determine the laser power requirements. Different materials (such as metals, non-metals, and composites) have different laser absorption rates and thermal conductivity, which directly affect the laser’s penetration ability. Generally, thicker materials require higher power to ensure that the laser beam can completely cut the material, while thinner materials require lower power to avoid excessive melting.
Cutting Speed
The cutting speed is proportional to the laser power. To improve production efficiency, it may be necessary to increase the power to support faster cutting speeds. However, too fast speeds may affect the cutting quality, especially when cutting complex or delicate shapes. Therefore, when setting the power, a balance should be found between speed and quality.
Cutting Quality
The cutting quality requirements also affect the power selection. To obtain smooth cutting edges and reduce slag, the laser power needs to be precisely controlled. Too high power may cause edge melting, while insufficient power may cause incomplete cutting or burrs. In actual operation, the effect of different power settings on cutting quality should be tested experimentally to find the best setting.
Calculating the power requirement for laser cutting is a multi-factor balancing process, which requires scientific calculations based on material properties, cutting speed, and quality requirements. The following formula can help determine:
Required power = material thickness × cutting speed × material property coefficient.
Through testing and adjustment, the most suitable power setting can be found to ensure an efficient and accurate cutting process.
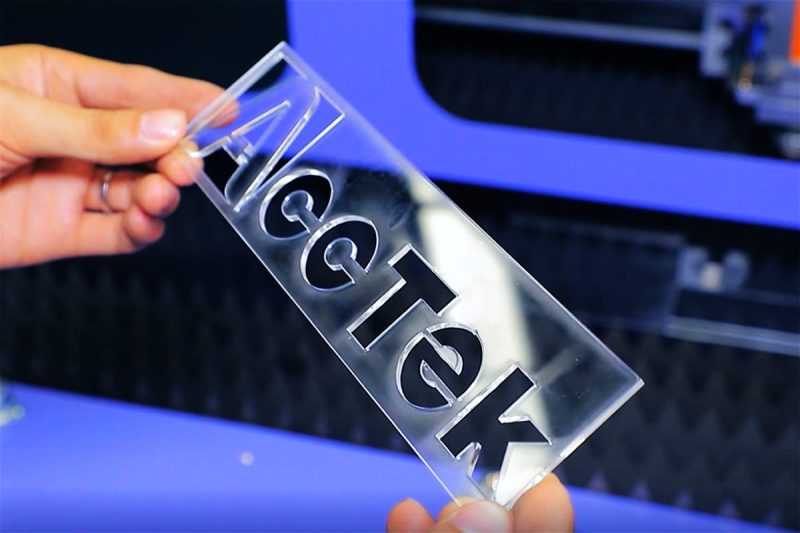
Practical Considerations for Selecting CO2 Laser Power
Even for the same material, small differences between batches may affect the laser cutting effect. For example, the composition of wood may vary slightly from batch to batch, resulting in different absorption rates of the laser. This requires that the laser power may need to be fine-tuned every time the material batch is changed to ensure consistent cutting results.
Influence of Environmental Factors
Factors such as ambient temperature, humidity, and air quality may affect the performance of the laser generator and the cutting effect. For example, temperature changes may affect the output stability of the laser generator, and excessive humidity may cause water vapor on the surface of the material, affecting the transmission of the laser. Therefore, under different environmental conditions, the laser power needs to be appropriately adjusted to adapt to environmental changes.
Equipment Maintenance and Wear
The state of the laser cutting equipment has a direct impact on the power demand. As the equipment is used for a longer time, the laser generator, lens, and optical system may be worn or contaminated, resulting in a decrease in beam quality, which in turn affects the cutting effect. Therefore, regular equipment maintenance and cleaning are essential to ensure that the equipment is always in optimal working condition. Equipment with greater wear may require increased power to compensate for the decrease in efficiency.
Cutting Speed and Path Complexity
In actual production, cutting speed and path complexity will directly affect power requirements. Higher cutting speeds usually require higher power to ensure cutting penetration, while complex paths (such as curves or fine patterns) may require more precise power control. Therefore, in actual operation, the design and actual execution of the cutting path need to match the power setting.
Real-Time Monitoring and Adjustment
In actual production, it is very important to monitor the cutting effect in real-time and adjust the power as needed. Even under the same materials and conditions, as production progresses, the equipment status or environmental conditions may change, resulting in reduced cutting quality. By real-time monitoring of the edge smoothness, penetration, and slag of the cutting, problems can be discovered in time and corrected by adjusting the power or other parameters.
Safety and Cost Considerations
In actual power settings, safety and cost-effectiveness must also be considered. Although excessive power settings can improve cutting efficiency, they may increase energy consumption and lead to higher costs. In addition, excessive power may also bring safety risks, such as overheating of materials or damage to equipment. Therefore, in actual operation, power settings should use energy as efficiently as possible to reduce production costs while ensuring safety.
In actual operation, the calculation and setting of laser cutting power needs to flexibly deal with a variety of realistic factors, such as material differences, environmental changes, equipment status, and cutting path complexity. By comprehensively considering these factors and conducting real-time monitoring and adjustments, the efficiency and stability of the cutting process can be ensured, while reducing costs and risks.
