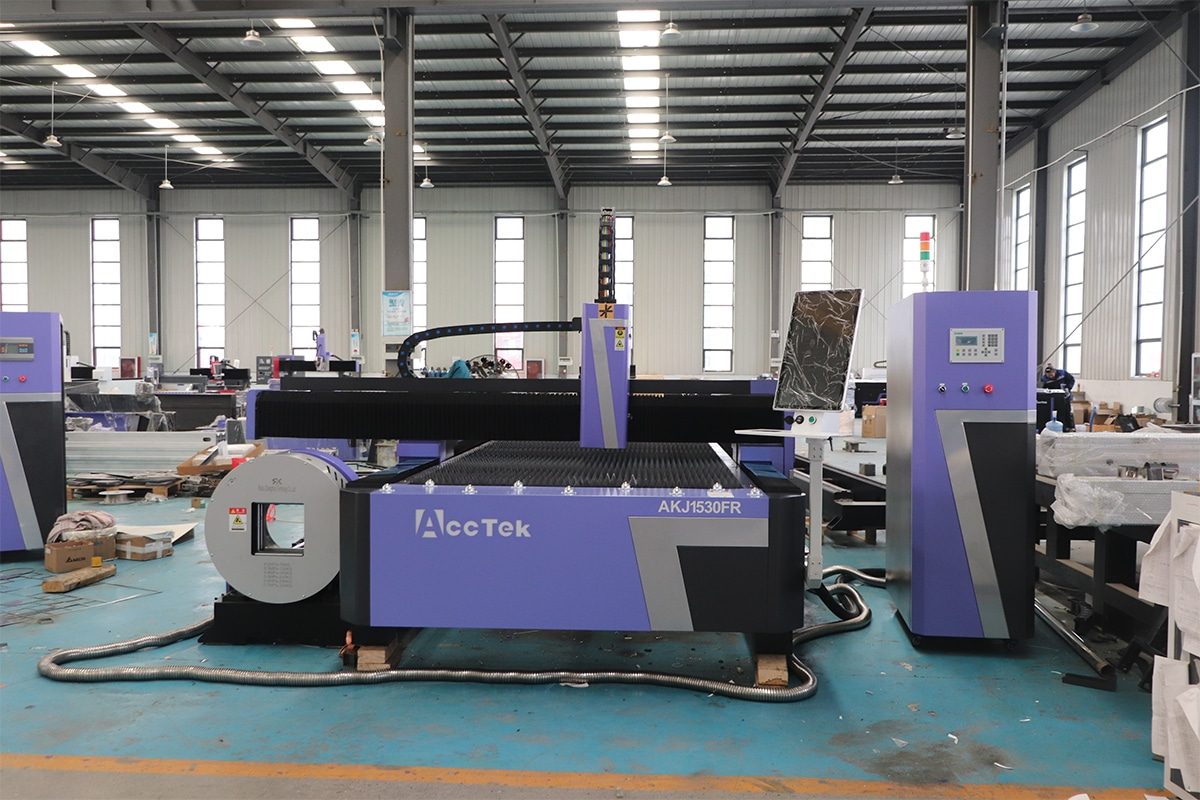
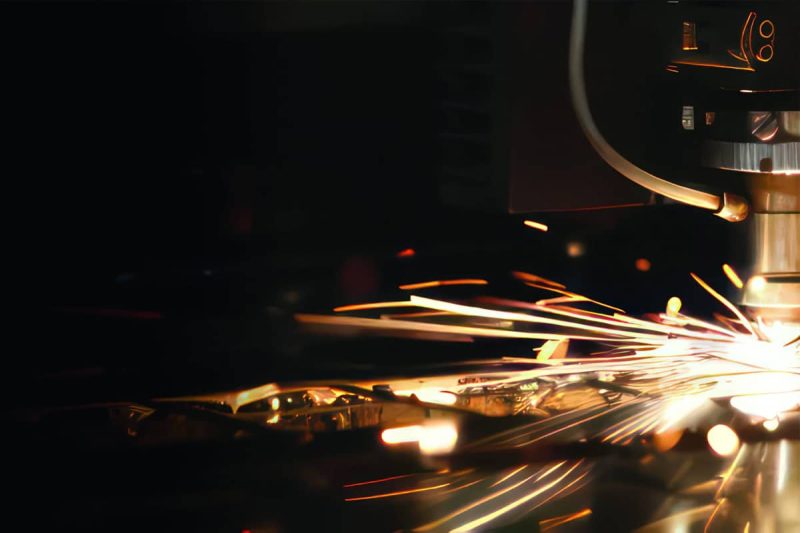
Understanding Laser Cutting Technology
What is Laser Cutting?
