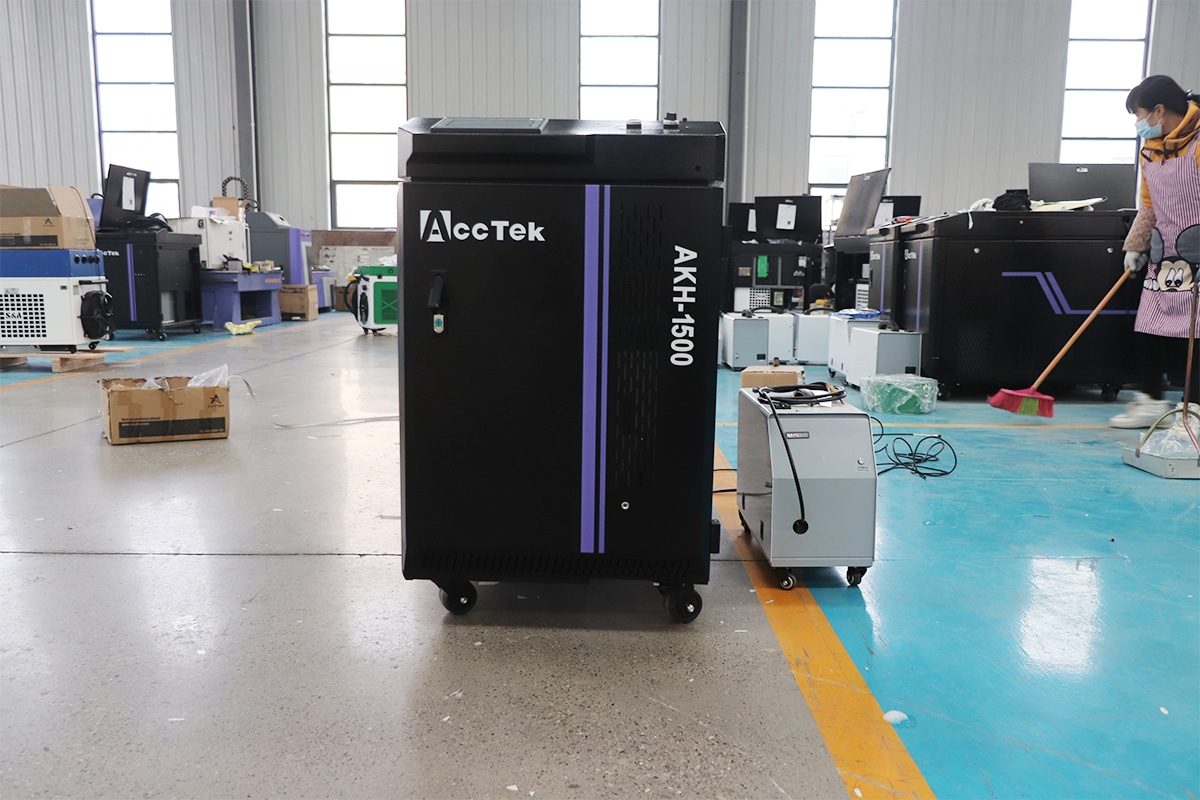
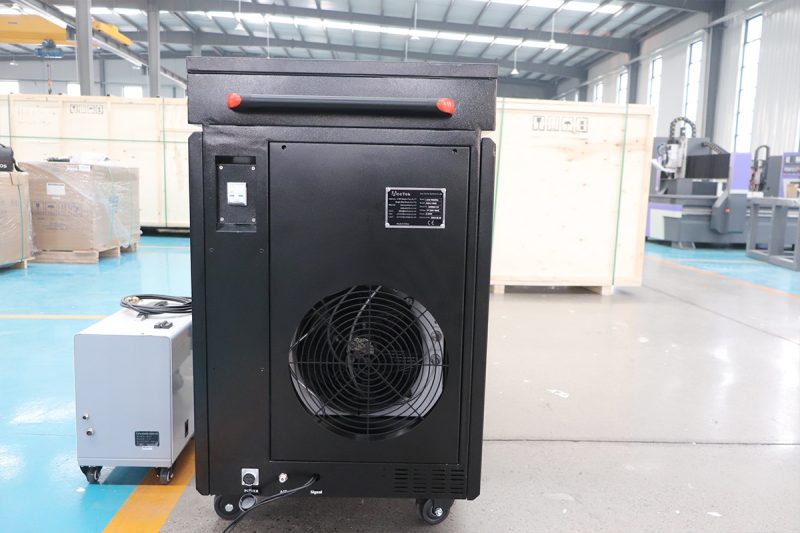
Understanding Laser Welding Power
The Role of Laser Power in Welding
Laser power, typically measured in watts (W) or kilowatts (kW), determines the amount of energy delivered to the material being welded. The power setting affects several key aspects of the welding process:
- Depth of Penetration: One of the primary functions of laser power is to determine penetration depth. Higher power levels allow the laser to penetrate deeper into the material, allowing for the welding of thicker sections. The relationship between power and penetration is generally linear up to a certain point, beyond which other factors such as beam quality and focus come into play.