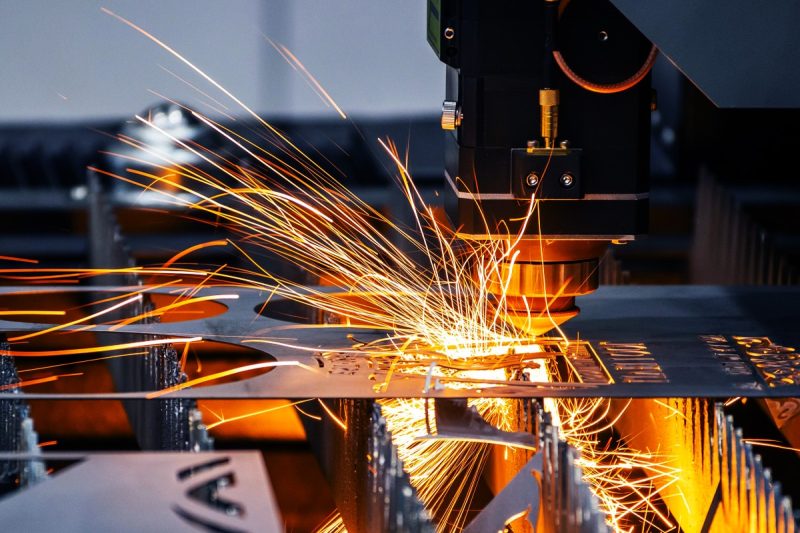
Summary
Choosing the power of a CO2 laser cutting machine is a multi-faceted process. Key factors include material type and thickness, cutting speed, cutting quality requirements, and machine configuration. Different materials have different absorption rates and thermal conductivity of lasers, so when choosing power, you first need to adjust it according to the material characteristics. Thicker materials generally require higher power, while thin materials need to carefully control the power to avoid excessive melting.
Cutting speed is closely related to power. Increasing power can increase cutting speed, but this may affect cutting accuracy, especially when dealing with complex graphics. Therefore, finding the best balance between speed and power is crucial to ensure production efficiency and quality. Cutting quality is another core factor. Too high or too low power will result in reduced cutting-edge quality, so the most suitable power setting should be determined through actual testing. In addition, the configuration of the laser cutting equipment, such as the type of laser generator and the optical system, will also affect the power requirements. Therefore, when choosing power, the specific capabilities and limitations of the equipment must be considered.
By fully considering these factors and conducting necessary tests and adjustments, the power selection can be optimized to achieve efficient and accurate cutting results.
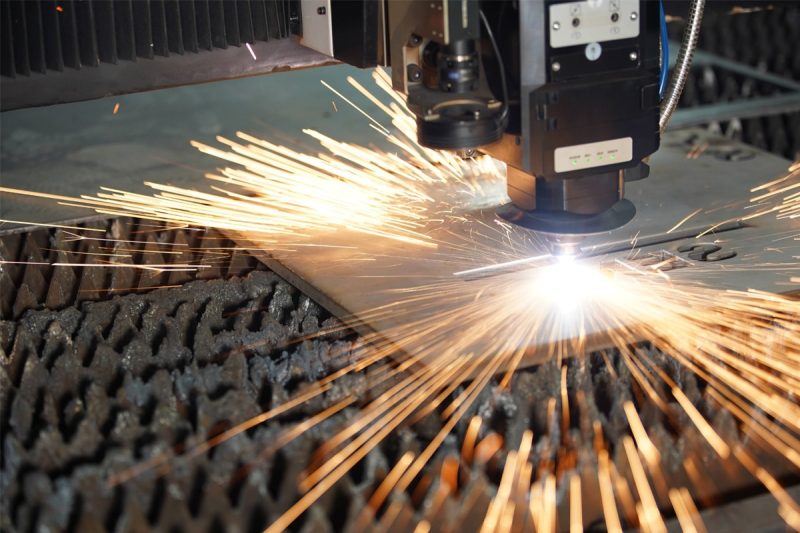
Get Laser Solutions
Choosing the correct CO2 laser cutting power can help optimize power consumption and achieve high operating efficiency. Working with a trusted supplier ensures access to advanced technology, tailored advice and ongoing support. At AccTek Laser, we offer a comprehensive range of CO2 laser cutting machine equipment designed to meet a variety of industrial needs. Our experts can help you choose the most energy-efficient model and configuration, taking into account factors such as material type, thickness and production volume. We also offer cutting-edge features such as high-efficiency laser generators, intelligent cooling systems and energy management software to maximize performance and minimize energy use. In addition, our team provides regular maintenance services and technical support to keep your equipment at peak efficiency. By partnering with AccTek Laser, you can achieve significant energy savings, reduce operating costs and enhance your sustainability efforts. Contact us today to learn more about our innovative laser solutions and how they can benefit your business.
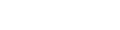
Contact information
- [email protected]
- [email protected]
- +86-19963414011
- No. 3 Zone A, Lunzhen Industrial Zone,Yucheng City , Shandong Province.
Get Laser Solutions