The Evolution of Laser Cutting Machines
1960s – The Inception
- Early Lasers: The first functional laser was invented in 1960, marking the beginning of laser technology.
- Initial Applications: Early lasers were primarily used for scientific research and had limited industrial applications due to their size and cost.
1970s – Industrial Adoption
- CO2 Lasers Emergence: The introduction of CO2 lasers made it feasible to cut non-metal materials like wood and plastics.
- Automotive Industry Use: Manufacturers began adopting laser cutting for its precision and efficiency in cutting complex parts.
1980s – Technological Advancements
- Enhanced Power and Control: Improvements in laser power sources and CNC technology expanded the capabilities of laser cutters.
- Metal Cutting: Advances allowed CO2 lasers to cut thin metals, broadening their industrial applications.
1990s – Introduction of Fiber Lasers
- Fiber Laser Development: Fiber laser technology emerged, offering higher efficiency and lower maintenance compared to CO2 lasers.
- Expanded Material Compatibility: Fiber lasers made it possible to cut a wider range of metals, including highly reflective materials like aluminum and copper.
2000s – Modernization and Optimization
- Improved Efficiency: Both fiber and CO2 lasers saw enhancements in energy efficiency and cutting speeds.
- Software Integration: The integration of advanced software allowed for better precision, automation, and ease of use.
2010s to Present – Cutting-Edge Innovations
- High-Power Lasers: The development of high-power laser sources enabled cutting thicker materials with greater speed.
- Smart Technology: Incorporation of IoT and AI for predictive maintenance and optimized performance.
- Environmental Considerations: Focus on energy efficiency and reducing the environmental impact of manufacturing processes.
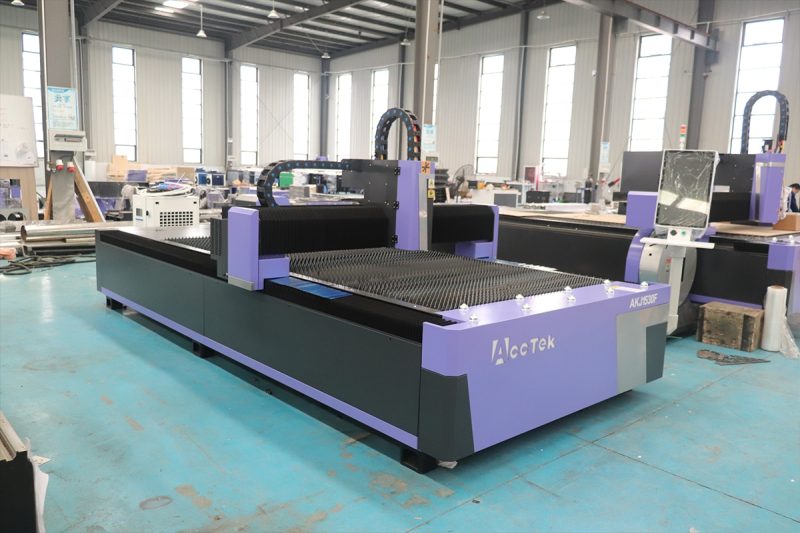
Overview of Fiber Laser Cutting Machines
How Fiber Lasers Work
Advantages of Fiber Laser Cutting Machines
Fiber laser cutting machines offer several notable advantages:
- High Efficiency: With electrical efficiency rates up to 30%, fiber lasers consume less power than other laser types, leading to lower operating costs.
- Superior Cutting Speed: Especially effective for thin to medium-thick metals, fiber lasers can cut materials up to three times faster than CO2lasers in certain applications.
- Excellent Beam Quality: The smaller focus diameter results in high-precision cutting, enabling intricate designs and tight tolerances.
- Low Maintenance: The solid-state design with fewer moving parts reduces maintenance requirements and minimizes downtime.
