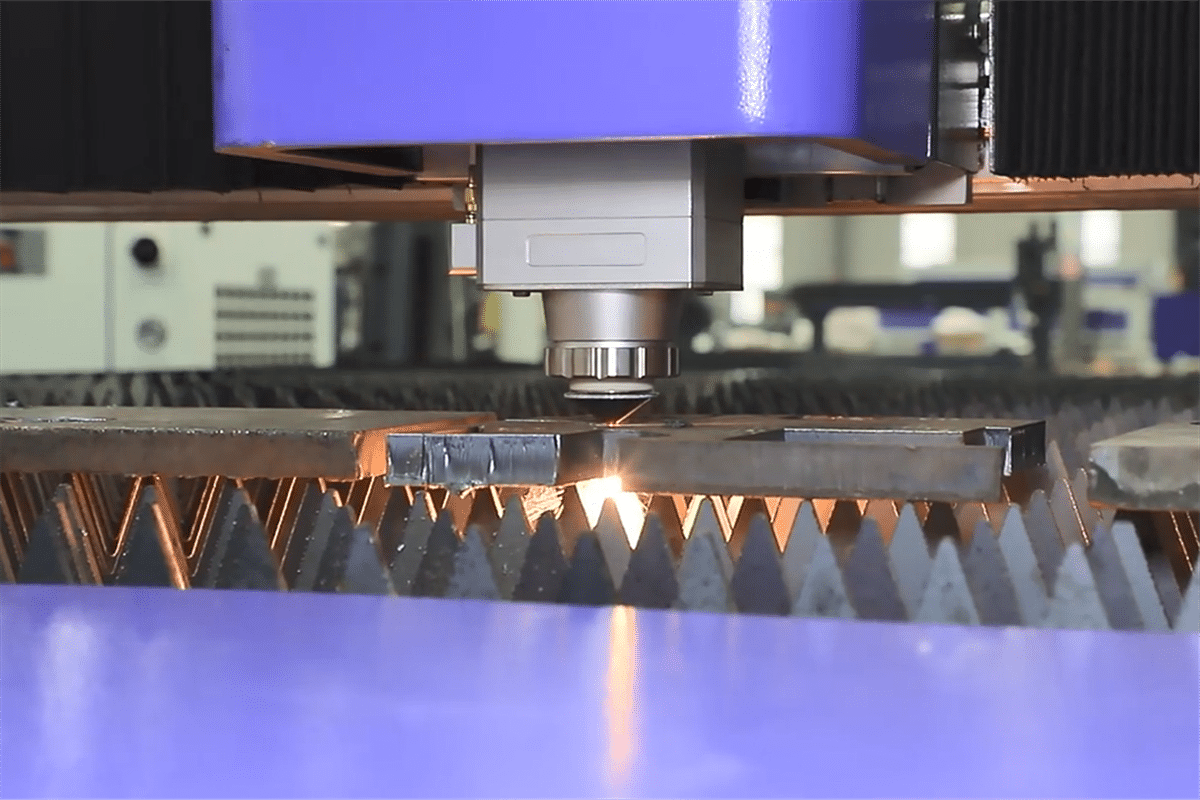
How to Choose The Right Auxiliary Gas For Laser Cutting
Fiber laser cutting machine is an advanced CNC metal cutting equipment, that can cope with the cutting requirements of various materials and complex shapes, and is widely used in the metal processing industry. In the laser cutting process, to obtain high-quality workpieces, in addition to a laser generator that can provide high energy, selecting the appropriate auxiliary gas is an important part of adjusting the cutting process.
Depending on the material and thickness of the cutting workpiece, the requirements for the use of auxiliary gas are also different. This article details the role of auxiliary gas and four common cutting auxiliary gas. Keep reading to learn how to choose the right auxiliary gas for your processing needs to help you complete your metal projects.
Table of Contents
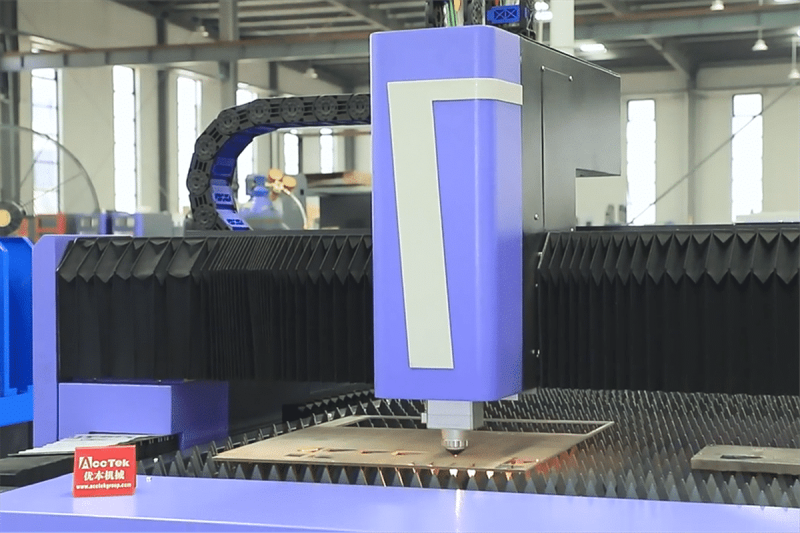
What is the role of auxiliary gas in the laser cutting process?