- Welding Speed: The power of the laser also affects welding speed. Higher powers allow for faster welding speeds, making them suitable for high-volume production environments. However, the increase in speed must be balanced with adequate penetration and heat input to ensure a strong weld.
- Heat Input and Thermal Management: Laser welding involves localized heating, and the amount of heat input is directly related to the laser power. Managing heat input helps avoid excessive thermal deformation, which can compromise the integrity and appearance of the weld. Higher power levels require efficient cooling systems to dissipate heat and prevent overheating of the workpiece and surrounding areas.
- Weld Quality: Weld quality is significantly affected by laser power. Insufficient power can result in incomplete fusion, which can lead to a weak joint, while too much power can result in burn-through or excessive spatter. Achieving the proper power balance can help produce clean, strong, and aesthetically pleasing welds.
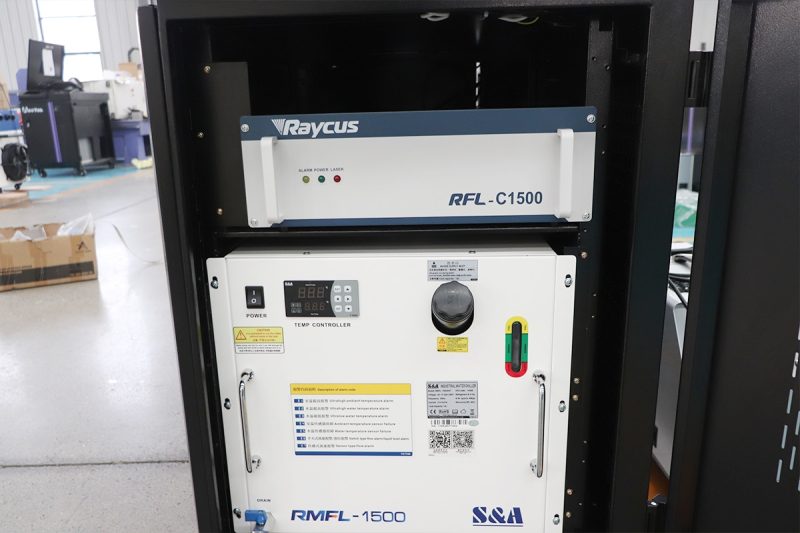
Factors Affecting Power Output Selection
Material Type
Due to their unique physical and chemical properties, different materials react differently to laser energy. Key considerations for material type include:
- Absorptivity and Reflectivity: Materials such as aluminum and copper have high reflectivity and low absorptivity, requiring higher laser powers to achieve effective welding. In contrast, materials such as stainless steel and titanium absorb laser energy more effectively, allowing for lower power settings.
- Thermal Conductivity: Materials with high thermal conductivity, such as copper, dissipate heat quickly and therefore require higher powers to maintain adequate weld penetration and quality.
Material Thickness
The thickness of the material being welded is directly proportional to the required laser power. Thicker materials require more power to achieve adequate penetration and a strong weld. Key points to consider include:
- Depth of Penetration: Higher power levels are required to ensure the laser beam penetrates deep enough to effectively weld thicker sections.
- Multi-Pass Welding: For very thick materials, multi-pass welding with a medium-power laser may be preferable to single-pass high-power welding to control heat input and minimize thermal distortion.