- Long Lifespan: Laser diodes in fiber lasers can operate for over 100,000 hours, providing long-term reliability.
- Compact Design: The fiber optic delivery system allows for a more compact machine footprint, saving valuable floor space.
- Cost-Effective Operation: Reduced energy consumption and maintenance needs contribute to lower overall operational costs.
- Enhanced Safety: Enclosed fiber optic systems minimize the risk of laser exposure, enhancing workplace safety.
Suitable Materials
Fiber laser cutting machines are particularly well-suited for cutting a variety of metal materials, including:
- Carbon Steel: Efficiently cuts carbon steel with high precision and clean edges.
- Stainless Steel: Ideal for cutting stainless steel sheets and plates used in various industries.
- Aluminum and Alloys: Capable of cutting aluminum materials with excellent edge quality.
- Copper and Brass: The ability to cut reflective metals like copper and brass sets fiber lasers apart from some other laser types.
- Titanium: Suitable for aerospace and medical applications requiring titanium components.
- Galvanized Steel: Effective in cutting coated steels without compromising the coating integrity.
- While fiber lasers excel at cutting metals, they are generally not recommended for non-metal materials like wood, plastics, or glass due to their wavelength and the absorption characteristics of these materials.
Applications
Fiber laser cutting machines are utilized across a wide range of industries due to their precision and efficiency:
- Automotive Industry: Manufacturing body panels, chassis components, and intricate parts with high accuracy.
- Aerospace and Aviation: Producing lightweight, high-strength components with exacting standards.
- Metal Fabrication: Crafting custom metal parts, enclosures, and structural elements for various applications.
- Electronics: Cutting and engraving components for electronic devices, including circuit boards and housings.
- Medical Equipment: Fabricating surgical instruments, implants, and medical devices that require precision and biocompatibility.
- Architectural and Interior Design: Creating decorative metal panels, fixtures, and art installations.
- Renewable Energy: Manufacturing parts for wind turbines, solar panels, and other renewable energy systems.
- Agricultural Machinery: Producing durable components for farming equipment.
- Signage and Advertising: Cutting metal signs, lettering, and display elements with intricate designs.
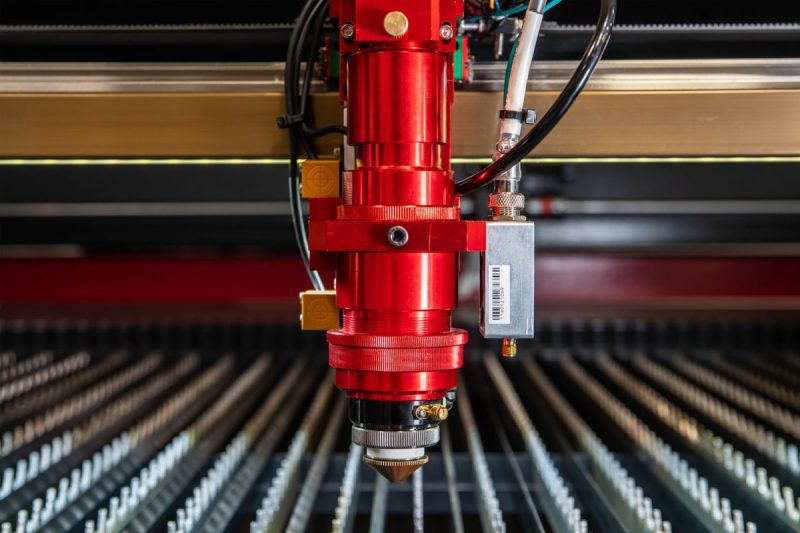
Overview of CO2 Laser Cutting Machines
How CO2 Lasers Work
Advantages of CO2 Laser Cutting Machines
CO2 laser cutting machines offer several significant advantages:
- Versatility with Non-Metals: Highly effective in cutting and engraving a wide range of non-metal materials such as wood, acrylic, plastics, glass, textiles, leather, and paper.
- Smooth Edge Quality: Produces clean cuts with smooth edges on thicker materials, often eliminating the need for additional finishing processes.
- Cost-Effective for Non-Metals: Generally more economical than fiber lasers when processing non-metal materials.
- Established Technology: As a mature and widely adopted technology, CO2 lasers have a proven track record and a wealth of available support and resources.