Users who use a laser cutting machine for the first time may have a question in their mind: why does the laser cutting machine need to rely on auxiliary gas for cutting? Here is an introduction to the role of auxiliary gas in the laser cutting of metals. After reading this, you will know that it is very necessary to use auxiliary gas during cutting.
- Material removal and cutting area cleaning: One of the primary functions of assist gas is to blow molten or vaporized material away from the cutting area. When the laser beam heats the material, it melts or vaporizes, creating a pool of molten material. An auxiliary gas (usually compressed air, nitrogen, oxygen, or a gas mixture) blows this material away, preventing it from interfering with the cutting process and ensuring that the laser can continue to cut through the material without obstruction.
- Cooling the material: One of the primary functions of an auxiliary gas (usually nitrogen or compressed air) is to cool the material being cut. Laser cutting generates intense heat at the cutting point, causing the material to melt or vaporize. The assist gas rapidly cools the surrounding area while blowing away molten or vaporized material. This cooling prevents the material from overheating, deforming, or being damaged during the cutting process.
- Nitrogen shielding: Nitrogen is often used as an assist gas when cutting materials such as stainless steel or aluminum. It acts as a shielding gas, preventing the material from reacting with oxygen, which could otherwise lead to oxidation and rough cutting edges. Nitrogen creates a clean, oxide-free cut edge.
- Promotes combustion: In some laser cutting applications, oxygen is used as an auxiliary gas. When a laser beam interacts with oxygen, it ignites and chemically reacts with the material being cut, a process called oxygen-assisted combustion cutting. However, oxygen flow needs to be controlled to prevent excessive oxidation. Excessive oxidation can cause rough edges or unwanted changes in material properties.
- Improve cut quality: The choice of assist gas and its flow rate will affect the quality of the cut edge. By selecting the right gas for the material and optimizing its flow rate, operators can achieve smoother edges, minimal burrs, and precise cuts.
- Protection of Optical Components: Auxiliary gas helps protect optical components by creating a barrier between them and debris generated during the cutting process, helping to reduce the build-up of residue and contaminants on the optics of the laser cutting head. This protects the optics from contamination or damage, ensuring the laser beam remains focused and accurate.
- Stabilizes the cutting process: The flow of assist gas stabilizes the cutting process by creating a controlled environment around the cutting area. It helps maintain consistent conditions for the laser beam to interact with the material, ensuring uniform and predictable cuts.
- Smoke removal: Laser cutting produces smoke, especially when cutting organic materials. Auxiliary gas helps clear these emissions from the cutting area, maintaining a clean, safe working environment.
Auxiliary gas plays a vital role in the laser-cutting process. It has several important features that help improve the efficiency and quality of laser cutting. The choice of assist gas depends on the type of material being cut and the specific requirements of the cutting operation, and it is an important parameter for optimizing the laser cutting process for various applications.
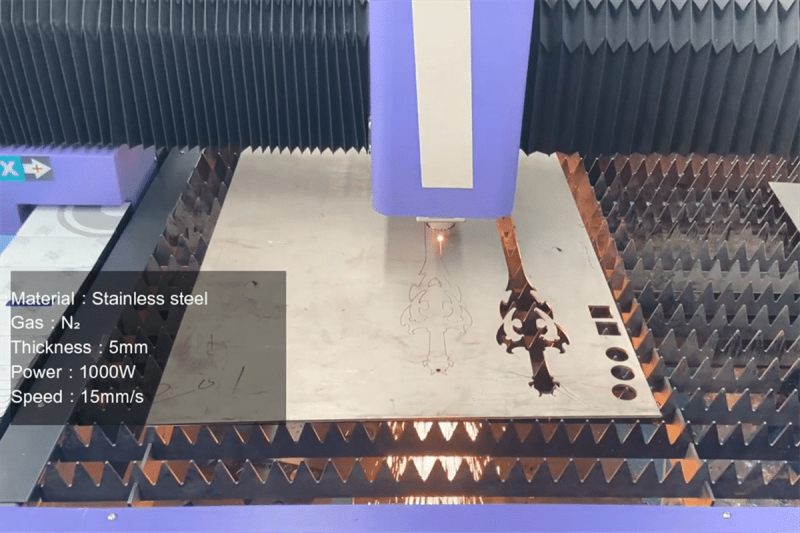
What are the common auxiliary gases?