Joint Configuration
The type and configuration of the joint significantly affect the power requirements for laser welding. Common joint types include:
- Butt Joints: These joints generally require less power than other joint types because the laser needs to penetrate a single interface.
- Lap Joints: More power is required due to the overlap of materials, which increases the thickness that the laser must penetrate.
- T-Joints and Corner Joints: These configurations often involve complex geometries and multiple interfaces, requiring precise control of laser power to achieve consistent weld quality.
Welding Speed
The required welding speed is a key factor in determining laser power:
- High-Speed Welding: Faster welding speeds require higher laser power to ensure sufficient energy is delivered within the shorter interaction time between the laser and the material.
- Slow-Speed Welding: This allows for lower power settings because the laser has more time to transfer energy to the material, achieving the desired penetration and weld quality.
Thermal Management and Cooling Systems
Effective thermal management prevents thermal deformation, material degradation, and other heat-related issues:
- Cooling Systems: High-power lasers generate a lot of heat, requiring a powerful cooling system to maintain optimal operating temperatures and prevent damage to the laser welder and materials.
- Heat-Affected Zone (HAZ): Proper thermal management ensures a minimal HAZ, preserving the mechanical properties and integrity of the welded materials.
Beam Quality and Focusing
The quality and focus of the laser beam affect the efficiency and precision of the welding process:
- Beam Quality: A high-quality beam with a consistent intensity distribution enables better welds at lower power levels than a poorer-quality beam.
- Focus Control: Accurate focus control ensures that the laser energy is concentrated in the weld area, maximizing efficiency and reducing power requirements.
Application-Specific Requirements
Different industries and applications have unique power requirements based on their specific needs.
- Automotive Industry: Welding thin to moderately thick components such as body panels and frames typically requires power levels in the 2-3 kW range for adequate penetration and strength.
- Aerospace Industry: Welding thin-walled structures and critical components made from titanium and nickel-based alloys generally require power settings in the 1.5-2.5 kW range for precision and minimal thermal distortion.
- Electronics Manufacturing: Micro-welding of delicate components requires lower power levels, often between 1-1.5 kW, to ensure precision and minimal heat impact.
- Medical Device Manufacturing: Welding biocompatible materials like stainless steel and titanium typically needs power levels in the 1.5-2.5 kW range for producing clean, high-quality welds with minimal thermal damage.
Economic Considerations
Economic factors also play a role in power output selection:
- Initial Cost VS Long-Term Savings: Higher-power lasers generally involve a higher initial cost, but can result in increased productivity, reduced cycle times, and long-term cost savings due to improved efficiency and quality.
- Operating Costs: Consider the operating costs associated with higher power settings, including energy consumption and maintenance of cooling systems.
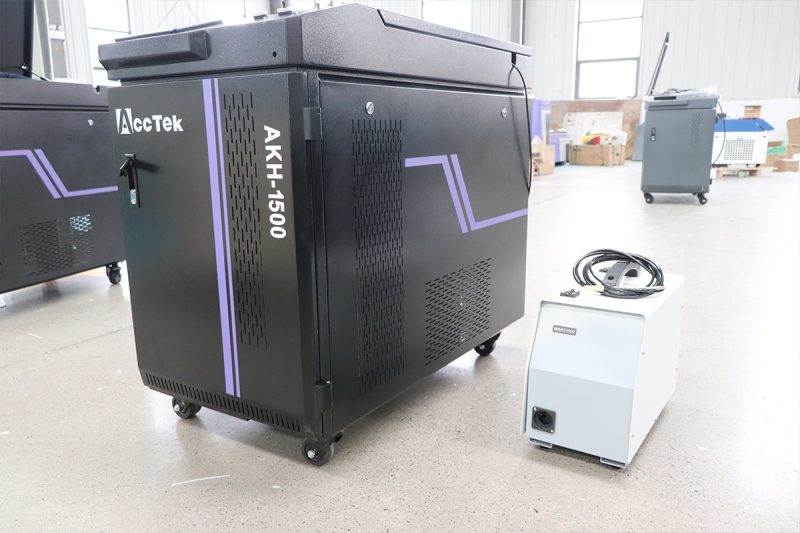
The Impact of Power Output on The Welding Process
Penetration Depth
Penetration depth is one of the most significant aspects influenced by laser power output. It refers to how deeply the laser beam can melt and join the materials being welded.