- Thicker Material Cutting: Capable of cutting thicker non-metal materials compared to other laser types.
- Large Working Area: Often designed with larger bed sizes, allowing for the processing of larger materials or multiple items simultaneously.
- Engraving Capability: Excellent for high-quality engraving on various materials, adding versatility to its applications.
Suitable Materials
CO2 laser cutting machines are particularly well-suited for a variety of materials, especially non-metals:
- Wood and Wood Products: Plywood, MDF, balsa wood, hardwoods, and veneers.
- Plastics and Acrylics: PMMA (acrylic), ABS, polycarbonate, polyethylene, and other plastics.
- Textiles and Fabrics: Cotton, polyester, nylon, silk, felt, and leather.
- Paper and Cardboard: Cardstock, corrugated cardboard, and paperboard.
- Rubber and Foam: Natural rubber, neoprene, EVA foam, and foam rubber.
- Glass and Ceramics: Engraving on glass surfaces and certain ceramics.
- Stone and Marble: Engraving applications on stone materials.
- Thin Metals (with limitations): Stainless steel, carbon steel, and aluminum up to certain thicknesses, often requiring higher power and assist gases.
Applications
CO2 laser cutting machines are widely used across numerous industries due to their versatility and ability to handle a variety of non-metal materials:
- Advertising and Signage: Cutting and engraving acrylic signs, display stands, promotional items, and lettering.
- Arts and Crafts: Creating intricate designs on wood, paper, and fabric for decorative items, personalized gifts, and artwork.
- Textile and Fashion Industry: Cutting patterns for clothing, accessories, lacework, and embroidery applications.
- Packaging and Prototyping: Designing custom packaging, prototypes, and architectural models from cardboard and other materials.
- Interior Design and Architecture: Crafting decorative panels, room dividers, lighting fixtures, and customized interior elements.
- Educational and Hobbyist Projects: Used in schools, universities, and by hobbyists for various projects and learning applications.
- Automotive and Aerospace (Non-Metal Components): Cutting interior components, upholstery fabrics, and insulation materials.
- Medical Equipment: Producing components from suitable materials for medical devices and equipment.
- Footwear Industry: Cutting leather and synthetic materials for shoes and accessories.
- Event and Exhibition Materials: Creating custom displays, exhibition stands, and event decorations.
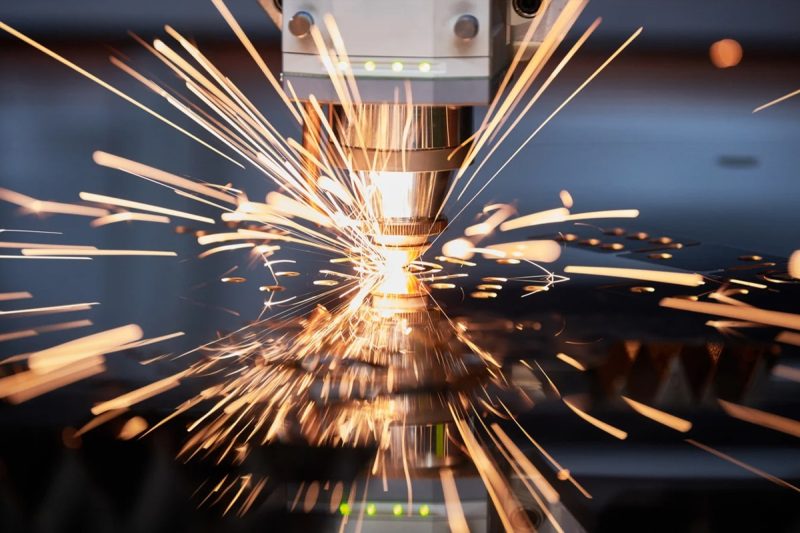
Comparative Analysis: Fiber Laser VS CO2 Laser
Cutting Speed and Efficiency
Fiber Lasers
- Speed Advantage on Metals: Fiber lasers excel at cutting thin to medium-thick metals, such as stainless steel and aluminum. They can cut these materials at speeds up to three times faster than CO2 lasers, especially for thicknesses up to 6 mm.
- High Energy Efficiency: With electrical efficiencies of up to 35%, fiber lasers consume less power, leading to reduced operational costs.