The use of auxiliary gas plays an important role in the operation of laser-cutting machines. Currently, there are four auxiliary gases commonly used in laser-cutting metal processes. Their specific characteristics are as follows:
Compressed Air
Air is a mixture of nitrogen, oxygen and other gases. Compressed air is compressed into an air storage tank through an air compressor, and then extracted after being filtered, cooled, and dried. Its collection method is relatively simple and it is the lowest-cost auxiliary gas. It should be noted that the compressed air should be free of water, oil, and dust to avoid contaminating the optical components of the laser cutting machine and causing damage. Therefore filters are needed to ensure clean air.
Oxygen
Oxygen was one of the first auxiliary gases used in laser cutting because of its reactive nature when cutting. The reaction between oxygen and metal actually produces additional energy in the form of heat, which supports the cutting process and acts as a combustion aid. During the cutting process, oxygen reacts with heat, which can greatly improve cutting efficiency. The resulting oxide film increases the beam spectral absorption index of the reflective material, allowing more efficient use of laser energy and speeding up the laser cutting machine.
Nitrogen
Nitrogen is chemically inactive and does not easily oxidize with the workpiece being processed. In most applications, with the exception of some specialty materials such as titanium, nitrogen is considered a non-reactive or inert auxiliary gas. This means that the nitrogen does not react with any components of the metal during the cutting process. In most cases, nitrogen is considered the auxiliary gas that can help obtain the best edge quality for the workpiece. When cutting with nitrogen, higher purity is required.
Argon
Argon is also an inert gas with inactive chemical properties and is not easily oxidized with the workpiece being processed. It is more expensive to use than other auxiliary gases and is the rarest and most expensive gas used by most metal fabricators. Materials that cut well with nitrogen can also be cut with argon, which can provide similar high-quality edges. The main reason for using more expensive argon is because cutting in pure nitrogen still leaves some of the metal chemically active.
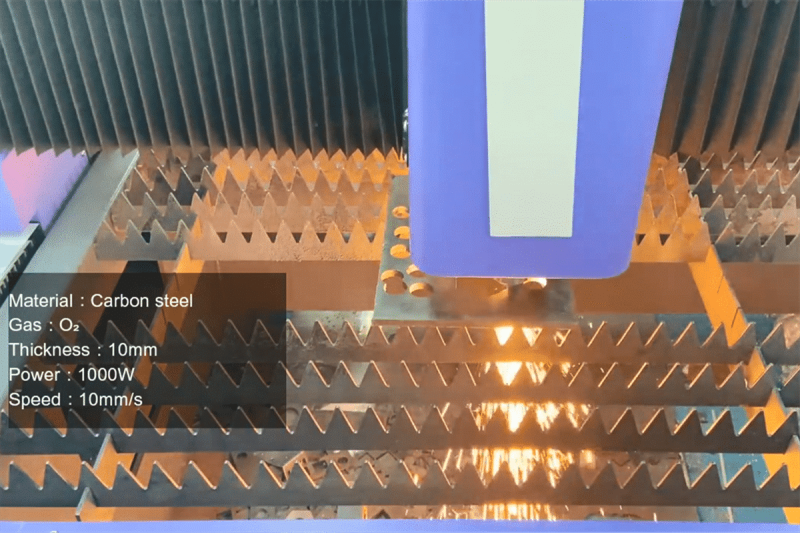
What kind of auxiliary gas is needed for laser cutting metal?
When starting a laser cutting project, you need to choose the correct auxiliary gas for the material and thickness of the sheet metal. Different auxiliary gases have their own functions and advantages. Only by correctly utilizing the advantages of different gases can we obtain higher cutting quality and faster cutting speed.
Application of compressed air in laser cutting
Compressed air is mainly used in processing scenarios where metal sheets are not very demanding on cutting end faces. It relies on laser energy to melt metal workpieces and uses high air pressure to blow away the molten material. When compressed air is used to assist in cutting the workpiece, the cut end surface of the workpiece will turn yellow. Compressed air is mainly suitable for cutting carbon steel, aluminum, aluminum alloy, brass, electroplated steel plate and other metal materials. It is widely used in some product industries such as sheet metal chassis, cabinets and cabinets. When using compressed air to assist cutting, you need to pay attention to the maintenance of the air compressor. If the air is not clean, it will cause certain damage to the laser cutting head, lens, and fiber laser generator, and will also have a great impact on the cutting quality of the workpiece.