- High Power Output: Greater power levels enable deeper penetration, making it possible to weld thicker materials effectively. For example, a laser welding machine operating at 3 kW can achieve significant penetration depths, suitable for welding materials up to 5 mm thick.
- Low to Moderate Power Output: Lower power settings (1-2 kW) are sufficient for welding thinner materials. These settings provide enough energy to melt and fuse the material without excessive penetration, which is ideal for thin sheets and delicate components.
Welding Speed
The speed at which welding occurs is another critical factor affected by power output. Higher power levels generally allow for faster welding speeds.
- High Power Output: Enables high-speed welding, increasing productivity and reducing cycle times. For instance, a 3 kW laser welding machine can weld at significantly higher speeds than a 1 kW laser welding machine, making it ideal for high-volume production environments.
- Low to Moderate Power Output: Suitable for slower welding speeds, which can be advantageous for intricate welding tasks requiring high precision and control. Lower speeds also reduce the risk of defects in sensitive materials.
Thermal Effects and Heat Management
Laser welding involves the application of concentrated heat, and the power output directly impacts the thermal effects on the welded material.
- High Power Output: Generates more heat, which can lead to a larger heat-affected zone (HAZ). This is suitable for applications where deeper penetration is required but needs effective cooling systems to manage the heat and prevent thermal distortion or damage to surrounding areas.
- Low to Moderate Power Output: Produces less heat, resulting in a smaller HAZ. This is beneficial for welding thin materials or components where maintaining the material’s mechanical properties is crucial. Lower heat input reduces the risk of warping, distortion, and other thermal issues.
Weld Quality
The quality of the weld is a critical outcome influenced by the laser power output. Factors such as consistency, strength, and appearance of the welds are all affected by power levels.
- High Power Output: Can produce strong, deep welds suitable for structural applications. However, excessive power can lead to defects such as spatter, porosity, and cracking if not properly managed. High power settings require precise control and optimized parameters to ensure high-quality welds.
- Low to Moderate Power Output: Provides better control over the welding process, leading to clean and precise welds. This is particularly important for applications requiring high precision and aesthetic quality, such as electronics and medical device manufacturing.
Adaptability to Material Types
Different materials have unique properties that influence how they respond to laser welding at various power levels.
- High Power Output: Essential for welding materials with high reflectivity and thermal conductivity, such as aluminum and copper. These materials require more energy to achieve proper fusion.
- Low to Moderate Power Output: Adequate for materials that absorb laser energy efficiently, such as stainless steel and titanium. These materials can be welded effectively at lower power settings, reducing the risk of overheating and thermal damage.
Joint Configuration and Complexity
The complexity of the joint configuration also dictates the necessary power output for effective welding.
- High Power Output: Suitable for complex joint configurations, such as multi-pass welds or thick lap joints, where substantial energy is required to penetrate multiple layers of material.
- Low to Moderate Power Output: Ideal for simpler joints, such as butt joints and thin lap joints, where less energy is needed to achieve a strong bond.
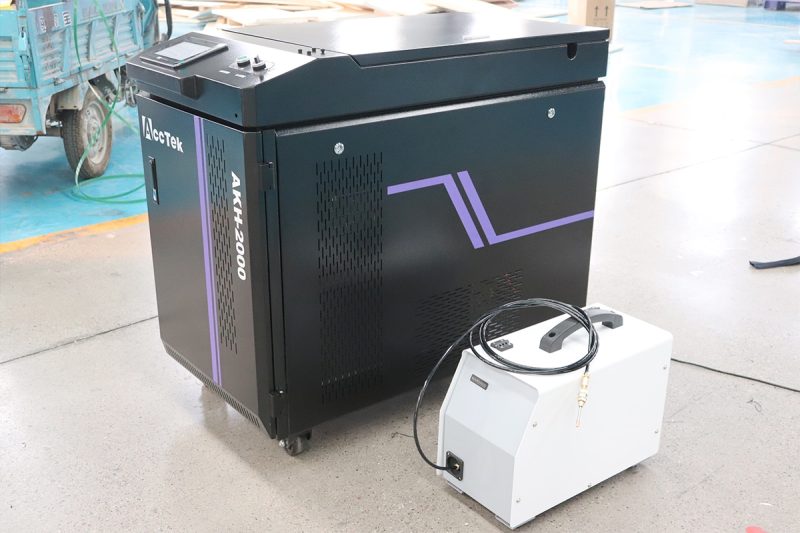
How To Choose The Correct Power Output
Assess Material Properties
The first step in selecting the correct power output is to thoroughly understand the properties of the materials you will be welding.