- Quick Piercing Times: The concentrated beam allows for faster piercing of materials, improving overall processing time.
- Minimal Warm-Up Time: Fiber lasers require little to no warm-up time, allowing for immediate operation and increased productivity.
CO2 Lasers
- Efficiency on Non-Metals: CO2 lasers are highly efficient when cutting non-metal materials like wood, acrylic, and plastics.
- Slower Metal Cutting Speeds: When cutting metals, CO2 lasers are generally slower compared to fiber lasers, particularly on thinner materials.
- Higher Power Consumption: Electrical efficiencies range from 10% to 15%, resulting in higher energy usage and costs.
- Longer Warm-Up Periods: CO2 lasers may require a warm-up period before reaching optimal performance.
Material Compatibility
Fiber Lasers
- Metals: Highly effective for cutting a wide range of metals, including Stainless Steel, Carbon Steel, Aluminum, Brass, Copper, and Titanium.
- Reflective Metal: Due to the shorter wavelength, it is more suitable for cutting reflective metals such as aluminum and copper, but long-term cutting will damage the laser source.
- Limitations: Not ideal for non-metal materials as these do not absorb the laser wavelength efficiently.
CO2 Lasers
- Non-Metals: Excellent for cutting and engraving non-metal materials such as Wood, Acrylic, Plastics, Glass, Textiles, Leather, and Paper.
- Metals: Can cut metals like steel and aluminum but less efficiently and with limitations, especially on reflective metals.
- Reflective Metals: Not recommended for cutting highly reflective metals due to potential laser back-reflection issues.
Maintenance and Operating Costs
Fiber Lasers
- Low Maintenance: Solid-state design with fewer moving parts reduces the need for regular maintenance.
- Minimal Consumables: Lack of mirrors and laser gas lowers the number of consumable components.
- Reduced Operating Costs: Higher energy efficiency and lower maintenance contribute to overall cost savings.
- Longevity of Components: Diode modules have a long operational life, reducing the frequency of replacements.
CO2 Lasers
- Higher Maintenance Needs: Require regular alignment and cleaning of mirrors and lenses.
- Consumable Components: Laser gas and optical elements need periodic replacement, increasing operational costs.
- Higher Energy Costs: Lower electrical efficiency leads to increased power consumption and higher energy bills.
- Maintenance Expertise: This may require specialized technicians for maintenance and repairs.
Precision and Cut Quality
Fiber Lasers
- High Precision: A shorter wavelength allows for a smaller focus diameter, resulting in precise cuts and intricate details.
- Edge Quality on Metals: Produces clean cuts with minimal thermal distortion, reducing the need for post-processing.
- Consistent Performance: Maintains high-quality cuts over time with stable beam quality.
CO2 Lasers
- Excellent on Non-Metals: Provides smooth and clean edges when cutting non-metal materials.
- Edge Quality on Thicker Materials: Better edge quality on thicker non-metals due to the wider kerf width.
- Metal Cutting Precision: This may produce more dross and require additional finishing when cutting metals.
Lifespan and Durability
Fiber Lasers
- Long Operational Life: Diode modules can last over 100,000 hours.
- Robust Construction: Solid-state design reduces wear and tear, enhancing durability.
- Environmental Resistance: Sealed fiber optics are less sensitive to environmental factors like dust and vibration.
CO2 Lasers
- Component Lifespan: Laser tubes and optical components have a shorter lifespan and need periodic replacement.
- Sensitive to Alignment: Optical mirrors and lenses require precise alignment, which can be affected by environmental conditions.
- Higher Downtime Risk: More frequent maintenance can lead to increased downtime.