The advantage of compressed air is that its cost is very low and it can be provided directly by an air compressor, so it is very convenient to use compared with other gases. However, compressed air also has obvious shortcomings in metal cutting. The cutting surface will produce burrs and may require secondary processing. In addition, because compressed air contains about 20% oxygen, the cut workpiece will turn black, affecting product quality, and the cutting efficiency is far less than that of oxygen cutting.
Application of oxygen in laser cutting
When cutting with oxygen, the material is heated to a certain temperature by the laser beam and then burns and vaporizes. Oxygen is the standard reactive auxiliary gas used for laser cutting carbon steel, and it can cut thicker steel because its reactive nature increases cutting heat. When cutting carbon steel, the oxygen burns the carbon in the carbon steel kerf to create additional heat, allowing less powerful laser generators to cut thicker materials.
Nonetheless, this reactivity of oxygen cutting can also have some negative effects. If good edge quality is required, typically the material’s cutting speed and air pressure are limited. During oxygen-assisted cutting, the chemical reaction increases as the gas pressure and flow rate increase. This results in increased heat in the workpiece and thus increased melting of the edges. This is not ideal for applications that require high quality cutting edges. In addition, oxygen cutting metal often also forms oxides on the cut edges, which makes the surface of the workpiece black and may require cleaning of the workpiece.
Application of nitrogen in laser cutting
Nitrogen-assisted laser cutting produces very high-quality edges on a variety of materials with very thin heat-affected zones. Nitrogen produces the best edge quality at an economical price with fast cutting speeds in most aluminum, mild steel, galvanized steel and UHSS automotive steel applications. When using nitrogen as an auxiliary gas for cutting, nitrogen will form a protective atmosphere around the molten metal to prevent the material from being oxidized, avoid the formation of oxide films, and achieve oxidation-free cutting. This feature makes nitrogen commonly used for parts that need to be stored for a period of time before use, as oxygen and air cutting can cause rust on the cut edges if stored for long periods of time. In addition, non-oxidation cutting workpieces have the characteristics of direct welding, strong corrosion resistance, etc., and the cut end surface is white. During nitrogen cutting, changes in gas flow have a great impact on cutting. While ensuring the cutting gas pressure, sufficient gas flow must be ensured.
Nitrogen also has shortcomings when used as an auxiliary gas for metal cutting. Because nitrogen does not react chemically with metal, there is no heat of reaction and the cutting ability is not as good as cutting with oxygen. The nitrogen consumption of nitrogen cutting is several times greater than that of oxygen, and the cutting cost is higher than that of oxygen cutting. In terms of consumption, oxygen cutting requires a pressure of 2 Bar and a consumption of approximately 10 m³/h. Nitrogen cutting requires a pressure of 22/30 Bar and a consumption of approximately 40 to 60/120 m³/h. In addition, nitrogen laser cutting speed is about 30% slower than oxygen laser cutting.
Application of argon gas in laser cutting
Argon is an inert gas used for metals that undergo chemical reactions when cutting in nitrogen. It can prevent oxidation and nitridation during laser cutting. Argon gas is often used to process titanium and titanium alloys. At the temperatures that laser cutters heat metal to, titanium will chemically react even in a pure nitrogen atmosphere, which is the main reason to choose argon over nitrogen. However, argon is very expensive and not suitable for long-term use.
Summarize
Through the above introduction, we can understand the functions and advantages of each auxiliary gas, as well as their limitations. Compressed air can be used in applications that do not have strict requirements on the color of the incision surface. It is easy to obtain and less expensive. Oxygen can be used for thick metals that do not require high cutting cross-sections, thereby increasing the cutting speed. Nitrogen can be used in application scenarios that require high cutting surface quality. The workpiece has high precision and can be directly processed in the next step. Argon gas is mainly used for titanium and titanium alloys.
Selecting the appropriate auxiliary gas according to the characteristics of the metal to be processed can help users save more operating costs while ensuring cutting quality. If you want to learn more about laser cutting, please pay attention to AccTek Laser.
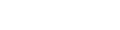
Contact information
- [email protected]
- [email protected]
- +86-19963414011
- No. 3 Zone A, Lunzhen Industrial Zone,Yucheng City , Shandong Province.
Get Laser Solutions