- Material Type: Identify the type of material (e.g., steel, aluminum, copper, titanium) and its specific properties, such as reflectivity, thermal conductivity, and melting point. Materials with high reflectivity and thermal conductivity, like aluminum and copper, require higher power levels.
- Material Thickness: Determine the thickness of the materials. Thicker materials require higher power to achieve adequate penetration, while thinner materials can be welded with lower power settings. For instance, materials less than 2 mm thick may require 1-1.5 kW laser welding machine, while those up to 5 mm thick may need up to 3 kW laser welding machine.
Define Welding Requirements
Next, outline the specific requirements of your welding application.
- Joint Configuration: Consider the type of joint (e.g., butt joint, lap joint, T-joint). Butt joints generally require less power than lap joints due to the difference in surface area and penetration depth needed.
- Welding Speed: Decide on the desired welding speed. High-speed welding applications require higher power to deliver sufficient energy in a shorter time. Conversely, slower welding speeds can be achieved with lower power settings, which may be beneficial for precision tasks.
Evaluate Heat Management Needs
Proper thermal management can prevent defects and maintain weld quality.
- Heat-Affected Zone (HAZ): Consider the size of the HAZ you can tolerate. High power settings increase the HAZ, which may be detrimental for applications requiring minimal thermal impact. Lower power settings produce a smaller HAZ, preserving the mechanical properties of the material.
- Cooling Systems: Ensure that the welding machine has adequate cooling systems to dissipate heat, especially when operating at higher power levels. Efficient cooling prevents overheating and maintains the integrity of both the machine and the materials.
Consider Application-Specific Factors
Different industries and applications have unique power requirements.
- Automotive Industry: For welding thick steel or aluminum components, power levels between 2-3 kW are often necessary to achieve deep, strong welds in body panels and frames.
- Aerospace Industry: Requires precise and high-quality welds on thin-walled structures and critical components, typically using power settings of 1.5-2 kW.
- Electronics Manufacturing: Micro-welding delicate components demands low power levels, usually between 1-1.5 kW, to ensure precision and minimal thermal impact.
- Medical Device Manufacturing: Welding biocompatible materials like stainless steel and titanium often require power settings in the range of 1.5-2 kW to achieve clean, high-quality welds with minimal thermal damage.
Perform Material Testing
Testing on sample materials can help determine the optimal power setting.
- Trial Welds: Perform trial welds using different power settings to observe the results. Analyze the weld quality, penetration depth, and the extent of the HAZ.
- Parameter Optimization: Fine-tune the welding parameters, such as power, speed, and focus, based on the results of your trial welds. This iterative process helps in identifying the best power setting for your specific application.
Consult with Experts
Leverage the expertise of laser welding professionals and equipment manufacturers.
- Manufacturer Recommendations: Consult with the manufacturer of the laser welding machine to get their recommendations based on your application requirements and material properties.
- Industry Experts: Engage with industry experts who have experience with similar applications. Their insights can provide valuable guidance in selecting the appropriate power output and optimizing your welding process.
Evaluate Economic Considerations
Consider the economic impact of your power selection.
- Initial Investment: Higher-power lasers typically have higher upfront costs. Evaluate the return on investment by considering the increased productivity and potential long-term savings.
- Operational Costs: Higher power settings may lead to increased energy consumption and maintenance costs. Balance these costs against the benefits of faster welding speeds and improved weld quality.