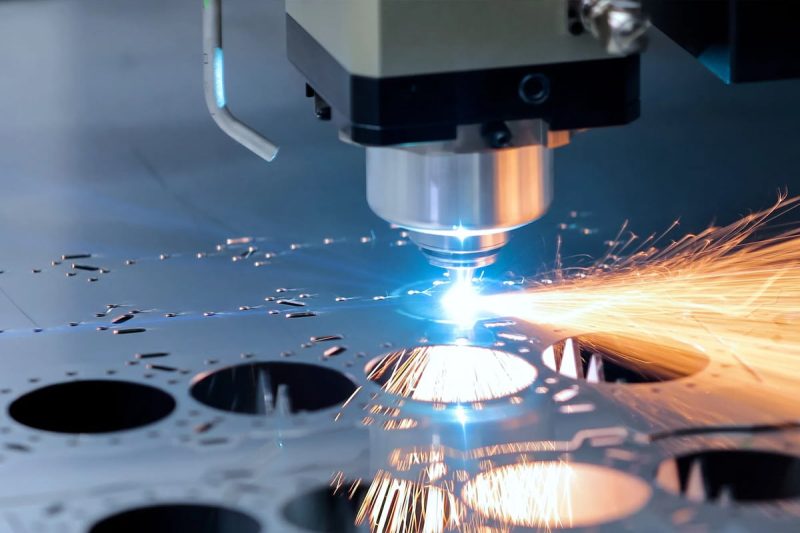
Key Factors to Consider When Choosing a Laser Cutting Machine
Material Types and Thicknesses
The type and thickness of the materials you plan to cut are fundamental considerations:
- Metals: If your primary focus is cutting metals such as steel, aluminum, brass, or copper, a fiber laser cutting machine is typically the most efficient choice. Fiber lasers excel at cutting thin to medium-thick metals with high precision.
- Non-Metals: For materials like wood, acrylic, plastics, textiles, and leather, a CO2laser cutting machine is more suitable due to its longer wavelength, which is better absorbed by non-metal materials.
- Material Thickness: Assess the maximum thickness you need to cut. Fiber lasers are efficient for thinner metals, while higher-powered models can handle thicker materials. CO2 lasers are effective for cutting thicker non-metals and metals up to certain thicknesses.
Cutting Speed and Efficiency
The cutting speed of a laser machine directly affects your production efficiency:
- Fiber Lasers: Offer faster cutting speeds on metals, especially thin to medium thicknesses. This increased speed can lead to higher productivity and quicker turnaround times.
- CO2 Lasers: Provide efficient cutting speeds on non-metals and thicker materials but are generally slower on metals compared to fiber lasers.
Considerations:
- Production Volume: High-volume operations benefit from the faster speeds of fiber lasers.
- Material Types: Match the machine’s efficiency to the materials you frequently process.
Precision and Accuracy
The precision and accuracy of your laser cutting machine determine the quality of your finished products:
- Fiber Lasers: Provide high precision with a smaller focal diameter, making them ideal for intricate designs and tight tolerances on metal parts.
- CO2 Lasers: Offer excellent precision on non-metals and are capable of producing smooth edges and fine details.
Factors Affecting Precision:
- Beam Quality: Higher beam quality leads to better precision.
- Machine Stability: A robust mechanical structure minimizes vibrations, enhancing accuracy.
- Control Systems: Advanced CNC controls improve cutting accuracy and repeatability.
Operating Costs and Maintenance
Fiber Lasers:
- Lower Operating Costs: Higher electrical efficiency reduces energy consumption.
- Minimal Maintenance: Solid-state design with fewer consumable parts lowers maintenance needs.
CO2 Lasers:
- Higher Operating Costs: Lower electrical efficiency and the need for laser gases increase expenses.
- Regular Maintenance: Optical components like mirrors and lenses require periodic cleaning and alignment.
Considerations:
- Budget Planning: Account for energy consumption, consumables, and maintenance when calculating the total cost of ownership.
- Downtime: Machines with lower maintenance needs reduce downtime, increasing productivity.
Initial Investment Cost
The upfront cost of the laser cutting machine is a significant factor:
- Fiber Lasers: Generally have a higher initial cost due to advanced technology and capabilities.
- CO2Lasers: Typically more affordable upfront, especially for lower-power models suitable for non-metal applications.
Financial Considerations:
- Return on Investment (ROI): Evaluate how quickly the machine will pay for itself through increased productivity and reduced costs.
- Financing Options: Explore leasing or financing solutions if the initial investment is substantial.
Space and Power Requirements
Consider the physical footprint and power needs of the machine:
- Machine Size: Ensure you have adequate space for the machine, including material loading and unloading areas.
- Facility Layout: Plan for proper ventilation and safety zones around the machine.
- Power Supply: Verify that your facility can meet the machine’s electrical requirements, including voltage and amperage.
Environmental Factors:
- Operating Environment: Maintain a clean, temperature-controlled environment to optimize machine performance.
- Noise and Fumes: Implement appropriate extraction systems to handle fumes and reduce noise levels.
Software and Control Systems
The software and control systems are the brains of the laser cutting operation:
- User-Friendly Interface: Intuitive controls reduce the learning curve and enhance operator efficiency.
- Software Compatibility: Ensure the machine’s software is compatible with your existing CAD/CAM programs.
- Advanced Features: Look for features like nesting software to optimize material usage and automation capabilities for improved productivity.
Connectivity:
- Industry 4.0 Integration: Machines that support IoT connectivity allow for monitoring and data analysis.
- Remote Diagnostics: Enables quick troubleshooting and reduces downtime.
After-Sales Support and Service
Reliable after-sales support can maintain machine performance:
- Technical Support: Access to knowledgeable technicians for troubleshooting and assistance.
- Training Services: Operator training ensures efficient and safe machine use.
- Warranty and Service Plans: Comprehensive warranties and optional service contracts provide peace of mind.
- Spare Parts Availability: Ready access to replacement parts minimizes downtime.
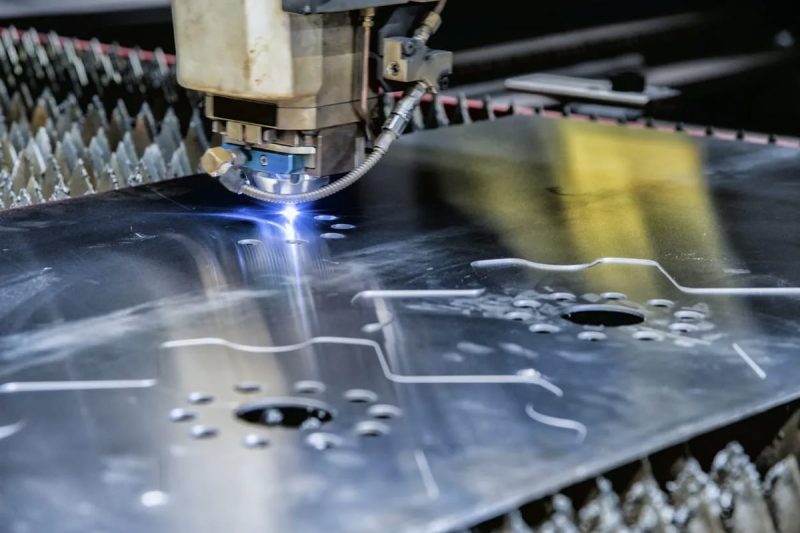
Summary
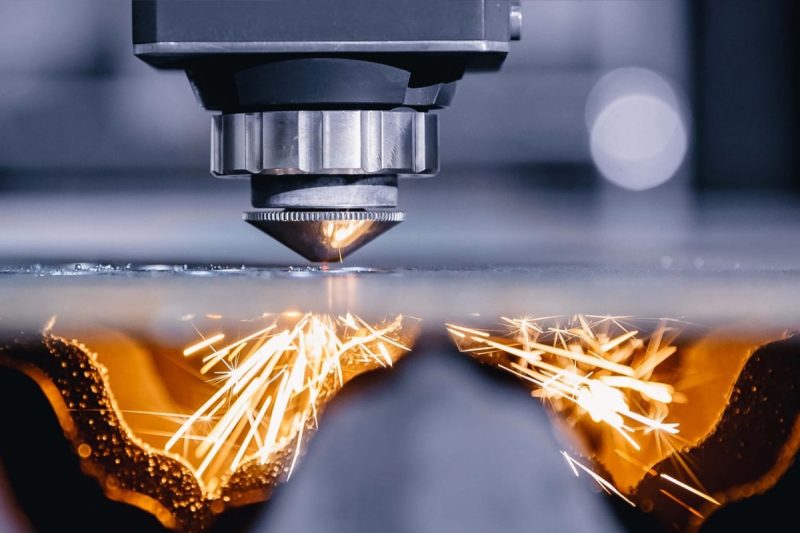
Get Laser Solutions
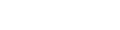
- [email protected]
- [email protected]
- +86-19963414011
- No. 3 Zone A, Lunzhen Industrial Zone,Yucheng City , Shandong Province.