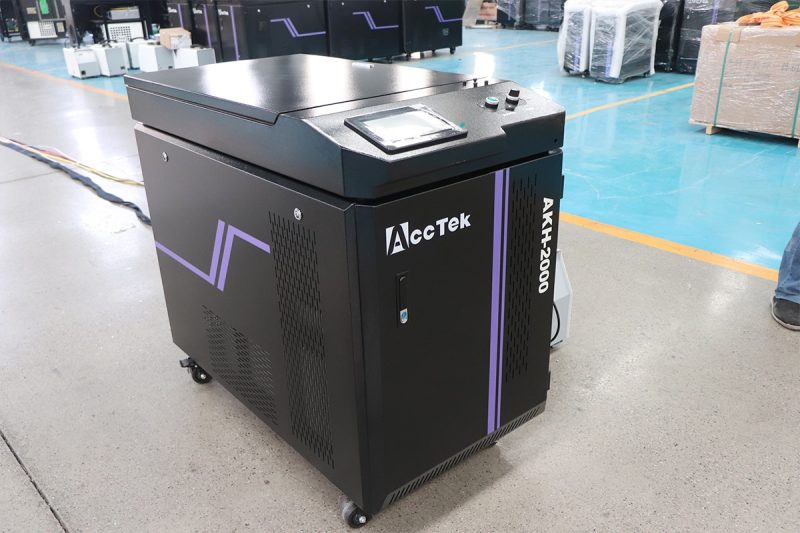
Application-Specific Considerations
Automotive Industry
The automotive industry extensively uses laser welding for manufacturing components like body panels, structural parts, and powertrain elements. The primary considerations for this industry include:
- Material Types: Common materials include steel and aluminum, which vary in reflectivity and thermal conductivity. Higher power levels, typically between 2-3 kW, are needed to weld these materials effectively.
- Material Thickness: Automotive parts often involve thicker materials requiring deep penetration. A power output of 2-3 kW ensures sufficient depth and strength for welding thicker sections.
- Welding Speed: High-speed welding is crucial to maintain productivity in high-volume production environments. Higher power enables faster welding speeds, reducing cycle times and increasing throughput.
- Joint Types: Butt joints, lap joints, and T-joints are common. Each joint type may require different power levels, with lap joints generally needing more power due to increased material overlap.
Aerospace Industry
Laser welding is used in the aerospace industry to manufacture components such as fuselages, engine parts, and fuel tanks, so welding precision and welding quality are very important.
- Material Types: Aerospace materials include titanium, aluminum, and nickel-based alloys, each requiring specific power settings to achieve clean and precise welds. Power levels of 1.5-2.5 kW are often sufficient for these materials.
- Thin-Walled Structures: Many aerospace components are thin-walled, necessitating lower power levels to prevent excessive heat input and distortion. Careful power management helps maintain structural integrity.
- Quality and Consistency: High-quality, defect-free welds are essential. Power settings must be optimized to achieve consistent penetration and minimal defects, with precise control over heat input.
- Complex Geometries: Aerospace parts often feature complex shapes and tight tolerances. Power levels must be adjusted to accommodate these complexities without compromising weld quality.
Electronics Manufacturing
In the electronics industry, laser welding is employed for assembling delicate components such as circuit boards, connectors, and microelectronics.
- Material Types: Common materials include copper, gold, and various alloys. These materials typically require lower power levels (1-1.5 kW) due to their thinness and high conductivity.
- Micro-Welding: Precision is critical for micro-welding tasks, necessitating fine control over laser power to avoid damaging sensitive components. Low power settings help maintain the necessary precision.
- Heat Sensitivity: Electronic components are often heat-sensitive, requiring minimal heat input to prevent damage. Lower power settings help achieve this, maintaining the functionality and reliability of the components.
- High Precision: Achieving high precision with minimal heat-affected zones is essential. Power settings must be optimized to ensure clean, precise welds with minimal thermal impact.
Medical Device Manufacturing
Laser welding is widely used in the medical device industry for fabricating components such as surgical instruments, implants, and diagnostic equipment.
- Material Types: Biocompatible materials like stainless steel, titanium, and certain polymers are common. Power levels in the range of 1.5-2.5 kW are typically required for these materials.
- Sterility and Cleanliness: Medical devices require sterile and clean welds with minimal contamination. Power settings must ensure smooth, high-quality welds with minimal spatter and oxidation.
- Precision and Control: High precision is essential to maintain the functionality and safety of medical devices. Lower to moderate power settings help achieve precise control over the welding process.
- Thin-Walled Components: Many medical devices feature thin-walled components, necessitating careful power management to avoid excessive heat input and distortion.
Jewelry and Watchmaking
Laser welding is also utilized in the jewelry and watchmaking industries for assembling and repairing delicate pieces.
- Material Types: Common materials include gold, silver, platinum, and various precious alloys. These materials often require lower power levels (1-1.5 kW) due to their thinness and high reflectivity.
- Delicate Components: Precision is critical for working with small, intricate parts. Low power settings help achieve the necessary precision without damaging the components.
- Aesthetic Quality: Welds must be clean and aesthetically pleasing. Power settings must be optimized to minimize spatter and discoloration, ensuring a high-quality finish.
- Heat Sensitivity: Precious metals are heat-sensitive, requiring minimal heat input to avoid warping or damaging the material. Lower power settings help maintain the integrity of the components.
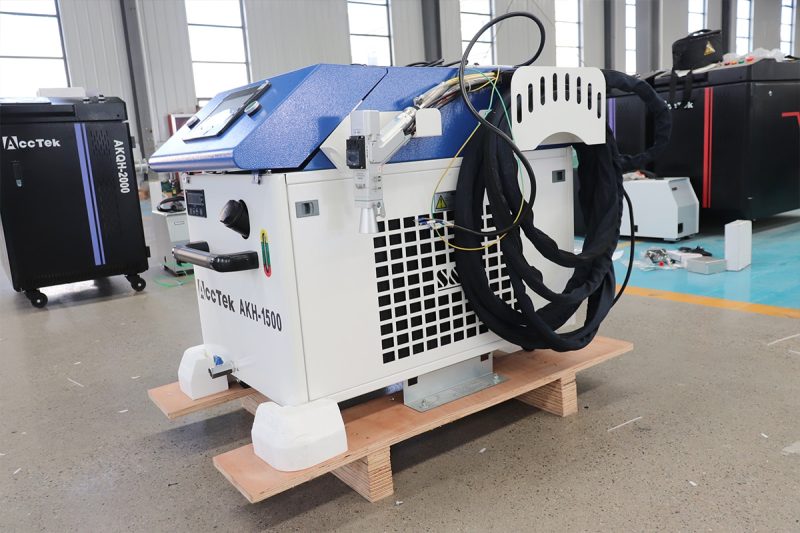
Summary
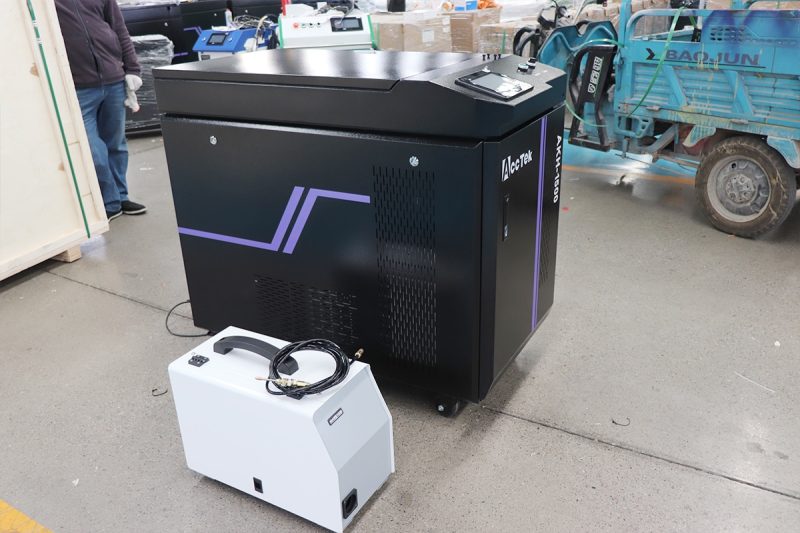
Get Laser Welding Solutions
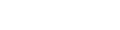
- [email protected]
- [email protected]
- +86-19963414011
- No. 3 Zone A, Lunzhen Industrial Zone,Yucheng City , Shandong Province.